Как изготавливаются плиты ДСП — информационная статья от компании Новатор
Древесно-стружечная плита – это материал, в состав которого входит несколько видов древесины. Этот вид плит изготавливают из отходов дерева: стружек либо опилок, которые связываются при помощи специальных компонентов, а затем соединяются горячим прессом. Производители используют разные породы древесины, которые входят в состав ДСП, и от этого зависит не только качество, но и цена на материал. Изготавливать этот стройматериал стали в середине 20-го века для производства мебели.
На сегодняшний день, мебельное производство ДСП является одним из самых популярных в деревообрабатывающей промышленности. Его применяют как в строительстве, так и для производства элементов домашнего интерьера. Является экономным стройматериалом, который не требует сложной обработки.
Все производители изготавливают плиты ДСП с использованием одной технологии, однако в состав входят разные виды древесины.
Стадии изготовления
Весь процесс изготовления древесно-стружечного сырья можно условно разделить на несколько стадий:
- Сбор необходимых компонентов. На этом этапе подбирают и смешивают разные виды древесины, от которых будет зависеть качество и цена полученного ДСП. Для изготовления ДСП плиты производство используются щепки, опилки или древесная стружка.
- Дробление древесины. На этом этапе сырье нужно раздробить до необходимого размера и придать всем компонентом однородную массу. Делается это для того, чтобы готовая плита имела необходимую прочность.
- Сушка древесины. После дробления, из древесины нужно удалить избыточную влагу. Это необходимо сделать для того, чтобы в последующем материал можно было склеить. Удаляется влага в основном методом высушивания.
- Объединение элементов. Когда древесина измельчена, высушена и полностью подготовлена, ее основательно смешивают с клеящей основой. После этой процедуры появляется однородная масса, из которой производят древесно-стружечные плиты.
- Придание формы. Перемешанная с древесиной клеящая основа помещается на специальную подвижную ленту, которая имеет определенные размеры. Далее эту массу спрессовывают до необходимых габаритов. Весь процесс прессовки материала проводится под высокими температурами.
- Распил. Готовый материал распиливают до необходимых габаритов и делают дополнительную процедуру высушивания.
- Процесс обработки.
Эта стадия является завершающей. На ней происходит процесс обработки готового материала на линии производства ДСП: на поверхность материала наносится один тонкий слой бесцветного компонента (ламинирование), а вторым слоем наносят шпон. Для таких плит используют специализированную пленку, которая накладывается поверх материала. Для дополнительной обработки могут применить бумагу либо пластик. Стоимость изготовление плит ДСП не большая, но их цена многократно выше, чем у отшлифованных древесно-стружечных плит.
Завод ДСП с ламинацией (15000 м3 в год)
1. Участок I подготовки сырья
2. Участок II сушки сырья
3. Участок III клееподготовки и осмоления
4. Участок IV формирования и подпрессовки плит
5. Участок V горячего прессования плит
6. Участок VI форматирования готовой продукции
Схема производства ДСП 10 000 — 15 000 м3/год
Древесно-стружечная плита (ДСП, ДСтП) — листовой композиционный материал, изготовленный путем горячего прессования древесных частиц, преимущественно стружки, смешанных со связующим неминерального происхождения с введением при необходимости специальных добавок на одно- и многоэтажных прессах. Типы смол могут использоваться разные, основное их назначение — выступить в роли связующего вещества. Плотность таких плит составляет 660-750 кг/м3 в зависимости от толщины. Класс эмиссии Е1 делает их крайне безвредными и позволяет использовать данную продукцию внутри помещений в непосредственной близости от людей.
Внешне сорт ДСП можно опознать по качеству обработки поверхности плиты. Более качественный первый сорт — это шлифованная ДСП, поверхность второго сорта не столь безупречна и имеет некоторые дефекты. Кроме того, существует еще ряд различий в сортах древесностружечной плиты: поверхность мелкоструктурная или обычная, по виду марки П-А, П-Б (зависит от механических показателей), по водостойкости (обычная или повышенная), по содержанию формальдегидной смолы (Е1, Е2). Плиты ДСП, в основном, зависят от плотности, формы и размера древесных частиц, а также от количества и качества связующего материала. Различают плиты одно-, трех- и пятислойные. Не рекомендуется применять в помещениях с повышенной влажностью, в таких помещениях следует применять только гидрофобизованные или защищенные покрытиями плиты.
Ламинированное ДСП, это обыкновенное шлифованное ДСП, покрытое посредством физико-химического процесса бумажно-смоляными пленками. Процесс изготовления ЛДСП осуществляется под действием температуры (140-210 С) и давления (25-28 МПа). В результате этого процесса декоративно-защитный слой на плите ламинированного ДСП образуется за счет растекания смолы по поверхности плиты с последующим затвердеванием и образованием прочного покрытия. ЛДСП обеспечивает привлекательный внешний вид, хорошие потребительские качества и физико-механические свойства, не требует дальнейшей отделки и широко применяется для производства мебели.
Одним из основных достоинств ДСП является прочность, которая у ДСП ни чуть не хуже прочности натуральной древесины. Ещё одним достоинством шлифованного ДСП является легкость обработки, несмотря на большую плотность.
Сферы применения ДСП:
— обшивка стен и крыш;
— изготовление стеновых панелей;
— изготовление полов, оснований под ковровые и линолеумные покрытия, перегородок;
— изготовление съемной опалубки;
— изготовление мебели, стеллажей, полок, упаковки;
— строительство ограждений и разборных конструкций;
— использование для декорирования и отделки, благодаря оригинальной текстуре поверхности.
Шлифованная ДСП Ламинированная ДСП (ЛДСП)
Плотность: по плотности ДСП делится на плиту малой плотности (менее 550 кг/м³), средней (550—750 кг/м³) и высокой (более 750 кг/м³).
Номинальные размеры плит:
Параметр | Значение, мм | Предельное отклонение, мм |
Толщина | От 8 до 38 | ±0,3* (для шлифованных плит) −0,3/ +1,7 (для нешлифованных плит) |
Длина | 1830, 2040, 2440, 2500, 2600, 2700, 2750, 2840, 3220 3500, 3600, 3660, 3690, 3750, 4100, 5200, 5500, 5680 | ± 5,0 |
Ширина | 1220, 1250, 1500, 1750, 1800, 1830, 2135, 2440, 2500 | ± 5,0 |
Технологический поток производства ДСП
рис.1
Ведущим производителем и потребителем ДСП является Западная Европа, за которой следуют Северная Америка и Восточная Европа. В России объемы потребления на ДСП составляют около 4,0 млн. м3/год, а текущий объем производства — 3,6 млн. м3/год, импорт — 0,4 млн. м3/год. Крупным потребителем ДСП является Китай, но лишь небольшая часть китайского спроса (7-8%) удовлетворяется за счет международной торговли. ДСП – относительно дешевая продукция и потому практически не является объектом международной и трансконтинентальной торговли. Так, российские производители экспортируют лишь около 5% своей продукции в страны СНГ (см. рис. 2).
рис.2
В Западной Европе ожидается незначительный рост спроса на ДСП; в период до 2015 г. темпы прироста составят 1,1%/год. В России годовые темпы прироста спроса прогнозируются на уровне 5,2%, что означает около 270 000 м3/год в объемном выражении. Значительный рост спроса (3,7%/год) ожидается также в др. странах Восточной Европы. По расчетам, прирост потребления ДСП в Японии не превысит 0,9%/год. В Северной Америке в период 2004-2015 гг. ожидается сокращение спроса на уровне -1,2% /год. Наиболее динамичный рост будет происходить в Китае; здесь темпы прироста составят 8,3%/год, т.е. около 870 000 м3/год.
Баланс спроса и предложения на ДСП в России
Размеры плит должны соответствовать указанным в табл. 1. ГОСТ 10632-89
Параметр | Значение, мм | Предельное отклонение, мм |
Толщина | От 8 до 38 | ±0,3 |
Длина | 1830, 2040, 2440, 2500, 2600, 2700, 2750, 2840, 3220 3500, 3600, 3660, 3690, 3750, 4100, 5200, 5500, 5680 | ± 5,0 |
Ширина | 1220, 1250, 1500, 1750, 1800, 1830, 2135, 2440, 2500 | ± 5,0 |
Примечания:
1. Толщина нешлифованных плит устанавливается как сумма номинального значения толщины шлифованной плиты и припуска на шлифование, который не должен быть более 1,5 мм.
2. Допускается выпускать плит размерами меньше основных на 200 мм с градацией 25 мм, в количестве не более 5% от партии.
3. По согласованию с потребителем допускается выпускать плиты форматов, не установленных в табл. 1.
4. Отклонение от прямолинейности кромок не должно быть более 2 мм.
5. Отклонение от перпендикулярности кромок плит не должно быть более 2 мм на 1000 мм длины кромки.
6. Перпендикулярность кромок может определяться разностью длин диагоналей пластин, которая не должна быть более 0,2% длины плиты.
7. Плиты должны изготовляться с применением синтетических смол, разрешенных Минздравом.

9. В условиях эксплуатации количество химических веществ, выделяемых плитками, не должно превышать в окружающей среде предельно допустимых концентраций, утвержденных Минздравом для атмосферного воздуха.
Физико-механические показатели плит плотностью от 550 кг/м2 до 820 кг/м2 должны соответствовать нормам, указанным в табл. 2. ГОСТ 10632-89
Наименование показателя | Норма для плит марок | |
П-А | П-Б | |
Влажность, % Тн* Тв* Разбухание по толщине: за 24 ч (размер образцов 100Х100 мм), %, (Тв) за 2 ч (размер образцов 25Х25 мм), % (Тв)** Предел прочности при изгибе, МПа, для толщин,мм (Тн): от 8 до 12 » 13 » 19 » 20 » 30 Предел прочности при растяжении перпендикулярно пласти плиты, МПа, для толщин, мм (Тн): от 8 до 12 » 13 » 19 » 20 » 30 Удельное сопротивление выдергиванию шурупов, Н/мм (Тн)***: из пласти » кромки Покоробленность, мм (Тв) Шероховатость поверхности пласти Rm, мкм (Тв), для образцов а) с сухой поверхностью: от для шлифованных плит с обычной поверхностью от для шлифованных плит с мелкоструктурной поверхностью от для нешлифованных плит б) после 2 ч вымачивания***: для шлифованных плит с обычной поверхностью для шлифованных плит с мелкоструктурной поверхностью для нешлифованных плит | 5 22 18 0. 0.30 0.25 60 50 150 | 5 33 16 0.30 55 63 180 |
** Для плит повышенной водостойкости.
*** Определяется по согласованию изготовителя с потребителем.
Качество поверхности плит должно соответствовать нормам, указанным в табл. 3. ГОСТ 10632-89
Дефекты по ГОСТ 27935 | Норма для плит | |||
шлифованных, сортов: | не шлифованных, сортов: | |||
I | II | I | II | |
Углубления (выступы) или царапины на пласти | Не допускаются | Допускаются на 1 м поверхности плиты не более двух углублений диаметром до 20 мм и глубиной до 0,3 мм или двух царапин длиной до 200 мм | Допускаются на площади не более 5% поверхности плиты, глубиной (высотой), мм, не более: 0,5 | 0,8 | |
Парафиновые и масляные пятна, а также пятна от связующего | То же | Допускаются на 1 м поверхности плиты пятна площадью не более 1 см в количестве 2 шт.![]() | Допускаются на площади не более 2% поверхности плиты | |
Пылесмоляные пятна | » | Допускаются на площади не более 2% поверхности плиты | Допускаются | |
Сколы кромок | Не допускаются (единичные глубиной по пласти 3 мм и менее протяженностью покромке15 мм и менее не учитываются) | Допускаются в пределах отклонений по длине (ширине) плиты | ||
Выкрашивание углов | Не допускается (длиной по кромке 3 мм и менее не учитываются) | Допускается в пределах отклонений по длине (ширине) плиты | ||
Дефекты шлифования(недошлифовка, прошлифовка, линейные следы от шлифования, волнистость поверхности) | Не допускаются | Допускаются площадью не более 10% площади каждой пласти | Не определяют | |
Отдельные включения частиц коры на пласти плиты размером, мм, не более | 3 | 10 | 3 | 10 |
Отдельные включения крупной стружки: для плит с мелкоструктурной поверхностью | Допускаются в количестве 5 шт. | |||
для плит с обычной поверхностью | Не определяют |
Допускается для плит с обычной поверхностью не более 5 шт. отдельных включений частиц коры на 1 м пласти плиты размером, мм: для I сорта более 3 до 10; для II сорта — более 10 до 15.
В зависимости от содержания формальдегида плиты изготовляют двух классов эмиссии, указанных в табл. 4. ГОСТ 10632-89
Класс эмиссии формальдегида | Содержание формальдегида, мг на 100 г абсолютно сухой плиты |
Е1 | До 10 включ. |
Е2 | Св. 10 до 30 включ. |
Е3 | Св. 30 до 60 включ. |
Допускается изготовлять плиты класса эмиссия формальдегида Е3 до 01.01.1991г.
ЛИНИЯ ПО ПРОИЗВОДСТВУ ПЛИТ ДСП ПРОИЗВОДИТЕЛЬНОСТЬЮ 10000 — 15000 М3/ГОД
№ |
Артикул |
Наименование |
Технические характеристики |
Кол-во |
Мощность (кВт) |
||
1 |
Секция подготовки сырья |
||||||
101 |
Zh2110/12 |
Конвейер ленточный |
Ширина=1 м; Длина=12 м |
1 |
4,0 |
||
102 |
Bh3110 |
Барабанная дробилка |
Диаметр барабана Ø=1000 мм |
1 |
200 |
||
103 |
BZ1110/26 |
Конвейер ленточный |
Ширина=1 м; Длина=26 м |
1 |
5,5 |
||
104 |
BP1110/7 |
Конвейер ленточный передвижной |
Ширина=1 м; Длина=7 м |
1 |
3,0 |
||
105 |
B2750 |
Бункер сырья (щепы) |
Объем=50 м3 |
3 |
3×15,0 |
||
106 |
BZ1160/6 |
Ленточный конвейер |
Ширина=0,6 м; Длина=6 м |
3 |
3×2,2 |
||
107 |
P-468 |
2-х барабанная дробилка для получения стружки |
Диаметр барабана Ø=800 мм |
3 |
3×200,0 |
||
108 |
MS5-54 |
Пневмотранспортер |
Циклон с роторным клапаном для регулировки скорости потока |
1 |
37,0 |
||
109 |
M32/22 |
Скребковый конвейер |
Ширина=0,8 м; Длина=22 м |
1 |
11,0 |
||
110 |
BL2650 |
Бункер для полученной стружки |
Объем=50 м3 |
3 |
3×15,0 |
||
2 |
Секция сушки и сортировки | ||||||
201 |
BW1160/16 |
Конвейер ленточный |
Ширина=0,6 м; Длина=16 м |
3 |
3×3,0 |
||
202 |
B233 |
Роторная сушка |
Диаметр корпуса внешний Ø=2,9 м |
3 |
2×70,9 |
||
203 |
BW1160/6 |
Конвейер ленточный |
Ширина=0,6 м; Длина=6 м |
3 |
3×2,2 |
||
204 |
BM1110/9 |
Конвейер ленточный |
Ширина=1 м; длина=9 м, с магнитным сепаратором |
1 |
4,0 |
||
205 |
B1437 |
3-х уровневое вибросито |
6×30 мм, 3×15 мм |
1 |
4,0 |
||
206 |
MS5-54 No. |
Пневмотранспортер |
Циклон с роторным клапаном для регулировки скорости потока |
1 |
37,0 |
||
207 |
MS5-54 No.8 |
Пневмотранспортер |
Циклон с роторным клапаном для регулировки скорости потока |
1 |
45,0 |
||
208 |
BR1160/6 |
Конвейер ленточный |
Ширина=0,6 м; Длина=6 м |
1 |
2,2 |
||
209 |
B5612 |
Дробилка для получения сырья тонкой фракции |
Диаметр барабана Ø=1200 мм |
1 |
200,0 |
||
210 |
MS5-54 No. |
Пневмотранспортер |
Циклон с роторным клапаном для регулировки скорости потока |
1 |
17,2 |
||
211 |
BC2750 |
Бункер для внутреннего слоя |
Объем=30 м3 |
1 |
8,5 |
||
212 |
BC2450 |
Бункер для внешних слоев |
Объем=15 м3 |
1 |
8,5 |
||
213 |
XC-12 | Система пылеудаления | — | 1 | — | ||
3 |
Секция клееподготовки и осмоления |
||||||
301 |
GS-1 |
Емкость для хранения клея |
Объем=20 м3 |
1 |
— | ||
302 |
GS-2 |
Насосная установка для клея |
Расход=250 л/мин |
1 |
2,2 |
||
303 |
GS-3 |
Помпа для подачи клея для внешних слоев |
Расход=0~60 л/мин |
1 |
1,5 |
||
304 |
GS-4 |
Помпа для подачи клея для внутреннего слоя |
Расход=0~60 л/мин |
1 |
1,5 |
||
305 |
GH-1 |
Клеевой миксер |
Объем=1,5 м3 |
1 |
2,2 |
||
306 |
GY-2 |
Бункер с клеем для внешних слоев плиты |
Объем=1,5 м3 |
1 |
1,5 |
||
307 |
GP-5 |
Бункер с клеем для внутреннего слоя плиты |
Объем=1,5 м3 |
1 |
1,5 |
||
308 |
BX1160/3 |
Конвейер ленточный |
Ширина=0,6 м; Длина=16 м |
2 |
2×3,3 |
||
309 |
BZ1250 |
Бункер осмоления стружки |
Ø=510 мм |
2 |
2х30,0 |
||
310 |
BR1160/22 |
Конвейер ленточный |
Ширина=0,6 м, Длина=22 м; с магнитным сепаратором |
2 |
2×4,0 |
||
311 |
BL12342/4 |
Виброконвейер |
Ширина=0,42 м; Длина=4 м |
2 |
2×4,0 |
||
4 |
Секция формирования и предварительного прессования |
||||||
401 |
B4313 |
Воздушнопоточный формовщик |
Рабочая ширина=1,83 м |
1 |
85,0 |
||
402 |
B8314/2 |
Роликовый предпресс |
Диаметр ролика Ø=0,96 м; Длина=2 м |
1 |
33,0 |
||
403 |
BJ1113 |
Форматно-раскроечный станок |
Пильный диск Ø=0,4 м; Рабочая ширина=1,3 м |
1 |
1,5+2,2 |
||
404 |
BB1250 |
Кромкообрезной станок |
Пильный диск Ø=0,3 м |
2 |
2х1,1 |
||
405 |
BY1232/3 |
Рециркуляционный шнековый конвейер |
Ширина=0,3 м; Длина=3 м |
1 |
3,0 |
||
406 |
BY1160/19 |
Рециркуляционный шнековый конвейер |
Ширина=0,6 м; Длина=19 м |
1 |
4,0 |
||
407 |
BY1015 |
Синхронный конвейер 1 |
Ширина=2 м |
1 |
2,2 |
||
408 |
BY1315 |
Конвейер ускоритель 1 |
Рабочая ширина=2 м; Длина=4 м |
1 |
2,2 |
||
409 |
BZY1315 |
Конвейер ускоритель 2 |
Рабочая ширина=2 м; Длина=4 м |
1 |
2,2 |
||
410 |
Bh2399 |
Система взвешивания |
— |
1 |
0,2 |
||
411 |
BY1315 |
Конвейер ускоритель 1 |
Рабочая ширина=2м; Длина=4м |
1 |
2,2 |
||
412 |
BY1315 |
Конвейер ускоритель 2 |
Рабочая ширина=2м; Длина=4м |
1 |
2,2 |
||
413 |
BZ1115/4 |
Бункер предварительной загрузки |
Рабочая ширина=2м; Длина=4,5м |
1 |
2,2+1,1 |
||
5 |
Секция горячего прессования |
||||||
501 |
B124×8/22 |
Загрузочный станок |
13 пролетов; |
1 |
3,0 |
||
502 |
B124×8/22 |
Горячий пресс |
13 пролетов; Расстояние между плитами =120 мм; Время прессования 15 сек. ![]() |
1 |
223,0 |
||
503 |
B114X8/15 |
Разгрузочный станок |
13 пролетов |
1 |
28,6 |
||
504 |
B114/V |
Система удаления горячего пара и паров клея из зоны прессования |
— |
2 |
2х4,0 |
||
505 |
DX-2 | Корпус системы удаления пара | — |
1 |
— | ||
506 |
BY354 |
Конвейер |
Ширина=0,4м; Длина=3,6м |
1 |
0,75 |
||
6 | Секция охлаждения и форматирования плит | ||||||
601 |
BJ422 |
Подающий конвейер |
— |
1 |
1,1 |
||
602 |
B4230 |
Система охлаждения плит |
— |
1 |
2,2 |
||
603 |
BC423 |
Конвейер на выходе |
— |
1 |
1,1 |
||
604 |
BY3715 |
Подающий конвейер |
— |
1 |
1,1 |
||
605 |
B1112 |
Пильный станок продольного форматирования |
Рабочая ширина=1,83 м |
1 |
2х4+1,5 |
||
606 |
BY1122 |
Ленточный конвейер |
— |
1 |
1,1 |
||
607 |
BY3215 |
Конвейер реверсивный |
— |
1 |
1,1+3,0 |
||
608 |
B2124 |
Пильный станок поперечного форматирования |
Рабочая ширина=2,44 м или 2,75 м |
1 |
2х4+1,1 |
||
609 |
BY3920 |
Разгрузочный роликовый конвейер |
— |
1 |
0,75 |
||
610 |
BJ114X8/2 |
Гидравлический стол |
Грузоподъемность ≤2 тонн; с роликами |
1 |
3,0 |
||
611 |
B-14 |
Укладчик |
— |
1 |
1,5 |
||
612 |
BY114 |
Подъемник с роликами |
— |
1 |
2,2 |
||
613 | ZX-3 | Система пылеудаления | — | 1 | 7,5 | ||
7 | Секция калибрования и шлифования | ||||||
701 |
BY114 |
Подъемник с роликами |
— |
2 |
2×1,5 |
||
702 |
BJ116X8/2 |
Гидравлический стол |
Грузоподъемность≤2 тонн |
2 |
2X1,5 |
||
703 |
BY |
Подающий роликовый конвейер |
— |
1 |
1,5 |
||
704 |
BG2719 |
4-х агрегатный калибровальный станок |
Калибрование плиты в размер |
1 |
110х2+90х2+11 |
||
705 |
BY |
Конвейер |
— |
1 |
1,5 |
||
706 |
BG2719A |
4-х агрегатный калибровально-шлифовальный станок |
Шлифование плиты |
1 |
75×2+55×2+15 |
||
707 |
BY-12 |
Ленточный конвейер |
— |
1 |
1,5 |
||
708 |
BY-14 |
Ленточный конвейер |
— |
1 |
1,5 |
||
709 |
CV-2 |
Разгрузочный укладчик плит |
— |
1 |
3 |
||
710 | BG-21 | Система удаления | — | 1 | 11 | ||
711 | SC-7 | Панель контроля управления | — | 1 | — |
линий ламинирования ДСП лист формата 8/4 (1220*2440 мм) без упаковки товара |
формат 9/6 (1875*2750 мм) |
линий ламинирования лист формата 4/8 (1220*2440 мм) без упаковки товара |
формата 6/9 (1875*2750 мм) |
ИСКЛЮЧЕНИЯ ИЗ КОМПЛЕКТНОСТИ ПОСТАВКИ И ЛОКАЛЬНО ПРИОБРЕТАЕМЫЕ МАТЕРИАЛЫ ДЛЯ МИНИ ЗАВОДА ДСП
Здания/фундаменты/доставка/транспорт
- Полное производственное здание с отоплением, освещением и т.
п.
- Все фундаменты, кладки, проведение коммуникаций в фундаментах и другие связанные с установкой строительные работы, крепежные элементы и приспособления, кабельные короба, крышки и проходы и т.п.
- Доставка, разгрузка и требующееся хранение оборудования, а также перевозка машин к месту установки.
- Кран, автокран/ специальные краны, грузоподъемники, подъемное снаряжение, инструменты для выгрузки, перемещение по заводу и сборки линии.
- Санитарно-гигиенические нормы для персонала.
- Защитные панели для пакетов исходных и готовых изделий.
- Сырьевой материал, необходимый для тестовых испытаний в достаточном количестве.
- Крановые системы, автопогрузчики, инструменты для работы на линии.
- Лабораторное оборудование.
- Все переходы и платформы, монтажные леса, включая поручни безопасности, лестницы, защитные ограждения, необходимые для предотвращения несчастных случаев на работе.
- Масляное наполнение гидропривода пресса.
Сжатый воздух/удаляемый воздух/вода
- Воздушный компрессор со всеми линиями подачи к индивидуальным секциям линии сухого, сжатого воздуха.
- Выводящий агрегат, включая трубы подачи и возврата от индивидуальных секций прессовой линии.
- Вытяжной короб над прессом и другими компонентами линии.
Электрика/передача данных
- Распределительная панель и главная энергоподача к отдельным коммутаторным шкафам всей линии, а также электроуправление всеми компонентами линии локальной поставки.
- Заземление всей линии.
- Кабельные связи/кабельные шкафы и их установка/подготовка для подсоединения кабелей между главными шкафами выключателей и панелей управления линией и т.п.
- Программный модуль.
- Модем для онлайн-контроля программного потока в ЧПУ.
- Одна линия связи.
Устройства безопасности
- Все специальные системы безопасности, такие как запорные цепи т.п., требуемые местными властями.
- Все меры, требуемые местными властями, правилами по экологической безопасности, а также все требования по шуму, загрязнениям земли, воды, воздуха.
- Оборудование по пожарной безопасности.
- Возможно необходимые шумоизоляционные кабины для разделительных пил, обрезных агрегатов и т.п.
Распил ЛДСП | Раскрой ЛДСП | Распил ДСП — Мебеталь
Производственная компания Мебеталь предлагает весь комплекс работ по распилу ДСП
- Прямолинейный распил
- Криволинейный распил
- Изготовление деталей с внутренним и наружным радиусом
- Изготовление скошенных деталей
- Изготовление сложных кривых
- Наклонный пил
Распил ЛДСП производится на автоматизированных форматно-раскроечных станках с ЧПУ. Благодаря современному оборудованию распил любого уровня сложности выполняется без сколов и трещин. Мебеталь по заказу клиентов производит изготовление мебельных деталей из ЛДСП, МДФ и ХДФ, входящих в складскую и заказную программу плитных материалов. Кроме того, Мебеталь принимает в распил материал заказчика.
Раскрой ЛДСП и столешниц производится на автоматизированных форматно-раскроечных центрах HOLZMA (группа HOMAG, Австрия) с ЧПУ, что обеспечивает высокую точность размеров мебельных деталей с минимальным отклонением 0,1 мм. Наличие в производственном парке Мебеталь двух центров позволяет производить распил больших объемов.
Изготовление деталей сложных и криволинейных форм производится на обрабатывающем станке MASTERWOOD путем фрезерования. Данное оборудование обеспечивает высокую точность при изготовлении криволинейных деталей.
1. Размеры прямолинейных деталей без обработки кромкой
- Минимальный размер детали для распила – 100×50мм.
- Максимальный размер детали – формат плиты, уменьшенный на 15 мм. по всему периметру листа после проведения технологических резов торцевания. В случае необходимости изготовления детали большего размера, с клиента берется письменное согласие (указывается в бланке заказа) на возможность образования сколов в связи с уменьшением размеров технологических резов.
Формат плиты, мм. |
Максимальный размер детали, мм. |
2800 х 2070 |
2770 х 2040 |
2440 х 1220 |
2410 х 1190 |
2. Детали с подрезкой торца под угол
- При торцевых скосах на деталях из ЛДСП отклонение от прямого угла происходит не более чем на 45 о.
- Минимальный размер детали – 100мм (ширина заготовки при этом должна быть увеличена на 100мм).
- В связи с возможностью выполнения торцевых скосов с углами 11,5;15;22,5;30;45° на обрабатывающем центре с ЧПУ, погрешность выполнения данной операции составляет ±0,5°. Погрешность выполнения углов, отличных от указанных ранее, составляет ±1°.
В случае оформления заказа с данной обработкой деталей с клиента берется письменное согласие (указывается в бланке заказа) на возможность образования сколов вдоль острого угла.
3. Фрезерование. Криволинейная обработка.
Сегодня фрезерование мебельных деталей стала востребованной операцией, без которой не обходится производство мебели. Наиболее оптимальный метод криволинейной резки плитного материала — фрезерование на станках с ЧПУ. В Мебеталь проведение подобных работ производится на обрабатывающем центре MASTERWOOD.
Ограничения по размерам криволинейных деталей
Минимальный размер криволинейной детали, мм. |
Максимальный размер криволинейной детали, мм. (на ОЦ с ЧПУ) |
200*150 |
3300*1360 |
Возможность изготовления детали меньшего или большего размера, относительно вышеуказанных min и max размеров, требует согласования через менеджера компании Мебеталь.
Ограничения по внутреннему и внешнему радиусу.
Радиус (R) |
При условии нанесения кромочного материала. Толщина кромки, мм. |
|||
0,4/0,5 |
1,0 |
1,3 |
2,0 |
|
Внутренний |
min 20 мм. |
min 40 мм. |
min 40 мм. |
min 80 мм. |
Внешний |
min 40 мм. |
min 50 мм. |
min 50 мм. |
min 50 мм. |
Без нанесения кромочного материала min внутренний R, мм. |
Плита 16-18 мм.: min внутренний R = 8-9 мм. |
Плита 25-50 мм. ![]() |
Ассортимент плитного материала
В складскую программу входят свыше 300 декоров ЛДСП и столешниц ведущих мировых производителей: Kronospan (Кроношпан), Slotex, Невский ламинат, Alternative UV-лак, Egger (Эггер), TSS SMart. Мы работаем напрямую с производителями плитных материалов и фурнитуры, поэтому предлагаем своим клиентам низкие цены на материалы.
В ассортименте плитных материалов Мебеталь присутствуют типоразмеры листов:
- ЛДСП Кроношпан и Egger формата 2800×2070 мм в толщине 8/10, 16 и 25 мм.
- ЛМДФ Кроношпан и Egger формата 2800×2070 мм в толщине 16, 19, 22, 25 мм.
- Шлифованный МДФ Кроношпан, Kastamonu формата 2800×2070 мм в толщине 6, 8, 10, 12 16, 18, 19, 22, 25 мм.
В распил принимается давальческое сырье от клиентов с наценкой на производственные услуги 30%Спектр оказываемых услуг компании Мебеталь охватывает все этапы изготовления мебельных деталей на заказ и корпусной мебели.
![]()
Давальческое сырье – это материалы, доставленные клиентом и купленные у другого поставщика для передачи под производственные заказы в «Мебеталь». В давальческое сырье не принимается: фанера и другой материал, который отличается по составу и свойствам от ДСП, ЛДСП, МДФ, ХДФ.
- Прием давальческого плитного материала производится кратно полноформатному листу. Материал, имеющийся в складской или заказной программе «Мебеталь» не принимается в качестве давальческого сырья.
- В случае поставки давальческого материала (плиты и кромки) необходимо заранее согласовать с менеджером Вашего заказа дату поставки. Давальческое сырье принимается не позднее 2-х рабочих дней до запуска заказа в производство.
- При сдаче давальческого материала на склад компании «Мебеталь» требуется присутствие Заказчика или представителя со стороны Заказчика для совместного визуального контроля качества поставляемого материала:
— отсутствие повреждения листа: царапин, сколов, нарушение целостности листа, проверка на предмет прямолинейности и т.д.
— проверка количества, маркировки плиты и ее соответствия заявленной в сопроводительных документах информации.
Заказчик (представитель со стороны Заказчика) обязан иметь при себе установленную форму АКТА ПРИЕМА ДАВАЛЬЧЕСКОГО СЫРЬЯ в 3-х экземплярах с подписью и печатью Заказчика. АКТ ПРИЕМА ДАВАЛЬЧЕСКОГО СЫРЬЯ выдается менеджером по работе с клиентами при оформлении заказа с участием давальческого сырья. Представитель со стороны Заказчика обязан предоставить доверенность от Заказчика с указанием в ней паспортных данных представителя, его полномочий. Форму доверенности и пример ее заполнения можно получить у менеджера по работе с клиентами.
В случае, если Заказчик является ООО или ИП (др. форма юридического образования), осуществляющим деятельность без печати, то следует предоставить единоразово заявление об этом. - При приемке плитного материала кратно паллете, также в присутствии представителя Заказчика производится визуальный осмотр паллеты, контроль соответствия маркировки плиты и заявленной информации в сопроводительных документах, количества паллет.
- При получении кромочного материала производится визуальный осмотр целостности упаковки, маркировки, если количество кратно целой бухте. Если кромочный материал поставляется кратно одному метру проверка количества метров, соответствие маркировки кромки и заявленной информации в АКТЕ ПРИЕМА ДАВАЛЬЧЕСКОГО СЫРЬЯ проводится в случае наличия подобного образца у лица, проводящего приемку. В случае отсутствия образца проверка проводится только в отношении количества метров кромки. При принятии давальческого сырья – кромки — лицо, проводящее приемку, маркирует бухту кромки номером производственного заказа.
- В результате приемки подписывается АКТ ПРИЕМА ДАВАЛЬЧЕСКОГО СЫРЬЯ, с указанием возможных недочетов или их отсутствия. АКТ ПРИЕМА ДАВАЛЬЧЕСКОГО СЫРЬЯ составляется в трех экземплярах на каждый вид материала: один экземпляр – клиенту, второй – сотруднику склада, третий – для производства.
- Остатки давальческого сырья подлежат возврату клиенту.
Хранение остатков компанией «Мебеталь» не осуществляется.
- В случае использования давальческого сырья, например, одного листа в нескольких заказах – интервал между сдачей заказов не должен превышать 2-х рабочих дней.
- Прием давальческого материала – стекла с различной обработкой, кожи на плитной основе (для изготовления дверей-купе) возможен при:
— Если в складской программе компании «Мебеталь» отсутствует данная позиция.
— Стекло на плитной основе принимается нарезанным в размер, согласно расчетным размерам технологического отдела. - Не принимаются для различной доработки (присадка, упил, кромление и т.д.):
— готовые детали (независимо от изготовителя, типа материала и т.д.)
— фасады (независимо от изготовителя и характера фасада)
Как заказать распил лдсп?
Компания Мебеталь в первую очередь ориентирована на мебельные компании, тем не менее частные клиенты так же могут оформить производственный заказ на изготовление мебельных деталей.
Оформить заказ на распил можно несколькими способами в офисе компании или дистанционно. Заказы по телефону не принимаются.
- Выберите необходимый декор плитного материала и кромки в шоу-руме компании.
- Обратитесь к менеджеру за получением консультации по порядку оформления и прохождения заказа, а так же порядку заполнения Бланка заказа.
- Заполните Бланк заказа мебельных деталей. При наличии в заказе деталей с присадкой, фрезеровкой, скосами и т.д. необходимо предоставить чертежи на эти детали.
- Далее, бланк путем автоматической выгрузки попадает к менеджеру, который производит точный расчет с учетом полученных чертежей и выставляет Вам счет на оплату. Оплатить счет Вы можете путем наличного и безналичного расчета.
- Вы можете заказать доставку заранее, для этого необходимо сообщить менеджеру точный адрес доставки.
- Перед заполнением Бланка заказа мебельных деталей необходимо ознакомится с подробной инструкцией.
- Заполните Бланк заказа мебельных деталей, который находится в разделе «Бланки» и нажмите «Отправить». Все отправленные Бланки хранятся в «Журнале заказов».
- ВАЖНО! После отправки Бланка заказа необходимо написать письмо по адресу: [email protected] c указанием номера заказа и прикрепить чертежи на детали. Чертежи необходимы только на детали с различной обработкой: присадка, фрезеровка, скосы и т.д.
- Менеджер произведет точный расчет в соответствиями с чертежами и отправит Вам счет на оплату. Срок обработки заказа от 1 до 3 рабочих дней, в зависимости от заказа и его особенностей.
- В случае внесения изменений в первоначально отправленном бланке, по причинам различного характера (замена декора, работ и т.д.) менеджер вместе с счетом на оплату вышлет Вам заказ-спецификацию на мебельные детали, которую необходимо проверить и подтвердить ответным письмом, написав фразу «Все верно. Подтверждаю». Счета на оплату высылаются ТОЛЬКО на подтвержденные заказы-спецификации.
- Если Вы хотите включить в счет доставку, напишите точный адрес доставки в комментариях к заказу.
- В графе «Заказчик» необходимо указать полное наименование юридического лица или Ф.И.О. заказчика.
- В графе «Телефон» необходимо указать контактный телефон заказчика с правильным кодом города/мобильного оператора.
- В графе «ЛДСП» Вы выбираете из перечня интересующий декор плитного материала и его толщину.
- В полях «Толстая кромка 1-2 мм(V2)» и «Тонкая кромка 0,4-0,6 мм(V0,4)» кромочный материал подбирается автоматически, в цвет выбранного ранее плитного материала. В случае если Вам необходим иной цвет кромочного материала, имеется возможность осуществить выбор производителя и цвета вручную из выпадающего списка в желтом поле, с внесенным словом «автоподбор».
- Переходим к заполнению параметров необходимых мебельных деталей.
ВАЖНО:
• во всех полях кроме поля «Обработка детали (Эскиз)» вносятся только цифровые показатели;
• все размеры мебельных деталей указывайте без учета кромочного материала;
• в случае заказа присадки изделия, одинаковые по размерам детали, не требующие различной присадки, заполняются в отдельные строки и с разными порядковыми номерами, в том числе левые и правые детали. - В случае если в заказе на изготовление мебельных деталей предполагаются типовые пазы, то в поле «пазы 4 мм» необходимо выбрать из перечня размер отступа от края детали.
- В первой колонке «Обработка детали (Эскиз)» необходимо выбрать из перечня «П» или «ФП».
«П» — присадка (без фрезеровки). Присаживаются отверстия диаметром 5, 8, 10, 15, 20, 35 мм;
«ФП» — фрезеровка-присадка (вырез, выпил, радиусы, сложные скосы, не типовые пазы). Фрезеруются отверстия диаметром более 35 мм. - В колонках «Длина детали» и «Ширина детали» необходимо указать размеры по длине и ширине детали в мм.
- В колонке «Количество деталей» необходимо указать количество деталей в штуках.
- В колонке «Скосы» указывается количество скосов, которые необходимо выполнить на каждой из деталей указанной в стоке. В случае если скосы не нужны, указывать ничего не надо.
- Кромление деталей.
Раздел «Количество сторон детали, обработанных кромкой и/или имеющих паз 4 мм» поделен на 2 колонки «по длине» и «по ширине», которые, в свою очередь, делятся на 2 толщины кромочного материала:
— «V2»;
— «V0,4».
Таким образом, на простых деталях (без сложных радиальных контуров), чьи стороны необходимо закромить, в соответствующих колонках «V2» и/или «V0,4» необходимо указать цифру 1 или 2, в зависимости от количества сторон подлежащих кромлению. В случае если кромить не нужно, указывать ничего не надо. - В случае если деталь имеет сложный радиальный контур, требующий кромления необходимо указать цифру 1 или 2, в зависимости от количества сторон подлежащих кромлению по длине и ширине в столбцах «В том числе кол-во сторон детали со сложным контуром, требующих кромления».
- Столбцы «Паз» по длине и ширине.
Существует 2 типовых проходных паза (от начала до конца детали) шириной 4 мм, глубиной 8 мм:
— Первый – 12 мм от края детали, включая кромочный материал
— Второй – 16 мм от края детали, включая кромку.
Такие пазы необходимо отмечать цифрами 1,2,3,4… по количеству пазов в колонке «Паз» по той стороне (длина и/или ширина), где он проходит. - Если паз не попадает под параметры типового, то Вам необходимо в колонке «Обработка детали (Эскиз)» выбрать из перечня «ФП» для соответствующего порядкового номера детали.
- Смотрим расчет стоимости заказа. Под таблицей параметров мебельных деталей располагается полная спецификация вашего заказа и общая стоимость заказа, которая считается автоматически.
- Вносим комментарии. В поле «Ваши комментарии» Вы можете внести все свои пожелания и пояснения, в целях ускорения обработки заказа и во избежание недопонимания.
Сроки изготовления
Срок выполнения заказа от 7 до 10 рабочих дней, при условии:
- Плитный и кромочный материал входит в складскую программу компании и на момент заказа находится в наличии.
- При плановой загрузке производства. В моменты сверхплановой загрузки производства сроки уточняйте у менеджера.
Срочный распил — в течение 2-х рабочих дней, с наценкой на производственные услуги 30%
Сроки изготовления мебельных деталей для частных лиц оговариваются отдельно при оформлении заказа.
Способы оплаты
- в кассе офиса продаж наличными или банковской картой.
- перевод с расчетного счета на расчетный счет. В назначении платежа необходимо указать «Оплата по счету №___ от дд.мм.гг за ___ (указать услугу, прописанную в счете)»
Важно: Оплату заказов на карты сотрудников мы не принимаем!
Способы доставки
Компания Мебеталь предоставляет услугу доставки готовых заказов по Москве и Московской области.
- Самовывоз
- Служба доставки Мебеталь. Подробнее о ценах и географии доставки в разделе Доставка.
Технология изготовления ДСП
Изготовление ДСП
Начнем с того, что это один из самых экологичных процессов, связанных с обработкой древесины. Само изготовление древесно-стружечной плиты или ДСП это сложный и длительный процесс, который начинается с распилки дерева на ровные круглые бревна, далее расщепление древесины в специальных машинах.
Всю технологию, можно разделить на несколько этапов, которые идут следующим образом:
- Измельчение чистой древесины либо отходов, в процессе этого процесса появляется продукт-щепа.
- В процессе переработки, всю щепу перемалывают до однородного состояния и перерабатывают роторные станки в результате чего появляется следующий продукт-стружка
Согласно технологическим регламентам по производству ДСП обязательным является соблюдение толщины стружки которая составляет 0,5 мм, ширина 8 мм, длина от 5 до 40 мм. Регламент является обязательным и имеет некие погрешности в несколько миллиметров, что позволяет незначительные колебания и отклонения от нормы.
Также есть требования, которые есть к форме и структуре стружки. Форма должна быть плоской и ровной по толщине с гладкой поверхностью. Для измерения толщины стружки используются специальные устройства. Ее отвозят в специализированные бункеры, где хранится все время предшествующие сушке.
В в такой бункер, ее завозят при помощи специализированного пневматического транспорта, далее ее передают на сушку. Высушивание стружки происходит только до 5% влажности, а вот внутренние слои не более 25%. Из-за этого стружку сушат в разных сушильных установках, чтобы добиться именно стандартного готового продукта.
Если смотреть на отличия внутренней сушки от внешней, то оно очень простое. Внешний слой нагревают и остужают быстро, а вот внутренний слой медленнее и дольше держат сушилке, что все процессы шли постепенно. Говоря про пневматические агрегаты сортирующие стружку для разных слоев, то пневматика из различает их по влажности.
Следующий процесс это смешивание готовой стружки со связующими веществами, а именно со смолами, как натурального происхождения, так и синтетического, которые находятся в жидком состоянии. Этот процесс преобразует стружки в однородную массу.
После получения единой массы, стружку отправляют в формовочные, где она подвергается горячей прессовке. После этого паллеты из стружки становятся твердыми и готовыми к шлифовке и покрытию закрепителями и смолами.
Купить ДСП для изготовления мебели
Последний этап этого длительного процесса, заключается в продаже готового ДСП для потребителя. Купить панели ДСП, любых видов можно напрямую с нашего склада.Из чего делают ДСП
Как известно, древесностружечные плиты (ДСП) широко используются для производства различных конструкций. Этот материал недорогой, достаточно прочный, практичный.
Однако, когда речь заходит об использовании в жилом доме, у многих возникает вопрос: какие материалы используются для изготовления таких плит? И это понятно: экологичность и безопасность — важный пункт.
Сейчас мы ответим на этот вопрос.
Итак…
Из чего производят ДСП
На самом деле технология изготовления довольно проста. И материалов используется немного. А именно:
- стружки, опилки;
- связующее вещество;
- специальные добавки.
Теперь давайте рассмотрим подробнее, из чего делают ДСП.
Опилки, стружки
Опилки — это основной материал, используемый для изготовления ДСП. Зачастую это отходы деревообрабатывающих, лесопильных предприятий.
Также могут быть использованы стружки и щепки, которые перед изготовлением ДСП загружают в специальные дробилки, где они размалываются на мелкие кусочки. По сути, получаются те же опилки.
Размеры частиц могут быть разные. Но в основном их толщина не превышает 1 мм. Из них самые крупные идут на образование внутреннего слоя плиты. А мелкие частицы образуют ее верхний слой (за счет этого получается сравнительно гладкая поверхность).
Обычно такое сырье для производства ДСП получают из малоценных пород древесины (хвойных и лиственных).
Связующее вещество
По сути, это клей, за счет которого частицы связываются (склеиваются) между собой, образуя твердое тело. В качестве такого клея выступает синтетическая смола. Нередко клей получают путем смешивания смолы, парафина, химических отвердителей и воды.
Кстати, наверняка вы слышали о том, что ДСП выделяет такое вредное вещество, как формальдегид. Это действительно так. И… вы уже догадались, откуда это берется? Да, всё верно — формальдегид выделяют именно связующие смолы. Это вещества неминерального происхождения.
Можно сказать, что выделение формальдегида и является основным недостатком ДСП. Ведь все знают, что это вещество оказывает негативное влияние на здоровье людей.
Другое дело — какое количество формальдегида содержится в ДСП тех или иных производителей. Это уже другой вопрос.
Специальные добавки
Используются не всегда. Их назначение — добавить плитам особые свойства. Как правило, объем таких добавок составляет примерно 6…10% от массы древесных частиц.
Могут быть использованы добавки, придающие ДСП огнестойкость, влагостойкость, дополнительную прочность (антипирены, гидрофобизаторы, антисептики).
Материалы для облицовки ДСП
Плиты, предназначенные для изготовления мебели и других изделий, могут облицовываться шпоном. Наверняка такие древесностружечные плиты вы встречали много раз. Выглядит весьма привлекательно, доступны самые различные цвета, оттенки, фактуры.
Пластик, используемый для облицовки ДСП, придает плитам неплохую влагостойкость. Да и внешний вид получается весьма привлекательным. Нередко такие плиты используются для изготовления кухонной мебели.
Кроме того, в качестве облицовочных материалов могут использоваться бумага, полимерные пленки всевозможных цветов и оттенков. Кстати, для укрепления бумаги применяются смолы, лаки и другие вещества.
После облицовки ДСП приобретает эстетичный внешний вид и может быть использовано для изготовления самых различных изделий.
Теперь знаете, из чего делают ДСП? Надеемся, что вы внимательно прочитали статью и всё поняли. И, конечно же, вам решать — насколько этот материал целесообразно использовать для тех или иных целей.
Обустраивайтесь с умом!
Vyborstm.ru
Производство ДСП – изготовление плит, шпонированное
Все о шпоне и мдф -> Производство древесно-стружечных плит
ДСП – широко распространенный бюджетный конструкционный материал. Для изготовления древесно-стружечной плиты используются отходы деревообрабатывающего производства (стружки, опилки и пр. мелких частиц), которые пропитываются связующим веществом. Производство ДСП ведется путем сухого прессования в условиях высокой температуры и давления, в качестве связующего материала используются смолы. Готовое изделие в дальнейшем выделяет в окружающее пространство небольшое количество формальдегида, который считается токсичным веществом. В производстве различают две категории ДСП Е1 и ДСП Е2. ДСП категории Е1 считается более экологичным материалом, излучающим незначительное количество вредного формальдегида. ДСП Е2 по гигиеническим и санитарным нормам непригоден для производства мебели для детей. Его также не рекомендуют использовать в больших количествах в качестве отделочного материала в спальнях и в помещениях, в которых организован процесс приготовления пищи. При изготовлении ДСП существует возможность придавать готовому изделию определенные (требуемые) физико-химические свойства – введение парафиновой составляющей обеспечивает влагостойкость (для отделки или изготовления мебели для ванн, кухонь и т.п.), введение антипиренов обеспечивает огнестойкость.
Специфика материала
ДСП отличается высокой прочностью, прочностью на изгиб и растяжение. Плиты способны на протяжении длительного времени эксплуатации удерживать на достаточном уровне такие показатели как низкий процент разбухания, коробления и деформации. Материал ДСП легко поддается механической обработке (распиловка, сверление, шлифовка и т.п.), способен надежно удерживать скрепляющую и декоративную фурнитуру, однако тонкая декоративная обработка (фигурные резные детали) для него не подходит. Кроме вышеперечисленных достоинств популярного и востребованного материала, плиты ДСП выгодно отличается низкой стоимостью.
Особенности цвета и поверхности
Для придания высоких эстетических характеристик, ДСП подвергают дополнительной обработке – облицовка бумагой, полимерной пленкой, пластиком и шпоном (шпонированное ДСП).
Ламинированное ДСП получают путем специальной технологии. Бумажная основа пропитывается меламиновыми смолами, после чего при помощи пресса надежно присоединяется к поверхности ДСП. Кроме самых разнообразных имитаций фактур (натуральное дерево, камень, кожа и пр.), оттенков и цветов, ламинированные ДСП отличаются высокой устойчивостью к механическим и термическим повреждениям. Ламинированное ДСП выгодно отличается от кашированного ДСП (менее низкие показатели по устойчивости), у которого со временем защитное покрытие отслаивается.
Шпонированное ДСП производится путем нанесения натурального шпона ценных пород с последующим прессованием. После прессования поверхность поддается двойной шлифовке (грубой и тонкой) и обработке кромки. Благодаря отделке натуральным шпоном, полученный материал приобретает благородный изысканный внешний вид. Шпонированное ДСП используется в отделке помещений (стеновые панели, потолки, полы, перегородки) для производства самой различной мебели, для изготовления межкомнатных дверей, в качестве отделки металлических и бронированных дверей.
АО «Казанский Гипронииавиапром» им. Б.И.Тихомирова»
АО «Казанский Гипронииавиапром» им. Б.И.Тихомирова» > Деятельность > Проектирование > Промышленность > Деревообрабатывающая и целлюлозно-бумажная промышленность > Завод по производству МДФ, ДСП, ОСБ плит в ОЭЗ «Алабуга»Завод по производству МДФ, ДСП, ОСБ плит в ОЭЗ «Алабуга»
Завод по производству МДФ, ДСП , ОСБ плит расположен на территории Особой экономической зоны промышленно-производственного типа «Алабуга» (ОЭЗ ППТ «Алабуга»).
На заводе предусмотрено производство плит МДФ, ДСП, ОСБ производственной мощностью 475 000 м3/год (МДФ), в том числе с финишной обработкой (шлифовка, ламинирование, производство ламинированного паркета). Исходным сырьем для производства является нестроевой лес в т.ч. образующийся при санитарной вырубке, отходы предприятий деревообработки.
Большим плюсом данного проекта является отсутствие технологических твердых отходов производства, так как древесные отходы в виде коры, древесной пыли и брака плит используется как топливо в технологических энергетических установках завода.
На территории завода запроектированы с учетом функционального зонирования следующие здания и сооружения:
-производственная зона: производственный корпус с внекорпусными производственными участками и погрузочными рампами, с которых осуществляется погрузка готовых изделий на железнодорожный состав и автомобильный транспорт, а так же бытовой корпус со столовой, соединенный надземным переходом с производственным корпусом.
-складская зона: склады леса с разгрузочными железнодорожными платформами, склад метанола со сливной эстакадой.
-зона технического сервиса: корпус технического обслуживания, стоянки технологического транспорта и грузовых автомобилей;
-зона вспомогательных объектов: инженерная инфраструктура, энергетические объекты, контрольно-пропускной пункт с автовесовой; административный корпус со столовой, служебной стоянкой транспорта.
Производственная годовая программа составляет:
– МДФ плита (шлифованная и ламинированная) 475 тыс.м3 в год
– ДСП плита (шлифованная и ламинированная) 725 тыс.м3 в год
– ОСБ плита 575 тыс.м3 в год
Производитель коробчатых перегородок из ДСП и гофрированного картона, коробчатых перегородок и прокладок
С момента открытия в 1987 году компания Multicell стала крупнейшим независимым производителем коробчатых перегородок в Северной Америке. Как Независимый производитель коробчатых перегородок , мы не связаны никакими корпоративными контрактами или обязательствами по закупке сырья у дочерней компании. Multicell имеет возможность окружить себя сырьевыми партнерами, предлагая лучший сервис и качество по конкурентоспособным ценам, чтобы помочь удовлетворить потребности наших клиентов.
Наша дочерняя компания Box Partition Technologies анализирует потребности клиентов и рынка, чтобы настроить и создать наиболее эффективное производственное оборудование для современного рынка упаковки. Это оборудование позволяет нам стабильно обеспечивать лучшие сроки выполнения заказов по конкурентоспособным ценам.
Кроме того, группа инженеров Multicell Innovative гордится тем, что разрабатывает наиболее экономичную внутреннюю упаковку для обеспечения надлежащей защиты продуктов клиентов.Дизайн упаковки и отбор проб выполняются своевременно, чтобы удовлетворить потребности наших клиентов в срочном порядке.
Multicell гордится своим Agility . Мы применяем наш гибкий подход к дизайну, расценкам и образцам и, в конечном итоге, к производству продуктов премиум-класса на самом передовом и эффективном оборудовании в мире. Строгая рабочая этика Multicell и стремление удовлетворить потребности клиентов — вот почему мы стали ведущим поставщиком на рынке.
Непрерывное стремление и внедрение инноваций в дизайн оборудования и продукции, привлечение Гибкость к нашему персоналу и процессам, а также опора на нашу Независимость от крупных поставщиков позволяет Multicell уверенно и последовательно удовлетворять потребности наших клиентов. потребности.
Tubula Процесс производства ДСП и правила классификации – Фанера
Процесс производства ДСП Tubula и правила классификации
Проверки сортировки и контроля качества проводятся на каждом этапе производственного процесса. Случайные образцы проверяются на соответствие установленным стандартам в нашей хорошо оборудованной заводской лаборатории.
- СЫРЬЕ
Волокнистые материалы представляют собой бревна, ветки и древесные отходы RubberWood.Каучуковое дерево представляет собой однородный материал средней плотности светлого цвета, пригодный для производства высококачественных древесно-стружечных плит. - ИЗМЕЛЬЧЕНИЕ И ОТШЛУПЛЕНИЕ
Материалы из каучукового дерева измельчаются перед измельчением до мелких хлопьев желаемой толщины и длины. Это способствует оптимальной прочности и гладкости поверхности плит. - СУШКА И ПРОСЕИВАНИЕ
Влажные хлопья сушат в сушилке с горячим газом до требуемого уровня влажности.Затем высушенные хлопья просеивают, чтобы отделить мелкие и сердцевинные частицы, и хранят в поверхностном бункере и силосе сердцевины. - СМЕШИВАНИЕ КЛЕЯ И СМЕШИВАНИЕ
Поверхностные и сердцевинные частицы отдельно смешиваются с клеем, восковой эмульсией и другими добавками, точно дозируемыми для достижения качества высокого стандарта. - ФОРМОВАНИЕ МАТОВ
Смоляные частицы распределяются с помощью воздушного и механического формования, включенного в компьютеризированную программируемую систему управления, что обеспечивает постоянную плотность мата и равномерное распределение веса. - ГОРЯЧЕЕ ПРЕССОВАНИЕ
Горячее прессование, работающее автоматически на основе программируемого логического управления, сжимает мат под высоким давлением и контролируемой температурой, формируя плиты точной толщины. - ОХЛАЖДЕНИЕ
Готовые плиты, выходящие из горячего пресса, автоматически взвешиваются, чтобы убедиться, что получена определенная плотность, а затем помещаются в охладитель Star Cooler для схватывания клея. - ШЛИФОВАНИЕ
Необработанные плиты хранятся для окончательного отверждения для стабилизации свойств плит.Позже эти плиты будут откалиброваны до точной толщины, отшлифованы до идеальной поверхности и откалиброваны. - РАЗМЕР
Основные панели проверяются на соответствие склеивания и допуски по толщине, прежде чем обрезать боковые стороны и обрезать до точного размера. Панели штабелируются для промежуточного хранения. - ЛАМИНИРОВАНИЕ
Сортированные гладкие плиты могут быть ламинированы декоративной бумагой, пропитанной меламином, методом прессования короткого цикла или натуральным шпоном.Платы пересортированы и упакованы для окончательной отправки
Производители трубчатых древесностружечных плит, производимых по современным передовым технологиям, выделяются своей ценой и моделями. Мебельный сектор является наиболее часто используемой областью, хотя есть разные области применения. Все изделия, используемые в гостиной, гостиной, спальне, прихожей, кухне и ванной комнате, могут быть изготовлены из трубчатой мебели из ДСП. Причем, с большим разнообразием рисунков и расцветок. Для тех, кто любит простоту, доступны различные цвета и дизайны для тех, кто любит простую, стильную и яркую жизнь.Мебель из ДСП можно приобрести во всех мебельных магазинах, а также в интернет-магазинах. В последние годы область применения пустотелых древесностружечных плит получает все большее распространение. В зависимости от постоянного развития технологий мебель из трубчатого ДСП каждый день предлагается в разных ценовых диапазонах.
如无特殊说明,文章均为本站原创,转载请注明出处。Если нет специальных указаний, статьи являются оригинальными, если вы хотите использовать или воспроизвести, пожалуйста, укажите первоисточник www.plywoodinspection.com, если вы обнаружите, что наши статьи нарушают ваши авторские права и интересы, своевременно напишите нам по адресу info@plywoodinspection.
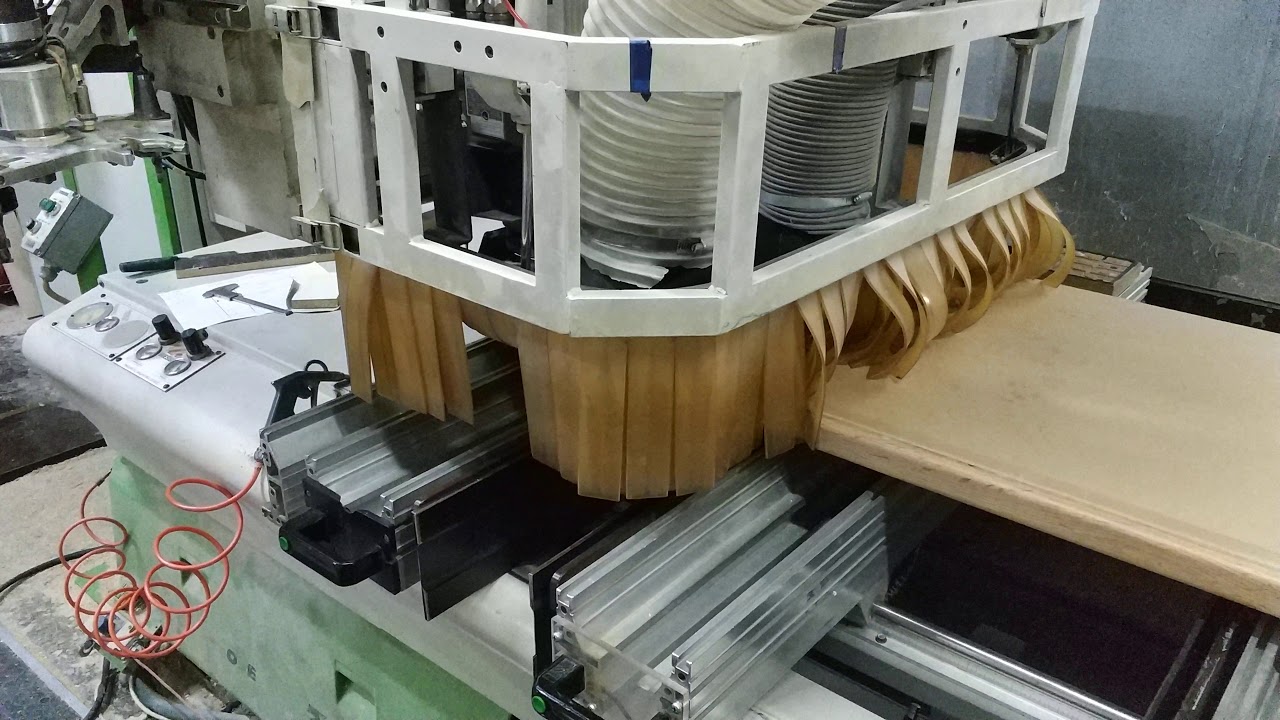
Производство ДСП | Склеивание — WOOD TEC PEDIA
Применение
Перед склеиванием щепы клеевой раствор смешивают с добавками или дозируют в смесительном узле. Ленточные весы на входе материала обеспечивают точное дозирование количества имеющегося материала. Клей распыляется на стружку или стружка смачивается в смесителе для клея объемом 2-6 м через встроенные форсунки.Содержание клея в верхнем слое составляет ок. 4-10% и в среднем слое ок. 8-15%.
Уровень заполнения смесителя поддерживается постоянным за счет электронного управления заслонкой на выходе из смесителя.
Клей
В производстве ДСП большое значение имеет выбор клея. Это зависит от технических, экономических, экологических и прикладных аспектов.
Синтетический клей
- Мочевиноформальдегидные (UF) смолы: это наиболее распространенные клеи, поскольку они наиболее рентабельны.Однако последующие выбросы формальдегида особенно высоки.
Для повышения влагостойкости применяют комбинации с меламиноформальдегидными (МФ) смолами или фенолоформальдегидными (ФФ) смолами.
- Меламиноформальдегидные (МФ) смолы: Меламин имеет характерное связывание формальдегида и повышает влагостойкость панелей.
- Фенолформальдегидные смолы (PF) имеют цвет от красновато-коричневого до темно-коричневого. Они используются для производства влагостойких панелей.
- PMDI (4,4-дифенилметандиизоцианат): смолы PMDI используются в производстве OSB и древесностружечных плит и считаются не содержащими формальдегида. Поэтому этот тип клея в основном используется для производства панелей по нормам CARB I, CARB II (США) и категории F**** (Япония). В качестве альтернативы они используются для склеивания возобновляемого сырья, такого как багасса или бамбук, или для производства влагостойких панелей. PMDI представляет собой безводный органический раствор, не содержащий растворителей, в котором изоцианаты реагируют с целлюлозой и лигнином древесины.
- Резорциновые смолы: Резорциновые смолы используются в производстве древесно-стружечных плит, когда требуются сложные клеевые соединения. Резорциноформальдегидные (RF) смолы представляют собой смолы холодного отверждения, т. е. фенолы и резорцины отверждаются формальдегидом при низких температурах. Они обеспечивают прочное и атмосферостойкое соединение.
Натуральный клей
Натуральный клей состоит из белков, дубильных веществ и лигнинов. В настоящее время протеины используются совместно со смолами ПФ, так как все они не соответствуют технологическому стандарту отрасли древесных материалов.
Дубильные вещества извлекаются из коры, листьев, плодов и древесины и используются в смесях со смолами PF. Из-за нежелательного эффекта темного цвета в швах они почти не используются в Европе.
Минеральный клей
Эти ламинированные панели изготовлены из портландцемента и гипса в качестве вяжущего. Они имеют лучшую огнестойкость, больший вес и более высокую степень износа обрабатывающих инструментов. Гипсовые ламинированные панели на древесной основе используются исключительно внутри помещений, так как не обладают свойствами атмосферостойкости и водостойкости цементно-клееных панелей.
Добавки
Добавки обычно добавляются в синтетическую смолу для оптимизации свойств плиты. Добавками могут быть парафин, отвердители, буферы, наполнители, пигменты, поглотители формальдегида, антипирены и фунгициды.
обзор завода по производству OSB
Завод ДСП (округ) | Сообщество PV
Если вы не получили электронное письмо с регистрацией для подтверждения своей учетной записи, отправьте нам электронное письмо с вашим именем пользователя.Убедитесь, что вы отправили электронное письмо с адреса электронной почты, который вы использовали при регистрации, чтобы мы могли вручную подтвердить вашу учетную запись. Отправьте электронное письмо на адрес [email protected]. Альтернативой является отправка вашего имени пользователя и электронной почты FloydN в разногласиях. Наш дискорд-сервер находится внизу страницы. Извините за неприятности.
JavaScript отключен. Для лучшего опыта, пожалуйста, включите JavaScript в вашем браузере, прежде чем продолжить.
Вы используете устаревший браузер.Он может некорректно отображать этот или другие веб-сайты.Вам следует обновить или использовать альтернативный браузер.
ПЕРЕЙДИТЕ В ПАНЕЛЬ АДМИНИСТРАТОРА > ДОПОЛНЕНИЯ И УСТАНОВИТЕ БОКОВУЮ ПАНЕЛЬ VERTIFORO, ЧТОБЫ ПРОСМОТРЕТЬ ФОРУМЫ И БОКОВУЮ ПАНЕЛЬ
B uil даблТребуются другие заводские продукты
Дополнительные заводские продукты: щепа для лесопилки/щепа для измельчения досок, клей 3M Adhesive’s Glue
Построен в округе Плезант-Вэлли
Этот цвет означает, что он применим только к версии карты округа Плезант-Вэлли.
|
| , полученные от | Выходы | |
Sawmill / Лесное хозяйство / Доска Чиппер / Отправляются 3M Клеи / Отправляются | ДСП |
Теперь на земле есть значки, чтобы вы знали, что там есть подсказка глобальной компании:
- Автор
- Раппрам
- просмотров
- 1 028
- Последнее обновление
Процесс производства ДСП с меламиновым покрытием
Меламиновая древесно-стружечная плита представляет собой разновидность композитного материала, относящегося к новому типу строительных отделочных материалов , также может называться древесно-стружечной плитой, которая представляет собой конструкционный древесный продукт, изготовленный из древесной щепы, стружки лесопиления или даже опилок. и синтетическую смолу или другое подходящее связующее, которое прессуют и экструдируют.
Сырье для меламиновой стружечной плиты подается в дисковый измельчитель с четырьмя-шестнадцатью радиально расположенными лезвиями и производится путем смешивания древесных частиц или хлопьев со смолой и формирования из этой смеси плиты. Когда смола находится в жидкой форме, она распыляется через форсунки на частицы. И говорят, что меламин является важным органическим химическим промежуточным продуктом, в основном используемым для производства меламиновой смолы, обладает отличной водостойкостью, термостойкостью, дугостойкостью и отличной огнестойкостью.Поверхность использует меламин и имеет высокую плоскостность, устойчивость к истиранию. Древесно-стружечные плиты сначала сушат, после чего отсеивают все крупные или мелкие частицы.
Существует несколько типов смол, которые широко используются, в том числе аминоформальдегидные смолы, мочевино-меламиновые смолы, фенолформальдегидные и меламин-мочевинофенолформальдегидные смолы. Смолы первого типа лучше всего подходят с точки зрения стоимости и простоты использования; Смолы мочевины и меламина используются для обеспечения водостойкости, а повышенное содержание меламина обеспечивает повышенную устойчивость; Фенолформальдегид обычно используется там, где панель используется для наружных работ из-за повышенной водостойкости, обеспечиваемой фенольными смолами, а также из-за цвета смолы, в результате чего панель становится более темной; Фенольно-формальдегидные смолы меламина и мочевины существуют в качестве компромисса.Меламиноформальдегидная смола представляет собой термореактивный полимер. Прозрачное огнезащитное покрытие для древесины на основе меламиноформальдегидной смолы в качестве сырья обладает хорошими декоративными свойствами, а также огнезащитными свойствами. Чтобы еще больше улучшить свойства панелей, используются резорциновые смолы, обычно смешанные с фенольными смолами, но обычно они используются с фанерой для морского применения и в редких случаях при производстве панелей.
Когда смола смешивается с ДСП с меламиновым покрытием, жидкая смесь превращается в лист.Весовое устройство регистрирует вес хлопьев, и они распределяются по месту с помощью вращающихся граблей. В древесно-стружечных плитах разной плотности хлопья распределяются воздушной струей, которая отбрасывает более мелкие частицы дальше, чем крупные. Две такие форсунки, перевернутые, позволяют частицам увеличиваться от мелких до крупных и снова до мелких.
Сформированные листы затем подвергают холодному прессованию, чтобы уменьшить их толщину и упростить транспортировку. Позже они снова сжимаются под давлением от двух до трех мегапаскалей и при температуре от 140 до 220 градусов по Цельсию.Этот процесс устанавливает и затвердевает клей. Все аспекты всего этого процесса должны тщательно контролироваться, чтобы обеспечить правильный размер, плотность и консистенцию плиты. Наконец, доски затем охлаждают, обрезают и шлифуют. Затем они могут продаваться как необработанная плита или поверхность, улучшенная за счет добавления деревянного шпона или ламината.
Нравится:
Нравится Загрузка…
РодственныеКитай Машина для производства ДСП Производители, Поставщики, Фабрика — Сделано в Китае
Полностью автоматическая полная линия по производству ДСП/ДСП на основе жома / машина для производства 5 000-100 000 м3 годовой мощности
Уважаемый клиент:
Добро пожаловать в наш Веб-сайт и надеемся, что наши продукты оставят вас довольными.
Мы мыслим творчески, смело проектируем, производим точно и
лояльно относимся к нашим клиентам. И у нас есть собственная фабрика. Поэтому мы можем производить продукцию
в соответствии с требованиями заказчика.
Дайте нам возможность договориться, это сделает вас сюрпризом. Ваш
Полностью автоматическая линия по производству ДСП/ДСП на основе жмыха/машина Производительность 5000-100000 м3 в год
ДСП изготавливается из древесины малого диаметра , ветки, древесные отходы и недревесные сельскохозяйственные отходы через секцию подготовки стружки, сушки, разбрасывания и горячего прессования. Готовые плиты можно использовать для изготовления мебели, строительства, упаковки, украшения и ламинирования автомобилей и овец.
1) Секция подготовки щепы 70000 куб. кольцевая дробилка, с помощью которой стружка превращается в хлопья,
, затем хлопья хранятся в бункере для влажных хлопьев.
2) Секция сушки и просеивания Полностью автоматическая линия по производству древесно-стружечных плит мощностью 70000 куб.Квалифицированные стержневые хлопья
хранятся в бункере стержневых хлопьев; Крупногабаритные хлопья отправляются на мельницу для повторного дробления, а
транспортируются в бункер поверхностных хлопьев.
4) Участок формовки и горячего прессования
Поверхностные и сердцевинные хлопья направляются в классиформовочную машину, и равномерно формируются на конвейере мата
. После процесса удаления металла, предварительного прессования, продольной пилы, поперечной пилы,
ускорительного конвейера, скребкового конвейера, складского конвейера и загрузочного конвейера маты
транспортируются на носитель, а затем на горячее прессование. Черновые доски после прессования проталкиваются в разгрузчик
через поддон.
5) Секция охлаждения и калибровки Полностью автоматическая линия по производству древесно-стружечных плит мощностью 70000 куб. доска, уложенная на гидравлический подъемник.
6) Шлифовальная секция 70000cbm/год Полноавтоматическая линия по производству ДСП на продажу
Доска шлифуется, проверяется и хранится.
Управление ПЛК используется в секции формирования матов. Подробное описание продукта
1. Линия по производству ДСП
2. Размер плиты: 4 * 8 футов
3. Толщина: 8-25 мм
4. Годовая мощность: 20000-120000CBM
5. Управление PLC 70000cbm/год Полностью автоматическая линия по производству древесно-стружечных плит на продажу
Преимущества
1. Профессиональный производитель, с 1990 года!
2. Высокая эффективность и стабильность
3.Удобный транспорт и идеальное послепродажное обслуживание
Почему выбирают нас
Мы являемся фабрикой (не дилером)
мой дорогой. Полностью автоматическая линия по производству древесно-стружечных плит мощностью 70000 куб.
Hot Tags: Машина для производства ДСП, Китай, производители, поставщики, фабрика, дешево, сделано в Китае
Передовые технологии — SicoCam с SICK AppSpace
Дорогостоящее ручное измерение необработанной ДСП осталось в прошлом. Встроенная система измерения плит SicoCam от Siempelkamp Logistics & Service теперь измеряет деревянные композитные плиты в непрерывном цикле. Он включает в себя четыре программируемые высокопроизводительные камеры InspectorP65x от SICK и SICK AppSpace.Они предоставляют измеренные значения для расчета размера доски и регулировки пил. Это повышает качество производимых плат, снижает количество брака и повышает производительность. Кроме того, повышается безопасность на рабочем месте.
Ежегодно на заводе по производству ДСП Fritz Egger GmbH & Co. OG в австрийском городе Санкт-Пельтен-Унтеррадльберг около трех миллионов кубометров древесины перерабатывается в 40 миллионов квадратных метров ДСП с покрытием. Этого достаточно, чтобы покрыть половину земной окружности, если их выстроить в линию. ДСП компании поставляется на промышленные предприятия и в специализированные магазины. В списке клиентов Egger есть все известные австрийские производители мебели. Необработанные доски изготавливаются путем прессования прядей доски с последующим выполнением необходимых надрезов многоугольными пилами. Как правило, за этими шагами следует измерение отдельных досок, чтобы исправить любые возможные отклонения в размерах. До сих пор эту задачу приходилось выполнять вручную, удаляя «приемлемые доски» с производственной линии или измеряя доски на заводе, например.г., в звездчатом охладителе.
Требуется решение для обеспечения безопасности, достигнута большая степень автоматизации
Долгое время и Зимпелькамп (инженер установки и установщик оборудования), и Эггер хотели найти техническое решение, которое устранило бы серьезные недостатки безопасности, присущие существующему подходу. «Существующее техническое решение для измерения досок после многоугольной пилы не соответствовало новейшим технологиям», — говорит д-р Франк Отто, руководитель проекта Siempelkamp Logistics & Service GmbH, в отношении первоначальной ситуации, с которой столкнулись обе компании. .«Что еще хуже, многодиагональная пила в наших высокопроизводительных системах выполняет большую часть распила в тандемном, тройном или четверном режиме, другими словами, с двумя или более пилами. В сочетании с ручной коррекцией параметров резки при обнаружении отклонений в размерах процесс ручного измерения доски оказался слишком сложным и слишком долгим для наших клиентов, не говоря уже о связанных с этим недостатках безопасности».
Раньше отдельные доски проверялись вручную с помощью рулетки и перемещались в стопку брака.Если обнаруживались отклонения в измеренных значениях, оператор на пиле должен был ввести и подтвердить необходимые параметры коррекции. К этому времени на завод уже должны были попасть несколько досок с неправильными размерами. Как только пила была отрегулирована, оператору приходилось вручную снимать другую доску и измерять ее, чтобы определить, были ли достигнуты желаемые результаты. Если доска не соответствовала спецификациям, оператору приходилось заново настраивать пилу.Этот процесс может занять от пятнадцати минут до получаса.
«Теперь, когда система измерения досок находится внутри станка, пила может быть откорректирована сразу же после обнаружения каких-либо отклонений в размерах», — отмечает Мартин Хинтерхофер, менеджер по технологиям Fritz Egger GmbH & Co. OG. «Благодаря новой системе мы также можем быстро реагировать на изменения процессов, чтобы стабилизировать наши процессы и обеспечить постоянное качество конечного продукта».
Измерение геометрии платы
В производстве древесно-стружечных плит формовочно-прессовая линия представляет собой наиболее ответственную системную единицу всего предприятия.Являясь центральным элементом завода, он играет важную роль в определении производительности завода и качества продукции. По этой причине выход машин, расположенных ниже по потоку, должен быть согласован с линией, что поможет избежать узких мест. Например, система измерения геометрии доски в идеале должна располагаться на линии и, по возможности, после пилы. Встроенная система измерения досок SicoCam от Siempelkamp измеряет длину и ширину доски, а также вычисляет диагонали и углы в четырех углах доски.Это позволяет оптимизировать обрезку и поперечную резку и помогает свести к минимуму количество отходов.
Siempelkamp добавляет (еще одну) вишенку на вершине
После обрезки по длине бесконечной пряди отдельные доски измеряются на конвейерной дорожке по мере их прохождения через систему. Над этой дорожкой четыре программируемые 2D-камеры Inspector65x установлены на портале, причем камеры установлены на подвижных салазках, расположенных в задней части прохода по направлению движения транспорта.С помощью салазок система камер настраивается на различную длину доски. Точность настройки находится на шкале 0,01 миллиметра. Небольшой фотоэлектрический датчик W12-2 Laser обеспечивает фронтальное обнаружение и активирует функцию захвата (запускает камеры). «У нас есть конвейерная лента или роликовый конвейер; портал SicoCam расположен над ним, и плата измеряется в том виде, в котором она поставляется», — отмечает д-р Франк Отто, описывая конструкцию. «Никакой механической связи с существующим заводом нет.Он полностью отделен, и нам не нужно вносить какие-либо модификации в существующее оборудование, включая функциональные модификации или замедление досок». «Все это можно сделать во время нормальной работы с кратковременной остановкой, так как нам просто нужно расположить систему над конвейером», — говорит Матиас Кёль, руководитель производства древесно-стружечных плит Fritz Egger GmbH & Co. OG.
SICK AppSpace: свобода разработки индивидуальных приложений
В оптоэлектронике, особенно в области обработки изображений, конфигурируемые продукты часто доводятся до предела своих возможностей, когда реализация определенных функций или характеристик производительности имеет решающее значение. Благодаря экосистеме SICK AppSpace компания SICK предлагает системным интеграторам и производителям оригинального оборудования новую свободу для разработки настраиваемых приложений и пользовательских интерфейсов на основе программируемых камер и оптических датчиков. Измерение геометрии доски требует компенсации высоты при скорости транспортировки доски до четырех метров в секунду. «Планка натягивается, когда выходит из-под пресса, и иногда немного выгибается вниз или вверх. Это нужно учитывать. Единственный способ компенсировать это — расположить лазеры на каждом углу доски и соответствующим образом запрограммировать приложение», — говорит Маркус Гропп, глава филиала Siempelkamp Logistics & Service GmbH, описывая трудности, с которыми пришлось столкнуться в ходе этого процесса.
«Вся система состоит не только из четырех камер, которые просто определяют границы. Это может сделать каждый», – добавляет доктор Франк Отто из Siempelkamp. «Здесь гораздо больше ноу-хау».