Доклад на тему Литье металлов 8 класс физика (описание для детей)
Доклады
- Доклады
- Физика
- Литье металлов
Литье металлов – это процесс заливки расплавленных металлов в специально подготовленные формы. С помощью литья в полые формы, можно получить заготовки очень сложной конфигурации, изготовление которых при ковке или штамповке невозможно – это корпуса автомобильных двигателей, водопроводные краны и задвижки, рабочие колеса турбин.
Для литейного производства используют железо-углеродистые сплавы, обладающие по своим физико-механическим свойствам низкой температурой плавления, высокой текучестью, устойчивостью к образованию трещин и раковин. Чем дольше горячий металлический сплав остается в жидком состоянии, тем быстрее он заполнит форму и преждевременно не затвердеет.
К таким легкоплавким и текучим материалам относятся:
- черные металлы – чугуны и литейные стали;
- цветные металлы — алюминий, магний, титан, бронза, латунь.
Для плавления металлов на производстве используют печи на твердом, жидком, газообразном топливе; электрические и индукционные печи.
Готовые отливки получают с помощью одно- и многоразовых форм, предназначенных для литья уникальных деталей или для серийного и массового производства:
- песчано-глинистые формы – это предварительно изготовленные деревянные конструкции, состоящие из двух половинок, которые устанавливаются на формовочную смесь и заливаются горячим металлом; применяются в единичном производстве;
- кокиль – это разъемные металлические формы, скрепленные между собой стержнями; используют для литья большого количества одинаковых деталей из чугуна;
- литье под давлением – применяют для изготовления стальных отливок, ускоряя течение стали по кокилю с помощью сжатого воздуха или поршня;
- формы из полистирола – используют для производства отливок сложных форм с большим количеством мелких деталей и отверстий.
После остывания и затвердения металла в формах, готовые отливки вынимают и очищают с помощью специальных инструментов.
Литейное производство – это сложный технологический процесс, в котором используются научные разработки в области физики, химии и материаловедения. Усовершенствование и улучшение свойств литейных сплавов оказывает непосредственное влияние на качество, точность и шероховатость получаемых отливок.
Способы литья металлов
Литье в землю. Данный метод является самым старинным. В древности металл выливали в формы, сделанные из глины и песка или в землю. Вроде ничего сверхъестественного, но непосредственно перед выливанием происходит большая подготовительная работа.
Изначально подготавливается в цехе модель для отливки, деревянная или металлическая. Модель помещается в землю или формовочную смесь. После модель вынимается и получается форма. Теперь в формы подается жидкий металл. Когда он застынет, заготовку извлекут из формы и доработают на шлиф станках.
Отливка в кокиль. Но, сегодня используются более новые способы отливки металла. Заливка в кокиль более совершенна и имеет ряд превосходств перед отливкой в землю. Металл твердеет достаточно быстро и при помощи одного кокиля можно отлить не менее ста заготовок. Но, в кокиль можно отливать только жидкотекучие металлы. Те материалы, которые не обладают нужной текучестью, подают под давлением, но уже не в кокиль, а в пресс форму. Кокиль уже не выдержит давления, а форма изготавливается из прочной стали.
Выплавляемые модели. Кроме моделей из металла или дерева, довольно давно смогли изготовить модель из парафина или другого легкоплавкого вещества. Такой вид модели для отливки металла покрывается специальной оболочкой и потом сформовывается в опоку. Сама модель при отливке расплавится, поэтому перед отливкой ничего извлекать не нужно, при этом точность и качество отливки данным способом очень высокое.
Литье металла в оболочку. Данный способ выгоден тогда, когда будущая заготовка не должна обладать строго точными размерами. Такие формы изготавливают из песка и смолы. Изначально предварительно изготавливают две половины модели и кладут их на плиту, которая разогрета до 250 градусов. На них насыпают смесь, которая и образует форму. Потом две готовые формы соединяют и заливают в них металл.
Центробежный метод отливки. Этот способ подходит для отливки заготовок, которые имеют форму тел вращения. Например, обода, трубы, шестеренки и другие детали. Форма во время заливки в нее металла вращается, при этом металл хорошо обволакивает стенки формы. Данный способ может похвастаться хорошим качеством изделий.
Электрошлак. Данный способ является современным. Данный способ довольно хорош для тех случаев, когда сложность отливки не велика. Например, с помощью электрошлакового литья выливают коленчатые валы.
Картинка к сообщению Литье металлов
Популярные сегодня темы
- Изделия палехских художников
Российская лаковая миниатюра является старинным и широко известным во всем мире видом искусства, своеобразной визитной карточкой нашей страны.
Самые известные школы росписи были основаны в се
- Животные живого уголка
В современном мире люди все меньше времени проводят на природе, лишь изредка они выбираются из душных квартир. От беспрерывного пребывания в городской среде особенно страдают дети
- История исследования Антарктиды
До 17 века большинство отважных исследователей считали это путешествие почти невозможным. В то время как Антарктида жаждала увидеть человека, знаменитый исследователь капитан Джеймс Кук
- Астероиды
Астероидами называются небольшие небесные тела, которые находятся в постоянном движении вокруг орбиты. У каждого из астероидов имеется неправильная форма. И напоминают они камень.
- Подорожник
Подорожник – известное всем травянистое растение, относящееся к семейству подорожниковых. Известно более 200 видов этого растения, но не все они обладают лечебными свойствами, большая их част
- Металлы
В химии вещества делятся на две группы: неметаллы и металлы.
Первая группа не так интересна, в отличие от другой. Сами металлы представляют собой группу простых веществ, обладающие металличес
Разделы
- Животные
- Растения
- Птицы
- Насекомые
- Рыбы
- Биология
- География
- Разные
- Люди
- История
- Окружающий мир
- Физкультура
- Астрономия
- Экология
- Физика
- Экономика
- Праздники
- Культура
- Математика
- Музыка
- Информатика
ТЕХНОЛОГИЯ ЛИТЬЯ ПЛАСТМАСС ПОД ДАВЛЕНИЕМ
Детали из пластмассы широко используются во всех отраслях промышленности. Сфера деятельности человека также связана с использованием пластика от строительных материалов и бытовой техники до кухонной утвари. Самым популярным способом изготовления различных изделий является технология литья пластмасс под давлением. Современное оборудование предоставляет возможность автоматизировать производственный процесс и получать продукцию с отличными техническими характеристиками в сжатые сроки при минимальных вложениях средств. Полимерные изделия подлежат вторичной переработке, поэтому являются экологичным материалом.
Что такое литье пластмасс под давлением
Крупносерийное и массовое производство пластиковых деталей предусматривает сложный технологический процесс по впрыскиванию расплавленного пластика под высоким давлением в подготовленную литьевую форму, изготовленную из металла. Жидкая масса равномерно заполняет объем и кристаллизируется, приобретая требуемую форму. Благодаря технологии литья под давлением удается получить качественные изделия. Для реализации метода применяется сложное дорогостоящее оборудование, обеспечивающее высокую производительность. С использованием данного способа производится почти половина полимерных деталей. В качестве сырья для производственного процесса применяются гранулы термопластов, а также термореактивные порошки, придающие готовым изделиям требуемые физические и эксплуатационные качества. Термопластичные компоненты сохраняют свои параметры при вторичной переработке, а термореактивные подвергаются невозвратным химическим реакциям и образуют неплавкий материал.
Подготовленные полимерные компоненты загружаются в бункер литьевой машины, в котором они плавятся и гомогенизируются. Далее масса на скорости, благодаря создаваемому давлению, впрыскивается через специальные каналы в подготовленную форму. Происходит быстрое заполнение полости. После застывания образуется отливка. От скорости впрыска зависит качество полимерных изделий. Большей популярностью пользуются червячные пластикаторы. Они характеризуются высокой производительностью и лучшей гомогенизацией расплавленной массы. Менее популярное оборудование поршневого типа. Оно обеспечивает подачу расплавленного полимера с высокой скоростью в литьевую форму и предоставляет возможность получить эффект мрамора в случае подготовки смеси из разноцветных пластмасс. На производстве допускается использование раздельного метода. Он предусматривает подготовку расплавленной массы в предпластикаторе с червячным механизмом, а дозирование и впрыскивание вязкой массы в форму выполняется благодаря оборудованию поршневого типа.
Разновидности пластикации
Пластикация, то есть расплавление полимерного материала под давлением, во мно¬гом определяет качество изделия. Различают червячную пластикацию и поршневую. Червячные пластикаторы имеют высокую производительность, обеспечивают отличную гомогенизацию расплава, что особенно важно при использовании дробленки или суперконцентрата, и поэтому имеют наибольшее распространение. Поршневые пластикаторы используются значительно реже, поскольку они не обладают перечисленными выше качествами. Но и они не без достоинств, среди которых: способность обеспечивать высокую скорость инжекции расплава в форму, возможность реализовывать эффект мрамора или, если необходимо, яшмы, пластикацией смеси разных по цвету пластмасс. Иногда применяют раздельную пластикацию, при которой полимер сначала поступает из бункера в вышеуказанный червячный предпластикатор, приготавливающий расплав, а затем через регулирующий кран расплав направляется в поршневой пластикатор, осуществляющий дозирование и высокоскоростную инжекцию в форму. Заметим, что такое нехитрое изделие как расческа, наиболее эффективно производится на литьевых машинах с раздельной червячно-поршневой пластикацией. На этапе пластикации основными технологическими параметрами являются: температура расплава по длине цилиндрической части материального цилиндра, температура сопла, установленного на выходе из материального цилиндра, скорость вращения червяка и величина противодавления при его отходе.
Сырье, материалы для литья пластмасс под давлением
Сырьем для литья пластмасс являются термореактивные порошки, а также гранулы термопластов и термоэластопластов. Все материалы обладают различными механическими и физическими характеристиками.
Преимущество термопластичных материалов в том, что их можно подвергать повторной переработке после процесса формовки. Термореактивные материалы в процессе формовки изделия подлежат химическим процессам, которые приводят к превращению сырья в неплавкий и нерастворимый материал.
Потенциальные потребители
Среди основных потребителей одноразовой посуды:
- точки общественного питания – доля более 50%;
- кейтеринг (проведение праздничных мероприятий, кооперативов) – 20-25%;
- сезонные кафе на улице – 15-20%
- розничная продажа в магазинах – около 10%.
Предпринимателю нужно рассчитывать сбывать товар в магазины оптом.
Также можно выделить направление вендинга — продажу продуктов питания через автоматы. В России это направление только развивается, поэтому перспективы предельно радужные.
Есть сравнивать ситуацию на российском и западном рынках, в нашей стране уровень потребления заметно ниже. Это говорит о том, что у рынка есть пространство для роста.
Область применения литья полимеров под давлением
Применяя технологию, которая предусматривает литье пластмасс под давлением, предоставляется возможность изготовить простые и сложные пластиковые детали. При этом отсутствуют ограничения по габаритам и количеству изделий. Данный способ применяется в автомобилестроении, электронике, химической и многих других отраслях промышленности. С использованием способа литья пластмасс удается быстро и с требуемым уровнем качества изготовить:
- разные упаковки, крышки и разные колпачки;
- широкий ассортимент детских игрушек;
- корпуса и комплектующие для электронной техники;
- комплектующие для медицинского оборудования и прочие изделия.
Обращаем внимание на вязкость материала
Следует обратить внимание на показатель вязкости материала. Чем она ниже, тем точнее получается форма
Этот момент особенно важен, если вы работаете с таким материалом, как заливочный силикон. Также берите в учет продолжительность полимеризации. Если вы пользуетесь заливочным силиконом, то мастер-модель следует поместить в опоку (ее основу может составлять сталь или же бронза), а затем залить силиконом.
Обмазочный материал с осторожностью наносится кисточкой. При этом учитываются все неровности
Силикону нужно дать остыть, после чего извлекается мастер-модель.
Опока – это емкость из металла. Она должна быть немногим больше мастер-модели.
Преимущества данной технологии
Для производства крупных партий изделий из полимеров технология литья пластмасс под давлением характеризуется достоинствами, которые заключаются в высокой точности отлива. Благодаря инжектированию расплавленной массы с повышенной скоростью обеспечивается равномерное наполнение формы, включая микроскопические отверстия. Метод характеризуется многими достоинствами, благодаря которым он пользуется популярностью:
- Возможность производства изделий любой геометрической формы и степени сложности. Изготавливаются тонкостенные детали. Сложность конструкции зависит от пресс-формы, имеющую высокую детализацию и учитывающую все изгибы, а также отверстия будущего изделия.
- Отсутствие потребности в последующей механической обработке деталей. Некоторые сложные по конструкции изделия могут подвергаться минимальной обработке.
- Массовое производство неограниченного количества пластиковых деталей.
Срок эксплуатации металлических пресс-форм исчисляется десятками лет, поэтому они применяются для изготовления огромного количества полимерных изделий.
- Быстрая окупаемость при организации производства крупной партии пластмассовой продукции. При этом себестоимость одного изделия уменьшается без ухудшения качества при увеличении количества произведенных экземпляров. Такая зависимость объясняется разовым вложением средств на подготовительном этапе к выпуску определенного типа товара.
Технология, предусматривающая давление литья, отличается существенными затратами на этапе подготовки, поэтому для изготовления единичных изделий или мелких партий ее использование является нерентабельным.
Изготовление пресс-формы
Hdpe, pet, pp5 и другие виды пищевого пластика
Далее смотрите видео о том, как сделать пресс-форму, чтобы лить пластмассу.
Станок для литья полипропилена
Автор канала ОумелецТВ показал изготовленный своими руками станок для домашнего литья пластмассы. Он электрический. Поршень ручной. Термостат для точного контроля температуры. На видео показана его испытания. Для этих целей он будет лить нейлон или полиамид. Есть еще одно название – капрон. Из нейлона обычно делают крестовины для стульев. Как раз такая нашлась у мастера, он её раскрошил. Перед применением кружку нужно просушить при температуре до 100 градусов. Это нужно делать в течение 2-4 часов.
Загрузим гранулы в станок. Установим 250 градусов. Это оптимальная температура для литья полиамида. Подождем, когда наберется необходимое градусы. Потом установим поршень. Станок вышел на оптимальный режим, индикаторная лампочка горит. Теперь нужно подождать 5 минут, чтобы пластик полностью прогрелся изнутри.
Полиамид нагрелся. Ставим его на пресс-форму. Вдавливаем. Делаем выдержку под давлением. Видно, что он залился. Дадим ему немного остыть. Теперь разбираем пресс-форму. Училась пластмассовое изделие. Как видите, усадки нет.
Поэтапное производство
Процесс, организованный по технологии литья под давлением, выполняется поэтапно. Комплексные работы состоят из подготовительных операций и формирования изделия.
Подготовительные работы предусматривают 3D моделирование будущих изделий. С целью создания модели специалистами анализируются и изучаются чертежи, фотографии и описания продукции. После создания с помощью специального программного обеспечения и утверждения трехмерной модели выполняются следующие операции:
- Изготавливается прототип, который представляет собой образец производимой детали. С целью ускорения процесса используется современное оборудование (принтеры), выполняющее 3D печать. Изготовленный прототип позволяет оценить, испытать на предельных нагрузках и протестировать готовое изделие. При обнаружении неточностей и дефектов оперативно вносятся изменения в трехмерную модель до получения идеальной детали, соответствующей всем требованиям.
- Проектируются пресс-формы. На данном этапе очень тщательно прорабатываются все тонкости (линии, изгибы, отверстия и пр.) на основании утвержденной 3D модели.
- Изготавливаются формы для заполнения расплавленной массой. С этой целью трехмерная модель разбивается на части. Каждый полученный элемент изготавливается отдельно. На последнем этапе из частей собирается форма.
- Отливка первого экземпляра из пластика. Он тщательно проверяется и тестируется. При обнаружении неточностей дорабатывается литьевая форма.
В зависимости от сложности изделий на выполнение подготовительных работ может потребоваться несколько недель или месяцев. От полноты и точности проведения операций на этом этапе, зависит качество будущей полимерной продукции.
Процесс формирования изделий предусматривает:
- Расплавление компонентов и подачу расплава в форму.
- Создание давления с целью быстрого заполнения и равномерного распределения полимерной массы по форме.
- Охлаждение наполненного объема до полного затвердевания пластмассы. Время, требующееся для кристаллизации полимера, зависит от многих параметров: типа применяемого пластика, вязкости расплава, температуры в форме и пр.
Для негабаритных деталей процесс охлаждения длится на протяжении нескольких секунд.
- Получение готового изделия. После полного остывания форма разъединяется с целью получения детали.
Окончательная стоимость продукции рассчитывается индивидуально для каждого вида и зависит от конструктивной сложности изделия, типа полимерного материала, объема партии продукции и прочих факторов.
Как отливать изделия своими руками?
К литью деталей из пластика в домашних условиях следует относиться как к промышленному производству, но в малом масштабе. В домашних условиях вполне возможно изготовление любых деталей, не очень больших по своим размерам. Это детские игрушки, посуда и различные сувениры, корпусные элементы различных изделий.
Используя настольные станки, вполне доступно организовать литье пластика своими руками у себя дома. Сделать формы для литья можно также без посторонней помощи. Достаточно сделать заказ модели-образеца будущей детали хозяину 3D-принтера или сделать её самому, например, из дерева. Дальнейшие действия должны происходить по следующему алгоритму:
- широкой малярной кистью нужно обмазать образец силиконовым составом;
- поместить образец в опалубку, приготовленную заранее;
- залить силиконом всю пустоту опалубки;
- после семи часов, необходимых для остывания формы, нужно сделать разрез получившегося силиконового блока и таким путём получить разрезную форму из силикона.
Когда форма проверена на точное соответствие размерам будущей детали, можно начать литьё пластика в силиконовую форму ручным способом прямо у себя дома.
Технология ручного литья пластмассовых изделий
Домашнее литье пластика своими руками очень похоже на аналогичный полноформатный производственный процесс, но в уменьшенном масштабе. Если разделить этапы работы ручным способом по последовательности их выполнения, то всё будет выглядеть в виде следующего готового алгоритма действий:
- на ручной станок устанавливается литьевая насадка;
- внутренняя поверхность формы покрывается силиконовым слоем с помощью кисти;
- форма устанавливается на платформу станка;
- в загрузочный бункер станка засыпается сырьё с нужными свойствами;
- шнековым устройством производится тщательное перемешивание полимера и затем он разогревается в тепловой камере до требуемой вязкости;
- выполняется литьё детали;
- форма с деталью охлаждается;
- производится разборка формы, из неё извлекается готовая деталь.
Настольный прессовый станок для ручного литья вполне подойдёт и для производства небольшого формата, так как он универсален по своему применению. Литьё на нём можно производить, используя совершенно разные полимеры. Чтобы ускорить процесс изготовления деталей, достаточно оснастить станок несколькими формами для одних и тех же деталей. Рабочий процесс в этом случае будет практически бесперебойным, производительность труда резко увеличится.
Чтобы изготавливать на ручном станке более сложные и объёмные изделия, достаточно приобрести сварочный экструдер. С его помощью большую деталь можно изготавливать из нескольких отдельных изделий меньших размеров. Это новшество значительно расширит бизнес на литье пластмасс по ассортименту изготавливаемых изделий и почти сразу же начнёт приносить более высокую прибыль.
Методы, используемые для литья пластмасс под давлением
Для реализации технологии производства изделий из расплавленных полимеров применяются термопластавтоматы (ТПА), представляющие собой специальные литьевые агрегаты, отличающиеся расположением инжекционных узлов. Обеспечивается впрыск расплава вертикально вниз или в горизонтальной плоскости. По типу применяемого сырья классифицируют ТПА, обеспечивающие однокомпонентное или многокомпонентное литье пластмасс под давлением, выполняемое разными способами.
Инжекционный
Данный способ является самым распространенным. Нужная порция расплавленной массы скапливается в цилиндре и под напором инжектируется в форму. Давление литья обеспечивается на уровне 200 МПа. Процесс подачи массы происходит за секунды. В результате удается изготовить сложные по конфигурации детали. Предоставляется возможность получить разную толщину стенок. В качестве сырья могут использоваться термопласты и термореактивные пластикаты. Возможно использование многогнездной литьевой формы. Объем расплавленной массы должен точно соответствовать литникам.
Интрузионный
Разработан для отлива толстостенных пластмассовых изделий. Данный метод литья пластмасс предусматривает подачу расплавленного материала в пресс-форму благодаря вращению червячного механизма. С целью компенсации естественной усадки, образуемой после охлаждения массы, червяк уже осевым движением подает недостающий расплав. При реализации этого способа количество впрыскиваемой массы может превышать объем, требующийся для отлива детали. Давление литья незначительное, поэтому метод применяется для получения изделий простой формы с ограниченной гнездностью.
Инжекционно-прессовый
Этот метод литья пластмасс позволяет производить изделия, характеризующиеся большой прессовочной площадью. Падение давления в процессе наполнения объема обуславливает разные прочностные характеристики в центре и в крайних зонах деталей. Особенность технологии в формировании давления массы не только благодаря инжекции, но и благодаря применению прессового механизма перемещающегося узла. Поэтому применяются формы, конструктивно предусматривающие перемещение частей после их соединения.
Инжекционно-газовый
ИГЛ является новым методом, использующимся для переработки полимеров. Сущность технологии заключается в расплаве сырья и подачи массы через инжекционные узлы с целью заполнения формы на 80‒95%. Через специальный ниппель с помощью компрессора под давлением 80 МПа закачивается газовая смесь (углекислый газ). Она раздувает расплав, заполняя все углубления и увеличивающая толщину пластика. После формирования детали газ испаряется в специальный приемник, а в форму подается необходимое количество расплавленной массы для окончания изготовления изделия.
Инжекционно-газовое литье под давлением предоставляет возможность сэкономить почти половину используемого дорогостоящего сырья, уменьшить вероятность получения брака, сократить время производственного цикла, а также оптимизировать стоимость оснастки. Технология требует точного управления ЛМ, отличается сложной конструкцией сопел и повышенными требованиями к литьевой системе.
Многослойный
Данный способ предусматривает применение для процесса двух или трех инжекционных узлов с целью пластикации полимера, отличающегося определенными свойствами. В результате получаются многоцветные детали, структуру которых составляют полимерные материалы разного вида. Многослойный метод литья пластмасс используется для производства гибридных конструкций, у которых неответственные части изготавливаются из вторичного сырья.
Сэндвич-литье
Технологией предусматривается переменная подача в форму расплавленного полимера из разных пластикаторов. С этой целью к литнику с переключающим механизмом, в качестве которого используется игольчатый клапан, подключаются два инжекционных модуля. Клапан с определенной последовательностью или одновременно подключает их к пресс-форме. Из первого под давлением инжектируется масса для формирования наружного покрытия изготавливаемой детали. Внутренние полости заполняются полимером, поступающим из второго узла. На последнем этапе снова коммутируется первый узел для добавления расплава.
Соинжекционный
С целью обеспечения литья под давлением данного типа используются сопла, изготовленные по специальной конструкции в виде разделительной головки. Этот способ широко используется с целью получения деталей, имеющих более двух слоев, полностью или частично отличающихся цветом.
Литье в многокомпонентные формы
Метод MСIM предоставляет возможность организовать производство разноцветных изделий, отличающихся разноплановой конструкцией. В этих деталях центральные и периферийные части изготавливаются из разного полимерного материала. При реализации этого способа инжекционные узлы работают в стандартном режиме, а конфигурация детали формируется с помощью особенной структуры пресс-формы. Она конструктивно состоит из двух систем, замыкающихся с первым и вторым узлом, а также включает подвижные вставки, сдвигающиеся с помощью пневмоприводов. Каждая вставка формирует конструктивные элементы детали. Узлы работают в разных режимах (инжекции или интрузионном) независимо друг от друга. Благодаря такой конструктивной особенности удается формировать изделия больших размеров.
Ротационный
Данный способ представляет собой разновидность литья пластмасс в сложные формы с применением вставки съемного типа. После того, как сформируется центральная часть детали (работает первый узел), вставка удаляется. В освободившийся объем поступает расплавленная масса из второго модуля. Производственный цикл отличается дополнительной операцией, предусматривающей разъединение литьевой формы с целью удаления или установки вставки. Данный метод отличается более низкой производительностью.
Мини-заводы
Заводом или мини-заводом в сфере переработки полимеров называют комплекс станков и линий. Для примера можно рассмотреть линию по переработке твердого пластика производительностью 800 кг/ч от компании СтанкоПолимер.
Так как данная линия содержит в своем составе не только станки, но и другие линии, ее по праву можно называть мини-заводом.
Состоит она из:
- моющей дробилки;
- горячей мойки для пластика;
- водоотделителя;
- универсальной мойки;
- сушки каскадной;
- циклона;
- дозатора шнекового;
- линии грануляции;
- транспортеров для загрузки и выгрузки.
Чтобы узнать, сколько стоит этот завод, нужно связаться с поставщиком на сайте.
Особенности применения различных полимеров
Для литья пластика под давлением используются разные компоненты, отличающиеся физическими параметрами.
Полиэтилен низкой плотности
ПЭНП характеризуется быстрым расплавлением. После охлаждения кристаллизируется и меняет твердость. Требуется соблюдать определенное давление и обеспечить максимально равномерный нагрев пресс-формы. Поэтому для охлаждения, вход воды обеспечивается возле литниковых сопел, а отвод в дальней точке. Заполнение охлаждающей жидкостью выполняется быстро с хорошей вентиляцией формы.
Полиэтилен высокой плотности
ПЭВП по сравнению с полиэтиленом НП отличается лучшей кристаллизацией и меньшей степенью текучести в расплавленном виде. Литье пластмассы этого типа широко практикуется для получения изделий с тонкими стенками, но при этом обеспечивается достаточная жесткость конструкции.
Полипропилен
ПП отличается кристалличностью, не превышающей 60%. Процесс выполняется при пониженном давлении и достаточно высокой температуре пластикации, которая в зависимости от марки материала может достигать 280 ºС. Давление расплава формируется на уровне 140,0 МПа. Вязкость полученной массы регулируется скоростью сдвига и незначительно зависит от температурного режима.
Полистирол
ПС представляет собой материал, который в результате применения технологии литья под давлением отличается легкой текучестью в расплавленном виде. Позволяет изготавливать изделия, которые характеризуются жесткостью конструкции и тонкими стенками. Полимер чувствительный к перегреву.
Полистирол ударопрочный
УПС – полимер, отличающийся несколько большей вязкостью, чем обычный полистирол и дает при охлаждении большую усадку. Применяется для тонкостенных деталей с повышенной устойчивостью против механического воздействия.
Акрилонитрил-бутадион-стирольный пластик
АБС-пластик характеризуется большой вязкостью в расплавленном состоянии, отличается трудной переработкой и требует повышенного давления. Применяется для изготовления деталей с тонкими стенками, но в отличие от, например, полистирола, АБС-пластик имеет высокую жесткость и устойчивость к ударам.
Полиметилметакрилат
ПММА позволяет получать изделия разной формы и конфигурации. Отличается низкой термической стабильностью и чувствительностью к перегреву с потерей физических параметров. Требует дополнительной сушки. В процессе обработки нужен точный температурный контроль. Особенность материала в образовании пузырей при инжектировании в холодную пресс-форму, поэтому в ней минимизируется количество плавных переходов.
Поливинилхлорид
Для литья под давлением широко применяется ПВХ, характеризующийся легкостью обработки. Материал чувствителен к соблюдению температурного режима и теряет свойства при перегреве. При нахождении в расплавленном состоянии отличается нестабильностью и автокаталитической деструкцией, проявляющейся в разном цветовом оттенке. Диапазон цвета может меняться от слоновой кости до вишневого оттенка. Для получения всех свойств полимера требуется осуществлять процесс пластикации за минимальное время.
Полиамид
ПА представляет собой кристаллический термопласт, отличающийся гигроскопичностью и хорошей текучестью массы. При нахождении в расплавленном состоянии объем увеличивается на 15%. По причине низкой термической стабильности процесс литья пластмасс этого типа выполняется за минимальное время. В расплаве возможно образование пузырей. Материал требует дополнительного времени для тщательной просушки. Процесс пластикации обеспечивается при давлении 100 МПа. При наполнении литьевых форм допускается ориентация частиц.
Поликарбонат
ПК является теплостойким полимером. Характеризуется высокой термостабильностью и повышенной вязкостью в расплавленном состоянии, зависящей от температурного режима. Пресс-форма нагревается до температуры 100 ºС. По причине повышенной гигроскопичности материала, для нормального литья под давлением требуется предварительный прогрев в цилиндре литьевой машины и тщательная сушка.
Полиэтилентерефталат, полибутилентерефталат и полиоксиметилен
ПЭТФ, ПБТФ и ПОМ классифицируются как полимеры, отличающиеся высокой термической стабильностью. Процесс литья пластмасс этого типа предусматривает дополнительную сушку, выполняемую до снижения влаги на уровень 0,01%. В расплавленном состоянии имеют вязкость средней степени, которая снижается при уменьшении температуры. Для получения тонкостенных изделий используется раздув с использованием воздуха.
Краткая история появления
Считается, что первооткрывателем пластмассы был британский изобретатель Паркс. В 1855г. он решил чем-нибудь заменить материал бильярдных шаров. В то время они состояли из слоновой кости.
Он смешал масло камфорного дерева, нитроцеллюлозу (хлопок + азотная и серная кислота) и спирт. При нагревании получил однородную жидкую смесь, которая при охлаждении застыла и стала твердой. Это и была первая разновидность пластмассы, полученная искусственным путем из природных и химических материалов.
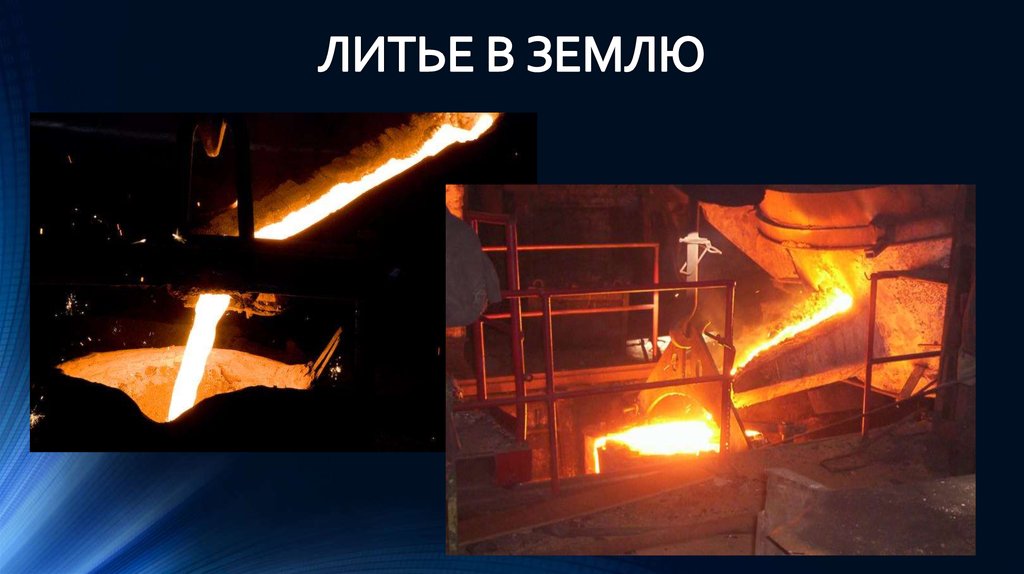
И только через сто лет в 1953г. немецкий профессор Штаудингер открыл синтетическую макромолекулу (молекула с очень большим количеством атомов и большой массой). Она то и стала базовой прародительницей для получения разнообразных видов промышленного пластика.
Если не вдаваться в научные подробности, новые виды пластмасс создаются следующим образом: в макромолекуле, особым образом, меняют расположение звеньев малых молекул. Эти цепочки называются полимерами. От этих «перестроений» рождаются материалы с определенными физико-механическими характеристиками.
Основные виды брака и методы его устранения
В процессе литья под давлением по причине нарушения технологичного процесса, превышения температуры расплава и по причине других факторов возникают дефекты, которые снижают качество продукции:
- Неполное наполнение пресс-формы (недолив). Возникает по причине недостаточного объема впрыскивающегося полимера. Такая ситуация возможна из-за слабого нагрева расплава, низкой текучести массы, засорения сопла или разводящих каналов.
- Превышение объема формы (перелив) в процессе литья пластмасс, вызывающее образование грата по стыку (облой). Дефект возникает по причине неисправности дозатора или превышения допустимой температуры расплавленного полимера. Выход излишка массы возникает также при недостаточно сильном смыкании пресс-формы.
- Видны стыковочные швы на границе спайки отдельных частей детали, отличающиеся низкой прочностью. Такие стыки образуются при слишком низкой температуре пластикации. Причина дефекта кроется также в неправильной конструкции или недостаточном нагреве литьевой формы, что приводит к преждевременному охлаждению потоков до того, как они сольются. В результате не удается добиться полного сваривания.
- На поверхности изделия образуются пузыри, в внутри пустоты. Такой брак является результатом наличия в расплаве летучих компонентов, отличающихся повышенным газовыделением при перегреве. Происходит вспучивание мягкой массы.
- Образование на поверхности усадочных раковин (углублений).
Причина дефекта в повышенной усадке массы в случае перегрева или недостаточном объеме расплавленной массы из-за низкого давления, а также недостаточной пропускной способности сопла. Подобные раковины появляются при неравномерном нагреве и недостаточной вентиляции литьевой формы.
- Коробление изготовленных деталей. Брак возникает при чрезмерной внутренней напряженности, возникающей по причине температурной неравномерности частей формы. Некачественные изделия получаются также при несоблюдении времени, необходимого для выдержки массы с целью полного застывания.
- Трещины на поверхности. Возникают по причине остаточного напряжения или в случае сильного прилипания жидкой массы к стенкам.
- Дефекты поверхности деталей, проявляющиеся царапинами и сколами. Брак появляется в случае небрежного обращения с готовой продукцией или некачественно оформленной пресс-формы.
- Узоры, которые напоминают морозную разрисовку на стекле, появляются по причине чрезмерного количества влаги в инжектируемой расплавленной массе.
Недостаток имеет место при нарушении процесса сушки и вентиляции формы.
- В случае наличия влаги в полимерном материале сверх установленной нормы происходит расслоение структуры. Дефект возникает также в случае наличия застывших литников, не совмещенных с основной массой.
- Неравномерная (разная) тоновая окраска изделия. Причина заключается в использовании термически нестойкого красителя и перегреве расплавленной массы.
- Несоответствие полученного изделия требуемым размерам, превышение стандартного допуска. Возникает по причине сильной усадки пластика при затвердении или некачественно изготовленной пресс-формы.
Параметры впрыска полимерного материала при ЛпД
Давление, развиваемое при впрыске ТПА, зависит от нескольких параметров:
- вязкости расплавленного полимера,
- особенностей литниковой системы, в частности наличия холодного или горячего канала,
- конструкции прессформы,
- конструкции пластикового изделия и места впуска расплава.
Давление в прессформе при впрыске расплавленной полимерной массы растет по мере заполнения формообразующей полости и дальнейшей выдержки отливки. При этом, как правило, величина заданного давления выдержки достигает 30-50 процентов от заданной величины параметра. Эти параметры на современных термопластавтоматах задаются в системе управления и реализуется при помощи гидравлической (реже самой современной – электрической) системы литьевой машины.
Примеры браков и способы устранения
Качественное и соответствующее требованиям стандартов литье пластмасс под давлением обеспечивается при условии использования технически исправной машины, строгого выполнения технологических этапов и применения качественного сырья. В таблице перечислены типы брака и действия по их недопущению.
Дефект | Почему появляется | Как устраняется |
На поверхности изделия: | ||
пузыри | Превышена влажность полимера | Сушка используемого сырья |
матовые пятна | Перегретая вязкая масса | Снижение нагрева расплава.![]() |
темные полосы | Локальный перегрев расплава. Свободные зоны во впускных каналах | Уменьшение температуры пластикации. Удаление мертвых зон |
пленка | Использовано много смазки для литьевой конструкции | Очистка цилиндра, пресс-формы. Минимизация смазки |
линии | Повышенная вязкость полимерного материала и неравномерное наполнение объема | Контроль полноты заполнения прессовочной формы |
наличие пустот | Нарушение температурного режима из-за просачивания воздуха в форму | Повышение эффективности вентиляции формы. Снижение скорости подачи расплава |
Локальный пережог детали | Нагрев газа в объеме для формовки вследствие его сжатия | Обеспечение вентиляции формы |
Грязное изделие | Попадание в расплав инородных частиц или дефекты червяка | Контроль используемого сырья и контактирующих с вязкой массой плоскостей |
Волнистость поверхности на противоположной литнику стороне детали | Остывание массы в процессе инжектирования | Регулировка температурного режима |
Белые вкрапления, похожие на пузыри | Превышен нагрев, слабое давление литья, короткая выдержка полимера | Понижение нагрева каналов, поднятие давления, добавление времени на кристаллизацию полимера |
Швы возле литника | Слишком быстрое охлаждение расплавленной массы в точке подачи | Нагрев формы возле литника, увеличение геометрии сопла |
Непрочные сварные стыки | Ускоренное охлаждение вязкой массы на этапе заполнения объема | Нагрев формы и полимера.![]() |
Расслоение детали | Попадание сторонних включений. Большая разница температуры вязкой массы и формы | Очистка цилиндра и каналов |
Грат на стыках | Неэффективное запирание пресс-формы для изготовления деталей | Увеличение запирающего усилия, уменьшение скорости подачи вязкой массы, снижение давления и уменьшение объема подающей массы |
Затрудненный съем изделий | Нарушение технологии, форма неоптимальной конструкции | Понижение давления, полирование зеркала формы, формирование воздушных прослоек |
Технология литья под давлением, реализуемая на современном оборудовании с соблюдением требований процесса и применением качественного сырья позволяет изготавливать в большом количестве качественные изделия, востребованные в разных отраслях промышленности и бытовых условиях. При выборе оптимального метода пластикации удается наладить рентабельное производство деталей любой сложности.
Принцип работы термопластавтомата
Литьевая машина осуществляют загрузку гранулированного (гораздо реже порошкобразного) полимера из загрузочного бункера сырья в зону загрузки материального цилиндра. Затем путем нагрева и пластикации (перемешивания) расплавленной массы шнеком осуществляется его переход в вязкотекучее (близкое к жидкому) состояние. После набора необходимой дозы полимера термопластавтомат при помощи создаваемого гидроцилиндром усилия производит инжекцию (впрыск) расплавленного пластика в прессформу. Затем в ее полости происходит выдержка отливки под давлением и стадия охлаждения (для реактопластов – отверждения).
В ходе последнего этапа производственного цикла машина размыкает форму и выталкивает готовый продукт, реже изделия вынимаются оператором (полуавтоматический режим). Современные производственные единицы включают кроме термопластавтомата так же различные средства автоматации, обычно называемые «роботами». Современные роботы участвуют в съеме отливки из области прессформы, также они могут закладывать в полость оснастки этикетки, закладные детали, а, кроме того, участвовать в «дальнейшей судьбе» отформованной детали, например в ее постобработке, укладке и упаковке.
Инжекционное прессование
Этот технологический процесс отличается от стандартного тем, что впрыск полимерного материала делают в слегка раскрытую прессформу (в этом случае уместно использовать именно такое название оснастки) за небольшое время до ее окончательного смыкания. Окончательное уплотнение полимера и формование готового продукта осуществляются при полном смыкании прессформы. Способом инжекционного прессования изготавливают различные изделия как из термопластов, так и реактопластов. Метод применим в случае недостаточных характеристик ТПА для данной отливки, в частности усилия смыкания. Также качество при таком прессовании на термопластавтомате в меньшей степени зависят от ориентации макромолекул при впрыске (анизотропии), что может повысить качество продукта в части меньшей усадки (если необходимо), лучших механических свойств и меньшего коробления.
Интрузия
Интрузией называется процесс частичного заполнения формообразующей полости в режиме экструзии за счет вращательного движения шнека. Обычно он применяется для производства тяжелых, материалоемких изделий из пластиков. Таким образом можно применять термопластавтоматы с недостаточным для данного изделия объемом впрыска, т.к. форма заполняется не только за счет поступательного, но и за счет вращательного движения шнека в исходном положении. Для интрузии важно, чтобы полимерный материал был достаточно текучим, а литниковые каналы достаточно большого сечения. Также важно отметить, что режимом интрузии оснащаются не все ТПА, необходимо проверить его наличие в спецификации машины.
Физика Перышкин 8 класс Доклад №1, История изобретения паровых машин — ГДЗ Решебники
Авторы: Перышкин Год: 2019 год Издательство: Дрофа
На данной странице предствлены решения к учебнику по Физике для учеников 8 класса, Учебник издательства «Дрофа» 2019 года.
Популярные учебники
Тепловые явления. (Параграфы с 1 по 24)
§1.

Вопросы:
1 2 3 4§2. Внутренняя энергия
Вопросы:
1 2 3 4§3. Способы изменения внутренней энергии тела
Задание:
1§4. Теплопроводность
Упражнение:
1 2§5. Конвекция
Вопросы:
1 2 3 4 5 6§6. Излучение
Задание:
1§7. Количество теплоты. Единицы количества теплоты
Упражнение:
1 2§8. Удельная теплоёмкость
Вопросы:
1 2 3 4§9. Расчёт количества теплоты, необходимого для нагревания тела или выделяемого им при охлаждении
Задание:
1§10. Энергия топлива. Удельная теплота сгорания
Упражнение:
1 2 3 4§11. Закон сохранения и превращения энергии в механических и тепловых процессах
Вопросы:
1 2 3 4 5 6§12. Агрегатные состояния вещества
Задание:
1§13. Плавление и отвердевание кристаллических тел
Упражнение:
1 2 3§14. График плавления и отвердевания кристаллических тел
Вопросы:
1 2 3§15.
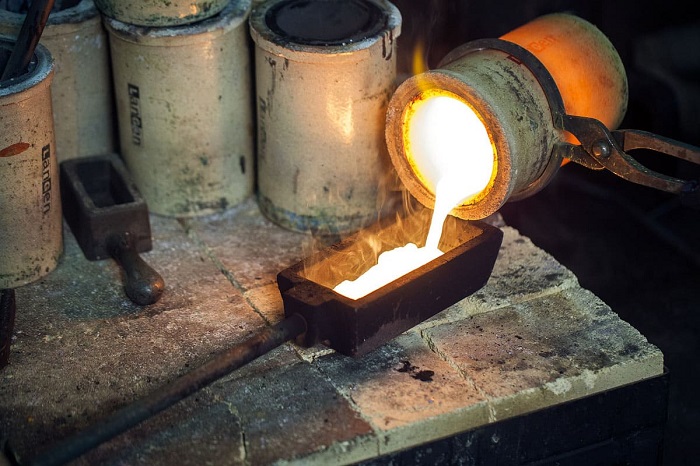
Задание:
1§16. Испарение. Насыщенный и ненасыщенный пар
Упражнение:
1 2 3§17. Поглощение энергии при испарении жидкости и выделение её при конденсации пара
Вопросы:
1 2 3 4 5 6§18. Кипение
Упражнение:
1 2§19. Влажность воздуха. Способы определения влажности воздуха
Вопросы:
1 2 3 4§20. Удельная теплота парообразования и конденсации
Упражнение:
1 2 3§21. Работа газа и пара при расширении
Вопросы:
1 2 3 4§22. Двигатель внутреннего сгорания
Упражнение:
1 2 3§23. Паровая турбина
Вопросы:
1 2 3§24. КПД теплового двигателя
Задание:
1Упражнение:
1 2 3 4Вопросы:
1 2 3 4 5Задание:
1Упражнение:
1 2 3 4Вопросы:
1 2 3 4Вопросы:
1 2 3Упражнение:
1 2 3 4 5Вопросы:
1 2 3Задание:
1Вопросы:
1 2 3 4 5 6Задание:
1 2Упражнение:
1 2 3 4 5Вопросы:
1 2 3 4 5 6 7 8Задание:
1 2 3Вопросы:
1 2 3 4 5 6Упражнение:
1 2 3 4 5 6 7Вопросы:
1 2 3Упражнение:
1 2 3Задание:
1Вопросы:
1 2 3 4 5Упражнение:
1 2 3Вопросы:
1 2 3 4 5Задание с докладом:
Доклад №1, Как образуется роса, иней, дождь и снег Доклад №2, Круговорот воды в природе Доклад №3, Литьё металловУпражнение:
1 2 3 4 5 6Вопросы:
1 2 3Вопросы:
1 2 3 4 5Вопросы:
1 2 3Вопросы:
1 2 3Задание с докладом:
Доклад №1, История изобретения паровых машин Доклад №2, История изобретения турбин Доклад №3, Первые паровозы Стефенсона и Черепановых Доклад №4, Достижение науки и техники в строительстве паровых турбинУпражнение:
1 2 3Электрические явления.
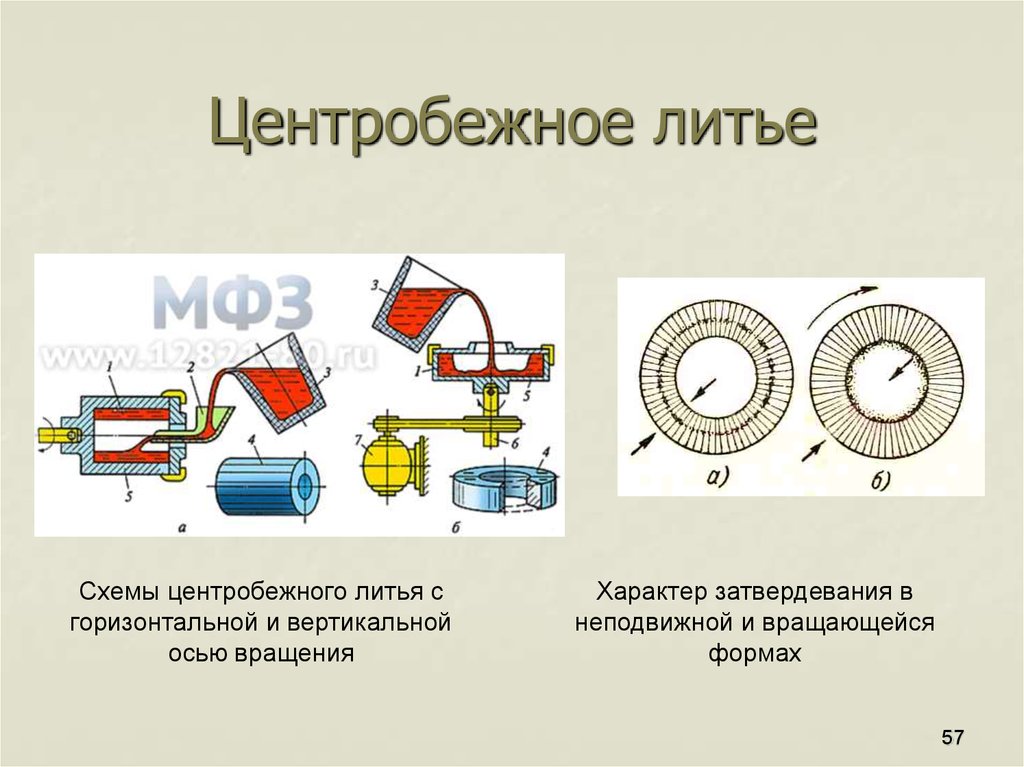
§25. Электризация тел при соприкосновении. Взаимодействие заряженных тел
Вопросы:
1 2 3 4§26. Электроскоп
Задание с докладом:
1 2§27. Электрическое поле
Упражнение:
1 2§28. Делимость электрического заряда. Электрон
Вопросы:
1 2 3 4§29. Строение атомов
Вопросы:
1 2 3 4§30. Объяснение электрических явлений
Упражнение:
1 2§31. Проводники, полупроводники и непроводники электричества
Вопросы:
1 2 3§32. Электрический ток. Источники электрического тока
Вопросы:
1 2 3 4 5§33. Электрическая цепь и её составные части
Упражнение:
1 2 3§34. Электрический ток в металлах
Вопросы:
1 2 3 4§35. Действия электрического тока
Упражнение:
1 2§36. Направление электрического тока
Вопросы:
1 2 3 4§37. Сила тока. Единицы силы тока
Упражнение:
1 2 3 4§38.
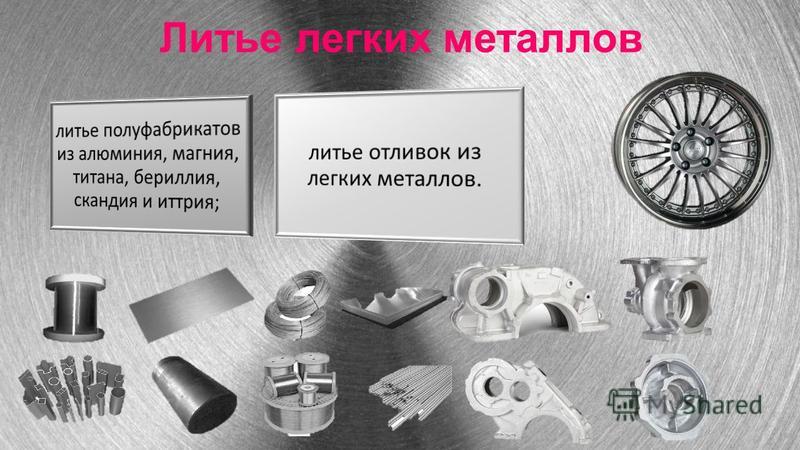
Вопросы:
1 2 3 4 5 6 7§39. Электрическое напряжение
Задание с докладом:
Доклад №1, Типы зарядных устройств Доклад №2, Применение аккумуляторов§40. Единицы напряжения
Вопросы:
1 2 3 4§41. Вольтметр. Измерение напряжения
Упражнение:
1 2 3 4§42. Зависимость силы тока от напряжения
Задание с докладом:
Доклад №1, Движение электоронов в металлах§43. Электрическое сопротивление проводников. Единицы сопротивления
Упражнение:
1 2 3 4§44. Закон Ома для участка цепи
Вопросы:
1 2 3 4 5§45. Расчёт сопротивления проводника. Удельное сопротивление
Задание:
1 2§46. Примеры на расчёт сопротивления проводника, силы тока и напряжения
Вопросы:
1 2 3§47. Реостат
Вопросы:
1 2 3 4 5 6§48. Последовательное соединение проводников
Упражнение:
1 2 3§49. Параллельное соединение проводников
Вопросы:
1 2 3§50.
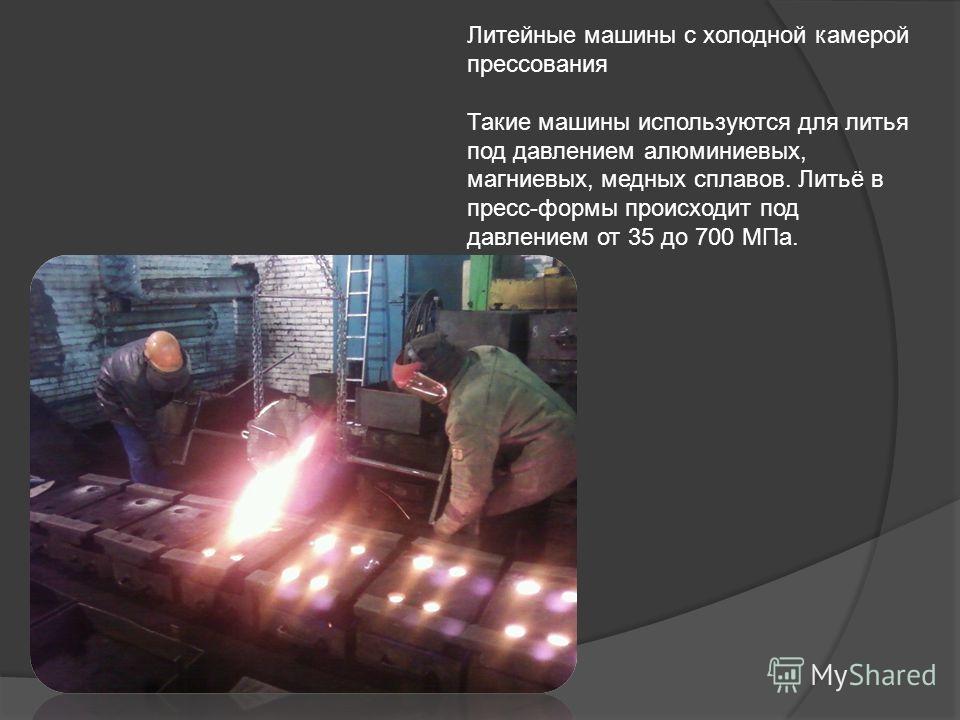
Упражнение:
1 2 3 4§51. Мощность электрического тока
Вопросы:
1 2§52. Единицы работы электрического тока, применяемые на практике
Вопросы:
1 2 3§53. Нагревание проводников электрическим током. Закон Джоуля—Ленца
Вопросы:
1 2 3 4§54. Конденсатор
Упражнение:
1 2 3§55. Лампа накаливания. Электрические нагревательные приборы
Вопросы:
1 2 3§56. Короткое замыкание. Предохранители
Упражнение:
1 2Вопросы:
1 2 3 4Упражнение:
1 2Вопросы:
1 2 3 4 5Упражнение:
1 2 3 4 5 6 7Вопросы:
1 2 3 4 5Упражнение:
1 2 3 4Вопросы:
1 2 3 4 5Упражнение:
1 2 3 4 5Вопросы:
1 2 3 4Упражнение:
1 2 3 4Вопросы:
1 2 3 4 5Упражнение:
1 2 3 4 5Вопросы:
1 2 3 4Упражнение:
1 2 3Вопросы:
1 2 3 4 5 6Задание:
1Упражнение:
1 2 3Вопросы:
1 2 3Задание:
1 2Упражнение:
1 2 3Вопросы:
1 2 3 4Упражнение:
1 2 3 4Вопросы:
1 2 3 4Задание с докладом:
Доклад №1, Лейденская банка Доклад №2, История создания конденсаторвУпражнение:
1 2Вопросы:
1 2 3 4Задание с докладом:
Доклад №1, Использование теплового действия электрического тока в устройстве теплиц и инкубаторовВопросы:
1 2 3 4 5Электромагнитные явления.
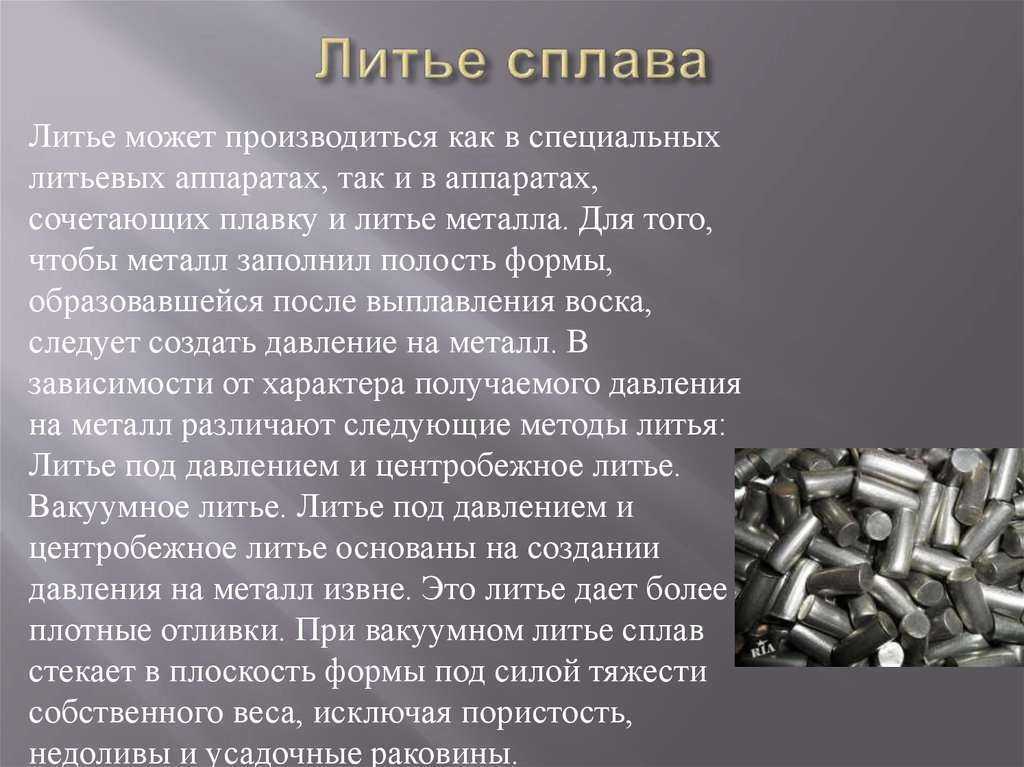
§57. Магнитное поле
Вопросы:
1 2 3 4§58. Магнитное поле прямого тока. Магнитные линии
Упражнение:
1 2§59. Магнитное поле катушки с током. Электромагниты и их применение
Вопросы:
1 2 3 4 5§60. Постоянные магниты. Магнитное поле постоянных магнитов
Упражнение:
1 2§61. Магнитное поле Земли
Вопросы:
1 2 3 4 5§62. Действие магнитного поля на проводник с током. Электрический двигатель
Задание:
1 2 3Упражнение:
1 2 3 4Вопросы:
1 2 3 4 5 6Задание:
1 2Упражнение:
1 2Вопросы:
1 2 3 4 5Задание:
1 2 3Упражнение:
1 2Вопросы:
1 2 3 4 5 6Задание:
1 2Световые явления. (Параграфы с 63 по 70)
§63. Источники света. Распространение света
Вопросы:
1 2 3 4 5 6§64. Видимое движение светил
Задание:
1 2 3§65. Отражение света.
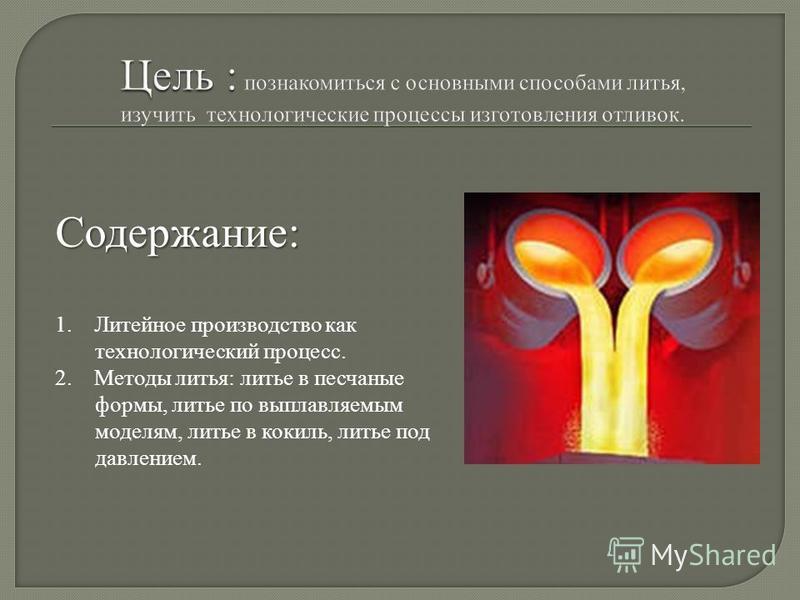
Упражнение:
1 2 3§66. Плоское зеркало
Вопросы:
1 2 3§67. Преломление света. Закон преломления света
Задание:
1 2 3 4§68. Линзы. Оптическая сила линзы
Вопросы:
1 2 3 4§69. Изображения, даваемые линзой
Упражнение:
1 2 3 4§70. Глаз и зрение
Вопросы:
1 2 3 4Лабораторные работы:
Упражнение:
1 2 3 4Задачи для повторения:
Вопросы:
1 2 3Задание:
1Упражнение:
1 2 3 4Вопросы:
1 2 3 4 5 6Упражнение:
1 2Вопросы:
1 2 3 4 5 6 7 8Упражнение:
1 2 3 4Вопросы:
1 2 3Задание:
1 2 Лабораторная работа №1 Лабораторная работа №2 Лабораторная работа №3 Лабораторная работа №4 Лабораторная работа №5 Лабораторная работа №6 Лабораторная работа №7 Лабораторная работа №8 Лабораторная работа №9 Лабораторная работа №10 Лабораторная работа №11 1 2 3 4 5 6 7 8 9 10 11 12 13 14 15 16 17 18 19 20 21 22 23 24 25 26 27 28 29 30 31 32 33 34 35 36 37 38 39 40 41 42 43 44 45 46 47 48 49 50 51 52 53 54 55 56 57 58 59 60 61 62 63 64 65 66 67 68 69 70 71 72 73 74 75БЕСПЛАТНОЕ ГДЗ ЗА 1-11 КЛАСС
Чтобы у учеников не было стресса от больших нагрузок, страха получить плохую оценку, но при этом оставалось время на полноценный сон, дополнительные занятия, спорт, общение со сверстниками, стоит делать уроки вместе с ГДЗ. Готовые домашние задания – это возможность качественно подготовиться по разным предметам, не платя деньги репетиторам.
Если не хочется скачивать материалы, написанные «на коленке» студентами, а нужно работать с ГДЗ, над которыми трудились опытные преподаватели, умеющие понятно рассказывать теорию и грамотно оформлять практические задания, то надо заходить на Помогалку. Здесь можно без регистрации смотреть корректные решения номеров из учебников разных авторов по всем предметам и классам. Пусть школьная жизнь проходит без проблем!
Магнитный отклик нержавеющих сталей
Свяжитесь с нами
Переключить навигацию
Поиск
Меню
Учетная запись
Примечание. Эта статья взята из технической заметки Atlas Specialty Metal 11 «Магнитный отклик нержавеющей стали». нержавеющие стали. Реакция нержавеющей стали на магнит представляет собой интересное физическое свойство и может быть полезным тестом на сортировку, но она не так однозначна, как часто думают.
КАКОВЫ ОСНОВНЫЕ МАГНИТНЫЕ СВОЙСТВА МАТЕРИАЛОВ?
Ферромагнитные материалы
Материалы, которые сильно притягиваются к магниту (постоянному или электрическому) и сами могут образовывать постоянные магниты. Это обычное свойство, когда материал называют «магнитным».
Магнитная проницаемость
Легкость, с которой магнитный материал может намагничиваться, выражается магнитной проницаемостью. Значения, близкие к 1,0, показывают, что материал немагнитен.
Магнитно-твердые или мягкие магнитные характеристики
Магнитные материалы можно классифицировать как «твердые» или «мягкие». Магнитотвердые материалы сохраняют большое количество остаточного магнетизма после воздействия магнитного поля. Магнитомягкие материалы могут намагничиваться относительно небольшим магнитным полем, и когда его удаляют, они возвращаются к низкому остаточному магнетизму.
Немагнитные материалы
Материалы, не реагирующие на магнит.
Температура Кюри
Некоторые металлы имеют температуру, при которой они из ферромагнитных превращаются в немагнитные. Для обычных углеродистых сталей это происходит примерно при 768°C.
КАКИЕ МЕТАЛЛЫ ЯВЛЯЮТСЯ МАГНИТНЫМИ?
Все распространенные углеродистые стали (включая низкоуглеродистые стали), низколегированные стали и инструментальные стали являются ферромагнитными. Некоторые другие металлы, такие как никель и кобальт, также являются ферромагнитными. Все марки нержавеющей стали, за исключением аустенитных, также являются магнитными – все ферритные марки (например, 430, AtlasCR12, 444, F20S), все дуплексные марки (например, 2205, 2304, 2101, 2507), все мартенситные марки (например, 431, 416, 420, 440C) и все степени дисперсионного твердения (например, 630/17-4PH). Несмотря на то, что дуплексные сплавы представляют собой смеси аустенита и феррита, они все равно сильно притягиваются к магниту.
КАКИЕ МЕТАЛЛЫ ЯВЛЯЮТСЯ НЕМАГНИТНЫМИ?
Большинство цветных металлов, таких как алюминий и медь, и их сплавы немагнитны. Аустенитные нержавеющие стали, как обычная серия 300 (Cr-Ni), так и серия 200 с низким содержанием никеля (Cr-Mn-Ni), немагнитны. Обычно кованые аустенитные нержавеющие стали содержат очень небольшое количество феррита, но этого недостаточно, чтобы существенно повлиять на магнитные характеристики, за исключением очень важных применений.
СВАРНЫЕ ОТДЕЛКИ И ОТЛИВКИ
Отливки из аустенитных нержавеющих сталей имеют несколько иной состав по сравнению с коваными аналогами. Литая версия 316L, например, имеет марку CF-3M. Большинство «аустенитных» литейных сплавов намеренно изготавливаются так, чтобы в них было несколько процентов феррита — это помогает предотвратить горячее растрескивание во время литья. Сварной шов можно рассматривать как небольшую длинную отливку, и по той же причине, что подробно описана выше, аустенитные сварные швы содержат около 4–8% феррита.
Как в сварных швах, так и в отливках небольшое количество феррита приводит к слабому магнитному отклику, но его можно легко обнаружить с помощью хорошего ручного магнита. С помощью подходящего «ферритомера» этот магнитный отклик можно использовать для измерения количества феррита в сварном шве. Если требуется, чтобы сварной шов не содержал феррита, доступны специальные расходные материалы.
Можно также приобрести пластину «без феррита» или протестировать существующую на складе пластину 316 для подтверждения уровня феррита. Продукты, не содержащие феррита, специально производятся для нескольких конкретных коррозионных условий, обычно не из-за их магнитных свойств.
ВЛИЯНИЕ ХОЛОДНОЙ ДЕФОРМАЦИИ
Несмотря на то, что деформируемые аустенитные нержавеющие стали немагнитны в отожженном состоянии, они могут проявлять магнитную реакцию при холодной обработке. Холодная обработка может превратить часть аустенита в мартенсит.
Это сильно влияет на прочность на растяжение и даже больше на предел текучести; сильно холоднотянутая проволока марки 304 может достигать предела прочности при растяжении примерно до 2000 МПа. Такой хорошо обработанный 304 также будет очень сильно притягиваться к магниту.
Сплавы с более высоким содержанием аустенитообразующих элементов – никеля, марганца, углерода, меди и азота – образуют меньше мартенсита при холодной обработке, поэтому не становятся такими сильно магнитными. Это можно оценить как отношение элементов, образующих аустенит, к элементам, образующим феррит, или просто как отношение Ni/Cr. Изделия класса 316 обычно лишь слегка магнитятся, а классы 310 и 904L почти полностью немагнитны, независимо от того, насколько сильно они работали на холоде. С другой стороны, марка 301 содержит меньшее количество никеля и упрочняется еще быстрее, чем 304…. и становится сильно магнитным даже после небольшой холодной обработки.
Эти сравнения показаны на графике выше. Обратите внимание, что разные плавки сталей одной и той же марки могут демонстрировать разные магнитные отклики из-за незначительных различий в количествах каждого элемента.
ТЕРМООБРАБОТКА
Если кусок аустенитной нержавеющей стали реагирует на магнит при холодной обработке, его можно удалить обработкой на твердый раствор – стандартной обработкой нагреванием примерно до 1050°C (в зависимости от марки) с последующей закалкой водой или другим способом. быстрое охлаждение. Высокая температура позволяет «мартенситу деформации» преобразоваться в аустенит, и сталь снова становится немагнитной. Он также возвращается к низкой прочности.
ВАЖЕН ЛИ МАГНИТНЫЙ ОТКЛИК?
Магнитный отклик не влияет на другие свойства. Холоднотянутый 304 (и в меньшей степени 316) притягивается к магниту, но это не влияет на коррозионную стойкость. Некоторые из нержавеющих сталей с наиболее высокой коррозионной стойкостью обладают сильными магнитными свойствами… примерами являются дуплексные и супердуплексные марки, а также высоколегированные ферритные марки, такие как 29-4С.
Холоднотянутая сталь 304 также обладает высокой прочностью на растяжение, но это не связано с магнитным откликом – и магнитный отклик, и высокая прочность обусловлены холодной обработкой. Приложения, в которых может потребоваться отсутствие магнитного отклика, включают оборудование МРТ и морские суда для поиска мин. Для таких применений можно использовать специальные нержавеющие стали с низким магнитным откликом.
МАГНИТНО-МЯГКИЕ НЕРЖАВЕЮЩИЕ СТАЛИ
Магнитомягкие стали используются в электротехнике, связанной с изменением электромагнитной индукции. Соленоиды и реле являются типичными примерами, и там, где эти компоненты также должны иметь коррозионную стойкость, хорошим выбором может быть ферритная нержавеющая сталь. Для ответственных применений доступны специальные ферритовые прутки (по запросу завода) с гарантированными магнитными свойствами.
СОРТИРОВКА СТАЛИ
Магнитный отклик куска стали — это быстрый и качественный тест, который может быть полезен для сортировки сортов нержавеющей стали. Другие качественные испытания перечислены в Atlas TechNote 1.
Сортировка по магнитному отклику |
---|
Что можно сортировать Все другие стали притягиваются к магниту, включая все ферритные, дуплексные, мартенситные и дисперсионно-твердеющие нержавеющие стали. Единственными другими немагнитными сталями являются аустенитные стали с содержанием 13% марганца (например, «P8»).![]() |
Метод Отметьте реакцию, если она есть, когда постоянный магнит приближается к стали. |
Наконечники и ловушки Некоторые марки аустенитной нержавеющей стали, особенно 304, в некоторой степени притягиваются к магниту при холодной обработке, например, при гибке, формовании, волочении или прокатке. Снятие напряжения при вишнево-красном нагреве устранит эту реакцию из-за холодной обработки, но это снятие напряжения может повысить чувствительность стали и не должно выполняться на изделии, которое впоследствии будет использоваться в коррозионной среде. Однако допустим полный отжиг. Даже несмотря на то, что дуплексные марки содержат только половину магнитной ферритной фазы по сравнению с полностью ферритными марками, такими как 430, разница в «ощущении» ручного испытания вряд ли будет достаточной, чтобы можно было сортировать дуплексные стали от ферритной, мартенситной или дисперсионно-твердеющей. также обычно слабомагнитны из-за преднамеренного включения небольшого процента феррита в аустенитный осадок. Процент феррита можно измерить по величине магнитного отклика, и для этого доступны специальные приборы. |
Меры предосторожности Нет опасностей, связанных с этим испытанием |
ССЫЛКИ И ДОПОЛНИТЕЛЬНАЯ ИНФОРМАЦИЯ
- Atlas TechNote1 «Качественные сортировочные тесты»
- Публикация Института никеля 2978 «Механические и физические свойства аустенитных хромоникелевых нержавеющих сталей при температуре окружающей среды»
- Специальное руководство ASM «Нержавеющие стали»
- ASSDA Technical FAQ № 3 «Магнитные эффекты нержавеющих сталей»
Дополнительная информация также представлена на веб-сайте Atlas по адресу www.atlasmetals.com.au
Copyright © Atlas Specialty Metals 2008
Использование металлов и неметаллов
жизни, включая железо, алюминий, медь, золото, серебро и многие другие. Мы также знакомы с такими элементами, как кислород, углерод и сера. Все они получены из встречающихся в природе веществ, содержащих один или несколько элементов или соединений. Минералы так их называют. Руды — это полезные ископаемые, содержащие компоненты, которые можно добывать в коммерческих целях.
Металлы – это элементы, хорошо проводящие тепло и электричество. Металлы, расположенные ниже периодической таблицы, известны как металлы. На самом деле около 80 % элементов периодической таблицы — это металлы.
Металлы, как правило, податливы, а это означает, что из металлов можно выковывать очень тонкие листы, не ломая их. Металлы также проявляют в своем свойстве пластичность, а это значит, что из них можно вытягивать провода.
Металлы характеризуются особым свойством, известным как точка плавления. Температура плавления металлов сильно различается. Температура плавления ртути -39°С. Металлы являются хорошими отражателями света. Они имеют блестящий вид всякий раз, когда любая свежая поверхность металла подвергается воздействию света. Металлы блестят по своей природе. Самым тугоплавким металлом является вольфрам (W), температура плавления которого составляет 3422 °C.
Существуют различные металлы, обладающие большим количеством свойств, таких как:
Золото
- Ювелирное дело многих цивилизаций.
- Мягкий и легко формованный в большое количество предметов.
- Используется для изготовления ценных предметов, таких как валюта и украшения.
Магний
- По прочности сравним с 2/3 веса алюминия.
- Используется для изготовления сплавов и гибридных металлов с определенными свойствами.
- Используется в производственных процессах.
- Используется в колесных дисках, блоках двигателей и картерах трансмиссии.
- Используется в автомобильной промышленности.
Предпочитается алюминию из-за высокопрочного снижения веса.
Алюминий
- Благодаря высокому соотношению прочности к весу алюминий отвечает за полет.
- Используется для изготовления пресноводных лодок, так как не подвергается коррозии при контакте с водой.
- Используется для изготовления банок из-под газировки, так как не ржавеет и легко поддается деформации.
- Используется для выполнения крупных достижений.
- Используется для барбекю из свежевыловленной рыбы до идеальной влажности, так как ее можно легко превратить в очень тонкий лист.
- Самый цветной (не содержащий железа) металл на планете.
Ртуть
- Существует в виде жидкости при комнатной температуре.
- Используется для изготовления ртутных выключателей.
- Используется для производства энергосберегающих лампочек, предусмотренных федеральным законодательством.
- Он использовался в термометрах, пока информация о его токсичности не стала вирусной.
Бронза
- Используется для изготовления скульптур, предметов искусства и гитарных струн.
- Используется при изготовлении сплавов, таких как бронза в сочетании с алюминием, никелем, цинком и марганцем.
- Используется для изготовления массивных церковных колоколов, так как не трескается и не гнется. Кроме того, он звучит лучше, когда звонит.
- Имеет историческое значение, например, бронзовый век.
Медь
- Используется для изготовления сплавов, преимущественно в чистом виде.
- Используется для изготовления водопроводных труб и электроники.
- Используется для изготовления гигантских статуй.
- Используется для изготовления антикоррозийных статуй, так как образует патину или оксидированный слой зеленовато-голубого цвета. Например, он используется в Статуе Свободы.
Латунь
- Используется для изготовления подшипников, так как хорошо скользит по другим металлам.
- Используется для изготовления духовых инструментов, таких как туба, труба и тромбон.
- Легко штампуется и формуется. Чрезвычайно пластичный и прочный.
- Используется в антикварной мебели, например, в ручках и ручках.
Сталь
- Сталь представляет собой смесь железа и углерода.
- Существуют различные типы стали, а именно: углеродистая сталь, легированная сталь, нержавеющая сталь
Железо (кованое или литое)
- Используется для изготовления оснований и рам тяжелого оборудования, что снижает вибрацию и обеспечивает жесткость.
- Используется для изготовления дровяных печей, так как железо обладает высокой температурой плавления, чтобы выдерживать высокие температуры.
- Используется для изготовления посуды.
Цинк
- Благодаря низкой температуре плавления металлический цинк очень легко отливается. Металл легко расплавить на куски, а затем переработать.
- Используется для создания покрытий, обеспечивающих защиту других металлов. Например, цинк используется для изготовления оцинкованной стали, которая предотвращает ржавчину.
Титан
- Металл устойчив к коррозии.
- Используется для изготовления медицинских имплантатов, так как титан биосовместим.
- Это седьмой по распространенности металл на Земле, который очень трудно очистить. Кроме того, это очень дорого.
- Поскольку он имеет высокое соотношение прочности и веса, он чрезвычайно ценен для летающих предметов.
- Нитрид титана используется для изготовления металлорежущих инструментов, поскольку он невероятно твердый и имеет покрытие с низким коэффициентом трения.
Вольфрам
- Используется при производстве карбида вольфрама.
- Используется для изготовления режущих инструментов (для горнодобывающей промышленности и металлообработки), абразивов и тяжелого оборудования.
Например, металлический вольфрам может легко резать титан и жаропрочные сплавы.
- Также известный как тяжелый камень, он примерно в 1,7 раза плотнее свинца.
- Он имеет самую высокую температуру плавления и самую высокую прочность на растяжение по сравнению с любым из чистых металлов.
- Используется для изготовления сплавов.
- Используется для изготовления ракетных сопел, которые должны выдерживать экстремальные температуры.
Никель
- Используется для нанесения покрытий и легирования.
- Используется для изготовления 25% состава пятицентовой американской монеты.
- Используется при производстве нержавеющей стали (70 %), что повышает прочность металла и коррозионную стойкость.
- Используется для покрытия лабораторного и химического оборудования, т.е. гладкой и полированной поверхности.
Кобальт
- Используется для получения синего пигмента в красках и красителях.
- Используется для изготовления износостойких высокопрочных стальных сплавов.
Олово
- Очень мягкий и пластичный.
- Используется для изготовления сплавов, таких как бронза (1/8 олова и 7/8 меди).
- Используется для производства олова (85-99 %).
Свинец
- Очень мягкий и податливый.
- Плотный и тяжелый.
- Используется для изготовления пуль и красок.
- Может вызвать повреждение головного мозга и поведенческие проблемы.
Неметалл — это элемент, плохо проводящий тепло и электричество. Неметаллы обычно обладают свойствами, противоположными свойствам металлов. Неметаллы присутствуют во всех трех агрегатных состояниях. Большинство неметаллов представляют собой газы, такие как азот и кислород.
Неметаллы существуют во всех трех агрегатных состояниях. В основном это газы, такие как азот и кислород. Бром — жидкость. Некоторые из них представляют собой твердые вещества, такие как углерод и сера. В твердом состоянии неметаллы хрупкие, а это означает, что они разобьются, если их ударить молотком. Твердые вещества не блестят. Температура плавления обычно намного ниже, чем у металлов. Зеленые элементы в таблице ниже — это неметаллы.
Неметаллы имеют широкий спектр применения, например:
Сера
- Используется для изготовления пороха, фейерверков и спичек для облегчения воспламенения.
- Используется в производстве резины для шин и других материалов.
- Используется как инсектицид или фумигант.
- Используется для получения серной кислоты.
Бром
- Используется в фармацевтике для лечения боли, рака и болезни Альцгеймера.
- Используется в качестве дезинфицирующего средства для обработки воды в плавательных бассейнах и джакузи.
- Используется в производстве огнестойких материалов, необходимых для детской одежды.
- Используется в красителях и пестицидах.
Водород
- Поскольку водород является самым легким элементом, его можно использовать в качестве подъемного агента в воздушных шарах.
- Используется в качестве топлива, так как легко воспламеняется.
Гелий
- Используется в научных исследованиях.
- Используется в воздушных шарах и лазерах, поскольку гелий химически неактивен и негорюч.
- Газообразный неметалл.
- Обнаружение течи в сосудах и другой высоковакуумной аппаратуре с помощью гелия.
- Используется отделом метеорологии для прогнозирования погоды.
- Жидкий гелий можно использовать для охлаждения сверхпроводящих магнитов при исследованиях изображений (МРТ, магнитно-резонансная томография).
Благородные газы
- Используются в цветных дисплеях для рекламных целей, например, аргон, ксенон.
- Используется для получения лазерных лучей, таких как неон, аргон, криптон.
- Используется для наполнения ламп ночных клубов, используемых в театрах и ночных клубах, таких как криптон и неон.
Азот
- Используется в промышленности для производства аммиака, который используется в удобрениях на сельскохозяйственных полях.
- Используется для производства аммиака и производства азотной кислоты в качестве удобрения.
- Присутствует в нитратах и нитритах в воде и почве. Эти соединения являются составной частью круговорота азота.
- Составная часть ДНК и часть генетического кода.
- Жидкий азот используется в качестве хладагента для транспортировки пищевых продуктов и в целях заморозки.
- Жидкий азот используется для консервации органов и репродуктивных клеток.
- Составляет 78 % атмосферы Земли.
- Входит в состав всех живых тканей.
- Соли азотной кислоты используются при получении соединений, таких как нитрат калия, нитрат аммония и азотная кислота.
- Азотированные органические соединения, такие как нитроглицерин, используются в качестве взрывчатых веществ.
Фтор
- Используется в холодильной технике, кондиционерах и инсектицидах.
- Используется в зубной пасте для предотвращения кариеса.
- Используется для изготовления тефлона.
- Используется для улучшения качества ракетного топлива.
Фосфор
- Используется в крекерах.
- Существует три разновидности фосфора: белый, черный, красный и фиолетовый.
- Используется в производстве тонкой фарфоровой посуды и специального стекла.
- Используется в фейерверках, удобрениях и разрыхлителях.
- Используется при производстве стали.
Радон
- Используется в больницах для лечения опухолей.
- Используется для лечения болезней.
Уголь
- Используется для производства сахара, белков и глюкозы.
- Алмаз — это форма углерода, используемая для изготовления ювелирных изделий. Он также используется в промышленных целях.
- Алмаз — самый твердый элемент.
- Используется для производства углеводов, которые являются важным источником энергии.
- Аморфный углерод используется в производстве чернил и красок.
- Аморфный углерод используется для изготовления аккумуляторов.
- Графит используется в качестве грифеля в ваших карандашах.
- Используется для радиоуглеродного датирования, то есть используется для измерения возраста вещей.
- Графит используется в производстве стали.
- Алмазная форма углерода может использоваться для изготовления ювелирных изделий.
- Углерод-14 используется для определения возраста окаменелостей, костей и т. д. Он используется для оценки срока службы указанного органического вещества. Это используется для определения возраста и периода окаменелостей и окаменелостей динозавров!
Селен
- Используется для лечения дефицита селена.
- Необходим для правильной работы щитовидной железы и иммунной системы.
Йод
- Используется для приготовления антибактериальных полосканий, которые используются для профилактики инфекции горла.
- Используется как антисептик, предотвращающий рост микроорганизмов.
Примеры вопросов
Вопрос 1: Отличие металлов от неметаллов?
Answer:
Following are the differences between Metals and Non-metals are:
Metals
Non-Metals
Malleable Brittle Ковкий Непластичный Хорошие проводники тепла и электричества. Плохие проводники тепла и электричества (Исключение: графит). Блестящий, можно полировать. Неблестящий (матовый) и не поддается полировке (Исключение: йод). Твердые вещества при комнатной температуре (Исключение: Ртуть). Может быть твердым, жидким или газообразным при комнатной температуре. Прочный и прочный. Слабый
Вопрос 2: Перечислите элемент, проявляющий свойства как металлов, так и неметаллов.
Ответ:
Кремний представляет собой материал, обладающий свойствами как металлов, так и неметаллов. Это металлоид. Он похож на металл, твердый и блестящий. Кроме того, он обладает высокой температурой плавления. Однако он не проводит электричество, в отличие от металлов.
Вопрос 3: Объясните, почему сера является неметаллом?
Ответ:
Сера является неметаллом из-за следующих свойств:
- Плохой проводник тепла и электричества.
- Ни ковкий, ни пластичный.
- Диоксид серы представляет собой кислотный оксид.
- S + O 2 → SO 2
- SO 2 + H 2 O → H 2 SO 3
2 SO 3
2 SO 3
(SO 3
2 3
2 . : Уточните использование(i) каучука и
(ii) цинка, которые используются для выделения водорода из разбавленной соляной кислоты.
Ответ:
(i) Поскольку резина является изолятором и не пропускает через себя ток, поэтому электрические провода покрыты резиноподобным материалом.
(ii) Цинк более реакционноспособен, чем водород. Он может легко вытеснить элемент водорода из разбавленной соляной кислоты (HCl) и высвободить его.
Вопрос 5: Почему магний считается металлом?
Ответ:
Магний считается металлом по следующим причинам:
- Хороший проводник тепла и электричества.
- Пластичный и пластичный.
- 2MG + O 2 → 2MGO
- MGO + H 2 O → Mg (OH) 2
(гидроксид магния)44499686 (магний гидроксид).
Вопрос 6. Перечислите все различия химических свойств металлов и неметаллов?
Answer:
Following are the differences in the chemical properties of metals and non-metals:
Metals
Non-Metals
Form основные оксиды.
Образуют кислотные оксиды или нейтральные оксиды.
Вытеснение водорода из воды (или пара).
Не реагировать с водой.
Замещение водорода из разбавленных кислот.
Не реагируют с разбавленными кислотами
Образуют ионные хлориды с хлором.
Образуют ковалентные хлориды с хлором.
Не сочетать с водородом.
Соединение с водородом с образованием стабильных ковалентных гидридов.
Сплавы – определение, состав, свойства и применение
Вещество, полученное в результате смешивания двух или более металлов, называется сплавом. Комбинации металлов и других элементов также могут быть использованы для создания сплавов. Свойства сплавов часто отличаются от свойств составляющих их компонентов. По сравнению с чистыми металлами сплавы часто обладают большей прочностью и твердостью. Красное золото, полученное путем соединения меди и золота, является примером сплава. Белое золото, изготовленное путем соединения серебра и золота, является еще одним важным сплавом золота. Несколько свойств металлов, таких как ковкость, пластичность, прочность и т. д., можно улучшить, смешивая с ними другие металлы. Смесь различных металлов называется сплавом.
Что такое сплавы?
Сплав представляет собой смесь двух или более металлов или сплав представляет собой смесь металла и небольшого количества неметаллов.
Чистые металлы никогда не используются в промышленности для производственных целей. Комбинация металлов используется для улучшения свойств одного металла, и эта комбинация металлов известна как сплав. Он также может содержать металл и неметалл. Как правило, сплав металлов получают путем плавления различных металлов в соответствующих пропорциях и последующего охлаждения смеси до комнатной температуры. Сплав металла и неметалла можно приготовить, сначала расплавив металл, а затем растворив в нем неметалл с последующим охлаждением до комнатной температуры. По сравнению с металлами сплавы обладают большей прочностью и служат дольше.
Например-
- Металлический алюминий легкий, но не прочный, но сплав алюминия с медью, магнием и марганцем легкий и прочный.
- Металлический алюминий легкий, но не твердый, а сплав алюминия с магнием легкий и твердый.
- Железо является наиболее широко используемым металлом. Но в чистом виде его никогда не используют, потому что чистое железо очень мягкое и очень легко растягивается в горячем состоянии. Когда небольшое количество углерода смешивается с железом, получается сплав, называемый сталью. Также, когда железо смешивается с хромом и никелем, мы получаем сплав, называемый нержавеющей сталью, который является прочным, жестким и совсем не ржавеет.
Различные составы сплавов
Некоторые из распространенных сплавов: латунь, сталь, нержавеющая сталь, бронза, припой, амальгама и т. д. Составы различных сплавов приведены ниже:
- Бронза была первым обнаруженным сплавом. Он состоит из меди и олова. Он имеет содержание меди 90% и содержание олова 10%. Для улучшения общих характеристик могут быть добавлены очень небольшие количества цинка, никеля или марганца.
- Из меди и цинка получают латунь. Он содержит примерно 80 % меди и 20 % цинка. Другие компоненты могут быть добавлены в меньших количествах. Латунь используется для улучшения электрических характеристик меди.
- Сталь производится путем смешивания 90 % железа и 1 % углерода. Он более устойчив к коррозии и долговечен.
- Нержавеющая сталь производится путем смешивания железа с хромом и никелем. Он содержит примерно 18 % хрома и 5 % никеля.
- Alnico представляет собой металлический сплав, состоящий из железа, никеля, кобальта и алюминия.
- Сплавы олова и свинца используются для изготовления припоя. Он состоит из 50 % свинца и 50 % олова.
- Чугун получают путем смешивания железа с углеродом. Он содержит 96-98% железа и 2-4% углерода. Также могут быть обнаружены следы кремния.
- Стерлинговое серебро производится путем соединения 92,5 % серебра и 7,5 % других металлов, чаще всего меди. Если воздух содержит соединения серы, серебро разъедает и чернеет.
Медь или другие металлы можно смешать с серебром, чтобы получить этот сплав, уменьшающий потускнение.
- Никель, хром и железо используются для производства нихрома. Обладает высокими сопротивлением, температурой плавления, пластичностью и другими свойствами. Он имеет высокое сопротивление потоку электронов и трудно окисляется.
- Амальгама представляет собой сплав ртути, включающий один или несколько дополнительных металлов. Раствор металлического натрия в жидкой металлической ртути известен как амальгама натрия.
- Золото чистотой 24 карата считается самым чистым. Чистое золото очень мягкое, из-за чего не подходит для изготовления украшений. Чтобы сделать золото более твердым, его смешивают с небольшим количеством серебра или меди. В Индии золотые украшения изготавливаются из 22-каратного золота, что означает, что 22 части чистого золота сплавляются с 2 частями серебра или меди.
Свойства сплавов
Каждый сплав обладает определенными полезными свойствами.
Свойства сплава отличаются от свойств отдельных металлов, из которых он изготовлен. Некоторые свойства сплавов приведены ниже.
- Сплавы тверже металлов, входящих в их состав.
- Сплавы более устойчивы к коррозии, чем чистые металлы.
- Сплавы более долговечны, чем металлы, из которых они сделаны.
- Электропроводность сплавов ниже, чем у чистых металлов.
- Сплавы имеют более низкую температуру плавления, чем металлы, из которых они сделаны.
- Сплавы обладают большей пластичностью, чем входящие в их состав металлы.
Использование сплавов
Сплавы используются в нашей повседневной жизни по-разному. Некоторые из наиболее распространенных применений сплавов приведены ниже.
- Латунь используется для изготовления кухонной утвари, винтов, замков, дверных ручек, электроприборов, застежек-молний, музыкальных инструментов, декоративных и подарочных изделий
- Бронза используется для изготовления статуй, монет, медалей, кухонной утвари и музыкальных инструментов, в том числе другие вещи.
- Альнико представляет собой ферромагнитное вещество и используется в постоянных магнитах.
- Припой используется для ремонта или соединения двух металлических деталей, т. е. для неразъемного соединения электрических компонентов.
- Хирургические инструменты, музыкальные инструменты, столовые приборы и украшения изготовлены из стерлингового серебра.
- Нержавеющая сталь используется для строительства железных дорог, мостов, дорог, аэропортов и т. д. Она также используется для изготовления посуды и других изделий.
- Сплавы алюминия легкие, поэтому их используют для изготовления корпусов самолетов и их деталей.
- Благодаря своей жаропрочности и сверхпластичности титановые сплавы широко используются в аэрокосмической промышленности.
- Амальгама представляет собой сплав ртути, используемый в медицинских процедурах. Стоматологи также используют его для исправления полостей в зубах.
- Некоторые сплавы золота, такие как розовое золото, используются для изготовления ювелирных изделий.
Железная колонна в Дели
Железная колонна возле Кутб-Минар в Дели состоит из кованого железа, представляющего собой низкоуглеродистую сталь. Его высота 8 метров, а вес 6000 кг. Индийские мастера по железу построили эту колонну в 400 г. до н.э. Хотя кованое железо медленно ржавеет со временем, мастера по металлу разработали процесс, который предотвратил ржавчину колонны из кованого железа даже через тысячи лет.
Образование тонкой пленки магнитного оксида железа на поверхности предотвращает коррозию. Этот тонкий слой образовался на поверхности столба в результате финишной обработки столба путем окрашивания его смесью различных солей с последующим нагревом и быстрым охлаждением. Эта колонна стоит в хорошем состоянии более 2000 лет после того, как была сделана. Этот столб совсем не заржавел. Это говорит о том, что древние индийцы хорошо разбирались в металлах и сплавах.
Примеры вопросов
Вопрос 1: Что означает 22 карата золота?
Ответ:
22 карата золота означает, что 22 части чистого золота сплавлены с 2 частями серебра или меди.
Вопрос 2: Как изготавливается сплав?
Ответ:
Сплав металлов получают путем смешивания различных металлов в расплавленном состоянии в необходимых пропорциях и последующего охлаждения их смеси до комнатной температуры.
Вопрос 3: Как сплавы используются в аэрокосмической промышленности?
Ответ:
Алюминий — легкий металл, его сплавы используются в аэрокосмической промышленности. Эти сплавы используются для изготовления корпусов самолетов и изготовления высокопрочных деталей реактивных двигателей. Эти части имеют дело с крайностями температуры, давления и вибрации. Они обеспечивают высокую прочность и способность функционировать при очень высоких температурах.
Вопрос 4: Какой сплав используют стоматологи?
Ответ:
Амальгама представляет собой сплав металлической ртути.