Как сделать форму для литья
Студент ФабЛаба рассказывает, как она сделала форму для литья на фрезерном станке Roland Modela, и отлила в форму металл и пластик.
Задача: Разработать произвольную фигурку или изделие, которое мы могли бы повторить несколько раз, сделав для него форму для литья.
Я решила скачать модель фигуры с Thingiverse и по-своему персонализировать её в Rhinoceros. Мне хотелось попробовать поработать с твёрдыми материалами такими как металл или жесткий пластик, поэтому сама форма для литья должна была быть мягкой. Контрформу мы делали из воска для моделирования с помощью фрезерного станка Roland Modela, а для самой формы мы использовали термостойкий силикон.
Скачать файл модели формы можно здесь:
Rhino 3D модель Формы для литья [.3dm]
Общие рекомендации при изготовлении формы и контрформы:
1) Рассчитайте диаметр используемой фрезы. Убедитесь, что вы оставляете достаточно места между вашим изделием и стенкой контрформы.
2) Оставьте отверстие достаточного размера для заливания материала, а также дополнительное вентиляционное отверстия для выхода воздуха.
3) Стенки контрформы должны быть немного наклонены.
4) Если вы делаете форму из двух частей, не забудьте сделать шипы и пазы для точного соединения половинок.
5) Помните, что для отливки твердых изделий нужны мягкие формы.
6) Обратите внимание на соотношение смешиваемых материалов отливки.
Процесс изготовления
Изменить форму черепа я пробовала двумя разными способами, чтобы получить двустороннюю форму для отливки. Так как отливать я буду из металла, и изделие будет твердым, то сама форма должна быть мягкой. Я подготовила 3D-модель контрформы в Rhinoceros, которую буду вырезать из бруска воска для моделирования размером 7,0 X 14,1 X 3,5 см. Также я учла и оставила необходимые отверстия для заливки металла и вентиляционные отверстия.
После того, как я закончила делать 3D-модель, я стала вырезать из бруска модельного воска контрформу, на фрезерном станке Roland Modela.
Когда контрформа была вырезана, я начала делать собственно саму форму из термостойкого силикона. Как я упоминала ранее, форма должна была быть не только мягкой, но и очень термостойкой, поэтому я использовала силикон повышенной термостойкости Mold MAX® 60.
Порядок действий изготовления нашей формы для литья:
1) Нанести некоторое количество универсальной разделительной смазки-спрея и дать ей подсохнуть в течение 3 минут.
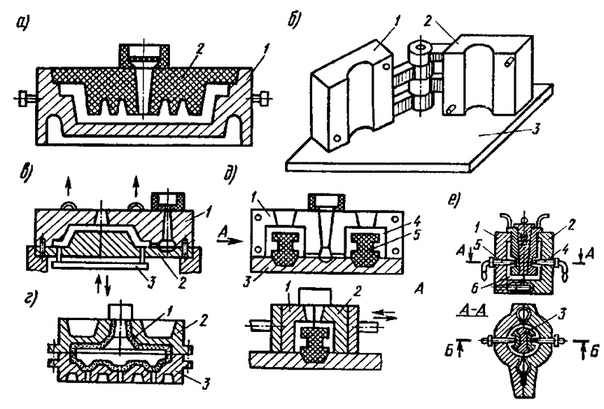
3) Вылить смесь в контрформу, убедившись, что внутрь не попали пузырьки воздуха.
4) На всякий случай тщательно простучать форму, пока все пузырьки воздуха не выйдут на поверхность.
5) Дать силикону застыть в течение суток.
К сожалению, в моём случае получилось так, что через сутки силикон был всё ещё незастывшим. Оказалось, что весы были испорчены, показывали неверный результат, и я смешала в неправильной пропорции! После очистки контрформы с помощью воды и мыла я постаралась сделать всё правильно.
Хоть и со второго раза, но получилось же!
Теперь всё готово к долгожданной отливке.
Для того, чтобы отлить металлические изделия я сделала следующие шаги:
2) Нагреть печку или сосуд, в котором будете плавить металл, подождать пока ваши заготовки расплавятся. Соблюдайте технику безопасности и работайте в перчатках!
3) Сложить обе части формы и выровняв сжать их каким-нибудь удобным для вас способом.
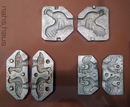
4) Аккуратно и неспешно залить расплавленный металл.
5) Сразу же окунуть форму в холодную воду для охлаждения. Оставить форму в воде до тех пор, пока она достаточно хорошо не остынет и можно будет её трогать.
6) Снять форму и достать ваше изделие.
Черепа вышли очень неплохими, с хорошей детализацией. Один из них я отполировала, а второй оставила без обработки (см. рисунки).
После завершения работ с металлом, я попробовала сделать то же самое из пластика.
Также пластиком легче оперировать, он не горячий и отливать из него проще.
Результат на картинке:
Литейные формы: какими бывают формы для литья
- льтье
- жидкая штамповка
- метод жижкой штамповки
- литье под давлением
При литье металлов расплав всегда заливают в форму. Формы для литья бывают разовыми и многоразовыми, которые, в свою очередь, также могут быть различных видов.
Одноразовые литейные формы имеют песчаную основу. Смешанный в специальной машине с водой и связующими веществами кремнистый песок идет на изготовление форм, в которых можно получить литье различной конфигурации, любых размеров.
В цветном литье в качестве разовых форм широко используют оболочковые формы. Гипсовые оболочковые формы (гипс с быстро затвердевающим полимером) применяют для облицовки модели отливки. После высыхания гипсовую форму разрезают пополам, сушат, после чего соединяют полученные половинки формы и заливают металлом.
Для литья по расплавляемым (выплавляемым) моделям используют оболочковые формы на основе диоксида кремня, порошок которого скрепляют связующим веществом. Такие формы применяют для литья металлов, которым присуща высокая температура плавления. Пресс-форму из легкоплавкого металла наполняют или парафином, или замораживаемой впоследствии ртутью, или пластмассой. Полученную модель облицовывают огнеупорным материалом, который уплотняют вибрацией. После затвердения форму нагревают, из-за чего модель расплавляется и вытекает, а в полученную оболочковую форму заливают расплав для получения отливки.
Также при данном методе литья используют керамические литейные формы. Их изготавливают из каолина (фарфоровой глины) или алюминиевых силикатов. Керамические формы можно использовать для литья несколько раз.
Многоразовые формы изготавливают из огнеупорных металлов: чугуна, жаростойкой стали, меди или латуни. Их используют для цветного литья (например, цинковых, алюминиевых, латунных сплавов). Кроме того, многократно (до нескольких сотен раз) можно использовать формы из графита. Графитовые литейные формы изготавливают, подвергая графит механической обработке. Обычно они состоят из нескольких, скрепляемых между собой деталей, открытым остается лишь отверстие для заливки расплава.
К многократным формам для литья относятся и изложницы – открытые формы, расплав в которые поступает самотеком.
Многократными формами для литья являются также кокили – закрытые металлические формы, внутренняя поверхность которых является точной копией конфигурации будущей отливки. Их широко применяют при литье из меди, алюминия, свинца, магния, олова, цинка. Это самые долговечные литейные формы, их ресурс достигает нескольких сотен тысяч циклов. Об окончании срока эксплуатации кокиля можно судить по качеству поверхностей отливок.
Услуги по проектированию и разработке пресс-форм для литья под давлением
Эффективное литье под давлением позволяет производить тысячи высококачественных отливок за относительно короткое время с использованием одной формы. Этот высокоэкономичный и рентабельный подход к проектированию формы для литья под давлением позволяет производить отливки с однородным качеством и высокой степенью точности. Разработка пресс-форм для литья под давлением обеспечивает превосходное качество деталей, близких к «чистой форме», по цене, которая является чрезвычайно рентабельной.
Процесс обработки литых под давлением деталей должен быть рассмотрен задолго до того, как будет выпущен какой-либо заказ на оснастку. Тщательная оценка требований к механической обработке может привести к перепроектированию для литья под давлением чистой формы или формы, близкой к чистой, с уменьшенным количеством операций.
Свяжитесь с SKS Die Casting для получения дополнительной информации о разработке конструкции формы для литья под давлением или запросите предложение сегодня.
Литье под давлением Услуги по литью под давлением
Разработка пресс-форм для литья под давлением
— Выберите один — О нас Камерное литье под давлением ISO 9001-2015Совместное предприятие Китай Литье под давлениемПорошковое покрытиеТонкостенное литье под давлениемЦинковое литье под давлением
3D-изображение отливки, переделанной из исходной конфигурации
Компьютерная графика формы для литья под давлением
Литье алюминиевого сплава для аэрокосмической промышленности
Процесс разработки формы для литья под давлением
Литье под давлением представляет собой автоматизированный процесс литья, при котором жидкий металл запрессовывается в форму под экстремальным давлением с высокой скоростью. Этот процесс литья очень подходит для массового производства компонентов и обычно используется для сплавов с более низкой температурой плавления. Поскольку для процесса литья под давлением используются постоянные металлические формы, можно производить большие и сложные компоненты с малой толщиной стенок.
Пресс-формы для литья под давлением
Формы, которые используются в процессе проектирования пресс-форм для литья под давлением, изготавливаются из высококачественных жаропрочных марок стали. Формы делятся пополам, образуя полость, в которую в процессе литья вдавливается жидкий металл. Форма для литья под давлением настолько прочна, что с помощью одной формы обычно можно создать более миллиона деталей. Однако фактический срок службы формы будет зависеть исключительно от используемых материалов для литья под давлением.
Преимущества разработки пресс-форм
Литье под давлением использует цветные металлы (такие как алюминиевые сплавы или цинковые сплавы) для изготовления компонентов. Выбор сплава для приложения зависит от бюджета, веса и свойств материала. Другие преимущества, связанные с использованием конструкции формы для литья под давлением, включают:
- Высокая теплопроводность
- Высокая электропроводность
- Хорошие свойства обработки
- Очень хорошая изоляция от электромагнитных и радиочастотных помех
- Высокая коррозионная стойкость
- Высокая прочность и твердость
Преимущества конструкции пресс-формы
Когда дело доходит до разработки высококачественной пресс-формы для литья под давлением, существует несколько факторов, влияющих на общий успех процесса. К этим факторам относятся следующие:
- Первоклассный инжиниринг, собственная разработка инструментов для литья под давлением. Управляйте и контролируйте все аспекты инструментов SKS.
- Разработка параметров процесса впрыска: размер литника, расположение, скорость подачи, время заполнения, давление впрыска, размер пресса.
- Линия разъема, направляющая, перелив, вентиляция, охлаждение.
- Минимальная и максимальная толщина стенки.
- Выбор материала пресс-формы и твердости на основе расчета сил пресс-формы.
- Superior или Premium Grade h23, Uddeholm Orvar или Dievar.
- Моделирование потока.
- Осадка, радиусы, скругления.
- Создание припуска для обработки.
- Использование инструментов отечественных и зарубежных поставщиков.
Дополнительные соображения по проектированию формы для литья под давлением
Некоторые из дополнительных факторов, которые следует учитывать перед началом проекта разработки формы для литья под давлением, включают следующее:
- Расчет литника, скорость подачи и время заполнения.
- Размер пресса, расчет силы зажима.
- Выбор и расчет съемной гильзы.
- Вентиляция и переливы.
- Установление литых и технологических баз
- Создание припуска для обработки.
Свяжитесь с SKS Die Casting & Machining, Inc. для производства пресс-форм для литья под давлением
Свяжитесь с нами для получения дополнительной информации о наших процессах разработки пресс-форм для литья под давлением или запросите предложение для углубленного анализа цен сегодня.
Компания SKS с 1945 года является ведущим поставщиком для разработки форм для литья под давлением.0001
Литье под давлением — важный процесс для применения в различных отраслях промышленности. Неотъемлемой частью процесса литья под давлением является форма для литья под давлением. Форма и характеристики формы влияют на характеристики конечного продукта.
Поэтому необходимо понимать конструкцию формы для литья под давлением. Это поможет вам спроектировать и выбрать правильную форму для ваших проектов литья под давлением. Кроме того, вы можете быть уверены, что конечный продукт будет соответствовать уникальным производственным требованиям.
Таким образом, эта статья даст вам подробный обзор различных типов оснастки для литья под давлением. Вы также узнаете, как спроектировать пресс-форму, и факторы, которые необходимо учитывать при изготовлении оснастки для литья под давлением.
Конструкция формы для литья под давлением играет жизненно важную роль в форме детали. Кроме того, это влияет на качество, однородность и конфигурацию компонентов процесса литья под давлением .
Неправильные спецификации могут привести к коррозии материала или инструмента. Тем не менее, правильная конструкция пресс-формы может увеличить время и эффективность продукта. В конечном счете, качество структуры формы будет определять, будет ли производство работать гладко, а отливки будут иметь наилучшее качество.
Кроме того, конструкция литого под давлением инструмента по существу отражает различные факторы, которые могут возникнуть в процессе производства. Таким образом, вы должны проанализировать структуру отливки во время проектирования. Также важно освоить условия подачи, внедрить критические параметры процесса и учитывать другие экономические эффекты. Это обеспечит соответствие инструментов для литья под давлением основным производственным требованиям.
Понимание формы для литья под давлением начинается со знания конструкции формы. К основным компонентам пресс-формы для литья под давлением относятся:
· Формовочная системаСюда входят полость, стержень, вставки, ползунки и штифты вставок. Полость для литья под давлением определяет форму отливки по мере закрытия движущегося стержня.
· Основа пресс-формы Основными компонентами базовой системы литейной формы для литья под давлением являются стальные пластины и рамы. Эта система объединяет различные части формы и позволяет устанавливать форму на машине для литья под давлением.
Эта система предназначена для выталкивания деталей из пресс-формы. К таким частям относятся выбрасывающая, возвращаемая и направляющая части.
· Система направляющихСистема направляющих соединяется с частью для литья под давлением и камерой давления. Таким образом, он направляет металлический материал в полость штампа в определенном направлении. Эта система напрямую влияет на давление и скорость расплавленного металла. Компоненты литниковой системы: литник, литник, внутренний литник и т. д.
· Система переливаЭтот канал удаляет воздух из камеры давления. Как правило, основными компонентами являются прорези для перелива и вентиляционные прорези. Однако производители устанавливают вентиляционные пробки в глубокие полости, чтобы улучшить условия вентиляции.
· Прочее Другие компоненты формы для литья под давлением включают детали для позиционирования для правильного размещения деталей в форме. Кроме того, имеются штифты и болты для крепления.
Существует несколько типов оснастки для литья под давлением, и они выполняют различные функции в зависимости от требований. Они включают:
Матрицы для прототипированияЗначительная инвестиция в литье под давлением — это полнофункциональная матрица, изготовленная по индивидуальному заказу. Таким образом, штамп-прототип помогает сделать большое количество отливок для проверки различных деталей. Стратегии прототипирования включают гравитационное литье, механически обработанные вырезы и 3D-печатные детали. Однако они предполагают компромиссы в отношении свойств, допусков и дизайна.
Прототип, полученный методом литья под высоким давлением, будет вашим лучшим вариантом, когда вам потребуется тот же сплав, свойства, процесс и геометрия для производства. В штампах для прототипирования могут использоваться предварительно закаленные инструментальные стали без покрытия и стандартизированные компоненты. В результате они могут быть произведены в короткие сроки и по сниженной цене.
В отличие от других методов производства, в этих формах также используются менее эффективные методы выталкивания или охлаждения. Поэтому вы должны учитывать, что инструмент не прослужит долго, а штамп не будет таким же эффективным, как производство. Однако это не будет проблемой, если вам нужно только небольшое количество литья.
Пластины Rapid ToolingБыстрорежущие инструменты относятся к вставкам и штампам, изготовленным с использованием методов с более коротким временем производства, чем обычные методы. В отличие от черновой механической обработки и термической обработки, к методам быстрой обработки относятся выборочное лазерное спекание, прямое напыление металла, лазерное формование сетки и т. д.
Таким образом, можно ожидать, что создание этих штампов для литья под давлением будет происходить намного быстрее. Производители могут использовать эти штампы либо в качестве штампов для прототипирования, либо в качестве штампов для производства. Наиболее жизнеспособный выбор будет зависеть от требований к объему производства.
Эти штампы являются наиболее распространенными типами штампов для литья под давлением. Производственные штампы необходимы, когда весь дизайн завершен и готов к запуску в аутентичный продукт.
У нас могут быть:
- Одногнездные матрицы без ползуна
- Многогнездные матрицы с несколькими вариантами ползуна
Материалом полости является высококачественная сталь, которая часто удерживается в держателе. Конструкция производственных штампов гарантирует, что они имеют критические размеры. Таким образом, вы можете быть уверены, что они соответствуют требуемым спецификациям обработки.
Штампы для литья под давлением Штамп для литья под давлением представляет собой особый тип формы для литья под давлением. Держатель литейного блока удерживает штампы блока или полость, принадлежащую заказчику, внутри полости в целости. У нас могут быть как одинарные, так и двойные держатели. Типичными примерами размеров блоков полостей, которые удерживают штампы, являются 8 x 10, 10 x 12, 12 x 15 и 15 x 18 (все в дюймах).
В единичных штампах используются стандартные детали, используемые для менее сложных компонентов небольшого объема. Изготовленная на заказ матрица более эффективна для деталей больших объемов со сложной геометрией. Эти штампы специально разработаны для детали, обеспечивая максимальный контроль и эффективность.
Штампы для обрезкиCMW использует штампы для обрезки для крупносерийного производства и производственных штампов. Обрезная матрица отрезает заусенец, желоб и перелив детали сразу после завершения литья. Некоторым триммерам требуются гидравлические движения или кулачок, в то время как другим требуются функции открытия и закрытия для эффективного удаления заусенцев.
Геометрия детали не позволяет полностью удалить заусенец с помощью штампа для обрезки. Таким образом, стратегии ручного дефлеширования и услуга индивидуальной обрезки — идеальный вариант в этой ситуации.
Нужны современные детали повышенной прочности и долговечности? Выберите процесс литья под давлением, требующий инструментов для производства ваших конечных деталей. Хорошая новость заключается в том, что услуги литья под давлением RapidDirect предоставляют вам универсальное решение.
Попробуйте RapidDirect прямо сейчас!
Вся информация и загрузки защищены и конфиденциальны.
Процесс проектирования формы для литья под давлениемВ этом разделе описывается процесс проектирования формы для литья под высоким давлением. Процесс имеет пять широких категорий:
Предварительный этап Перед проектированием пресс-формы важно проверить технологичность изготовления детали по технологии литья под давлением. Этот этап включает в себя оценку практичности продукта по геометрическим и размерным характеристикам.
Габаритный вид : Необходимо знать размеры детали и количество полостей, необходимых для каждой отливки. Это поможет узнать силу открытия и объем отливки. Знание этих данных значительно облегчит технико-экономическое обоснование.
Геометрический вид : Геометрия деталей включает рисование линии разъема. Линия разъема делит форму для литья под давлением на две части, что позволяет легко открывать форму и извлекать отливку. Кроме того, поверхность деталей зависит от их положения от линий разъема. Следовательно, поверхности должны быть спроектированы в направлении открытия пресс-формы.
Геометрический допуск котировок, обнаруженных на 2D-модели, может быть довольно сложно воспроизвести из-за усадки, вызванной охлаждением металла. Чем выше количество котировок, тем сложнее получить одинаковое значение на отливке. Таким образом, вы можете приступить к проектированию пресс-формы для литья под давлением, как только подтвердите технологичность детали.
Чтобы узнать количество полостей, необходимо учитывать количество деталей, которые нужно изготовить, ориентацию полостей и гипотетическое время цикла. Таким образом, вы можете выбрать лучший вариант между многогнездной или одногнездной пресс-формой.
При выборе многогнездной пресс-формы помните, что, помимо увеличения количества фаз выталкивания и сложности заполнения, на производственный процесс могут влиять размеры полости и расположение продукта.
Площадь проекции Площадь проекции – это поверхность, полученная в результате проекции полостей на плане. Он перпендикулярен направлению отверстия пресс-формы. Площадь проекции является жизненно важным компонентом этапа проектирования. Он связывает усилие открытия расплавленного металла со стенками пресс-формы. В результате сила силы будет зависеть от ориентации размера формы. Сильное усилие вызовет перелив материала, что приведет к образованию заусенцев.
Поэтому вам необходимо оценить силы, создаваемые расплавленным металлом, чтобы предотвратить этот дефект литья. Сила является произведением удельного давления машины, площади проекции и предварительно установленных коэффициентов безопасности. Фактор предлагает более широкий запас, чтобы помочь противостоять максимальному давлению после заполнения. Многие называют это гидроударом.
Машина передает динамическую и статическую силу в конце процесса. Таким образом, создается отмычка, которую должна поглощать сила закрывающей машины. Это закрывающее усилие зависит от размера хода и модели пресса.
Объем и форма штампаОбъем и форма штампа важны для проектирования пресс-формы. В дополнение к желаемому объему учтите, что большие детали будут сжиматься из-за более длительного времени охлаждения, увеличивая скорость усадки. Следовательно, необходимо соответствующим образом подобрать размеры полостей пресс-формы.
Кроме того, рекомендуется учитывать различные переменные, влияющие на окончательный размер пресс-формы. Наиболее важные факторы, которые следует учитывать:
Каналы впрыска : Размер каналов впрыска зависит от количества полостей и положения литников и деталей. Форма каналов нагнетания должна отвечать некоторым требованиям гидродинамики. Например, производители уменьшают сечение, чтобы правильно прилегать к стенке формы при движении в направлении расплавленного металла. Из-за усадки происходит ускоренный поток, и они отрываются от стен. Более гладкий внешний слой предотвратит турбулентность, воздушные ловушки и другие дефекты.
Тип закрытия штампа : Закрытие пресс-формы «открыто/закрыто» является самым простым закрытием штампа. Это лучше всего подходит для продуктов с чистыми, простыми формами, которые можно легко извлечь. Однако это не лучший вариант для деталей со сложной геометрией. Изделия со сложной геометрией будет трудно удалить, поэтому производителю необходимо увеличить общий размер штампа.
Наличие переливов : Переливы представляют собой небольшие колодцы, спроектированные в стратегических частях формы для литья под давлением. Они важны при сборе первых металлических дробей, потому что они часто холоднее последующих. В результате можно избежать холодных напусков и других подобных эстетических дефектов. Кроме того, переливы служат источником тепла, повышая температуру штампа в критических зонах для окончательной отливки.
После завершения начального этапа проектирования следующим этапом является моделирование заполнения пресс-формы с использованием полуэмпирических режимов. Моделирование помогает в расчете модальности заполнения формы. Кроме того, модальность зависит от функции отливки и процесса заполнения. Для деталей сложной конструкции лучше всего наводить компактность и механическую стойкость. Между тем, для эстетичных деталей отделка поверхности должна быть первоклассной.
Характеристики можно изменить, изменив время заполнения. Чем быстрее опиление, тем выше качество поверхности, а более длительное шлифование повлияет на прочность компонентов. После завершения анализа будет легче заметить, возникнут ли какие-либо проблемы с кастингом.
Проектирование алюминиевой формы для литья под давлением начинается с анализа технологичности, затем расчета усилий и проверки каналов впрыска. Оптимизация и дизайн этих каналов выполняются посредством моделирования, чтобы узнать режим подачи и обнаружить любую проблему. После успешного завершения этого этапа можно переходить к изготовлению разработанной пресс-формы.
Факторы, которые необходимо учитывать для изготовления идеальной оснастки для литья под давлениемПеред изготовлением оснастки для литья под давлением следует обратить внимание на некоторые моменты, на которые следует обратить внимание при проектировании оснастки для литья под давлением. К ним относятся:
Вытяжка штампа Вытяжка — это степень, до которой вы можете вмешиваться в сердцевину пресс-формы. Вам нужна точная тяга, чтобы безопасно извлечь отливку из формы. Однако тяга не постоянна и зависит от угла наклона стены. Таким образом, такие характеристики, как тип используемого расплавленного сплава, глубина формы и форма формы, могут влиять на весь процесс.
Еще одним фактором, влияющим на сквозняки, является геометрия пресс-формы. Как правило, ненарезанные отверстия необходимо нарезать из-за риска усадки. Точно так же внутренние стены нуждаются в большем проектировании, чем внешние стены, потому что внутренние стены имеют тенденцию к усадке.
СкругленияСкругление — это вогнутое соединение, помогающее сгладить наклонную поверхность. Криволинейная поверхность мешает процессу литья, поэтому складки имеют скругления для получения заточенной кромки и снижения риска производственных ошибок. Хотя есть исключение для линий разъема, вы можете добавить скругления к любой части пресс-формы.
Скругление увеличивает срок службы инструмента. Чтобы обеспечить непрерывность гладкости, сделайте скругление постоянного радиуса. Кроме того, для инструментов с глубокой внутренней частью потребуются скругления большего размера.
Линии разъема, также известные как поверхности разъема, соединяют вместе различные секции пресс-формы. Если линия разъема деформирована из-за рабочей нагрузки или неправильно расположена, материалы могут проходить через пространство между деталями пресс-формы. Это может привести к чрезмерному и неравномерному сшиванию.
ВтулкиВтулки представляют собой литые ручки, которые служат опорами или точками крепления в литом инструменте. В обрабатывающей промышленности обычно добавляют отверстие во внутреннюю структуру бобышки, чтобы стенки имели одинаковую толщину. Заполнение бобышек металлом является сложной задачей, поэтому для решения этой проблемы необходимы оребрение и скругление.
Ребра Ребра, полученные литьем под давлением для повышения прочности материала для изделий с недостаточной толщиной стенок. Выборочное размещение ребер улучшает заполняемость и снижает вес продукта. Это также уменьшает возникновение неравномерной толщины и растрескивания под напряжением.
Наличие отверстий и окон в алюминиевой форме для литья под давлением позволяет создавать существенные сквозняки и облегчает удаление готовой формы. Однако такие функции, как перекрытия, поперечные питатели и переливы, необходимы для предотвращения потока материала и нежелательного выброса в отверстия. Отверстия и окна являются одними из основных элементов геометрии дизайна. Они влияют на течение расплавленного металла и играют жизненно важную роль в конечном качестве продукта.
Символы При литье под давлением производители всегда добавляют логотипы продуктов или торговые марки в дизайн формы. У некоторых отливок есть дата, чтобы отличить партию от другой партии. Хотя символы не усложняют процесс проектирования, они могут увеличить стоимость производства. Приподнятый логотип потребует разного металла для каждой изготовленной детали, в то время как символ с отступом потребует меньшего количества металла.
Литье под давлением имеет тонкую стенку, для которой нет жестких и жестких правил максимальной и минимальной толщины стенки. Необходимо создать равномерную толщину стенки по всей детали. Равномерность обеспечит плавное течение металла при заливке и уменьшит коробление, возникающее в результате охлаждения и усадки. Основная цель состоит в том, чтобы форма для литья под давлением была заполнена до процесса затвердевания, чтобы предотвратить холодное запирание.
RapidDirect Chasing для идеальных деталей для литья под давлением Понимание конструкции формы для литья под давлением облегчит ваш проект литья под давлением. Это также поможет вам сэкономить немного времени и денег. Тем не менее, вам нужны услуги экспертов, чтобы получить правильный инструмент для достижения наилучших результатов. RapidDirect предлагает лучшие услуги по прецизионному литью под давлением для металлических деталей на заказ, предоставляя качественные инструменты, экспертов и простые процессы.
У нас есть широкий выбор материалов, производственных процессов и вариантов обработки поверхности для ваших деталей, отлитых под давлением. Кроме того, наши специалисты предлагают вам производственные предложения, чтобы гарантировать, что вы получите наиболее эффективное решение. После размещения заказа на детали для литья под давлением партнеры-производители RapidDirect изготовят идеальные инструменты для литья под давлением для изготовления лучших деталей для литья под давлением. Загрузите файл с дизайном сегодня и получите мгновенное предложение.
Часто задаваемые вопросыЯвляется ли литье под давлением постоянной формой?
Для несъемной формы металл поступает непосредственно в полость из резервуара.