Древний мир бронзового литья: starcheolog — LiveJournal
Сенсационные знания древних, которые утаивают от простых людей: Вторцветмет в древнем мире, Причины хромоты Гефеста, Преимущества олова, Кипение холодной воды и иные секреты древнего бронзового литья.
Для тех, кто только присоединился — данный цикл показывает поступательное развитие металлургии от неолита до …
Продолжение цикла публикаций из энциклопедии «Металлургия и время».
Предыдущие статьи цикла:
Истоки рудной металлургии
Ювелирное искусство — основа металлургии
Древний мир бронзового литья
До тех пор пока люди не научились использовать железо, цветные металлы и их сплавы были основным материалом для изготовления вооружения, орудий труда, инструментов, предметов домашнего обихода и, естественно, украшений.
Главными металлургическими технологиями были литейные: искусство обработки жидкого металла позволяло получать уникальные бронзовые изделия и бытовые предметы. Именно в эту эпоху появились вещи, сопровождающие человека в его повседневном существовании, и инструменты, являющиеся символами основных технических профессий. Это время получило название бронзового века.
В 2000 г. Япония первой в мире провозгласила себя страной с «рециркуляционной» экономикой. Был принят ряд законов, направленных на максимальное использование вторичных ресурсов, в том числе металлического лома. Принцип «3R» сегодня знает каждый японский первоклассник: это «Recycling» (использование в качестве вторичных ресурсов), «Reuse» (повторное использование) и «Recovery» (восстановление вторичных материалов). Впервые официальное определение приведенных понятий было дано в Постановлении о переработке использованных автомобилей, принятом Евросоюзом в 1997 г. Однако подобные, причем очень строгие, законы о порядке переработки металлического лома существовали во всех великих империях Древнего мира: в Ассирии, Китае, Египте, Риме. Использование технологий бронзового литья и ковки позволяло с успехом воплощать принцип «3R» в древней цветной металлургии.
Древняя цветная металлургия
Ключевыми техническими преобразованиями бронзового века, продолжавшегося в течение двух тысячелетий, принято считать освоение ирригационного земледелия и полного металлургического цикла производства металлов, включавшего добычу руды, выжиг древесного угля, подготовку материалов, выплавку и рафинирование чернового металла, литье, ковку, волочение проволоки, другие виды металлообработки и рециклинг металлолома.
В этот период были освоены технологии выплавки и обработки металлов, получивших название «семь металлов древности»: меди, золота, свинца, серебра, железа, ртути и олова. Общепризнано, что определяющую роль в техническом прогрессе в бронзовую эпоху сыграло появление литых топоров, мечей и мотыг – основных видов орудий труда и оружия. Основой цивилизации стала металлургия меди и бронзы.
Топор. Село Кобан, Северная Осетия. Конец 2-го – начало 1-го тысячелетия до н.э.
Для производства меди повсеместно использовались как окисленные, так и сернистые руды. Месторождения меди обычно делятся на две зоны. Верхняя часть, находящаяся над уровнем грунтовых вод, представляет собой зону окисления. В ней располагаются минералы, основу которых составляют легковосстановимые оксиды меди – малахит, азурит. Нижняя, основная часть месторождения формируется сульфидными рудами – халькопиритом (CuFeS2) и халькозином (Сu2S). Содержание меди в сульфидных рудах намного ниже, чем в окисленных. После истощения верхних слоев человеку пришлось использовать более бедные сульфиды, а это потребовало разработки принципиально новых (инновационных) металлургических технологий.
Древние металлурги нашли решение проблемы. Было обнаружено, что добавление в шихту в достаточном количестве (около 30 %) красноватого или коричневого материала приводит к увеличению объема выплавки и повышению качества меди. Этим материалом была железная руда в виде гематита или лимонита, часто присутствующая на открытых частях месторождений халькопирита. Добавление железной руды принципиально изменяло процесс выплавки меди. Одним из продуктов реакций восстановления становился монооксид железа. При температуре около 1200 °С он реагировал с SiO2 пустой породы с образованием фаялита (Fe2SiO4), который превращался в основную составляющую жидкого шлака. Таким образом, железная руда играла роль флюса. Такая технология имела определяющее влияние на дальнейшее развитие металлургии. Шлак, образующийся при выплавке меди, практически идентичен шлаку, который позднее получался при выплавке железа в сыродутных горнах.
При использовании сернистых руд требовалось проведение ряда подготовительных операций. Широко практиковалось окисление раздробленной руды на воздухе в течение длительного времени. Благодаря воздействию влажного воздуха и атмосферных осадков руда обогащалась кислородом и теряла часть серы. Важную роль играл предварительный обжиг сернистой руды, при котором происходили выгорание серы и разрыхление руды. Его проводили в кучах, в специально устраиваемых ямах, а также в особых сооружениях – стойлах. Размеры стойл были значительны: их каменные стены достигали 12,5 м в длину и 1,5 м в ширину.
Повышение температурного уровня плавки зависело, прежде всего, от совершенствования техники и технологии дутья. Определяющую роль играло использование естественного дутья – силы ветра. Эффективными были печи, встраиваемые в естественный ландшафт. Они часто строились с подветренной стороны холма, имели соединяющиеся горизонтальный и вертикальный каналы, были обложены камнями и обмазаны глиной. В этом случае достигался «эффект трубы», усиливавший приток воздуха в агрегат. В поду некоторых печей были металлоприемники – углубления для установки горшков, в которые через специальные отверстия стекал металл.
Значительный прогресс последовал вслед за изобретением простейших ручных, а затем и ножных мехов. Они изготовлялись из шкур животных и представляли собой примитивный тип насоса с резервуарами, приспособленными для наполнения их воздухом. Ручные и ножные мехи широко использовались уже в 3-м тысячелетии до н. э. Металлургические печи с искусственным дутьем были, как правило, прямоугольными или цилиндрическими, с толстыми стенками высотой до 1 м, сложенными из камня и изнутри обмазанными глиной, целиком глинобитными или выложенными из кирпича.
Выплавленные из руды слитки меди содержали значительное количество шлаковых включений. Их отделяли ударами молотов. Рафинирование черновой меди осуществляли в тиглях и небольших горнах. При этом на расплавленную черновую медь дутьевыми трубками подавали воздух, основная масса оставшихся в ней примесей, кроме благородных металлов (золота и серебра), окислялась и формировала шлак.
Бронзолитейное искусство
Бронзовый век представляет собой эпоху бурного развития металлообработки. Технология изготовления металлических изделий в это время, как правило, включала совместное применение приемов, как литейной, так и кузнечной технологии, последующие полирование и гравирование изделий.
Сначала применяли литье в открытые глиняные или песчаные формы. Их сменили открытые формы, вырезанные из камня, и формы, у которых углубление для отливаемого предмета находилось в одной створке, а другая, плоская, играла роль крышки. Следующим шагом стало изобретение разъемных форм и закрытых форм для фигурного литья. В последнем случае сначала из воска лепили точную модель будущего изделия, затем ее обмазывали глиной и обжигали в печи. Воск плавился, а глина принимала точный слепок модели и использовалась в качестве литейной формы. Этот способ получил название литья по восковой модели. Мастера получили возможность отливать пустотелые предметы очень сложной формы. Для образования полости практиковалась вставка в формы особых глиняных сердечников – литейных стержней. Несколько позднее были изобретены технологии литья в стопочные формы, в кокиль, в различные формы с креплением литейного стержня на каркасе, литье по выплавляемым моделям и армированное литье.
Древние литейные формы изготовляли из камня, металла и глины. Глиняные литейные формы, как правило, получали путем оттиска в глине специально сделанных моделей из дерева и других материалов. В качестве моделей могли применяться и сами отлитые металлические изделия. Следует отметить, что формы, вырезанные из камня или литые металлические, вследствие их большей ценности не всегда служили для литья изделий, а могли использоваться для изготовления в них легкоплавких моделей. Например, в некоторых районах Англии была отмечена отливка в бронзовых литейных формах свинцовых моделей.
Развитие литейных технологий
Металлические формы в основном изготовляли из меди, так как она имеет значительно более высокую температуру плавления, чем бронза, для отливки которой они и предназначались. Применение кокилей позволяло получать отливки сложного профиля, с мелкими деталями, точный негатив которых было трудно вырезать в каменной форме. Переход на металлическую форму, более прочную, чем глиняная, и более простую в изготовлении, чем каменная, позволил соединить преимущества двустворчатых форм, приспособленных к многократному использованию, и отливок по восковой модели. Например, в рассматриваемое время повсеместно применялось литье удил из двух или четырех свободно соединенных звеньев, для получения которых на каждое звено требовались отдельный литник (канал для подвода металла) и складная форма, по крайней мере, из четырех частей.
Постоянной практикой стала дополнительная проковка отлитых изделий без изменения формы в целях повышения твердости, плотности и эластичности (пластичности) материала. Основным видом изделий, подвергавшихся подобной обработке, являлись орудия труда и некоторые виды оружия – мечи и кинжалы. Ковку использовали в процессе изготовления булавок, которые подвергались также гравированию или чеканке. Такие же приемы обработки применяли и к украшениям.
а. Литье в открытую форму
б. Литье в разъемную форму с литейным стержнем
Эпоха металлов наступила тогда, когда повсеместно была освоена технология изготовления литых топоров и мечей. Необходимость объединить в одном орудии труда каменное рубило и деревянную палицу возникла у человека уже в каменном веке. Первые бронзовые топоры, изготовленные методом литья, повторяли форму каменных, однако новые требования к орудиям труда и необычные в сравнении с камнем свойства бронзы способствовали быстрому совершенствованию литых изделий. Появились топоры сложных форм, с закраинами, вислообушные, кельты. Их изготовление требовало высокого развития литейного ремесла: сложная конфигурация отливки и наличие отверстия значительно усложняли устройство разъемных каменных форм. Появление усовершенствованных литых бронзовых топоров сыграло исключительную роль в развитии многих народов: облегчило строительство жилищ и изготовление других орудий труда и предметов быта, упростило освоение лесистых местностей земледельцами и т. п. Литые мечи и кинжалы раньше других бронзовых изделий стали произведениями искусства. Древние мечи, найденные при археологических раскопках, часто снабжены не только замысловатыми рукоятями с литыми узорами, но и богатой инкрустацией из серебра, золота и драгоценных камней.
Как отмечалось выше, ранний бронзовый век представлял собой эпоху безраздельного господства мышьяковой бронзы. Олово пришло на смену мышьяку только во 2-м тысячелетии до н. э. Отметим, что технология обработки оловянной бронзы заметно сложнее, так как зачастую требует горячей ковки (хотя и при низких температурах). На поверхности земли минералы олова встречаются достаточно редко. Почему же в позднем бронзовом веке оловянная бронза практически повсеместно вытеснила мышьяковую? Главная причина заключалась в следующем. В древности люди относились к металлическим предметам чрезвычайно бережно ввиду их высокой стоимости. Поврежденные предметы отправлялись в ремонт или на переплавку. Отличительной особенностью мышьяка является возгонка при температуре около 600 °С. Именно при такой температуре проводился отжиг ремонтируемых бронзовых изделий. С потерей мышьяка механические свойства металла ухудшались и изделия, изготовленные из бронзового лома, получались низкого качества. Объяснить это явление древние металлурги не могли. Однако достоверно известно, что вплоть до 1-го тысячелетия до н. э. изделия из медного и бронзового лома стоили дешевле, чем изделия из рудного металла.
Было и еще одно обстоятельство, способствовавшее вытеснению мышьяка из металлургического производства. Пары мышьяка ядовиты: их постоянное воздействие на организм приводит к ломкости костей, заболеваниям суставов и дыхательных путей. Хромота, сутулость, деформация суставов были профессиональными заболеваниями мастеров, работавших с мышьяковой бронзой. Данное обстоятельство находит отражение в мифах и преданиях многих народов: в древнейших эпосах металлурги часто изображаются хромыми, горбатыми, иногда – карликами, со скверным характером, с косматыми волосами и отталкивающей внешностью. Даже у древних греков бог металлург Гефест был хромым.
Оловянная бронза
Олово, необходимое для производства оловянной бронзы, стало последним из семи великих металлов древности, ставшим известным человеку. Оно не присутствует в природе в самородном виде, а касситерит – его единственный минерал, имеющий практическое значение, является трудновосстановимым и малораспространенным.
Тем не менее, этот минерал был известен человеку уже в глубокой древности, поскольку касситерит является спутником (хотя и редким) золота в его россыпных месторождениях. Благодаря высокой удельной массе золото и касситерит в результате промывки золотоносной породы оставались на промывочных лотках древних старателей. И хотя факты использования касситерита древними ремесленниками не известны, сам минерал был знаком человеку уже во времена неолита.
По-видимому, впервые оловянная бронза была произведена из полиметаллической руды, добытой из глубинных участков медных месторождений, в состав которой наряду с сульфидами меди входил и касситерит. Древние металлурги, уже располагавшие знаниями о положительном влиянии на свойства металла реальгара и аурипигмента, достаточно быстро обратили внимание на новый компонент шихты – «оловянный камень». Поэтому появление оловянной бронзы произошло, скорее всего, сразу в нескольких промышленных регионах Древнего мира.
Производство и рециклинг изделий из оловянной бронзы во 2-м тысячелетии до н. э.
В гробнице высокопоставленного египетского чиновника XVIII династии (около 1450 г. до н. э.) найдено изображение технологического процесса получения бронзовых отливок. Трое рабочих под наблюдением надсмотрщика подносят металл. Двое рабочих с мехами раздувают огонь в горне. Рядом изображены плавильные тигли и куча древесного угля. В центре показана операция разливки. Иероглифический текст поясняет, что эти картины иллюстрируют отливку больших бронзовых дверей для храма, и что металл по приказу фараона доставлен из Сирии.
Литье бронзы в Древнем Египте около 1450 г. до н. э.
Древнейшими предметами из олова считаются браслеты, найденные на острове Лесбос. Они датируются 3-м тысячелетием до н. э. Олово было одним из наиболее дефицитных и дорогих металлов Древнего мира. Даже в 1-м тысячелетии до н. э. металлическое олово имело крайне ограниченное распространение. Оно применялась, главным образом, для изготовления мелкой косметической посуды и некоторых деталей защитного вооружения, требовавших высокой пластичности (например, из олова делали книмиды – доспехи, защищавшие голени ног, которые держались на них без шнуров и застежек, а лишь благодаря упругости и эластичности). Практически все добываемое в то время олово расходовалось на производство бронзы.
Основные месторождения олова в эпоху Древнего мира были в Испании, Индокитае, Британских островах, которые греки называли «оловянными» – касситеридами. Кроме того, оловянная руда добывалась на Апеннинском полуострове (этрусками), в Греции (в Хризейской долине около города Дельфы), в Сирии. По мнению большинства историков, своим названием бронза обязана крупному римскому порту Брундизию, через который осуществлялась торговля империи с восточными странами. Однако существует и другая версия, упоминаемая римским историком Плинием, который считал, что название сплава произошло от персидского слова, обозначавшего «блеск меча».
Преимущества оловянной бронзы перед медью, мышьяковой бронзой и латунью заключались в высоких твердости, коррозионной стойкости и прекрасной полируемости. От способности олова повышать твердость бронзы и происходит его современное международное название – «станнум». Отметим, что корень «ст», звучащий в слове «стан» и во многих производных от него словах современных языков, является одним из древнейших общеиндоевропейских корней и обозначает признак прочности или устойчивости.
Зеркало, бритва и маникюрные ножницы
Многие предметы быта и вооружения стало возможно производить только после освоения технологии производства и обработки оловянной бронзы. Это относится, например, к изготовлению длинных мечей, бритвенных ножей и особенно к полированным зеркалам. Можно сказать, что появление оловянной бронзы ознаменовало переворот в древней магии.
Особое отношение к зеркалу характерно для всей территории древней Евразии. С помощью зеркала древний человек мог вступать в магические отношения с потусторонним миром: у многих народов существовало представление об отражении лица в зеркале как о выражении духовной сущности человека. В связи с этим нельзя не вспомнить сохранившееся до наших дней поверье, согласно которому разбитое зеркало означает несчастье.
Наибольшее распространение зеркало получило в качестве главного ритуального предмета культа женского солнечного божества. В эпоху античности ручки зеркал обычно выполнялись в виде женской фигуры, держащей над собой зеркало. Зеркало было главным атрибутом богинь Солнца в Иране, Египте, Индии, Китае и Японии. Особое отношение к зеркалу отразилось на выборе металла для его изготовления. Перечень требований, предъявляемых в древности к зеркальному сплаву, включал цвет и блеск, имитирующие солнечный, высокую отражательную способность и нетускнеющую поверхность.
На зеркалах, как ни на одном другом виде бронзовых изделий, можно проследить этапы освоения древними мастерами технологии термической и механической обработки медно-оловянных сплавов. Например, древние греческие, египетские и скифские зеркала, содержащие до 12 % масс. олова, подвергались только холодной ковке. Это не давало возможности достигать высоких параметров твердости и полируемости. Этруски делали зеркала из сплава с 14–15 % масс. олова. Перед холодной ковкой такой сплав необходимо было подвергнуть «гомогенизации». Этрусские металлурги проводили гомогенизацию сплава в течение 4–5 ч при температуре около 650 °С. Поэтому этрусские зеркала обладали прекрасной полируемостью и высокой коррозионной стойкостью. Еще больше олова (до 23 %), содержат золотисто-желтые зеркала сарматов, изготовленные в V–III вв. до н. э. Изделия из такого сплава можно было получить только путем горячей ковки бронзы при температуре «красного каления» (600–700 °С) и последующей закалки в воде. Подобную технологию использовали также в Индии, Китае и Таиланде.
На пороге новой эры практически повсеместное распространение получил тройной сплав меди, олова и свинца. Такие бронзы, содержащие до 30 % олова и до 7 % свинца, являются самыми твердыми и сложными для обработки. Однако они позволяют производить металл с высокой отражательной способностью, а также с прекрасными литейными свойствами и полируемостью. Изделия из такого сплава получили распространение в Китае, Средней Азии и Римской империи, хотя Плиний отмечает, что они имели чрезмерно высокую стоимость и были доступны только очень состоятельным людям.
Кусковая формовка
Уникальные технологии бронзового литья были созданы металлургами Древнего Китая. Известно, что уже во 2-м тысячелетии до н. э. в Китае существовала оригинальная технология литейного производства. В то время, когда металлурги Запада и Ближнего Востока получали сосуды ковкой, литьем в песчаные формы или по выплавляемым моделям, китайцы освоили гораздо более трудоемкий, но и существенно более прогрессивный метод «кусковой формовки».
Технология заключалась в следующем. Сначала из глины изготовляли модель, на которой вырезали требуемый рельеф. Затем получали обратное изображение, напрессовывая пластины глины, кусок за куском, на ранее изготовленную модель. На каждом куске формы выполняли тонкую доводку рельефа. После этого куски глины обжигали, что само по себе требовало виртуозного мастерства, так как не должен был нарушаться рисунок.
Первоначальную глиняную модель зачищали на толщину стенок будущей отливки, получая стержень для формирования ее внутренней полости. Куски формы собирали вокруг стержня, создавая таким образом цельную форму. При этом швы и стыки между кусками формы специально не заделывались наглухо, чтобы в них мог затекать металл. Это делалось для того, чтобы застывший в швах металл приобретал вид изящной кромки, придававшей изделию особый декоративный оттенок. Традиция использования вертикальных литейных швов для украшения изделий стала отличительной чертой китайского металлургического искусства.
Китайские бронзовые вазы
Еще одним примером оригинальных китайских литейных технологий является изготовление бронзовых тазиков с «кипящей» водой. На днище таких тазиков мастерами размещались литые рисунки определенного вида и направления. Они изменяли акустические свойства предмета, наполненного водой, таким образом, что стоило потереть его ручки, как с поверхности воды начинали подниматься фонтанчики, как будто вода, оставаясь холодной, действительно закипела. Современные исследования позволили установить причину такого необыкновенного эффекта: от трения возникают звуковые волны, которые резонируют и вызывают быстрые колебания в литых выступах в днище тазика, в результате чего вверх выталкиваются струйки воды.
Возможно, ни одна культура бронзового века не соответствует своему названию лучше, чем культура Древнего Китая в период династии Шан Инь (конец 2-го тысячелетия до н. э.). В то время в городах были целые кварталы ремесленников, занятых обработкой металлов, изготовлением оружия и специальных ритуальных изделий из бронзы. Кроме нескольких мраморных скульптур этой эпохи, все сохранившиеся произведения искусства сделаны именно из бронзы.
Античное статуарное литьё
В античном мире и Римской империи большое распространение получила мода на бронзовые статуи, которые посвящались богам, царям, выдающимся деятелям, победителям игр. Статуи часто переплавлялись, особенно по политическим мотивам.
На керамической чаше, относящейсяк V в. до н. э., греческий художник изобразил различные этапы изготовления бронзовых статуй человека в натуральную величину. Специальная печь позволяет получать бронзу и поддерживать ее в жидком состоянии. Стоящий за печью юноша раздувает мехи, чтобы увеличить температуру в печи. На рогах висят раскрашенные пластины и маски – это благодарственные приношения, обеспечивающие защиту от неудач в работе, или демонстрация типов изделий, изготовляемых в мастерской. В следующей сцене мастер прилаживает правую руку к бронзовой статуе, располагающейся на глиняном ложе. Отдельно отлитая голова еще лежит на полу. На стене висят модели кисти руки и ступни. Чуть дальше двое рабочих полируют большую статую воина в шлеме, стоящую на помосте. За работой наблюдают два человека. Предполагают, что один из них скульптор – автор статуи, а другой – бронзолитейщик, воплотивший замысел скульптора в металле.
Изготовление бронзовой статуи (рисунок на керамической вазе)
Обычно после отливки частей и сборки статуи устраняли неровности верхнего слоя, полировали поверхность, резцом и зубилом отделывали детали: бороду, волосы, складки одежды. Губы делали из красной меди, зубы – из серебра, глаза инкрустировали стеклянной массой или камнем, наносили цветные штрихи.
Изготовление бронзовой статуи
Древние не любили патину, покрывающую сегодня старинные изделия из бронзы. В момент создания скульптуры имели не нынешние (зеленые, коричневые или черные) оттенки: тон фигур был теплым и золотистым, как бронзовый загар. На фоне обилия разнообразных статуй, посвященных пусть великим, но смертным людям, скульптуры могущественных богов выделялись размерами и убранством. Самая крупная из известных в древности металлических статуй – «Колосс Родосский» – входила в число семи чудес света.
Источник: Энциклопедия «Металлургия и время», Голубев О.В., Карабасов Ю.С., Коротченко Н.А., Черноусов П.И.
Бонус:
Работа по металлу (часть 8)
Сообщение
Содержание материала
- Работа по металлу (часть 8)
- Чеканка
- Дополнительное оборудование
- Инструменты
- Канфарник
- Бобошники
- Пурошники
- Трубочки
- Молотки
- Материал
- Черные металлы и сталь
- Подготовительные работы
- Ящики для подложек
- Насмолка металлической пластины
- Приготовление рисунка или лепной модели
- Подготовка металлической заготовки (бляшки)
- Перевод рисунка на металл
- Все страницы
Страница 1 из 17
Техники декоративной обработки металлов
В этой части книги представлены основные техники декоративной обработки металлов. В древности многие кузнецы владели богатым набором методов и создавали замечательные произведения искусства, достойные царского двора. Поэтому можно попробовать объединить предложенные техники и сделать какую-нибудь вещь от начала до конца самому.
Чеканка – один из древнейших видов художественной обработки металла. Чеканные изделия могут быть различными по форме и по технике исполнения: объемно-скульптурными, рельефными и горельефными, орнаментальными, фигурными, графическими. Чеканку можно использовать для обработки и отделки изделий, созданных другими способами, для набивки фактуры, создания фоновых поверхностей для различных изображений. Широко используется чеканка в ювелирном деле. Чеканные изделия применяют при оформлении интерьеров и т. д. Техника чеканки позволяет создавать узоры и рисунки на уже готовых изделиях. Для работы чеканщику необходимы высокая точность движений и твердая рука.
Ковка – самый древний способ обработки металлов. Задолго до того, как научились выплавлять железо, мастера ковали различные сплавы цветных металлов, например легендарную бронзу. Изготовлялись как украшения, так и оружие. Ковка требует немалой физической силы и большого мастерства. Один из сложнейших видов ремесла – художественная ковка. Не каждый кузнец возьмется отковать узорную ограду или подсвечник. Большинство мастеров предпочитает пользоваться чеканкой, выколоткой или делать ажурные узоры выгибанием и сваркой стальных прутков и полос.
Человечество научилось выплавлять металл в глубокой древности. Еще в Древнем Египте с помощью литья мастера изготавливали предметы домашнего обихода. Раскопки скифских могильников доказывают, что наши далекие предки также применяли литье для изготовления самых различных предметов быта и украшений. Первыми мастерами литья на Руси были женщины, которые плели из нитей, пропитанных воском, украшения. Затем изделие заливалось глиной и обсушивалось. Такую форму прокаливали и заливали металлом. Когда форма остывала, ее осторожно, чтобы не повредить отливку, удаляли.
С помощью литья можно получить предметы, различающиеся по назначению и размерам. Можно изготовить ювелирные украшения из серебра, золота или других металлов. Монументальные памятники, скульптуры и архитектурные детали тоже можно сделать посредством литья. В домашних условиях, конечно, монументы и памятники отливать никто не будет, поэтому мы остановимся подробно на микролитье – изготовлении небольших изделий.
Гравирование достаточно широко распространено в народном творчестве. Этот способ пришел к нам из древнейших времен. Гравировкой украшали не только ювелирные изделия, но и оружие, предметы домашней утвари. Сам термин «гравирование» в переводе с немецкого и французского языков означает вырезание какого-либо изображения, орнамента или надписи на поверхности таких материалов, как металл, дерево, камень, линолеум, стекло.
Искусство изготовления просечного железа появилось в очень давние времена. Родилось оно из кузнечного дела и применялось вместе с ковкой железа. Узорчатое просечное железо украшало на Руси крыши домов и купола церквей, фонари на улицах, посуду, сундуки, поставцы и шкатулки. Просечное железо было самых разных цветов, его покрывали позолотой, лудили и воронили.
С помощью гальванопластики можно получить наиболее точную металлическую копию с определенного объемного предмета. Она позволяет даже в домашних условиях создавать различные ажурные украшения, шкатулки, картинные рамы, металлизированный гербарий. Причем ни один из других способов не даст такой чистоты линий, как гальванопластика. Снятая с тонкого кружева или живого цветка копия передаст все прожилки и, более того, получится металлической, то есть пригодной для крепления на металлическую основу.
Легкость в использовании гальванопластики и точность передачи линий и мелких штрихов предметов делают данную технику удобным способом в изготовлении небольших настольных статуэток, бюстов, медалей. Кроме того, это позволяет любому скульптору сохранить свое глиняное или гипсовое ваяние от разрушения на многие годы.
: Металлургия: образование, работа, бизнес :: MarkMet.ru
Н.А. Коротченко, П. И.Черноусов
Скачать полный текст
Ссылка доступна только зарегистрированным пользователям.
Древнейшие металлоносные культуры Евразии, зародившиеся в среде культур каменного века, расширяли свои территориальные границы в эпоху Бронзового века, который охватывает период III и II тысячелетий до н.э. За это время «металлическая цивилизация» распространилась на территорию свыше 40 млн км2. Последовавшие эпохи железа и средневековья почти не раздвинули её границ. Все основные события и революционные сдвиги в сферах технологии и социального развития совершались по преимуществу внутри этого обширного, но четко ограниченного пространства [1].
Ключевыми революционными техническими преобразованиями Бронзового века принято считать освоение ирригационного земледелия и полного металлургического цикла производства металлов, включая добычу руды, выжиг древесного угля, подготовку материалов, выплавку и рафинирование чернового металла, литьё, ковку, волочение проволоки, другие виды металлообработки и рециклинг металлолома. В Бронзовом веке были освоены технологии выплавки и обработки металлов, получивших название «семь металлов Древности»: меди, золота, свинца, серебра, железа, ртути и олова [2-8].
Были изобретены новые технологии для добычи и обработки камня. В строительном деле началось широкое применение металлических инструментов и орудий труда: кирок, кайл, сверл, молотов, тесел, резцов.
Возникновение цивилизации Древнего мира потребовало развития транспорта. Для этих целей использовались естественные водные магистрали и многочисленные водные каналы, прокладывались дороги для колесных повозок.
Первое изображение колесного транспорта, относящееся к III тысячелетию до н.э., обнаружено на территории бывшего Шумера (рис. 1) [2-6]. Появились легкие боевые колесницы — древнейший вид военной техники. Колесницы составляли главную силу всех армий Древнего мира вплоть до наступления позднего Железного века (т.е. до середины I тысячелетия до н. э). Для них требовалось легкое колесо, изготовить которое можно только с использованием специального металлического инструмента (рис. 2) [9].
Общепризнано, что определяющую роль в техническом прогрессе в бронзовую эпоху сыграло появление литых топоров, мечей и мотыг — основных видов орудий труда и оружия [4-6, 8-10]. Основой цивилизации стала металлургия меди.
Для производства меди повсеместно использовались как окисленные, так и сернистые руды. Месторождения медной руды обычно делятся на две зоны. Верхняя часть, находящаяся над уровнем грунтовых вод, представляет собой зону окисления, содержащую легковосстановимый оксид, а нижняя, основная, часть месторождения является зоной цементации, состоящей из сульфидных руд, в основном халькопирита (CuFeS,) или халькоцита (Cu9S) [11-13].
Содержание меди в сульфидных рудах намного ниже, чем в окисленных. После истощения верхних слоев начали использовать более бедные медью сульфиды. Это потребовало более высокого уровня горно-металлургических технологий, применения предварительного обжига, операций по очистке различного рода штейнов и рафинированию «черновой» меди.
Металлургические печи, наиболее характерные для бронзового века, были обнаружены в Австрии (Миттеберг), в Азербайджане (Мингечаур), на Сардинии. Четырехугольные или цилиндрические печи имели толстые стенки, высоту до полуметра, были сложены из камня и изнутри обмазаны глиной (или целиком глинобитные). На поду печи имели небольшое углубление для сбора металла. Передняя стена внизу была снабжена отверстием, через которое мехами осуществлялась подача дутья и выпускался из печи шлак.
Выплавленные из руды слитки меди содержали значительное количество шлаковых включений. Их отделяли ударами молотов. Рафинирование черновой меди осуществляли в тиглях и небольших горнах. При этом на расплавленную черновую медь дутьевыми трубками подавали воздух, основная масса оставшихся в ней примесей, кроме благородных металлов (золота и серебра), окислялась и формировала шлак [7, 8,15].
В бронзовую эпоху высокого уровня достигли технологии холодной ковки и литья.
Ковка — древнейший способ обработки металлов давлением. Освоение способа обработки самородного металла ковкой базировалось на накопленных навыках и опыте изготовления каменных орудий труда путем «обивки» камня каменным же молотом [15,16].
Самородная медь, которую первобытные люди вначале тоже считали разновидностью камня, при ударах каменного молота не давала характерных для камня сколов, а изменяла свою форму и размеры без нарушения сплошности материала. Это замечательное технологическое свойство «нового камня» явилось мощнейшим стимулом добычи самородного металла и использования его человеком. Кроме того, было замечено, что ковка повышает твердость и прочность металла.
В качестве молота вначале применяли обычные куски твердого камня. Первобытный умелец, зажимая камень в руке, наносил им удары по куску самородного или выплавленного из руды металла. Эволюция этого простейшего способа ковки привела к созданию прообраза кузнечного молота, снабженного рукояткой [3-6].
Вторым из древнейших способов обработки металлов стало литье [3-6, 10]. Расплавленный металл при затвердевании мог принять форму любого предмета. Сначала отливку производили в открытых глиняных или песчаных формах. Их сменили открытые формы, вырезанные из камня, и формы, у которых углубление для отливаемого предмета находилось в одной створке, а другая была просто плоской, прикрывающей.
Следующим шагом стало изобретение разъемных форм и закрытых форм для фигурного литья. В последнем случае сначала лепилась из воска точная модель будущего изделия. Затем ее обмазывали глиной и обжигали в печи. Воск плавился, а глина принимала точный отпечаток модели и использовалась в качестве литейной формы. Этот способ получил название литья по восковой модели. Мастера получили возможность отливать пустотелые предметы очень сложной формы. Для образования полости практиковалась вставка в формы особых глиняных сердечников (литейных стержней). Несколько позднее были изобретены другие, более сложные технологии литья [10,11].
Древние литейные формы делались из камня, металла и глины. Последние, как правило, изготовлялись путем оттиска в глине специально сделанных моделей (из дерева и других материалов) изделий. Могли употребляться и сами отлитые металлические изделия. Следует отметить, что формы, вырезанные из камня или же литые металлические, вследствие их большей ценности не всегда служили для получения литых изделий, а могли использоваться для изготовления в них легкоплавких моделей. Например, в некоторых районах Англии было зафиксировано изготовление свинцовых моделей в бронзовых литейных формах.
Литые мечи и кинжалы раньше других бронзовых изделий стали произведениями искусства. Древние мечи, найденные при археологических раскопках, часто снабжены не только замысловатыми рукоятями с литыми узорами, но и богатой инкрустацией из серебра, золота и драгоценных камней. Они изготовлялись как цельнолитыми, так и биметаллическими, с использованием технологии налива. Это позволяло клинок меча или кинжала отливать из твердых сортов бронзы и проковывать, а рукояти — из мягкой бронзы, с хорошими литейными свойствами и цветом. Биметаллические мечи, как правило, отливали по восковым моделям.
Согласно современным представлениям, ранний бронзовый век — это эпоха безраздельного господства мышьяковой бронзы. Олово пришло на смену мышьяку только во II тысячелетии до н.э. Отметим, что качество изделий из оловянной и мышьяковой бронз примерно одинаково, при этом технология обработки оловянной бронзы заметно сложнее, так как зачастую требует горячей ковки (хотя и при низких температурах). Редко на поверхности земли встречаются минералы олова. Тем не менее, оловянная бронза практически повсеместно вытеснила мышьяковую [8].
Главная причина заключалась в следующем. В древности люди относились к металлическим предметам чрезвычайно бережно, ввиду их высокой стоимости. Поврежденные предметы отправлялись в ремонт или на переплавку. Но отличительной особенностью мышьяка является возгонка при температурах около 600 °С. Именно в таких условиях проводился смягчающий отжиг бронзовых изделий. Теряя часть мышьяка, металл изменял свои механические свойства в худшую сторону. Объяснить это явление древние металлурги не могли. Однако достоверно известно, что вплоть до I тысячелетия до н.э., изделия из медного и бронзового лома стоили дешевле, чем изделия из «первородного» металла [7].
Было и еще одно обстоятельство, способствовавшее вытеснению мышьяка из металлургического производства. Постоянное воздействие ядовитых паров мышьяка на организм приводит к ломкости костей, заболеваниям суставов и дыхательных путей. Неудивительно, что древние металлурги не производили впечатления крепких и здоровых людей. Хромота, сутулость, деформация суставов были профессиональными заболеваниями мастеров работавших с мышьяковой бронзой. Недаром в мифах и преданиях многих народов, в древнейших эпосах металлурги часто изображаются хромыми, горбатыми, иногда — карликами, со скверным, раздражительным характером, косматыми волосами и отталкивающей внешностью. Даже у древних греков бог-металлург Гефест был хромым.
Олово стало последним из семи великих металлов древности, ставшим известным человеку. Оно не присутствует в природе в самородном виде, а его единственный минерал, имеющий практическое значение, касситерит является трудновосстановимым и малораспространенным [12-17]. Тем не менее, этот минерал был известен человеку уже в глубокой древности. Дело в том, что касситерит является спутником (хотя и редким) золота в его россыпных месторождениях. Благодаря высокой удельной массе золото и касситерит в результате промывки золотоносной породы оставались на промывочных лотках древних старателей. И хотя факты использования касситерита древними ремесленниками неизвестны, сам минерал был знаком человеку уже во времена неолита.
По-видимому, впервые оловянная бронза была произведена из полиметаллической руды добытой из глубинных участков медных месторождений, в состав которой наряду с сульфидами меди входил и касситерит. Древние металлурги, уже располагавшие знаниями о положительном влиянии на свойства металла реальгара и аурипигмента, достаточно быстро обратили внимание на новый компонент шихты — «оловянный камень». Поэтому появление оловянной бронзы произошло, скорее всего, сразу в нескольких промышленных регионах Древнего мира [1, 7, 8].
Несмотря на выдающиеся достижения в металлургии меди, самым «технологичным» металлом Бронзового века было золото [4-6]. В III тысячелетии до н.э. жильное золото добывалось на территории Европы и Азии практически из всех известных его месторождений. В древнеегипетских и шумерских текстах часто можно найти упоминания о разновидностях употреблявшегося в древности золота. Усматривалось различие в его происхождении: «речное», «горное», «скалистое», «золото в камне», а также по цвету. Цвет нерафинированного золота зависит от его природных примесей: меди, серебра, мышьяка, олова, железа и пр. Древние металлурги принимали все эти сплавы золота за разновидности самого золота. Археологами найдены древние золотые изделия, охватывающие большую гамму цветов: от тускло-жёлтого и серого до различных оттенков красного цвета.
Технология очистки (рафинирования) золота от примесей была известна шумерам уже в начале III тысячелетия до н. э. Её описание содержится в рукописях библиотеки ассирийского царя Ашшурбанипала. Согласно этой технологии золото плавили вместе со свинцом, солью и ячменными отрубями в специальных горшках, изготовленных из глины, смешанной с костной золой. Образующийся шлак впитывался пористыми стенками горшка, а на его дне оставался очищенный сплав золота с серебром. Таким образом, из золота удалялись все примеси, кроме серебра. На Ближнем Востоке и в Египте широко применялось листовое золото — фольга. Фольгой покрывали самые различные предметы: как металлические, так и деревянные. Например, с помощью ковки или органического клея золотая фольга прикреплялась к изделиям из бронзы, меди и серебра. При этом золотое покрытие спасало медь и бронзу от коррозии. Золотой фольгой часто покрывали деревянную мебель, прикрепляя ее при помощи маленьких золотых заклепок. Более тонкие золотые листы приклеивались к дереву, предварительно покрытому слоем специальной штукатурки [16].
В эпоху Древнего мира широкий размах получило производство ювелирных изделий и шитых золотом одежд. Ювелирные ремесла потребляли огромное количество благородных металлов и их сплавов, прежде всего в виде проволоки. Золотая и серебряная проволока использовалась также в качестве эквивалента стоимости в торговле.
В первой половине III тысячелетия до н.э. металлообработка, особенно ювелирное дело, достигла высокого уровня в Месопотамии. Широкое развитие здесь получила обработка золота, серебра и электрона. Особый интерес представляет известное погребение царицы Шубад (XXVI-XXVвв. до н.э.). Ее одежда была покрыта богатыми украшениями из золота, ляпис-лазури, сердолика. Массивный головной убор состоял из диадемы, венка из золотых листьев, золотых колец и трех золотых цветков. В диадеме использована тонкая золотая проволока диаметром 0,25-0,30 мм, свитая в спираль диаметром около 2,38 мм. Считают, что проволока изготовлена волочением.
Наиболее древние образцы проволоки изготовлены либо ковкой, либо разрезкой кованого листового металла. В Абидосе (Египет) найден проволочный браслет, датируемый 3400 г. до н.э. Он состоит из двух групп бусинок, соединенных прядью из свитых вместе золотых проволочек и толстого волоса. Искусно отделанная проволока имела такой же диаметр (0,33 мм), какой был у волоса.
Существовало два основных способа получения кованой проволоки. При первом способе слиток или кусок металла расковывался молотком в пруток заданной толщины и профиля. При втором способе из слитка или куска металла ковкой получали лист, а затем разрезали его на полоски, края которых округляли ударами молотка. При циркулярной резке получались длинные куски проволоки — в этом заключалось её преимущество. Примером практического применения циркулярной резки металла могут служить полоски из золота длиной более 1,5 м, найденные в одной из гробниц Ура [17].
В Уре найдены также сканные (филигранные) изделия, датированные III тысячелетием до н.э. Сущность сканного производства состоит в том, что из тонкой золотой, серебряной или медной проволоки круглого или четырехугольного сечения выполняются ажурные или напаянные на металлическую основу узоры. Для большей красоты проволока предварительно скручивается в две или три нити и сплющивается. Значительное распространение получили у древних народов шитые золотом одежды. Особенность этого вида искусства заключается в умении изготовлять тончайшие нити проволоки, которые с основой материала образуют эластичную ткань.
Попытки производить более изящную и тонкую проволоку привели к тому, что постепенно был выработан новый способ ее получения. Для сглаживания неровностей, калибрования и уплотнения проволоку стали проталкивать через отверстия в твердых материалах. Образцы такой проволоки из золота, датируемые IV тысячелетием до н.э., найдены в Египте. Впоследствии эта операция выравнивания поверхности проволоки развилась в волочение [16].
Считают, что в самом примитивном виде способ волочения начали применять в древнейший период (еще до появления металлических орудий) для отделки стержней дротиков и гарпунов. Стержни изготовляли из сырого дерева и затем калибровали протаскиванием (волочением) через костяные выпрямители. Раскопки погребений в Египте периода Среднего царства (2800-2500 гг. до н.э.) подтверждают, что техника выпрямления деревянных прутков была широко распространена в древности. Обнаружена роспись, изображающая двух ремесленников, занятых выпрямлением прутков из дерева.
Технология разделения металлов была освоена в связи с развитием металлургии серебра. Древнейшие серебряные изделия обнаружены на территории Ирана и Анатолии (современная Турция). В Иране их нашли в местечке Тепе-Сиалк: это пуговицы, датируемые началом V тысячелетия до н.э. В Анатолии, в Бейджесултане, найдено серебряное кольцо, датируемое концом того же тысячелетия.
Металлургия серебра возникла в прямой связи с добычей свинца из соединений, содержащих свинец и серебро одновременно. Археологические находки из двух этих металлов, как правило, синхронны. Свинцовые руды, содержащие значительное количество серебра распространены во многих регионах мира. Известны их месторождения в Испании, Греции, Иране, на Кавказе. Процесс отделения серебра от свинца, называемый купеляцией, был известен уже в IV тысячелетии до н.э. Для разделения свинца и серебра применяли купеляцию: окисление свинца, отделение оксида (глета) от серебра и последующее «повторное» восстановление свинца из оксида [2-7].
В быту серебро почти повсюду появилось позднее меди и золота. Из него изготавливали, главным образом, посуду, украшения и ювелирные изделия. Быстро научились делать серебряную фольгу и фурнитуру, которыми украшали одежду и мебель. Уже в III тысячелетии до н.э. серебро использовали для пайки медных изделий.
Таким образом. Бронзовый век можно считать периодом зарождения цветной металлургии. Основы известных термических процессов извлечения цветных металлов из руд, механической обработки и литья были освоены к началу I тысячелетия до н.э.
Процесс литья металла • Bernier Metals
Изложнице придается геометрическая форма желаемой детали. Затем расплавленный металл заливается в форму, форма удерживает этот материал в форме по мере его затвердевания.
Этот тип формы редко используется в производстве, особенно для металлических отливок любого уровня качества. Другой тип пресс-формы — это закрытая форма, она содержит систему доставки расплавленного материала в полость формы, где деталь будет затвердевать внутри формы. Очень простая закрытая форма показана на рис. 2. Закрытая форма намного важнее при производстве операций литья металла.
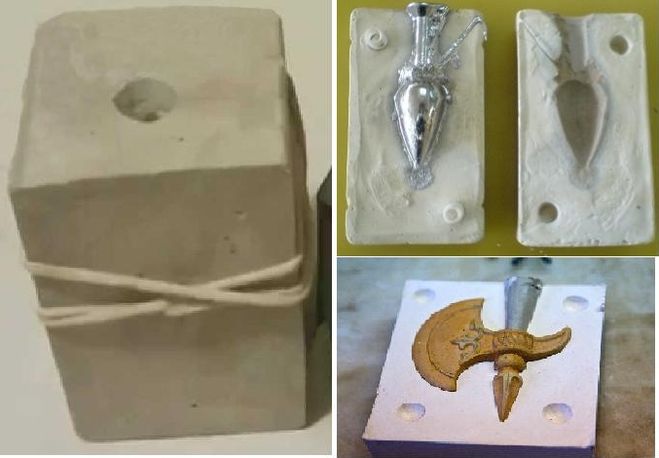
Одноразовая форма
| Постоянная форма
|
Шаблоны:
Для одноразовых форм требуется определенный шаблон. Внутренние полости формы, в которых будет затвердевать расплавленный металл, образуются оттиском этого узора. Дизайн модели имеет решающее значение для успеха производства путем литья в одноразовые формы. Шаблон представляет собой геометрическую копию изготавливаемой металлической отливки. Он сделан немного большего размера, чтобы компенсировать усадку, которая произойдет в металле во время затвердевания отливки, и любое количество материала, которое впоследствии будет снято с отливки. Хотя механическая обработка добавит дополнительный процесс к изготовлению детали, механическая обработка может значительно улучшить качество поверхности и размеры детали. Кроме того, увеличение припуска на машинную обработку поможет компенсировать неизвестные переменные усадки и уменьшить количество проблем, связанных с участками металлической отливки, которые изначально могли быть слишком тонкими или сложными.
Материал выкройки:
Материал, из которого изготавливается выкройка, зависит от типа формы и процесса литья металла, геометрии и размера отливки, требуемой точности размеров и количества металлических отливок, которые будут изготовлены с использованием выкройки. . Узоры могут быть изготовлены из дерева, например сосны (хвойная древесина) или красного дерева (лиственная древесина), различных пластиков или металла, например алюминия, чугуна или стали. В большинстве производственных операций шаблоны покрывают разделительным составом , чтобы облегчить их извлечение из формы.
Стержни:
Для металлических отливок с внутренней геометрией используются стержни . Сердечник — это копия (фактически обратная) внутренних особенностей отливаемой детали. Как и шаблон, размер сердечника рассчитан на усадку во время операции литья металла. В отличие от шаблона, во время заливки металла стержень остается в форме. Следовательно, сердцевина обычно изготавливается из того же материала, что и форма. Как только металлическая отливка затвердевает, сердцевина разбивается и удаляется так же, как форма. В зависимости от расположения и геометрии сердечника в отливке может потребоваться его поддержка во время операции, чтобы предотвратить его перемещение или смещение. Структурные опоры, которые удерживают сердечник на месте, называются 9.0050 венки . Венчики изготавливаются из материала с более высокой температурой плавления, чем материал отливки, и усваиваются деталью при ее затвердевании. Обратите внимание, что при изготовлении металлической отливки с использованием постоянной литейной формы стержень будет частью самой литейной формы.
Форма:
Стержень помещается в металлическую отливку после удаления модели. На рис. 5 показан оттиск модели с установленным сердечником. При изготовлении методом литья металла важно учитывать форму. Выкройка помещается в форму, и вокруг нее упаковывается материал формы. Форма состоит из двух частей: перетаскивания (внизу) и крышки (вверху). Линия разделения между валиком и перетяжкой позволяет открыть форму и удалить рисунок после того, как будет сделан оттиск.
Теперь оттиск в форме содержит всю геометрию отливаемой детали. Однако эта установка для литья металла не завершена. Чтобы эта форма была функциональной для изготовления отливки, помимо оттиска детали, полость формы также должна включать литниковую систему. Иногда литниковая система вырезается вручную или в более сложных производственных процедурах литниковая система включается в шаблон вместе с деталью. По сути, литниковая система функционирует во время операции литья металла, чтобы облегчить поток расплавленного материала в полость формы.
Элементы литниковой системы:
Разливочный бассейн:
Это место, где расплавленный металл, используемый для изготовления детали, поступает в форму. Разливочный бассейн должен иметь выступ с радиусом вокруг него, чтобы уменьшить турбулентность.
Нижний литник:
Из разливочной ванны расплавленный металл для литья проходит через нижний литник. Он должен быть сужающимся, чтобы его поперечное сечение уменьшалось по мере того, как он идет вниз.
Основание литника:
Нижний литник заканчивается у основания литника. Здесь начинается внутренняя полость отливки.
Зона входа/дросселя:
Оказавшись у основания литника, расплавленный материал должен пройти через вход, чтобы попасть во внутреннюю область формы. Затвор очень важен для регулирования потока во время операции литья металла.
Направляющие:
Направляющие — это каналы, распределяющие жидкий металл по различным областям внутри формы.
Основная полость:
Отпечаток фактической отливаемой детали часто называют основной полостью.
Вентиляционные отверстия:
Вентиляционные отверстия способствуют отводу газов, выбрасываемых из расплавленного металла на этапе затвердевания в процессе литья металла.
Райзеры:
Райзеры представляют собой резервуары с расплавленным материалом. Они подают этот материал в секции формы, чтобы компенсировать усадку по мере затвердевания отливки. Существуют различные классификации стояков.
Верхние стояки: Верхние стояки, подающие металлическую отливку сверху.
Боковые проставки: Райзеры, подающие металлическую отливку сбоку.
Глухие стояки: Подступенки, которые полностью помещаются в форму.
Открытые стояки: Подступенки, открытые сверху для внешней среды
Подробнее
Материалы для металлического литья
Литье в широком смысле определяется как процесс придания веществу определенной формы с использованием формы и литья металла. использует различные литейные материалы и металлы для создания формованного конечного продукта и насчитывает тысячи лет.
Изображение предоставлено: Funtay/Shutterstock
Некоторые процессы литья металлов и материалы, использовавшиеся для литья в древние времена, все еще используются сегодня. Существует множество надежных и эффективных материалов для литья металлов, которые используются в промышленных целях. Наиболее часто используемые ресурсы:
- Серый чугун
- Ковкий чугун
- Алюминий
- Сталь
- Медь
- Цинк
Отливка из серого чугуна
Серый чугун является одним из наиболее часто используемых литейных материалов в промышленном производстве. На него приходится большая часть рынков поставок литья, это прочное и универсальное вещество. Серый чугун легко поддается механической обработке, проверяется на качество без использования разрушающих методов, формулируется в соответствии с конкретными требованиями применения и экономически эффективен при больших объемах производства.
- Демпфирование или контроль вибрации
- Высокое соотношение прочности и веса
- Размерная стабильность
Литье из ковкого чугуна
Для процессов, требующих большей прочности, чем отливка из серого чугуна, полезной альтернативой может быть отливка из ковкого чугуна. Ковкий чугун имеет сходные черты с серым чугуном и, таким образом, имеет многие из тех же преимуществ. Однако ковкий чугун отличается от литья из серого чугуна следующими особенностями:
- Большая сила
- Повышенная износостойкость
- Повышенная ударная вязкость
- Превосходная пластичность
- Уменьшенный вес
- Уменьшенная усадка
- Более низкая стоимость
Алюминиевое литье
Литье алюминия также является широко используемым методом, во многом благодаря превосходной универсальности металла. Как один из немногих материалов, способных подвергаться большинству процессов литья металлов, алюминий является относительно адаптируемым материалом для работы.
- Литье под давлением
- Литье в постоянную форму
- Литье по выплавляемым моделям
- Литье в песчаные формы
- Литье по газифицируемым моделям
- Литье под давлением
- Горячее изотоническое прессование
Стальное литье
Сталь— это прочный литейный материал, хорошо подходящий для деталей, которые будут подвергаться исключительному износу, ударам или большим нагрузкам. Это полезно из-за его коррозионной стойкости в водной среде и для применений, связанных с повышенными температурами. Сталь часто смешивают с хромом, железом и никелем для дальнейшего повышения ее коррозионной или термостойкости.
Медное литье
Основным преимуществом меди в качестве материала для литья является то, что она обладает превосходной электропроводностью. В результате в строительной отрасли часто используется медь для изготовления электрических компонентов. Другие преимущества меди включают в себя:
- Хорошая пластичность
- Превосходная пластичность
- Хорошая теплопроводность
Однако медь и отливки могут быть подвержены поверхностному растрескиванию, пористости и образованию внутренних полостей. Следовательно, его часто смешивают с другими металлами (кремний, никель, цинк, хром, олово и серебро), чтобы облегчить эти проблемы.
Цинковое литье
Низкая температура плавления цинка (425 градусов Цельсия) делает его подходящим материалом для литья под давлением. Это относительно легкий сплав из-за его быстрого заполнения и быстрого охлаждения. С точки зрения стоимости цинк может быть экономичным вариантом для литья небольших деталей большого объема.Промышленное литье
Литье используется во многих производственных процессах и играет важную роль в строительстве. Многие отрасли промышленности в значительной степени зависят от литья для создания однородных продуктов. Некоторые из ведущих рынков литейных материалов:
- Автомобили и легкие грузовики
- Трубы и фитинги
- Строительное, горнодобывающее и нефтепромысловое оборудование
- Двигатели внутреннего сгорания
- Железная дорога
- Клапаны
- Сельскохозяйственное оборудование
- Муниципальные отливки
Что следует учитывать при выборе материалов для литья
- Требуемый уровень громкости
- Экономичность
- Температура плавления
- Скорость охлаждения
- Износостойкость
- Вес
- Возможности демпфирования
Цинк является эффективным выбором для операций литья под давлением, однако его низкая износостойкость и долговечность могут быть не идеальными для определенных применений, например, связанных с высоким риском коррозии или деформации материала. Для проектов литья под давлением, которые сосредоточены на производительности и устойчивости, алюминий может быть полезным вариантом. Например, алюминиевый сплав часто используется для литья корпусов газонокосилок, стоматологического оборудования, сковородок, авиационной и морской техники.
Для конструкционных применений или других задач, требующих прочности и долговечности, может быть целесообразным рассмотрение серого чугуна или ковкого чугуна. Серый чугун может быть эффективен для проектов, требующих сложных отливок без усадки, таких как блоки двигателей. Ковкий чугун подходит для деталей, требующих прочности и ударной вязкости, таких как критические компоненты двигателя (коленчатые валы, оси грузовых автомобилей, суппорты дисковых тормозов и т. д.).
Другие изделия для литья
- Усадка при литье: причины и решения
- Процессы, связанные с литьем
- Кремний в электронике и литье
- Как спроектировать форму для литья под давлением
- Альтернативы литью
- Руководство по кастингу
- Машины для литья под давлением
- Различные типы процессов литья, используемые в производстве
- Литье сплавов под давлением: обзор типов сплавов, литых под давлением, и их использование
- Как делают отливки
- Все о литье в гипсовые формы — что это такое и как это работает
- Литье и ковка – в чем разница?
- Процесс планирования спроса: ключевые этапы процесса S&OP, связанные с прогнозированием компонентов в цепочке поставок
- Типы процессов литья под давлением
- Все о литье по выплавляемым моделям — что это такое и как это работает
- Все о литье в песчаные формы: что это такое и как это работает
- Типы дефектов литья и способы их предотвращения
Еще от Изготовление и изготовление на заказ
Введение в литье металлов и способы сочетания 3D-печати с рабочими процессами литья
Литье металлов — это старинный процесс металлообработки, при котором расплавленный металл охлаждается и затвердевает в форме для формирования металлических деталей. Несмотря на свои древние корни, литье металлов по-прежнему остается одним из самых популярных процессов для компаний, занимающихся производством металлических деталей.
В этой статье рассказывается, что такое литье металлов, как оно работает, а также рассказывается о наиболее распространенных процессах литья металлов и преимуществах, которые производители могут получить, сочетая современные цифровые инструменты, такие как 3D-печать, с традиционными рабочими процессами литья.
Информационный документ
Ознакомьтесь с рекомендациями по созданию 3D-печатных моделей, пройдите пошаговый процесс литья по прямым выплавляемым моделям и изучите рекомендации по литью по непрямым выплавляемым моделям и литью в песчаные формы.
Загрузить информационный документ
Пошаговое литье металла от первоначального проекта до окончательного литья.
С момента появления металлического литья методы развивались и менялись. Однако его основные методы остались неизменными. Вот общий пошаговый процесс литья металла:
Кольца, напечатанные на 3D-принтере из Castable Wax 40 Resin.
Чтобы начать процесс литья металла, производитель сначала должен разработать представление желаемого образца. Этот шаблон необходим при разработке формы, используемой для отливки. Он традиционно изготавливается из дерева, пенопласта, пластика или воска и обеспечивает точное изготовление готовой металлической детали. Сегодня 3D-печать также является распространенным методом создания шаблонов, который позволяет дизайнерам создавать точные шаблоны непосредственно из цифровых программных инструментов САПР.
Шаблон не является точной копией желаемой детали. Он имеет дополнительные элементы, которые делают возможным процесс литья, в том числе заслонки, которые позволяют расплавленному металлу течь с постоянной скоростью, и вентиляционные отверстия для выхода газа. Кроме того, шаблоны также больше, чем детали, которые они представляют, чтобы учесть усадку, возникающую во время охлаждения.
Если отливка полая, производитель также создает сердцевину из песка или металла для придания внутренней формы. Это ядро удаляется после завершения литья.
Следующий шаг — создание литейной формы, которая может быть многоразовой (одноразовой) или одноразовой (одноразовой). Одноразовые формы обычно изготавливаются из песка, гипса, воска или с помощью 3D-печати, и, как следует из названия, они разрушаются в процессе литья. Многоразовые формы изготавливаются из металла и других прочных материалов и могут повторно использоваться для нескольких циклов литья.
Керамические оболочки после выжигания и 3D-печати из прозрачной смолы.
Расплавленное олово заливают в форму для 3D-печати из высокотемпературной смолы для литья металла.
На этом этапе металл нагревается в печи, пока не расплавится. В зависимости от применения производители могут использовать различные металлы, наиболее часто отливаемыми металлами являются железо, алюминий, алюминиевый сплав, сталь, медь и цинк, а также драгоценные металлы, такие как золото и серебро. Как только металл расплавится, производитель заливает его в полость формы и дает ему остыть и затвердеть.
Последующая обработка металлического литья.
Когда металл остынет и затвердеет, детали извлекаются из формы. В зависимости от типа пресс-формы это может быть сделано за счет вибрации в процессе выбивки, вымывания паковочной массы или выталкивающих штифтов. Затем с деталей удаляют лишний материал, такой как вентиляционные отверстия, ворота и кормушки. Наконец, детали подвергаются шлифовке, шлифовке, механической обработке или пескоструйной обработке, чтобы сгладить поверхность и достичь требуемой окончательной формы.
Хотя все методы литья металлов основаны на одном и том же основном процессе, существуют различные методы, более подходящие для различных областей применения. Некоторые из наиболее распространенных методов включают литье под давлением, литье по выплавляемым моделям и литье в песчаные формы.
Литье под давлением использует стальную форму и высокое давление. (Источник: buhlergroup.com)
Литье под давлением — это процесс литья металла, при котором производитель нагнетает расплавленный металл в полость стальной формы под высоким давлением для быстрого изготовления металлических деталей. При литье под давлением производитель соединяет вместе две половины матрицы или многоразовой формы и использует сопло для впрыска расплавленного металла под давлением в форму. Когда металл остывает, матрица открывается, и штифты выталкивателя выталкивают отливку.
Двумя наиболее распространенными процессами литья под давлением являются литье с горячей камерой и литье с холодной камерой. Хотя специфика этих процессов различается, есть несколько общих характеристик процесса литья под давлением в целом.
Литье под давлением с горячей камерой является наиболее распространенным из двух основных процессов литья под давлением. Машины для литья под давлением с горячей камерой имеют встроенную печь для нагрева металла внутри машины. Как только металл достигает расплавленного состояния, машина опускает цилиндрическую камеру в расплавленный металл. Форма «гусиная шея» системы впрыска металла позволяет камере быстро наполняться, а затем проталкивать материал в форму с помощью давления воздуха или поршня.
Погружение механизма впрыска для его заполнения обеспечивает быстрое и оптимизированное впрыскивание в форму в этом процессе литья. Однако, поскольку камера подвергается прямому нагреву от расплавленного металла, системы литья под давлением с горячей камерой подвержены риску коррозии, что делает их менее жизнеспособным вариантом для металлов с высокой температурой плавления. Вместо этого он лучше подходит для материалов с низкой температурой плавления и высокой текучестью, таких как свинец, магний, цинк и медь.
Напротив, процесс литья под давлением с холодной камерой работает медленнее, чтобы избежать коррозии. При использовании этого метода литейщик заливает расплавленный металл в систему впрыска. Затем поршень проталкивает металл в форму.
Этот процесс ограничивает коррозию, которая чаще встречается при литье под давлением с горячей камерой. Это идеальный вариант для металлов с высокой температурой плавления, таких как алюминий и алюминиевые сплавы.
Процесс литья под давлением является быстрым и позволяет производить детализированные детали. Он идеально подходит для производства больших объемов сложных деталей, а также может производить прочные детали с гладкой поверхностью. Способность литья под давлением производить большие объемы деталей делает его важнейшим процессом в автомобильной и аэрокосмической промышленности.
Поскольку инструменты и оборудование для литья под давлением дороги, этот процесс нерентабелен для небольших производственных циклов. Кроме того, пластичность металлов, используемых в процессе, может повлиять на сложность продукта.
Отлитые детали из шаблонов SLA, напечатанных из Clear Resin на 3D-принтере Formlabs.
Литье по выплавляемым моделям, также известное как литье по выплавляемым моделям, представляет собой процесс, в котором для производства сложных деталей используются воск, суспензия и формы. Это один из старейших методов литья металла, но он до сих пор ценится за способность создавать точные металлические детали сложной формы.
Этот процесс до сих пор широко используется для производства ювелирных изделий, стоматологии и искусства. Его промышленная форма, литье по выплавляемым моделям, является распространенным способом создания прецизионных металлических деталей в машиностроении и производстве.
Модели для литья по выплавляемым моделям обычно изготавливаются из воска или полимеров, напечатанных на 3D-принтере. Узоры собираются в древовидную структуру и погружаются в суспензию кремнезема или помещаются в колбу и заливаются жидким гипсом. После того, как паковочная масса высохнет, опоку помещают вверх дном в печь, которая расплавляет модель, оставляя негативную полость в форме исходной модели. Металл расплавляют, а затем заливают под действием силы тяжести или вакуума, чтобы втянуть металл в полость. Отлитые детали опиливаются, шлифуются, подвергаются механической обработке или пескоструйной обработке для достижения окончательной геометрии и чистоты поверхности.
Литники с литыми кольцами.
Литье по выплавляемым моделям — универсальный процесс. Это позволяет производителям производить точные и воспроизводимые детали практически из любого металла, доступного для литья, и сложных форм, которые были бы трудны или невозможны при других методах литья. Литые детали также имеют превосходное качество поверхности и низкие допуски, при этом требуется минимальная обработка поверхности или механическая обработка.
Благодаря этим характеристикам литье по выплавляемым моделям идеально подходит для сложных деталей автомобильной, аэрокосмической и промышленной промышленности, медицинских инструментов, зубных имплантатов, а также ювелирных изделий и предметов искусства.
Литье по выплавляемым моделям — сложный и трудоемкий процесс. Для изготовления формы требуется специальное оборудование, дорогостоящие огнеупоры и связующие, а также множество ручных операций. Отливка деталей, для которых требуются стержни, может быть затруднена, и этот процесс лучше подходит для мелких деталей.
Половина формы для литья в песчаные формы.
Литье в песчаные формы — это метод литья металлов, который был впервые использован 3000 лет назад, но остается наиболее широко используемым методом литья по сей день. Этот процесс позволяет производителям отливать металл, не полагаясь на механическую обработку.
В процессе литья в песчаные формы производитель сначала создает литейный образец или копию отливки, чаще всего из дерева или пластика. Выкройка увеличена, что позволяет дать усадку. Для деталей с элементами на одной стороне требуется только открытая форма. Для деталей с несколькими детализированными поверхностями производитель разделяет литейный образец на две формы, чтобы сформировать форму с закрытой полостью. Верхняя половина называется копьем, а нижняя — перетаскиванием.
После того, как производитель создал шаблон, он плотно набивается песком вокруг шаблона. Затем они добавляют литники и литники, чтобы обеспечить плавное течение расплавленного металла через полость формы. Производитель удаляет шаблон, а затем скрепляет две половины песчаной формы вместе. Когда металл плавится до расплавленного состояния, его заливают в форму и оставляют остывать. Отсюда песчаная форма удаляется с помощью вибраций или воды под высоким давлением. Наконец, производитель дорабатывает деталь, удаляя литники и заслонки и полируя литую металлическую деталь.
Литье в песчаные формы — это адаптируемый процесс, работающий вне ограничений машинного оборудования. Благодаря этому он может создавать сложные детали практически любого размера. Песок недорог и доступен в большом количестве, что снижает стоимость установки и делает возможными модификации. Это единственный практичный или экономичный способ производства очень больших отливок. Время выполнения литья в песчаные формы также короткое, что делает его жизнеспособным процессом для небольших производственных циклов.
Универсальность литья в песчаные формы делает его пригодным для производства в самых разных отраслях промышленности. Он может производить медицинское оборудование, автомобильные детали, электронное оборудование, бензобаки, блоки цилиндров и многое другое.
Литье в песчаные формы позволяет получать высокопористые текстурированные металлы. Усадка и шероховатость поверхности также снижают размерную точность деталей. В результате получается низкопрочный конечный продукт, который требует длительной последующей обработки для достижения более высокого качества отделки.
Чтобы выбрать правильный процесс промышленного литья металлов, необходимо учитывать несколько факторов. Мы создали эту сравнительную таблицу, чтобы помочь вам сравнить литье под давлением, литье по выплавляемым моделям и литье в песчаные формы с точки зрения типов металлов, объема производства, затрат, времени производства, сложности деталей и в каких отраслях они обычно используются.
Die Casting | Investment Casting | Sand Casting | |
---|---|---|---|
Compatible metals | Aluminum, copper, lead, magnesium, zinc | Most metals | Most metals |
Production volume | Большие объемы | От малых до больших объемов | От разовых до средних объемов |
Удельные расходы | От низких | От умеренных до высоких | Moderate |
Tooling costs | High | Moderate | Low |
Cycle time | Rapid | Long | Moderate |
Industries | Automotive, aerospace, consumer products, furniture, power инструменты | Автомобильная, аэрокосмическая, ювелирная, медицина, стоматология, искусство | Автомобильная, аэрокосмическая, промышленное оборудование, электроника, потребительские товары |
Рисунок ювелирного кольца и литой металлической детали, напечатанный на 3D-принтере.
Инженеры, дизайнеры, ювелиры и любители могут извлечь выгоду из скорости и гибкости 3D-печати, комбинируя процессы литья, такие как непрямое литье по выплавляемым моделям, литье по прямым выплавляемым моделям, литье олова и литье в песчаные формы с 3D-печатными моделями или литьем металла в 3D-печатные формы. . Литые металлические детали с использованием инструментов для быстрой 3D-печати могут быть изготовлены за долю времени, затрачиваемого на традиционное литье, и со значительно меньшими затратами, чем 3D-печать металлом.
Стереолитографические (SLA) 3D-принтеры предлагают высокую точность и обширную библиотеку материалов, которые хорошо подходят для рабочих процессов литья и могут производить металлические детали с меньшими затратами, с большей свободой проектирования и за меньшее время, чем традиционные методы.
Веб-семинар
На этом веб-семинаре мы рассмотрим, как настольные стереолитографические (SLA) 3D-принтеры используются для прямой печати моделей, как работать с моделями SLA для литья по выплавляемым моделям и как преимущества генеративного проектирования увеличивают спрос для печатных моделей.
Посмотреть вебинар
3D-форма из прозрачной смолы для впрыска воска.
Процесс изготовления моделей из форм или оснастки называется непрямым литьем по выплавляемым моделям, поскольку он требует создания форм для изготовления моделей в дополнение к окончательным формам по выплавляемым моделям.
Жесткие формы для воска (часто называемые инструментами) обычно изготавливаются путем механической обработки алюминия или стали. Производство обработанных металлических форм стоит тысячи долларов, а обработка и полировка занимают недели, прежде чем можно будет выполнить первые выстрелы и оценить детали модели в процессе литья.
С помощью 3D-печати производители могут напрямую печатать в 3D форму для своего рисунка, используя такие материалы, как High Temp Resin или Rigid 10K Resin, смолы, устойчивые к высоким температурам. Для оптимальной обработки поверхности формованных деталей обработайте внутренние поверхности формы шлифованием и полировкой для получения гладкого вида или дробеструйной очисткой, если требуется однородный матовый вид. Чтобы убедиться, что окончательные отлитые детали имеют точные размеры, компенсируйте усадку, увеличив масштаб напечатанной формы. Точную усадку воска и процесс литья можно получить из спецификаций поставщика.
3D-печатные формы для литья металлов сокращают время между созданием концепции и первыми испытаниями до нескольких дней, поскольку производители могут напрямую печатать инструменты, необходимые для запуска и оценки деталей.
В то время как формованные детали должны соответствовать правилам проектирования в отношении формуемости (например, отсутствие поднутрений, благоприятный уклон и т. д.), вы можете повысить сложность модели, используя сборочные шаблоны для объединения нескольких компонентов в единую конструкцию.
Информационный документ
Загрузите наш технический документ, чтобы узнать о шести процессах изготовления форм, которые возможны с помощью собственного 3D-принтера SLA, включая литье под давлением, вакуумное формование, формование силикона и многое другое.
Загрузить информационный документ
Ювелирные изделия, напечатанные на 3D-принтере, и отлитые из металла кольца.
Литье по выплавляемым моделям — это разновидность литья по выплавляемым моделям, при которой процесс переходит непосредственно от создания модели к окружению модели паковочной массой. Он идеально подходит для изготовления деталей с геометрией, слишком сложной для формования, или для деталей с обширными поднутрениями и тонкой текстурой поверхности, где формование возможно, но сопряжено с высокими затратами на инструмент.
Традиционно модели для прямого литья по выплавляемым моделям вырезаются вручную или обрабатываются на станке, если деталь является единичной или ожидается, что ее будет всего несколько единиц. Однако с помощью 3D-печати производители могут напрямую печатать шаблоны, устраняя ограничения по дизайну и времени, характерные для других процессов.
С помощью 3D-печати инженеры, дизайнеры и ювелиры могут направлять модели 3D-печати, чтобы сократить время выполнения заказа и добиться геометрической свободы, превышающей проектные ограничения технологичности процессов литья. Formlabs разработала ряд литейных материалов, подходящих для литья по выплавляемым моделям, в частности, для ювелирной промышленности.
Белая книга
Способы работы ювелиров меняются, и лидируют литейные фотополимерные смолы. Из этого руководства вы узнаете, как отливать ювелирные украшения с помощью 3D-печати на принтерах Formlabs.
Загрузить информационный документ
Образец детали
Убедитесь сами и убедитесь в качестве Formlabs. Мы отправим бесплатный образец детали в ваш офис.
Запросить бесплатный образец Деталь
Серая смола Печатный рисунок и готовое алюминиевое литье из открытой песчаной формы.
Подобно литью по выплавляемым моделям, 3D-печать можно использовать для создания моделей для литья в песчаные формы.
По сравнению с традиционными материалами, такими как дерево, 3D-печать позволяет производителям создавать сложные формы и сразу переходить от цифрового проектирования к литью.
Металлические миниатюры, отлитые из олова и напечатанные на 3D-принтере.
Олово — это ковкий металлический сплав с низкой температурой плавления, который можно использовать для изготовления полностью металлических предметов декоративного назначения, таких как детализированные металлические миниатюры, ювелирные изделия, масштабные модели и копии антиквариата.
Благодаря недавним разработкам в области термостойких материалов для 3D-печати, таких как High Temp Resin для 3D-принтеров Formlabs SLA, теперь стало возможным печатать формы для прямого литья олова в 3D.
Существует два варианта конструкции пресс-формы: жертвенная или съемная форма. В жертвенной форме есть оболочка, предназначенная для разрушения в процессе. Разборные формы состоят из отдельных половинок, поэтому форму можно использовать повторно.
По сравнению с прямой печатью металла отливка олова в 3D-печатные формы обеспечивает значительно лучшую детализацию и качество поверхности при небольшой доле затрат. По сравнению с восковым литьем, прямая 3D-печать формы требует меньше шагов и требует меньше ручных усилий, сохраняя при этом максимально возможные детали.
Веб-семинар
Посмотрите наш веб-семинар, чтобы узнать, как изготовление форм с использованием 3D-печатных шаблонов и многоразовых или жертвенных форм может позволить вам производить детали из фарфора, драгоценных и недрагоценных металлов, силикона и биосовместимых гибких материалов и т. д.
Посмотреть вебинар сейчас
Процесс литья ювелирных изделий по выплавляемым моделям с использованием 3D-моделей.
Предприятия, стремящиеся расширить свободу проектирования или сократить расходы и время выполнения заказов, имеют надежное решение в области литья металлов с помощью 3D-печати.
Определенные типы сложных металлических отливок, такие как крупные формы с поперечным сечением и детали с несколькими стержнями, трудно изготовить с использованием традиционных методов литья металлов. 3D-печать позволяет производителям создавать сложные конструкции. Например, ювелиры могут создавать сложные и нестандартные конструкции, которые были бы невозможны без 3D-печати.
3D-печать также устраняет зависимость от нескольких машин или поставщиков услуг для создания деталей. Вместо этого компаниям просто нужен цифровой файл, 3D-принтер и материалы для печати. Это может сократить расходы и отходы, поскольку весь используемый материал идет на конечный продукт.
Наконец, сочетание 3D-печати с литьем металла может сократить расходы и время выполнения заказа. Вместо того, чтобы неделями ждать дорогостоящих инструментов, прежде чем можно будет отлить конечный продукт, 3D-принтер может создать шаблон или форму за несколько часов.
Литье металла в сочетании с 3D-печатью помогает компаниям быстро и эффективно создавать металлические детали. С 3D-принтером Formlabs SLA вы можете ускорить процесс литья металла и одновременно сократить расходы.
Узнайте больше о настольном 3D-принтере Form 3 SLA и запросите бесплатный образец детали, чтобы лично оценить качество.