виды, их применение и технические характеристики. Как правильно выбрать ДСП
Современный рынок строительных материалов предлагает огромное их количество. Однако, среди всего разнообразия, особого внимания заслуживает один – ДСП. Это самый востребованный на сегодняшний день материал для изготовления мебельной продукции и один из самых популярных для отделки. За рубежом его используют очень давно — particle board (доска из маленьких частиц), так она там называется.
ДСП – это древесно-стружечная плита, которая является листовым композиционным материалом. Производится он методом горячей прессовки из отходов различных пород дерева – это могут быть опилки, стружка и прочие. В процессе производства сюда добавляется связующие компоненты – как правило, формальдегидные смолы.
ДСП плиты используются уже почти 100 лет. Они стали лучшим экономичным вариантом, который по своим основным показателям не уступает натуральной древесине. Впервые промышленное изготовление ДСП было запущено в Германии и Швейцарии и это стало необходимым по нескольким причинам.
Кроме того, было нужно удешевить и облегчить производство мебели, так как деревянная мебель является чрезвычайно массивной. Уже с 1950-х годов производство этого материала было поставлено на конвейер.
ДСП отличается отличными эксплуатационными параметрами и техническими характеристиками. Преимуществ у него также огромное количество, это:
- Простота обработки – не потребуется специального технологичного оборудования;
- Устойчивость к влаге, которая позволяет их устанавливать даже в особо влажных помещениях;
- Высокая плотность, обеспечившая отличные показатели прочности;
- Стойкость к высоким и низким температурам, а также агрессивным химическим средам;
- Доступная стоимость;
- Механическая стойкость и многое другое.
Эти характеристики ДСП сделали его таким популярным и распространенным. Кроме того, это универсальный материал и может быть использован во многих сферах хозяйства и строительства.
Существует заблуждение, что данные плиты являются вредными для здоровья и опасными, так как выделяют токсические вещества. Это совершенно не так: возможно, на начальных этапах, когда они только появились, так и было, однако сегодня, благодаря развитию технологий деревообработки и совершенствования состава соединительных смол, данные плиты отличаются высоким классом безопасности. Многочисленные ГОСТы не пропустили бы в массовую продажу ДСП, если бы материал нес хотя бы какие-то риски для здоровья. Также характеристики ДСП зависят и от других факторов – изготовителя, формата и функционального назначения.
Древесно-стружечные плиты очень легко поддаются различным видам обработки – фрезерованию, сверлению, склейке и окрашиванию. Кроме того, их очень любят дизайнеры, так как ДСП позволяют воплощать различные концепции оформления в жизнь. Данный материал является уникальным сочетанием дизайна и прочности, износостойкости и надежности, благодаря чему он стал лидером в мебельной и строительной индустрии.
Существует несколько классификаций данного материала. Одним из наиболее популярных является разделение по сортаменту – от него зависит сфера использования ДСП. Так, выделяют три сорта:
- Первый – соответствует стандартам отделочных материалов, обладает ровной поверхностью и однородной структурой;
- Второсортный ДСП отличается более грубым исполнением. По краям может иметь небольшое отклонение или скол, также может быть незначительно поцарапанным — по остальным характеристикам от первого сорта практически не отличается;
- Бессортовой. Такой вид используется преимущественно в строительной сфере. ДСП этого типа производятся из стружки коры дерева, поэтому обладают грубой и неоднородной текстурой.
Для изготовления мебели рекомендовано применять только материалы первого сорта. Они проходят тщательную проверку и максимально соответствуют всем экологическим стандартам, поэтому совершенно безопасны для здоровья человека. Второсортный и бессортный больше подойдут в качестве отделочного материала для нежилых помещений.
На сегодняшний день существует огромное количество производителей данного материала, однако все же наиболее популярными являются такие зарубежные бренды, как «Egger», «Kronospan» и «Cleaf».
Технология изготовления ДСП очень сложна и с каждым годом совершенствуется. Сырье, которое состоит из древесной стружки, предварительно тщательно сушится. После этого, под воздействием высокой температуры оно прессуется и во время этого пропитывается специальными клеящими составами на основе синтетических смол. В роли таких оставов могут выступать формальдегидовые и фенол-формальдегидовые материалы.
Данные пропитки используются для значительного улучшения физических характеристик ДСП. Благодаря пропиткам увеличивается прочность, влагостойкость и защита от разнообразных механических воздействий. Кроме того, эти смолы делают материал чрезвычайно долговечным и незаменимым для осуществления различных строительных работ. Еще одним преимуществом ДСП перед натуральным деревом является то, что он не имеет никаких сучков и неровностей, полностью гладкий и весьма эластичный.
Что касается габаритов, то необходимо знать, какой толщины бывает ДСП и какие у него размеры. Это необходимо для того, чтобы правильно подобрать материал для конкретных целей. Луше всего типоразмеры продемонстрирует данная таблица:
Характеристика | Размер в мм. | Показатель предельного отклонения,в мм |
Показатели толщины | От 4 и более с градацией 1 | ±0,3* (для шлифованной плиты) ?0,3/ +1,7 (для нешлифованной плиты) |
Показатели длины | 1825, 2040, 2440, 2500, 2600, 2700, 2750, 2800, 2840, 3220 3500, 3600, 3660, 3690, 3750, 4100, 5200, 5500, 5680 | ± 5,5 |
Показатели ширины | 1220, 1250, 1500, 1750, 1800, 1830, 2070, 2135, 2440, 2500 | ± 5,5 |
Какую ДСП выбрать?
Среди большого количества предложений на современном рынке можно растеряться.
- Плоского прессования, которые изготавливаются посредством прессовального усилия перпендикулярно плоскости всей плиты;
- Экструзионные, предполагающие направление прессовочного усилия параллельно плите.
Конструктивно плиты могут выпускаться в однослойном, трехслойном и пятислойном исполнении (для плоского прессования) и однослойными сплошными, а также однослойными с внутренними каналами (для экструзионных). Однослойные плиты отличаются одинаковым содержанием связующих частиц по всей толщине, а в трехслойных и более, внешние стороны содержат большее количество связующих веществ. Такие плиты отличаются еще большей прочностью и гладкостью.
Также возможно изготовление облицованных и необлицованных плит. Первый тип предполагает нанесение специальной пленки по всей площади плиты, что позволяет сразу же собирать мебельные конструкции.
Также, выбирая ДСП, необходимо обращать внимание и на класс эмиссии. Это параметр, который характеризует содержание в плитах формальдегидной смолы, поэтому существует три класса — Е1, Е2 и Е3. Самая чистая и безопасная – это Е1, в ней содержание смолы находится в минимальных количествах, допустимых для здоровья человека (не более 10 мг) и может без проблем применяться для нежилых помещений. А вот класс Е2 уже нельзя использовать для некоторых целей, например, детской мебели. Е3 необходимо применять только в технических целях и нежилых помещениях. Это очень важный фактор при выборе данного материала. Поэтому всегда необходимо отдавать предпочтение только сертифицированной продукции. В сертификате всегда указан класс и характеристики плиты.
Совет: лучшим индикатором качества для ДСП плит может стать Ваше обоняние. Даже, если документы можно напечатать на принтере, то собственный нос не обманешь. Плиты с высокой концентрацией формальдегидов отличаются резким химическим запахом, который несравним ни с чем. Поэтому, в случае обнаружения такого запаха, лучше сразу отказаться от покупки.
Для Российской Федерации стандарты содержания смол такие:
Класс эмиссии | Содержание формальдегидных смол на 100 г |
Е1 | до 10 мг |
Е2 | 10-30 мг |
Е3 | 30-60 мг |
Стоит отметить, что для европейских стран и Америки эти стандарты значительно более жесткие.
Виды ДСП и применение
Особого внимания среди всех видов данного материала заслуживает ламинированная ДСП. Что это такое? Это древесно-стружечная плита, облицованная специальной декоративной пленкой, которая, в свою очередь, пропитывается дополнительно слоями меламина. Такой материал является одним из самых популярных в мебельном производстве и связано это с особыми эксплуатационными характеристиками ДСП ламинат. Смолы меламина добавляют плите совершенно новые возможности – значительно увеличиваются показатели стойкости к перепадам температур и влажности, а также механическим повреждениям. Кроме того, такая плита не потребует дополнительной отделки в дальнейшем. Все эти свойства сделали материал наиболее применимым в производстве мебельных элементов
Так как ламинированная ДСП не может быть повреждена под воздействием горячих и холодных предметов, ее можно даже использовать для кухонной мебели – чаще всего это столешница. За нее можно не переживать, что она повредится при попадании брызг влаги или останутся царапины от ножа, а также следы от горячей посуды. Применяется ламинированная ДСП еще для изготовления офисной мебели.
Это связано с тем, что материал дает возможность создавать чрезвычайно износостойкие изделия, которые при этом остаются презентабельными. Широкий выбор цветов и оттенков, а также покрытий пленки дает возможность подбирать любой дизайн, в полном соответствии с любым стилем. Кроме того, материал является весьма недорогим.
Недостатков плиты не так уж и много: единственным является тот факт, что из плиты нельзя вырезать фигурные изображения или элементы, как из натурального дерева, а также невозможность тонкой обработки плиты. К преимуществам же следует отнести все перечисленные эксплуатационные характеристики и то, что плита изготавливается только из стружки высокого качества, создавая полностью однородную структуру, так как тут отсутствуют сучки, пустоты и сколы. Поэтому его можно использовать не только для мебели, но и для декора, например, укладывать в качестве напольного покрытия. Регулируется качество материала государственными стандартами (ДСП ламинированное ГОСТ 10632-2007).
Видов ламинированного ДСП может быть несколько, в зависимости от слоев и производителя, а также применения.
- Например, влагостойкая ДСП покрывается дополнительной полимерной пленкой, которая предотвращает попадание влаги внутрь материала, а также защищает его от пара и сырости.
Используется, как правило, в ванных комнатах, туалетах, банях и на кухне. ДСП шпунтованное влагостойкое – это лучший выбор для помещений с повышенным уровнем влажности;
- ДСП для пола укладывается, чтобы защитить или выровнять поверхность, создав основу для настила чистового напольного покрытия. Тут используется просто плита, без пленки или ламинирования;
- ДСП для стен выпускается в форме ДСП-щитов или ДСП-панелей, поэтому всегда имеет ламинацию. Также возможна форма шпунтованной ДСП – со специальными зазорами для сборки по типу конструктора.
Данный материал является действительно универсальным. На сегодняшний день древесно-стружечные плиты изготавливаются на многих производствах и наблюдается тенденция роста качественной продукции. Мировой рынок древесно-стружечных плит характеризован наличием большой конкуренции. Конструкция, исполнение и технология изготовления ДСП постоянно совершенствуется и развивается.
ДСП: свойства, характеристики и применение
Содержание статьи:Древесно-стружечная плита является материалом, который производят в виде листов. В строительстве он пользуется очень большой популярностью. Изготовление происходит способом горячей прессовки отходов и стружки из дерева. Связующим веществом при производстве ДСП служат фенолформальдегидные смолы или иные клейкие вещества.
Свойства ДСП
Этот материал имеет низкую стоимость, поэтому в строительстве используется достаточно широко. Но среди его достоинств также можно отметить простоту работы с материалом, малый вес.
Листы производят различной плотности. В зависимости от этого показателя определяется область применения данного материала.
Листы бывают низкой, средней и высокой плотности. Также плиты ДСП производят с использованием разного количества клеящего вещества. Кроме того, различают плиты, имеющие 1, 3 или 5 слоев.
Этот материал не подходит для мест с высокой влажностью воздуха. В этом случае используются плиты, которые обработаны веществами, обладающими водоотталкивающими свойствами.
Отличают ламинированное и дсп шлифованное. Шлифованные плиты ничем не отличаются с каждой стороны. А на ламинированную плиту с одной стороны нанесена пленка из меламина. Такая пленка может выполнять также декоративную функцию, так как кроме однотонных покрытий бывают также и покрытия с рисунком. Ламинированные плиты чаще используют при изготовлении мебели благодаря их внешним характеристикам. А обычные шлифованные используется в строительстве там, где их внешний вид не играет роли, так как они скрыты от глаз.
Сорта ДСП
- Первый сорт. В этом случае изделие не должно иметь выступов или углублений. На нем не должно быть пятен от смолы или парафина. По краю плита должна быть идеально ровной.
- Плиты второго сорта могут иметь некоторые дефекты. Но они не должны занимать более 10% площади всей плиты. В них могут присутствовать крупные фракции отходов.
Сфера применения
Из этого материала производят следующие элементы:
- Ограждения для стройплощадок;
- Мебельные профили;
- Обшивку крыши;
- Недорогую мебель для кухни или детской, а также двери;
- Стенды для выставки;
- Опалубку для обустройства фундамента;
- Перегородки и облицовку для стен и потолка;
- Основу для настила пола и другие.
Больше всего ДСП применяют именно в строительстве и производстве мебели.
-
Строительство.
- Обшивка зданий с внешней стороны;
- Внутренняя отделка кровли;
- Облицовка стен;
- Подоконники и балки.
В строительстве используются в основном второсортные плиты. Внутри помещений они могут использоваться как перегородки или основа под напольное покрытие.
Но если вы приняли решение использовать при строительстве данный материал, важно помнить о том, что он неуместен в местах, где часто наблюдается повышенная влажность воздуха. При воздействии влаги этот материал портится очень быстро. Он не только разбухает, но и утрачивает свою прочность.
При покупке обратите внимание на раскрой плиты. Он должен быть выполнен профессионально, чтобы снизить вероятность возникновения сколов.
-
Мебельное производство.
В мебельной промышленности ДСП компании Будмакс, используется также очень широко. Это вторая область применения данного материала после строительства. Чаще всего в этой области используются именно ламинированные панели. Но если это задняя стенка изделия, то может использоваться и шлифованная.
Из этого материала изготавливают мебель для офисов, которая не требует особой вычурности и отличается достаточно низкой ценой. Материал достаточно хрупкий, поэтому следует обращаться с ним бережно. Обращайте внимание на маркировку, где должно быть указано количество формальдегидов, используемое при производстве.
классификация, выбор и сферы применения
При создании древесно-композитных материалов преследуются в первую очередь две основные цели. Найти применение низкокачественной древесине или древесным отходам и получить доступный экономичный материал. ДСП полностью удовлетворяет этим целям. Среди всех древесных плит этот материал один из самых известных. Это определяется широкой сферой применения, встретить изделия из стружечной плиты можно в виде мебели и строительных материалов.
В этой статье мы поговорим о выборе ДСП, его особенностях и сфере применения.
ДСП – аббревиатура от древесностружечной плиты. Материал производится из измельченной древесины, в качестве сырья используется неликвидное дерево, которое непригодно для других работ. Его измельчают до состояния опилок, затем опилки просушивают и смешивают с формальдегидными смолами, которые объединяют всю эту массу в монолитные плиты. Плиты прессуют и обрабатывают высокими температурами.
Древесностружечные плиты подразделяются на марки в зависимости от характеристик и области применения. Современный ГОСТ был принят в 2014 году, а для влагостойких материалов — в 2013 году, он заменил собой стандарт 2007 года. В нем были изменены некоторые обозначения в маркировке изделий, так как многие пользователи продолжают ориентироваться на старые обозначения, мы приведем обе классификации.
- Общего (Р1) назначения — рассчитаны на использование в сухих условиях, могут использоваться для строительных задач без несущей нагрузки.
Влажность самого изделия не превышает 13%, максимальная допустимая прочность на изгиб зависит от толщины плиты, чем толще плита, тем ниже этот параметр. Для ДСП до 3 мм прочность на изгиб составляет 11,5 МПа, для изделия больше 4 см – 5,5 МПа.
Мебель остается одной из самых широких сфер применения ДСП
- Марка для помещений (P2) — рассчитана на сухие условия эксплуатации. По прочности ничем не отличаются от P1. Эта марка имеет меньше шероховатостей и более ровную геометрию, поэтому P2 больше подойдет для отделочных работ.
Стружечные плиты с декоративным покрытием широко применяются для обшивки стен
По ГОСТу 2007 года эти стружечные плиты обозначались только двумя марка П-А и П-Б, влагостойкость обозначалась буквой В. П-А имел большую допустимую прочность на изгиб, для изделий толщиной свыше 4 см показатель составлял 7 МПа, для П-Б – 5,5 МПа.
- P3 – марка стружечных плит, которая характеризуется повышенной влагостойкостью, т.
е. может применяться в условиях, когда влажность воздуха достигает 85%. Использование в условиях, когда влажность превышает допустимый порог, возможно только в течение непродолжительного времени. ДСП P3 также предназначены для отделочных работ и не могут выдерживать большую нагрузку. При воздействии воды лист может разбухнуть на 12 – 25%. Прочность на изгиб составляет 13 – 7,5 МПа в зависимости от толщины. Фактически изделия соответствуют старой марке влагостойкой П-А.
Водостойкие плиты имеют характерный зеленоватый цвет на срезе
Во влагостойкие плиты часто добавляется меламин и парафин.
- P5 – влагостойкая марка, может использоваться в качестве конструкционного материала для полов и потолков. По своим характеристикам при толщине листа 10 – 20 мм по максимальной допустимой прочности на изгиб демонстрирует показатели сопоставимые с параметрами ОСП-3 (марка ориентированно-стружечной плиты), но при большей толщине P5 становится более хрупкой.
Показатель разбухания от воды тоже находится на одинаковом с ориентированно-стружечной плитой уровне. Только в данном случае зависимость обратная, чем толще лист, тем меньше он набухает (плита толщиной больше 4 см увеличивается на 9 %).
- P7 предназначена для использования во влажных условиях, относится к материалам, несущим повышенную нагрузку, конструкции из P7 применяются для стен, потолков и др. Прочность при изгибе составляет 20 – 15 МПа, а набухание от влажности – 10 — 9 %.
Использование ДСП очень часто становится предметом споров о безопасности этого материала для здоровья человека. Основным поводом для беспокойства обычно становятся синтетические смолы на основе формальдегида, которые используются для связывания общей массы стружечного материала в монолитную конструкцию. Наиболее распространены фенолформальдегидные и мочевиноформальдегидные смолы.
Вред от древесностружечных плит часто преувеличивается на фоне других загрязнений. При этом главным источником формальдегида в больших городах являются автомобили, а вовсе не мебель из ДСП.)
Часто в советах по определению качества материала рекомендуют понюхать плиту. На запах, конечно, ориентироваться можно, во всяком случае странный аромат должен настораживать при покупке, но нос далеко не у всех обладает свойством определять в процентном соотношении содержание формальдегида в изделии. Поэтому в первую очередь лучше обращать внимание на такой параметр, как класс эмиссии формальдегида. Если древесностружечная плита изготовлена по ГОСТам, то класс обозначается буквой E и цифрой от 0,5 до 2. Опасность для человека представляет даже не сам формальдегид, содержащийся в смоле, а его испарения.
- E0,5 – предполагается только в разновидностях ДСП для использования в сухих помещениях (влагостойкие материалы обычно содержат больше формальдегида). Максимальное допустимое содержание для этого класса – 4 мг на 100 г стружечного материала.
Испарения должны составлять до 0,08 мг на м.куб.
- E1 – встречается как среди влагостойких плит, так и среди изделий общего назначения. Содержание вещества должно находиться на уровне от 4 до 8 мг на 100 г. Испарение – от 0,8 до 0,124 мг/м.куб.
- E2 – изделия с таким классом эмиссии нельзя использовать в помещении. В ДСП с таким классом может содержаться от 8 до 20 мг, в испарении – от 0,124 до 0,5 мг/м.куб.
Маркировка по классам наносится на изделие. Чтобы обезопасить себя от приобретения некачественного продукта, лучше всего отдавать предпочтение материалам, которые соответствуют ГОСТу.
Поверхность древесностружечной плиты обрабатывается разными способами. На количество дефектов влияет сорт изделия. В качестве сырья может использоваться крупная или мелкая стружка. По этому признаку поверхности подразделяют на несколько типов.
- Мелкоструктурная – состоит из мелкой стружки, которая образует ровный гладкий слой.
Обозначается буквой М. Иногда такой тип покрытия называют мелкозернистым. В большинстве случаев он используется для отделочных работ.
- Обычная – поверхность средней зернистости, обозначается буквой О. Используется в разных видах работ.
- Крупнозернистое покрытие по ГОСТу не имеет специальных обозначений, обычно такие материалы используются для строительства.
В некоторых случая поверхность плиты шлифуется на заводе в этом случае изделия маркируются буквой Ш. Шлифованные ДСП имеют более ровную поверхность. Нешлифованные обозначаются сочетание НШ и при проведении некоторых видов работ (например, при укладке пола) нуждаются в дополнительном шлифовании. Стружечные плиты разной обработки бывают двух сортов, которые обозначаются римскими цифрами.
- Первый сорт (I) – на шлифованных изделиях первого сорта не допускается технологических пятен, сколов, трещин, вздутий и других дефектов, включения коры допускаются только размером не более 3 мм.
На нешлифованных могут присутствовать пятна, выступы и царапины, которые по своим размерам не должны превышать 0,5 мм.
- Второй сорт (II) допускает содержание различных дефектов, у шлифованных плит иногда присутствует недошлифовка, которая не может превышать 10% от площади плоскости. На шлифованных и нешлифованных изделиях второго сорта чаще всего присутствуют технологические пятна смолы, парафина и масла, на нешлифованных поверхностях их процент обычно больше.
На производстве древесностружечные плиты могут подвергаться дополнительной декоративной обработке. В таком виде они часто используются для производства мебели и для отделочных работ. Нанесение текстурного слоя осуществляется с помощью ламинирования или кеширования. Конечный результат обработки обычно называют ламинированным ДСП.
Отделка стены ламинированными плитами
- Ламинирование – листы бумажной пленки обрабатывают при помощи карбамидоформальдегидных смол, затем с помощью пресса и высоких температур наносят их на стружечную плиту.
Благодаря этому покрытие становится частью материала. Ламинирование позволяет повысить влагостойкость и износостойкость изделий. На поверхности плиты появляется древесная текстура, характерная для дуба, ореха, бука, красного дерева и др.
- Кеширование – способ нанесения декоративного покрытия, при котором лист бумаги с древесными или любыми другими текстурами просто приклеивается на поверхность. В этом случае давление меньше, а соответственно хуже адгезия декоративного слоя с основным материалом.
Шпунтовка – это особый способ обработки торцов плит, он заключается в вырезании шпунтовочных соединительных элементов, которое более известно под названием соединение «паз-гребень». Такая разновидность стыковки позволяет образовывать более ровные поверхности, так как для соединения необходимо соединить паз с гребнем. Шпунтованные ДСП проще монтировать, так как не приходится заботиться о ровном конструкционном шве. К тому же вся поверхность покрытия получается более монолитной и прочной.
Шпунтованные листы для соединения «паз-гребень»
Конструкционный (деформационный) шов делается на случай изменения размеров материала под воздействием влаги.
ДСП применяется в самых разнообразных сферах, особенно широко этот материал используется при производстве мебели, мы же подробнее остановимся на строительных возможностях стружечных плит.
- Черновой пол – представляет собой основание под чистовой пол. Черновой пол служит для выравнивания поверхности. В качестве чернового пола используется ДСП марок P5 или P7, лучше для этой задачи подойдет материал с соединением «паз-гребень». Для пола используются материалы с повышенной влагостойкостью.
Сооружение чернового пола из стружечной плиты на лагах
- Межкомнатные перегородки – стружечные плиты могут использоваться для разграничения пространства внутри помещения. Листы устанавливаются на стальной или деревянный каркас.
При создании перегородок разновидность материала следует выбирать в зависимости от последующей обработки. Наиболее простым вариантом является ламинированная ДСП она уже имеет покрытие с древесной текстурой, поэтому никакой последующей отделки поверхности не потребуется. Под обои, шпаклевку или покраску лучше взять материал без покрытия. При «мокрой» отделке следует обратить внимание на изделия с хорошим уровнем влагостойкости. Для перегородок подойдут листы толщиной 9 – 10 мм.
Офисные перегородки из ДСП
ДСП имеет свойство крошиться при установке в него крепежных элементов, под нагрузкой куски материала могут отваливаться. По этой причине на перегородки из древесной плиты не рекомендуется вешать тяжелые объекты.
- Потолок – ДСП используется для отделки, выравнивания и звукоизоляции потолочных пространств. Принцип использования тут похож на перегородки – на выбор материала влияет последующая отделка. В любом случае лучше остановиться на марках P3, P5 и P
- Кровельные работы – чаще для подобных работ все-таки используется фанера или ОСП, но если кровля хорошо изолирована и не пропускает воду, то ДСП можно покрыть обрешетку.
Материал должен быть влагостойкий и прочный, чтобы по нему можно было ходить при монтаже.
- Подоконники и двери – для создания подоконников и дверей подойдут листы толщиной более 16 мм. Лучше выбрать ламинированные водостойкие изделия.
Ламинированный подоконник из стружечной плиты
Древесностружечная плита – универсальный и практичный материал, которым часто незаслуженно пренебрегают. Современные разновидности по влагостойкости и прочности не уступают другим древесно-композитным изделиям. Они хорошо подходят для чернового пола, потолочного покрытия и создания перегородок.
ДСП: классификация, выбор и сферы применения
характеристика и описание, чем отличаются, в чем разница и что лучше
Технологии изготовления ДСП и ДВП похожи: плиты формируются методом прессования исходной массы при повышенных температурах. По прочности древесно-стружечные плиты превосходят древесно-волокнистые изделия. ДСП выпускаются большей толщины (до 5 см), чем ДВП, благодаря чему могут выдерживать нагрузку, при которой древесно-волокнистые образцы деформируются или ломаются.
Фото: nikolaev.sindom.com.ua
Как видно из названия, древесно-стружечная плита изготавливается из стружек или опилок с применением синтетических полимеров и специальных добавок при помощи метода горячего прессования. В качестве материала исходного обычно используют древесину хвойных и лиственных пород.
Примеры использования и недостатки
Рассчитайте точную стоимость ремонта на онлайн-калькуляторе
и бесплатно получите подробную смету на ремонт
РассчитатьС помощью древесно-стружечной плиты при производстве ремонтных и строительных работ делается так называемая сухая стяжка, монтаж настилов. ДСП используется в качестве сплошной обрешетки — для усиления вертикальной основы. Кроме того, древесно-стружечные плиты применяются для строительства навесов, перегородок, ограждений, настилов, ларей, некоторых предметов мебели — чаще всего кроватей и столов.
Фото: architizer.com
Фото: architizer.com
К минусам ДСП следует отнести некоторую рыхлость и гигроскопичность материала, а также жесткость, которая провоцирует трещины в плите при попытках ее крепления к неровной основе. Данные нюансы следует учитывать в строительном дизайн проекте.
Не рекомендуется использовать ДСП в условиях постоянной сырости или частых перепадов влажности — срок службы таких конструкций может резко сократиться. Многократное применение древесно-стружечной плиты тоже под вопросом — из них нельзя делать сборно-разборные конструкции, потому что переустановка крепежных деталей приводит к тому, что материал на этом сегменте начинает трескаться и ломаться, а саморезы или шурупы уже не держат плиту.
Фото: mit24h.com
Древесно-стружечные плиты бывают малой, средней и высокой плотности, средней и высокой водостойкости, а также шлифованные, нешлифованные и ламинированные. Плиты с повышенной водостойкостью, как правило, используют при изготовлении столешниц для кухонь, мебели для ванных комнат, а также специальных строительных целей. Ламинированные ДСП имеют многообразие цветов и фактур, устойчивость к механическим повреждениям, к термическому воздействию.
Фото: ca-news. org
Фото: masterpotolok.com
Фото: mit24h.com
Особенности ДВП
Древесно-волокнистая плита изготавливается из нескольких компонентов: древесной пыли, синтетического волокна и полимерных добавок. От типа таких добавок зависят некоторые свойства ДВП. К примеру, парафин способствует снижению уровня влагопоглощения материала.
Технология производства древесно-волокнистой плиты та же, что и для производства древесно-стружечной: горячее прессование. Однако за счет того, что в качестве сырья используются мельчайшие фракции, листы ДВП получаются более тонкими — всего от 2 до 10 мм.
Фото: budrukamy.in.ua
Фото: budrukamy.in.ua
К плюсам древесно-волокнистой плиты можно отнести более высокую плотность, чем у древесно-стружечной. Этот материал более податлив на изгиб, благодаря чему из него можно делать больший ассортимент изделий, в том числе и в отделке интерьеров. ДВП имеет низкий уровень гигроскопичности по сравнению с ДСП. Стоимость листа ДВП ниже, чем ДСП с такими же размерами.
Древесно-волокнистая отделка обладает высокой степенью тепло- и звукоизоляции, чего нельзя сказать о древесно-стружечных изделиях. ДВП бывают простыми, окрашенными или с ламинированием, но в целом их ассортимент более разнообразен, чем у ДСП.
Фото: reformasmadridinnova.wordpress.com
Примеры использования и недостатки
Древесно-волокнистая плита применяется для изготовление различной тары, но наиболее широко используется в мебельном производстве для выпуска днищ ящичков и задних стенок комодов, шкафов, стеллажей и полок.
Используется ДВП при монтаже многоуровневых потолков и точечном ремонте рассохшихся дощатых полов. Древесно-волокнистыми листами обшивают разные каркасные конструкции, утепляют поверхности — чаще всего металлические.
Древесно-волокнистые плиты более устойчивы к разного рода механическим повреждениям, чем древесно-стружечные.
К минусам ДВП можно отнести недостаточную прочность — такой лист не выдержит серьезной нагрузки. Впрочем, такой недостаток не мешает дизайнерам использовать панели из ДВП в качестве отделки стен в разных помещениях домов и квартир.
Фото: lentinemarine.com
Фото: ninetynine.nl
Древесно-стружечные и древесно-волокнистые плиты отличаются по своим свойствам и характеристикам, имеют разное предназначение, поэтому нельзя утверждать, что один из этих материалов хуже другого. У каждого из них есть свои достоинства и недостатки, так что для каждого вида работ и предназначения изделия можно подобрать оптимальный вариант.
Древесно-стружечная плита (ДСП) — характеристика и особенности
ДСП (а правильнее ДСтП – именно так называется этот материал согласно ГОСТу) – это древесно-стружечные плиты. Недорогой и практичный строительный и мебельный материал – вот, что такое ДСП.
Древесно-стружечные плиты – изобретение немецкое. Они были разработаны в Германии времён Второй Мировой войны, испытывавшей дефицит древесины для производства фанеры. Именно как дешёвый заменитель фанеры этот материал и задумывался автором – изобретателем М. Химмельхебером. Производить новые плиты стало возможно не из самой древесины, как фанеру, а из отходов лесопильных производств. Первая фабрика, на которой был запущен технологический процесс производства ДСП, находилась в городе Бремене.
Что представляют собой плиты ДСП? Они изготавливаются из стружки, связанной с помощью фенолформальдегидной смолы в монолитную массу, которая, собственно, и формуется в листы и плиты. Полученный материал по потребительским свойствам близок к древесине и фанере, и может с успехом их заменять. Правда, ДСП отличается определёнными недостатками, которые не свойственны натуральным материалам.
Первый недостаток органически присущ всем материалам на основе фенолформальдегидных смол: они способны выделять формальдегид, вредный и опасный для здоровья человека органический газ. Правда, значительные количества этого газа выделяются только при сгорании ДСП, а в нормальных условиях он выделяется в следовых концентрациях. Взрослому человеку при нормальной температуре такие концентрации не повредят. Но следует избегать использования ДСП дешёвых сортов в детских комнатах (организм ребёнка намного более чувствителен к газу формальдегиду), а также в банях, саунах и других высокотемпературных помещениях (при высокой температуре выделение формальдегида резко повышается).
Второй недостаток механический: ДСП плохо держит крепёжные материалы и резьбу. Вкрученные прямо в ДСП шурупы, если их выкрутить и снова вкрутить, будут держаться ненадёжно. Равно же и гвозди удерживаются в этом материале плохо. Решить эту проблему можно при помощи дюбелей.
Кроме стандартных плит ДСП, существуют также плиты особого типа – ламинированные и экструзионные. Первые отличаются от обычных древесностружечных плит только тем, что покрыты особой плёнкой или покрытием, для улучшения внешнего вида. Такие плиты ДСП идут на производство мебели. Вторые несколько отличаются технологией производства: стружки размещают не параллельно, а перпендикулярно плите. Соответственно, изменяются и свойства полученного материала: он лучше изолирует звук, но хуже сопротивляется изгибу. Используются экструзионные плиты ДСП преимущественно в изготовлении дверей. В России технологии изготовления этого вида ДСП не очень распространены, подавляющее большинство их на нашем рынке – импортные.
ЛДСП — это ламинированная древесно-стружечная плита. ЛДСП представляет собой материал, сделанный из нескольких слоев древесных частиц, которые связываются между собой экологически чистыми синтетическими смолами. ЛДСП является очень функциональным, экологически чистым и безопасным для здоровья человека материалом, поэтому он широко используется в таких отраслях промышленности, как мебельное производство, а также для проведения отделочных работ, укладки полов, изготовления дверей и т.п.
ЛДСП изготавливается только из частиц древесины исключительно высокого качества, поэтому такие плиты характеризуется однородной структурой – наличие сучков, сколов и внутренних пустот в ЛДСП недопустимо.
Назад к каталогу статей
|
ДСП для пола: особенности выбора и монтажа
Довольно часть в процессе обустройства пола используется такой материал как ДСП. Среди его главных преимуществ следует выделить прочность и дешевизну. Но, все же именно от выбора данного материала зависит конечный результат работы над полом. Об особенностях и характеристике ДСП поговорим далее.
Оглавление:
- ДСП для пола: свойства и характеристика материала
- Плиты ДСП для пола: преимущества и недостатки
- Рекомендации по выбору листов ДСП для пола
- ДСП шпунтованная влагостойкая для пола — характеристика
- Укладка полов ДСП: как соорудить черновой пол
- Покрытие полов ДСП: как обустроить плавающий пол
- Установка ДСП на бетонное основание
ДСП для пола: свойства и характеристика материала
ДСП представляет собой материал в виде древесно стружечной плиты, для изготовления которого используют древесную стружку, спрессованную с помощью горячего метода. Кроме того, в составе ДСП присутствует клеящее вещество, имеющее не минеральное происхождение.
В соотношением с конструктивными особенностями ДСП бывает:
- одно-;
- трех-;
- многослойным.
Кроме того, выделяют марку А и В, которые отличаются по прочностных характеристиках к изгибу, деформации, влагостойкости и другим техническим показателям.
Также ДСП бывает первого и второго сорта. Материал, принадлежащий к первому сорту практически не имеет дефектов в виде трещин, пятен, сколов, выступов или углублений. Второсортный материал отличается наличием крупных дефектов. Кроме того, существует ДСП без сортный, то есть, плита, на которой присутствуют кардинальные дефекты.
В соотношении с особенностями наружного слоя ДСП бывает:
- с наличием мелкостружечной поверхности, возможен вариант отделки с помощью полимеров;
- стандартный материал, подвергается отделке с помощью шпона;
- ДСП с наличием крупнозернистой поверхности, чаще всего применяется в строительной отрасли.
В соотношении с уровнем отделки поверхности ДСП бывает:
- шлифованной;
- нешлифованной.
Кроме того, существует критерий распределения материала в зависимости от содержания в нем формальдегидных компонентов. В соотношении с влагоустойчивостью различают плиты склонные к деформации, при попадании на них влаги и несклонные к деформации.
Возможен вариант обработки материала специальными пропитками, которые улучшают его пожарную безопасность. В соотношении с плотностью выделяют три класса ДСП:
- высокий;
- средний;
- низкий.
В соотношении с типом покрытия ДСП бывает:
- ламинированной;
- экструзионной.
Первый вариант предполагает материал, который подвергался воздействия высокой температуры и давлении, при этом, на него наклеивается специальный пленочный материал. Более дорогие разновидности такого ДСП покрывают с помощью специального лака, повышающего его стойкость перед механическими повреждениями и влагой. С помощью ламинирования удается достичь привлекательного внешнего вида покрытия. Этот вид ДСП широко распространен в мебельной промышленности.
Второй вариант является материалом, в котором деревянные волокна располагаются в перпендикулярном направлении по отношению к плите. Таким образом, данный материал имеет пониженную прочность.
Применение ДСП связано прежде всего с утеплением деревянных полов или перекрытий бетонного назначения. Именно данный материал позволяет в итоге получить идеально ровную конструкцию, обладающую высокими теплоизоляционными и звукоизоляционными свойствами. При этом, затраты на обустройство данного покрытия будут минимальными.
Плиты ДСП для пола: преимущества и недостатки
Начнем характеристику ДСП с ее недостатков, так как их у нее не так уж и много. Прежде всего, это внешний вид материала, который хоть и является деревянным, но мало напоминает древесину. Также, существенным недостатком ДСП является добавление в нее смол, выполняющих функцию связующего вещества для опилок или других компонентов деревообрабатывающей промышленности.
Среди преимуществ ДСП выделим:
1. Доступная ДСП для пола цена.
Данный фактор делает этот материал одним из популярных как в строительной, так и в мебельной отраслях.
2. Легкость и простота работы.
Материал хорошо режется, легко устанавливается и не требует особых навыков работы с ним.
3. Экологическая безопасность.
Данное преимущество является актуальным в том случае, если при изготовлении ДСП были выдержаны все технологические нормы и требования по качеству связующего вещества.
4. Отличные эксплуатационные свойства.
Использование ДСП в качестве основания под укладку основного пола характеризуется значительным сроком использования материала.
5. Многофункциональность.
Отлично подходит для установки числового пола из паркета или покрытия синтетического происхождения.
6. Высокие звуко- и теплоизоляционные показатели.
Благодаря этому ДСП широко распространено при изготовлении дверей, мебели, для настила полов и даже для отделки стен.
Рекомендации по выбору листов ДСП для пола
Перед тем как ознакомиться с советами по выбору ДСП, следует рассмотреть классификацию данного материала. Чаще всего плиты ДСП разделяют в соотношении с их сортом:
- ДСП 1 сорта;
- 2 сорта;
- 3 сорта.
Материалы первого, второго и третьего сортов различаются в соотношении с прочностью, ровностью, наличием шлифовки, дефектами и другими техническими показателями. Для того, чтобы плита ДСП приобрела идеально ровный край используется специальное оборудование.
1. Плиты, которые относятся к первому сорту, отличаются отсутствием какого-либо покрытия. Наружная их сторона, такая же как и наполнение. Однако, данные плиты покрываются с помощью меламиновой пленки, которая внешне схожа с пластиком. На ее поверхность наносятся разного рода картинки или фото. Стоимость ламинированной ДСП для пола намного выше, чем обычной.
2. Древесно стружечные плиты, принадлежащие ко второму сорту имеют небольшие царапины и сколы. Их стоимость намного ниже, чем у ДСП первого сорта. Сфера применения данного материала ограничивается строительной отраслью. В то же время, именно такой тип ДСП является отличным вариантом для отделки пола.
3. ДСП 3 сорта отличается низким качеством и наличием достаточно большого количества дефектов, особенно механического происхождения, которые располагаются на торцевых участках плит. Такой тип ДСП отлично подходит для сооружения таких элементов как опалубки или межстенные перегородки.
Для того, чтобы купить ДСП для пола следует обратиться в любой строительный магазин. Кроме того, немаловажным фактором при выборе ДСП является эмиссионный класс. Каждая из плит в какой-то степени содержит в составе формальдегидные смолы. Определенные классы имеют меньше данного вещества, а другие — больше. Данный материал способен испаряться из ДСП при воздействии на него влаги или повышенной температуры. Существует два варианта, которые описывают количество формальдегида в плитах, класс Е1 и Е2.
Первый вариант — более безопасен и чаще всего применяется при обустройстве помещений жилого назначения. Стандарт изготовления плит класса Е1 допускает содержание в ста граммах плиты не более десяти грамм формальдегида. Именно данные плиты используются при изготовлении мебели, предназначенной для детей.
Второй класс Е2 обозначает тот факт, что сто грамм плиты содержит около тридцати граммов формальдегида. Менее популярный вариант, который практически не используется в жилых помещениях, из-за токсичности.
Сфера применения ДСП чаще всего связана со строительством. Данный материал часто используется при проведении внутренних отделочных работ, в процессе изготовления дверных конструкций, основ под потолок или пол.
ДСП шпунтованная влагостойкая для пола — характеристика
Как говорилось ранее, ДСП является материалом, который изготавливается с помощью метода горячего прессования. Именно поэтому, ДСП практически не склонна к расширению. Для более удобного соединения плит между собой производители изготавливают плиты с наличием на них двух паз и двух гребней, которые обеспечивают ровность и плотность их соединений.
При установке такого рода ДСП практически не требуется никакой инструмент, а время монтажных работ значительно уменьшается. Кроме того, влагостойкое ДСП для пола содержит в своем составе специальные добавки в виде влагоустойчивых полимеров. Именно они позволяют применять этот материал в комнатах со средним уровнем влаги, таким как кухня или балкон.
Среди преимуществ шунтированного ДСП для пола выделяют:
- легкость установки. которая обеспечивается благодаря наличию шипо-пазового соединения;
- наличие идеально ровной поверхности, на которой отсутствуют перепады, зазоры и другие дефекты;
- простота работы с материалом;
- возможность использования в помещениях с повышенным уровнем влажности;
- хорошие эксплуатационные свойства.
Именно замковый тип ДСП позволяет обустроить отличный пол плавающего типа. Кроме того, с помощью данного материала возможно соорудить фальш пол или сухую сборную стяжку, без использования раствора или дополнительных строительных материалов.
В соотношении с размерами ДСП для пола различают плиты 1,5х4, 1,5х6, 1,5х8 м и так далее. Толщина ДСП для пола составляет 1, 1,8, 2, 3 см.
Укладка полов ДСП: как соорудить черновой пол
Черновое напольное покрытие еще называют сухой стяжкой, так как в процессе его обустройства не используются материалы, в состав которых входит вода. Именно черновой пол является базовым основанием на которое производится установка основного напольного покрытия.
Инструкция по выравниванию пола ДСП:
1. На бетонное основание производится установка лаг, интервал между которыми составляет 300-400 мм, в том случае если толщина листа не более 1,6 см и 400-600 мм, при установке листов толщиной в 2,2 см. Учтите, что возле стен оставляется зазор в 20 мм. При наличии неровного пола, все просветы следует заполнить с помощью песка или шлака.
2. Если пол находится на первом этаже, то все пространство между лагами заполняется с помощью утеплителя пенопласта или пенополистирола. Учтите, что в таком случае на бетонное основание предварительно укладывается пароизоляция.
3. С помощью строительного уровня проверьте горизонтальность основания. Для того, чтобы пол не скрипел в процессе его эксплуатации необходимо использовать строительный пластик или бумагу, которой накрывается поверхность.
4. Начинайте укладывать ДСП от стены, расположенной в дальнем углу комнаты. Уложите первый и зафиксируйте его на полу с помощью саморезов. Сначала фиксируется центральная часть листа, шаг установки крепежей составляет около двадцати сантиметров. Старайтесь утопить шляпки саморезов минимум на один миллиметр.
5. Чтобы герметизировать кромки промажьте шипо-пазовые соединения с помощью клея ПВА или строительной мастики на основе из латекса.
6. Далее устанавливается следующая плита и плотно прижимается к поверхности предыдущей. Во избежание повреждения материала в комплекте с ДСП идут бруски, которые предназначенные для его подгонки.
7. Затем производится монтаж следующих брусков. Они устанавливаются таким образом, чтобы швы между ними находились непосредственно на лагах. Если обустраивается пол узкого коридора, то каркас располагается перпендикулярно по отношению к движению.
8. При образовании вертикальных неровностей они шлифуются и очищаются от пыли и грязи. Далее производится чистовая отделка пола, предполагающая монтажные работы по установке покрытия из ламината, линолеума, кафеля или паркетной доски.
Покрытие полов ДСП: как обустроить плавающий пол
Обустройство плавающего пола предполагает отсутствие жесткой связи между плитами, устанавливаемыми на полу. Таким образом, производится формирование промежуточного слоя, который позволяет обеспечить тепло- и звукоизоляцию пола.
Использование данной технологии связано с обустройством полов, имеющих сильные изъяны и перепады. Для обустройства плавающего пола из ДСП следует выполнить такие действия:
1. Уложите пароизоляцию на основу из бетона. Если же основной пол выполнен из дерева лучше всего воспользоваться пергамином.
2. Насыпьте наполнитель в виде сухого керамзита или шлака. Произведите его выравнивание и разравнивание.
3. Установите материал в виде строительной мембраны или бумаги.
4. Возле стены, которая является началом монтажа следует установить клинья.
5. Начните установку ДСП, в процессе выполнения работ используйте клей, который поможет соединить плиты между собой.
6. Позаботьтесь о наличии интервала между стеной и ДСП размером в один сантиметр.
Установка ДСП на бетонное основание
Существует два способа монтажа ДСП на основание выполненное из бетона:
- монтаж непосредственно на пол;
- установка на лаги.
Первый вариант представляется возможным лишь в том случае, если пол, выполненный из бетона является идеально ровным и не имеет перепадов по горизонтали.
Если на полу имеются небольшие неровности, то предварительно его заливают тонко стяжкой. Для отстаивания стяжки следует подождать минимум 3-4 недели. После того как бетон станет прочным, основание очищается от пыли и грязи с помощью строительного пылесоса. Листы ДСП раскраиваются в соотношении с размером помещения.
Совет: Перед началом монтажных работ рекомендуется нанести на поверхность листов ДСП олифу или антисептик, улучшающие его эксплуатационные характеристики.
На основании следует провести работы по его разметке. В соотношении с разметкой в бетоне просверливаются отверстия, в которые будут установлены дюбели. Уложите лист таким образом, чтобы получить зазор в 15 миллиметров. Для фиксации материала на бетонном основании используйте дюбеля.
Второй вариант укладки ДСП предполагает выполнение таких действий:
1. Выбор толщины ДСП зависит от шага с которым были установлены лаги. Учтите, что ДСП более хрупкий материал, чем например фанера или дерево, поэтому лаги должны располагаться вблизи друг друга.
2. Обустройство стяжки, при выборе данного метода является необязательным. В таком случае, нет необходимости тратить время и лишние материальные средства для ее изготовления.
3. Для того, чтобы компенсировать неровности, образовавшиеся в процессе обустройства лаг, под них подкладываются небольшие части фанеры или дерева.
4. Сначала следует разметить основание в соотношении с местами расположения лаг. Уложите лаги таким образом, чтобы шаг их укладки был одинаковым.
5. Далее в пространстве между лагами производится укладка утеплителя. С помощью анкеров лаги фиксируются на полу.
6. Уложите утеплитель, лучше всего подойдет минеральная вата. Она должна плотно прилегать к лагам. Все щели, которые образовались между слоем утеплителя и минеральной ваты заделываются с помощью монтажной пены.
7. Далее производится монтаж гидроизоляции, в виде фольги или клеенки. Довольно приемлемым вариантом станет использование пенофола, который сыграет роль не только гидро-, но и теплоизоляции.
8. Затем производится непосредственная установка ДСП, которые фиксируются на полу гвоздями.
материалов | Бесплатный полнотекстовый | Влияние структуры ДСП на ее физические и механические свойства
1. Введение
Отрасль первичной обработки древесины является крупнейшим получателем древесных отходов. Однако даже в высокоразвитых и промышленно развитых странах конечный продукт в виде пиломатериалов, размещаемых на рынке, составляет лишь 50% обработанной древесины. Остальные 50% составляют так называемые материальные потери, из которых 16% приходится на опилки и 22% на стружку. Остальные 12% являются результатом потери толщины, вызванной изменениями десорбции.Опилки — это самый тонкий материал, образующийся при пилении, и их форма зависит от используемых режущих инструментов. Чипы бывают немного больших размеров. Их размер во многом зависит от материала, из которого они сделаны. Щепа также производится из других уже фрагментированных материалов, таких как обрезные кромки, поврежденные пиломатериалы, древесные отходы или отходы, образующиеся при формировании сваи.

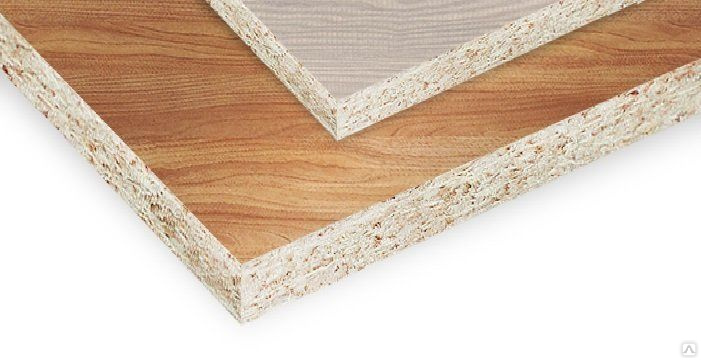
Таким образом, целью данного исследования было определить возможность использования стружки в качестве замены стружки, предназначенной для внутреннего слоя мебельных ДСП. Предлагаемое решение может способствовать снижению затрат на производство плит за счет использования необработанного материала. Интенсивность сортировки будет сведена к минимуму, а операция измельчения будет исключена.
2. Материалы и методы
В исследовании использовалась древесная щепа, полученная путем дробления большей части окоренного древесного материала (Pinus Sylvestris L.), и опилки, образующиеся в процессе лесопильной обработки. Стружку, оставшуюся на сите 50 × 50 мм, предварительно отсортировали и вручную удалили большие куски коры, прошедшие через это сито. Опилки собирали непосредственно из резервуара для ежедневного сбора материала от всего потока обработки древесины.Таким образом, опилки содержали материал, полученный как распиловкой, так и строганием. Весь древесный материал подвергали фракционному анализу и сушили до содержания влаги примерно до 3,5% перед прессованием. Материал сушили в лабораторной барабанной сушилке при 120 ° C (на входе) –110 ° C (на выходе). Процесс продолжался до достижения предполагаемой влажности.
Оба типа частиц были склеены с помощью смолы MUF (меламин-мочевина-формальдегид), полученной от Pfleiderer Silekol Sp. z o.o. Аммиачная селитра (20%), добавленная при 1.5% от сухой массы смолы использовали в качестве отвердителя для смолы MUF. Стружку и опилки приклеивали отдельно. Степень приклеивания стружки составляла 6%, опилок добавлялось к древесно-опилочным плитам на уровне 8%.


3. Результаты и обсуждение
С точки зрения размеров и фракционного состава стружка была типичной для тех, что образуются как отходы лесопиления (Таблица 1). Они содержали большую долю относительно мелкой фракции (менее 18 мм). В таком виде их можно было использовать в основном для производства ДСП. Их немаловажным преимуществом было минимальное содержание коры. Материал, определяемый как опилки, содержал фракцию осколков размером 4 мм или более и более мелкую фракцию менее 2 мм, включающую древесную пыль, очень мелкие опилки и волокнистую стружку (Таблица 2).Фракция 2 и 2,5 мм представляла собой смесь щепок и крупных опилок, причем преобладали последние. В целом материал состоял из 34% древесной щепы, 36% опилок и 30% древесной пыли. Это невыгодный состав с технологической точки зрения. Из-за своей огромной внешней площади древесная пыль и мелкие опилки могут впитывать значительное количество клея. Фактически, только древесные частицы в виде стружки являются желательным компонентом для производства плит.
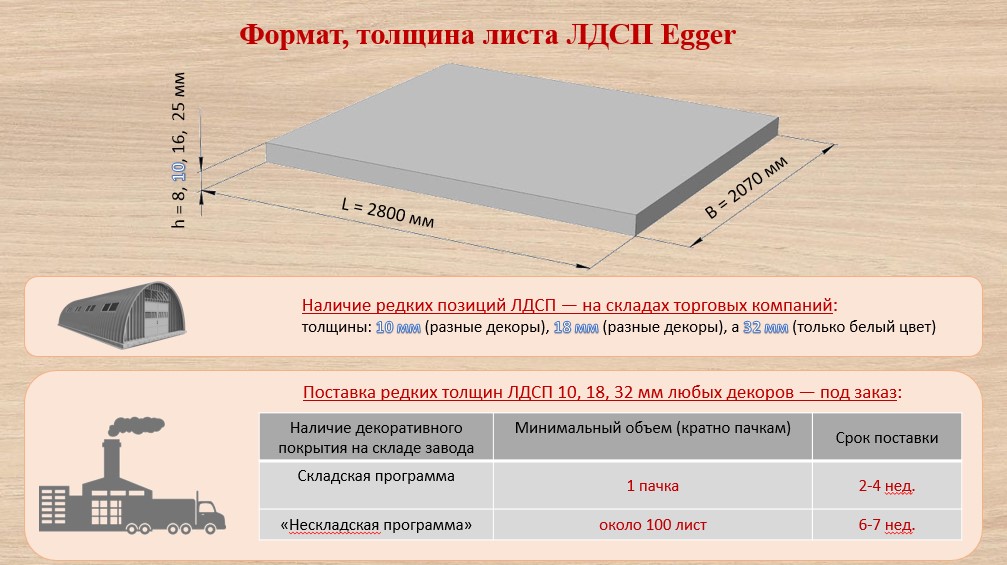
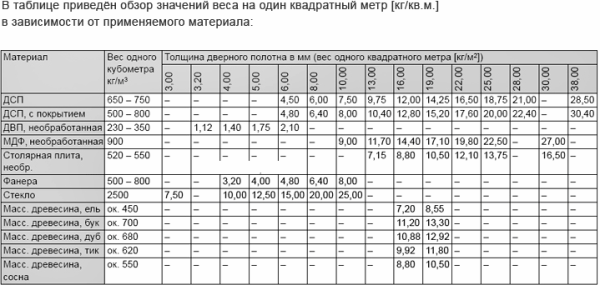
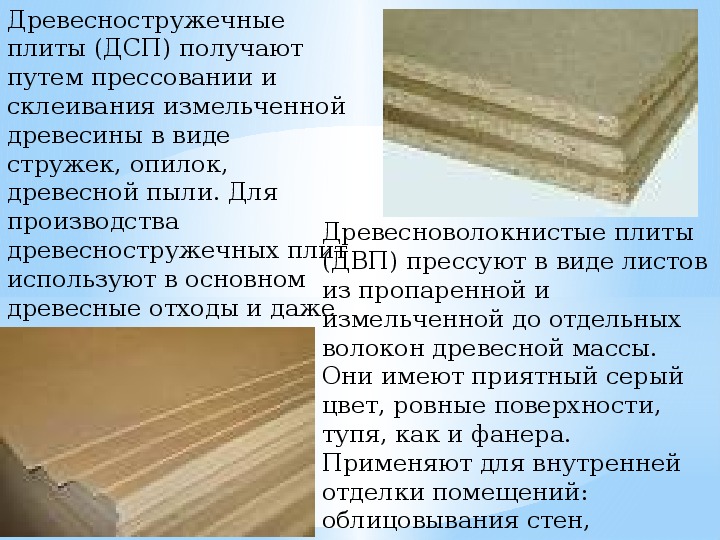
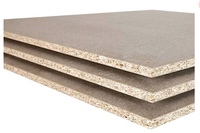
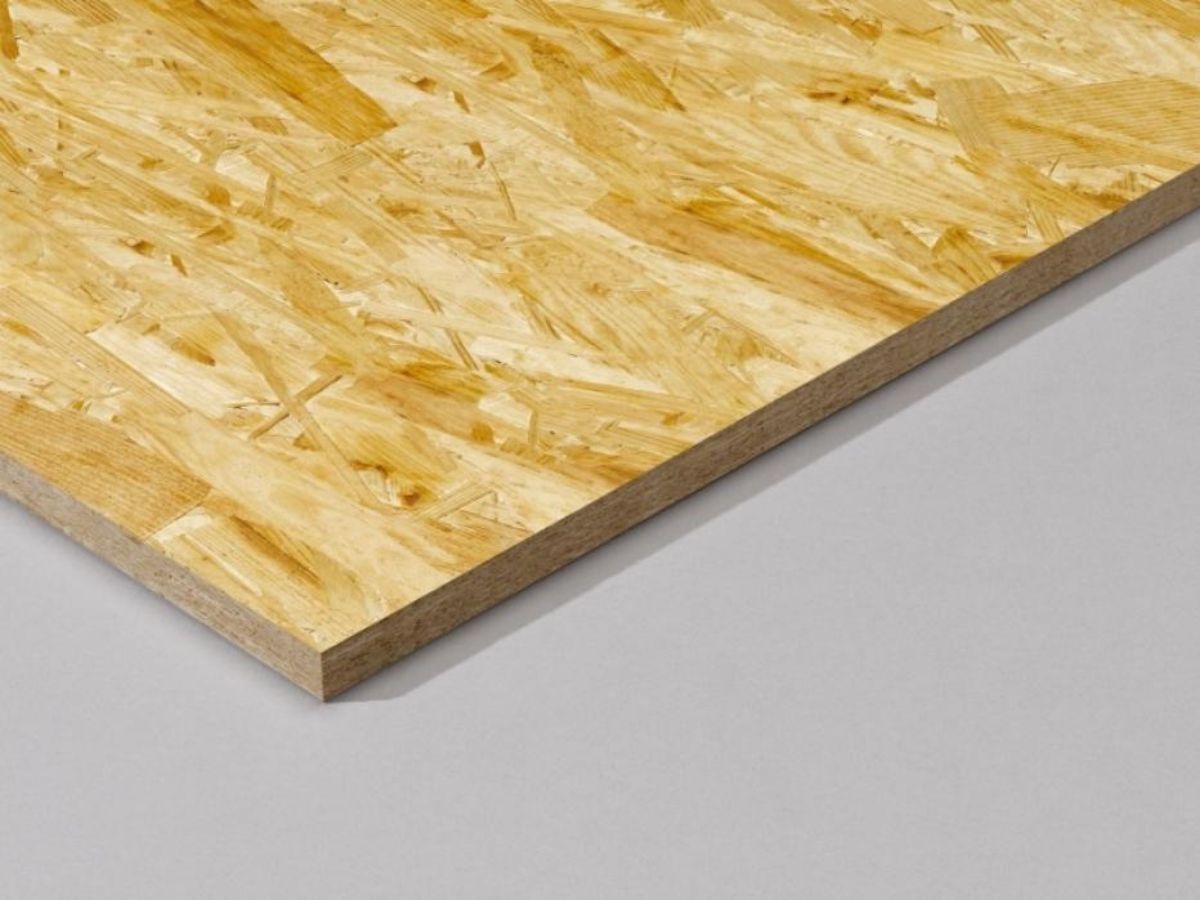
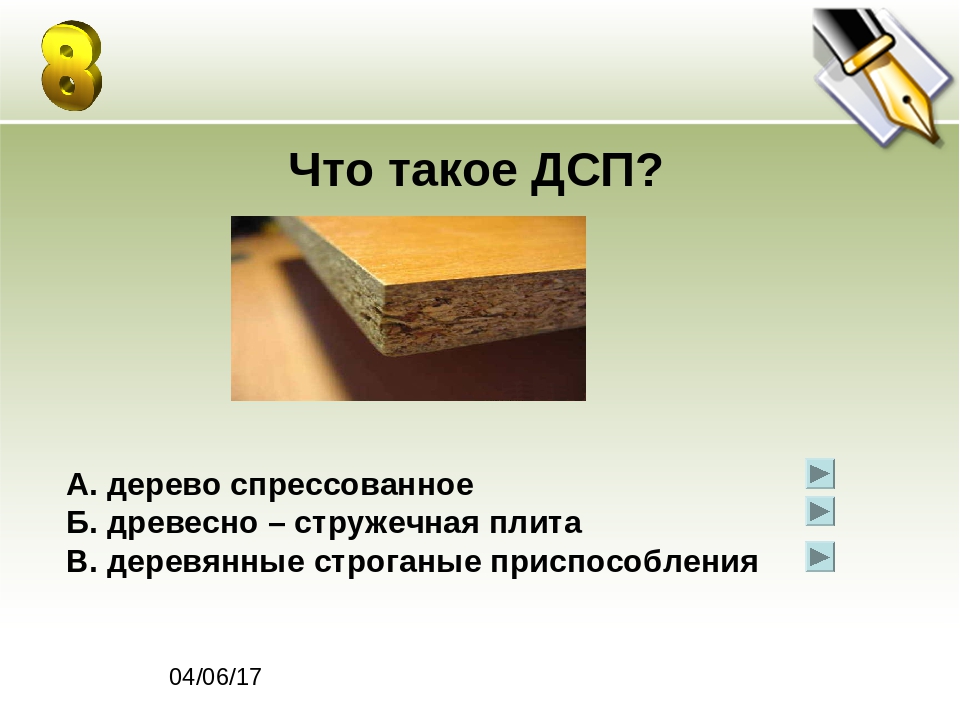
Eef = 1Jx ∑i = 13Ei [Jxi + Ai (di) 2]
(1)
Экспериментальные доски оценивали в соответствии с EN 310.Полученные свойства представлены в таблице 6. Собранные в ней данные ясно показывают, что модуль упругости тонких однослойных плит значительно различается. Результат ANOVA p = 0,01878 был ниже предполагаемого уровня значимости = 0,05 (F (3,52) = 3,6278, p = 0,01878). Однако более подробный анализ показал, что распределения для отдельных типов плат были похожи, поскольку тесты POST HOC не дали результатов. Тест Тьюки не показал значительных различий в среднем модуле упругости проанализированных досок.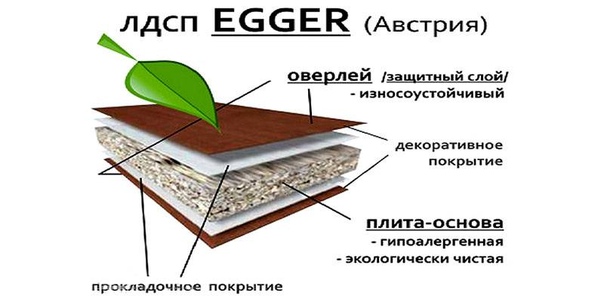


Что такое ДСП и для чего используется
Лаконичный и невероятно универсальный, ДСП является одним из наиболее широко используемых листовых материалов в мире, предлагая доступные и удобные решения для многих домашних нужд и строительных нужд.Но что такое ДСП и для чего его можно использовать? Если вы ищете листовые материалы для своего следующего проекта своими руками, читайте дальше, чтобы узнать, может ли ДСП стать идеальным материалом для работы.
Что такое ДСП?
ДСП — также иногда называемое ДСП или ДВП низкой плотности — изготавливается путем смешивания небольших древесных частиц с эпоксидной смолой, которые спрессовываются вместе под сильным нагревом и давлением для получения жесткой плиты, обычно с гладкой поверхностью. ДСП выпускается с различной плотностью для различных нужд и применений, в том числе с низкой, средней и высокой плотностью. ДСП с более низкой плотностью довольно мягкие и податливые, тогда как древесно-стружечные плиты с более высокой плотностью более жесткие и могут использоваться для более тяжелых условий эксплуатации.
ДСП как листовой материал имеет различные достоинства и недостатки. Основными преимуществами, конечно же, являются рентабельность и универсальность использования ДСП. Основным недостатком является то, что необработанная ДСП является пористой и поэтому впитывает воду, с которой соприкасается.Это верно для всех сортов ДСП, даже с самой высокой плотностью, поэтому важно, чтобы необработанная ДСП оставалась сухой и обработанной, чтобы предотвратить впитывание воды и разбухание, поскольку это сделает плиту непригодной для использования. К счастью, ДСП очень легко обрабатывать и покрывать водостойкими фанерами, меламиновыми покрытиями и лаками, чтобы сделать их более прочными.
Для чего используется ДСП?
В зависимости от плотности, ДСП применяют для самых разных внутренних строительных и отделочных работ.ДСП высшей плотности используются для производства таких вещей, как:
- Кухонные столешницы (покрытые меламином)
- Основные конструкции кухонных шкафов
- Полы и изоляция пола / подложка
- Плоская мебель (обычно покрытая шпоном)
- Строительная изоляция
Более мягкая древесно-стружечная плита меньшей плотности также часто используется для:
- Внутренние элементы мебели (например, днища ящиков, спинки шкафов и
- Внутренние акценты дома e.грамм. накладки и молдинги вокруг окон и дверей
- Звукоизоляция и звукопоглощение (например, динамики и стены и пол концертного зала)
- Упаковка
Звучит ли ДСП как материал, который вам нужен для вашего следующего проекта? Вот несколько быстрых советов о том, как работать с этой универсальной доской, в том числе о том, как безопасно ее резать и красить.
Как резать ДСП
Как и большинство древесных материалов, ДСП лучше всего подходит для резки любой механической пилой, такой как ленточная пила, настольная пила, циркулярная пила или лобзик.Из-за особого характера древесно-стружечной плиты мы не рекомендуем вам пытаться резать древесно-стружечную плиту с помощью ручной ручной пилы, поскольку это приведет к очень грубым краям и неточной обработке поверхности.
Если вы режете необработанную древесно-стружечную плиту, процесс резки очень прост. Однако, если вы режете ДСП с фанерным или меламиновым покрытием с одной стороны, лучше всего разрезать доску так, чтобы сторона с покрытием была направлена вверх, поскольку пила может оставить неровный край на нижней стороне, что не будет выглядеть очень привлекательно.
В соответствии с примечанием по технике безопасности , всегда надевайте респиратор на рот и нос при резке ДСП, чтобы защитить от вдыхания любой мелкой пыли и эпоксидных химикатов, выделяемых из плиты.
Как покрасить и запечатать ДСП
ДСПможет быть очень универсальным и экономичным, но его может быть сложно покрасить и обработать, если вы не знакомы с правильным процессом. Вот основные шаги, как покрасить ДСП и заклеить его; идеально, если вы планируете строить своими руками из ДСП.
1. Подготовить ДСП
ДСП не покроет вашу краску, если она не будет полностью чистой, без масляных пятен и частиц пыли. Надев перчатки, начните с тщательного осмотра поверхности ДСП и сотрите масляные пятна тканью, смоченной водой с жидкостью для мытья посуды (обязательно отожмите ее, чтобы она была влажной, чтобы не пропитать доску). Неплотно накройте доску защитной пленкой, чтобы защитить ее от дальнейшей пыли и мусора, и оставьте в хорошо проветриваемом помещении для полного высыхания на два дня, прежде чем переходить к следующему шагу.
2. Отшлифуйте доску
Используя кусок наждачной бумаги средней зернистости (или электрическую шлифовальную машину для больших площадей доски), отшлифуйте всю доску, чтобы удалить любые дефекты поверхности. Шлифовка до получения гладкой поверхности также облегчит прилипание герметика и краски к доске. После того как вы отшлифовали всю доску, протрите ее сухой тканью и удалите все оставшиеся частицы.
3. Загрунтовать ДСП
Грунтование ДСП создает защитный слой от влаги и грязи, а также создает лучшую поверхность для прилипания краски.Для начала положите доску на защищенную поверхность в хорошо проветриваемом помещении и убедитесь, что вы надели перчатки перед началом, так как вы не хотите, чтобы эти вещества попали на кожу.
Используя гладкий малярный валик, нанесите грунтовку тонким ровным слоем и дайте ей полностью высохнуть в соответствии с инструкциями к выбранной грунтовке. Повторите два или три раза, чтобы создать несколько слоев грунтовки, так как эти слои будут прилипать друг к другу и обеспечивать более прочный, более защитный барьер, чем вы получили бы с одним слоем.
4. Начните красить ДСП
Теперь ДСП готово к покраске. Лучшим типом краски для ДСП является акрил или любая краска без тяжелой воды или масла. Краски, содержащие слишком много воды или масла, могут впитаться в пористую поверхность ДСП даже при грунтовании, создавая неровную поверхность. Используя свежий малярный валик, нанесите краску ровными слоями, как и с грунтовкой. Дайте полностью высохнуть перед нанесением следующего слоя — вам может потребоваться три или четыре слоя, прежде чем вы достигнете желаемого уровня покрытия.
5. Закройте ДСП
Когда краска высохнет, пора заклеить ДСП. Герметизация доски защитит вашу краску от повреждений и придаст ей привлекательный глянцевый вид, а также добавит дополнительный защитный барьер от влаги. Найдите прозрачный герметик, подходящий для ДСП, и нанесите ровным слоем чистым валиком. Дайте первому слою высохнуть, а затем нанесите второй слой для большей точности.
И все! Вот как красить ДСП — просто, когда знаешь как.
Если вы ищете прочную высококачественную древесно-стружечную плиту для вашего следующего напольного покрытия или создания мебели, ознакомьтесь с нашим ассортиментом ДСП для пола и мебели здесь, в компании Arnold Laver, чтобы начать работу.
ДСП — обзор
3.10.4.2 ДСП
Ежегодно в Европе производится около 28,4 млн. М 2 3 древесностружечных плит в основном для мебели и строительства (Klímek et al. , 2016). Дерево является основным сырьем, используемым для этой цели, хотя возможность использования недревесных альтернатив изучается в течение многих десятилетий.В последнее время многие факторы, в том числе нехватка древесины, экологическая осведомленность и низкая стоимость недревесных материалов, стимулировались не только интенсификацией этих исследований, но и серьезными последствиями для отраслей.
В 2005 году по крайней мере 30 промышленных предприятий во всем мире интегрировали использование недревесных лигноцеллюлозных агрегатов в производство древесностружечных плит (Bektaş et al. , 2005). Сегодня, хотя техническая осуществимость недревесных древесностружечных плит общепринята (Bajwa et al., 2015), необходимы дальнейшие исследования, чтобы полностью понять, как внутренние свойства сырья могут способствовать повышению общих характеристик разработанных материалов. Подавляющее большинство примеров разработок недревесных древесностружечных плит сосредоточено на использовании различных видов натуральных волокон. Это согласуется с тем фактом, что волокна вносят важный вклад в улучшение механических свойств плит. Волокнистые материалы из сельскохозяйственных культур предпочтительны из-за их доступности и легкости доступа.Примерами являются солома (из пшеницы, ячменя, риса и т. Д.), Хлопковый джин или жмых, волокна кокосового волокна и кенафа или банана. Были проведены некоторые исследования, в которых оценивались растения, богатые растительной сердцевиной; однако примеры использования изолированной растительной сердцевины при производстве древесностружечных плит встречаются редко.
Хорошо известно, что размер и форма частиц влияют на свойства древесностружечных плит. Агрегаты сердцевины растений имеют тенденцию к формированию довольно сферических частиц (Magniont, 2010; Palumbo, 2015, 2015a, b).Как правило, более сферические частицы положительно влияют на внутреннее связывание ( IB ), но пагубно влияют на MOR и MOE, которым больше выгодны более длинные частицы или волокна (Bajwa et al. , 2015; (Klímek et al. al. , 2016). Действительно, наличие растительной сердцевины, как сообщается, оказывает негативное влияние как на MOE, так и на MOR (Balducci et al. , 2008; Klímek et al. , 2016).
С другой стороны. С другой стороны, когда растительная сердцевина измельчается вместе с волокнистыми тканями растений, получается смесь сферических и удлиненных частиц (Nozahic et al., 2012). Такие смеси не могут компактно укладываться в плиты, что резко снижает плотность и IB (Bajwa et al. , 2015). Такой недостаток может быть компенсирован уменьшением размера частиц, увеличением целевой плотности древесностружечных плит, уменьшением толщины плиты (Klímek et al. , 2016) или эффективным удалением растительной сердцевины перед формированием плиты.
Salvado et al. Компания (2003) произвела экспериментальные древесноволокнистые плиты без связующего на основе мискантуса ( Miscanthus sinensis, ). После уборки стебли мискантуса очищали и измельчали. Стружку взорвали паром с помощью процесса термомеханического водного пара в реакторе периодического действия для получения пульпы. Полученный материал сушили, слегка измельчали и использовали для производства древесноволокнистых плит. Были определены предварительная обработка и условия прессования, которые оптимизируют физико-механические характеристики. Полученные плиты показали довольно хорошие результаты: модуль упругости до 7630 МПа, MOR до 61 МПа, внутреннее сцепление до 4.1 МПа, набухание по толщине всего 2,5% и водопоглощение всего 8,9%. Средняя плотность досок составила 1240 кг / м 3 . Ниже 1100 кг / м 3 плиты не соответствовали требованиям MOR, установленным в EN 31094.
Bajwa et al. (2015) оценил возможность использования рогоздов для производства древесностружечных плит для коммерческого использования. ДСП на основе соломы и рогоза, скрепленные 3% полиметилендифенилдиизоцианата ( pMDI ), были изготовлены с использованием пресса с горячей плитой (190 ° C и 1 ° C). 54 МПа за 420 с). Целевая плотность поддерживалась на уровне 480 кг / м 3 , а доля рогоза и пшеничной соломы варьировалась между 100%, 50% и 25% для получения четырех различных рецептур. Рогоз (как стебли, так и листья) и солома использовались в виде щепок размером от 2 до 6 см. Было обнаружено, что добавление рогоза привело к улучшению общих свойств по отношению к 100% -ной соломе. Однако не самые лучшие результаты показали и экземпляры 100% рогоза.Наилучшие результаты были получены для смесей, состоящих из 70% рогоза и 25% соломы, которые показали превосходную среднюю жесткость на изгиб (MOE 446,3 Н / мм 2 ), прочность на изгиб (MOR 17,95 Н / мм 2 ) и внутреннее сцепление. и меньшее водопоглощение и набухание по толщине. Кроме того, разброс результатов измерений был ниже, чем для остальных составов. Слабое связывание между частицами соломы из-за присутствия кутикулярного воскового слоя было сочтено причиной плохих результатов, полученных для древесностружечных плит на основе соломы, в то время как плохие результаты, полученные для 100% образцов рогоза, объяснялись потерей плотности упаковки случайно организованные частицы.
По мнению авторов, использование смесей заполнителей рогоза и соломы для производства древесностружечных плит возможно, и следует ожидать лучших результатов, если содержание влаги и размеры частиц двух заполнителей совпадают.
Binici et al. (2016) разработали композиты на основе кукурузных початков и проанализировали влияние размера частиц и соотношения матрица / заполнитель на термические, механические и звукоизоляционные свойства плит. Кукурузные початки измельчали с помощью молотка и просеивали до частиц размером от 1 до 1 мкм.6 и 6,3 мм и смешанный с эпоксидной смолой, добавленный в пропорции 50% и 75% и прессованный в течение 1 мин при комнатной температуре и переменном давлении (от 0,07 до 0,27 МПа). Полученные материалы имели плотность от 250 до 410 кг / м 3 и теплопроводность от 0,159 до 0,075 Вт / мК. Было обнаружено, что давление является основным движущим фактором, влияющим на анализируемые свойства: более высокое производственное давление привело не только к более высокой плотности и, следовательно, к лучшим механическим свойствам, но также к более высокой теплопроводности и звуковой проводимости.
Klímek et al. (2016) в качестве сырья для производства использовали два растения с богатой костной растительностью, подсолнечник ( Helianthus annuus ) и топинамбур ( Helianthus tuberosus ), а также третье недревесное растение, чашечное растение ( Silphium perfoliatum ). ДСП. Смолы MDI и UF использовались в качестве связующих веществ. Растительный материал измельчали с помощью молотка и просеивали для получения агрегатов размером 5 и 1,24 мм. Было проанализировано соотношение сторон (отношение длины / ширины) агрегатов.В то время как топинамбур и чашечное растение образовывали довольно удлиненные частицы, частицы подсолнечника были «кубиками», вероятно, из-за меньшего количества волокнистых тканей и / или более низкого лигнификации пучков волокон. Разброс по размерам в заполнителях оказался выше, чем в древесной щепе. Агрегаты смешивали со смолами в барабанном смесителе с использованием распылительной насадки. MDI был добавлен в количестве 4% и 6%, а UF — в количестве 8% и 12%. Маты предварительно прессовали вручную перед горячим прессованием при 200 ° C и 3,2 МПа в течение 100 с до расчетной плотности 600 кг / м 3 , что является обычной плотностью для мебельного применения.Между тремя используемыми видами сырья были обнаружены небольшие различия, хотя плиты на основе чашечных растений дают несколько лучшие результаты. Напротив, тип и количество связующего играют более решающую роль. Наиболее благоприятные результаты были получены с MDI 6%. Хотя полученные плиты соответствовали механическим требованиям класса EN 312 P1 (использование в сухих условиях), их характеристики (измеренные с точки зрения MOR, MOE, IB, разбухания по толщине и водопоглощения) были хуже, чем у обычных древесно-стружечных плит.
Bektas et al. (2004) разработали трехслойные ДСП из стеблей подсолнечника ( Helianthus annuus ) и древесины тополя ( Populus alba ). Соотношение частиц из древесины или подсолнечника составляло 100%, 75%, 50% и 25%. Смеси заполнителей, просеянные на 1,5 мм для среднего слоя и 0,8 мм для поверхностного слоя, были связаны с UF (9% для среднего слоя и 11% для поверхностного слоя) и катализатора (1% хлорида аммония). горячего прессования (24–26 МПа и 150 ° C в течение 7 мин) для формования ДСП конечной плотностью 700 кг / м 3 .Были проанализированы свойства, связанные с влажностью (набухание по толщине и водопоглощение), механические свойства (внутренняя связь, модуль упругости и MOR) и способность удерживать винты панелей. Все полученные древесно-стружечные плиты соответствовали требованиям, установленным в стандарте EN 312 для общего использования. Однако эффективность всех досок, содержащих стебли подсолнечника, была ниже, чем у 100% образцов древесины тополя. Композит из стеблей подсолнечника показал худшие характеристики.
Balducci et al. (2008) отобрал различные части культурных растений, богатые растительной сердцевиной, такие как подсолнечник, топинамбур, мискантус, стебли кукурузы и костры конопли, с целью производства легких древесностружечных плит. Однослойные и трехслойные древесно-стружечные плиты, связанные с 6% pMDI и UF смолами, характеризовались механическими и влагозависимыми свойствами. Ориентиром послужили ДСП из дерева. Растительный материал был разрезан и обработан молотком для получения агрегатов.Сердцевина и коры использовались вместе. Типичный размер частиц не упоминается; однако авторы сообщают о важных различиях в форме и плотности полученных частиц. Агрегаты смешивали со смолой и прессовали до целевой плотности 400 или 600 кг / м 3 . Было обнаружено, что плотность является основным фактором вытяжки, влияющим на исследуемые свойства. Легкие плиты не соответствовали требованиям P2 (EN 312, плита для внутреннего использования, включая мебель, в сухих условиях), в отличие от большинства плит плотностью 600 кг / м 3 , которые соответствовали таким требованиям.При одинаковых плотностях и составах плиты, склеенные pMDI, дают лучшие результаты. Существенных различий между однослойными и трехслойными ДСП по механическим свойствам не обнаружено.
В тех же условиях доски топинамбура имели более высокий IB, чем остальные материалы, тогда как стебли кукурузы показали самый низкий IB.
Характеристики фанеры | Руководства по дому
Универсальность фанеры обеспечила ей важную роль в строительстве, изготовлении мебели и изделиях из дерева, а материал бывает самых разных форм и размеров.Фанера может быть изготовлена из древесины хвойных или твердых пород, и в зависимости от того, как фанера была изготовлена и / или обработана, она может особенно хорошо подходить для использования в самолетах или на море. Некоторые фанеры для декоративного эффекта даже облицованы натуральным деревом. Тем не менее, независимо от типа фанеры, материал имеет набор общих характеристик.
Прочность
Фанера представляет собой ламинат, в котором несколько слоев древесной стружки и стружки уложены друг на друга и склеены. Прочность ламината повышается за счет расположения каждого слоя таким образом, что волокна древесины чередуются, что делает большинство типов фанеры более прочными, чем эквивалентные куски того же самого настоящего дерева. Фанера также примерно в два раза более устойчива к отслоению, чем обычная древесина.
Стоимость
Поскольку фанера изготовлена из древесной стружки и стружки, она может быть получена из частей деревьев, которые не подходят для фрезерования балок, блоков и досок. Как правило, это также делает фанеру дешевле, чем ее эквивалент из натурального дерева, особенно для крупномасштабного применения.
Стабильность
Чередование зерен и использование клея в фанере делает ее такой же стабильной или более устойчивой, чем обычная древесина.Фанера иногда менее склонна к поглощению и / или выделению влаги, и когда это происходит, чередующийся рисунок волокон сопротивляется расширению и усадке. В результате древесина иногда более устойчива к усадке и деформации.
Гибкость
Поскольку фанера является продуктом промышленного производства, ее размер, форма и внешний вид не ограничиваются, как натуральное дерево, от природы. Листы фанеры бывают разной толщины и, как уже отмечалось, с широким диапазоном облицовки. На фанеру с гладким шпоном можно отделывать многие из тех же отделочных материалов, что и для натурального дерева.
Характеристики меламиновой плиты — Фанера
Какие характеристики у меламиновой плиты?
Часто говорят, что для того, чтобы сделать простыню лучшего качества, мы должны идти в ногу с кровью времени. Современные плиты включают эко-плиты, меламиновые плиты, плиты без краски, огнестойкие плиты и т. Д. Плиты из меламина популярны из-за большого объема продаж и очевидных характеристик.Меламиновая плита известна как панели на древесной основе, пропитанные меламином. Бумагу разного цвета или текстуры пропитывают клеями из меламиновой смолы, затем сушат до определенной степени отверждения и укладывают на поверхность ДСП, ДВП средней плотности или твердого ДВП после горячего прессования. Меламиновая плита обладает такими преимуществами, как плоская поверхность, легкая деформация за счет одинакового коэффициента расширения с обеих сторон плиты, яркий цвет, износостойкая поверхность, устойчивость к коррозии и экономичная цена. Дверные панели из меламинового шпона, производимые в Китае, представлены панелями «река роса», и все показатели соответствуют международным стандартам.
Недостатки меламиновой плиты: низкое качество, легкое схлопывание краев, более очевидные следы клея, меньший цвет, не может быть цветок гонга, может быть только прямая кромка.
Меламиновая плита обычно состоит из поверхностной бумаги, декоративной бумаги, покрывающей бумаги и нижней бумаги.
Поверхностная бумага кладется на верхнюю часть декоративной доски для защиты декоративной бумаги.Это делает поверхность доски очень прозрачной после нагрева и прессования. Поверхность доски твердая и износостойкая. Эта бумага требует хорошего водопоглощения, после окунания она чистая и прозрачная. (2) Декоративная бумага, то есть бумага с древесной текстурой, является важной частью декоративного картона. У него есть цвет фона или нет цвета фона. Декоративная бумага, на которой нанесены различные рисунки, помещается под поверхность бумаги, которая в основном играет декоративную роль. Этот слой требует, чтобы бумага имела хорошую укрывистость, пропитку и качество печати.(3) Покровная бумага, также известная как белая титановая бумага, обычно помещается под декоративную бумагу при изготовлении светлой декоративной доски, чтобы предотвратить проникновение фенольной смолы на поверхность. Его основная функция — закрывать цветные пятна на поверхности подложки. Поэтому требуется хорошее покрытие. Вышеупомянутые три вида бумаги были пропитаны меламиновой смолой. (4) Бумага-основа является основным материалом для декоративной доски. Он играет роль в механических свойствах картона. Его получают путем погружения в фенольную смолу и сушки.При производстве можно определить несколько слоев в зависимости от использования или толщины декоративной доски.
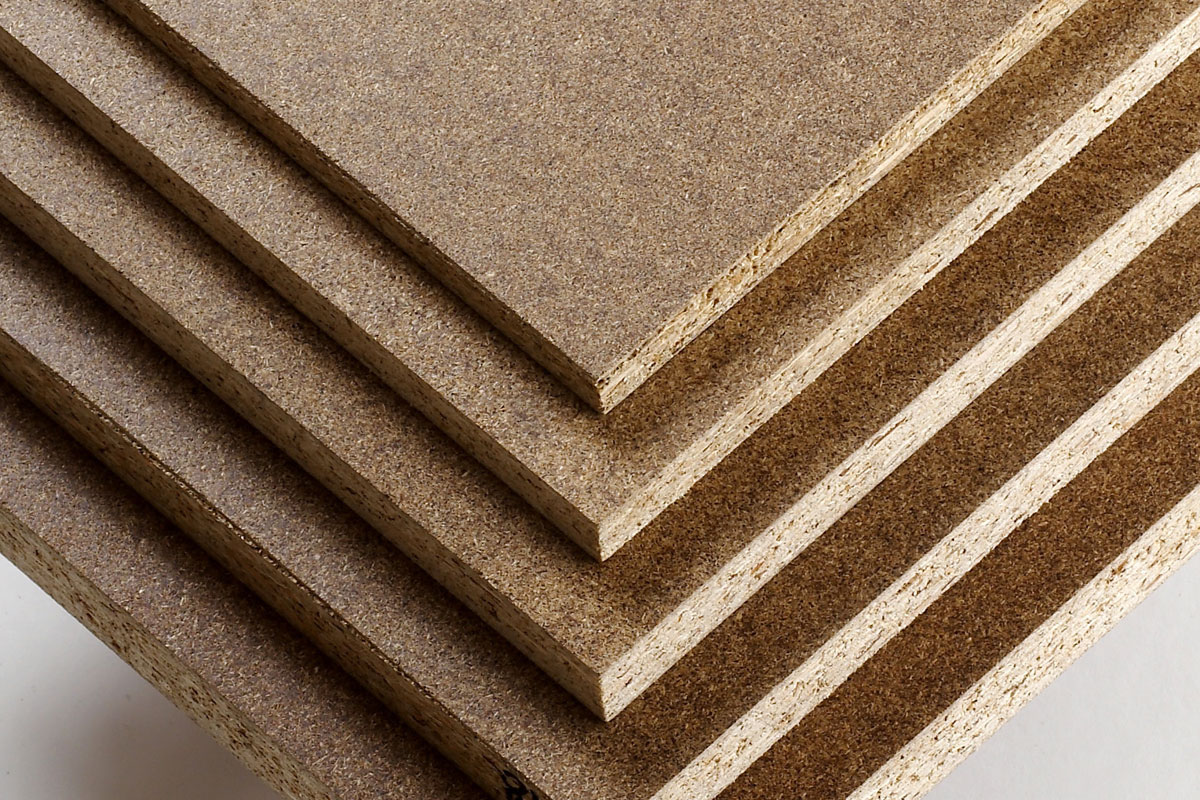
Свойства древесностружечных плит, изготовленных из постиндустриальной фанеры, склеенной УФ и ПФ
Фракционный состав эталонных частиц (P_CL) был следующим: 25.7, 59,1, 13,8, 1,4% для крупных, средних, мелких частиц и пыли соответственно.
В результате измельчения были получены частицы трех типов: подобные промышленным частицам P_CL, осколки и «слоистые частицы» (рис. 1а). Осколочные частицы имели неправильное поперечное сечение и были больше, чем частицы P_CL. «Слоистые частицы» строились из двух или трех связанных слоев. Частицы этого типа были получены путем выдирания фрагментов фанеры без отслоения соседних слоев фанеры.Некоторая часть частиц имела одну или обе поверхности, покрытые затвердевшим клеем (UF — рис. 1b; PF — рис. 1c, d), а также древесными волокнами (рис. 1b, d), что указывало на разрушение древесины по линии соединения при измельчении. Таким образом, очевидно, что прочность как древесины, так и прочности склеивания влияет на морфологию частиц. Во всех исследованных группах были обнаружены частицы с УФ-покрытием, однако частицы с УФ-покрытием преобладали в типе «слоистых частиц». Это явление возникло из-за того, что прочность UF-связки в сухом состоянии была сопоставима с прочностью древесины, в то время как прочность PF была даже выше.Доля «слоистых частиц» была низкой и не оказывала существенного влияния на различия между фракционными составами смесей UF- и PF-связанных частиц.
Частицы, извлеченные из отходов фанеры: a «слоистые частицы», b UF- и древесные волокна с покрытием, c с покрытием PF, d с покрытием PF и древесными волокнами
Стоит отметить, что слой затвердевшего клея является механическим барьером для жидкого клея при вторичном растекании клея (Deppe and Ernst 1996; Lee et al.2002; Pocius 2002).
Фракционные составы частиц P_CL и извлеченных частиц показаны на фиг. 2. Было обнаружено, что гранулометрический состав в каждой смеси был аналогичным, за исключением фракций 25_PF и 38_PF. Статистический анализ фракционных составов не показал существенной разницы между 10_UF и 10_PF, а также между смесями 14_UF и 14_PF. Таким образом, очевидно, что тип связующего не повлиял на фракционный состав извлеченных частиц.Поэтому измельчитель древесины, оснащенный ситами 25 и 38 мм, применялся только для измельчения фанеры, склеенной ПФ. Фракция 2,00 мм составляла большую часть (30,5–41,2%) как промышленного P_CL, так и извлеченных частиц. В смеси 38_PF преобладала фракция 10,00 мм (28,8%).
Фракционный состав промышленных частиц (P_CL) и частиц, извлеченных из отходов фанеры
Использование сита с размером ячеек 14 мм в измельчителе позволило получить гранулометрический состав, аналогичный таковому у промышленных частиц P_CL.В полученной смеси крупные, средние и мелкие частицы составили 27,4, 56,4, 14,3 и 1,9% пыли соответственно. С другой стороны, использование сита с ячейками 10 мм привело к образованию 14,6, 63,8, 19,3% крупной, средней и мелкой фракции соответственно и 2,3% пыли. Такое распределение по размерам указывает на то, что использование более плотного сита дает более высокую долю более мелких фракций. Из литературы общеизвестно, что древесностружечные плиты, содержащие большое количество мелких частиц и пыли, обладают более низкими физико-механическими свойствами (Nemli et al.2007; Sackey et al. 2008 г.).
В смесях 25_PF и 38_PF было в 2 и 2,5 раза больше крупных частиц, соответственно, по сравнению с эталонными промышленными частицами P_CL. Для сит 25 или 38 мм содержание пыли было снижено до 0,4 и 0,5% (смеси 25_PF и 38_PF соответственно).
Распад фанеры происходит в зазоре между ножом и контрножом. Поскольку зазор был установлен на уровне 2,21 мм и оставался постоянным, фактором, влияющим на размер получаемых частиц, был размер ячеек сита.Таким образом, очевидно, что измельчение постиндустриальной фанеры на ситах с большими ячейками привело к снижению содержания пыли и мелких фракций, а также к увеличению содержания крупных частиц.
Влагосодержание и насыпная плотность извлеченных частиц представлены в таблице 3. Насыпная плотность промышленных частиц составила 193 кг / м. 3 при содержании влаги 6,7%. Объемная плотность извлеченных частиц была значительно выше, чем у промышленных эталонных частиц P_CL.Значения, определенные для смесей, изготовленных с ситами 10 и 14 мм, были выше на 66 и 58% соответственно. Повышенная объемная плотность восстановленных частиц может быть объяснена уплотнением шпона во время производства фанеры, а также содержанием отвержденных связующих в материале (Wang et al. 2006). Объемная плотность также зависит от формы и размеров частиц, так что мелкие частицы и пыль более плотно упаковываются в единицу объема. Также постулируется, что на характеристики полученных частиц повлияло низкое содержание влаги в отходах фанеры (5.8–7,5%), что облегчило дополнительное измельчение за счет трения между частицами в камеру измельчения. Поэтому выделялось значительное количество пыли и мелких фракций.
Более высокая насыпная плотность восстановленных частиц может быть преимуществом для процесса прессования мата, поскольку в единице объема мата будет присутствовать меньшее количество частиц, а общий объем пустого пространства в мате будет больше. Таким образом, передача тепла в сердцевину мата будет проще и быстрее, что может привести как к изменению реологических свойств древесных частиц, так и к профилю плотности плиты (Болтон и др., 1989; Хамфри и Болтон, 1989; Хата и др., 1990; Томен и Хамфри 2001).
Результаты показывают, что частицы 14_UF и 14_PF проявляют свойства, наиболее близкие к свойствам промышленных частиц серии P_CL. Таким образом, эти две марки были использованы для изготовления картона. Было обнаружено, что смесь частиц, используемая в центральном слое (I – V), не влияла на кривые давления мата, кривую температуры сердцевины мата или кривую толщины мата.Таким образом, тип связующего (УФ, ПФ) не был фактором, влияющим на прессование мата. Типичные изменения параметров в реальном времени показаны на рис. 3.
Рис. 3Кривые давления, температуры сердцевины мата и толщины мата, записанные в реальном времени при прессовании
Содержание рекуперированных частиц в смеси не повлияло ни на кривую давления, ни на толщину мата по сравнению с эталонными, так что заданная толщина плиты (16 мм) была достигнута за 20–25 с.
Стоит отметить, что количество восстановленных частиц увеличивало динамику теплообмена. В результате заданная температура сердцевины мата была достигнута за более короткое время. Принимая во внимание феноменологию, описанную Graser (1962) и Bolton et al. (1989) максимальный эффект наблюдался в фазе II (испарение воды), которая длилась от 20 до 120 с. В результате время, необходимое для нагрева мата, содержащего 20% извлеченных частиц, до 60, 80 и 100 ° C, было сокращено на 22, 16 и 8% соответственно.В одинаковых условиях время нагрева мата, содержащего 100% восстановленных частиц, было на 29, 25 и 15% меньше, чем для эталона.
Предполагается, что время прессования (t p ) можно регулировать, контролируя время гелеобразования клея (t g ) и время нагрева мата (t o ). Таким образом, из соотношения t p = t g + t o очевидно, что чем короче t o , тем короче общий t p может быть.
Представленные результаты показывают, что маты, несущие восстановленные частицы, требуют меньшего времени прессования, чем промышленные маты из частиц.Например, время прессования матов с 20 или 100% восстановленного материала было сокращено на 3 и 6% соответственно.
Это явление можно объяснить увеличением насыпной плотности рекуперированных частиц на 58% по сравнению с промышленными (P_CL). Повышенная доля извлеченных частиц привела к менее плотной структуре слоя сердцевины, так что пар легко проникал через мат и ускорялась передача тепла. Многочисленные литературные сообщения согласуются с этим объяснением (Хамфри и Болтон, 1989; Болтон и др.1989; Томен и Хамфри 2001). Кроме того, восстановленные частицы представляют собой частично уплотненный материал, обладающий более высокой теплопроводностью (Kollmann 1955). Принимая во внимание, что содержание влаги в извлеченных и промышленных частицах было сопоставимым, эффектом этого можно пренебречь.
Древесно-стружечные плиты, содержащие в среднем слое 80% смеси IV, V, и древесностружечные плиты, содержащие в среднем слое 100% смеси III, IV и V (рис. 4), показали снижение плотности на 6–23% по сравнению к справке (644 кг / м 3 ).Вероятно, это происходит из-за недостаточного связывания покрытых PF частиц с УФ-смолой внутри слоя сердцевины, что впоследствии привело к ослаблению структуры и снижению плотности картона.
Плотность ДСП из рекуперированных частиц
Испытания на набухание по толщине (TS) показали набухание, сопоставимое с эталонным для древесностружечных плит со смесью I (8–10%). ПС плит смесей II – V увеличилось на 25–200% (рис.5). Еще более серьезный эффект наблюдался для древесностружечных плит, содержащих 100% смеси IV и V, где расслоение произошло еще до замачивания образца. Согласно стандарту EN 312 (2010) требуемый TS для плит типа P7-P3 толщиной 16 мм составляет 10–15%. Таким образом, было показано, что все древесностружечные плиты, содержащие 100% частиц с УФ-смолой, и древесно-стружечные плиты, содержащие до 20% частиц с УФ-смолой, удовлетворяли требованию.
Набухание по толщине ДСП из рекуперированных частиц
Видно, что добавление рекуперированных частиц повлияло на MOR плит (рис.6). Снижение составило от 13 до 91% по сравнению с эталоном. Наблюдение можно объяснить меньшей гибкостью и плоскостностью, что привело к уменьшению площади контакта между частицами (Arabi et al. 2011). Эффект был особенно заметен для древесностружечных плит, содержащих частицы с ПФ-смолой. Это дополнительно предполагает, что щелочной характер связующего может препятствовать УФ-отверждению (Czarnecki et al. 2003). Повышенная MOR (16%), достигаемая для плит, содержащих 20% смеси I, достигается за счет более компактной структуры среднего слоя, обеспечиваемой восстановленными частицами меньшего размера.Все плиты, содержащие частицы с УФ-смолой, и плиты, содержащие до 40% частиц с УФ-смолой, демонстрировали достаточный MOR, чтобы соответствовать требованиям стандарта EN 312. Таким образом, добавление 40% частиц PF-смолы является рекомендуемым верхним пределом для извлеченного материала.
Модуль разрыва ДСП из восстановленных частиц
Аналогичные соотношения были обнаружены для MOE (рис. 7). Однако результаты показывают, что влияние частиц с PF-смолой на снижение MOE было очевидным.Соответствующим требованиям стандарта EN 312 соответствовали плиты, состоящие из 20–80% смеси I, 20–60% смеси II или III и 20–40% смеси IV. Ни одна из плит, несущих смесь V, не соответствовала требованиям.
Рис. 7Модуль упругости древесностружечных плит из рекуперированных частиц
Что касается внутреннего связывания (IB), можно видеть, что добавление 20% смеси I, II или III не оказало значительного влияния на параметр (рис.8). Более того, чем выше было содержание частиц с PF-смолой, тем ниже IB. Таким образом, соответствующее требование стандарта EN 312 (минимум IB 0,24 Н / мм 2 ) соблюдалось только для плит, содержащих 20–80% смеси I, 20–60% смеси II или III и 20–40% смеси. IV или V.
Внутреннее склеивание древесностружечных плит из рекуперированных частиц
Наблюдаемые эффекты имеют сложный и, вероятно, синергетический характер, поэтому как химические свойства PF- и UF-клеев, так и размер, анизотропия, пористость и смачивание древесного материала также играют важную роль.Полученные результаты в целом указывают на то, что частицы с покрытием PF являются плохо связывающимся материалом по сравнению с частицами с покрытием UF. Объяснение ингибирования УФ-отверждения остается в соответствии с отчетом Czarnecki et al. (2003). Более низкая адгезионная способность восстановленных частиц также может быть объяснена их более низкой пористостью, вызванной предварительным уплотнением и, как следствие, более трудным проникновением и смачиванием поверхности жидкого клея (Pocius 2002). Следовательно, тип связующего, присутствующего в переработанном материале, и его химическая природа сильно влияют на способность к связыванию частиц и конечные характеристики плит.
дерево | Свойства, производство, использование и факты
Древесина , основная укрепляющая и проводящая питательные вещества ткань деревьев и других растений и один из самых распространенных и универсальных природных материалов. Произведенная многими ботаническими видами, включая голосеменные и покрытосеменные, древесина доступна в различных цветах и структурах. Он прочен по отношению к своему весу, изолирует тепло и электричество и обладает желаемыми акустическими свойствами.Кроме того, он придает ощущение «тепла», которого нет у конкурирующих материалов, таких как металл или камень, и относительно легко обрабатывается. В качестве материала дерево используется с тех пор, как на Земле появились люди. Сегодня, несмотря на технологический прогресс и конкуренцию со стороны металлов, пластмасс, цемента и других материалов, дерево сохраняет свое место в большинстве своих традиционных ролей, и его эксплуатационные качества расширяются за счет новых применений. Помимо хорошо известных продуктов, таких как пиломатериалы, мебель и фанера, древесина является сырьем для изготовления древесных плит, целлюлозы и бумаги, а также многих химических продуктов.Наконец, древесина по-прежнему является важным топливом во многих странах мира.
Британская викторина
Строительные блоки повседневных предметов
Из чего сделаны сигары? К какому материалу относится стекло? Посмотрите, из чего вы на самом деле сделаны, проанализировав вопросы в этой викторине.
Производство и потребление древесины
С ботанической точки зрения древесина является частью системы, которая переносит воду и растворенные минералы от корней к остальным частям растения, хранит пищу, созданную в результате фотосинтеза, и обеспечивает механическую поддержку. Его производят примерно от 25 000 до 30 000 видов растений, в том числе травянистые, хотя только от 3 000 до 4 000 видов производят древесину, пригодную для использования в качестве материала. Древесные деревья и другие древесные растения делятся на две категории: голосеменные и покрытосеменные. Голосеменные или шишковидные деревья производят мягкую древесину, такую как сосна и ель, а покрытосеменные — лиственные породы умеренного и тропического климата, такие как дуб, бук, тик и бальза. Следует отметить, что различие между лиственной древесиной и мягкой древесиной верно не во всех случаях.Некоторые лиственные породы, например бальза, мягче, чем мягкие породы, например тис.
Древесина — материал большого экономического значения. Его можно найти по всему миру, и его можно рационально использовать как возобновляемый ресурс — в отличие от угля, руд и нефти, которые постепенно истощаются. За счет лесозаготовок, транспортировки, обработки в мастерских и на промышленных предприятиях, а также торговли и использования древесина обеспечивает рабочие места и поддерживает экономическое развитие, а в некоторых странах — средства к существованию. Об этой важности свидетельствует сохраняющийся высокий спрос на древесину и изделия из нее.
По весу потребление древесины намного превышает потребление других материалов. Более половины производимого круглого леса (бревен) используется в качестве топлива, в основном в менее развитых странах. Производство бумаги и картона показало самый быстрый рост среди изделий из древесины; Ожидается, что эта тенденция сохранится по мере приближения потребления на человека в менее развитых странах к уровню потребления в развитых странах.Рост мирового населения является движущей силой увеличения потребления древесины и, как следствие, обезлесения. Истощение многих лесов, особенно в тропиках, делает сомнительным обеспечение достаточного количества древесины для удовлетворения ожидаемых потребностей. Усилия, направленные на то, чтобы остановить сокращение лесного покрова Земли и повысить продуктивность существующих лесов, создание обширных программ лесовосстановления и посадки быстрорастущих древесных пород, переработка бумаги и более эффективное использование древесины посредством исследований могут облегчить проблему поставок древесины и помогают уменьшить вредное воздействие на окружающую среду лесной промышленности.