Технология производства МДФ — mebeldok.com
Материалы «
Понятие современного МДФ материала произошло от английского MDF (Medium Density Fiberboards), что переводится как древесноволокнистая плита со средней плотностью. Впервые изготавливать МДФ начали в Америке в 1966 году. В СНГ производство этого незаменимого сегодня материала освоили только в 1997-м.
Как делают МДФ
Производство МДФ схоже с технологией производства ДСП и ДВП, хотя по своей прочности этот материал превышает прочность древесно-стружечных плит почти в 2 раза. Также МДФ является экологически чистым материалом, не причиняющим вреда здоровью человека. Чтобы понять, как удалось достичь таких замечательных показателей, давайте более детально углубимся в изучение процесса изготовления данного материала.
Технология производства МДФ состоит из нескольких этапов:
- 1. Первый этап – подготовка сырья. Для производства МДФ используют круглые бревна, которые очищают от коры с помощью станков, рубят в щепу в специальных машинах.
Щепу сортируют, промывают для удаления грязи, песка, камешков и производят нагревание паром.
- 2. На втором этапе подготавливают волокна. В рафинере материал проходит измельчение. Полученная масса связывается веществом, которое выделяется при нагревании древесины, лигнином, а также другими природными, а не синтетическими смолами. Поэтому специалисты по изготовлению МДФ с уверенностью могут сказать, что это один из самых экологически чистых продуктов. Затем материал проходит сушку, где он сушится и получает однородную по влажности массу. Далее с помощью циклонов из нее вытягивают воздух.
- 3. Третий этап технологии производства МДФ — это формирование ковра и подпрессовка. Волокно проходит обработку на специальном формировочном станке, где благодаря формировочным роликам оно выравнивается. Затем полученный ковер взвешивают на весах и проводят предварительное прессование, выдавливая таким способом из плиты воздух.
- 4.
Заключительный, четвертый этап — прессование. Плита проходит главный пресс, из которого поступает готовая лента МДФ. Ее режут делительной пилой и охлаждают 20-25 минут.
Декоративная обработка МДФ
Существует еще один важный момент – шлифование панели МДФ. Готовые плиты проходят шлифование с целью выравнивания толщины, придания поверхности гладкости и удаления внешних дефектов. Дальше плиты могут отправляться потребителю, либо уходить на декоративную отделку, которая делится на три категории: окрашивание МДФ (красками или эмалями), ламинирование МДФ (плёнкой ПВХ) и шпонирование МДФ (путем приклеивания шпона из ценных пород деревьев).
Процесс того, как делают МДФ, проверяется лабораториями по многим параметрам: по влагостойкости, плотности, шероховатости, разбуханию, прочности и т.д.
Сегодня МДФ широко используют для изготовления мебельных фасадов, для отделки интерьера (потолочные и стеновые панели, планки, плинтусы, профили), для производства столярных изделий, таких как двери и наличники, под основу ламинированного паркета. Преимущество плит МДФ – их гигиеничность и безопасность в быту благодаря устойчивости к различным грибкам и микроорганизмам. Плиты МДФ имеют плотность 700-870 кг/м3, что дает возможность обрабатывать их на фрезерных станках и получать различные рельефы. Также этот материал легко монтируется и не требует специальных инструментов и оборудования. Его отдельные части легко заменяются при необходимости.
Плиты МДФ отличаются особой долговечностью, так как материал не коробится, не трескается и не рассыхается от перемены температуры. Для этого он обработан специальными пропитками, которые не требуют повторного покрытия лаком или подкраски. Таким образом, технология производства МДФ дала возможность широкому кругу потребителей получить материал высокого качества за доступную цену.
Материалы «
Технология производства МДФ
Что представляет собой МДФ
Изготовление плит МДФ отличается особой тщательностью обработки. Такая древесноволокнистая плита делается по технологии изготовления бумаги. Сырье для этих плит готовится аналогично. Измельчение происходит до отдельных волокон дерева, поэтому производство МДФ использует любые отходы деревообрабатывающей промышленности. МДФ это английская аббревиатура словосочетания древесно-стружечная плита.
Этапы производства МДФ следующие:
- измельчение древесных отходов до состояния пыли;
- термообработка в печи;
- прессовка;
- обработка;
- декорирование.
В дизайне внутренних жилых помещений нарастает объем использования панелей МДФ. Это тонкие, похожие на картон листы.
Панели МДФ бывают:
- шпонированные;
- ламинированные;
- окрашенные.
Ламинированные панели МДФ самые популярные. Некоторые из них имеют респектабельный вид, неотличимый от натурального дерева. Окрашенные панели МДФ самые дешевые. Их отличительная особенность от других древесно-стружечных плит в том, что красят их не под натуральное дерево.
Технология производства МДФ панелей делает их похожими на фанеру. Этот материал используется для декорирования стен и потолков под дерево. Такие панели неотличимы от натурального дерева, а стоят значительно дешевле.
Технология производства МДФ
Стружки и опилки измельчаются и крошатся, потом сырье пропаривается подающимся под давлением паром. Очищенная и пропаренная масса измельчается еще раз на дефибрере, до самых маленьких размеров частиц.
После этого сырье сушится и смешивается с карбамидными смолами. На конечном этапе производства происходит горячее прессование плит МДФ. По такой технологии получается материал, во многом не уступающий натуральному деревянному массиву. Плита МДФ стоит дороже других материалов. Поэтому этот материал используют в мебельной промышленности для изготовления фасадов.
Технология производства МДФ позволяет придавать этим плитам особые качества. Чаще всего увеличивают их влагостойкость и уменьшают горючесть. Волокно, из которого делается МДФ, придает плитам различный цвет в зависимости от используемой древесины.
Для мебельного производства и обработки внутренних помещений плиты МДФ декорируют. Мебель изготовленная из этого материала популярна. Метод обработки панелей и фасадов позволяет соблюдать нужные дизайнеру линии.
Преимущества материала МДФ
Экологичность
Это самый экологичный заменитель древесины, потому что производится с помощью карбамидных смол, которые выделяют мало вредного формальдегида. Из некоторых видов МДФ разрешается даже делать детскую мебель.
Устойчивость к влаге
Из древесных заменителей плиты МДФ лучше всех сопротивляются влажности. Древесноволокнистые плиты МДФ настолько плотные, что при попадании в воду держат форму дольше некоторых пород дерева. Если намокает только декорированная поверхность, форма плиты не изменяется.
Легкость обработки
Плиты МДФ из-за своей уникальной плотности лучше других материалов поддаются обработке, их можно пилить и фрезеровать. Фигурную поверхность на плитах других заменителей дерева, не имеющих такой плотности материала, сделать не получится.
Легкость декорирования
Плиты МДФ сразу поступают на декоративное покрытие, настолько они гладкие. Остальные виды заменителей дерева сначала шлифуют, а потом декорируют.
Удержание крепежа
Мебель из МДФ можно неоднократно собирать и разбирать, тогда как, мебель из ДСП не разбирается, шурупы второй раз не ввинтишь. Из-за этого мебель ДСП перевозить нельзя.
24.06.2019
Как сделать МДФ?
Справочная информация:
Композитные лесоматериалы или инженерная древесина относятся к материалам, изготовленным из древесины, которые склеены между собой. В Соединенных Штатах ежегодно производится около 21 миллиона тонн (21,3 миллиона метрических тонн) композитной древесины. К наиболее популярным композиционным материалам относятся фанера, столярные плиты, ДВП, ДСП и клееный брус. Большинство этих продуктов основано на том, что ранее было древесными отходами или малоиспользуемыми или некоммерческими породами. При производстве композитов теряется очень мало сырья.
Древесноволокнистая плита средней плотности (МДФ) — это общий термин для панели, состоящей в основном из лигноцеллюлозных волокон в сочетании с синтетической смолой или другой подходящей связующей системой и соединенных вместе под воздействием тепла и давления. Панели сжимаются до плотности от 0,50 до 0,80 по удельному весу (31-50 фунтов/фут3). Во время производства могут быть введены добавки для улучшения определенных свойств. Поскольку древесноволокнистую плиту можно разрезать на самые разные размеры и формы, у нее множество применений, включая промышленную упаковку, дисплеи, экспонаты, игрушки и игры, мебель и шкафы, стеновые панели, молдинги и дверные детали.
Поверхность МДФ плоская, гладкая, однородная, плотная, без сучков и зернистости, что делает отделочные работы более легкими и однородными. Однородная кромка МДФ позволяет выполнять сложные и точные методы обработки и отделки. Отходы обрезков также значительно сокращаются при использовании МДФ по сравнению с другими подложками. Улучшенная стабильность и прочность являются важными преимуществами МДФ, при этом стабильность способствует соблюдению точных допусков в точно вырезанных деталях. Это отличная замена массивной древесине во многих интерьерах. Производители мебели также чеканят поверхность объемными рисунками, поскольку МДФ имеет такую ровную текстуру и стабильные свойства.
За последние 10 лет рынок МДФ в США быстро вырос. Отгрузки увеличились на 62%, а мощность завода выросла на 60%. Сегодня в Америке ежегодно потребляется более миллиарда квадратных футов (93 миллиона квадратных метров) МДФ. Мировые мощности MDF увеличились на 30% в 1996 году до более чем 12 миллиардов квадратных футов (1,1 миллиарда квадратных метров), и в настоящее время действует более 100 заводов.
История:
МДФ был впервые разработан в Соединенных Штатах в 1960-х годах, производство началось в Депости, Нью-Йорк. Аналогичный продукт, оргалит (прессованное древесноволокнистое покрытие), был случайно изобретен Уильямом Мейсоном в 1925, когда он пытался найти применение огромному количеству древесной щепы, которую выбрасывали лесопилки. Он пытался впрессовать древесное волокно в изоляционную плиту, но изготовил прочный тонкий лист, забыв выключить свое оборудование. Это оборудование состояло из паяльной лампы, печатного станка восемнадцатого века и старого автомобильного котла.
Сырье:
Древесная щепа, стружка и опилки обычно являются сырьем для производства древесноволокнистых плит. Однако, поскольку вопросы вторичной переработки и защиты окружающей среды становятся нормой, также используются макулатура, кукурузные рыльца и даже багасса (волокна сахарного тростника). Другие материалы также перерабатываются в МДФ. Одна компания использует сухие отходы
Древесная щепа, стружка и опилки обычно являются сырьем для изготовления древесноволокнистых плит. Однако с учетом того, что вопросы вторичной переработки и защиты окружающей среды становятся нормой, используются макулатура, кукурузные рыльца, багасса (волокна сахарного тростника), картон, картонные контейнеры для напитков, содержащие пластик и металлы, телефонные справочники и старые газеты.
из расчета 100 000 тонн в год. Помимо древесных отходов, на этом предприятии используется картон, картонная тара из-под напитков, содержащая пластмассу и металл, телефонные справочники и старые газеты. Синтетические смолы используются для соединения волокон вместе, а другие добавки могут использоваться для улучшения определенных свойств.
Передовые технологии и обработка улучшили качество древесноволокнистых плит. К ним относятся инновации в подготовке древесины, рецепты смол, технология прессования и методы шлифования панелей. Усовершенствованная технология прессования позволила сократить общие циклы прессования, а антистатическая технология также способствовала увеличению срока службы ленты в процессе шлифования.
Подготовка древесины- 1 Производство качественных древесноволокнистых плит начинается с выбора и очистки сырья, большая часть которого перерабатывается из стружки и стружки, получаемых на лесопильных и фанерных заводах. Сырье сначала очищают от любых металлических примесей с помощью магнита.
Далее материал разделяется на крупные куски и мелкие хлопья. Хлопья разделяются на штабеля опилок и щепы.
- 2 Материал снова проходит через магнитный детектор, при этом отбракованный материал отделяется для повторного использования в качестве топлива. Хороший материал собирается и отправляется в бункер для предварительного пропаривания. В бункер впрыскивается пар для нагрева и смягчения материала. Волокна подаются сначала в боковой шнековый питатель, а затем в поршневой шнековый питатель, который сжимает волокна и удаляет воду. Затем сжатый материал подается в рафинер, который разрывает материал на пригодные для использования волокна. Иногда волокно может пройти вторую стадию рафинирования, чтобы улучшить чистоту волокна. Моторы большего размера на рафинерах иногда используются для отсеивания посторонних предметов из процесса.
- 3 Смола добавляется перед стадией рафинирования для контроля допусков формальдегида в смеси, а после рафинирования добавляется катализатор.
- имеют уравновешенные системы одновременного закрывания, в которых используются гидравлические цилиндры для выравнивания плиты, что при работе в сочетании с четырехточечным управлением положением обеспечивает больший контроль толщины отдельных панелей.
Гидравлическая система может закрывать пресс со скоростью и давлением, которые уменьшают проблемы с предварительным отверждением плиты и сокращают общие циклы прессования.
- 4 Для получения гладкой поверхности панели шлифуются с помощью лент с абразивным покрытием. Обычно используется карбид кремния, но с учетом требований к более тонкой поверхности используются другие керамические абразивы, в том числе оксид циркония и оксид алюминия. Восьмиголовочное шлифовальное оборудование и двусторонняя планировка улучшают постоянную гладкость поверхности. Антистатическая технология используется для снятия статического электричества, которое способствует быстрой нагрузке и избыточной шлифовальной пыли, тем самым увеличивая срок службы ремня.
- 5 В зависимости от конечного продукта панели могут подвергаться различным этапам отделки. Возможно нанесение различных цветов лака, а также различных рисунков под дерево.
Гильотинная резка используется для резки ДВП на большие листы (например, шириной 100 дюймов). Для листов меньшего размера, таких как 42 на 49 дюймов (107 на 125 см), используется высечка. Специальные машины используются для резки ДВП на узкие полосы шириной от 1 до 24 дюймов (от 2,5 до 61 см).
- 6 Ламинаторы используются для нанесения на поверхность винила, фольги и других материалов. Этот процесс включает в себя разматывание рулона древесноволокнистого материала, его подачу между двумя валами, на которые наносится клей, соединение древесноволокнистой плиты с клеевым покрытием с ламинирующим материалом между другим набором валов и отправку объединенных материалов в ламинатор.
Контроль качества:
Большинство заводов МДФ используют компьютеризированный контроль процесса для контроля каждого этапа производства и поддержания качества продукции. В сочетании с непрерывными грузовыми лентами, измерителями основного веса, мониторами профиля плотности и толщиномерами поддерживается однородность продукта. Кроме того, Американский национальный институт стандартов установил спецификации продукта для каждого применения, а также предельные значения выбросов формальдегида. Поскольку экологические нормы и рыночные условия продолжают меняться, эти стандарты пересматриваются.
Самый последний стандарт для MDF, ANSI Standard A208.2, является третьей версией этого отраслевого стандарта. Этот стандарт классифицирует МДФ по плотности и использованию (внутри или снаружи) и выделяет четыре сорта продукции для внутренней отделки. Определенные спецификации включают в себя физические и механические свойства, допуски на размеры и пределы эмиссии формальдегида. Спецификации представлены как в метрических, так и в дюймово-фунтовых пределах.
Измеряемые физические и механические свойства готового продукта включают плотность и удельный вес, твердость, модуль разрыва, сопротивление истиранию, ударную вязкость, модуль упругости и предел прочности при растяжении. Кроме того, также измеряются водопоглощение, набухание по толщине и прочность внутренней связи. Американское общество испытаний материалов разработало стандарт (D-1037) для проверки этих свойств.
Будущее Хотя в 1996 г. было построено более 750 новых заводов, в 1997 г. ожидалось, что потребление МДФ упадет на 10% ниже прогнозируемого уровня. Показатели использования снизились для некоторых рынков, а экспорт сократился. Несмотря на эту тенденцию, некоторые заводы продолжат инвестировать в высокотехнологичное оборудование и экологический контроль для производства высококачественной продукции.
Экологические нормы будут по-прежнему бросать вызов промышленности древесноволокнистых плит. Хотя карбамидоформальдегидные смолы в основном используются в производстве МДФ из-за их низкой стоимости и характеристик быстрого отверждения, они имеют потенциальные проблемы с выделением формальдегида. Возможным решением являются фенолформальдегидные смолы, поскольку они не выделяют формальдегид после отверждения. Эти смолы, однако, более дорогие, но предварительные исследования показали, что их можно использовать в гораздо меньших количествах и добиться того же времени обработки, что и мочевинной смолы.
Строительство из МДФ — FineWoodworking
Предварительно обработанные поверхности плоские, как сланец на бильярдном столе, что, наряду с стабильностью размеров, делает его отличным основанием для облицовки. Кромки хорошо обрабатываются, без сколов, а МДФ принимает весь спектр столярных и крепежных изделий. Рискуя вызвать насмешки со стороны некоторых пуристов, я здесь, чтобы сделать смелое заявление: для окрашенных корпусов нет лучшего и более подходящего продукта, чем древесноволокнистая плита средней плотности (МДФ). И практически любой вид, доступный в качестве лицевого шпона фанеры лиственных пород, также доступен с сердцевиной из МДФ.
Конечно, идеальных материалов не бывает, но в случае с МДФ плюсы намного перевешивают минусы. МДФ недорог и чрезвычайно стабилен, и он производится одинаковой толщины (в отличие от большинства видов фанеры). В некотором смысле использование МДФ более экологично, чем использование цельного пиломатериала, потому что существует неисчерпаемый, возобновляемый источник сырья, из которого изготавливается МДФ, — источник, который будет доступен для будущих поколений. С другой стороны, листы МДФ тяжелые, и пыль, которая поднимается, когда вы режете и фрезеруете материал, может быть в лучшем случае раздражающей неприятностью; в худшем случае это может быть опасно для здоровья, если вы подвергаетесь экстремальному воздействию.
Что такое МДФ? Резьбовые стыковые соединения — самый простой способ соединения компонентов корпуса. Клей не очень эффективен, потому что края МДФ пористые.
До проведения исследования для подготовки к этой статье я мало что знал о МДФ, кроме того, что это древесный композит. Мне попались отраслевые документы, описывающие состав и производство МДФ в терминах, которые звучат почти так же, как язык, который вы ожидаете услышать в медицинской школе — целлюлозные волокна, трахеиды, пендисторы и дефибраторы. С точки зрения непрофессионала, большинство МДФ можно определить как панельные изделия, изготовленные из древесины, которая была измельчена в крошечные волокна, нагрета, смешана с клеем, спрессована до постоянной толщины, высушена и нарезана по размеру.
Печенье добавляет умеренной структурной мускулатуры. Бисквитные соединения можно быстро разрезать, и их можно легко выровнять без механических застежек. Шурупы можно добавить между печеньем. Сердечники МДФ не так прочны, как большинство пиломатериалов и фанеры, но при соединении кусков МДФ вы можете использовать практически любое соединение, которое вы использовали бы с фанерой: стыковые соединения с винтами, бисквиты, шлицы, полностью шпунтованные края и шпунтованные языки в зубчатых канавках. Вы также можете скосить края, если хотите, чтобы шов был незаметен в предварительно облицованной панели, но обязательно используйте много клея на скошенных краях, потому что они очень пористые.
МДФ имеет свои ограничения
Решение о том, использовать ли простые или сложные столярные изделия в шкафах, всегда зависит от решения. Большинство корпусов довольно просты, и их редко приходится проектировать, чтобы выдерживать большие нагрузки, поэтому достаточно стыковых соединений с помощью винтов. Но когда шкафы будут подвергаться нагрузкам (тяжелый телевизор, каменная столешница) или жестокому обращению (маленькие дети, которые любят хлопать дверьми), не скупитесь на клей и шурупы.
Вы должны просверлить направляющие отверстия подходящего размера всякий раз, когда ввинчиваете шуруп в кромку МДФ; в противном случае он легко расколется. Для работы с корпусом я предпочитаю использовать шпунтованный язычок в канавке с выступом. Это соединение не так важно для дополнительной клеевой поверхности и прочности, которое оно может обеспечить, как для помощи, которую оно оказывает при сборке больших шкафов. Это значительно упрощает работу, особенно если вы работаете в одиночку.
В промышленности различают три сорта МДФ по плотности: низкий (вес менее 40 фунтов на куб. фут), стандартный (от 40 до 50 фунтов на куб. фут) и высокий (более 50 фунтов). за куб. фут). И, как и любой продукт, производимый на конкурентной основе, существует огромное разнообразие видов и качества, даже в пределах класса стандартной плотности, который составляет большую часть производимых и продаваемых МДФ.
Сплайны стали немного прочнее. Они идеально выравнивают угловые соединения, а при достаточном количестве клея им не нужны винты или гвозди. Шаг вперед от стыков. Шпунты можно вырезать с помощью паза, установленного на настольной пиле, или с помощью фрезерного станка. Детали могут быть скреплены винтами или гвоздями. Для язычков и канавок с пазами требуется две установки. Вы должны фрезеровать соответствующие формы в сопрягаемых деталях, но сборка корпуса не составляет труда.
Устойчивые варианты
Карбамидоформальдегидные (UF) смолы были основным клеем для производства композитных панелей с момента его создания вскоре после Второй мировой войны. Смолы UF придают прочность и стабильность готовым панелям по разумной цене, но они обеспечивают лишь ограниченную влагостойкость.
Они также выделяют небольшое количество формальдегида, который может вызывать раздражение глаз и дыхательных путей и, возможно, вызывать более серьезные проблемы со здоровьем у людей с повышенной чувствительностью к нему. Если вы или член вашей семьи подходите под эту категорию, вы можете купить панель без формальдегида. Корпорация Medite производит Medex и Medite II — влагостойкие МДФ-панели для внутренних работ, выделяющие чрезвычайно низкий уровень формальдегида.
Обогащенные меламином UF-смолы и фенолформальдегидные (PF) смолы представляют собой клеи, иногда используемые для повышения водостойкости конечного продукта. Метилдиизоцианатные клеи используются в панелях из агроволокна по той же причине. Не существует такой вещи, как водостойкий МДФ, но Medex, который был разработан для ненесущих конструкций с высокой влажностью, таких как столешницы, шкафчики для ванных комнат, плинтусы и окрашенные подоконники, имеет высокую водостойкость.
В Руководстве покупателей и спецификаторов, опубликованном Ассоциацией композитных панелей, перечислены несколько заводов в Канаде, которые производят МДФ для наружных работ, используя в качестве сырья ель и сосну.
Для поверхностей, которые будут окрашиваться, МДФ не имеет себе равныхДля окрашенных шкафов, мебели, стеновых панелей и некоторых молдингов отлично подходит МДФ. Поверхностные поверхности поставляются с завода, отшлифованными до зернистости 150 или лучше, практически готовыми к покраске. Я быстро шлифую поверхность наждачной бумагой с зернистостью 120 или 150, чтобы удалить грязь и копоть и обеспечить лучшую адгезию грунтовочного слоя.
Грунтовка на основе растворителя для первого слоя.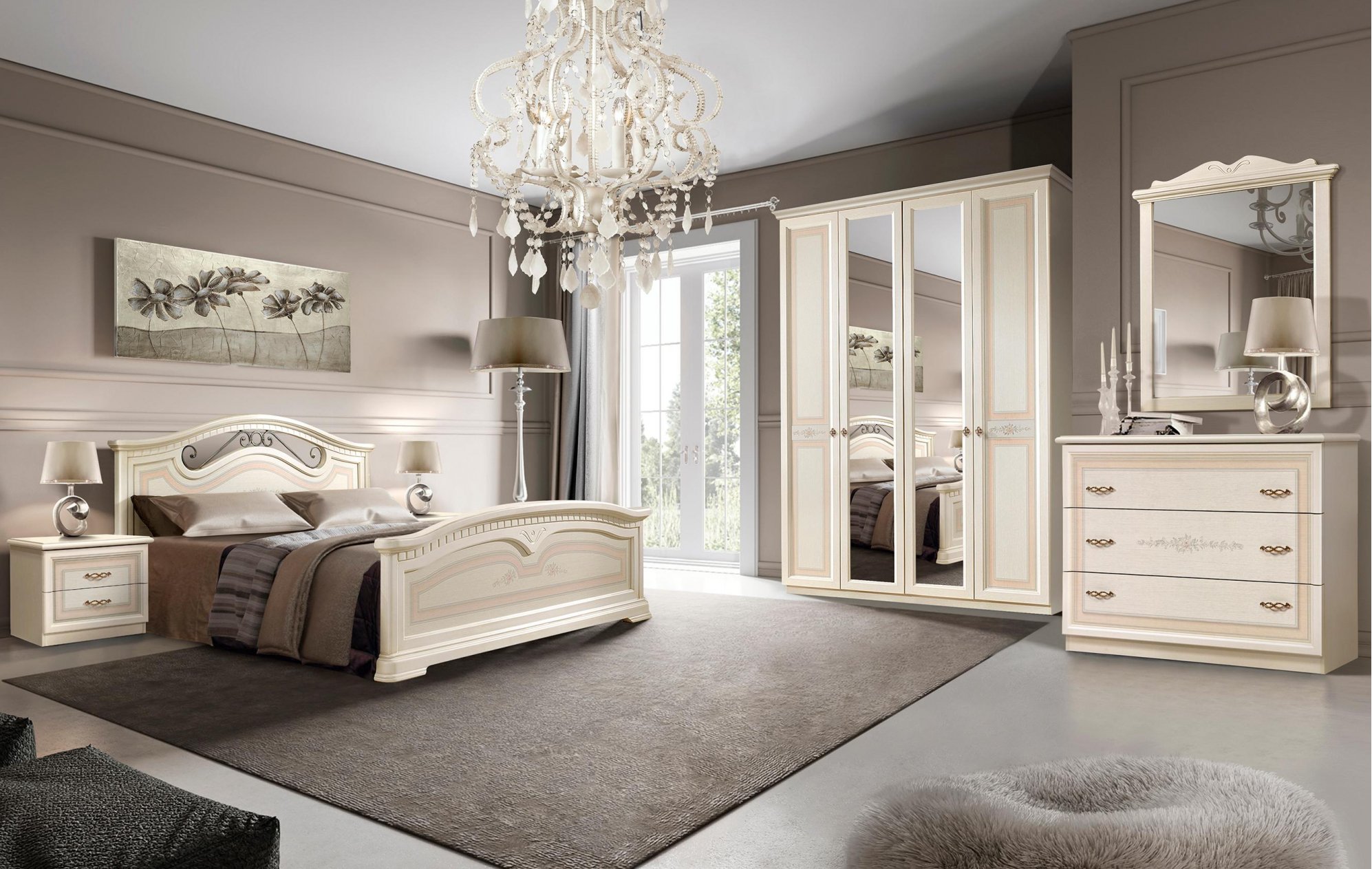
Грунтовки на основе растворителя (на основе масла, спирта или лака) обязательны. Никогда не используйте продукт на водной основе для начального финишного слоя. Древесные волокна будут слишком сильно набухать, когда они впитают воду, и вы получите то, что, по сути, является выпуклой текстурой на поверхности, которая не будет отшлифовываться. Однако после того, как поверхность была покрыта чем-то другим, краска на водной основе не окажет неблагоприятного воздействия на МДФ. Я использую латексную краску поверх должным образом запечатанных стеновых панелей и молдингов, но для окрашенной мебели или шкафов я предпочитаю качество отделки масляной или лаковой краской, наносимой с помощью пистолета-распылителя.
Я использую состав для гипсокартона, чтобы заполнить края, независимо от того, обрезаны ли они прямо или с помощью фрезы, и я наношу состав обильно пальцем или ладонью. В отличие от шпаклевки или обычных шпаклевок по дереву, смесь для гипсокартона имеет жидкую текстуру, поэтому она немного неаккуратна. Но после высыхания легко стирается.
Для краев, обработанных фрезером, вы можете использовать ту же фрезу в качестве скребка, чтобы удалить лишние комки пасты перед подкрашиванием краев наждачной бумагой с карбидом кремния зернистостью 220.
Быстрое соединение «шип-паз» на настольной пиле Два пропила, одно соединение. С помощью фрезы с головкой, настроенной на ширину паза, сначала вырежьте паз (слева).
Уильям Дакворт — столяр из Вудбери, штат Коннектикут, и бывший редактор Fine Woodworking.
Первоначально эта статья была опубликована в нашем новом выпуске стенда «Встроенные материалы» в 2006 году. Некоторая информация взята из Руководства столяра по древесноволокнистым плитам средней плотности.
Советы по покраске МДФ Закрепите края шпаклевкой для гипсокартона, чтобы обеспечить равномерное покрытие при покраске ДВП средней плотности. |