область применения и этапы изготовления.
Главная
Новости компании
Изготовление пресс-форм из алюминия
29 Января 2020
Для массового производства мелких деталей широко используется метод литья из пластиковых композитов, для которого нужны алюминиевые пресс-формы. Форма для литья представляет собой заготовку из цветного металла – алюминия, которая повторяет контуры будущего изделия. Использование пресс-форм позволяет существенно ускорить массовый выпуск деталей из пластика, резины, композитных материалов, гарантируя высокую точность отливаемых изделий.
К преимуществам алюминиевых пресс-форм относятся:
- выпуск полностью идентичных изделий;
- высокая точность заданным геометрическим параметрам;
- многократное использование для крупносерийного производства;
- устойчивость к высоким температурам и резкому охлаждению;
- отсутствие деформаций в процессе использования.
Область применения
Алюминиевые пресс-формы широко применяются для изготовления:
- бытовых изделий;
- предметов для домашнего обихода;
- комплектующих электроинструментов;
- деталей для автомобилей, мотоциклов, другого транспорта;
- элементов компьютерной и бытовой техники;
- других деталей и элементов, которые можно изготовить методом литья.
Принцип работы
Производство пресс-форм из алюминия – это технически сложный процесс, требующий высокой точности. Они включают подвижную часть – матрицу и неподвижную – пуансон. С их помощью формируются полости, которые являются обратным оттиском внешней поверхности заготовки. Чтобы сделать отверстия используются гладкие знаки. Если нужно создать элементы с внутренней и внешней резьбой, применяются резьбовые знаки и кольца.
Подвод расплавленного материала будущего изделия выполняется через литьевую систему.
Этапы изготовления
Процесс изготовления пресс-форм для литья включает несколько основных этапов:
- подготовка конструкторско-технологической документации;
- производство заготовок;
- доводка и обработка изделий;
- испытания.
1. Конструкторско-технологическая документация.
На первом этапы готовятся эскизы изделий, строятся 3D-модели. Затем выполняется проектирование пресс-форм, оно заключается в конструкторской проработке модели и ее разделение на отдельные конструкционные элементы. Далее проводится проработка каждого отдельного элемента, формирование линии разделения детали, шиберов и вставок.
2. Производство.
Этап производства включает конструирование, прототипирование и сборку пресс-формы. Она включает в себя большое число деталей, которые должны точно соответствовать друг другу. В конечном итоге, кроме пакета плит, структура пресс-формы включает следующие системы:
- центрирования;
- литниковая;
- выталкивания;
- охлаждения;
- формообразующих элементов.
В пресс-формах может использоваться литниковая система трех типов:
- холодноканальная;
- горячеканальная;
- комбинированная.
Наиболее дешевой является холодноканальная литниковая система.
3. Обработка и доводка.
Чтобы гарантировать требуемое соответствие выливаемых деталей 3D-модели, проводится финишная обработка. Основная часть работ выполняется на фрезерном станке, а затем проводится полирование. Фрезерная обработка алюминия чередуется с термическим закаливаем. Весь цикл состоит из следующих процедур:
- отжиг для снятия остаточных напряжений металла;
- предварительная механическая обработка;
- нормализация;
- получистовая механическая обработка;
- закалка;
- финишная обработка.
На последнем этапе производства выполняют полировку, подгонку и сборку пресс-форм.
4. Испытания.
Испытания выполняются в условиях, которые максимально приближены к реальному производству. Для этой процедуры используются специальные термопластавтоматы. Лучше проводить испытания на тех станках, где будут применяться формы при производстве деталей.
Виды пресс-форм
По принципу действия они делятся на две категории:
- прямого прессования – используются для деталей простой формы;
- литьевого прессования – подходят для серийного производства деталей сложной формы.
По числу формируемых объектов могут быть:
- одногнездными – за один цикл производится одна деталь;
- многогнездными – за цикл выпускается несколько деталей.
По использованию:
- съемные;
- стационарные.
По размещению плоскости разъема:
- вертикальные;
- горизонтальные.
Популярное
21 Июля 2020
Возможности и сферы применения 3D печати
21 Июля 2020
Токарная обработка металла: оборудование и виды работ
5 Февраля 2020
Изготовление технологической оснастки
Пресс формы для литья алюминия, преимущества и применение
30 декабря 2019 года
Изделия из алюминия широко востребованы в разных областях промышленности, благодаря высоким эксплуатационным характеристикам и низкой стоимости.
Большинство алюминиевых изделий изготавливается методом литья в термопластавтоматах.
Пресс формы для литья создаются на специализированных предприятиях, имеющих высокотехнологичное металлообрабатывающее оборудование и штат квалифицированных токарей, фрезеровщиков, проектировщиков, ИТР.
Преимущества алюминия и применение
Изготовление стальных пресс-форм пользуется большим спросом, благодаря множеству преимуществ материала:
Отличные технические свойства позволяют применять изделия из алюминия в медицинской и пищевой промышленности, авиа- и машиностроении, станкостроении и строительстве.
Литые алюминиевые детали используются в автомобилях, ручных и электрических инструментах, бытовой технике.
В пресс-формах изготавливаются емкости и тара для пищевой промышленности, детали мебели и спортивной экипировки, отопительные приборы, корпуса телевизоров, телефонов и ноутбуков.
Описание форм
Пресс-формы, куда впрыскивается алюминиевый расплав, состоят из неподвижной матрицы и подвижного пуансона. Внутри конструкции находится формообразующая полость различных форм.
Формы бывают многогнездовыми и одногнездовыми. Конструкции оснащаются устройствами механизации в виде ползунов, выталкивателей или съемников, а так же нагревателями или охлаждающими элементами.
Расплав в пресс-формы подается через литники, или систему литниковых каналов в многогнездовых конструкциях.
Форма «Крепеж»
Представляет собой двухместную конструкцию, размерами 400×450×461 мм. Габариты получаемых изделий составляют 114×200×92 мм. Сырьё впрыскивается в формы через щелевые литники. Для удаления отливок применяются толкатели диаметром около восьми миллиметров.
Форма «Крепеж изогнутый»
Литьевая двухместная пресс-форма габаритами 440×425×459 мм разработана для изделий размерами 56×188×123 мм. Впрыск в форму осуществляется через щелевые литниковые каналы. Конструкция имеет полости различных размеров. Готовые изделия удаляются выталкивателями, диаметром от 4 до 8 мм.
Форма «Корпус»
Форма одногнездовая, размерами 390×430×350 мм, предназначена для литья деталей габаритами 203×156×40 мм. Заливка алюминия осуществляется через щелевые литники. Поднутрения формируются механическим ползуном.
Форма «Крепление»
Одноместная форма размерами 730×610×490 мм со щелевым литником. Предназначена для литья изделий размерами 467×286×74. Два ползуна, имеющиеся в форме, формируют поднутрения.
Форма «Планка для крепления»
Изделия представляют собой конструкцию с крепежными отверстиями. Пресс-форма состоит из двух гнезд, впрыск в которые осуществляется через щелевые литники. Отверстия формируются при помощи стальных знаков. Размеры формы составляют 490×480×566 мм.
Изготовление пресс-форм — важный технологический процесс. От точности геометрических размеров оснастки зависит качество алюминиевых отливок.
Изготовление форм
Формы выполняются по техническому плану, составляемому заказчиком. Оно должно содержать требования по производительности и условиям литья, информацию о сырье и габаритные размеры будущих изделий. По возможности, предоставляются образцы детали или их эскизные чертежи.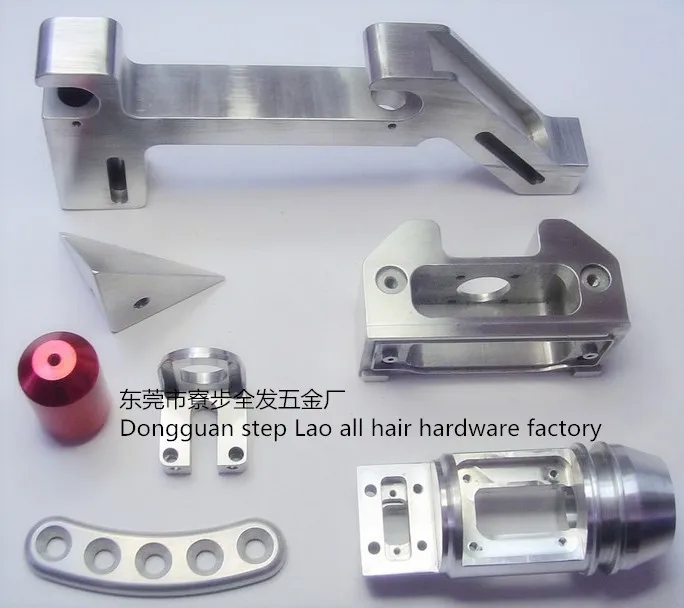
Процесс создания форм выполняется поэтапно:
- Определяются технические и эксплуатационные параметры:
- производительность и количество гнезд;
- тип литниковой системы;
- необходимость в дополнительных устройствах и механизмах.
- Разрабатывается рабочий проект, создается объемная модель будущего изделия.
- Проектно-конструкторская документация и 3D заготовка согласовывается с клиентом.
- Пресс-формы изготавливаются из инструментальной нержавеющей стали на металлообрабатывающих станках с ЧПУ.
- Выполняется закаливание заготовок путем термообработки сначала при температуре выше 650°С, а затем в условиях резкого охлаждения до экстремально низких температур. Закаливание позволяет значительно повысить прочность и долговечность конструкции.
- Формообразующие поверхности полируются и хромируются для создания идеально гладких и износостойких формообразующих поверхностей.
Детали пресс-форм передаются в цех сборки, где выполняется тестирование и испытание. Выпускаются пробные отливки алюминиевых изделий.
Готовая оснастка с контрольными образцами и комплектом конструкторской и сопроводительной документации отправляется заказчику.
Чтобы заказать пресс-формы для литья алюминия, звоните по контактным телефонам или каналу обратной связи в компанию «Имстек».
В кратчайшие сроки изготовим оснастку в точном соответствии с вашей заявкой.
Осуществим запуск и наладку оборудования. Возьмем на техническое обслуживание. Выполним ремонт инструментов и оснастки.
Вахитов Ринат
Похожие статьи
Комплекс горячей штамповки, высокопрочные алюминиевые детали
Масштабируемая линия позволяет производить большие и малые объемы производства
- 23 мая 2019 г.
- Артикул
- Гибка и формовка
Первая в мире масштабируемая производственная линия AP&T для горячей штамповки высокопрочного алюминия предлагает новые методы изготовления легких компонентов кузова автомобиля.
Чтобы соответствовать все более строгим требованиям правительства в отношении выбросов CO2, автомобильная промышленность уже много лет работает над снижением расхода топлива новых автомобилей за счет уменьшения их веса. Новые материалы, конструкции и методы производства сделали возможными более легкие детали и компоненты.
Закалка листовой стали под прессом сыграла важную роль в достигнутом прогрессе. Поскольку эта технология продолжает совершенствоваться, были разработаны другие материалы и комбинации материалов, такие как высокопрочный алюминий. Хотя этот материал значительно легче стали, он требует больших затрат и создает некоторые трудности при формовании.
От проекта до производственной линии
В 2013 году компания AP&T приступила к исследованию разработки нового процесса горячей штамповки деталей сложной конструкции из высокопрочного алюминия. В течение следующих трех лет компания работала с клиентами, университетами и поставщиками над тестированием материалов, производственных процессов и оборудования. Результатом в 2016 году стала первоначальная линия прототипов и ряд прототипов компонентов, которые показали потенциал для использования в будущем.
В 2017 году компания AP&T ввела в эксплуатацию свою первую полномасштабную производственную линию для горячей штамповки высокопрочного алюминия, включая горячую штамповку, W-отпуск и теплую штамповку, в своем испытательном центре в Ульрисехамне, Швеция. Первая в своем роде линия открыла новые возможности для производства легких компонентов кузова автомобиля. Массу кузова потенциально можно уменьшить на 40 процентов, если заменить обычную листовую сталь высокопрочным алюминием, который можно сделать значительно тоньше, сохранив при этом прочность.
Масштабируемая система
Сегодня компания предлагает масштабируемую систему производителям оригинального оборудования и многоуровневым поставщикам. В состав производственной линии входят:
Скоростные штабелеры для подачи заготовок в печь.
Печь для быстрого и равномерного нагрева, разработанная для алюминиевых сплавов 6ХХХ и 7ХХХ.
Станция промежуточного охлаждения для улучшения формуемости заготовок и коррозионной стойкости.
Скоростной перенос заготовки на пресс.
Высокоскоростной сервогидравлический пресс с низким энергопотреблением.
Этот сложный алюминиевый компонент демонстрирует элементы дизайна дверного кольца и внутренней геометрии двери.
Инструменты для формовки и охлаждения.
Мойка и предварительное старение.
Конечная автоматизация.
Масштабируемость делает новую технологию подходящей для больших и малых объемов производства, а производственные мощности можно относительно легко увеличить.
Способность к формованию высокопрочного алюминия позволяет использовать его в производстве цельных деталей, полученных методом горячей штамповки, в качестве альтернативы деталям, состоящим из нескольких различных компонентов, соединенных вместе. Это сокращает количество операций в производственном процессе, что приводит к упрощению обработки и логистики, меньшему количеству инструментов и более эффективному использованию материалов и, следовательно, снижению производственных затрат на единицу продукции.
Новый метод искусственного старения
Одной из задач оптимизации производства было сокращение времени процесса искусственного старения.
При горячей штамповке алюминия обычный подход к упрочнению материала заключается в нагревании его до температуры термообработки на раствор, формовании и охлаждении в инструменте. Чтобы получить желаемые механические свойства, материал затем необходимо искусственно состарить, снова нагревая его до определенной температуры в течение определенного периода времени. Однако это может занять несколько часов, а материал затвердевает до того, как деталь будет собрана в кузов автомобиля, что может привести к трудностям при стыковке.
Чтобы сократить время цикла, AP&T выполняет процесс предварительного старения после формовки и закалки детали, чтобы подготовить материал для последующего процесса сушки краски, который обеспечивает окончательное отверждение после сборки кузова автомобиля. Этот этап предварительного старения, который занимает от 5 до 30 минут, приводит к очень пластичному поведению материала во время окончательной сборки компонента в кузовном цехе и обеспечивает хорошую соединяемость. Компания разработала эту последовательность предварительного старения в сотрудничестве с Hydro Aluminium, которая разработала алюминиевый сплав (AA6XX), адаптированный для этого процесса.
Разработка оснастки с помощью моделирования
Высокие стандарты предъявляются к инструментам, используемым для формовки листового металла, чтобы обеспечить соответствие корпусных деталей требуемым допускам и предотвратить растрескивание. AP&T объединила покрытия инструментов и смазочные материалы, чтобы помочь оптимизировать трибологические свойства между поверхностью инструмента и высокопрочными алюминиевыми заготовками.
Для эффективного моделирования методом конечных элементов (МКЭ) при формовании листа компания проанализировала механические свойства различных марок высокопрочного алюминия. Он также подтвердил свои возможности моделирования с использованием различных тестовых геометрий, чтобы обеспечить эффективное взаимодействие между моделированием FEM, проектированием инструмента и производством инструмента.
AP&T, www.aptgroup.com
Преимущества и процесс формования деталей из алюминия методом глубокой вытяжки
Опубликовано администратором | Оставить комментарий
Свойства алюминиянаделяют его многими преимуществами, отличающими его от других металлов. Алюминий универсален, устойчив и пригоден для вторичной переработки, и его вес составляет всего около одной трети веса стали.
Детали из алюминия глубокой вытяжкистановятся все более популярными как среди производителей, так и среди покупателей. Некоторые преимущества, связанные с алюминием глубокой вытяжки, включают:
- Возможность использования в широком диапазоне приложений
- Высокая ударопрочность и устойчивость к ржавчине
- Исключительное соотношение прочности и веса
Эти свойства сделали его популярным выбором для применения в аэрокосмической, автомобильной и медицинской промышленности, и это лишь некоторые из них.
Преимущества алюминиевых компонентов
Производство алюминиевых деталей методом глубокой вытяжки может предоставить клиентам широкий спектр преимуществ. Ниже приведены некоторые ключевые преимущества этого процесса:
- Некоторые аэрокосмические продукты могут работать только в пределах определенных допусков по весу. Поскольку алюминий имеет высокое отношение прочности к весу, в таких случаях он является идеальной альтернативой стали.
- Внешние автомобильные панели всегда подвержены риску образования вмятин в результате ударов и столкновений. Высокий уровень стойкости к вмятинам из алюминия глубокой вытяжки означает, что для вдавливания алюминиевых панелей требуется больше усилий, чем для панелей из других металлов. Алюминий
- полностью пригоден для повторного использования, а это означает, что даже когда срок службы приложения подходит к концу, сырье не должно быть потрачено впустую. Естественная коррозионная стойкость алюминия
- означает, что ему не нужно подвергаться обширной регулярной обработке, и он сам по себе может выдерживать большой износ окружающей среды.
- является электрическим и тепловым проводником высочайшего порядка. Детали из алюминия глубокой вытяжки
- очень экономичны, и их можно адаптировать для работы как в мелкосерийном, так и в крупносерийном производстве.
Процесс формования деталей из алюминия методом глубокой вытяжки
Штамповка алюминия сжимает алюминий в заданные формы и формы. Глубокая вытяжка дает много преимуществ по сравнению с растяжением алюминия, поскольку алюминий является очень неэластичным материалом. Процесс глубокой вытяжки алюминия состоит из нескольких этапов.
В начале процесса глубокой вытяжки алюминиевая деталь втягивается или вытягивается в полость штампа штамповочной машины. Глубина полости равна или превышает минимальную ширину детали. Оператор должен обеспечить приемлемую степень вытяжки, так как сжатый металл имеет тенденцию сопротивляться потоку. Впоследствии в процессе глубокой вытяжки используется радиальное растяжение-тангенциальное сжатие для придания металлу желаемой формы.
Этот процесс превращает плоский листовой металл, также известный как «заготовки», в полые цилиндрические или коробчатые корпуса с прямыми или скошенными сторонами. Конечные продукты также могут иметь форму комбинации сужающихся, изогнутых и прямых сторон.
Серия штампов перекраивает корпус и постепенно уменьшает его диаметр при одновременном увеличении длины. Во время выполнения этих операций толщина стенки детали изменяется минимально.
Поскольку глубокая вытяжка является процессом холодной обработки, побочным эффектом этих операций является затвердевание алюминиевого материала, что делает его более прочным и долговечным. Кроме того, зернистая структура алюминия претерпевает изменения по мере того, как заготовка формируется и вытягивается до своей окончательной формы. Это также повышает прочностные характеристики алюминия.
Лидер в производстве алюминия для глубокой вытяжки
Формование алюминиевых деталей методом глубокой вытяжки предлагает ряд ключевых преимуществ для конечного применения.