Литейные стали и их свойства
К литейным сталям относят железоуглеродистые сплавы, содержащие до 2,14% С и другие элементы (Mn, Si, Р, S, Cr, Ni, W, Mo, V и т. д.), попавшие в сталь из шихтовых материалов либо специально введенные в нее в определенных количествах для придания сплаву необходимых эксплуатационных и технологических свойств.
В настоящее время стальные отливки используют во всех отраслях машиностроения; по объему производства они занимают второе место после чугунов. Из сталей отливают обычно детали, к которым предъявляют повышенные требования по прочности, пластичности, надежности и долговечности в процессе эксплуатации. Литейные стали классифицируют в основном по способу выплавки, химическому составу, структуре, назначению. По химическому составу литейные стали разделяют на углеродистые, а также низко-, средне- и высоколегированные.
По структуре углеродистые стали могут быть ферритными или перлитными, а легированные — ферритными, мартенситно-ферритными, мартенситными, аустенитно-мартенситными, аустенитно-ферритными и аустенитными.
В зависимости от назначения литой детали и требований к ней конструкционные нелегированные и легированные стали разделены (согласно ГОСТ 977—75) на три группы: для изготовления отливок общего назначения, ответственного назначения и особо ответственного назначения.
По способу выплавки различают стали, выплавленные в печах с кислой и основной футеровкой, так как состав футеровки оказывает существенное влияние на ход процесса плавки и свойства готового сплава. В печах с кислой футеровкой, главной составляющей которой является кремнезем SiO2, выплавляются обычно углеродистые и многие низколегированные конструкционные стали. В печах с основной футеровкой (магнезитовой, магнезитохромитовой, хромомагнезитовой) выплавляют преимущественно средне- и высоколегированные стали.
Большую часть фасонных отливок (около 65%) изготовляют из углеродистых конструкционных сталей (ГОСТ 977—75) следующих марок 15Л, 20Л, 25Л, 30Л, 35Л, 40Л, 45Л, 50Л, 55Л. В обозначении марки число означает среднее содержание углерода в сотых долях процента (например, для марки 25Л—0,25% С), а буква «Л» указывает, что сталь предназначена для литья (табл. 5.5.). Как видно из приведенных в таблице данных, с увеличением содержания углерода повышается прочность и снижаются пластические свойства сталей. Одновременно улучшается жидкотекучесть их и уменьшается усадка. Важное значение имеют требования, указанные в примечаниях в отношении содержания вредных примесей — серы и фосфора. Сера вызывает склонность сталей к образованию горячих трещин, а фосфор — хрупкость при обычных и низких температурах.
5.5. Свойства некоторых углеродистых конструкционных литейных сталей.
* В зависимости от назначения сталей содержание в них вредных примесей имеет различные ограничения: для отливок общего назначения допускается содержание серы до 0.06% и фосфора до 0,08%, тогда как для отливок особо ответственного назначения количество каждого из этих элементов не должно превышать 0,05%; содержание кремния в сталях всех указанных марок должно быть в пределах 0,2—0,52%. а Cr. Ni, Cu — не более 0.3% (каждого).
В ГОСТ 977—75 (СТ СЭВ 4459—84, СТ СЭВ 4561-84) предусмотрено также сорок пять марок легированной (Cr, Ni, Mn, Mo, V, Cu и др.) конструкционной стали с содержанием каждого из легирующих элементов не более 2% (мае.).
На отливки из высоколегированных сталей со специальными свойствами установлен ГОСТ 2176—77. Стандартом установлено 30 марок высоколегированных сталей указанного назначения. Марки включают буквенное обозначение легирующих элементов и следующие за ним числа, указывающие на среднее содержание этого элемента в массовых процентах. Числа в начале наименования марки характеризует среднее содержание углерода в процентах, а буква «Л» в конце показывает, что сталь предназначена для фасонного литья. Так, широко используемая в машиностроении коррозионностойкая (нержавеющая) сталь аустенитного класса 10Х18Н9ТЛ содержит не более 0,12% углерода, 17— 2U% хрома, 8—11% никеля и до 0,6% титана, а отличающаяся высокой износостойкостью высокомарганцовистая сталь 110Г13Л, идущая, например, на отливку звеньев гусениц тракторов и других гусеничных машин, содержит 0,9—1,3% углерода и 11,5—14,5% марганца.
ГОСТ 21357—75 установлен на отливки из хладно-стойкой и износостойкой стали для деталей машин и металлоконструкций, эксплуатируемых при температурах до —60°С. К числу этих сталей относят углеродистые и легированные конструкционные (например, 15ЛС, 35МЛС, ЗОХМЛС, 35ХГСМЛС), а также высоколегированные со специальными свойствами 10Х18Н9МЛС и 110Г13МЛС. Буква «С» в конце марки указывает, что эта сталь предназначена для работы при температурах до —60°С. В рассматриваемых сталях хладностойкость и повышенная износостойкость обеспечиваются низким содержанием вредных примесей — серы и фосфора (не более 0,02% каждой), а также обработкой этих сталей при плавке комплексными раскислителями и лигатурами редкоземельных и других металлов в сочетании со специальными режимами термической обработки готовых отливок.
Литейные сплавы и их свойства
В зависимости от метода переработки в заготовки металлические сплавы разделяют на литейные (используемые при изготовлении фасонных отливок) и деформируемые, получаемые вначале в виде слитков, а затем перерабатываемые ковкой, прокаткой, волочением, штамповкой. Различия в методах переработки оказывают существенное влияние на требования к свойствам, а следовательно, и на требования к составам литейных и деформируемых сплавов.
Литейные сплавы классифицируются в зависимости от их состава, свойств, назначения. Сплавы на основе железа называют черными. К ним относят все разновидности чугунов и сталей. Остальные литейные сплавы на основе алюминия, магния, цинка, олова, свинца, меди, титана, молибдена, никеля, кобальта, бериллия и других металлов, в том числе и благородных (серебра, золота, платины), называют цветными.
Для обеспечения требуемых эксплуатационных свойств литых деталей, например прочности, твердости, износостойкости, в сплавы в определенном количестве вводят специальные добавки, так называемые легирующие компоненты. По содержанию их сплавы делят на низколегированные (менее 2,5% легирующих компонентов по массе), среднелегированные (от 2,5 до 10%) и высоколегированные (свыше 10%).
Помимо специально вводимых в литейные сплавы компонентов в них обычно присутствуют постоянные примеси, наличие которых связано с особенностями металлургических процессов приготовления сплава и составом исходных металлургических материалов (руд, топлива, флюсов). Часто эти примеси (например, сера и фосфор в сталях) являются вредными и содержание их ограничивают.
Литейные сплавы либо приготовляют из исходных компонентов (шихтовых материалов) непосредственно в литейном цехе, либо сплавы поступают с металлургических комбинатов в готовом виде и их только переплавляют перед заливкой в литейные формы. Как в первом, так и во втором случае отдельные элементы в процессе плавки, входящие в состав литейного сплава, могут окисляться (угарать), улетучиваться при повышенных температурах (возгоняться), вступать в химическое взаимодействие с другими компонентами или с футеровкой печи и переходить в шлак. Для восстановления требуемого состава сплава потери отдельных элементов в нем компенсируют, вводя в расплав специальные добавки (лигатуры, ферросплавы), приготовляемые на металлургических предприятиях. Лигатуры представляют собой вспомогательные сплавы, используемые как для введения в расплав основного литейного сплава легирующих элементов, так и для компенсации их угара.
Лигатуры содержат помимо легирующего элемента также и основной металл сплава, поэтому они легче и полнее усваиваются расплавом, чем чистый легирующий элемент. Применение лигатур становится особенно необходимым, если температуры плавления основного литейного сплава и легирующего элемента имеют значительную разницу. Наиболее широко применяют лигатуры из цветных металлов, например: медь — никель (15— 33% Ni), медь — алюминий (50% Al), медь — олово (50% Sn), алюминий—магний (до 10% Mg). При литье черных сплавов широко используют ферросплавы: ферросилиций (сплав железа с 13% и более кремния), ферромарганец, феррохром, ферровольфрам, ферромолибден и др. для введения легирующих элементов, а также для раскисления расплава. Используют также ферросплавы, состоящие из трех компонентов и более. К ферросплавам условно относят и некоторые сплавы, железо в которых содержится только в виде примеси, например силикоалюминий и силикокальций.
Раскисление, для которого часто используют ферросплавы, представляет собой процесс удаления из сплава кислорода, содержащегося в виде растворенных в металле оксидов (например, закиси железа FeO в стали). В процессе раскисления элементы, содержащиеся в ферросплавах, выполняют роль восстановителей:
они соединяются с кислородом оксида, растворенного в расплаве, восстанавливают металл, а сами, окислившись, переходят в шлак. Так, раскисление стали кремнием, содержащимся в ферросилиции, происходит по реакции 2FeO+Si→2Fe+SiO2.
Очищение (рафинирование) расплава раскислением способствует значительному улучшению качества металла отливки, повышению его прочности и пластичности.
Ряд сплавов, так же как и металлов либо неметаллических материалов (солей и др.), используют в качестве модификаторов, которые при введении в литейный сплав в небольших количествах существенно влияют на его структуру и свойства, например измельчают зерно и способствуют повышению прочности металла. Так, для получения высокопрочного чугуна широко используют модифицирование магнием.
Б настоящее время в СССР около 95% всех производимых отливок (по массе) составляют чугунные и стальные. Следует однако учитывать, что из черных сплавов изготовляют большое количество крупных отливок, масса которых доходит до нескольких десятков и даже сотен тонн, а из сплавов цветных металлов отливают в основном мелкие и средние детали массой от нескольких граммов до нескольких десятков и редко — до нескольких сотен килограммов. Поэтому, несмотря на то что в общем выпуске масса отливок из цветных сплавов составляет около 5%. номенклатура их, так же как и методы литья, весьма разнообразна, а количество значительно.
ЗНАЕТЕ ЛИ ВЫ? |
К литейным сталям относят железоуглеродистые сплавы, содержащие до 2,14 % С и другие элементы (Мn, Si, P, S, Cr, Ni, W, Mo, V и др.), попавшие в сталь из шихтовых материалов либо специально введенные в нее в определенных количествах для придания сплаву необходимых эксплуатационных и технологических свойств. Стальные отливки по объему производства занимают второе место по- сле чугуна и применяются во всех отраслях машиностроения. Из стали отли- вают детали, к которым предъявляют повышенные требования по прочности, пластичности, надежности и долговечности в процессе эксплуатации. В машиностроении для изготовления стального фасонного литья в соответствии с ГОСТ 977 и ГОСТ 7832 применяются три группы литейных сталей: нелегированные (углеродистые), легированные, легированные со спецсвойствами.
Классификация литейных сталей
Наиболее широко применяются для отливок углеродистые нелегиро-ванные стали (около 2/3 всех стальных отливок), их стандартные марки обозначаются буквой Л (литейная) и числом, указывающим среднее содержание углерода в сотых долях процента; например, 15Л, 25Л, З0Л, 45Л, 50Л, 55Л и др. Углеродистые литейные стали применяются обычно в нормализованном, нормализованном и отпущенном состоянии, в улучшенном состоянии и после нормализации, закалки и высокого отпуска. В последнем случае нормализация выполняет роль предварительной термообработки, целью которой является подготовка литой структуры для окончательной термической обработки. Для изготовления отливок применяют легированные и легированные стали со специальными свойствами (с. Легированные литейные стали обозначают цифрами и буквами аналогично деформируемым конструкционным сталям, за исключением того, что в конце литейной марки стоит буква Л вместо А, Ш, В, Д. Например, сталь 30ХГСЛ аналогична деформируемой стали 30ХГСА. Например, обозначение марки одной из конструкциионных сталей 20Х13Л: 0,20 % углерода; 13 % хрома; литейная сталь. В обозначениях марок литейной хладостойкой и износостойкой сталей, используемых для деталей машин и эксплуатируемых при температуре до —60 °С, после буквы Л (литейная) ставится буква С. Например, 15ЛС—0,15 % углерода; 30ХМЛС: 0,30 % углерода; хром; молибден и др. (ГОСТ 21357—75). В группу легированных литейных сталей входят марганцовистые (например, 35ГЛ), марганцекремнистые (например, 20ГСЛ), хромистые (например, 40ХЛ), хромоникелевые (например, 35ХНЛ), хромомарганцекремнистые (например, ЗОХНМЛ), хромомарганцеванадиевые (например, 23ХГС2МФЛ) и так называемые медистые (например, 08ГДНФЛ и 12ДН2ФЛ), в которые дополнительно специально введена медь (Д) для обеспечения эффекта дисперсного упрочнения стали. Для удобства выбора легированных литейных сталей при изготовлении конкретных стальных отливок с заданным уровнем характеристик механических свойств все они разбиты на группы в соответствии с обеспечиваемой ими величиной предела текучести s0,2, и обозначаемые после нормализации и отпуска буквой К, а после закалки и отпуска — буквами КТ. В соответствии с этим все легированные литейные стали разделены на две группы: стали, обеспечивающие категории прочности К в пределах от К-25 до К-55, и стали; •стали, обеспечивающие категории прочности КТ в пределах от КТ-35 до КТ-120. Причем одни и те же стали могут входить в обе эти группы. Например, сталь 08ГДНФЛ может обеспечивать категорию прочности К-30 и КТ-40. Индексы ≪К≫ и ≪КТ≫ являются условными обозначениями категории прочности, следующее за ними число означает значение требуемого предела текучести (кг/мм2). Точный химический состав сталей указывается в таблицах ГОСТ 977–88. Можно отметить, что в разработанных в 80-е годы литейных высоко-прочных экономнолегированных сталях, входящих в ГОСТ 977, (например, 15Х5ГСФЛ, 23ХГС2МФЛ, 25Х212ФЛ, 17Х5Г5С2МЛ и 30Х3С3ГМЛ удалось получить наряду с высоким уровнем прочностных свойств также высокие значения пластичности и вязкости, которые сравнимы с аналогичными значениями деформируемых сталей. Такие уникальные свойства в них удалось получить за счет снижения развития ликвационных процессов оптимизацией состава: 1) снижением содержания углерода; 2) снижением количества элементов, образующих стойкие химические соединения в виде карбидов, нитридов, которые ликвируют сильнее остальных; 3) введением в сталь элементов, уменьшающих ликвацию (Ni, Si и др). К высоколегированным литейным сталям, представленным в ГОСТ 7832, входят коррозионностойкие стали 20Х13Л, 10Х18Н9Л, 12Х18Н9ТЛ и др., жаростойкие и жаропрочные стали 20Х20Н14С2Л, 20Х25Н19С2Л, 40Х24Н12СЛ и др.; износостойкая сталь 110Г13Л. Для получения качественных стальных отливок необходимо учитывать особенности литейных свойств сталей на стадии конструирования литой детали и при разработке технологии ее изготовления. В технологии литья следует предусматривать расположение отливки в форме и подвод металла таким образом, чтобы отливка затвердевала последовательно. Скопления металла в местах сопряжения стенок недопустимы, поэтому отливка должна иметь плавные переходы от утолщенных мест к тонким или равномерную толщину стенок.
Контрольные вопросы………………………………………………
Лекция 8 Читайте также: |
Литейная сталь и чугуны — свойства и производство по ГОСТ
Кроме изготовления стальных конструкций путем сварки или сборки болтовыми соединениями, широко используются и методы литья. Мы не будем останавливаться на способах литья, отметим лишь, что литейные сплавы должны обладать совокупностью свойств, характеризующих способность расплавленного металла образовывать качественные отливки. Среди черных металлов вполне приличными литейными свойствами обладают литейные стали и чугуны.
Важны, в основном, две характеристики – наличие достаточно большого интервала температуры плавления и минимальная величина усадки при затвердевании. Для литейных сталей температура плавления лежит в пределах 1400-1525°С и литейная усадка 1,6-1,2 %; для чугунов эти величины равны 1150-1200°С и 0,8-1,2 %, соответственно.
Литейные стали имеют химический состав, мало отличающийся от химического состава нелегированных низкоуглеродистых. Содержание углерода оказывает серьезное влияние на литейные свойства стали – чем оно выше, тем хуже литейные свойства. Поэтому марки литейных сталей обычно ограничиваются содержанием углерода 0,17-0,25 %, редко выше. Так как литейные стали, в отличие от конструкционных сталей, изготавливаются при наличии кислой обкладки в печах, а не основной, как при изготовлении конструкционных сталей, то и содержание вредных примесей в них несколько выше, а именно, содержание серы и фосфора ограничено величинами не более 0,05%. Обозначаются литейные стали так: сначала содержание углерода в сотых долях процента, округленное до числа, кратного пяти, затем добавляется буква Л: сталь 15Л, 25Л, 35Л.
Чугуны имеют значительно большее разнообразие вследствие того, что структура чугуна и его свойства зависят как от химического состава, так и от скорости охлаждения. В зависимости от формы графита и количества цементита выделяют: белый, серый, ковкий и высокопрочный чугуны. Чугуны содержат постоянные примеси (кремний, марганец, фосфор и серу), а в некоторых случаях легирующие элементы, как полученные в результате доменных процессов из-за особенностей состава руд, так и привнесенные дополнительно (хром, ванадий, алюминий и др.)
Белые чугуны – это железо-углеродистые сплавы, содержащие от 2 до 6,67% углерода, в структуре которого углерод присутствует только в виде цементита. Свое название этот чугун получил из-за светлого цвета излома.
Железо-углеродистые сплавы, у которых углерод полностью или частично находится в свободном состоянии в виде графита, называются серыми чугунами. Излом такого чугуна имеет серый цвет. В зависимости от степени распада цементита на перлит и графит, могут быть ферритоперлитные, перлитные или перлитоцементитные серые чугуны.
Ковкий чугун получают длительным отжигом белого чугуна, в результате которого образуется графит хлопьевидной формы; металлическая основа такого чугуна – феррит и реже перлит.
Высокопрочный чугун имеет в своей основе шаровидный графит, который образуется в процессе кристаллизации. Шаровидный графит ослабляет металлическую основу не так сильно, как пластинчатый.
Обозначения литейных чугунов: Л1, Л2,… Л6; рафинированный марганцем ЛР1, ЛР2 … ЛР6, чугун с пластинчатым графитом (СЧ с номером, обозначающим величину временного сопротивления разрыву в кгс/мм), чугун с шаровидным графитом (ВЧ с числом, аналогичным предыдущему). Содержание углерода в них 3,5-3,6 %, кремния 1,6-3,6 %; марганца 0,3-1,5 %, фосфора 0,08-1,2 % и серы 0,02-0,05 %.
Кроме этих, существуют специальные формы чугуна (антифрикционный и легированный), но они, как правило, в практике горячего цинкования не встречаются.
ГОСТ 977-88 Отливки стальные. Общие технические условия
ГОСТ 977-88
Группа В82
МКС 77.140.80
ОКП 41 1200
Дата введения 1990-01-01
1. УТВЕРЖДЕН И ВВЕДЕН В ДЕЙСТВИЕ Постановлением Государственного комитета СССР по стандартам от 22.12.88 N 4458
2. Стандарт полностью соответствует СТ СЭВ 4559-84, СТ СЭВ 4561-84 и СТ СЭВ 4563-84 в части марок
3. ВЗАМЕН ГОСТ 977-75, ГОСТ 2176-77
4. ССЫЛОЧНЫЕ НОРМАТИВНО-ТЕХНИЧЕСКИЕ ДОКУМЕНТЫ
5. Ограничение срока действия снято по протоколу N 7-95 межгосударственного совета по стандартизации, метрологии и сертификации (ИУС 11-95)
6. ПЕРЕИЗДАНИЕ. Август 2004 г.
Настоящий стандарт распространяется на стальные отливки, изготавливаемые всеми способами литья из нелегированных и легированных конструкционных, легированных со специальными свойствами литейных сталей.
1. МАРКИ
1.1. Для изготовления отливок предусмотрены следующие марки стали:
конструкционные нелегированные:
15Л, 20Л, 25Л, 30Л, 35Л, 40Л, 45Л, 50Л;
конструкционные легированные:
20ГЛ, 35ГЛ, 20ГСЛ, 30ГСЛ, 20Г1ФЛ, 20ФЛ, 30ХГСФЛ, 45ФЛ, 32Х06Л, 40ХЛ, 20ХМЛ, 20ХМФЛ, 20ГНМФЛ, 35ХМЛ, 30ХНМЛ, 35ХГСЛ, 35НГМЛ, 20ДХЛ, 08ГДНФЛ, 13ХНДФТЛ, 12ДН2ФЛ, 12ДХН1МФЛ, 23ХГС2МФЛ, 12Х7Г3СЛ, 25Х2ГНМФЛ, 27Х5ГСМЛ, 30Х3С3ГМЛ, 03Н12Х5М3ТЛ, 03Н12Х5М3ТЮЛ;
конструкционные легированные, применяемые в договорно-правовых отношениях между странами — членами СЭВ:
15ГЛ, 30ГЛ, 45ГЛ, 70ГЛ, 55СЛ, 40Г1, 5ФЛ, 15ФЛ, 30ХЛ, 25ХГЛ, 35ХГЛ, 50ХГЛ, 60ХГЛ, 70Х2ГЛ, 35ХГФЛ, 40ХФЛ, 30ХМЛ, 40ХМЛ, 40ХНЛ, 40ХН2Л, 30ХГ1, 5МФРЛ, 75ХНМФЛ, 40ГТЛ, 20ГНМЮЛ;
легированные со специальными свойствами:
а) мартенситного класса
20Х13Л, 08Х14НДЛ, 09Х16Н4БЛ, 09Х17Н3СЛ, 10Х12НДЛ — коррозионностойкие; 20Х5МЛ, 20Х8ВЛ, 40Х9С2Л — жаростойкие; 20Х12ВНМФЛ — жаропрочная; 85Х4М5Ф2В6Л (Р6М5Л), 90Х4М4Ф2В6Л (Р6М4Ф2Л) — быстрорежущие;
б) мартенситно-ферритного класса
15Х13Л — коррозионностойкая;
в) ферритного класса
15Х25ТЛ — коррозионностойкая;
г) аустенитно-мартенситного класса
08Х15Н4ДМЛ, 08Х14Н7МЛ, 14Х18Н4Г4Л — коррозионностойкие;
д) аустенитно-ферритного класса
12Х25Н5ТМФЛ, 16Х18Н12С4ТЮЛ, 10Х18НЗГЗД2Л — коррозионностойкие; 35Х23Н7СЛ, 40Х24Н12СЛ, 20Х20Н14С2Л — жаростойкие;
е) аустенитного класса
10Х18Н9Л, 12Х18Н9ТЛ, 10Х18Н11БЛ, 07Х17Н16ТЛ, 12X18Н12М3ТЛ — коррозионностойкие; 55Х18Г14С2ТЛ, 15Х23Н18Л, 20Х25Н19С2Л, 18Х25Н19СЛ, 45Х17Г13Н3ЮЛ — жаростойкие; 35Х18Н24С2Л, 31Х19Н9МВБТЛ, 12Х18Н12БЛ, 08Х17Н34В5Т3Ю2РЛ, 15Х18Н22В6М2РЛ, 20Х21Н46В8РЛ — жаропрочные; 110Г13Л, 110Г13Х2БРЛ, 110Г13ФТЛ, 130Г14ХМФАЛ, 120Г10ФЛ — износостойкие;
легированные со специальными свойствами, применяемые в договорно-правовых отношениях между странами — членами СЭВ:
а) мартенситно-ферритного класса
15Х14НЛ, 08Х12Н4ГСМЛ — коррозионностойкие;
б) аустенитно-ферритного класса
12Х21Н5Г2СЛ, 12Х21Н5Г2СТЛ, 12Х21Н5Г2СМ2Л, 12Х19Н7Г2САЛ, 12Х21Н5Г2САЛ, 07Х18Н10Г2С2М2Л; 15Х18Н10Г2С2М2Л, 15Х18Н10Г2С2М2ТЛ — коррозионностойкие.
Область применения конструкционных легированных сталей приведена в приложении 1, легированных со специальными свойствами — в приложении 2.
1.2. Сталь должна выплавляться в печах с основной футеровкой. Допускается выплавка стали в печах с кислой футеровкой при условии выполнения требований настоящего стандарта.
Примечание. Возможность применения конверторной стали должна быть указана в конструкторской документации (КД) и (или) нормативно-технической документации (НТД).
1.3. Химический состав конструкционной нелегированной и легированной стали должен соответствовать указанному в табл.1, легированной со специальными свойствами — в табл.2.
Таблица 1
Марка стали | Массовая доля элемента, % | |||||||
Код ОКП | Обозначение | Обозна- | Углерод | Марганец | Кремний | Фосфор | Сера | Хром |
не более | ||||||||
Стали конструкционные нелегированные | ||||||||
41 1200 | 15Л | 52731 | 0,12-0,20 | 0,45-0,90 | 0,20-0,52 | По табл. | По табл.4 | — |
20Л | — | 0,17-0,25 | 0,45-0,90 | 0,20-0,52 | То же | То же | — | |
25Л | 52821 | 0,22-0,30 | 0,45-0,90 | 0,20-0,52 | « | « | — | |
30Л | — | 0,27-0,35 | 0,45-0,90 | 0,20-0,52 | « | « | — | |
35Л | 52831 | 0,32-0,40 | 0,45-0,90 | 0,20-0,52 | « | « | — | |
40Л | 52861 | 0,37-0,45 | 0,45-0,90 | 0,20-0,52 | « | « | — | |
45Л | 52862 | 0,42-0,50 | 0,45-0,90 | 0,20-0,52 | « | « | — | |
50Л | — | 0,47-0,55 | 0,45-0,90 | 0,20-0,52 | « | « | — | |
Стали конструкционные легированные | ||||||||
41 1220 | 20ГЛ | 52763 | 0,15-0,25 | 1,20-1,60 | 0,20-0,40 | 0,040 | 0,040 | — |
35ГЛ | 52833 | 0,30-0,40 | 1,20-1,60 | 0,20-0,40 | 0,040 | 0,040 | — | |
20ГСЛ | — | 0,16-0,22 | 1,00-1,30 | 0,60-0,80 | 0,030 | 0,030 | — | |
30ГСЛ | 52834 | 0,25-0,35 | 1,10-1,40 | 0,60-0,80 | 0,040 | 0,040 | — | |
20Г1ФЛ | 55244 | 0,16-0,25 | 0,90-1,40 | 0,20-0,50 | 0,050 | 0,050 | — | |
20ФЛ | 55242 | 0,14-0,25 | 0,70-1,20 | 0,20-0,52 | 0,050 | 0,050 | — | |
30ХГСФЛ | 55142 | 0,25-0,35 | 1,00-1,50 | 0,40-0,60 | 0,050 | 0,050 | 0,30-0,50 | |
45ФЛ | 55243 | 0,42-0,50 | 0,40-0,90 | 0,20-0,52 | По табл. | По табл.4 | — | |
32Х06Л | — | 0,25-0,35 | 0,40-0,90 | 0,20-0,40 |
Виды сталей и методы литья
Сталь – один из наиболее распространённых в глобальной промышленности строительных материалов. Она используется в металлообрабатывающей, автомобильной, пищевой, строительной и многих других отраслях. Иными словами, сегодня трудно представить жизнь без стальных деталей, присутствующих в каждом доме. Литье стали – это сложный технологический процесс, начавший активно развиваться и совершенствоваться ещё в XIX в.
Значение стали в мировой индустрии
Металлургия — производство стали
Мировая сталелитейная промышленность – одна из самых развитых отраслей металлургии. Несмотря на недавний спад производства в связи с финансовым кризисом 2012 года, литье стали получило новый толчок и сейчас стремительно набирает обороты. Ежегодный спрос на этот метод неуклонно растёт в связи с тенденциями к урбанизации и индустриализации. Основные покупатели стальных изделий – страны с хорошо развитой инфраструктурой и промышленностью. Производство стали в мире составляет около 90% от объёма всех металлов.
Сталь широко применяется в строительстве дорог, зданий и инфраструктурных сооружений: самые крупные стадионы, аэропорты и мосты имеют, как правило, стальной скелет. Болты, гвозди и винты также изготовлены методом отливки стали в специальные формы. Несмотря на растущую долю алюминия на мировом рынке, литье стали ещё долго не сдаст свои позиции. В то же время сталелитейное производство характеризуется цикличностью, а, следовательно, и относительной нестабильностью.
Характеристика стали
Характеристика стали
Своим появлением сталь обязана железу – это сплав железа (Fe) с определённым содержанием углерода (C). Доля последнего в смеси должна варьироваться в пределах от 0,1 до 2,14%. Причём сплавы, содержащие более 0,6% углерода в своём составе, получили название «высокоуглеродистые». Такие материалы отличаются особенной прочностью, так как углерод придаёт стали твёрдость и снижает её пластичность. Если содержание углерода превышает отметку в 2,14%, то материал относится к чугунам.
В процессе литья стали в сплав могут быть добавлены так называемые легирующие элементы (вольфрам, ванадий, марганец, хром, титан, кобальт и другие). Эта процедура направлена на то, чтобы придать конечному материалу нужные свойства, такие как прочность, пластичность, обрабатываемость и т. д. При этом массовая доля содержания железа должна оставаться на уровне не менее 45%.
Вне зависимости от способа получения стали, материал содержит небольшое количество примесей марганца, фосфора, серы и кремния. Эти элементы способны негативно влиять на здоровье человека, поэтому сталь не относится к высокоэкологичным материалам.
Разновидность сталей
Есть несколько общепризнанных классификаций литья стали в зависимости от критерия оценки. По качеству и способу производства стали подразделяются на:
- обыкновенного качества;
- качественные;
- повышенного качества;
- высококачественные.
Отношение к той или иной категории определяется процентом содержания вышеупомянутых вредных примесей и соответствием технологическим и механическим характеристикам. Каждый из видов имеет свою сферу применения. По химическому составу стальные сплавы делятся на:
- Углеродистые, предназначенные для статических нагрузок. Внутри себя группа делится на низко-, средне- и высокоуглеродистую сталь.
- Легированные, содержащие дополнительные элементы, влияющие на физические свойства материала.
Классификация
Кроме того, существует классификация по способу применения стали:
Классификация сталей
- Строительная – обыкновенный материал с хорошей свариваемостью.
- Конструкционная – характеризуется высоким содержанием углерода, подходит для каркасов, кровельных работ, изготовления рельсов.
- Инструментальная – применяется для режущего инструмента (резец, стамеска, долото, сверло, напильник и др.).
- Легированная – универсальная смесь со специальной примесью. Подвид – низколегированная сталь для суровых климатических условий.
- Сталь особого назначения используется в точном судостроении и электротехнике.
Свариваемость – ещё один важнейший критерий для литья стали, ставший основанием для разделения сплавов на группы. Это свойство определяется способностью к раскислению:
- Спокойные – полностью раскисляются, содержат минимальное количество неметаллических примесей.
- Полуспокойные, схожие со спокойными по качеству.
- Кипящие – неокисленные стали с высоким процентным содержанием неметаллических компонентов.
Для удобства была введена специальная маркировка, которая позволяет определить, к какому виду относится тот или иной сплав и какими основными характеристиками он обладает.
Важно помнить, что общемировой системы нет, и у каждой страны она своя. Так, на территории России принято придерживаться численно-буквенных обозначений.
Основные процессы и технологии литья стали
С развитием промышленности спрос на более устойчивый к внешним воздействиям материал возрастал, и перед человеком встала задача создать его, имея в арсенале лишь научные догадки и оборудование, оставлявшее желать лучшего. Благодаря пытливости учёных было разработано множество способов выплавки стали. Процесс состоит из нескольких этапов.
Плавка
Устройство для плавки стали
С открытия стали как строительного элемента прошло несколько веков, в течение которых было запатентовано и реализовано множество методов литья. С недавнего времени она стала плавиться в основном несколькими способами. Большую их часть объединяет принадлежность к электроплавильным способам обработки металла. Электропечи – лучшие на сегодня агрегаты, позволяющие наиболее быстро и качественно выплавить смесь, точно настроив температуру плавления и заливки.
Первый метод – дуговые электропечи. В качестве источника тепла используется электрическая дуга с рабочим напряжением до 600 В и силой тока до 10 кА. Длина дуги регулируется, а также печь оснащена огнеупорным кожухом и рабочим окном для контролирования плавильного процесса. Ёмкость дуговой печи может достигать 400 т.
Второй востребованный метод обработки стали – индукционные электропечи. Эти агрегаты подразделяются на конструкции с сердечником и без. Первая группа – печи низкой частоты, которые состоят из шахты и каналов, охватывающих сердечник и первичную обмотку трансформатора (индуктор). Залитый в канал жидкий металл провоцирует создание вторичного витка с мощным электрическим током, чья энергия трансформируется в тепловую. Материал быстро нагревается, что значительно экономит сырьё и электроэнергию. Дополнительное преимущество агрегата – отсутствие необходимости чистить каналы после предыдущей отливки.
Кислородно-конверторный способ плавки стали
Дополнительные методы
Индукционная печь
Индукционные печи без сердечника – это воздушные трансформаторы, принцип работы которых основан на поглощении выделяемой электромагнитной энергии загруженной в тигель шихтой (металлическим сырьём). Печи данного типа подразделяются на оборудование промышленной частоты (50 Гц) и высокочастотные (более 500 Гц).
Электричество позволяет быстро нагреть форму, поэтому в вышеперечисленных агрегатах выгодно изготавливать легированную сталь. Однако не меньшей популярностью пользуются такие способы как кислородно-конвертерный и мартеновский процессы.
Кислородно-конвертерный метод предусматривает литье стали из чугуна посредством окисления его примесей при помощи продувания кислородом. Система отличается простотой и высокой скоростью производства. Температура в камере поддерживается самим процессом окисления, обычно она составляет около 1600 °C.
Мартеновский процесс уходит корнями глубоко в историю – лишь в 1864 году удалось добиться температурных показателей, необходимых для срабатывания химических реакций. Тем не менее, ввиду относительной простоты реализации способ и по сей день широко используется.
Внутри себя процесс плавки также традиционно подразделяется на 3 основных этапа:
- Нагревание шихты и её расплавление.
- «Кипение» ванны – нагревание до максимальных температур для интенсивного окисления.
- Раскисление – на этом же этапе при необходимости проводится легирование.
Схема индукционной печи со стальным сердечником
Отливка сплава
После того как внутри печи или камеры произошло нагревание, расплавление и трансформация сырья в стальной сплав, его необходимо отлить в формы. Это происходит благодаря так называемой литниковой системе. Она является совокупностью каналов и резервуаров для подвода металла к форме для отливки.
Существуют различные типы форм для отливки стали, самые распространённые из них:
Особенности технологии производства фасонных отливок из алюминиевых сплавов
- песчаные формы для отливки – одноразовые, изготавливаются из смеси кварцевого песка, огнеупорной глины и каменноугольной пыли с опилками;
- оболочковые формы для отливки – обеспечивают герметическую точность, автоматизируют производство отливки, слитки получаются менее шероховатыми;
- выплавляемые формы для отливки – применяются для изготовления деталей высокой точности и любой сложности.
Каждый из видов форм для отливки обладает и достоинствами, и рядом недостатков, поэтому выбор в пользу того или иного способа осуществляется с учётом специфики производства конкретного изделия. Так, песчаные формы – это дёшево, но некачественно, в то время как литье стали с использованием выплавляемых моделей гарантирует высокую точность, но далеко не всегда оправдывает высокую себестоимость.
Был разработан самый экономичный способ отливки стальных слитков, получивший название «непрерывный» – получившийся сплав из ковша поступает в промежуточную форму для отливки, а оттуда – в медный кристаллизатор, где он начинает медленно затвердевать. На выходе слиток захватывается специальными тянущими роликами и дополнительно охлаждается водой. Скорость вытягивания стали из кристаллизатора составляет около 1 м/мин, после чего получившийся профиль режется на куски нужных размеров при помощи ацетиленокислородного лезвия.
Машина для литья отливок
Выводы
Сталелитейное производство обладает огромным промышленным потенциалом, так как спрос на литье стали ежегодно растёт. Совершенствование уже имеющихся технологий позволит создавать ещё более качественные элементы с нестандартными физическими свойствами.
Видео по теме: Литье по выплавляемым моделям
сталь | Состав, свойства, типы, марки и факты
Основной металл: железо
Изучение производства и структурных форм железа от феррита и аустенита до легированной стали.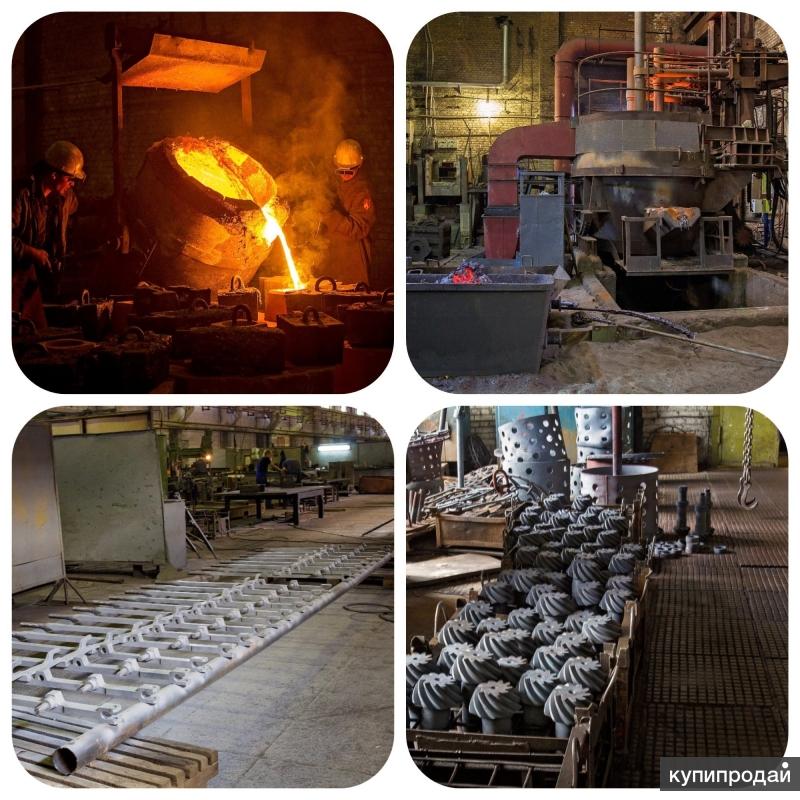
Железная руда — один из самых распространенных элементов на Земле, и одно из ее основных применений — производство стали. В сочетании с углеродом железо полностью меняет свой характер и становится легированной сталью.
Encyclopædia Britannica, Inc. Посмотреть все видео для этой статьи Основным компонентом стали является железо, металл, который в чистом виде не намного тверже меди.За исключением крайних случаев, железо в твердом состоянии, как и все другие металлы, является поликристаллическим, то есть состоит из множества кристаллов, которые соединяются друг с другом на своих границах. Кристалл — это упорядоченное расположение атомов, которое лучше всего можно представить как сферы, соприкасающиеся друг с другом. Они упорядочены в плоскостях, называемых решетками, которые определенным образом пронизывают друг друга. Для железа структуру решетки лучше всего можно представить в виде единичного куба с восемью атомами железа в углах. Для уникальности стали важна аллотропия железа, то есть его существование в двух кристаллических формах. В объемно-центрированной кубической (ОЦК) конфигурации в центре каждого куба находится дополнительный атом железа. В расположении гранецентрированного куба (ГЦК) есть еще один атом железа в центре каждой из шести граней единичного куба. Важно отметить, что стороны гранецентрированного куба или расстояния между соседними решетками в ГЦК-конфигурации примерно на 25 процентов больше, чем в ОЦК-структуре; это означает, что в структуре ГЦК больше места, чем в структуре БЦК, для хранения посторонних ( i.е., легирующих) атомов в твердом растворе.
Железо имеет аллотропию ОЦК ниже 912 ° C (1674 ° F) и от 1394 ° C (2541 ° F) до точки плавления 1538 ° C (2800 ° F). Называемое ферритом, железо в его ОЦК-образовании также называется альфа-железом в более низком температурном диапазоне и дельта-железом в более высокотемпературной зоне. Между 912 ° и 1394 ° C железо находится в порядке ГЦК, которое называется аустенитом или гамма-железом. Аллотропное поведение железа сохраняется, за некоторыми исключениями, в стали, даже когда сплав содержит значительные количества других элементов.
Существует также термин бета-железо, который относится не к механическим свойствам, а к сильным магнитным характеристикам железа. При температуре ниже 770 ° C (1420 ° F) железо является ферромагнитным; температуру, выше которой он теряет это свойство, часто называют точкой Кюри.
Сэкономьте 50% на подписке Britannica Premium и получите доступ к эксклюзивному контенту. Подпишитесь сегодня В чистом виде железо мягкое и обычно не используется в качестве конструкционного материала; основной метод его упрочнения и превращения в сталь — добавление небольшого количества углерода.В твердой стали углерод обычно присутствует в двух формах. Либо он находится в твердом растворе в аустените и феррите, либо находится в виде карбида. Форма карбида может быть карбидом железа (Fe 3 C, известный как цементит) или карбидом легирующего элемента, такого как титан. (С другой стороны, в сером чугуне углерод проявляется в виде хлопьев или кластеров графита из-за присутствия кремния, подавляющего образование карбидов. )
Влияние углерода лучше всего иллюстрируется диаграммой равновесия железо-углерод.Линия A-B-C представляет точки ликвидуса (, т.е. — температуры, при которых расплавленное железо начинает затвердевать), а линия H-J-E-C представляет точки солидуса (при которых затвердевание завершается). Линия A-B-C показывает, что температура затвердевания снижается по мере увеличения содержания углерода в расплаве железа. (Это объясняет, почему серый чугун, содержащий более 2 процентов углерода, обрабатывается при гораздо более низких температурах, чем сталь.) Расплавленная сталь, например, с содержанием углерода 0.77 процентов (показано вертикальной пунктирной линией на рисунке) начинают затвердевать при температуре около 1475 ° C (2660 ° F) и полностью затвердевают при температуре около 1400 ° C (2550 ° F). С этого момента все кристаллы железа находятся в аустенитном — т. Е. гцк — расположении и содержат весь углерод в твердом растворе. При дальнейшем охлаждении происходит резкое изменение примерно при 727 ° C (1341 ° F), когда кристаллы аустенита превращаются в тонкую пластинчатую структуру, состоящую из чередующихся пластинок феррита и карбида железа. Эта микроструктура называется перлитом, а изменение называется эвтектоидным превращением. Перлит имеет твердость алмазной пирамиды (DPH) приблизительно 200 килограммов-сил на квадратный миллиметр (285 000 фунтов на квадратный дюйм), по сравнению с DPH 70 килограммов-сил на квадратный миллиметр для чистого железа. Охлаждение стали с более низким содержанием углерода (, например, 0,25 процента) дает микроструктуру, содержащую около 50 процентов перлита и 50 процентов феррита; он мягче, чем перлит, с DPH около 130.Сталь с содержанием углерода более 0,77 процента, например 1,05 процента, содержит в своей микроструктуре перлит и цементит; он тверже перлита и может иметь DPH 250.
Диаграмма равновесия железо-углерод.
Encyclopædia Britannica, Inc.Компании-производители отливок из нержавеющей стали Китай: нержавеющая сталь
Производители отливок из нержавеющей стали
Кто мы? Мы являемся сертифицированным ISO производителем отливок из нержавеющей стали в Китае. Мы являемся одной из лучших сталелитейных компаний .
Что такое отливка из нержавеющей стали?
Сталь — это сплав, состоящий из железа и углерода, где термин «сталь» используется для обозначения амальгам железа с ограниченной долей углерода, которая должна быть менее 1,9%. Когда в чугуне содержится более 2% углерода, это чугун, а не сталь.
Нержавеющая сталь, также называемая INOX, — это сталь, известная своей стойкостью к коррозии после контакта с водой.Помимо основных компонентов, железа и углерода, нержавеющая сталь дополнительно содержит хром (Cr) и никель (Ni). Прежде чем его можно будет назвать нержавеющей сталью, в составе стали должно быть не менее 12% хрома. Помимо основных компонентов, широкий ассортимент нержавеющей стали также содержит азот, марганец, молибден или кремний. Мы являемся одной из литейных компаний и обеспечиваем нержавеющую сталь с лучшими свойствами.
В любом случае, каково влияние компонентов хрома и никеля на нержавеющую сталь? В момент взаимодействия хрома с кислородом происходит химическая реакция, в результате которой образуется незаметный слой оксида хрома (Cr2O3). Это иначе называют «оксидной пленкой». Этот слой защищает основной металл от ржавчины (окисления). В любой момент, когда оксидная пленка повреждается, необходимо создать другой слой. Учитывая все обстоятельства, ржавчина может возникнуть на первый взгляд, когда поврежденный слой взаимодействует с водой. Эта ржавчина никогда не протолкнется, поскольку за это время снова образуется еще один оксидный слой.
Нержавеющая сталь с содержанием никеля от 6% до 26% является аустенитной и немагнитной по своей природе. Подразумевается, что никель в нержавеющей стали убивает магнитные воздействия хрома.В тот момент, когда в нержавеющей стали доступно умеренно большое количество хрома, а также ограниченное количество никеля, нержавеющая сталь может быть магнитной. Учитывая все обстоятельства, нержавеющая сталь, конечно же, не является немагнитной. Существуют также другие виды нержавеющей стали с ферритной структурой, которая содержит только хром, а не никель. По этой причине они не обладают магнитными свойствами.
Наши отливки из нержавеющей стали включают:
Сплавывключают аустенитную нержавеющую сталь — CF8 (304), CF3 (304L), CF8M (316), CF3M (316L), Monel®, купроникелевый сплав, Hastelloy®, Duplex Grade и другие сплавы на основе никеля.
Максимальный размер и вес: максимальный размер 1 метр x 1 метр x 1 метр и вес 650 фунтов (300 кг).
Свойства и качество нержавеющей стали:
Мы проводим химический анализ, испытания на механическую прочность, испытания по Шарпи, испытание на твердость по Бринеллю, неразрушающий контроль рентгеновских лучей и испытания под давлением. Сертификация материалов сторонними лабораториями часто предоставляется международным клиентам. Мы можем следовать этим стандартам: ASTM, SAE, AISI, BS и т. Д.
Мы являемся одной из компаний по литью нержавеющей стали в Китае и работаем в следующих отраслях:
Насосная и арматурная промышленность, медицинское оборудование, пищевая промышленность, строительное оборудование, военное дело, нефтепереработка, морская арматура и промышленное оборудование.
Литейное производство стали | China Dawang Steel Casting Company
Дефект 1 отверстие
Дефект отверстия включает пористость, усадку, усадку, отверстие для шлака, отверстие для песка, железную фасоль. №
Профилактические мероприятия:
Пористость: шихта должна быть очищена, ферросплав должен хорошо пропечься, ковш должен хорошо пропечься при разливке; температура и время перегрева расплавленного металла должны контролироваться разумным процессом плавления, скорость охлаждения отливок должна быть увеличена или затвердевать под давлением, а газ должен выпадать в осадок; следует выбрать соответствующий процесс заливки, систему вентилей и условия заливки, чтобы облегчить выпуск газа; следует улучшить воздухопроницаемость оболочки формы, а при необходимости добавить выпускное отверстие; следует добавить подходящую температуру расплавленного металла, температуру разливки и температуру обжига оболочки формы; оболочка формы для запекания должна быть полностью прожарена; размер частиц связующего и огнеупора следует выбирать разумно.
Усадка: правильная конструкция литниковой системы для облегчения литья и последовательного затвердевания и усадки; улучшение структуры отливки с целью сделать толщину стенок как можно более однородной или увеличить технологические субсидии и холодное железо; использование соответствующего процесса разливки, такого как разливка при высокой или низкой температуре; увеличить скорость охлаждения пресс-формы или разумное формирование пресс-формы, увеличить расстояние между восковыми формами и улучшить условия локального рассеивания тепла; снизить температуру расплавленного металла при разливке и увеличить высоту напора; при необходимости выберите плавильный сплав с низкой усадкой.
Усадка: регулировка состава сплава, уменьшение диапазона затвердевания сплава, полное раскисление и дегазация во время плавления и разливки, чтобы уменьшить влияние газа на усадку при затвердевании; улучшить структуру отливки, разумно настроить систему разливки, увеличить высоту напора и увеличить усадочную способность; выбрать подходящий процесс разливки, строго контролировать температуру разливки расплавленного металла; выбрать материал оболочки с хорошей теплопроводностью, улучшить условия охлаждения отливок и увеличить скорость охлаждения отливок; улучшить положение внутренних ворот, что способствует последовательному затвердеванию.
Отверстие для песка: содержите воск и шток заслонки в чистоте, не допускайте попадания корпуса формы в полость во время депарафинизации, обработки, хранения, обжарки, заливки или заполнения песком. Перед заливкой следует использовать пылесос для очистки полости формы; выбрать подходящий материал оболочки, разумный процесс изготовления оболочки, строго работать, избегать расслоения слоя оболочки; улучшить конструкцию системы стробирования, избегать прямого ввода огнеупорного материала в полость и замедлить воздействие расплавленного металла на поверхности полости; обратите внимание на операцию заливки, замедлите и ускорите перед заливкой, избегайте сильного размыва расплавленного металла в полость.
Шлаковое отверстие: усилить управление загрузкой, использовать чистую загрузку при плавке; используйте надлежащее количество шлакообразующего агента и раскислителя при плавке, расплавленный металл должен иметь достаточное статическое время, что способствует всплыванию шлака; перед разливкой удалить шлак на ковше; улучшить конструкцию стробирующей системы; Увеличьте высоту сопла ковша до чашки шибера.
Железная фасоль: при нанесении покрытия на первые два слоя обратите внимание на операцию, чтобы устранить острый угол, угловой пузырь; новое покрытие должно быть статичным в течение определенного времени, при добавлении смачивающего агента следует добавить соответствующее количество пеногасителя; восковую форму перед нанесением покрытия необходимо обезжирить; улучшить дизайн отливки, острый угол, угол должен быть плавным переходом.
2 шизоидных дефекта
К трещинам относятся: горячая трещина, холодная трещина.
Профилактические меры:
Горячие трещины: улучшить структуру отливки, сделать толщину стенок максимально равномерной, увеличить скругленный угол отливки или добавить технологическую полосу; улучшить материал оболочки или уменьшить количество слоев оболочки, добавить соответствующее количество добавки, увеличить температуру заливки, увеличить уступку оболочки; улучшить конструкцию системы заливки; выбрать разумный процесс заливки; выбирать материалы с низкой склонностью к термическому растрескиванию, поддерживать чистоту печи, выбирать разумный процесс плавки, добавлять редкоземельные элементы в соответствующем количестве, улучшать жаропрочность и пластичность отливок.
Холодная трещина: улучшение структуры отливки, например равномерная толщина стенок, устранение острого угла, добавление технологической арматуры, контроль скорости охлаждения для адаптации к усадке сплава; использовать печь с меньшим содержанием фосфора, применять разумный процесс плавления, снизить содержание примесей, улучшить качество расплавленного металла; При очистке отливок или снятии ворот сила удара не должна быть слишком большой.
3 Поверхностные дефекты отливок
Поверхностные дефекты включают налипание песка, образование царапин, прижим песка и холодную изоляцию.
Профилактические меры:
Шлифовка: разумный выбор материалов оболочки и обеспечение их качества, полное раскисление, минимизация окисления расплавленного металла и удаление образующихся оксидов; контроль влажности и сроков хранения скорлупы на месте хранения, использование разумного процесса обжарки; правильное снижение температуры расплавленного металла и температуры корпуса при разливке; улучшение конструкции отливки и теплоотвода деталей; надлежащее улучшение вязкости поверхностного покрытия; правильное снижение температуры расплавленного металла при разливке; надлежащее снижение температуры заливки формованной оболочки; правильное уменьшение высоты напора.
Рубцевание: покрытие необходимо полностью перемешать, после развешивания на воздухе хорошо просохнуть и полностью затвердеть; снизить плотность связующего в поверхностном покрытии; снизить температуру расплавленного металла и оболочки при правильной заливке, уменьшить оксид в расплавленном металле и включения с низкой температурой плавления на поверхности оболочки; улучшить структуру отливки.
Зажим песка: предотвращение расслоения оболочки формы, выбор разумного процесса разливки, снижение напряжения, предотвращение разрыва внутренней поверхности оболочки формы, улучшение структуры отливки, предотвращение большой плоскости или вогнутости, насколько это возможно, правильное проектирование внутреннего литника, предотвращение местного перегрева; Выбрать разумный процесс изготовления оболочки и строго выполнять, полностью затвердеть или хорошо высохнуть, сделать покрытие плотным сочетанием, улучшить прочность оболочки.
Холодная изоляция: должным образом увеличьте температуру расплавленного металла и корпуса во время разливки, улучшите конструкцию литниковой системы, увеличьте количество и положение поперечного сечения и внутренней литниковой системы, чтобы сократить время заполнения расплавленным металлом в полости ; должным образом увеличьте скорость разливки, сделайте так, чтобы расплавленный металл входил в полость непрерывно и плавно, и избегайте явления прерывания потока; при разливке заранее залить в ковш укрывное средство, чтобы предотвратить вторичное окисление расплавленного металла; сделать заливку расплавленным металлом плавно во время заливки.
4 Дефекты размера, формы и веса
К габаритной форме и массе неквалифицированных дефектов относятся: летающие крылья, неправильная заливка, деформация, дислокация, остатки в полости, ямки, включения.
Профилактические меры:
Fly wing: строго контролировать температуру и давление парафинизации воска
Производитель стальных отливок | Стальные отливки Sawbrook
Sawbrook Steel Casting, LLC. с 1924 года производит отливки из высококачественной углеродистой и низколегированной стали в Цинциннати, штат Огайо.По сей день мы продолжаем производить стальные отливки размером от 1 фунта до 12 500 фунтов, чтобы удовлетворить потребности наших клиентов.
Заявление о миссии
Sawbrook Steel Casting, LLC стремится обеспечить исключительную производительность для наших клиентов и развивать прочные отношения за счет высококачественного литья, отличного обслуживания клиентов и своевременных поставок.
Политика качества
Sawbrook Steel Casting, LLC стремится производить высококачественные стальные отливки по конкурентоспособным ценам.В Sawbrook Steel Casting, LLC все сотрудники несут ответственность за качество. Мы стремимся постоянно улучшать наши процессы, систему качества и цели в области качества, чтобы гарантировать, что клиент получает максимальную продукцию и удовлетворяет потребности клиентов.
Сталь 101
Хотите узнать больше о процессе производства отливок? Компания Sawbrook Steel Casting, LLC разработала эту презентацию Steel 101, чтобы дать вам подробный обзор нашей деятельности.
Foundry News
Более 85 лет обслуживания сталелитейной промышленности во всем мире
Более 85 лет компания Sawbrook Steel Castings Co.является лидером в производстве отливок из высококачественной углеродистой и низколегированной стали для широкого спектра отраслей промышленности по всему миру.
Одобрено АБС
Компания Sawbrook Steel Castings была добавлена в утвержденный список литейных предприятий Американского бюро судоходства.
Служба поддержки клиентов
Наши сотрудники службы поддержки клиентов чрезвычайно хорошо осведомлены во всех аспектах стального литья и занимаются обслуживанием до, во время и после покупки.Наш технический персонал готов ответить на любые ваши вопросы.
Возможности шаблонов
Sawbrook Steel имеет на месте современную мастерскую по шаблонам, способную создавать новые шаблоны или вносить все необходимые корректировки. Узнайте больше о наших возможностях разработки выкроек.
Чтобы узнать больше о решениях по поставке отливок , посетите наши дочерние компании в группе Speyside Metal Forming Group.
Лучшее стальное литье — выгодные предложения от мировых продавцов стального литья
Отличные новости !!! Вы попали в нужное место для стального литья.К настоящему времени вы уже знаете, что что бы вы ни искали, вы обязательно найдете это на AliExpress. У нас буквально тысячи отличных продуктов во всех товарных категориях. Ищете ли вы товары высокого класса или дешевые и недорогие оптовые закупки, мы гарантируем, что он есть на AliExpress.
Вы найдете официальные магазины торговых марок наряду с небольшими независимыми продавцами со скидками, каждый из которых предлагает быструю доставку и надежные, а также удобные и безопасные способы оплаты, независимо от того, сколько вы решите потратить.
AliExpress никогда не уступит по выбору, качеству и цене. Каждый день вы будете находить новые онлайн-предложения, скидки в магазинах и возможность сэкономить еще больше, собирая купоны. Но вам, возможно, придется действовать быстро, так как эти лучшие стальные отливки в кратчайшие сроки станут одним из самых востребованных бестселлеров. Подумайте, как вам будут завидовать друзья, когда вы скажете им, что купили стальные отливки на AliExpress.Благодаря самым низким ценам в Интернете, дешевым тарифам на доставку и возможности получения на месте вы можете еще больше сэкономить.
Если вы все еще не уверены в стальных отливках и думаете о выборе аналогичного товара, AliExpress — отличное место для сравнения цен и продавцов. Мы поможем вам разобраться, стоит ли доплачивать за высококачественную версию или вы получаете столь же выгодную сделку, приобретая более дешевую вещь.А если вы просто хотите побаловать себя и потратиться на самую дорогую версию, AliExpress всегда позаботится о том, чтобы вы могли получить лучшую цену за свои деньги, даже сообщая вам, когда вам будет лучше дождаться начала рекламной акции. и ожидаемая экономия.AliExpress гордится тем, что у вас всегда есть осознанный выбор при покупке в одном из сотен магазинов и продавцов на нашей платформе. Реальные покупатели оценивают качество обслуживания, цену и качество каждого магазина и продавца.Кроме того, вы можете узнать рейтинги магазина или отдельных продавцов, а также сравнить цены, доставку и скидки на один и тот же продукт, прочитав комментарии и отзывы, оставленные пользователями. Каждая покупка имеет звездный рейтинг и часто имеет комментарии, оставленные предыдущими клиентами, описывающими их опыт транзакций, поэтому вы можете покупать с уверенностью каждый раз. Короче говоря, вам не нужно верить нам на слово — просто слушайте миллионы наших довольных клиентов.
А если вы новичок на AliExpress, мы откроем вам секрет.Непосредственно перед тем, как вы нажмете «купить сейчас» в процессе транзакции, найдите время, чтобы проверить купоны — и вы сэкономите еще больше. Вы можете найти купоны магазина, купоны AliExpress или собирать купоны каждый день, играя в игры в приложении AliExpress. Вместе с бесплатной доставкой, которую предлагают большинство продавцов на нашем сайте, вы сможете приобрести steel castings по самой выгодной цене.
У нас всегда есть новейшие технологии, новейшие тенденции и самые обсуждаемые лейблы.На AliExpress отличное качество, цена и сервис всегда в стандартной комплектации. Начните самый лучший шоппинг прямо здесь.
Что такое инвестиционное литье? — Процесс литья по выплавляемым моделям
Что такое отливка по выплавляемым моделям?
Литье по выплавляемым моделям относится к керамике, сформированной вокруг восковых моделей для создания оболочки для разливаемого расплавленного металла.После создания восковых узоров их расплавляют на затворной системе, погружают в суспензию и песок, чтобы сформировать многослойный кожух, а затем заменяют расплавленными металлами, такими как нержавеющая сталь, алюминий и многое другое. Ниже приведены короткие видеоролики с некоторыми этапами процесса литья по выплавляемым моделям.
Как изготавливаются отливки по выплавляемым моделям?
Разработка отливок по выплавляемым моделям включает создание оригинального воскового рисунка, покрытие изображения гипсом и построение последовательных слоев до тех пор, пока модель не окутается прочной оболочкой.После расплавления воска в форму заливается расплавленная сталь, нержавеющая сталь или бронза, создавая идеальную копию оригинального воскового узора. По сравнению с механической обработкой, литье по выплавляемым моделям экономично обеспечивает поднутрения, высокое разрешение, сложные детали и гладкую поверхность.
Чаще всего литье по выплавляемым моделям — единственный способ экономичного изготовления детали.
Часто задаваемые вопросы
Отливки по выплавляемым моделям используются в широком спектре отраслей промышленности, включая огнестрельное оружие, общественное питание, газовую и нефтяную промышленность, а также в энергетической промышленности.Хотя это некоторые из отраслей, обслуживаемых методом литья по выплавляемым моделям, Milwaukee Precision Casting обслуживает не только их. Отливки по выплавляемым моделям можно использовать практически для всего, где требуется сталь, алюминий, латунь и многие другие материалы.
Milwaukee Precision Casting может предложить широкий спектр отделочных работ, включая: механическую обработку, термообработку, неразрушающий контроль, полировку, пассивацию / электрополировку, удаление заусенцев / полировку шариков, лазерное травление, нанесение покрытия, упаковку и многое другое, в зависимости от потребностей любой детали. .Компания Milwaukee Precision Casting поддерживает тесные отношения со многими местными поставщиками, чтобы предлагать лучшие детали по минимально возможной цене.
Разница в прочности между отливками и другими методами обработки металла, пока есть, незначительна. Отливки по выплавляемым моделям уже много лет используются в военной, аэрокосмической и медицинской областях, и до сих пор используются в этих отраслях. Благодаря испытаниям и тщательной проверке мы можем гарантировать, что ни одна деталь, выпускаемая Milwaukee Precision Casting, не будет соответствовать самым строгим требованиям.
ПОДРОБНЕЕ Часто задаваемые вопросы
Что такое отливки по выплавляемым моделям из воска?
Благодаря впрыскиванию воска в штамп для постоянного формования для формирования восковых моделей, литье по выплавляемым моделям является решением для многих сложных деталей, требующихся в больших количествах. Мы производим отливки по выплавляемым моделям по выплавляемым моделям от нескольких граммов до 40 фунтов и можем экономично производить небольшие партии с помощью ручного инструмента или большие объемы с использованием многогнездных автоматических форм.
Происхождение литья по выплавляемым моделям, также известного как процесс литья по выплавляемым моделям, восходит к 1100/1700 г. до н.э. Работы созданы из восковых моделей ручной лепки с тонкими деталями. В послевоенный период этот процесс развился и распространился практически на все отрасли и рынки, как это наблюдается сегодня.
Почему Milwaukee Precision Casting, Inc.?
Свойства материала для литья под давлением
Найдите свойства, настроив фильтры ниже.
Твердость
Алюминий-бронза C95400 литье RB85 Алюминий-бронза
Инконель 600 литой RB90 Инконель
Алюминиевая бронза C95400 закаленная и отпущенная RB91-RB96 Алюминий-бронза
Алюминиевая бронза C95500 закаленная и отпущенная RB91-RB96 Алюминий-бронза
Алюминиевая бронза C95500 в литом виде RB98 Алюминий-бронза
Инконель 625 отожженный RC20 Инконель
Кобальт 6 литой RC45 Углеродистый никель
8630 Закаленная сталь RC25-RC50
4340 Закаленная сталь RC20-RC55
4140 Закаленная сталь RC29-RC57
8640 Закаленный никель-хром-молибден RC30-RC60
6150 Закаленный RC30-RC60 Углерод-хром
Прочность на разрыв
Инконель 600 литой 75000 Инконель
Алюминиевая бронза C95400 литая 85,000 Алюминиевая бронза
Инконель 625 отожженный 100000 Инконель
Алюминиевая бронза C95500 закаленная и отпущенная 100,000 Алюминиевая бронза
Кобальт 36 в литом состоянии 105000 КобальтАлюминиевая бронза C95400 закаленная и отпущенная 105,000 Алюминиевая бронза
Алюминиевая бронза C95500 в литом виде 120,000 Алюминиевая бронза
8620 Закаленный 130000 углерод-никель-хром-молибден
8630 Закаленная 170,000 Сталь
8640 Закаленный 200000 Никель-Хром Молибден
4140 Закаленная 200000 Сталь
4340 Закаленная 200000 Сталь
6150 Закаленная 200000 Углерод-хром
Castablility
Алюминий бронза C95400 литой алюминий-бронза
Алюминиевая бронза C95400 Закаленная и отпущенная алюминиевая бронза
Алюминиевая бронза C95500 Закаленная и отпущенная Алюминий-бронза
Алюминий бронза C95500 литой алюминий-бронза
Инконель 600 литой Инконель
8620 Углеродно-никелевый закаленный
8630 Закаленная сталь
8640 Никель-хромомолибден закаленный
Инконель 625 отожженный Инконель
4140 Закаленная сталь
4340 Закаленная сталь
6150 Углерод-хром закаленный
.2% Предел текучести
Инконель 600 литой 35-40 000 Инконель
Алюминий бронза C95400 литой 30-40,000 Алюминий-бронза
Алюминиевая бронза C95500 закаленная и отпущенная 40-50,000 Алюминий-бронза
Алюминиевая бронза C95400 закаленная и отпущенная 45-55,000 Алюминий-бронза
Инконель 625 отожженный 40-55000 Инконель
Алюминий бронза C95500 в литом виде 60-70,000 Алюминий-бронза
Кобальт 36 в литом виде 60-70,000 Кобальт8620 Закаленный 80-110 000 Углерод-Никель Хром Молибден
8630 Закаленная сталь 100-130 000
4140 Закаленная 100-155000 Сталь
6150 Закаленная 120-180 000 Углерод-Хром
4340 Закаленная сталь 100-180 000
8640 Закаленный 100-180 000 Никель-Хром Молибден
% удлинение
Наименее пластичный Самый пластичныйАлюминий бронза C95500 литой 5-8% Алюминий-бронза
Алюминиевая бронза C95500 закаленная и отпущенная 6-10% Алюминий-бронза
Алюминиевая бронза C95400 закаленная и отпущенная 6-10% Алюминий-бронза
6150 Закаленная 5-10% углерод-хром
Инконель 600 в литом виде 10-20% Инконель
Алюминий бронза C95400 литой 10-20% алюминий-бронза
Кобальт 36 в литом виде 15-20% кобальта8620 Закаленный 10-20% углерод-никель, хром, молибден
8630 Закаленная 7-20% сталь
4140 Закаленная сталь 5-20%
4340 Закаленная сталь 5-20%
8640 Закаленный 5-20% никель-хром-молибден
Инконель 625 отожженный 15-30% Инконель
.