пошаговая инструкция. Технология плавки алюминия в домашних условиях :: BusinessMan.ru
Алюминий часто используется для изготовления деталей. Иногда плавят кусочки алюминия, чтобы заделать дефект, делают отливки. Плавить можно обломки дюраля, ненужные радиодетали. В обзоре представлены способы, как в домашних условиях расплавить алюминий, что для этого потребуется. Специалисты поделятся опытом, расскажут, какие свойства легкого металла необходимо учитывать, чтобы плавить металл самостоятельно.
Характеристики алюминия
Все характеристики металла для домашних самоделок знать необязательно. Но есть несколько моментов, которые могут стать значительными или даже опасными в работе.
Алюминий хорошо поддается литью, плавится при относительно невысокой температуре в 660 °С. Для справки: чугун начинает плавиться при температуре 1100°С, а сталь – 1300 °С.
Поэтому плавка алюминия в домашних условиях на газовой плите трудно осуществима, так как домашние газовые приборы такую температуру обеспечить не могут. Правда, отечественные «кулибины» могут все, но об этом позже.
Снизить температуру плавления алюминия можно, растерев его в порошок или используя в качестве сырья готовый порошковый продукт. Но здесь важным становится еще одно свойство алюминия. Он достаточно активный металл, который при соединении с кислородом воздуха может воспламениться или просто окислиться. А температура плавления оксида алюминия — больше 2000 °С. При плавлении оксид все равно образуется, но в небольших количествах, именно он формирует окалину.
Та же активность может сыграть плохую шутку, если в расплавленный металл попадет вода. При этом происходит взрыв. Поэтому если в процессе плавки нужно сырье добавлять, то нужно следить, чтобы оно было сухим.
Применение
Механические свойства алюминия не столь хороши, чтобы применять его в чистом виде. Поэтому чаще всего используются сплавы на основе данного вещества. Таких много, можно назвать самые основные.
- Дюралюминий.
- Алюминиево-марганцевые.
- Алюминиево-магниевые.
- Алюминиево-медные.
- Силумины.
- Авиаль.
Основное их отличие — это, естественно, сторонние добавки. Во всех основу составляет именно алюминий. Другие же металлы делают материал более прочным, стойким к коррозии, износоустойчивым и податливым в обработке.
Можно назвать несколько основных областей применения алюминия как в чистом виде, так и в виде его соединений (сплавов).
- Для изготовления проволоки и фольги, используемой в быту.
- Изготовление посуды.
- Самолетостроение.
- Кораблестроение.
- Строительство и архитектура.
- Космическая промышленность.
- Создание реакторов.
Вместе с железом и его сплавами алюминий — самый важный металл. Именно эти два представителя периодической системы нашли самое обширное промышленное применение в руках человека.
Сырье для плавки
Если предстоит плавка алюминия в домашних условиях, из-за сложности работы с порошковым металлом его в качестве сырья не используют.
Можно приобрести алюминиевую чушку или использовать обычную алюминиевую же проволоку, которую нарезать ножницами на небольшие кусочки и для уменьшения площади контакта с воздухом плотно спрессовать пассатижами.
Если не предполагается особо высокое качество изделия, то можно в качестве сырья использовать любые бытовые предметы, консервные банки без нижнего шва или обрезки профиля.
Вторичное сырье может быть окрашено или испачкано, это не страшно, лишние составляющие отойдут в виде шлаков. Только нужно помнить, что вдыхать пары сгоревшей краски нельзя.
Чтобы из вторичного сырья получилась качественная плавка алюминия в домашних условиях, флюсы, задача которых состоит в том, чтобы связывать и выводить на поверхность расплавленного металла все примеси и загрязнения, лучше приобрести готовые. Но можно сделать самостоятельно из технических солей.
Покровный флюс готовится из 10 % криолита и по 45 % хлорида натрия и хлорида калия.
В рафинирующий флюс для получения алюминия без пористости добавляют еще 25 % от общей массы фтористого натрия.
Автомобильный транспорт
Одним из основных требований к материалам, применяемым в автомобильном транспорте, является малая масса и достаточно высокие показатели прочности. Принимаются во внимание также коррозионная стойкость и хорошая декоративная поверхность материала.
Рисунок 3 – Автомобиль
Высокая удельная прочность алюминиевых сплавов увеличивает грузоподъемность и уменьшает эксплуатационные расходы передвижного транспорта. Высокая коррозионная стойкость материала продляет сроки эксплуатации, расширяет ассортимент перевозимых товаров, включая жидкости и газы с высокой агрессивной концентрацией.
При изготовлении элементов каркаса, обшивки кузова полуприцепа автофургона, рефрижератора, скотовоза и т.п. перспективным материалом являются алюминиевые сплавы АД31, 1915 (прессованные профили) и сплавы АМг2, АМг5 (лист).
Находят применение алюминиевые сплавы АМц, АМгЗ и 1915 при изготовлении отдельных узлов легкового автомобиля (навесные детали, бамперы, радиаторы охлаждения, отопители).
В автомобилестроении США широко используются алюминиевые свариваемые сплавы серии Зххх, 5ххх и 6ххх.
Из прессованных полуфабрикатов сплавов 2014 и 6061 изготовляют балки, рамы тяжелых грузовых автомобилей. Панели и отдельные элементы из сплава 5052 поступают на изготовление кабины. В качестве обшивочного материала кузова грузовика используют лист из сплавов 5052, 6061, 2024, 3003 и 5154. Стойки кузова выполняются из прессованных полуфабрикатов сплавов 6061 и 6063. Магналиевые сплавы серии 5ххх (5052, 5086, 5154 и 5454) являются основным материалом при изготовлении автоцистерн.
Средства индивидуальной защиты при плавке
Плавка алюминия в домашних условиях – процесс небезопасный. Поэтому нужно пользоваться средствами индивидуальной защиты (СИЗ). Даже если такая плавка нужна один раз на минимальном оборудовании, то по меньшей мере нужно защитить руки, например специальными перчатками сварщика, отлично предохраняющими от ожогов, ведь температура жидкого алюминия — больше 600 °С.
Глаза тоже желательно защищать, особенно если плавка происходит достаточно часто, очками или маской. И совсем в идеале работать нужно в специальном костюме металлурга с повышенной стойкостью к огню и высоким температурам.
Если нужен очень чистый алюминий с использованием рафинирующего флюса, то работать следует в химическом респираторе.
Авиация
На современном этапе развития дозвуковой и сверхзвуковой авиации алюминиевые сплавы являются основными конструкционными материалами в самолетостроении.
В авиации США широко применяются сплавы серии 2ххх, Зххх, 5ххх, 6ххх и 7ххх. Серия 2ххх рекомендована для работы при высоких рабочих температурах и с повышенными значениями коэффициента вязкости разрушения. Сплавы серии 7ххх — для работы при более низких температурах значительно нагруженных деталей и для деталей с высокой сопротивляемостью к коррозии под напряжением. Для малонагруженных узлов применяются сплавы серии Зххх, 5ххх и 6xxx. Они же используются в гидро-, масло-и топливных системах.
В России при изготовлении авиационной техники успешно используются упрочняемые термической обработкой высокопрочные алюминиевые сплавы Al-Zn-Mg-Cu и сплавы средней и повышенной прочности Al-Mg-Cu. Они являются конструкционным материалом для обшивки и внутреннего сплавного набора элементов планера самолета (фюзеляж, крыло, киль и др.). Сплав 1420, принадлежащий системе Al-Zn-Mg, используют при конструировании сварного фюзеляжа пассажирского самолета. При изготовлении гидросамолетов предусмотрено применение свариваемых коррозионностойких магнолиевых сплавов (AМг5, АМг6) и сплавов Al-Zn-Mg (1915, В92, 1420).
Рисунок 1 – Гражданский самолет
Бесспорное преимущество имеется у свариваемых алюминиевых сплавов при создании объектов космической техники. Высокие значения удельной прочности, удельной жесткости материала позволили обеспечить изготовление баков, межбаковых и носовых частей ракеты с высокой про-дольной устойчивостью. К достоинствам алюминиевых сплавов (2219 и др. ) следует отнести их работоспособность при криогенных температурах в контакте с жидким кислородом, водородом и гелием. У этих сплавов происходит так называемое криогенное упрочнение, т.е. прочность и пластичность параллельно растут с понижением температуры.
Сплав 1460 принадлежит системе Al-Cu-Li и является более перспективным для проектирования и изготовления баковых конструкций применительно к криогенному типу топлива – сжатому кислороду, водороду или природному газу.
Литейная форма
Если требуется только отлить чистый алюминий для припоя, то литейная форма не нужна. Достаточно использовать стальной лист, на котором расплавленный металл остынет. Но если нужно отлить хотя бы простенькую деталь, то понадобится литейная форма.
Литейную форму можно сделать из скульптурного гипса, именно гипса, а не алебастра. Жидкий гипс заливается в смазанную маслом форму, ему дают немного застыть, периодически встряхивая, чтобы вышли пузырьки воздуха, вставляют в него модель и накрывают второй емкостью с гипсом. В удобном месте нужно в гипс вставить цилиндрический предмет, чтобы в итоге в форме появилось отверстие, так называемый канал, в который будет заливаться расплавленный алюминий. Когда гипс окончательно застынет, две части формы разъединяются, вынимается модель, и форма с готовым слепком соединяется опять.
Изготовить литейную форму можно и из смеси 75 % формовочного песка, 20 % глины и 5 % каменноугольного песка, которая засыпается в специальный ящик из досок и трамбуется. В утрамбованную землю отжимается модель, получившийся отпечаток присыпается тальком и графитом (угольной пылью), чтобы остывшую алюминиевую деталь можно было легко отделить от формы.
Тигель для плавки
Плавка алюминия в домашних условиях требует наличия специальной емкости с носиком из тугоплавкого материала. Это так называемый тигель. Тигли могут быть фарфоровые, кварцевые, стальные, чугунные, изготовленные из корунда или графита. В домашних условиях можно использовать покупной тигель или изготовить его, например, из отрезка стальной трубы достаточно большого диаметра. Правда, для этого нужна болгарка, сварочный аппарат и навыки владения этими инструментами.
Размеры тигля зависят от необходимого количества алюминия, который нужно расплавить. Этот ковш должен равномерно прогреваться, а его тепло — передаваться к сырью.
Печи для плавки
Технология плавки алюминия в домашних условиях достаточно проста. В специальном ковше нагревается лом алюминия до температуры, превышающей температуру плавления этого металла, расплав некоторое время выдерживается в разогретом состоянии, с его поверхности снимается шлак, затем чистый металл разливается в форму для остывания. Время плавки зависит от конструкции печи, то есть той температуры, которую она способна обеспечить.
Если используется паяльная лампа или газовая горелка, то они нагревают алюминий сверху. Правда, печь при этом все равно складывается из кирпичей колодцем без связующего раствора, внутри которого будут прогорать угли для нагревания емкости снизу и поддержания ее в нагретом состоянии.
Примерно так же выглядит конструкция печи, если тигель прогревается снизу с помощью обычных дров и фена для сушки волос. Только в этом случае дрова укладываются в кирпичном колодце не на дно, а на решетку, расположенную на первом ряду кирпичей, а в этом ряду оставляется отверстие для металлической трубы, надетой на горловину фена и закрепленной на ней изолентой. Тиглем в этом случае служит консервная банка, естественно, не алюминиевая, в которой на небольшом расстоянии от верха проделываются диаметрально противоположные сквозные отверстия. В эти отверстия продевается стальной прут, за который банка должна подвешиваться в печи. Фен нужен для нагнетания горячего воздуха в пространство между кирпичами и тиглем. Иногда вместо кирпичей используют металлическую бочку.
Если плавка должна происходить достаточно часто, то можно своими руками изготовить муфельную печь с вертикальной загрузкой тигля или купить готовую.
Физические свойства
- Плотность — 2712 кг/м3.
- Температура плавления — от 658°C до 660°C.
- Удельная теплота плавления — 390 кДж/кг.
- Температура кипения — 2500 °C.
- Удельная теплота испарения — 10,53 МДж/кг.
- Удельная теплоемкость — 897 Дж/кг·K.
- Электропроводность — 37·106 См/м.
- Теплопроводность — 203,5 Вт/(м·К).
Плавка с помощью паяльной лампы
Плавка алюминия в домашних условиях паяльной лампой должна происходить не в помещении. Кроме сырья, паяльной лампы, тиглей и кирпичей, нужно подготовить дрова, пассатижи и стальной прут.
Итак, из кирпичей изготовлен небольшой колодец так, чтобы сверху можно было установить ковш с алюминием и стальной небольшой лист. В колодце разжигается костер, который должен немного прогореть, чтобы образовались угли.
Дальше и происходит, собственно, плавка алюминия в домашних условиях. Пошаговая инструкция процесса:
— На кирпичи устанавливается емкость с сырьем. Ее нужно греть примерно 15 минут.
— После этого на полную мощность включается горелка паяльной лампы и алюминий прогревается сверху.
— В течение нескольких секунд начинается процесс, но для того чтобы прогрев был равномерным, металл в емкости нужно аккуратно перемешивать стальным прутом, придерживая ее пассатижами (не забыв при этом надеть рукавицы). Можно обойтись и без прута, периодически встряхивая ковш с помощью тех же плоскогубцев, но очень осторожно.
— Когда жидкость становится однородной, нужно пассатижами взять емкость и вылить содержимое на прокаленный стальной лист таким образом, чтобы вся образовавшаяся окалина осталась в ковше, а на лист для застывания попал только чистый металл.
Так обычно из вторичного сырья получают чистый алюминий, если с его помощью нужно запаять алюминиевые детали.
Строительство
Перспективность применения алюминиевых сплавов в строительных конструкциях подтверждается технико-экономическими расчетами и многолетней мировой практикой в области сооружения различных строительных объектов.
Внедрение алюминиевых сплавов в строительстве уменьшает металлоемкость, повышает долговечность и надежность конструкций при эксплуатации их в экстремальных условиях (низкая температура, землетрясение и т. п.). В зависимости от назначения строительных алюминиевых конструкций рекомендуются различные марки сплавов: АД1, АМц, АМг2, АД31, 1915 и др.
Рисунок 4 – Здание со светопрозрачными конструкциями из алюминия
Опыт, накопленный в США, подтверждает целесообразность использования алюминиевых сплавов в строительных конструкциях. На них расходуется больше алюминия, чем в любой другой отрасли промышленности. При этом предпочтение отдается внедрению свариваемых сплавов серии Зххх, 5ххх и 6ххх.
Плавка на дровах или газе
Плавка алюминия в домашних условиях на дровах происходит в легких разборных печах. Минусом такого способа является неконтролируемость процесса. Увеличить или уменьшить температуру нагрева невозможно. Вмешаться в процесс возможно, только сняв емкость с алюминием с огня.
Плавка алюминия в домашних условиях на газу — это единственно возможный вариант для квартиры. Греть емкость нужно долго, периодически сливая расплавленный металл. В таком случае отливка выполняется слоями. Для работы понадобятся две металлические емкости таких диаметров, чтобы одна надевалась на другую. Меньшая служит тиглем. Она с ломом, например нарезанной алюминиевой проволокой, ставится на конфорку, с которой нужно снять рассекатель пламени, бытовой газовой плиты. Над большей емкостью придется предварительно поработать. В ее днище выполняются около десятка небольших отверстий. В два или три из них вкручиваются болты, которые исполняют роль рукояток, за которые пассатижами раскаленную емкость можно поднять.
Эта емкость кверху дном надевается на тигель. Такая конструкция и позволяет прогревать алюминий. Периодически верхнюю емкость нужно снимать и металлическим прутом или ножом перемешивать лом. Перед тем как слить расплавленный металл, с его поверхности нужно снять шлак.
Плавка алюминия в муфельной печи
Муфельная печь – это уже достаточно серьезное оборудование для получения качественного расплавленного металла. Поэтому при плавке используют флюс для очистки алюминия от примесей. И это уже почти производственный процесс, а не плавка алюминия в домашних условиях.
Пошаговая инструкция включает еще и несколько пунктов по подготовке сырья:
- Сначала в тигле расплавляется флюс, которого нужно взять в количестве от 2 до 5 % от веса алюминия, а затем в него добавляется лом.
- Насколько флюс активен, можно определить по поверхности расплава – она должна быть зеркальной. Если это не так, в расплав добавляется еще немного флюса, затем нужно будет добавить его перед окончанием плавки, чтобы шлак было легче удалять с поверхности металла стальной ложкой.
- Плавку нужно вести примерно при 700-750 °С. Это температура красного свечения.
- В процессе плавки может потребоваться добавлять сырье в тигель, так как расплавленный металл сильно уменьшается в объеме.
- Рафинирующий флюс добавляют при необходимости в конце плавки в количестве 0,25 % от веса расплавленного металла. Выдерживание такой пропорции в домашних условиях – задача непростая.
После добавления флюса расплав нужно перемешать ложкой, дать постоять около 5 минут, затем снять шлак.
- Когда в результате нагрева алюминий превратился в однородную блестящую каплю, тигель нужно еще некоторое время подержать в печи, чтобы металл стал более текучим.
- Затем алюминий из тигля через носик (в этот момент становится понятно, зачем нужен именно такой ковш) заливается тонкой непрерывной струйкой в форму.
- После полного остывания форма аккуратно разделяется на половинки, из нее извлекается готовая деталь, которую еще нужно окончательно обработать: просверлить отверстия, если нужно, зачистить и наждачной бумагой отшлифовать поверхность. Вот и все. Процесс завершен.
Так что не стоит заранее пугаться, если предстоит в домашних условиях расплавить алюминиевый лом, чтобы получить чистый металл или изготовить деталь взамен поломавшейся. Серьезные профессиональные навыки для организации такого литейного производства совсем не нужны. Желание и умелые руки обычного мастера-любителя способны творить чудеса.
Химический состав алюминиевых сплавов
Алюминиевые сплавы | |||||||||||||
Марка | Массовая доля элементов, % | Плотность, кг/дм³ | |||||||||||
ГОСТ | ISO209-1-89 | Кремний (Si) | Железо (Fe) | Медь (Cu) | Марганец (Mn) | Магний (Mg) | Хром (Cr) | Цинк (Zn) | Титан (Ti) | Другие | Алюминийне менее | ||
Каждый | Сумма | ||||||||||||
АД000 | A199,8 1080A | 0,15 | 0,15 | 0,03 | 0,02 | 0,02 | 0,06 | 0,02 | 0,02 | 99,8 | 2,7 | ||
АД00 1010 | A199,7 1070A | 0,2 | 0,25 | 0,03 | 0,03 | 0,03 | 0,07 | 0,03 | 0,03 | 99,7 | 2,7 | ||
АД00Е 1010Е | ЕА199,7 1370 | 0,1 | 0,25 | 0,02 | 0,01 | 0,02 | 0,01 | 0,04 | Бор:0,02 Ванадий+титан:0,02 | 0,1 | 99,7 | 2,7 |
Температура плавления алюминия и его сплавов в домашних условиях
data-ad-client=»ca-pub-6800991780184491″
data-ad-slot=»3086014295″>
Данный элемент (Al) является самым распространенным среди всех металлов. Благодаря своим особым свойствам (небольшой вес, мягкость и ряд других), он нашел широкое применение не только в промышленности. С алюминием часто имеют дело и домашние умельцы, так как его обработка труда не представляет ввиду невысокой температуры плавления.
Иногда приходится расплавлять этот металл для заливки в определенные формы. Как это сделать, причем в бытовых условиях, без специального оборудования – этот вопрос интересует многих. Прежде всего, нужно отметить, что плавление можно осуществить двумя способами – поверхностным нагревом металла и «внутренним». Последний способ в домашних условиях вряд ли осуществим, так как предусматривает применение специального оборудования. Например, для нагрева индукционного. Следовательно, самостоятельно можно использовать только способ внешнего воздействия (теплового) на Al.
Мы не будем рассматривать все нюансы, так как точная температура плавления зависит от нескольких факторов – давления, химической чистоты материала и некоторых других.
Поэтому приведем только усредненное значение – 660 ºС (по шкале Кельвина это 993,5 º).
А вот мнения о том, можно ли достигнуть такой температуры в домашних условиях, встречаются разные. Одни «самоделкины» утверждают, что сами плавили Al на обычном костре (даже указывают температуру в 560 ºС), другие над этим смеются и говорят, что придется применять мощные нагревательные приборы и при этом не смотреть на эл/счетчик, а то мол, «сердце прихватит» от того, как он «накручивает».
Правильность утверждений о том, что алюминий можно расплавить на открытом огне, можно проверить только на практике. Попробуйте, может, и получится.
Остается добавить, что не все изделия, которые мы считаем «алюминиевыми» (например, кастрюли), на самом деле являются таковыми. В чистом виде этот металл в производстве редко используется. Как правило, все разновидности подобной продукции сделаны из различных сплавов Al, которые в обиходе имеют общее название «дюраль». А она плавится и при меньших значениях температуры.
data-ad-client=»ca-pub-6800991780184491″
data-ad-slot=»8527752561″>
Как правильно расплавить алюминий в домашних условиях подручными средствами.
Статьи о промышленности
Сегодня мы напишем, как правильно расплавить алюминий в домашних условиях на газовой плите. Осуществляя плавление мы будем использовать подручные средства в частности у нас имеется отдельная часть половника который сделан из нержавеющей стали поэтому при повышении температуры он не расплавится и его можно использовать как ковш для плавления алюминия. В нашем ассортименте находится алюминиевые и дюралевые кусочки, которые были взяты из радиотехники.
Что бы правильно расплавить алюминий в домашних условиях мы на первом этапе включаем газовую плиту и оставляем гореть на 15 минут. Прогревание для того чтобы достичь максимальной температуры наших кусочков алюминия.
Конечно, расплавить алюминий средствами одной конфорки в домашних условиях у нас не получится, тем не менее, используя данную конфорку, мы прогреем алюминий до нужной температуры и затем выполним расплавление, используя китайскую газовую горелку.
При таком плавлении желательно использовать респиратор или другие средства защиты с тем, чтобы не дышать краской, которой покрыты наши куски алюминия при обжигании. Такой подход позволит правильно расплавить алюминий в домашних условиях с максимальной безопасностью.
Еще важный момент касаемо безопасности при плавлении алюминия на газовой плите в домашних условиях. Так необходимо работать под вытяжкой, которая включена. Все манипуляции с емкостью необходимо проводить с использованием плоскогубцы с тем, чтобы жестко фиксировать наш алюминий и тем самым обезопасить от высказываний. При использовании пинцетов или зажимов есть вероятность опрокинуть расплавленный алюминий в домашних условиях.
На конечной стадии плавления алюминия используем плоскогубцы и слегка встряхиваем форму и видим жидкий алюминий. Для отделения шлака мы используем тонкую проволоку которую также фиксируем пассатижами и размешиваем расплавленный металл . Что бы правильно расплавить алюминий в домашних условиях необходимо все манипуляции проводить очень аккуратно с тем чтобы не опрокинуть нашу емкость.
В результате у нас получился слиток алюминия выплавленного в домашних условиях. По своему виду он достаточно сильно похож на каплю ртути. Таким видом обладают практически все выплавляемые металлы.
Шлаг или аплой необходимо вытряхнуть из нашей плавильни пока он полностью не остыл и не присох к поверхности, что затрудняет его дальнейшее удаление.
Отвечая на вопрос как правильно расплавить алюминий в домашних условиях подручными средствами, не забываем о безопасности. Так, после того как капля остынет, использует пассатижи и аккуратно опускаем каплю в воду только после этого можно брать слиток алюминия плавленый в домашних условиях руками.
Печь для плавки алюминия своими руками
Содержание статьи:
Один из самых известных и распространенных на земле металлов – алюминий. Его технические характеристики позволяют его использовать в машиностроении и производить летательные аппараты, витринное остекление и детали для газового, тепло- и электрооборудования. Из него делают амальгаму для зеркал и составы для пиротехники.
Работа с этим металлом в домашних условиях осложняется тем, что температура плавления его составляет 660оС. Такие высокие температуры для плавки не очень легко получить, а производственный метод электролиза оксида алюминия с другими химикатами попросту не осуществим.
Однако расплавить алюминий можно, если сделать самодельную муфельную печь, которая при соблюдении всех правил может развить температуру свыше 1100оС.
Список материалов для изготовления муфельной печи
- Огнеупорный шамотный кирпич;
- Нить накала (фехраль Х23Ю5Т, сечение – 1мм) – 18 м;
- Контроллер 1300 с твердотельным реле;
- Термопара (датчик температуры) на номинал выше расчетного;
- Пара керамических предохранителей;
- Минвата для теплоизоляции;
- Вспомогательные комплектующие.
Инструменты
- Болгарка с диском по камню;
- Термоусадка или изолента;
- Ручной слесарный и разметочный инструмент.
Изготовление самодельной печи для плавки алюминия
На куске картона размечаем проекцию будущей печи. В сечении это будет полый цилиндр с толщиной стенок, равной толщине кирпича.
Разбиваем окружность цилиндра на шесть равных частей по количеству элементов. В очертание окружности вписываем грани кирпичей, чтобы затем сделать единый шаблон для деталей этих стенок.
Кирпичи выставляем в вертикальном положении на так называемый тычок (торец). На него выставляем шаблон подрезки и очерчиваем его по контуру карандашом. Из шести прямоугольных кирпичей (параллелепипедов) должна получиться окружность цилиндра. Стыки остаются прямыми без четвертей, однако опытные мастера подтверждают, что значительная часть теплопотерь образуется именно ввиду расширения этих зон во время нагрева внутренности печи.
Для подрезки рекомендуется использовать крупную болгарку с диском по камню. При отсутствии охлаждения водой необходимо взять диск для сухого реза по камню. На быструю руку можно сделать приспособление в виде небольшого станка с закрепленной болгаркой и подвижной кареткой для более удобной резки.
Стесываем внешние края кирпичей, а на внутренних стенках делаем по 5 борозд в каждой для расположения нити накала. Также снаружи делаем 3 поперечных колеи для того, чтобы связать кирпичи проволокой в единую конструкцию. Должно выйти шесть таких заготовок (фото).
Изготавливаем спираль из нити накала (фехраль Х23Ю5Т, сечение – 1мм). Она более доступна по цене чем нихром, продается в виде проволоки. Наматываем на сердечник с помощью дрели или токарного станка. В нашем случае получился нагреватель мощностью 1,7КВт. Размещаем его внутри печки в готовых бороздах, а сами кирпичи стягиваем между собой.
Для корпуса печки была выбрана нержавеющая емкость подходящего размера. На небольшой высоте от днища закрепляем два небольших квадрата (15х15 или 20х20), а на них располагаем пару шамотных кирпичей в виде днища печи.
Корпус изнутри прокладываем теплоизолятором, для которого была выбрана минеральная вата. Такой теплоизолятор не очень долговечен, однако его при случае легко заменить.
Кирпичный цилиндр печи помещаем на его место, контакты вводим снаружи корпуса, защищая их от нагрева керамическими предохранителями.
Электронная схема данной печи не очень сложна. Все детали продаются как в местных магазинах электроники, так и на Алиэкспресс. За регулировку температуры отвечает контроллер с электронным циферблатом настройки температуры. Датчиком служит термопара, реле твердотельное с охлаждающим радиатором.
Корпус блока питания взят от стационарного компьютера, и размещен на двух угловых кронштейнах на расстоянии от корпуса. Подключаем печь к сети и пробуем прогреть ее до нужной температуры. По всем расчетам на это понадобится не менее 2-х часов.
В итоге у нас получилась отличная модель высокотемпературной печи, в которой можно не только плавить алюминий, но и производить закалку, отпуск металлов, и даже обжиг керамики.
Видео по изготовлению муфельной печи для плавки алюминия
Самодельная печь для плавки алюминия в домашних условиях
3.7/5 — Оценок: 3Можно ли расплавить фольгу. Плавка алюминиевых сплавов.
Для многих термин «литейное производство» тесно связано с непосильным трудом и специальными профессиональными умениями и навыками. На самом деле отлить деталь из необходимого металла реально для самого обычного человека без профессиональной подготовки в домашних условиях. Процесс имеет свои тонкости, но по силам для выполнения в домашних условиях своими руками. Внешне напоминает изготовление свинцовых грузов для рыбалки. Особенности процесса литья алюминия связаны с техническими характеристиками материала.
Характеристика алюминия. Алюминий один из самых распространённых металлов.
Он серебристо-белого цвета, достаточно хорошо поддаётся литью и механической обработке. В силу своих особенностей алюминий оснащён высокой теплопроводимостью и электропроводимостью, а также обладает коррозионной стойкостью.
У технического алюминия температура плавления равна 658 градусам, у алюминия высокой чистоты — 660, температура кипения алюминия составляет 2500 градусов.
Для отливки алюминия домашние нагревательные приборы вряд ли будут полезны и обеспечат нужной температурой. Нужно расплавить алюминий, нагревая его до температуры свыше 660 градусов.
Литье алюминия: выбор источника тепла
В качестве источника тепла для плавки алюминия можно использовать:
- Очень действенный способ достигается благодаря собственноручной тигельной муфельной печи.
В рабочую поверхность данной печи устанавливается тигля (необходимый инструмент для плавки алюминия), в него добавляют сырье. С помощью муфельной печи можно очень просто отлить алюминий.
- Для получения температуры плавления алюминия достаточно температуры горения сжиженного или природного газа, в этом случае процесс можно выполнить в самодельной печи.
- При небольшом объеме плавки можно воспользоваться теплом, получаемом при горении газа в бытовой газовой плите.
- Необходимую температуру обеспечат газовые резаки или ацетиленовые генераторы, если таковые имеются в домашнем хозяйстве.
Подготовка алюминия
Несмотря на то что процесс плавки будет выполняться в домашних условиях, к нему необходимо отнестись ответственно. Металл предварительно необходимо очистить от грязи, раздробить на небольшие куски. В этом случае процесс плавки пойдет быстрее.
Выбор останавливают на более мягком алюминии, как более чистом материале, с меньшим количеством примесей. Во время плавки с жидкой поверхности металла убирают шлак.
Литье в песчаные формы
Для изготовления деталей литьем применяется несколько технологий. Самая простая — литье в песчаные формы:
- Если требуется изготовить алюминиевую деталь простой формы, то выполнять литье можно открытым способом непосредственно в грунт — кремнезем. Изготавливают небольшую модель из любого материала: дерево, пенопласт. Устанавливают в опоку. Грунт укладывают вокруг небольшими слоями и тщательно трамбуют. После того как образец извлекают, кремнезем хорошо держит форму и литье выполняют прямо в нее.
- В качестве формирующей смеси можно использовать песок, соединенный с силикатным клеем, или цемент, замешанный на тормозной жидкости. Соотношение материалов должно быть таким, чтобы если смесь сжимать, она сохраняла форму.
Видео «Литьё алюминия в земляную (песочную) форму в домашних условиях»
Для деталей сложной формы применяется иная технология.
Литье по выплавляемым моделям
Этот известный давно способ для изготовления алюминиевых изделий в домашних условиях может быть немного изменен.
Из легкоплавкого материала изготавливается модель. Укладывается в определенную форму, заливается гипсом. Устанавливается один литник или несколько. После того как гипс застыл, его хорошо просушивают. При высокой температуре легкоплавкий материал переходит в жидкое состояние и вытекает через литник. В полученную форму льют алюминиевую заготовку.
Подробности процесса можно уточнить по видео.
Видео «Литье алюминия под высоким давлением»Таким образом, изготовить необходимую деталь из алюминия различной формы можно даже самому обычному мастеру-любителю.
Как отлить деталь сложной формы из алюминияНа промышленных предприятиях зачастую используют металлические формы. Литейные формы для отливки алюминия можно получить из различных материалов. Чаще всего, используют гипс. Гипс можно приобрести в любом строительном магазине по любой приемлемой для вас цене. Рекомендуется использовать скульптурный или белый гипс.
Отличный вариант — скульптурный, который маркируется Г-16. В связи с высокою ценою можно заменить на Г-7 — обычный белый гипс. Категорически запрещается выполнять замену на алебастр, несмотря на то что они в строительных работах часто взаимозаменяемые.
Рассмотрим простой способ отливки детали из алюминия своими руками в домашних условиях.
Чтобы отлить деталь из алюминия нам потребуется:
- сосуд для плавки;
- металлолом;
- форма для плавки.
Основные этапы процесса:
1. Подготавливаем сосуд для плавки (можно использовать сосуд из части стальной трубы).
2. Изготавливаем форму для плавки. Если деталь имеет сложную конструкцию, то форма может иметь несколько составляющих.
В нашем варианте форма будет состоять из двух частей. Сначала продумайте, как упростить деталь для удобства (рекомендуем укрепить отверстия с помощью скотча).
Форму очень просто сделать из скульптурного гипса (не применяйте алебастр!). Можно воспользоваться пластилином.
3. Прежде чем заливать гипс, следует смазать ёмкость маслом, чтобы гипс не смог прилипнуть к ёмкости.
4. Аккуратно залейте гипс, периодически встряхивайте форму для того, чтобы вышли пузырьки.
Важно знать: процесс затвердевания гипса достаточно быстрый, поэтому будьте внимательны и постарайтесь вовремя установить модель в гипс.
5. Необходим первичный слой для предстоящей заливки.
Берём сверло и делаем 4 небольших отверстия, форму обрабатываем маслом. Это необходимо для того, чтобы готовые детали форм лежали максимально устойчиво в процессе отливки.
6. Делаем заливку второго слоя.
7. После того, как произойдёт затвердевание, необходимо аккуратными движениями извлечь форму из ёмкости и разделить половинки.
8. Перед отливкой обрабатываем форму сажей, чтобы избежать прилипания жидкого алюминия. Форму необходимо просушить. Естественным путем процесс сушки происходит целый день. Желательно просушить гипсовую заготовку в духовом шкафу. Начинать с температуры 11 — один час и два часа при температуре 300
С. В гипсе необходимо предусмотреть отверстия для заливки алюминия и удаления остатков воздуха.
Таким способом плавим алюминий.
9. Затем жидкий металл помещаем в форму и ждём полного остывания.
В результате получаем нужную заготовку, затем её шлифуем и делаем специальные отверстия.
Литье по выжигаемым моделям: особенности технологии
Изготовление детали из алюминия с помощью литья по выжигаемым моделям имеет свои особенности, которые будут рассмотрены ниже. Работы выполняются в следующей последовательности:
- В качестве материала для модели в домашних условиях используют пенопласт. С помощью режущих элементов и клея изготовьте фигуру, очертаниями напоминающую требуемую форму.
- Приготовьте емкость для изготовления модели. Можно воспользоватся старой коробкой из-под обуви. Смешайте алебастр с водою.
Залейте смесь в коробку. Поместите пенопластовую модель. Разровняйте. Дайте время материалу хорошо застыть. В связи с быстрым процессом застыванию алебастра, работы выполняйте в ускоренном темпе.
- Удалите коробку. Прогрейте форму в печи для того чтобы просушить алебастр и убрать остатки влаги. В противном случае вся воды из алебастра поступит в алюминий и превратится в пар, что приведет к порам в металле и выплескиванию алюминия из формы при выполнении работ.
- Расплавьте алюминий. Удалите с жидкой поверхности расплавленный шлак. Заливайте металл в форму на место пенопласта. От высокой температуры последний начнет выжигаться и его место займет алюминий.
- После того как металл остынет, разбейте форму и достаньте полученную литую алюминиевую модель. Посмотреть процесс подробнее можно по видео.
Техника безопасности и подготовка рабочего места
Высокотемпературные работы отличаются вредными испарениями и сопровождаются выделением дыма, поэтому выполнять их необходимо на открытом воздухе или принудительно проветриваемом помещении. Необходимо использовать вентилятор с боковым обдувом.
Процесс литья сопровождается брызгами, возможны потоки расплавленного металла. Рабочее место потребуется предварительно застелить листом металла. Не рекомендуется работы выполнять в жилом помещении — это небезопасно для окружающих.
Основные ошибки при литье алюминия
Прежде чем выполнять литье алюминия в домашних условиях, обратите внимание на основные ошибки, которые наблюдаются при выполнении работ:
- При изготовлении гипсовых форм необходимо чтобы в процессе сушки испарилась вся влага. В противном случае при заполнении формы вода начинает испаряться, превращается в пар и может остаться внутри алюминия в виде пор и раковин.
- При недостаточном нагреве или если перед началом выполнения работ алюминий успел остыть, металл будет плохо заполнять форму и отдаленные участки останутся полыми.
- Не стоит охлаждать металл погружением в жидкость. В этом случае нарушается внутренняя структура материала.
Алюминий может гнуться как бумага или быть твёрдым как сталь. Алюминий повсюду, даже внутри нас.
Каждый взрослый получает около 50 мг алюминия каждый день вместе с пищей, это ни какая-то диета, просто этого не избежать.
Алюминий самый распространённый металл на планете. Его содержание в земной коре 8 %, но его не просто добывать, по крайней мере, в чистом виде.
В отличие от золота и серебра, алюминии не встречается в виде самородков или целых жил. Алюминий в 3 раза легче железа или меди.
Алюминий в своём первоначальном виде совсем не похож на металл, это всё из-за особой «любви» алюминия к кислороду.
Фактически первое применения алюминия в истории произошло, когда восточные гончары добавляли глину богатую алюминием в свои изделия, чтобы сделать их крепче.
Достаточный для производства пивных банок, прочный для гоночных автомобилей, гибкий для обшивки самолётов, способный превратиться во что угодно, алюминий – не заменимый материал для современного мира.
И это ещё не все особенности, который хранит этот полезный металл.
Плавка большинства алюминиевых сплавов не составляет затруднений Легирующие компоненты, за исключением магния, цинка, а иногда и меди, вводят в виде лигатур При выплавке небольших порций литейных сплавов в тигельных печах защитные флюсы, как правило, не применяют. Обязательной операцией является рафинирование от неметаллических включений и растворенного водорода. Наиболее сложными в плавке являются алюминиевомагниевые и многокомпонентные жаропрочные сплавы.
При плавке деформируемых сплавов особое внимание уделяется очистке печи от шлака и плен предшествующей плавки. При переходе на другую марку сплава, кроме переходных плавок, печь и миксеры промывают с целью удаления остатков старого сплава. Количество металла для промывки должно составлять не меньше четверти емкости печи. Температуру металла во время промывки поддерживают на 40-50 °C выше температуры разливки сплава до промывки. Для ускорения очистки металл в печи интенсивно перемешивают в течение 8-10 мин. Для промывки используют алюминий или переплав Б тех случаях, когда металл из печи сливается полностью, можно ограничиться промывкой флюсами. Плавку сплавов ведут под флюсом
Шихтовые материалы загружают в такой последовательности: чушковый алюминий, крупногабаритные отходы, переплав, лигатуры (чистые металлы). В жидкий металл при температуре не выше 730 °C разрешается загружать сухую стружку и малогабаритный лом. Медь вводят в расплав при температуре 740-750 °С, кремний — при 700-740 °С с помощью колокольчика. Цинк загружают перед магнием, который обычно вводят перед сливом металла. Максимально допустимый перегрев для литейных сплавов 800- -830 «С, а для деформируемых 750-760 °С.
При плавке на воздухе алюминий окисляется. Основными окислителями являются кислород и пары воды. В зависимости от температуры и давления этих газов, а также кинетических условий взаимодействия в результате окисления алюминия образуются оксид алюминия Al2O3, а также Al2O и AlO. Вероятность образования возрастает с увеличением температуры и уменьшением парциального давления кислорода в системе. В обычных условиях плавки термодинамически устойчивой фазой является твердый оксид алюминия γ-Al2O3, которая не растворяется в алюминии и не образует с ним легкоплавких соединений. При нагреве до 1200 °C γ-Al2O3, перекристаллизовывается в α-Al2O3. По мере окисления на поверхности твердого и жидкого алюминия образуется плотная, прочная пленка оксида толщиной 0,1-10 мкм в зависимости от температуры и длительности выдержки. При достижении такой толщины окисление практически приостанавливается, так как диффузия кислорода через пленку резко замедляется.
Процесс окисления жидких сплавов алюминия очень сложен и недостаточно изучен. Имеющиеся литературные данные показывают, что интенсивность окисления составляющих сплава является функцией давления кислорода, давления диссоциации их оксидов, концентрации составляющих в сплаве, скорости диффузии атомов навстречу атомам кислорода, взаимодействия оксидов между собой и т. д. Кинетика окисления определяется сплошностью, плотностью и прочностью окисной пленки. При одинаковой концентрации прежде всего окисляются наиболее активные элементы, у которых образование окисла связано с наибольшим уменьшением изобарно-изотермического потенциала.
Большинство легирующих элементов (медь, кремний, марганец) не оказывают существенного влияния на процесс окисления алюминия и защитные свойства окисной пленки, так как обладают отношением VMem0/mVMe≥1. Окисная пленка на двойных сплавах алюминия с этими элементами при низкой их концентрации состоит из чистой γ-Al2O3. При значительных содержаниях этих элементов образуются твердые растворы оксидов легирующих элементов в γ-Al2O3 и соответствующие шпинели.
Щелочные и щелочноземельные металлы (калий, натрий, барий, литий, кальций, стронций, магний), а также цинк (0,05-0,1 %) сильно увеличивают окисляемость алюминия. Причина этого — рыхлое и пористое строение оксидов этих элементов. Окисная пленка на двойных расплавах в этом случае обогащена оксидами щелочных и щелочноземельных металлов. Для нейтрализации вредного влияния цинка в алюминиевые расплавы вводят 0,1- 0,15 % Mg.
Сплавы алюминия с магнием образуют окисную пленку переменного состава. При малом содержании магния 0,005 % (по массе) — окисная пленка имеет структуру γ-Al2O3 и представляет собой твердый раствор MgO в γ-Al2O3; при содержании 0,01-1,0 % Mg окисная пленка состоит из шпинели (MgO*Al2O3) переменного состава и кристаллов оксида магния; при содержании свыше 1,5 % Mg окисная пленка почти полностью состоит из оксида магния.
Бериллий и лантан замедляют окисление алюминиевых сплавов. Добавка 0,01 % бериллия или лантана снижает скорость окисления сплавов Al-Mg до уровня окисления алюминия. Защитное действие этих элементов объясняется уплотнением окисной пленки посредством заполнения образующихся пор окислами бериллия и лантана.
Сильно снижают окисляемость алюминиевых расплавов фтор и газообразные фториды (SiF4, BF3, SF6 и др.), присутствующие в печной атмосфере в количестве до 0,1 % (по массе). Адсорбируясь на поверхности окисной пленки, они уменьшают скорость проникновения кислорода к поверхности металла.
Перемешивание расплава в процессе плавки сопровождается нарушением целостности окисной пленки и замешиванием обрывков ее в расплав, Обогащение расплавов окисными включениями происходит и в результате обменных реакций с футеровкой плавильных устройств. Наиболее существенное влияние на степень загрязнения расплавов пленками оказывает поверхностная окисленность исходных первичных и вторичных шихтовых материалов. Отрицательная роль этого фактора возрастает по мере уменьшения компактности и увеличения удельной поверхности материала.
Окисная пленка шихты является также источником насыщения расплава водородом, так как на 30-60 % состоит из Al(OH)3. Химически связанная влага с трудом удаляется с поверхности шихтовых материалов даже при температуре 900 С. Гидроксид, попадая в расплав, сильно насыщает его водородом. По этой причине нежелательно вводить в шихту стружку, опилки, обрезь, сплесы и другие некомпактные отходы. Особое значение имеет организация хранения и своевременная переработка отходов и возврата собственного производства, предотвращающие окисление и коррозию с образованием гидроксидов. Введение в шихту собственных возвратов связано также с неизбежным накоплением в сплавах вредной примеси железа, образующего с компонентами сплавов сложные твердые интерметаллические соединения, снижающие пластические свойства и ухудшающие обработку отливок резанием.
Наряду с оксидами и интерметаллидами в расплаве могут присутствовать и другие неметаллические включения — карбиды, нитриды, сульфиды. Однако количество их по сравнению с содержанием оксидов мало. Фазовый состав неметаллических включений в алюминиевых сплавах разнообразен. Кроме оксидов алюминия, в них может содержаться оксид магния (MgO), магнезиальная шпинель (MgAl2O4), нитриды алюминия, магния, титана (AlN, Mg3N2, TiN), карбид алюминия (Al4C3), бориды алюминия и титана (AlB2, TiB2) и др. Основную массу включений составляют оксиды.
В зависимости от происхождения неметаллические включения, встречающиеся в сплавах, можно подразделить на две группы: дисперсные включения и пленки Основная масса дисперсных включений имеет размер 0,03-0,5 мкм. Они сравнительно равномерно распределены в объеме расплава. Наиболее вероятная толщина окисных пленок 0,1-1,0 мкм, а протяженность — от десятых долей миллиметра до нескольких миллиметров. Концентрация таких включений сравнительно мала (0,1-1,0 мм2/см2), а распределение крайне неравномерно. При выстаивании расплавов крупные включения могут всплывать или осаждаться. Однако ввиду большой удельной поверхности пленок и малого отличия их плотности от плотности расплавов всплывание (осаждение) идет медленно, большая часть пленок остается в расплаве и при заполнении формы увлекается в отливку. Еще более медленно отделяются тонкодисперсные взвеси. Практически все количество их переходит в отливку.
Во время плавки алюминий насыщается водородом, содержание которого может достигать 1,0-1,5 см3 на 100 г металла. Основным источником водорода являются пары воды, парциальное давление которых в атмосфере газовых плавильных печей может достигать 8-16 кПа.
Влияние легирующих элементов и примесей на равновесную растворимость водорода в алюминии мало изучено. Известно, что медь и кремний уменьшают растворимость водорода, а магний — увеличивает. Растворимость водорода увеличивают также все гидрообразующие элементы (титан, цирконий, литий, натрий, кальций, барий, стронций и др), Так, сплав алюминия с 2,64 % Ti может выделить до 25 см3 водорода на 100 г, а сплав алюминия с 5 % Zr — 44,5 см3 на 100 г. Наиболее активно увеличивают растворимость водорода и алюминия щелочные и щелочноземельные металлы (натрий, литий, кальций, барий), образующие гидриды.
Существенную долю растворенного в сплавах водорода составляет газ, вносимый лигатурами и электролитической медью Так, например, лигатура алюминий-титан в зависимости от технологии выплавки может содержать до 10 см3 водорода на 100 г, а электролитическая медь с наростами — до 20 см3 на 100 г. Литейные сплавы содержат большее количество примесей и неметаллических включений, чем деформируемые. Поэтому они в большей степени предрасположены к поглощению газов
Кинетика процесса наводороживания алюминиевых расплавов лимитируется массопереносом водорода в жидком металле, через поверхностную окисную пленку и в газовой среде. Наиболее существенное влияние на массоперенос оказывают состав сплава и содержание неметаллических включений, определяющих проницаемость окисной пленки, диффузионную подвижность водорода и возможность выделения его из расплава в виде пузырьков. На проницаемость пленки существенное влияние оказывает также состав газовой среды. Диффузионную подвижность водорода в алюминии уменьшают медь, кремний и особенно магний, марганец и титан. Тонко дисперсные неметаллические включения, обладая высокой адсорбционной способностью по отношению к водороду, сильно замедляют его диффузионную подвижность в алюминиевых расплавах.
Пленка оксида алюминия обладает малой проницаемостью для атомов водорода, она замедляет реакции взаимодействия расплава с влагой атмосферы. При толщине пленки 1-10 мкм газообмен между металлом и атмосферой практически прекращается. На проницаемость пленки большое влияние оказывает состав сплава. Все элементы, увеличивающие окисляемость алюминия (магний, литий, натрий, стронций, кальций), увеличивают проницаемость окисной пленки для водорода. Легирующие элементы (медь, цинк, кремний) мало влияют на газообмен. Они несколько разрыхляют окисную пленку и поэтому способствуют более быстрому насыщению сплавов водородом.
На водородопроницаемость окисной пленки существенно влияет состав атмосферы над расплавом. Проницаемость пленки значительно увеличивается, если в газовой среде присутствуют Cl2, C2Cl6, BF4, SiF4, фреоны и другие галоиды. Хлориды, обладая высоким сродством к алюминию, адсорбируются, проникают под окисную пленку и разрушают ее в результате образования газообразного хлорида алюминия. Фториды менее активно взаимодействуют с алюминием. Взаимодействуя с окисной пленкой, они способствуют дегидратации ее поверхности и десорбции молекул и атомов кислорода. Обладая высокой адсорбционной способностью, фториды занимают освобождающиеся активные центры на пленке и создают оксифторидные комплексы типа Al2O2F2, которые прекращают доступ кислорода и паров воды к расплаву, делают пленку тонкой и проницаемой для водорода. Жидкие флюсы, содержащие фториды, также разрушают окисную пленку и облегчают дегазацию расплавов.
Растворенный водород, выделяясь при кристаллизации расплавов, вызывает образование газовой и газоусадочной пористости в отливках. С увеличением концентрации водорода газовая пористость отливок возрастает. Предрасположенность алюминиевых сплавов к газовой пористости определяется степенью пересыщенности твердого раствора водородом, которая выражается отношением η — (Сж-Ств)/Ств, где Cж и Cтв — концентрации водорода в жидком и твердом сплаве, см3/100 г. Газовая пористость не образуется, когда Стп=Сж. Степень пересыщения твердого раствора увеличивается с увеличением скорости охлаждения.
Для каждого сплава имеются предельные концентрации водорода, ниже которых не происходит образование газовых пор в отливках при заданных скоростях охлаждения. Так, например, для того чтобы предотвратить образование газовых пор при затвердевании толстостенных отливок из сплава Al — 7 % Si, содержание водорода в расплаве не должно превышать 0,15 см3 на 100 г. Предельным содержанием водорода в дуралюминах считается 0,12-0,18 см3 на 100 г в зависимости от интенсивности охлаждения при кристаллизации.
Предохранение алюминиевых расплавов от окисления и поглощения водорода достигается плавкой под флюсами в слабоокислительной атмосфере. В качестве покровного флюса при плавке большинства сплавов, содержащих не более 2 % Mg, используют смесь хлоридов натрия и калия (45 % NaCl и 55 % KCl) в количестве 1-2 % от массы шихты. Состав флюса соответствует твердому раствору с минимальной температурой плавления 660 °С. Для этой цели рекомендуют также и более сложный по составу флюс (табл. 12).
Для алюминиевомагниевых сплавов в качестве покровного флюса используют карналлит (MgCl2*KCl) и смеси карналлита с 40-50 % хлористого бария или 10-15 % фтористого кальция. Если применение флюса невозможно, защиту от окисления осуществляют введением бериллия (0,03-0,05 %). Защитные флюсы широко используют при плавке сплавов в отражательных печах.
Для предотвращения взаимодействия с влагой принимают меры к удалению ее из футеровки плавильных печей и разливочных устройств, из рафинирующих и модифицирующих флюсов; подвергают прокалке и окраске плавильно-разливочный инструмент, производят подогрев, очистку и сушку шихтовых материалов.
Однако как бы тщательно не защищали расплав, при плавке на воздухе он всегда оказывается загрязненным оксидами, нитридами, карбидами, включениями шлака и флюса, водородом, поэтому перед заливкой в формы его необходимо очищать.
Рафинирование расплавов
Для очистки алюминиевых сплавов от взвешенных неметаллических включений и растворенного водорода применяют отстаивание, продувку инертным и активным газами, обработку хлористыми солями и флюсами, вакуумирование, фильтрование через сетчатые и зернистые фильтры, электрофлюсовое рафинирование.
Как самостоятельный процесс отстаивание может быть применимо в тех случаях, когда разность плотностей достаточно велика и размер частиц не слишком мал. Ho и в этих случаях процесс идет медленно, требуется повышенный расход топлива и он оказывается малоэффективным.
Очистка расплавов продувкой инертными или активными газами основана на протекании двух процессов диффузии растворенного газа в пузырьки, продуваемого и флотирующего действия пузырьков по отношению к включениям и мельчайшим газовым пузырькам.
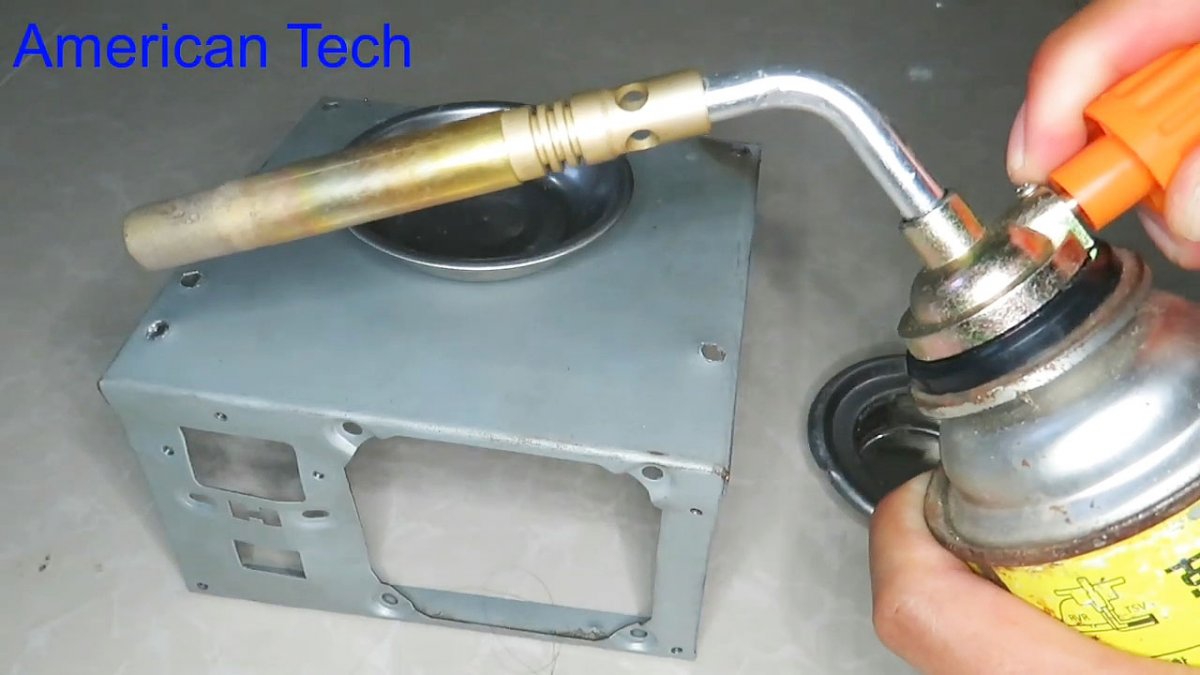
Продувку расплавов газами широко используют в литейных цехах по производству слитков. Ее осуществляют в специальных футерованных коробах, установленных на пути перелива металла из миксера в кристаллизатор. Для рафинирования алюминиевых расплавов используют азот, аргон, гелий, хлор и смесь его с азотом (90 %), очищенные от влаги и кислорода.
Продувку азотом или аргоном ведут при 720-730 °С. Длительность продувки в зависимости от объема расплава колеблется в пределах 5-20 мин; расход газа составляет 0,3-1 % от массы расплава. Такая обработка позволяет снизить содержание неметаллических включений до 1.

Обработку расплавов хлором осуществляют в герметичных камерах или ковшах, имеющих крышку с отводом газов в вентиляционную систему. Хлор вводят в расплав через трубки с насадками при 710-720 °C. Длительность рафинирования при давлении хлора 108-118 кПа составляет 10-12 мин; расход хлора — 0,2-0,8 % от массы расплава. Применение хлора обеспечивает более высокий уровень очистки по сравнению с техническим азотом и аргоном. Однако токсичность хлора, необходимость обработки расплавов в специальных камерах и трудности, связанные с его осушкой, существенно ограничивают применение хлорирования расплавов в промышленных условиях. Замена хлора смесью его с азотом (90 %) обеспечивает достаточно высокий уровень очистки, но не позволяет решить проблемы, связанные с токсичностью и осушкой.
Дегазация продувкой сопровождается потерями магния: при обработке азотом теряется 0,01 % магния; при обработке хлором эти потери увеличиваются до 0,2 %.

Рафинирование хлоридами широко используют в фасонно-литейном производстве. Для этой цели применяют хлористый цинк, хлористый марганец, гексахлорэтан, четыреххлористый титан и ряд других хлоридов. Ввиду гигроскопичности хлоридов их подвергают сушке (MnCl2, C3Cl6) или переплавке (ZnCl2). Технология рафинирования хлоридами состоит во введении их в расплав при непрерывном помешивании колокольчиком до прекращения выделения газообразных продуктов реакции Хлористые цинк и марганец вводят в количестве 0,05-0,2 % при температуре расплава 700-730 °С; гексахлорэтан — в количестве 0,3-0,7 % при 740-750 °C в несколько приемов. С понижением температуры эффективность рафинирования снижается в связи с повышением вязкости расплавов; рафинирование при более высоких температурах нецелесообразно, так как оно сопряжено с интенсивным окислением расплава.
В настоящее время в цехах фасонного литья для рафинирования широко используют таблетки препарата «Дегазер», состоящие из гексахлорэтана и 10 % (по массе) хлористого бария, которые вводят в расплав без применения «колокольчиков».
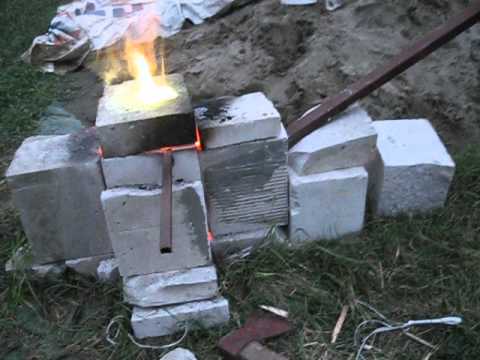
Хлористые соли взаимодействуют с алюминием по реакции: 3МnСl2 + 2Al → 2AlCl3 + 3Мn.
Пузырьки хлористого алюминия, поднимаясь на поверхность расплава, увлекают взвешенные неметаллические включения; внутрь пузырьков диффундирует растворенный в металле водород, происходит очистка расплава. По окончании перемешивания расплаву дают отстояться в течение 10-45 мин при 720-730 °C для удаления мелких пузырьков газа.
Рафинирование хлоридами ведут в печах или ковшах с малой удельной поверхностью расплава. В печах с небольшим по высоте слоем расплава рафинирование хлоридами малоэффективно. По уровню очистки от неметаллических включений и газа обработка хлоридами уступает продувке хлором.
Очистка алюминиевых расплавов флюсами применяется при плавке литейных и деформируемых сплавов. Для рафинирования используют флюсы на основе хлористых солей щелочных и щелочноземельных металлов с добавками фтористых солей — криолита, плавикового шпата, фтористых натрия и калия (табл.

В практике плавки большинства алюминиевых деформируемых сплавов для рафинирования используют флюс № 1.
Для очистки сплавов алюминия с магнием применяют флюсы на основе карналлита — 80-90 % MgCl2*KCl, 10-20% CaF2, MgF2 или K3AlF6. Предварительно переплавленные и высушенные флюсы в количестве 0,5-1 % от массы металла засыпают на поверхность расплава при 700-750 °С. Затем в течение 3-5 мин флюс энергично замешивают в расплав, удаляют шлак и дают расплаву отстояться 30-45 мин. После повторного удаления шлака расплав используют для заполнения литейных форм. При обработке больших объемов металла флюс вводят на дно расплаве с помощью «колокольчика».
Для рафинирования литейных алюминиевых сплавов (силуминов) широко применяют флюсы № 2 и 13. Их вводят в расплавы в жидком виде в количестве 0,5-1,5 % (по массе) и энергично замешивают. Они способствуют разрушению пены, образующейся при наполнении раздаточных ковшей, и обогащают расплавы натрием.
Высокий уровень дегазации получают при вакуумировании Этот способ очистки применяют преимущественно в фасоннолитейных цехах. Сущность его состоит в том, что выплавленный по стандартной технологии в обычных печах металл переливают в ковш, который затем помещают в вакуумную камеру. Металл в камере выдерживают при остаточном давлении 1330 Па в течение 10-30 мин; температуру расплава при этом поддерживают в пределах 720-740 °С. В тех случаях, когда вакуумирование ведут без подогрева, расплав перед обработкой перегревают до 760-780 °С. Схема установки для вакуумной дегазации приведена на рис. 93.
В последние годы для очистки алюминиевых расплавов от неметаллических включений все в больших масштабах применяют фильтрование через сетчатые, зернистые и пористые керамические фильтры. Сетчатые фильтры широко используют для очистки расплавов от крупных включений и пленок Они отделяют те включения, размер которых больше ячейки сетки. Для изготовления сетчатых фильтров используют стеклоткань различных марок с размерами ячейки от 0,5х0,5 до 1,5х1,5 мм и металлические сетки (из титана). Фильтры из стеклоткани устанавливают в распределительных коробках и кристаллизаторах, в литниковых каналах и раздаточных тиглях (рис. 94), применение их позволяет в 1,5-2 раза снизить содержание крупных неметаллических включений и пленок; они не оказывают влияния на содержание дисперсных включений и водорода.
Значительно больший эффект очистки дают зернистые фильтры. Отличительная особенность их состоит в большой поверхности соприкосновения с металлом и наличии длинных тонких каналов переменного сечения. Очистка металлических расплавов от взвешенных включений при фильтровании через зернистые фильтры обусловлена механическими и адгезионными процессами. Первым из них принадлежит решающая роль при отделении крупных включений и пленок, вторым — при отделении тонкодисперсных включений. За счет сеточного эффекта зернистые фильтры задерживают лишь те включения, размер которых превышает эффективный диаметр межзеренных каналов. Чем меньше диаметр зерен фильтра и плотнее укладка их, тем выше достигаемый уровень очистки расплавов от крупных включений и пленок (рис. 95).
С увеличением толщины слоя фильтра эффективность очистки увеличивается. Фильтры, смачивающиеся расплавами, более эффективны, чем несмачивающиеся.
Фильтры из сплава фторидов кальция и магния позволяют получать отливки из сплавов АЛ4, АК6 и АМг6 в 1,5-3 раза менее загрязненными крупными включениями, чем фильтры из магнезита.
Существенное влияние на полноту отделения крупных включений и пленок оказывают скорость и режим течения расплава по межзеренным каналам фильтра. С увеличением скорости уменьшается возможность осаждения включении из движущегося потока под действием силы тяжести и увеличивается вероятность смыва уже осевших включений в результате гидродинамического воздействия, степень которого пропорциональна квадрату скорости фильтрования.
Эффективность очистки алюминиевых расплавов от тонкодисперсных включений зернистыми фильтрами возрастает по мере ухудшения смачивания фильтра и включений расплавом.
Для изготовления фильтров используют шамот, магнезит, алунд, кремнезем, сплавы хлористых и фтористых солей и другие материалы. Полнота удаления взвешенных неметаллических включений зависит от природы материала фильтра. Наиболее эффективны фильтры, изготовленные из фторидов (активных материалов) (рис. 95 и 96).
Активные материалы наряду с крупными включениями и пленками позволяют отделить до 30 40 % тонкодисперсных взвесей и на 10-20 % снизить содержание водорода в сплавах, прошедших рафинирование флюсом или хлоридами. По мере удаления тонкодисперсных взвесей увеличивается размер зерна в отливках» снижается газосодержание, растут пластические свойства сплавов (рис. 97), Высокий уровень очистки сплавов АК6 и АЛ4 от включений и водорода наблюдается при использовании фильтров из сплава фторидов кальция и магния с размером зерен 4-6 мм в поперечнике и высотой фильтрующего слоя 100-120 мм.
Зернистые фильтры, так же как и сетчатые, устанавливают на пути перемещения металла из миксера в форму. При непрерывном литье слитков оптимальным местом установки является кристаллизатор; при фасонном литье фильтр располагают в стояке, раздаточном тигле или литниковой чаше.
Типовые схемы расположения зернистых фильтров при литье фасонных отливок и слитков приведены на рис. 98.
Перед использованием фильтр нагревают до 700-720 °C для удаления адсорбированной влаги и предотвращения замораживания металла в каналах.
Заливку ведут таким образом, чтобы верхний уровень фильтра был покрыт слоем металла в 10-15 мм, а истечение металла после фильтра происходило под затопленный уровень. При соблюдении этих условий остаточное содержание неметаллических включений и пленок в отливке может быть доведено до 0,02-0,08 мм2/см2 по технологической пробе В.И. Добаткина и В.К. Зиновьева, т. е. в 2-4 раза снижено по сравнению с фильтрованием через сетчатые фильтры.
Самый эффективный способ очистки алюминиевых расплавов от пленок и крупных неметаллических включений — электрофлюсовое рафинирование. Сущность этого процесса состоит в пропускании тонких струй расплава через слой жидкого флюса с одновременным наложением на металл и флюс поля постоянного или переменного тока, создающего более благоприятные условия для адсорбции включений флюсом в результате снижения межфазного натяжения на границе с металлом. С увеличением удельной поверхности и длительности контакта металла с флюсом эффективность очистки возрастает. Поэтому конструкции устройств для флюсового и электрофлюсового рафинирования предусматривают дробление струи (рис. 99).
Оптимальный режим электрофлюсового рафинирования предусматривает пропускание струи металла диаметром 5-7 мм, нагретого до 700-720 °С, через слой расплавленного флюса толщиной 20-150 мм с наложением поля постоянного тока силой 600—800 А и напряжением 6-12 В с катодной поляризацией металла. При расходе флюса (карналлитового с 10-15 % CaF2, MgF2 или K3AlF6 для сплавов Al — Mg и Al — Mg — Si и криолитового для других алюминиевых сплавов) 4-8 кг на 1 т расплава и тщательном удалении влаги из флюса и разливочных устройств, содержание крупных неметаллических включений в сплавах АК6, АМг6, В95 может быть снижено до 0,003-0,005 мм2/см2 по технологической пробе.
В отличие от зернистых фильтров электрофлюсовое рафинирование не оказывает влияния на макроструктуру сплавов, что указывает на меньшую эффективность его по очистке от дисперсных неметаллических включений.
Деформируемые и литейные сплавы подвергают рафинированию и от металлических примесей: натрия, магния, цинка и железа.
Удаление натрия из алюминия и алюминиевомагниевых деформируемых сплавов АМг2, АМг6 осуществляют продувкой расплавов хлором или парами хлоридов (C2Cl6, CCl4, TiCl4), фреона (CCl2F2) и фильтрованием через зернистые фильтры из AlF3 с размером зерна 4-6 мм. Использование этих методов позволяет довести остаточное содержание натрия в расплаве до 2/3*10в4 %. Вредное влияние натрия на технологические свойства сплава может быть подавлено введением в расплав присадок висмута, сурьмы, теллура или селена , образующих с натрием тугоплавкие интерметаллиды.
Вторичные алюминиевые сплавы в ряде случаев подвергают очистке от примесей магния, цинка и железа методами флюсования, вакуумной дистилляции и отстаивания с последующим фильтрованием. Удаление магния флюсом основано на реакции 2Na3AlF6 + 3Mg → 6NaF + 3MgF2 + 2A1. Поверхность расплава покрывают флюсом, состоящим из 50 % криолита и 50 % хлористого натрия. Затем сплав нагревают до 780-800 °C и интенсивно перемешивают вместе с флюсом в течение 10-15 мин. Продукты реакции, всплывшие на поверхность расплава, удаляют; при высоком содержании магния (1-2,5 %) процесс рафинирования повторяют несколько раз. При помощи криолита содержание магния в расплаве может быть снижено до 0,1 %. Рафинирование вторичных алюминиевых сплавов от магния можно успешно осуществлять флюсом, состоящим из 50 % Na2SiF6, 25 % NaCl и 25 % KCl. Для этих целей можно использовать кислородсодержащие флюсы, например хлорат калия (KClO3).
Очистку расплавов от магния и цинка производят в вакуум-дистилляционных печах при 950-1000°C. В результате такой обработки получают сплавы, содержащие 0,1-0,2 % Mr и 0,02-0,05 % Zn. Очистку расплавов от магния способом дистилляции производят в тех случаях, когда содержание его в сплаве велико и применение очистки флюсованием становится невыгодным.
Отстаиванием можно снизить содержание железа в алюминиевом сплаве до 1,7 %, т. е. почти до эвтектического содержания, согласно равновесной диаграмме состояния алюминий — железо. Дальнейшее снижение достигается совмещением процесса отстаивания с введением в сплав хрома, марганца или магния Присадка этих элементов сдвигает эвтектическую точку в сторону алюминия и способствует отделению избытка железа. При введении в расплав 1-1,5 % Mn содержание железа в нем может быть снижено до 0,7 %. Присадка магния в количестве 25-30 % позволяет довести содержание железа до 0,1-0,2 %. Процесс отделения интерметаллидов железа ускоряется при совмещении отстаивания с фильтрованием. Фильтрование осуществляют через нагретый до 700 °C базальтовый фильтр с применением вакуума. Рафинирование от железа при помощи магния применимо для сплавов, содержащих не более 1,0 % Si, При более высоком содержании кремния образуются силициды, сильно затрудняющие фильтрацию и выводящие из цикла значительное количество магния. Кроме того, сплав обедняется кремнием.
johnlc написал:
состав бы еще запостили
Не вопрос, плиз
Марка Основа Компоненты, примеси и присадки, % не более Стандарт, дополнения.
01311С Al осн. Cu 0,08-0,12. Mg 0,4-0,9. Si 0,3-0,6 Fe-0,08. Mn-0,03. Ni-0,01. Zn-0,03. Ti-0,02. Прочие примес. Каждой 0,02. .ТУ 1-2-15-77 Профили пресованные шифров по 125 и по 126 из алюминиевого сплава. Марки 01311С и АД31
01315с ТУ 1-9-1043-85 Листы из АМЦ плакированные силумином 01315 с двух сторон. Сплав 01315 поставляется по ТУ1-1-62-79
34А Al 67,5-64,5. Cu 27-29. Si 5,5-6,5. Температура плавления 525-535єС, Температура пайки-540єС. ПРИПОЙ Для пайки и лужения изделий из алюминия и его сплавов. Места пайки обладают повышенной механической прочностью.
34А Al осн. Cu 27,0-29,0. Si 5,5-6,5. примеси-0,8. Прутки припоя. ТУ1-92-46-76.
35А Al 72. Cu 28, Si 7. Начало плавления-525єС, Полное расплавление-537єС. ПРИПОЙ Для пайки и лужения изделий из алюминия и его сплавов. Места пайки обладают повышенной механической прочностью
101 (1901) Al осн. Mg 2,4-3,0. Mn 0,1-0,3. Zn 5,4-6,2. Ti-0,03-0,10. Cr 0,12-0,25. Zr 0,07-0,12. Be 0,0002-0,0050. Cu-0,2. Fe-0,3. Si-0,2. Прочие элементы сумма-0,1. ОСТ1-92014-90 Сплавы алюминиевые деформируемые.
102 (1903) Al осн. Mn 0,05-0,15. Mg 2,1-2,6. Zn 4,7-5,3. Ti 0,03-0,10. Cr 0,12-0,25. Zr 0,07-0,12. Be 0,0002-0,003. Cu-0,2. Fe-0,35. Si-0,25. Прочие элементы сумма-0,1. ОСТ1-92014-90 Сплавы алюминиевые деформируемые.
1010 (АД00) (1070А) Al≥99,70 Si-0,2. Fe-0,25. Cu-0,03. Mn-0,03. Mg-0,03. Zn-0,07. Ti-0,03. Прочие эл. каждый -0,03. АЛЮМИНИЙ И СПЛАВЫ ДЕФОРМИРУЕМЫЕ ГОСТ 4784-97. и ИСО 209-1.
1010Е (АД00Е) (EAl99,7) (1370) Al≥99,70 Si-0,10. Fe-0,25. Cu-0,02. Mn-0,01. Mg-0,02. Zn-0,04. Cr-0,01. B-0,02. V+Ti-0,02. Прочие элементы каждый -0,02.Сумма-0,10. АЛЮМИНИЙ И СПЛАВЫ ДЕФОРМИРУЕМЫЕ ГОСТ 4784-97. и ИСО 209-1.
1011 (АД0) (А199,5) (1050А) Al≥99,50 Si-0,25. Fe-0,40. Cu-0,05. Mn-0,05. Mg-0,05. Zn-0,07. Ti-0,05. Прочие эл. каждый -0,03. (Для листовых заготовок, подвергаемых дальнейшей формовке Ti-0,15) АЛЮМИНИЙ И СПЛАВЫ ДЕФОРМИРУЕМЫЕ ГОСТ 4784-97. и ИСО 209-1.
1011Е (АД0Е) (EAl99,5) (1350) Al≥99,50 Si-0,10. Fe-0,40. Cu-0,05. Mn-0,01. Zn-0,05. Cr-0,01. B-0,05. V+Ti-0,02. Прочие эл. каждый -0,03.∑-0,10. АЛЮМИНИЙ И СПЛАВЫ ДЕФОРМИРУЕМЫЕ ГОСТ 4784-97. и ИСО 209-1.
1013 (АД1) (Al99,3) Al≥99,30 Si-0,3. Fe-0,3. Cu-0,05. Mn-0,025. Mg-0,05. Zn-0,1. Ti-0,15. Прочие эл. каждый -0,05. АЛЮМИНИЙ И СПЛАВЫ ДЕФОРМИРУЕМЫЕ ГОСТ 4784-97. и ИСО 209-1.
1015 (АД) (Al99,0) (1200) Al≥99,0 Si+Fe-1,0. Cu-0,05. Mn-0,05. Zn-0,10. Ti-0,05. Прочие эл. каждый-0,05.Cумма-0,15. АЛЮМИНИЙ И СПЛАВЫ ДЕФОРМИРУЕМЫЕ ГОСТ 4784-97. и ИСО 209-1.
1050А (1011) (А199,5) (АД0) Al≥99,50 Si-0,25. Fe-0,40. Cu-0,05. Mn-0,05. Mg-0,05. Zn-0,07. Ti-0,05. Прочие эл. каждый -0,03. (Для листовых заготовок, подвергаемых дальнейшей формовке Ti-0,15) ИСО 209-1. и АЛЮМИНИЙ И СПЛАВЫ ДЕФОРМИРУЕМЫЕ ГОСТ 4784-97.
1060 (Аl99,6) Al≥99,60 Si-0,25. Fe-0,35. Cu-0,05. Mn-0,03. Mg-0,03. Zn-0,05. Ti-0,03. V-0,05. Прочие элементы каждый -0,03. ИСО 209-1. и АЛЮМИНИЙ И СПЛАВЫ ДЕФОРМИРУЕМЫЕ ГОСТ 4784-97.
1070А (1010) (АД00) Al≥99,70 Si-0,20. Fe-0,25. Cu-0,03. Mn-0,03. Mg-0,03. Zn-0,07. Ti-0,03. Прочие эл. каждый -0,03. ИСО 209-1. и АЛЮМИНИЙ И СПЛАВЫ ДЕФОРМИРУЕМЫЕ ГОСТ 4784-97.
1080А (Аl99,8) (АД000) Al≥99,80 Si-0,15. Fe-0,15. Cu-0,03. Mn-0,02. Mg-0,02. Zn-0,06. Ti-0,02. Прочие эл. каждый-0,02. ИСО 209-1. и АЛЮМИНИЙ И СПЛАВЫ ДЕФОРМИРУЕМЫЕ ГОСТ 4784-97.
1105 Al ост. Cu 2,0-5,0. Mn 0,3-1,0. Mg 0,4-2,0. Si-3,0. Fe-1,5. Zn-1,0. Ni-0,2.Ti+Cr+Zr-0,2. Пр. эл. каждый -0,05. Cумма-0,2. АЛЮМИНИЙ И СПЛАВЫ ДЕФОРМИРУЕМЫЕ ГОСТ 4784-97.
1110 (Д1) (AlCu4MgSi) (2017) Al ост. Si 0,20-0,8. Cu 3,5-4,5. Mn 0,40-1,0. Mg 0,40-0,8. Fe-0,7. Сr-0,10. Zn 0,25. Ti-0,15. Ti+Zr-0,20. Прочие элементы каждый-0,05. Cумма-0,15. АЛЮМИНИЙ И СПЛАВЫ ДЕФОРМИРУЕМЫЕ ГОСТ 4784-97. и ИСО 209-1.
1117 (Д1П) Al ост. . Cu 3,8-4,5. Mn 0,4-0,8. Mg 0,4-0,8. Si-0,5. Fe-0,5. Zn 0,1. Ti-0,1. Прочие элементы каждый -0,05. Cумма-0,1. АЛЮМИНИЙ И СПЛАВЫ ДЕФОРМИ-РУЕМЫЕ ГОСТ 4784-97. Для изготовления проволоки для холодной высадки.
1140 (АК4). Al ост. Si 0,5-1,2. Fe 0,8-1,3. Cu 1,9-2,5. Mg 1,4-1,8. Zn-0,3. Mn 0,2. Ti-0,1. Ni 0,8-1,3. Прочие эл. каждый -0,05. Cумма-0,1. АЛЮМИНИЙ И СПЛАВЫ ДЕФОРМИ-РУЕМЫЕ ГОСТ 4784-97.
1141 (АК4-1) Al ост. Fe 0,8-1,4. Cu 1,9-2,7. Mg 1,2-1,8. Ti 0,02-0,10. Ni 0,8-1,4. Si-0,35. Mn 0,2. Cr-0,1. Zn-0,3. Пр. эл. каж.-0,05. Cумма-0,1. АЛЮМИНИЙ И СПЛАВЫ ДЕФОРМИ-РУЕМЫЕ ГОСТ 4784-97.
1160 (Д16) (AlCuMg1) (2024). Al ост. Cu 3,8-4,9. Mn 0,30-0,9. Mg 1,2-1,8. Si 0,50. Fe-0,50. Сr-0,10. Zn 0,25. Ti-0,15. Ti+Zr-0,20. Прочие эл. каждый -0,05. Cумма-0,15. АЛЮМИНИЙ И СПЛАВЫ ДЕФОРМИРУЕМЫЕ ГОСТ 4784-97. и ИСО 209-1.
1163 хим.состав по ОСТ1-90048-90 Fe-0,12. Н2-0,25см2/100г. мет. ОСТ1.90369-86 Профили прессованные из алюминиевых сплавов марок Д16Ч и 1163
ОСТ1-90048-90 Сплавы алюминиевые деформируемые хим.сост.
1165 (В65) Al ост. Cu 3,9-4,5. Mn 0,3-0,5. Mg 0,15-0,30. Si 0,25. Fe-0,2. Zn-0,1. Ti-0,1. Прочие эл. каждый -0,05. Cумма-0,1. АЛЮМИНИЙ И СПЛАВЫ ДЕФОРМИРУЕМЫЕ ГОСТ 4784-97.
1167 (Д16П) Al ост. Cu 3,8-4,5. Mn 0,3-0,7. Mg 1,2-1,6. Si-0,5. Fe-0,5. Zn-0,1.Ti-0,1. Прочие элементы каждый -0,05. ∑-0,1. АЛЮМИНИЙ И СПЛАВЫ ДЕФОРМИРУЕМЫЕ ГОСТ 4784-97. Для изготовления проволоки для холодной высадки.
1177 Al ост. Cu 4,7-5,6. Mg 3,2-4,1. Mn 0,32-0,5. Ti 0,08-0,15. Fe 0,16-0,28. Be 0,0008-0,003. Si-0,07. Zn-0,1. Прочих примесей: каждой-0,05. сумм-0,1. Mg=0,4ХCu+1,64 ТУ 1-9-1031-83 Проволока сварочная из алюминиевого сплава марки 1177
1180 (Д18) (AlCu2,5Mg) (2117) Al ост. Cu 2,2-3,0. Mg 0,20-0,50. Si-0,8. Fe-0,7. Mn 0,2. Cr-0,10. Zn-0,25. Прочие эл. каждый -0,05. Cумма-0,15. АЛЮМИНИЙ И СПЛАВЫ ДЕФОРМИРУЕМЫЕ ГОСТ 4784-97. и ИСО 209-1.
1190 (Д19) Al ост. Cu 3,8-4,3. Mn 0,5-1,0. Mg 1,7-2,3. Si-0,5. Fe-0,5. Zn-0,1.Ti-0,1. Ве 0,0002-0,005. Прочие элементы каждый -0,05. Cумма-0,1. АЛЮМИНИЙ И СПЛАВЫ ДЕФОРМИРУЕМЫЕ ГОСТ 4784-97.
- (Д24) (ВАД1) .ОСТ1-90048-90 Сплавы алюминиевые деформируемые. (хим. сост)
1197 (Д19П) Al ост. Ве 0,0002-0,005. Mn 0,5-0,8. Mg 2,1-2,6. Si-0,3. Fe-0,3. Cu 3,2-3,7. Zn-0,1. Ti-0,1. Прочие элементы каждый -0,05.∑-0,1. АЛЮМИНИЙ И СПЛАВЫ ДЕФОРМИРУЕМЫЕ ГОСТ 4784-97. Для изготовления проволоки для холодной высадки.
1200 (Al99,0) (1015) (АД) Al≥99,0 Si+Fe-1,0. Cu-0,05. Mn-0,05. Zn-0,10. Ti-0,05. Прочие элементы каждый -0,05. Cумма-0,15.
ИСО 209-1. и АЛЮМИНИЙ И СПЛАВЫ ДЕФОРМИРУЕМЫЕ ГОСТ 4784-97.
1201 (AlCu6Mn) (2219) Al ост. Cu 5,8-6,8. Mn 0,20-0,40. Ti 0,02-0,10. V 0,05-0,15. Zr 0,10-0,25. Si-0,20. Fe-0,30. Mg-0,02. Zn-0,10. Прочие элементы каждый -0,05. Cумма-0,15. АЛЮМИНИЙ И СПЛАВЫ ДЕФОРМИРУЕМЫЕ ГОСТ 4784-97. и ИСО 209-1.
1230пч (ВАД23пч) Al осн. Cu 4,8-5,8. Mn 0,4-0,8. Li 0,9-1,4. Ti 0,03-0,15. Cd 0,1-0,25. Fe-0,15. Si-0,1 Zn-0,1. Mg-0,03. Прочие примесей: каждая-0,05. сумм-0,1. ОСТ1-90026-80 Сплавы алюминиевые деформируемые повышенной чистоты.
1305 Al ост. Si 9,7-10,7. Cu3,3-4,7. Fe-0,5. Mn-0,5. Zn-0,08. Ti-0,15. Ca-0,10. Прочие примесей: каждой-0,05. сумм-0,1. ТУ 1-9-422-75 Листы АД33 плакированные силумином спецхимсостава (СПЛ. 1305)
1310 (АД31), (AlMg0,7Si) (6063) Al ост. Si 0,20-0,6. Mg 0,45-0,9. Fe-0,35. Cu-0,10. Mn-0,10. Cr-0,10. Zn-0,10. Ti 0,10. Прочие элементы каждый -0,05. Cумма-0,15. АЛЮМИНИЙ И СПЛАВЫ ДЕФОРМИРУЕМЫЕ ГОСТ 4784-97. и ИСО 209-1.
1310Е (АД31Е), (E-AlMgSi) (6101) Al ост. Si 0,30-0,7. Mg 0,35-0,8. Fe-0,50. Cu-0,10. Mn-0,03. Cr-0,03. Zn-0,10. В 0,06. Прочие элементы каждый -0,03. Cумма-0,10. АЛЮМИНИЙ И СПЛАВЫ ДЕФОРМИРУЕМЫЕ ГОСТ 4784-97. и ИСО 209-1.
1310Е (АД31Е) Al осн. Si 0,45-0,90. Mg 0,45-0,9. Fe 0,10-0,60. Cu-0,10. Mn-0,03. Zn-0,10. Ni-0,05. Ti 0,03. Cr-0,03. В 0,08. Ti+Mn+W+Cr-0,03. Прочие примеси: каждый -0,01. Cумма-0,10. ОСТ1-92014-90 Сплавы алюминиевые деформируемые.
1320 Al осн. Cu 0,05-0,15. Mg 0,45-0,75. Ti 0,01-0,05. Mn 0,05-0,15. Si 0,4-0,65. Be 0,001-0,005. Zn-0,05. Fe-0,15. Ni-0,03. Cr-0,03. Zr-0,03. ∑ прочих примесей-0,1 ОСТ1-92014-90 Сплавы алюминиевые деформируемые.
1330 (АД33), (AlMgSiCu), (6061) Al ост. Si 0,40-0,8. Cu 0,15-0,40. Mg 0,8-1,2. Cr 0,04-0,35. Fe-0,70. Mn-0,15. Zn-0,25. Ti 0,15. Прочие элементы каждый -0,05. ∑-0,15. АЛЮМИНИЙ И СПЛАВЫ ДЕФОРМИРУЕМЫЕ ГОСТ 4784-97. и ИСО 209-1.
1340 (АВ) Al ост. Si 0,50-1,2. Cu 0,1-0,5. Mn 0,15-0,35. Mg 0,45-0,90. Fe-0,5. Cr-0,25. Zn-0,2. Ti 0,15. Прочие элементы каждый -0,05. ∑-0,1. АЛЮМИНИЙ И СПЛАВЫ ДЕФОРМИРУЕМЫЕ ГОСТ 4784-97.
1350 (АД35), (AkSi1MgMn) (6082) Al ост. Si 0,70-1,3. Mn 0,40-1,0. Mg 0,6-1,2. Fe-0,50. Cu-0,10. Cr-0,25. Zn-0,20. Ti 0,10. Прочие элементы каждый -0,05. Cумма-0,15. АЛЮМИНИЙ И СПЛАВЫ ДЕФОРМИРУЕМЫЕ ГОСТ 4784-97. и ИСО 209-1.
1350 (EAl99,5) (АД0Е) (1011Е) Al 99,50 Si-0,10. Fe-0,40. Cu-0,05. Mn-0,01. Zn-0,05. Cr-0,01. B-0,05. V+Ti-0,02. Прочие элементы каждый -0,03.Cумма-0,10. ИСО 209-1. и АЛЮМИНИЙ И СПЛАВЫ ДЕФОРМИРУЕМЫЕ ГОСТ 4784-97.
1360 (АК6) Al ост. Si 0,7-1,2. Cu 1,8-2,6. Mn 0,4-0,8. Mg 0,04-0,8. Fe-0,7. Zn-0,3. Ti-0,1. Ni-0,1. Прочие элементы каждый -0,05. Cумма-0,1. АЛЮМИНИЙ И СПЛАВЫ ДЕФОРМИРУЕМЫЕ ГОСТ 4784-97.
1370 (АД00Е), (EAl99,7), (1010Е) Al≥99,70 Si-0,10. Fe-0,25. Cu-0,02. Mn-0,01. Mg-0,02. Zn-0,04. Cr-0,01. B-0,02.V+Ti-0,02. Прочие элементы каждый -0,02. Сумма-0,10. ИСО 209-1. и АЛЮМИНИЙ И СПЛАВЫ ДЕФОРМИРУЕМЫЕ ГОСТ 4784-97.
1380 (АК8) (AlCu4Mg) (2014) Al ост. Si 0,50-1,2. Cu 3,9-5,0. Mn 0,40-1,0. Mg 0,20-0,8. Fe-0,7. Zn-0,25. Ti-0,15. Cr-0,10. Ti+Zr-0,20. Прочие элементы каждый -0,05. Cумма.-0,15. АЛЮМИНИЙ И СПЛАВЫ ДЕФОРМИРУЕМЫЕ ГОСТ 4784-97. и ИСО 209-1.
1400 (АМц), (AlMn1Cu) (Al 3003) Al ост. Cu 0,05-0,20. Mn 1,0-1,5. Si-0,6. Fe-0,7. Zn-0,10. Прочие элементы каждый -0,05. Cумма-0,15. АЛЮМИНИЙ И СПЛАВЫ ДЕФОРМИРУЕМЫЕ ГОСТ 4784-97. и ИСО 209-1.
1401 (АМцС) Al ост. Si 0,15-0,35. Fe 0,25-0,45. Mn 1,0-1,4. Mg- 0,05. Cu-0,1. Zn-0,1. Ti-0,1. Прочие элементы каждый -0,05. Cумма-0,1. АЛЮМИНИЙ И СПЛАВЫ ДЕФОРМИРУЕМЫЕ ГОСТ 4784-97.
1403 (ММ), (AlMnMg0,5) (3005) Al ост. Mn 1,0-1,5. Mg 0,20-0,6. Si-0,6. Fe-0,7. Cu-0,30. Zn-0,25. Ti-0,10. Cr-0,10. Прочие элементы каждый -0,05. Cумма-0,15. АЛЮМИНИЙ И СПЛАВЫ ДЕФОРМИРУЕМЫЕ ГОСТ 4784-97. и ИСО 209-1.
1420 Al осн. Mg 4,5-6,0. Zr 0,08-0,15. Li 1,9-2,3 Si-0,15. Fe-0,2. Ti-0,1. Na-0,0006. Прочие элементы -0,15. каждый 0,05. ОСТ1 90048-77
1505 (АМг0,5) Al ост. Mg 0,4-0,8. Si-0,1. Fe-0,1. Cu-0,1. Mn-0,2. Прочие элементы каждый -0,05. Cумма-0,1. АЛЮМИНИЙ И СПЛАВЫ ДЕФОРМИРУЕМЫЕ ГОСТ 4784-97.
1510 (АМг1), (AlMg1) (5005) Al ост. Mg 0,50-1,1. Zn-0,25. Si-0,30. Fe-0,7. Cu-0,20. Mn-0,20. Сr-0,10. Прочие элементы каждый-0,05. Cумма-0,15. АЛЮМИНИЙ И СПЛАВЫ ДЕФОРМИРУЕМЫЕ ГОСТ 4784-97. и ИСО 209-1.
1520 (АМг2), (AlMg2) (5251) Al ост. Mn 0,10-0,50. Mg 1,7-2,4. Si-0,40. Fe-0,50. Cu-0,15. Zn-0,15. Сr-0,05. Ti-0,15. Прочие элементы каж.-0,05. Cумма-0,15. АЛЮМИНИЙ И СПЛАВЫ ДЕФОРМИРУЕМЫЕ ГОСТ 4784-97. и ИСО 209-1.
1521 (Д12) (AlMn1Mg1) (3004) Al ост. Mn 1,0-1,5. Mg 0,8-1,3. Zn-0,25. Si-0,30. Fe-0,7. Cu 0,25. Прочие элементы каждый -0,05. Cумма-0,15. АЛЮМИНИЙ И СПЛАВЫ ДЕФОРМИРУЕМЫЕ ГОСТ 4784-97. и ИСО 209-1.
1530 (АМг3) Al ост. Si 0,5-0,8. Mn 0,3-0,6. Mg 3,2-3,8. Fe-0,50. Cu-0,1. Zn-0,2. Cr-0,05. Ti-0,1. Прочие элементы каждый -0,05. Cумма-0,1. АЛЮМИНИЙ И СПЛАВЫ ДЕФОРМИРУЕМЫЕ ГОСТ 4784-97.
1540 (АМг4,0) (AlMg4), (5086) Al ост. Mn 0,20-0,7. Mg 3,5-4,5. Cr 0,05-0,25. Si-0,40. Fe-0,50. Cu-0,10. Ti-0,15. Zn-0,25. Прочие эл. каждый-0,05. Cумма-0,15. АЛЮМИНИЙ И СПЛАВЫ ДЕФОРМИРУЕМЫЕ ГОСТ 4784-97. и ИСО 209-1.
1541 Al осн. Mg 3,8-4,8. Mn 0,2-0,5. Fe 0,1-0,3. Ti 0,002-0,1. Si-0,2. Cu-0,05. Прочих примесей: каждой-0,05. сумма-0,1. ОСТ1-92014-90 Сплавы алюминиевые деформируемые.
1541 (В отожженном состоянии 1541м) Al осн. Mg 3,8-4,8. Mn 0,2-0,5. Fe 0,1-0,3. Ti 0,02-0,1. Be 0,0005-0,005. Si-0,2. Cu-0,05. Прочих примесей: каждой-0,05. сумма-0,1. ТУ 1-1-82-87 Листы и круги из алюминиевого сплава марки 1541 для основы магнитных дисков
1541пч Al осн. Mg 3,5-4,5. Cr 0,03-0,06. Cu-0,02. Mn-0,02. Zn-0,02. Fe-0,07. Si-0,07. Ti-0,05. Прочих примесей: каждой-0,02. сумма-0,1. ОСТ1-92014-90 Сплавы алюминиевые деформируемые.
1543 Al осн. Mg 3,8-5,0. Mn 0,2-0,5. Ti 0,02-0,1. Be 0,0002-0,005. Si-0,5. Fe-0,5. Cu-0,1. Zn-0,1. Прочих примесей: каждой-0,05. сумма-0,1. ОСТ1-92014-90 Сплавы алюминиевые деформируемые. .ТУ Ленты из алюминиевого сплава марки 15431-1-81-92
1550 (АМг5) Al ост. Mn 0,3-0,8. Mg 4,8-5,8. Ti 0,02-0,10. Be-0,0002-0,005 Si-0,5. Fe-0,5. Cu-0,1. Zn-0,2. Пр. эл. каждый -0,05. Cумма-0,1. АЛЮМИНИЙ И СПЛАВЫ ДЕФОРМИРУЕМЫЕ ГОСТ 4784-97.
5754 (AlMg3) Al ост. Mg 2,6-3,6. Mg+Cr 0,10-0,6. Si-0,40. Fe-0,40. Cu-0,10. Mn-0,50. Zn-0,20. Ti-0,15. Cr-0,30. Прочие эл. каждый -0,05. Cумма-0,15. ИСО 209-1. и АЛЮМИНИЙ И СПЛАВЫ ДЕФОРМИРУЕМЫЕ ГОСТ 4784-97.
1557 (АМг5П) Al ост. Mn 0,2-0,6. Mg 4,7-5,7. Si-0,4. Fe-0,4. Cu 0,2. Прочие элементы каждый -0,05. Cумма-0,1. АЛЮМИНИЙ И СПЛАВЫ ДЕФОРМИРУЕМЫЕ ГОСТ 4784-97. Для изготовления проволоки для холодной высадки.
1560 (АМг6) Al ост. Mn 0,5-0,8. Mg-5,8-6,8. Ti 0,02-0,10. Be 0,0002-0,005. Si-0,4. Fe-0,4. Cu-0,1. Zn-0,2. Прочие элементы каждый -0,05. Cумма-0,1. АЛЮМИНИЙ И СПЛАВЫ ДЕФОРМИРУЕМЫЕ ГОСТ 4784-97.
1561 (АМг61) Al осн. Mn 0,7-1,1. Mg 5,5-6,5. Be 0,0001-0,003. Zr 0,2-0,12 Si-0,4. Fe-0,4. Cu-0,1. Zn-0,2. Прочие элементы каждый -0,05. Cумма-0,1. ОСТ1-92014-90 Сплавы алюминиевые деформируемые.
1561Н Al осн. Mg 5,5-6,5. Mn 0,5-0,8. Zr 0,10-0,17. Be 0,0001-0,003. Fe-0,4. Si-0,4. Cu-0,15. Zn-0,2 ОСТ1-92073-82 Листы из алюминиевых сплавов для судостроения.
1901 (101) Al осн. Mg 2,4-3,0. Mn 0,1-0,3. Zn 5,4-6,2. Ti-0,03-0,10. Cr 0,12-0,25. Zr 0,07-0,12. Be 0,0002-0,0050. Cu-0,2. Fe-0,3. Si-0,2. Прочие элементы сумма-0,1. ОСТ1-92014-90 Сплавы алюминиевые деформируемые.
1903 (102) Al осн. Mn 0,05-0,15. Mg 2,1-2,6. Zn 4,7-5,3. Ti 0,03-0,10. Cr 0,12-0,25. Zr 0,07-0,12. Be 0,0002-0,003. Cu-0,2. Fe-0,35. Si-0,25. ОСТ1-92014-90 Сплавы алюминиевые деформируемые.
1905 Al осн. Cu 1,0-3,0. Mn 0,2-1,0. Mg 0,6-3,0. Zn 0,8-4,0.
Si-1,5. Fe-1,5. Ni-0,2. Cr-0,25. Ti+Zr-0,2. Прочие элементы: каждый -0,05. Cумма-0,2. ОСТ1-92014-90 Сплавы алюминиевые деформируемые.
1911 Al осн. Cu 0,1-0,2. Mn 0,2-0,5. Mg 1,6-2,1. Zn 3,8-4,4. Cr 0,07-0,25. Zr 0,13-0,22 Fe-0,3. Si-0,2. Прочие элементы: каждый -0,05. Cумма-0,1. ОСТ1-92014-90 Сплавы алюминиевые деформируемые.
1915, (AlZn4,5 Mg1,5Mn) (7005) Al ост. Mn 0,20-0,7. Mg 1,0-1,8. Cr 0,06-0,20. Zn 4,0-5,0. Ti 0,01-0,06. Zr 0,08-0,20. Si 0,35. Fe-0,40. Cu-0,10. Прочие элементы каждый -0,05. Cумма-0,15.
АЛЮМИНИЙ И СПЛАВЫ ДЕФОРМИРУЕМЫЕ ГОСТ 4784-97. и ИСО 209-1.
1920 (В92) Al осн. Mg 3,9-4,6. Mn 0,6-1,0. Zn 2,9-3,6. Be 0,0001-0,005. Cu-0,05. Fe-0,3. Si-0,2. Ti-0,2. Прочие примеси: каждая-0,05. сумма-0,1. ОСТ1-92014-90 Сплавы алюминиевые деформируемые.
1925, (AlZnMg1,5Mn) Al ост. Mn 0,2-0,7. Mg 1,3-1,8. Zn 3,4-4,0. Zr 0,1-0,2. Si 0,7. Fe-0,7. Cu-0,8. Ti 0,1. Cr-0,2. Прочие эл. каждый-0,05. Cумма-0,1. АЛЮМИНИЙ И СПЛАВЫ ДЕФОРМИРУЕМЫЕ ГОСТ 4784-97. и ИСО 209-1.
1930 (В93) Al осн. Cu 0,8-1,2. Mg 1,6-2,2. Zn 6,3-7,2. Fe 0,20-0,45. Si-0,3. Mn-0,1. Ti-0,1. Прочие примеси: каждая-0,05. сумма-0,1. ОСТ1-92014-90 Сплавы алюминиевые деформируемые.
1935 Al осн. Mg 0,6-1,1. Mn 0,2-0,5. Zn 3,6-4,1. Zr 0,15-0,22. Ce 0,0001-0,005. Cu-0,2. Fe-0,4. Si-0,3. Cr-0,2. Прочие примеси: каждая-0,05. сумма-0,2. ОСТ1-92014-90 Сплавы алюминиевые деформируемые.
1950 (В95) Al ост. Cu 1,4-2,0. Mn 0,2-0,6. Mg 1,8-2,8. Cr 0,10-0,25. Zn 5,0-7,0. Si-0,5. Fe-0,5. Ti-0,05. Ni-0,1. Прочие эл. каждый -0,05. Cумма-0,1. АЛЮМИНИЙ И СПЛАВЫ ДЕФОРМИРУЕМЫЕ ГОСТ 4784-97.
1953 Al осн. Cu 0,4-0,8. Mg 2,4-3,0. Mn 0,1-0,3. Zn 5,6-6,2. Ti 0,02-0,1. Cr-0,15-0,25. Fe-0,25. Si-0,2. Zr-0,1. Прочие примеси: каждый -0,05. Cумма-0,1. ОСТ1-92014-90 Сплавы алюминиевые деформируемые.
1955 Al осн. Cu 0,2-0,6. Mg 0,7-1,2. Zn 4,6-5,4. Cr-0,08-0,15. Zr 0,1-0,22. Ce 0,001-0,1. Mn-0,2. Fe-0,7. Si-0,3. Ni-0,1. Ti-0,1. Прочие примеси: каждый -0,05. Cумма-0,1. ОСТ1-92014-90 Сплавы алюминиевые деформируемые.
1957 (В95П) Al ост. Mn 0,3-0,5. Mg 2,0-2,6. Cr 0,1-0,25. Zn 5,5-6,5. Si-0,3. Fe-0,3. Cu 1,4-2,0. Прочие элементы каждый -0,05. Cумма-0,1. АЛЮМИНИЙ И СПЛАВЫ ДЕФОРМИРУЕМЫЕ ГОСТ 4784-97. Для изготовления проволоки для холодной высадки.
1960пч (В96Цпч) Al осн. Cu 2,0-2,6. Mg 2,3-3,0. Zn 8,0-9,0. Zr 0,1-0,2. Fe-0,15. Si-0,1. Mn-0,1. Cr-0,05. Прочие элементы каждый-0,05. Cумма-0,1. ОСТ1-90026-80 Сплавы алюминиевые деформируемые повышенной чистоты.
1980 (В48-4) .ТУ 1-4-007-77 Штамповки, поковки и трубные заготовки из сплава марки В48-4(1980) (без хим. состава). .ТУ 1-4-012-77 Трубы прессованные из сплава марки В48-4 (1980)
2014 (AlCu4Mg), (АК8)(1380) Al ост. Si 0,50-1,2. Cu 3,9-5,0. Mn 0,40-1,0. Mg 0,20-0,8. Fe-0,7. Zn-0,25. Ti-0,15. Cr-0,10. Ti+Zr-0,20. Прочие элементы каждый -0,05. Cумма.-0,15. ИСО 209-1. и АЛЮМИНИЙ И СПЛАВЫ ДЕФОРМИРУЕМЫЕ ГОСТ 4784-97.
2017 (AlCu4MgSi), (Д1) (1110) Al ост. Si 0,20-0,8. Cu 3,5-4,5. Mn 0,40-1,0. Mg 0,40-0,8. Fe-0,7. Сr-0,10. Zn 0,25. Ti-0,15. Ti+Zr-0,20. Прочие элементы каждый -0,05. Cумма-0,15. ИСО 209-1. и АЛЮМИНИЙ И СПЛАВЫ ДЕФОРМИРУЕМЫЕ ГОСТ 4784-97.
2024 (AlCuMg1) (Д16)(1160) Al ост. Cu 3,8-4,9. Mn 0,30-0,9. Mg 1,2-1,8. Si 0,50. Fe-0,50. Сr-0,10. Zn 0,25. Ti-0,15. Ti+Zr-0,20. Прочие элементы каждый-0,05. Cумма-0,15. ИСО 209-1. и АЛЮМИНИЙ И СПЛАВЫ ДЕФОРМИРУЕМЫЕ ГОСТ 4784-97.
2117 (AlCu2,5Mg) (Д18), (1180) Al ост. Cu 2,2-3,0. Mg 0,20-0,50. Si-0,8. Fe-0,7. Cr-0,10. Mn 0,2. Zn-0,25. Прочие элементы каждый -0,05. Cумма-0,15. ИСО 209-1. и АЛЮМИНИЙ И СПЛАВЫ ДЕФОРМИРУЕМЫЕ ГОСТ 4784-97.
2124 (Д16ч) Al ост. Cu 3,8-4,9. Mn 0,30-0,9. Mg 1,2-1,8. Si-0,20. Fe-0,30. Сr-0,10. Zn 0,25. Ti 0,15. Прочие элементы каждый -0,05. Cумма-0,15. ИСО 209-1. и АЛЮМИНИЙ И СПЛАВЫ ДЕФОРМИРУЕМЫЕ ГОСТ 4784-97.
2219 (AlCu6Mn) (1201) Al ост. Cu 5,8-6,8. Mn 0,20-0,40. Mg-0,02. Ti 0,02-0,10. Zr 0,10-0,25. V 0,05-0,15. Si-0,20. Fe-0,30. Zn-0,10. Прочие элементы каждый -0,05. Cумма-0,15. ИСО 209-1. и АЛЮМИНИЙ И СПЛАВЫ ДЕФОРМИРУЕМЫЕ ГОСТ 4784-97.
2618 (АК4-1ч) Al ост. Si 0,10-0,25. Fe 0,9-1,3. Cu 1,9-2,7. Mg 1,3-1,8. Ti 0,04-0,10. Ni 0,9-1,2. Zn-0,10. Пр. эл. каждый -0,05. ∑ -0,15. ИСО 209-1. и АЛЮМИНИЙ И СПЛАВЫ ДЕФОРМИРУЕМЫЕ ГОСТ 4784-97.
3003 (AlMn1Cu) (АМц)(1400) Al ост. Cu 0,05-0,20. Mn 1,0-1,5. Si-0,6. Fe-0,7. Zn-0,10. Прочие элементы каждый -0,05. Cумма-0,15. ИСО 209-1. и АЛЮМИНИЙ И СПЛАВЫ ДЕФОРМИРУЕМЫЕ ГОСТ 4784-97.
3004 (AlMn1Mg1) (1521), (Д12) Al ост. Mn 1,0-1,5. Mg 0,8-1,3. Si-0,30. Fe-0,7. Cu 0,25. Zn-0,25. Прочие элементы каждый -0,05. Cумма-0,15. ИСО 209-1. и АЛЮМИНИЙ И СПЛАВЫ ДЕФОРМИРУЕМЫЕ ГОСТ 4784-97.
3005 (AlMnMg0,5) (ММ), (1403) Al ост. Mn 1,0-1,5. Mg 0,20-0,6. Si-0,6. Fe-0,7. Cu-0,30. Zn-0,25. Ti-0,10. Cr-0,10. Прочие элементы каждый -0,05. Cумма-0,15. ИСО 209-1. и АЛЮМИНИЙ И СПЛАВЫ ДЕФОРМИРУЕМЫЕ ГОСТ 4784-97.
5005 (AlMg1), (1510), (АМг1) Al ост. Mg 0,50-1,1. Si-0,30. Fe-0,7. Cu-0,20. Mn-0,20. Zn-0,25. Сr-0,10. Прочие элементы каждый -0,05. Cумма-0,15. ИСО 209-1. и АЛЮМИНИЙ И СПЛАВЫ ДЕФОРМИРУЕМЫЕ ГОСТ 4784-97.
5050 (AlMg1,5), (АМг1,5) Al ост. Mg 1,1-1,8. Si-0,40. Fe-0,7. Cu-0,20. Mn 1,0. Cr-0,10. Zn-0,25. Прочие элементы каждый -0,05. Cумма-0,15. ИСО 209-1. и АЛЮМИНИЙ И СПЛАВЫ ДЕФОРМИРУЕМЫЕ ГОСТ 4784-97.
При плавке и разливке на воздухе алюминиевые сплавы легко окисляются и насыщаются водородом, причем вредное влияние растворенных газов на качество отливок заметно уже при небольших количествах их в расплаве. Практикой установлено, что предельно допустимое количество водорода в алюминиевых сплавах, позволяющее получать качественное литье, оценивается 0,1-0,20 см 3 /100 г металла. Поэтому основное внимание при плавке уделяют предупреждению излишнего окисления и газонасыщения сплава. Учитывая вредное влияние примесей в алюминиевых сплавах, стремятся также получить сплав с минимальными количествами этих примесей, особенно железа.
Способы плавки алюминиевых сплавов зависят от применяемого типа печей и шихтовых материалов. Тип плавильных печей выбирают в зависимости от характера производства и назначения сплава.
Плавку алюминиевых сплавов производят в тигельных печах с нефтяным, газовым и электрическим обогревом, в пламенных отражательных печах, подовых электропечах сопротивления и индукционных печах. По назначению различают печи плавильные, раздаточные и плавильно-раздаточные.
Наиболее качественный металл получается при плавке в индукционных печах. В этих печах плавка идет быстро, металл получается хорошо перемешанным и менее газонасыщенным. Отражательные печи, отапливаемые газом, применяют для плавки алюминиевых сплавов в цехах заготовительного литья, а также для переплавки отходов и стружки. В фасоннолитейных цехах распространены отражательные электропечи сопротивления.
Тигельные печи с различными способами нагрева применяют для плавки сравнительно небольших количеств металла (особенно они удобны как раздаточные печи).
Для плавки алюминиевых сплавов применяют преимущественно металлические сварные, литые, реже кованые тигли.
При плавке в металлических тиглях имеется опасность взаимодействия сплава с тиглем и загрязнение его примесями железа. Наиболее агрессивны по отношению к чугунным тиглям алюминиевые сплавы с кремнием, затем с магнием и менее с медью и цинком. Поэтому стенки тиглей перед плавкой покрывают специальными защитными красками, кроме того, подбирают составы чугуна или стали, более стойкие по отношению к алюминию. Например, серые чугуны более стойки, если в них больше графита и он находится в сильно разветвленной форме. Кремний в чугуне (как и кремний в расплаве) способствует взаимодействию металла с материалом тигля поэтому стремятся снижать содержание его в чугуне до нижнего предела, а в качестве графитизирующего элемента при выплавке используют алюминий (1,2-3,0%). Алюминий, кроме того, снижает окисляемость тигля и с наружной стороны. Содержание марганца должно быть минимальным. Высокую стойкость имеют тигли из чугуна с содержанием алюминия до 8% и с присадками хрома (0,4-1,0%), а также никеля и молибдена.
- При плавке на свежих шихтовых материалах и лигатурах в первую очередь загружают (целиком или по частям) алюминий, а затем растворяют лигатуры.
- Если плавка ведется на предварительном чушковом сплаве или на чушковом силумине, в первую очередь загружают и расплавляют чушковые сплавы, а затем подшихтовывают сплав необходимым количеством алюминия и лигатур.
- Сильно склонные к угару металлы, например цинк, магний, вводят в сплав в последнюю очередь, желательно под слой флюса.
- Если шихта состоит из отходов и чушковых металлов, очередность загрузки определяется количеством составных частей шихты: в первую очередь загружают в печь и расплавляют наибольшую часть шихты. Если, однако, отходы сильно загрязнены, то лучше их вначале расплавить, дегазировать и затем загружать чушковый металл.
- Если емкость печи и габариты шихты позволяют загружать различные ее составляющие одновременно, то вместе загружают то, что имеет близкую температуру плавления, например силумин, отходы, чушковый алюминий. Шихту подбирают с наименьшим количеством примесей для данного сплава. Укладку шихты в печь надо производить компактно, расплавление вести быстро. При загрузке в жидкую ванну твердую шихту необходимо предварительно подогревать.
Шихтовые материалы и возвраты необходимо хранить в сухих и теплых помещениях. Хранение их в сырых помещениях или же на открытом воздухе приводит к адсорбции влаги и усиленному окислению.
Шихту обычно составляют из отходов и 20-60% свежих материалов, тщательно взвешивают в соответствии с расчетными данными. Расчет шихты литейных алюминиевых сплавов проводят по данным ГОСТа (по среднему или оптимальному составу). В зависимости от особенностей сплавов и требований к свойствам отливки состав одних компонентов рассчитывают по минимальному количеству, других — по максимальному, а третьи компоненты рассчитывают по среднему количеству.
Например, при расчете шихты для приготовления слитков из алюминиевых сплавов АК4, АК5, АК6 и Д16 содержание меди в сплавах берут по верхнему пределу, что способствует снижению склонности сплавов к трещинообразованию, а содержание железа, магния и кремния принимают, наоборот, по нижнему пределу, для уменьшения ликвации.
Сплав АЛ4 имеет следующие пределы химического состава по ГОСТу: 8-10,5% Si, 0,25-0,5% Mn, 0,17-0,3% Mg, остальное Al. Обычно расчет ведут на содержание кремния 8,25-9,25%. Пониженное по сравнению со средним (9,25%) содержание кремния берут потому, что это способствует повышению прочности, уменьшению концентрированной усадки и ликвации сплава. Но чрезмерное понижение кремния вызывает уменьшение жидкотекучести и механических свойств, что особенно важно при литье тонкостенных деталей. Поэтому в таких случаях расчет ведут на содержание кремния 9,25%. Марганец вводят в сплав АЛ4 главным образом для устранения вредного влияния железа, но повышенное содержание марганца может вызвать сильную ликвацию. Поэтому если шихта сравнительно чистая по железу, то расчет ведут на среднее содержание марганца (0,37%), а если шихта сильно загрязненная, то количество марганца доводят до 0,45%, т. е. ближе к верхнему пределу. Особенно важно при составлении шихты сплава АЛ4 учитывать влияние магния на механические свойства этого сплава. При содержании магния на нижнем пределе сплав будет иметь пониженную прочность и твердость, но высокую пластичность.
Часто при выборе оптимального состава сплава приходится учитывать одновременно влияние на свойства сплава нескольких компонентов и затем выбирать наиболее удобные их сочетания. Например, сплав Д19 (3,8-4,3% Cu; 1,8-2,3% Mg) высокие жаропрочные свойства имеет в том случае, если суммарное количество меди и магния в сплаве будет равным 6,1%, что необходимо учитывать при расчете шихты. При плавке сплава АЛ19 (4,5-5,3% Cu, 0,6-1,0% Mn, 0,25-0,35% Ti,
Поэтому при плавке некоторых алюминиевых сплавов (особенно многокомпонентных) приходится иногда вначале готовить из чистых металлов подготовительный сплав определенного химического состава, разливать его в чушки, анализировать состав и потом уже при условии соответствия заданному составу использовать его в качестве исходной шихты для приготовления рабочего сплава, непосредственно идущего для заливки литейных форм.
Стандартные сплавы, технология плавки которых достаточно хорошо отработана, обычно готовят однократно из шихтовых материалов и сразу же заливают металл в формы.
Расплавление шихты ведут форсировано, но не рекомендуется чрезмерно перегревать расплав. Если шихта мелкогабаритная, та для предохранения от чрезмерного окисления плавку осуществляют с применением покровных флюсов из смеси хлористых солей, которые загружают вместе с металлической шихтой в количестве 2-3% от массы металла. По достижении необходимого перегрева металл контролируют по технологическим пробам на газонасыщенность и загрязненность окисными включениями и в случае необходимости приступают к рафинированию и дегазации сплава. На всем протяжении плавки, начиная с подготовки шихтовых материалов, необходимо не допускать излишнего окисления и газонасыщения расплава. Для этого надо тщательно готовить к плавке шихту и очищать ее от посторонних примесей, а также держать чистыми печь и весь инструмент. Чем больше внимания и времени уделяется подготовке шихты и печи, тем меньше окислов и газов окажется в расплаве и тем легче отрафинировать расплав перед разливкой. Небрежная плавка, в том случае, когда используют загрязненную, влажную шихту, не просушивают футеровку печи (в расчете на последующую очистку расплава в результате рафинирования и дегазации в конце плавки), не дает хороших результатов, так как зачастую легче предотвратить попадание в расплав окислов и газов, чем затем освободиться от них.
Практика плавки алюминиевых сплавов показывает, что существует прямая связь между количеством окисных пленок в расплаве и его газонасыщенностью. Чем больше в сплаве окисных пленок, тем выше газонасыщенность. Поэтому излишнего перемешивания расплава следует избегать, особенно если плавку ведут без покровных флюсов.
Алюминиевые и дюралевые отходы нетрудно расплавить буквально в домашних условиях. И для этого не нужно строить доменные печи, создавать тягу, как это принято в соответствии со стандартными условиями.
Автор метода плавления алюминия на газовой плите использует в качестве тигля половник из нержавейки. Температура плавления алюминия 660 градусов. Газовая плита не может обеспечить такого нагрева. Сначала, в течение 15-ти минут тигль с содержимым прогревается, затем включается газовая горелка, которая обеспечивает температуру, нужную для плавления алюминия. Готовые плавильные печи в этом магазине.
Внимание! Не используйте такой неустойчивый тигль, как на этом видео. Используйте обязательно вытяжку, оставляйте открытой форточку и не работайте дома с расплавленным алюминием часто.
Что можно сделать, используя подобные плавильные печи? Например, как в на нашем сайте, можно изготовить алюминиевую модель оружия. Для этого нужен пенопласт, песок и плавильня. Кстати, в статье есть также ссылка на аналог плавильни, которая представлена здесь.
Литье алюминия в домашних условиях: технология, фото и видео
Литье алюминия в домашних условиях является отличным хобби, которое поможет скоротать свободное время и может выручить в самый неожиданный момент. Существует несколько методик подобного литья, множество из которых применяется в промышленном производстве, но некоторые также подходят для домашнего применения.
Алюминий обрел большую популярность у домашних умельцев. Это связано с его эксплуатационными характеристиками, легким весом и простотой литья. С помощью литья можно легко и быстро изготовить различные детали, необходимые для бытовых нужд.
Литье алюминия в домашних условияхНаиболее распространенными способами являются: литье под давлением и литье с помощью форм. Первый способ требует особого оборудования, поэтому более популярным является второй. Это очень простая технология, которую можно применять в домашних условиях.
Характеристики алюминия
Алюминий – серебристо-серый металл, отличающейся пластичностью и легкостью, очень хорошо поддается штамповке и неплохо гнется. Температура плавления алюминия составляет около 660 градусов, а точка кипения 2500 градусов.
Этот металл отличается высокой степенью проводимости тепла. Ему характерно активное взаимодействие с кислородом, из-за чего на поверхности алюминия образуется оксидная пленка. Она отличается цветом и физическими характеристиками, защищает металл от полного окисления под воздействием агрессивной внешней среды. Имеет высокую температуру плавления, превышающую температуру алюминия, что влияет на конечный результат.
Этот металл имеет свойство изменения структуры после плавки. Резкое его охлаждения не желательно, так как оно может привести к усадке полученного изделия. Это свойство стоит учитывать про домашнем литье изделий из алюминия.
Технология
Технология литья деталей из алюминия в домашних условиях довольно проста, но требует тщательного выполнения требований и большого внимания к деталям. Наиболее простая технология заключается в заливке расплавленного алюминия в подготовленные формы. При этом необходимо иметь минимальный набор необходимого оборудования.
Главной задачей является расплавление воска или парафина внутри формы с заменой пустот алюминием, после чего остывшую деталь можно легко достать. Первое, что нужно сделать – это подготовить опалубку, в качестве которой можно взять любую картонную коробку, например, из-под обуви, или изготовить ее из фанеры. В нее заливается парафин или воск.
Парафиновая форма для литья
При работе с парафином следует учитывать некоторые особенности:
- Залитый в форму парафин очень быстро остывает, поэтому не следует ускорять этот процесс. Деталь должна остыть самостоятельно, это позволит сохранить однородную структуру. Для полного остывания нужно подождать около суток, после чего можно перейти к его обработке.
- Парафин может сильно просесть в центре заготовки, поэтому нужно учитывать этот факт при оценке необходимых габаритов заготовки.
Вырезать правильную форму из заготовки – очень трудная задача. Поэтому человек, не имеющий должного опыта, не сможет справиться с ней.
Чтобы не терять время, рекомендуется изготавливать сразу несколько заготовок, чтобы в случае неудачи можно было быстро залить новую форму.
Форму для заливки алюминия следует изготовить из оргстекла, который прочно скрепляется с помощью герметика. После этого на дне подготовленного «аквариума» располагается заготовка, которую нужно закрепить, чтобы она не сместилась в процессе заливки гипсом. Сделать это можно с помощью пластилина.
Затем следует подготовить гипсовую смесь, которая приготавливается с добавлением мелкозернистого песка (в соотношении один к одному). Это очень важно, так как чистый гипс содержит много влаги, которая испаряется при отливке детали и влияет на качество готового изделия.
Смесь должна быть однородной, густота должна напоминать сметану. Важно, чтобы смесь полностью покрывала парафиновую заготовку.
Стоит помнить, что гипс очень быстро застывает, поэтому выполнять работы нужно в быстром темпе. Полностью залив форму, ее стоит встряхнуть, чтобы избавиться от пузырьков воздуха.
После застывания гипса форму из оргстекла необходимо снять. Затем следует удаление парафина. Это можно сделать, положив форму вверх ногами на горячий лист железа, разогреваемого на огне. Также можно прокипятить форму в воде, что позволит более тщательно избавиться от парафина. После этого гипсовую форму нужно высушить.
Существует несколько способов расплавления алюминия, но технология литья в домашних условиях предусматривает самостоятельное изготовления тигельной печи или использование муфельной. Тигельная печь изготавливается только из огнеупорного кирпича.
Плавка алюминия в домашних условиях
После расплавления металла можно начинать процесс литья алюминия. С помощью ложки из нержавеющей стали следует снять окисную пленку. Плавление металла можно попробовать произвести с помощью газовой горелки, которой будет достаточно при небольшом объеме.
После застывания форма извлекается из гипса, очищается и полируется.
Технология может видоизменятся в зависимости от требований к готовому изделию и имеющихся инструментов. Методом проб и ошибок можно добиться оптимальной технологии.
Подготовка деталей
Домашнее литье требует особой подготовки, а также наличия определенных инструментов, среди которых нужно выделить:
- Лом алюминия. В качестве лома можно использовать множество изделий, в том числе проволоку. Но следует выбирать более мягкую, так как она содержит меньшее количество оксидов.
- Гипс. Формы для литья алюминия в домашних условиях лучше всего изготавливать из скульптурного гипса.
Но стоимость его довольно высока, поэтому вполне подойдет обычный белый гипс. Его легко найти в любом строительном магазине. Главное, не перепутать его с алебастром, который похож на белый гипс, но категорически не подходит для литья.
- Воск или парафин. Воск является оптимальным вариантом, но парафин дешевле и его проще найти. Можно использовать обычные свечи, избавившись от фитиля и расплавив их.
- Емкости для плавления. Для плавления парафина можно использовать обычную жестяную посуду, а вот для плавления алюминия рекомендуется применять тару из нержавейки или чугуна.
- Источник высокой температуры. Использовать можно как специализированные муфельные или тигельные печи, так и обычные газовые горелки. Выбор источника нагрева индивидуален, зависит от объема требуемого расплавленного металла.
Самодельный горн для плавки
Основные ошибки при литье алюминия
Многие новички при изготовлении алюминиевых отливок совершают банальные ошибки, поэтому перед выполнением работ рекомендуется с ними ознакомиться. Следует выделить такие базовые ошибки:
- Следует тщательно изготавливать гипсовую форму. Очень важно, чтобы из нее полностью испарилась вся влага. Если этого не произойдет, то во время заливки металла влага испарится, оставив поры и пустоты. Это значительно влияет на качество готового изделия.
- Недостаточный нагрев металла может привести к плохой заполняемости формы, из-за чего могут остаться незаполненные пустоты.
- Не нужно дополнительно остужать металл, процесс охлаждения должен происходить естественным путем.
Предупредив появление вышеуказанных ошибок, можно получить качественный результат.
Выплавка алюминия в домашних условиях
Алюминий используется в быту и промышленности на протяжении многих лет. Свойства материала позволяют создавать разнообразные изделия. Плавка алюминия может выполняться в домашних условиях, поскольку для этого не требуется высокая температура. Свойства металла нужно знать, чтобы правильно провести такую процедуру.
Характеристики
Чистота материалов определяет температуру их плавления. Алюминий пригоден для проведения разных технологических процедур, благодаря небольшому весу и хорошей пластичности. При высокой температуре происходит взаимодействие с кислородом. На поверхности металла возникает оксидная пленка, которая защищает его от коррозии и окисления. Плавление алюминия способствует изменению структуры вещества, поэтому защитное покрытие полезно для него. Усадка и дополнительное внутреннее напряжение появляется при резком охлаждении.
Особенности технологического процесса
Тигель — это тугоплавкая емкость для разогрева металла. Используются изделия из таких материалов:
В бытовых условиях применяется готовый тигель или емкость из широкой железной трубы. Чтобы изготовить ее, потребуется болгарка и сварочное оборудование. Объем тигля выбирается индивидуально, емкость прогревается равномерно, измельченный металл плавится в результате теплопередачи.
Перед термообработкой нужно уменьшить температуру плавления, чтобы состояние металла менялось быстрее. Для этого алюминий дробят на мелкие фрагменты. Воспламенение или окисление происходит часто после такого измельчения. Состояние образовавшегося оксида алюминия меняется при более высоких температурах. Это вещество удаляется вместе с другими шлаками после переплавки основного металла.
В процессе термообработки придется избегать попадания жидкости в тигель. Резкое испарение воды становится причиной взрыва. При погружении металла в емкость необходимо убедиться в том, что на нем отсутствует влага. Чаще всего плавят алюминиевую проволоку. Сначала материал делится на фрагменты ножницами, затем сдавливается пассатижами. Такой способ позволяет предотвратить воздействие кислорода на металл. Если нет необходимости в получении деталей высокого качества, измельчать сырье не нужно.
Технологию литья придется смоделировать самостоятельно при необходимости получить расплавленный алюминий в бытовых условиях. Материал предварительно очищается от грязи, примесей, шлаков. Крупные заготовки делятся на несколько малых фрагментов. Метод отливки требует соблюдения инструкции: для плавки металла используется самый удобный способ. Шлак удаляется с поверхности текучего вещества. Жидкий алюминий наливают в форму, которая разбивается после затвердевания.
Какой источник тепла использовать?
Для переплавки алюминия в бытовых условиях применяются:
- Муфельная печь, которую можно изготовить самостоятельно. Это эффективный метод, позволяющий быстро расплавить алюминий.
- Паяльная лампа может расплавить алюминий в малых количествах.
- Иногда используется газовый резак.
Из кирпичей сооружается очаг, каркас изготавливается из металлической емкости. Сбоку сверлится отверстие для подачи кислорода. К металлической трубке присоединяется пылесос, фен или другой прибор, нагнетающий воздух. После разведения огня тигель помещают в очаг.
Чтобы добиться лучшей термообработки, по бокам тоже выкладываются угли. Чтобы избежать потери тепла, можно соорудить крышку, оставить отверстия для выхода дыма. Если металл нужно расплавить один раз, нет необходимости оборудовать печь. Простая газовая плита поможет раскалить алюминий до нужной температуры. Небольшие куски металла плавятся примерно за полчаса.
Обычно жестяная банка применяется в качестве тигля. Чтобы добиться равномерного распределения температуры, емкость с алюминием помещают в другую банку таким образом, чтобы зазор между стенками равнялся 1 см. Чтобы обеспечить доступ пламени, нужно проделать в большой банке несколько отверстий по 3-4 см в диаметре. Рассекатель на конфорке удалять необязательно. Так можно добиться равномерного обогрева банки с металлом. Большую жестянку накрывают крышкой, чтобы тепло не выходило.
Как сделать форму для отливки
Создание простого материала для припоя не требует изготовления специальной формы. Можно вылить металл на стальной лист.
Для создания формы используются такие материалы:
- Гипс.
- Песок.
- Глина.
- Каменноугольный пепел.
- Жидкое стекло.
Сплав заливается в форму разными способами:
Открытый метод отличается простотой. Расплавленный металл переливается в обычную емкость, консервную банку, чашку и т. д. Когда вещество застывает, болванку извлекают из емкости. Если форма металлического предмета неважна, можно оставить алюминий на прочной поверхности.
Сложная отливка требует соответствия изделия указанным параметрам, для этого используются формировочные элементы. Кремнезем – это распространенное вещество, которое часто применяется при открытой заливке. Изделие состоит из двух емкостей, в которые засыпается и трамбуется земля. Элементы кремнезема сжимаются, между ними закладывается макет для отливки. Так можно получить точный отпечаток необходимой детали. Макет удаляется, в форму помещают раскаленный алюминий. Для закрытого способа отливки применяется речной песок, смешанный с жидким стеклом.
Гипс можно использовать для одноразового литья. Из парафина или пенопласта изготавливаются макеты. Применение таких материалов требует выполнения работ на открытом пространстве с хорошим доступом воздуха. Пенопласт не удаляется из твердого гипса, заливается раскаленным алюминием. Продукты горения этого вещества вредны для здоровья.
Распространенные ошибки и как их избежать
Гипсовые формы отличаются удобством и высокой чувствительностью к влаге. Простая сушка не позволяет удалить жидкость, поэтому качество отливки ухудшается. Придется ждать несколько дней, добиться полного высыхания гипсовой формы. Алюминий нужно держать на огне до самой заливки, чтобы успеть распределить его по всей форме.
Нежелательно использовать воду для охлаждения детали. Внутренняя структура вещества при этом нарушается, появляются трещины.
Меры безопасности
Требуется использование индивидуальной защиты при плавке алюминия. Руки, лицо, открытые участки тела должны быть защищены. Рекомендуется использовать перчатки сварщика, которые выдерживают температуру больше 600 градусов. Это главное средство защиты, поскольку шансы попадания жидкого алюминия на руки самые высокие. Очки и маска предотвращают попадание раскаленных элементов в глаза. Чтобы защититься полностью, можно проводить плавильные работы в костюме металлурга с высокой огнестойкостью. Химический респиратор применяется при очистке алюминия сварочным флюсом.
Плавка алюминия в бытовых условиях не представляет сложности. Металл разогревается в заранее подготовленной емкости. С поверхности жидкого вещества удаляются шлаки, затем чистый алюминий заливают в форму. Конструкция печи и температура определяют время плавки. При использовании газовой горелки тепло должно воздействовать на металл сверху.
Самым распространенным металлом на Земле является алюминий. Алюминиевые предметы неотъемлемая часть любого домашнего интерьера и, к сожалению, именно они чаще всего ломаются. Именно поэтому чаще всего могут понадобиться знания о том, как расплавить алюминий в домашних условиях. И хоть это и звучит устрашающе и кажется что это очень сложный процесс, это не так. Главное знать, как плавить алюминий в домашних условиях.
Какой алюминий использовать?
Прежде чем приступать к плавке стоит обратить внимание на характеристики данного металла. Температура плавления алюминия достаточно не высокая и составляет всего лишь 660 градусов по Цельсию. Тогда как чугун и сталь переходят в жидкое состояние при более высокой температуре. Поэтому плавить алюминий дома на газовой плите или горелке невозможно в виду недостаточного количества теплоты.
Чтобы снизить максимальную температуру, при которой алюминий плавится, достаточно будет перетереть его в порошок. Но тут стоит учитывать то, что алюминий плохо реагирует с воздухом и в процессе перетирания может запросто вызвать воспламенение или попросту окислиться. Также стоит следить за сухостью добавляемого сырья и избегать попадания воды.
Таким образом, стоит отметить, что сырье алюминия не используют для домашней плавки ввиду тяжелой с ним работы. Лучше всего для расплавки подойдут цельные алюминиевые изделия, это минимизирует его контакт с воздухом.
Как расплавить алюминий в домашних условиях и как не навредить себе?
Чтобы плавить алюминий следует знать следующее:
- Вам необходим тигель для плавки. Представляет собой сосуд из тугоплавкого материала с носиком. Собственно в нем и плавится алюминий. Изготовлен тигель может быть из чугунного, стального или графитового материала. Можно изготовить тигель в домашних условиях из стальной трубы, но это трудоемкий процесс для тех, кто умеет работать с болгаркой, паяльной лампой и т.д.;
- Печь для плавки. Она должна обеспечивать достаточную для плавления температуру, чтобы быстро перевести его в жидкое состояние именно поэтому для этих целей больше подойдет муфельная печь.
Можно также воспользоваться паяльной лампой или газовой горелкой. Правда в таком случае для более эффективного плавления стоит в дальнейшем поддерживать температуру под тигелем на костре;
- Литейная форма. Необходимый предмет если Вы хотите выплавить предмет даже самой незаурядной формы. По сути, она представляет из себя форму, состоящую из двух частей со слепком необходимого предмета внутри и отверстием для заливания внутрь алюминия. Ее можно изготовить дома, а можно купить уже готовую, подходит также для многоразового использования.
Если Вы решили расплавить алюминий с помощью газовой горелки или паяльной лампы Вам стоит запастись кирпичами, дровами, пассатижами и стальным прутом. Для начала нужно подготовить колодец из кирпичной кладки, затем в нем разжигается огонь, который должен прогореть до углей. Ставится сосуд с алюминием и нагревается в течение двадцати минут. После горелкой или паяльником нужно начинать прогревать алюминий вверху, помешивая при этом прутом. Завершающим этапом будет выливание алюминия на лист из стали, который предварительно уже должен быть раскаленным.
В итоге Вы получаете чистый алюминий без примесей, который идеально подойдет для пайки.
Если же Вы живете в квартире, и Вам ничего не остается, как плавить алюминий дома, то Вам придется долго греть смесь на конфорке без рассекателя. При этом нужно периодически сливать уже расплавленный и жидкий алюминий.
Когда стало понятно, как плавить алюминий, стоит напомнить о мерах предосторожности при работе с металлами плавления. Руки стоит защищать перчатками для сварки, очки для сварки идеально подойдут, чтобы защитить глаза. Если же Вы планируете работать с алюминием или другими металлами постоянно, то идеальной станет покупка специального металлургического костюма. В любом случае нужно обезопасить себя при работе с горячими металлами.
Не стоит пугаться плавки алюминия дома, если есть необходимость изготовления алюминиевой детали. Чтобы освоить литейное производство такого вида достаточно посмотреть простые обучающие видео курсы или фото производственного процесса.
«AnexMetall» — металлоприемка, оказывающая комплекс услуг по приему черного и цветного металлолома, лома кабеля, утилизации, демонтажу и прочее.
Алюминий – один из самых распространенных металлов на земле. Он присутствует даже в человеческом организме, так что уж говорить об окружающей действительности. В каждом доме или личном автомобиле есть алюминиевые функциональные элементы, детали или узлы, которые, увы, достаточно часто ломаются. Это мебельная и оконная фурнитура, направляющие для дверей и ставен, защелки замков и другие нужные мелочи.
Их можно заменить покупными новыми изделиями, отремонтировать или изготовить самостоятельно. В последних двух случаях и может понадобиться плавка алюминия в домашних условиях.
Характеристики алюминия
Все характеристики металла для домашних самоделок знать необязательно. Но есть несколько моментов, которые могут стать значительными или даже опасными в работе.
Алюминий хорошо поддается литью, плавится при относительно невысокой температуре в 660 °С. Для справки: чугун начинает плавиться при температуре 1100°С, а сталь – 1300 °С.
Поэтому плавка алюминия в домашних условиях на газовой плите трудно осуществима, так как домашние газовые приборы такую температуру обеспечить не могут. Правда, отечественные «кулибины» могут все, но об этом позже.
Снизить температуру плавления алюминия можно, растерев его в порошок или используя в качестве сырья готовый порошковый продукт. Но здесь важным становится еще одно свойство алюминия. Он достаточно активный металл, который при соединении с кислородом воздуха может воспламениться или просто окислиться. А температура плавления оксида алюминия — больше 2000 °С. При плавлении оксид все равно образуется, но в небольших количествах, именно он формирует окалину.
Та же активность может сыграть плохую шутку, если в расплавленный металл попадет вода. При этом происходит взрыв. Поэтому если в процессе плавки нужно сырье добавлять, то нужно следить, чтобы оно было сухим.
Сырье для плавки
Если предстоит плавка алюминия в домашних условиях, из-за сложности работы с порошковым металлом его в качестве сырья не используют.
Можно приобрести алюминиевую чушку или использовать обычную алюминиевую же проволоку, которую нарезать ножницами на небольшие кусочки и для уменьшения площади контакта с воздухом плотно спрессовать пассатижами.
Если не предполагается особо высокое качество изделия, то можно в качестве сырья использовать любые бытовые предметы, консервные банки без нижнего шва или обрезки профиля.
Вторичное сырье может быть окрашено или испачкано, это не страшно, лишние составляющие отойдут в виде шлаков. Только нужно помнить, что вдыхать пары сгоревшей краски нельзя.
Чтобы из вторичного сырья получилась качественная плавка алюминия в домашних условиях, флюсы, задача которых состоит в том, чтобы связывать и выводить на поверхность расплавленного металла все примеси и загрязнения, лучше приобрести готовые. Но можно сделать самостоятельно из технических солей.
Покровный флюс готовится из 10 % криолита и по 45 % хлорида натрия и хлорида калия.
В рафинирующий флюс для получения алюминия без пористости добавляют еще 25 % от общей массы фтористого натрия.
Средства индивидуальной защиты при плавке
Плавка алюминия в домашних условиях – процесс небезопасный. Поэтому нужно пользоваться средствами индивидуальной защиты (СИЗ). Даже если такая плавка нужна один раз на минимальном оборудовании, то по меньшей мере нужно защитить руки, например специальными перчатками сварщика, отлично предохраняющими от ожогов, ведь температура жидкого алюминия — больше 600 °С.
Глаза тоже желательно защищать, особенно если плавка происходит достаточно часто, очками или маской. И совсем в идеале работать нужно в специальном костюме металлурга с повышенной стойкостью к огню и высоким температурам.
Если нужен очень чистый алюминий с использованием рафинирующего флюса, то работать следует в химическом респираторе.
Литейная форма
Если требуется только отлить чистый алюминий для припоя, то литейная форма не нужна. Достаточно использовать стальной лист, на котором расплавленный металл остынет. Но если нужно отлить хотя бы простенькую деталь, то понадобится литейная форма.
Литейную форму можно сделать из скульптурного гипса, именно гипса, а не алебастра. Жидкий гипс заливается в смазанную маслом форму, ему дают немного застыть, периодически встряхивая, чтобы вышли пузырьки воздуха, вставляют в него модель и накрывают второй емкостью с гипсом. В удобном месте нужно в гипс вставить цилиндрический предмет, чтобы в итоге в форме появилось отверстие, так называемый канал, в который будет заливаться расплавленный алюминий. Когда гипс окончательно застынет, две части формы разъединяются, вынимается модель, и форма с готовым слепком соединяется опять.
Изготовить литейную форму можно и из смеси 75 % формовочного песка, 20 % глины и 5 % каменноугольного песка, которая засыпается в специальный ящик из досок и трамбуется. В утрамбованную землю отжимается модель, получившийся отпечаток присыпается тальком и графитом (угольной пылью), чтобы остывшую алюминиевую деталь можно было легко отделить от формы.
Тигель для плавки
Плавка алюминия в домашних условиях требует наличия специальной емкости с носиком из тугоплавкого материала. Это так называемый тигель. Тигли могут быть фарфоровые, кварцевые, стальные, чугунные, изготовленные из корунда или графита. В домашних условиях можно использовать покупной тигель или изготовить его, например, из отрезка стальной трубы достаточно большого диаметра. Правда, для этого нужна болгарка, сварочный аппарат и навыки владения этими инструментами.
Размеры тигля зависят от необходимого количества алюминия, который нужно расплавить. Этот ковш должен равномерно прогреваться, а его тепло — передаваться к сырью.
Печи для плавки
Технология плавки алюминия в домашних условиях достаточно проста. В специальном ковше нагревается лом алюминия до температуры, превышающей температуру плавления этого металла, расплав некоторое время выдерживается в разогретом состоянии, с его поверхности снимается шлак, затем чистый металл разливается в форму для остывания. Время плавки зависит от конструкции печи, то есть той температуры, которую она способна обеспечить.
Если используется паяльная лампа или газовая горелка, то они нагревают алюминий сверху. Правда, печь при этом все равно складывается из кирпичей колодцем без связующего раствора, внутри которого будут прогорать угли для нагревания емкости снизу и поддержания ее в нагретом состоянии.
Примерно так же выглядит конструкция печи, если тигель прогревается снизу с помощью обычных дров и фена для сушки волос. Только в этом случае дрова укладываются в кирпичном колодце не на дно, а на решетку, расположенную на первом ряду кирпичей, а в этом ряду оставляется отверстие для металлической трубы, надетой на горловину фена и закрепленной на ней изолентой. Тиглем в этом случае служит консервная банка, естественно, не алюминиевая, в которой на небольшом расстоянии от верха проделываются диаметрально противоположные сквозные отверстия. В эти отверстия продевается стальной прут, за который банка должна подвешиваться в печи. Фен нужен для нагнетания горячего воздуха в пространство между кирпичами и тиглем. Иногда вместо кирпичей используют металлическую бочку.
Если плавка должна происходить достаточно часто, то можно своими руками изготовить муфельную печь с вертикальной загрузкой тигля или купить готовую.
Плавка с помощью паяльной лампы
Плавка алюминия в домашних условиях паяльной лампой должна происходить не в помещении. Кроме сырья, паяльной лампы, тиглей и кирпичей, нужно подготовить дрова, пассатижи и стальной прут.
Итак, из кирпичей изготовлен небольшой колодец так, чтобы сверху можно было установить ковш с алюминием и стальной небольшой лист. В колодце разжигается костер, который должен немного прогореть, чтобы образовались угли. Дальше и происходит, собственно, плавка алюминия в домашних условиях. Пошаговая инструкция процесса:
— На кирпичи устанавливается емкость с сырьем. Ее нужно греть примерно 15 минут.
— После этого на полную мощность включается горелка паяльной лампы и алюминий прогревается сверху.
— В течение нескольких секунд начинается процесс, но для того чтобы прогрев был равномерным, металл в емкости нужно аккуратно перемешивать стальным прутом, придерживая ее пассатижами (не забыв при этом надеть рукавицы). Можно обойтись и без прута, периодически встряхивая ковш с помощью тех же плоскогубцев, но очень осторожно.
— Когда жидкость становится однородной, нужно пассатижами взять емкость и вылить содержимое на прокаленный стальной лист таким образом, чтобы вся образовавшаяся окалина осталась в ковше, а на лист для застывания попал только чистый металл.
Так обычно из вторичного сырья получают чистый алюминий, если с его помощью нужно запаять алюминиевые детали.
Плавка на дровах или газе
Плавка алюминия в домашних условиях на дровах происходит в легких разборных печах. Минусом такого способа является неконтролируемость процесса. Увеличить или уменьшить температуру нагрева невозможно. Вмешаться в процесс возможно, только сняв емкость с алюминием с огня.
Плавка алюминия в домашних условиях на газу — это единственно возможный вариант для квартиры. Греть емкость нужно долго, периодически сливая расплавленный металл. В таком случае отливка выполняется слоями. Для работы понадобятся две металлические емкости таких диаметров, чтобы одна надевалась на другую. Меньшая служит тиглем. Она с ломом, например нарезанной алюминиевой проволокой, ставится на конфорку, с которой нужно снять рассекатель пламени, бытовой газовой плиты. Над большей емкостью придется предварительно поработать. В ее днище выполняются около десятка небольших отверстий. В два или три из них вкручиваются болты, которые исполняют роль рукояток, за которые пассатижами раскаленную емкость можно поднять.
Эта емкость кверху дном надевается на тигель. Такая конструкция и позволяет прогревать алюминий. Периодически верхнюю емкость нужно снимать и металлическим прутом или ножом перемешивать лом. Перед тем как слить расплавленный металл, с его поверхности нужно снять шлак.
Плавка алюминия в муфельной печи
Муфельная печь – это уже достаточно серьезное оборудование для получения качественного расплавленного металла. Поэтому при плавке используют флюс для очистки алюминия от примесей. И это уже почти производственный процесс, а не плавка алюминия в домашних условиях. Пошаговая инструкция включает еще и несколько пунктов по подготовке сырья:
- Сначала в тигле расплавляется флюс, которого нужно взять в количестве от 2 до 5 % от веса алюминия, а затем в него добавляется лом.
- Насколько флюс активен, можно определить по поверхности расплава – она должна быть зеркальной. Если это не так, в расплав добавляется еще немного флюса, затем нужно будет добавить его перед окончанием плавки, чтобы шлак было легче удалять с поверхности металла стальной ложкой.
- Плавку нужно вести примерно при 700-750 °С. Это температура красного свечения.
- В процессе плавки может потребоваться добавлять сырье в тигель, так как расплавленный металл сильно уменьшается в объеме.
- Рафинирующий флюс добавляют при необходимости в конце плавки в количестве 0,25 % от веса расплавленного металла. Выдерживание такой пропорции в домашних условиях – задача непростая. После добавления флюса расплав нужно перемешать ложкой, дать постоять около 5 минут, затем снять шлак.
- Когда в результате нагрева алюминий превратился в однородную блестящую каплю, тигель нужно еще некоторое время подержать в печи, чтобы металл стал более текучим.
- Затем алюминий из тигля через носик (в этот момент становится понятно, зачем нужен именно такой ковш) заливается тонкой непрерывной струйкой в форму.
- После полного остывания форма аккуратно разделяется на половинки, из нее извлекается готовая деталь, которую еще нужно окончательно обработать: просверлить отверстия, если нужно, зачистить и наждачной бумагой отшлифовать поверхность. Вот и все. Процесс завершен.
Так что не стоит заранее пугаться, если предстоит в домашних условиях расплавить алюминиевый лом, чтобы получить чистый металл или изготовить деталь взамен поломавшейся. Серьезные профессиональные навыки для организации такого литейного производства совсем не нужны. Желание и умелые руки обычного мастера-любителя способны творить чудеса.
Как расплавить алюминиевые банки в домашних условиях
Алюминий — распространенный и полезный металл, известный своей коррозионной стойкостью, ковкостью и легкостью. Он достаточно безопасен для использования рядом с едой и при контакте с кожей. Этот металл намного проще переработать, чем очистить от руды. Вы можете расплавить старые алюминиевые банки, чтобы получить расплавленный алюминий. Вылейте металл в подходящую форму для изготовления украшений, посуды, украшений, скульптур или для другого проекта по обработке металла. Это отличное введение в домашнюю переработку.
Ключевые выводы: алюминиевые банки из расплава
- Алюминий — это распространенный и универсальный металл, который легко перерабатывается.
- Температура плавления алюминия достаточно низка, чтобы его можно было расплавить с помощью ручной горелки.
Однако проект реализуется быстрее при использовании печи или обжиговой печи.
- Из переработанного алюминия можно делать скульптуры, емкости и украшения.
Материалы для плавки алюминиевых банок
Плавление банок не сложно, но это проект только для взрослых, потому что здесь участвуют высокие температуры.Вам нужно работать в чистом, хорошо проветриваемом помещении. Банки не нужно чистить перед их плавлением, поскольку органические вещества (пластиковое покрытие, остатки соды и т. Д.) Сгорают во время процесса.
- Алюминиевые банки
- Небольшая печь электрической печи (или другой источник тепла, который достигает соответствующей температуры, например, пропановая горелка)
- Стальной тигель (или другой металл с температурой плавления намного выше, чем у алюминия, но ниже вашей печь (может быть прочная чаша из нержавеющей стали или чугунная сковорода)
- Термостойкие перчатки
- Металлические щипцы
- Формы, в которые вы будете заливать алюминий (сталь, железо и т.
д.)—Будь креативным)
Плавление алюминия
- Первый шаг, который вам нужно сделать, это раздавить банки, чтобы вы могли загрузить как можно больше в тигель. На каждые 40 банок вы получите около 1 фунта алюминия. Загрузите банки в контейнер, который вы используете в качестве тигля, и поместите тигель в печь. Закройте крышку.
- Разожгите печь или печь до 1220 ° F. Это точка плавления алюминия (660,32 ° C, 1220,58 ° F), но ниже точки плавления стали.При достижении этой температуры алюминий плавится почти сразу. Подождите полминуты или около того при этой температуре, чтобы алюминий расплавился.
- Наденьте защитные очки и термостойкие перчатки. При работе с очень горячими (или холодными) материалами вы должны носить рубашку с длинным рукавом, длинные брюки и обувь с закрытым носком.
- Откройте печь. Используйте щипцы, чтобы медленно и осторожно вынуть тигель. Не кладите руки в печь! Лучше всего выстелить путь от печи до формы металлической сковородой или фольгой, чтобы облегчить удаление разливов.
- Вылейте жидкий алюминий в форму. Чтобы алюминий затвердел сам по себе, потребуется около 15 минут. При желании через несколько минут можно поместить форму в ведро с холодной водой. В этом случае будьте осторожны, так как будет выделяться пар.
- В тигле могут быть остатки материала. Вы можете выбить мусор из тигля, ударив его вверх дном о твердую поверхность, например бетон. Вы можете использовать тот же процесс, чтобы выбить алюминий из форм.Если возникнут проблемы, измените температуру формы. Алюминий и форма (это другая мета) будут иметь другой коэффициент расширения, который вы можете использовать в своих интересах, отделяя один металл от другого.
- Не забудьте выключить печь или печь, когда закончите. Переработка не имеет большого смысла, если вы тратите энергию зря, верно?
Знаете ли вы?
Повторное плавление алюминия с целью его рециркуляции намного дешевле и требует меньше энергии, чем производство нового алюминия путем электролиза оксида алюминия (Al 2 O 3 ). При переработке используется около 5% энергии, необходимой для производства металла из сырой руды. Около 36% алюминия в США производится из переработанного металла. Бразилия лидирует в мире по переработке алюминия. В стране перерабатывается 98,2% алюминиевых банок.
Источники
- Моррис, Дж. (2005). «Сравнительные LCA для рециркуляции обочины по сравнению с захоронением или сжиганием с рекуперацией энергии». Международный журнал оценки жизненного цикла , 10 (4), 273–284.
- Оскамп С. (1995). «Ресурсосбережение и переработка: поведение и политика». Журнал социальных проблем . 51 (4): 157–177. DOI: 10.1111 / j.1540-4560.1995.tb01353.x
- Шлезингер, Марк (2006). Переработка алюминия . CRC Press. п. 248. ISBN 978-0-8493-9662-5.
Быстрый ответ: как расплавить металл дома?
Какой металл плавить легче всего?
— Quora.
Галлий — это металл, который плавится при взятии в руки и имеет температуру плавления около 29 градусов Цельсия.
Как плавить алюминиевую фольгу в домашних условиях?
Установите крышку на литейный цех и дайте ей нагреться.
- Дайте литейному цеху нагреться примерно 10 минут, прежде чем помещать в него алюминий.
- Температура в литейном цехе должна быть выше 1220 градусов по Фаренгейту (660 градусов по Цельсию).
- Когда тигель загорится оранжевым светом, литейный цех станет достаточно горячим, чтобы расплавить алюминий.
Как плавить сталь?
Если вы хотите расплавить металл, вам нужно найти способ приложить к нему много тепла.Это можно сделать с помощью литейного цеха или горелки. В литейном производстве металл можно превратить в жидкость, из которой затем придать любую форму. С помощью горелки вы можете расплавить металл и разрезать его на различные формы.18 ноя 2019
Между прочим, металлы превращаются в окалину независимо от того, плавятся они или нет. Цинк и олово имеют очень низкие температуры плавления металлов и легко плавятся в печи (или пламени горелки) .4 августа 2010 г.
На самом деле невозможно соединить металлы с помощью клея — во всяком случае, с помощью обычного клея.Но вы можете соединить их, сплавив их вместе в процессе, известном как сварка. Основная идея проста: вы применяете источник тепла, чтобы расплавить два металла, чтобы они сплавились и образовали надежное соединение. 22 марта 2019 г.
Алюминий — это распространенный и универсальный металл, который легко перерабатывается. Температура плавления алюминия достаточно низкая, поэтому его можно расплавить с помощью ручной горелки. Однако проект реализуется быстрее при использовании печи или обжиговой печи. Из переработанного алюминия можно делать скульптуры, емкости и украшения.29 авг 2019
Токсична ли расплавленная алюминиевая фольга?
Алюминиевая фольга не считается опасной, но она может незначительно увеличить содержание алюминия в вашем рационе. Если вас беспокоит количество алюминия в вашем рационе, вы можете прекратить готовить с использованием алюминиевой фольги. 27 апр 2017
Сколько алюминиевых банок нужно, чтобы приготовить фунт?
32 банки
Что происходит при плавлении алюминиевой фольги?
Температура плавления алюминиевой фольги составляет 660 градусов по Цельсию (1220 градусов по Фаренгейту) при стандартном давлении, поэтому она не плавится при температурах, встречающихся в стандартной домашней духовке.24 апр 2017
Можете ли вы использовать печь как кузницу?
Кузницы обычно работают на газе, а печи — на электричестве. Печи, если они не дорогие, скорее всего, не дойдут до температуры ковки. Вы можете использовать кузницу для термообработки, поскольку температура обычно ниже, чем при ковке. 5 Май 2008 г.
Сталь — это просто элементное железо, обработанное для контроля количества углерода. Железо, извлеченное из земли, плавится при температуре около 1510 ° C (2750 ° F). Сталь часто плавится при температуре около 1370 ° C (2500 ° F).
Можно ли расплавить серебро в печи?
Серебро плавится при 900 градусах, поэтому подойдет бисквит или глазурь, поскольку самая низкая температура, до которой я горю, составляет 1000 градусов по Цельсию. Я вижу много проблем, таких как возгорание, разрушение печи и т. Д., Но мне бы очень хотелось помочь.10 мая 2013 г.
Эпоксидный клей
Эпоксидные клеи образуют наиболее прочную связь металл-металл. Большинство эпоксидных продуктов требуют смешать равные части клея и отвердителя и нанести смешанный материал с помощью соответствующего инструмента на одну из склеиваемых поверхностей.
Насколько прочен JB Weld?
J-B Weld ™ имеет предел прочности на разрыв 5020 фунтов на квадратный дюйм и затвердевает в течение ночи. После полного отверждения он может выдерживать температуры до 550 ° F.
Проволока для припоя
Плавкий металлический сплав, используемый для соединения двух металлических поверхностей. Они бывают разных сплавов в зависимости от того, какой тип металлов вы пытаетесь паять. Будьте осторожны при использовании припоя, он может расколоться, и он будет горячим и болезненным при контакте с вашей кожей.
Как плавить алюминиевые банки для литья
Узнайте здесь, как плавить алюминиевые банки, и получите еще один бесценный навык выживания!
В этой статье:
- Создание собственных кузнечных инструментов своими руками
- Создайте собственное литейное производство
- Как превратить лом в маффины
- Как расплавить алюминиевые банки в домашних условиях на мини-литейном производстве
- Литье металла или как превратить металл в полезные инструменты
Кузнечное дело на заднем дворе: плавление алюминиевых банок
Кузнечное дело — важный навык выживанияКузнечное дело: полезные хобби и навыки выживания. Фото: Survival Life
.Когда SHTF, навыки выживания, которые у вас есть под рукой, становятся невероятно бесценными! Один из навыков, который, к сожалению, в последние годы отошел на второй план, — это кузнечное искусство.
Кузнечное дело — это навык выживания своими руками, который окажется более полезным, чем вы думали.
Умение плавить алюминий — действительно важный навык выживания. Это потому, что вы не можете быть уверены, что в неопределенном будущем кто-то другой сделает это за вас.
Вы должны уметь делать собственные материалы.
1. Изготовление собственных кузнечных инструментов своими руками
К сожалению, кузницы и печи будут пользоваться большим спросом, но не всегда в наличии.Затем у вас должна быть возможность создать свою собственную плавильную печь, чтобы начать производить необходимое сырье.
Таким образом, имея собственный тигель, вы создадите небольшую металлообрабатывающую промышленность на заднем дворе (или в бомбоубежище).
Выживание DIYТермин «сделай сам для выживания» можно легко неправильно понять, если понимать его буквально. Это просто означает способность делать большинство вещей самостоятельно.
При SHTF, электросеть может выйти из строя вместе с другими источниками энергии.Возможности безграничны и непредсказуемы.
Вы не сможете сделать это без надлежащих повседневных инструментов, так что научитесь делать это своими руками, чтобы выжить в долгосрочной перспективе.
Работайте с тем, что есть или с тем, что осталось, потому что это будет единственный выход. Вам придется переработать или перепрофилировать материалы для изготовления оружия, инструментов и даже посуды.
2. Создайте собственное литейное производство
Алюминиевые сплавы сложно производить самостоятельно, но наличие стопки слитков, сделанных из расплавленного алюминия, может предоставить вам большое количество сырья для изготовления инструментов.
К счастью, потратив немного времени, усилий и некоторых предметов домашнего обихода, вы сможете построить свой собственный! Прежде чем приступить к плавке, нужно произвести литейный цех.
В собственном литейном производстве вы можете плавить такие металлы, как алюминий, и использовать их в необходимых вам инструментах. У нас есть пошаговые инструкции, как построить мини-литейный цех и как плавить алюминий.
Теперь, когда вы знаете, как делать печи для плавления алюминия своими руками, у вас есть больше возможностей для творчества с инструментами.
Ознакомьтесь с видеоуроком ниже, чтобы узнать, как:
3. Как превратить лом в маффины
Как только вы построите этого плохого парня, вы сможете делать с ним все, что угодно! Посмотрите это короткое обучающее видео ниже, в котором показано, как превратить отходы в «кексы».
В основном маффины изготавливаются из расплавленного алюминия. Расплавив алюминиевые банки, вы можете превратить их во множество отличных вещей, которые пригодятся в целях выживания.
После того, как вы сделаете «кексы» в своей мини-литейной, используйте их, чтобы отлить инструменты для выживания или припасы. Конечно, при обращении с расплавленным металлом следует соблюдать осторожность.
СВЯЗАННЫЕ: Самодельные горелки для алюминиевых банок
4. Как расплавить алюминиевые банки в домашних условиях на мини-литейном производстве
Научиться плавить алюминий может спасти вашу жизнь, когда вам понадобится средство самообороны или что-то, чем можно торговать.
С таким количеством банок из-под соды, которые валяются повсюду в мусорных баках, вам не нужно смотреть очень далеко, чтобы начать таять.Это даже не ограничивается банками; можно использовать алюминиевую фольгу или любые изделия на основе алюминия.
Если вы хотите изготавливать алюминиевые сплавы, потребуется немного больше работы, но этот навык самодельного выживания стоит вашего времени. Плавка алюминия для производства сырья — хороший способ устроиться в условиях глобального кризиса.
Предупреждение: В этом литейном цехе температура может достигать более 1200 градусов по Фаренгейту! Убедитесь, что вы используете все необходимое защитное оборудование, прежде чем пытаться использовать литейный цех.
Навыки выживания, которые должен знать каждый, когда SHTF
377 Приемы и навыки выживания, которые вы должны знать Фото: Survival Life
Наш мир находится в одной катастрофе от того, чтобы превратиться в пустошь. Когда это произойдет, у вас нет выбора, кроме как жить так, как жили наши предки несколько веков назад.
Это означает изучение незнакомых навыков выживания, таких как плавление алюминия. Никогда не знаешь, когда тебе может понадобиться самодельное оружие для выживания или самодельные предметы для торговли.
Металлолом будет нелегко, и будет полезно иметь готовый запас банок из-под газировки. Так что копите, что можете, пока можете.
Впрочем, это должны быть не только банки из-под газировки и пива. Из фольги, алюминиевого порошка и т. П. Можно получить ценные слитки, которые можно использовать для изготовления дополнительных инструментов.
Наличие большого количества металлического лома и банок с расплавленной содой — хороший способ иметь под рукой сырье.
5. Отливка металла или как превратить металл в полезные инструменты
Литье металла само по себе является видом искусства, и формальное образование обязательно поможет вам.Конечно, нельзя просто положить вещи в духовку и ожидать, что они окажутся полезными.
Итак, попробуйте найти к себе класс металлистов. Если вы не можете найти его, на YouTube есть масса информации, готовой для вашего выбора.
Со временем вы можете даже стать постапокалиптическим Легатом Легионисом с собственной армией, оснащенной самодельными инструментами для выживания.
С помощью этого изделия можно также ковать металл в домашних условиях.
Узнайте, как плавить банки с газировкой, в этом видео из The King of Random:
Весь процесс плавления алюминия до литья кажется довольно сложным, но как только вы освоите его, навык останется с вами.На самом деле, многим людям нужно время, чтобы изучить этот навык только ради развлечения.
На данный момент плавление алюминиевых банок с целью получения прибыли имеет тенденцию, но когда SHTF, у них будет очень ценный навык, который они смогут использовать, чтобы выжить. Так что найдите время, чтобы изучить этот навык как для развлечения, так и для выживания!
Что вы думаете? Кузнечное дело на заднем дворе — это навык, которым вы владеете? Стоит ли добавлять в свой набор навыков выживания? Дайте нам знать в комментариях ниже!
Следующее: Как сделать самодельный фонарь для кемпинга
Если вы ищете потрясающее снаряжение для выживания, которое нельзя сделать дома, загляните в магазин Survival Life Store!
Подписывайтесь на нас в Facebook, Instagram, Twitte
Примечание редактора: он был впервые опубликован 16 апреля 2018 г. и был обновлен для обеспечения качества и актуальности.
Продолжить чтение сообщений в той же категории: Цинк — хороший металл для детского литья. Его легко купить у торговца металлоломом (по крайней мере, раньше) практически за бесценок. Он плавится при достаточно низкой температуре, чтобы его можно было растопить на плите, приложив усилие или пропановой горелкой. И он довольно нетоксичен, гораздо менее токсичен, чем свинец.(У меня есть специальная страница о безопасности цинка, на которой подробно рассматривается вопрос о том, представляет ли металлическое цинковое литье опасность для здоровья.) Возможно, олово — лучший металл для любительского литья, но он намного дороже и обычно недоступен в качестве металлолома, если только вы живете в большом городе, где торгуют экзотическим металлоломом. В любом случае, когда я рос, у меня никогда не было доступа к олову, но у меня было много цинка. Литье по выплавляемым моделям — столь же древняя технология, как и раньше. Первый шаг — сделать что-нибудь из воска.Подойдет любой вид, но учтите, что парафин — это не воск, и вы не можете обрабатывать его, кроме как вырезать его. Пчелиный воск лучше, и вы сможете купить его в магазинах для рукоделия (секция изготовления свечей). (Я приобрел свои запасы в аптеке в Цюрихе и отвез их в Америку в тканевом чемодане. Когда я поднял чемодан после полета, его внешняя сторона была покрыта толстым слоем жирно-воскообразного вещества, которое, конечно же, должно быть пусть мой воск расплавится, чтобы вызвать ужас при прохождении таможни.Оказалось, что мой воск был в порядке, это была просто какая-то самолетная слизь, попавшая на чемодан.) В любом случае, после того, как вы закончили восковой объект, вы прикрепляете конический стержень, также сделанный из воска, затем заливаете форму … сделайте смесь вокруг всего этого, оставив только конец воскового конуса торчащим. Есть много подходящих способов сделать это и много подходящих составов для форм. У меня, конечно, не было, поэтому лепил лепки из гипса. Он дешевый и его можно найти в любом строительном магазине (в разделе расходных материалов для гипсокартона). Я бы сделал картонную коробку примерно на 2-3 дюйма больше со всех сторон, чем восковой объект, и открыл бы ее сверху. Затем я капал горячий воск на дно и наклеивал на него верхнюю часть воскового конуса, оставляя объект стоять, как если бы он был восковым цветком на восковом стебле. Затем я вставлял длинные булавки или иглы через картон в восковой объект в нескольких местах (места, которые становились высокими точками внутри формы, когда она была повернута правой стороной вверх для литья). Штифты помогали удерживать восковой объект на месте, а при удалении отверстия предотвращали образование воздушных карманов при заливке металла. Я смешивал гипс до консистенции кашицы и заливал его в коробку. Через некоторое время я узнал, что очень важно избавляться от пузырьков воздуха. С тех пор я видел фильмы, показывающие специальные вибрационные машины, предназначенные именно для этого, но я делал это, встряхивая, а также протягивая руку и проводя пальцами по объекту, чтобы отряхнуть любые пузыри, которые могли прилипнуть к нему. После затвердевания штукатурки я снимал картон (который был весь мокрый), затем запекал форму на противне из алюминиевой фольги, чтобы удалить воск. На выпекание формы уходит очень и очень много времени, для большой — целый день. И я определенно научился не экономить на времени выпечки. Вы должны убедиться, что все воска и что из гипса была удалена вся остаточная вода. Если вы попробуете это, вы, вероятно, испортите несколько, прежде чем поверите мне в этом. Если форма не полностью обожжена, металл будет брызгать и пузыриться, когда вы ее заливаете, часто стреляя шариками из еще расплавленного металла. Единственный раз, когда я обжигался, работая с металлом (или порохом), был когда такая капля упала мне на руку.После этого я каждый раз надевала перчатки. И, конечно, это тоже портит форму. (Само собой разумеется, что вы, , должны носить защитные очки каждый раз, когда заливаете расплавленный металл в форму. Просто представьте, как было бы больно, если бы даже крошечный кусочек расплавленного металла впился вам в глазное яблоко.) Большинство металлы сжимаются при затвердевании, что приводит к образованию пустот в отливке. (Есть несколько способов избежать этого, но они включают вращение формы на высокой скорости в своего рода центрифуге.Это кажется мне опасным.) Я попытался свести к минимуму проблему, дав форме остыть после выпечки (но не в течение ночи, так как она снова впитает влагу), а затем зажег пропановую горелку над конусом расплавленного металла справа. после заливки. Моя теория заключалась в том, что это заставит металл затвердеть снизу вверх, втягивая при необходимости больше жидкости из конуса. Не уверен, что это имело большой эффект. Как только металл затвердел, я начинал поливать водой верхнюю часть формы, чтобы ускорить процесс охлаждения.Это было опасно, потому что, если бы оставался жидкий металл, он мог бы вызвать паровой взрыв. Но мне, конечно, не терпелось увидеть, что я сделал! Горячий обожженный гипс из Парижа удивительно пористый: вы можете вылить на него постоянную струю воды, и вода исчезнет еще до того, как она расплывется по поверхности, как если бы вы наливали ее прямо на твердый материал. Когда металл хорошо затвердел и вода переставала шипеть, я брал молоток и ударял по штукатурке, пока она не раскололась, обнажив металлический предмет внутри.Чтобы удалить всю штукатурку, потребовалось немного почистить отверткой и металлической щеткой. И, конечно же, мне всегда приходилось отрезать и подпиливать стержень наполнителя вместе с любыми неровностями, вызванными пузырьками, и маленькими усами из отверстий иглы. Я не говорю, что это лучший способ литья по выплавляемым моделям: это не так. Я так и сделал. Другие хорошие металлы для литья включают свинец, который очень легко расплавить и его легко достать в хозяйственных магазинах, но он достаточно токсичен, чтобы о нем беспокоиться, особенно если его подпилить или отшлифовать.Из-за возможности необратимого повреждения головного мозга дети никогда не должны использовать самоуправления. Дело не в том, что пары токсичны, а в том, что дети не должны тщательно мыть руки после прикосновения к свинцу или чему-либо, что с ним соприкасалось. Другими действительно хорошими металлами для литья являются олово и алюминий.У меня никогда не было достаточно дешевого олова, поэтому я не могу сказать вам никаких подробностей. Наверное, это очень похоже на свинец. Алюминий плавится выше цинка, олова и свинца, но не так высоко, как медь. Подойдет электрическая печь или пропановая горелка. Алюминий действительно легко получить, его можно достать из консервных банок, разбитых оконных рам, старых горшков и т. Д. Но вот слово от мудрых людей (Дэвида Рида, а не меня): вы получите гораздо лучшие результаты литья, если расплавите старые отлитые предметы, а не экструдированный алюминий.Литой алюминий содержит кремний, который значительно увеличивает способность расплавленного металла соответствовать деталям в форме. |
Обзор литья металлов для начинающих — плавка, плавка, литье и литье
Привет всем, решил, что сделаю свой первый пост чем-то полезным, а не вопросом. Я знаю о литье больше, чем кузнечное дело, поэтому решил, что помогу немного добавить в раздел литья, предоставив общий обзор того, как начать литье, справочники, необходимое оборудование, меры безопасности и т. Д.Надеюсь, это будет что-то, на что можно будет сослаться, чтобы дать какое-то направление людям, спрашивающим «как мне начать лить металл» или «могу ли я отлить свою собственную наковальню» и т. Д., Поскольку, похоже, таких сообщений довольно много. Я только что пролил бронзу и в итоге неоднократно объяснял процесс всем своим соседям по дому, где я живу и работаю, так что все это в любом случае было у меня в голове на этой неделе. Перед всей информацией я покажу несколько фотографий заливки, так как это всегда выглядит довольно круто.
Вид работающей печи с паковочными формами на переднем плане:
Я что-то проверяю или тыкаю:
Вынимаю тигель из печи:
Заливка:
Заливка:
Вот что было внутри (16 желудей + стробоскоп):
Acorn TIG, приваренный к стальному заглушке (будет прикреплен к кованой ветви на воротах):
Пучок желудей, готовый к прикреплению к воротам:
БЕЗОПАСНОСТЬ
Не делайте этого, если вы не выполнили надлежащую проверку.В идеале вы должны учиться у кого-то лично, но если это невозможно, вам следует прочитать несколько книг (рекомендации в конце этого поста) и посмотреть несколько видеороликов о разливке домашнего металла в Интернете. Расплавленный металл в любом количестве, превышающем сварочную лужу, чрезвычайно опасен, и несоблюдение этого требования может привести к серьезной аварии. Если есть вопросы, задавайте. Не вини меня, если ты поранишься.
РАСПЛАВЛЕННЫЙ МЕТАЛЛ
Если у вас есть какое-либо количество расплавленного металла, влага становится чрезвычайно опасной.Капля расплавленного металла на бетон (который удерживает влагу) превратит воду в порах в пар, вызывая небольшой взрыв, который выбрасывает жидкий металл и крошку бетона в воздух. А теперь подумайте, что было бы, если бы вы пролили целый тигель. ВСЕГДА ПЕРЕНОСИТЕ МЕТАЛЛ НА СУХИЙ ПЕСК.
Если вы воткнете что-нибудь — палочку для перемешивания, скиммер, еще куски металла для расплавления — в тигель, когда в нем есть расплавленный металл, этот объект должен быть DRY .Это так же просто, как предварительный нагрев металла на верхней части печи во время ее работы и удерживание конца любых инструментов в вытяжном пламени в течение нескольких секунд, но если вы забудете, вы заставите расплавленный металл взорваться, пока вы стоите там. с вашим лицом над ним. Точно так же ваши изложницы (в которые вы заливаете оставшийся металл после заполнения форм) необходимо предварительно нагреть в печи, иначе произойдет взрыв. ПРИНЯТЬ, ЕСЛИ ЧТО-ТО НЕ СЛИШКОМ ГОРЯЧЕ, ЧТО ЭТО ВЛАЖНОЕ .
ПРЕДОХРАНИТЕЛЬНОЕ ОБОРУДОВАНИЕ
Очки и маска для лица, а не одно или другое. Плотная кожаная куртка, сварочные перчатки, джинсы и толстые кожаные ботинки. Это то, что я ношу. Прекрасно работает, чтобы защитить от случайных брызг, и, по крайней мере, не тает на вашей коже в случае бедствия. Всегда держите под рукой ведро с сухим песком и лопату на случай разлива, а также охлаждающую штангу (кусок тяжелого углового железа, приваренный к концу трехфутового стержня), чтобы задержать поток в случае разрыва формы или течь.
ДОМАШНИЕ ТИГИ
Из-за серьезных опасностей, связанных с работой с расплавленным металлом, я настоятельно рекомендую НЕ использовать самодельные тигли для чего-либо более горячего, чем алюминий (например, для любых медных сплавов и чугуна). Подходящие тигли будут описаны ниже для каждого отдельного металла, и будет объяснен подходящий самодельный тигель для алюминия и других низкотемпературных сплавов.
Правильные тигли необходимы, даже если вы выполняете все остальные настройки:
—————————— ————-
Сначала я кратко расскажу о различных металлах, которые вы, возможно, захотите отлить, а затем расскажу некоторые подробности об общем оборудовании, которое вам нужно сделать. для небольшого литейного производства.
——————————————-
МЕТАЛЛЫ
СТАЛЬ
Хорошо, во-первых, вы, вероятно, никогда не будете отливать сталь дома, и вы определенно никогда не собираетесь делать стальную отливку размером с наковальню. Это просто реальность. Довести тигельную печь до температуры, необходимой для разливки стали, можно, но это превратит вашу печь в расходный материал. Я коснусь этого в первую очередь, поскольку похоже, что многие люди интересуются литьем стали.
Вот приблизительные точки плавления некоторых металлов (все температуры в F):
Мягкая сталь: 2750
Чугун: 2100
Кремниевая бронза: 1800
Алюминий: 1200
Свинец: 680
Имейте в виду, что вам нужно, чтобы металл был перегрет на несколько сотен градусов выше этих температур, чтобы его успешно разлить, так, например, железо будет разливаться около 2300-2500 (горячее для более тонких отливок). Температура в вашей печи должна быть еще выше, а это значит, что внутренняя температура печи будет близка к 3000.Огнеупор, который я использовал для своей печи, рассчитан на 3000, а поскольку низкоуглеродистая сталь плавится около 2750, вы можете понять, почему его плавление быстро разрушит вашу печь. Вот картина огнеупорной футеровки на моей печи, где капли расплавленного железа высадились на него:
бронзы и алюминий будет просто прилипает к поверхности, но расплавленное железо буквально съедает прямо в него. Печь настолько нагревается, что вам понадобится одна из зеленых оксиацетиленовых масок, чтобы увидеть ее с открытой крышкой. Он просто не выдерживает температуры, необходимой для плавления стали.
ЧУГУН
Тем не менее, с правильно сконструированной печью плавление чугуна совсем не сложно, однако вам необходимо использовать песчаные формы, поскольку формы для выплавки, которые вы делаете дома (обсуждаются ниже), не выдерживают температуры расплавленного металла. железо (пробовал). Формование из песка — это само по себе искусство, и для его правильного выполнения потребуется немало практики. В конце поста есть несколько хороших книг по этому поводу. Наконец, для чугуна вам необходимо приобрести графитовый тигель на глиняной связке. НЕ РАСПЛАВАЙТЕ ЖЕЛЕЗ В ЧТО-ТО, ЧТО ВЫ СДЕЛАНО СЕБЯ . Тигель обойдется вам в 50-100 долларов. Это очень дешевый страховой полис, который стоит каждого пенни. Серьезно. Без шуток. Практически все литейное оборудование, которое у меня есть, — самодельное, кроме тиглей для бронзы и железа.
BRONZE
Хорошо, перейдем к цветным металлам. Лично я использую только кремниевую бронзу для отливок из медного сплава по ряду причин. Во-первых, это состав: 96% меди, 3% кремния и 1% марганца.Вот почему это важно: латунь и другая бронза обычно содержат значительное количество цинка, олова и / или свинца помимо меди. Чтобы расплавить эти сплавы, их нужно нагреть выше температуры, при которой легирующие элементы испаряются. Это означает, что некоторое количество цинка, свинца, олова и т. Д. Улетучится с поверхности в виде газа, особенно когда вы перемешиваете или снимаете слой расплава. Это означает, что вы не только подвергаете себя воздействию токсичных паров, но и меняете состав металла каждый раз, когда его плавите.Кремниевая бронза не меняет состав даже после плавления в течение нескольких десятков раз (если вы держите тигель только для этого сплава), что делает ее идеальной для домашнего использования, где мы не можем проверить состав наших сплавов и где мы хотим немедленно повторно используйте металл, из которого состоит система ворот. Кроме того, вы можете купить прутки из кремнистой бронзы у большинства поставщиков сварочных материалов, что означает, что вы можете сварить их с помощью кислородно-ацетиленовой горелки или сварочного аппарата TIG и получить идеальное цветовое соответствие (особенно хорошо для фиксации небольших ямок в отливках и сварки двух отливок вместе и смешивание сварного шва).По этим причинам я считаю целесообразным покупать кремниевую бронзу вместо того, чтобы использовать куски лома неизвестного состава.
Что касается бронзы, вы действительно действительно хотите купить тигель, а не делать его. В частности, купите тигель из карбида кремния — опять же, около 50–100 долларов, и снова он того стоит. Я использовал самодельный тигель описанного ниже типа для плавления чистой меди, так как я не хотел загрязнять свой тигель для кремниевой бронзы и не хотел тратить 100 долларов на одноразовый эксперимент.Все шло хорошо, медь плавилась, я снял ее, а затем закрыл крышку печи, чтобы нагреть ее еще минуту, так как отливка должна была быть довольно тонкой, и я хотел, чтобы она была действительно горячей. Когда я снова открыл крышку, чтобы вынуть тигель, она вышла из строя, и дно печи было озером расплавленной меди. Если бы я не решил нагреть его еще на минуту, он бы вышел из строя, когда я поднимал его из печи. Это было бы примерно полгаллона расплавленного металла на моих ногах и ботинках.
АЛЮМИНИЙ
Алюминий отлично работает с ломом, но для достижения наилучших результатов используйте литой (а не экструдированный) алюминий. Это означает, что автомобильные колеса, детали велосипеда и т. Д. Идеальны, но не так много трубок, листов, пивных банок и т. Д. Поскольку алюминий плавится при такой низкой температуре, вы можете безопасно использовать стальной тигель ИДЕАЛЬНОЙ КОНСТРУКЦИИ или, еще лучше, чугунный тигель. Чтобы сделать стальной тигель, достаточно приварить кусок толстостенной трубы к более толстой пластине. Я с большим успехом использовал стенку 1/4 дюйма и 4-дюймовую трубу высотой около 10 дюймов, приваренную к куску пластины 3/8 дюйма.Сбоку приварил проушины для захвата клещами. Если вы не являетесь квалифицированным сварщиком, попросите кого-нибудь сварить его для вас, это не тот сварной шов, который вы хотите испортить. Кроме того, как и в случае с любым тиглем, вам нужно специально изготовить щипцы, которые очень хорошо подходят без люфта.
LEAD
Свинец плавится при такой низкой температуре, что вам даже не понадобится печь, только подходящий стальной или чугунный контейнер и несколько горелок. Мой сосед недавно отлил свинцовый киль весом 1100 фунтов для лодки, которую он строит, поместив свинец в модифицированную чугунную ванну, расплавив его несколькими кровельными горелками и вставив его снизу в деревянную форму с песчаным покрытием.Я не рекомендую деревянные формы — обработка поверхности не самая лучшая из-за влаги в форме, а пожарная часть была вызвана из-за чрезмерного копчения. Все вышеперечисленные меры безопасности применяются даже без печи, и помните, что свинец чрезвычайно токсичен.
ОБОРУДОВАНИЕ
Помимо тиглей для бронзы и / или железа, а также воздуходувки, вы можете легко сделать все, что вам нужно, самостоятельно. Вся моя литейная стоимость легко составляла менее 1000 долларов, включая несколько хороших книг (купленных новых, перечисленных ниже), два тигля, мою печь (материалы стоили около 300 долларов), гончарную печь (60 долларов на Craigslist и необходимые только для потерянного воска). литье), электрическая воздуходувка (25 долларов на Craigslist) и множество самодельного оборудования, в основном сделанного из лома стали.Моя печь надстроена и, вероятно, больше, чем могло бы понадобиться многим здесь людям. Вы можете гораздо меньше потратить на простую настройку. Вот весь мой литейный цех, запакованный в углу моего цеха (он выходит только время от времени):
ПЕЧЬ
Центральным оборудованием в литейном цехе является печь. Что касается масштабов, о которых мы говорим, тигельная печь — безусловно, самая разумная вещь для строительства, так что это все, что я буду обсуждать. Вы можете построить относительно печь, работающую на пропане или природном газе, которая в основном представляет собой вертикальную газовую кузницу с крышкой.Однако в этих печах будет трудно плавить железо, если они вообще смогут это сделать. Я настоятельно рекомендую купить у Колина Пека (в Англии) руководство под названием «Печь для отработанного масла от литья чугуна искусного Боджера». Это то, что я сделал, и никогда не стал бы строить печь другого стиля. Конструкция корпуса печи проста и легко модифицируется для использования имеющегося у вас лома, и он усовершенствовал конструкцию горелки, в которой для сжигания отработанного масла используется гравитационная подача (отработанное растительное масло, отработанное моторное масло и дизельное топливо работают хорошо. ).На горелке есть форсунка, поэтому топливо не распыляется, что означает, что вы можете использовать отработанное масло (свободное, но загрязненное частицами), не забивая горелку. Кроме того, поскольку оно подается под действием силы тяжести, нет необходимости в насосе, а масло при атмосферном давлении НАМНОГО безопаснее, чем сжатый газ, когда вы работаете с расплавленным металлом. Кроме того, он выделяет намного больше тепла, чем пропан или природный газ — я могу расплавить 30 фунтов бронзы при холодном запуске менее чем за 45 минут. Правильно построенный, он очень чисто горит (не дымится) и может легко плавить чугун.Он определенно может расплавить сталь, если вы захотите, но это быстро испортит футеровку печи. Используя в основном подручные материалы, я потратил около 300 долларов на свою печь. Стоимость — это, прежде всего, литой огнеупор с температурой 3000 градусов (очень рекомендуется), который, как мне кажется, стоил 65 долларов за мешок весом 50 фунтов (я использовал 3) около 5 лет назад. Я не буду вдаваться в подробности о конструкции печи, поскольку Колин пытается продать свою книгу, поэтому вам придется купить ее у него, если вам нужны планы (обратите внимание, я никоим образом не извлекаю выгоду из этого, и я не даже знаю Колина.Просто это такой хороший дизайн, что это все, что я хочу порекомендовать).
РУЧНЫЕ ИНСТРУМЕНТЫ
Вам понадобятся различные простые инструменты, которые вы легко можете изготовить самостоятельно. Здесь изображены разливочный стержень (длинная вещь, которая удерживает тигель во время разливки), щипцы для тигля (для подъема тигля в печь и из печи), скиммер (угловая сталь, приваренная к стержню, изогнутая на конце, чтобы соответствовать моему тиглю, используется для снятия шлака перед разливкой) и изложницы (угловой чугун с закрытыми концами и рукояткой для выливания остатков металла после заполнения изложниц).Другие инструменты, не изображенные на рисунке, включают стальной стержень 1/2 дюйма для перемешивания, охлаждающую штангу (описанную выше в разделе «Оборудование безопасности»), пару клещей для загрузки предварительно нагретого металла в тигель. Действительно простые вещи. Также обратите внимание, что для измерения температуры вам не нужен пирометр. Просто возьмите стержень диаметром 1/2 дюйма, который вы используете для перемешивания, воткните его на секунду в расплав, а затем вытащите. Если расплавленный металл соскользнет с конца, вы готовы к заливке. Если он на нем слипается, значит, он недостаточно горячий. Этот метод никогда не подводил меня для алюминия, бронзы и железа.
ИНСТРУМЕНТЫ ДЛЯ ФОРМЫ
Это зависит от того, выполняете ли вы литье в песчаные формы или по выплавляемым моделям. Я не делал форм для песка несколько лет, и у меня больше нет инструментов для этого, поэтому я не буду пытаться перечислять то, что вам нужно, это просто простые ручные инструменты и мюллер, если вам повезет, чтобы скрестить дорожки с одним. Я бы порекомендовал новичкам использовать Petrobond (песок на масляной основе), а не песок на водной основе, так как с ним легче работать и поддерживать его.
Я не буду вдаваться в подробности фактического процесса литья под давлением, но если вам интересно, вы должны купить последнюю книгу, указанную в конце этого поста.Я скажу, однако, что «микрокристаллический воск» — это то, что вы хотите купить, если делаете скульптурные изделия. Он становится очень мягким при нагревании от ваших рук, а затем может выдерживать любое скручивание или изгиб, не трескаясь, и очень плавно перетекает в себя. Подобно кремниевой бронзе, этот продукт настолько превосходен, что стоит своих денег. Паковочные формы легко сделать из 1 части воды, 1 части гончарного гипса и 2 частей грубого песка.
Для этого процесса вам нужно будет выжечь формы в печи, чтобы расплавить, сжечь и, наконец, испарить воск, а также прокалить формы.Вам нужно запустить его в течение нескольких дней и медленно повышать температуру, в конечном итоге поддерживая формы на уровне 1200 в течение дня и заполняя их расплавленным металлом, когда они остынут примерно до 800. Стандартная гончарная печь работает нормально, но будьте готовы проснуться вставайте один или два раза каждую ночь, чтобы проверить температуру, если у вас нет цифрового контроллера. Кроме того, вы можете выжечь другие органические предметы (овощи, палки и т. Д.) Вместо того, чтобы лепить что-то воском.
ПОСТАВЩИКИ / МАТЕРИАЛЬНЫЕ РЕСУРСЫ
Budget Casting Supply — ваш лучший выбор для покупок в Интернете, но если вы живете в большом городе или рядом с ним, вам действительно следует искать местных поставщиков.Если вы не знаете ни одного, попробуйте поискать в ThomasNet. Если вы не знакомы, этот веб-сайт представляет собой базу данных производителей и поставщиков с возможностью поиска, что очень полезно. Часто предприятия, поставляющие литейное оборудование или огнеупоры, никогда не имеют случайных клиентов, и если вы объясните, чем вы занимаетесь, они часто будут очень заинтригованы и постараются помочь вам. Мне еще предстоит заплатить за изоляцию из керамического волокна, хотя я получил ее в большом количестве между различными кузницами и моей печью — крупный поставщик огнеупоров обычно может предоставить вам «образец», которого более чем достаточно для того, что вы работаете на.
——————————————-
Вот и все У меня есть для вас, не написав об этом книги. Надеюсь, это будет полезно для некоторых из вас, кто хочет добавить литье в свои навыки работы с металлом. Я буду более чем счастлив ответить на любые ваши вопросы, и если кто-то находится в районе Филадельфии и хочет увидеть разлив, просто дайте мне знать, и я приглашаю вас к следующему.
——————————————-
РЕКОМЕНДУЕМЫЕ ЧТЕНИЯ
— «Печь для отработанного масла от литья чугуна Искусного Боджера», автор Колин Пек
… Доступно у автора по адресу http: //www.artfulbod…alcasting.com/. Это руководство — то, что я использовал, чтобы построить свою печь, описанную выше. Я не думаю, что когда-либо построил бы тигельную печь, не основанную на этой конструкции. Ужасно написано, никогда даже не корректируется, но тем не менее бесценно.
— «Библия литейщика» К. В. Аммена
— «Полное руководство по литью в песчаные формы» также К. В. Аммен
… Книги Аммена очень удобочитаемы и понятны. Получите их независимо от того, делаете ли вы формы из песка или паковочные массы.
— «США. Руководство по литейному производству военно-морского флота », перепечатанное Lindsay Publications
… бесценный ресурс, но не из тех книг, которые вы читаете насквозь (например, скучное техническое руководство). Опять же, хотя он написан, в частности, для литья в песчаные формы, большая часть информации также имеет отношение к литью по выплавляемым моделям.
— «Литейный уголь» Дэйва Джинджери
… отлично подходит для начала, это песочное литье в самой упрощенной форме. Идеально подходит для супер-недорогой установки, чтобы залить немного алюминия, чтобы узнать, нравится ли он вам.
— «Литье металла: руководство по литью в песчаные формы для малых литейных производств» Стива Честейна
… есть два тома. Хорошие книги, но не обязательно, если вас интересует только литье по выплавляемым моделям.
— «Студийное бронзовое литье: метод потерянного воска» Джона Миллса и Майкла Гиллеспи
… для литья по выплавляемым моделям.
Также проверьте Lindsay Publications, чтобы узнать о других книгах по кастингу, включая некоторые из перечисленных выше.
Подбор тигля к вашему применению
Если вы плавите металл или держите ванну с расплавом, скорее всего, ваша операция уникальна.Ваша конкретная комбинация печей, сплавов, методов работы, металлургической обработки, устройств разливки и конечных продуктов вряд ли будет скопирована на каком-либо другом предприятии. Поэтому выбор тигля, который обеспечит максимальную производительность вашей операции, — это индивидуальная и сложная задача.
Эта статья призвана служить руководством по выбору оптимального тигля для вашей работы. Он объясняет взаимосвязь между плавкой / выдержкой металла и конкретными характеристиками тигля.Он обеспечивает поддержку, но не отменяет необходимость тесного сотрудничества между плавильными предприятиями и поставщиками тиглей в процессе выбора тиглей.
Современный тигель представляет собой крайне неоднородный композитный материал на основе графита, который зависит от его состава и контроля структурного выравнивания графита для достижения требуемых характеристик. Тигли могут быть размером с чайные чашки или вмещать несколько тонн металла. Они могут быть закреплены на месте внутри конструкции печи или могут быть предназначены для извлечения из печи для разливки в конце каждой плавки.Тигли используются в топливных печах, в электрических печах сопротивления, в индукционных печах или просто для перекачки расплавленного металла. Они бывают с разливочными носиками или без них и имеют широкий спектр традиционных и специализированных форм.
Они также обладают множеством различных рабочих характеристик, поскольку каждое приложение представляет собой сложный набор температурных, химических и физических параметров, которые определяют технические границы, в которых должен быть разработан тигель для работы.
Итак, как выбрать правильный тигель для вашей работы из обширного диапазона доступных вам тиглей и материалов?
Лучший подход — начать с вашей собственной детальной оценки ваших операций.Вам необходимо полностью задокументировать и, по возможности, количественно оценить все аспекты ваших процессов плавки, выдержки и обработки металла. К ним относятся:
- Вместимость, размеры и тип вашей печи
- Конкретный сплав или ряд сплавов, которые вы плавите
- Поддерживаемые вами температуры плавления и / или выдержки
- Скорость изменения температуры тигля
- Как заряжается тигель
- Используемые флюсы или добавки
- Процессы дегазации или рафинирования
- Как удаляются шлак или окалина
- Как опорожняется тигель.
Эти девять категорий отражают наиболее общие факторы, которые необходимо учитывать при выборе тигля в соответствии с вашими конкретными требованиями. Вы также должны учитывать любые дополнительные процессы или требования, которые могут быть специфичными для вашей деятельности. Примером может служить ваша способность терпеть или необходимость избегать перекрестного загрязнения сплава.
В то время как вы вносите подробную информацию о ваших собственных операциях в процесс выбора тиглей, ваш поставщик тиглей должен предоставить высокий уровень знаний о материалах, характеристиках и характеристиках тиглей.Чтобы получить наибольший выбор, ищите поставщика тиглей, который может предложить совпадающие линейки продуктов для тиглей, подходящие для каждого конкретного металла, но предлагающие разные рабочие характеристики. Затем, работая вместе, вы сможете точно подобрать тигель в соответствии с вашими конкретными требованиями. Достижение этого соответствия является ключом к безопасности, производительности и максимальному сроку службы тиглей.
Однако имейте в виду, что на практическом уровне не может быть ни одного типа тигля, который предлагал бы наивысший уровень всех желаемых характеристик для вашего приложения.Рабочие характеристики тигля часто требуют компромиссов. Например, тигель с наилучшей теплопроводностью может не обеспечивать наилучшей защиты от теплового удара. Таким образом, вы должны определить приоритетность списка свойств тигля, наиболее важных для вашего приложения, и обсудить эти приоритеты с вашим поставщиком тиглей.
Объем печи, размеры и тип
Мощность, размеры и тип печи, которую вы используете, определят большинство наблюдаемых деталей о вашем тигле.Например, если вы знаете, на какую металлическую емкость была рассчитана ваша печь, вы будете знать, какую емкость должен обеспечивать ваш тигель. Точно так же размеры пространства для тигля в вашей печи будут определять размеры и форму вашего тигля. Это также определит, должен ли ваш тигель иметь сливной носик. Но выбор тигля, соответствующего типу вашей печи, даст вам множество других менее очевидных факторов, которые необходимо учитывать.
Топливные печиТопливные печи включают печи, работающие на газе, масле, пропане или коксе.Каждое из этих видов топлива напрямую подвергает тигель воздействию источника тепла, и каждое из них обеспечивает разный уровень тепла, обычно измеряемый в БТЕ. Любой выбранный тигель должен выдерживать максимальное количество БТЕ, которое топочное топливо способно подать в тигель. В газовых, масляных и пропановых печах тигель должен выдерживать воздействие пламени горелки у основания тигля, а тигель должен иметь сужение, чтобы пламя могло циркулировать по тиглю снизу вверх. Это позволяет равномерно нагревать тигель.Материал тигля также должен быть в состоянии противостоять окислительному повреждению пламени и выдерживать скорость теплового изменения, которое будет испытывать тигель.
Хорошая теплопроводность и равномерный нагрев являются важными свойствами тигля для передачи тепла изнутри печи через тигель к металлической загрузке. Тигли с высоким содержанием графита в углеродной связке обладают высокой теплопроводностью для быстрого плавления в газовых печах.
Печи сопротивленияЭлектрические печи сопротивления обеспечивают равномерный всесторонний нагрев тигля и идеально подходят для точного контроля температуры при хранении металлов.Но они медленнее, чем топочные печи в плавильных установках. Следовательно, энергоэффективные тигли с высоким содержанием графита в углеродном связующем часто выбирают для обеспечения высокой теплопроводности для более быстрого плавления в этих печах.
Тигли, предназначенные для электрических печей сопротивления, обычно имеют форму чаши и обеспечивают одинаковое расстояние между тиглем и нагревательными элементами печи.
Индукционные печиВыбор тиглей для индукционных печей — более сложная задача.В некоторых применениях, таких как рафинирование драгоценных металлов, для плавления шихты используются тигли, предназначенные для нагрева в индуктивных полях печи. В других приложениях используются тигли, которые позволяют индуктивному полю проходить через них и напрямую нагревать металлическую шихту. Поэтому важно, чтобы электрические характеристики тигля соответствовали рабочей частоте печи и условиям плавления. Например, в некоторых конструкциях низкочастотные индукционные печи требуют тиглей с высоким содержанием карбида кремния, а в других приложениях для высокочастотных индукционных печей требуются тигли с высоким содержанием глины.Согласование удельного электрического сопротивления тигля с индукционной печью является ключом к предотвращению перегрева тигля.
Большинство тиглей, разработанных для индукционных печей, имеют цилиндрическую форму, чтобы обеспечить одинаковое расстояние между тиглем и змеевиком печи. Однако некоторые небольшие печи, предназначенные для съемных тиглей, имеют конический змеевик, который соответствует профилю трюмных тиглей.
Съемные тигельные печиВсе вышеперечисленные типы печей могут быть сконструированы для использования съемных тиглей.Эти тигли можно загружать снаружи или при установке в печи, но они извлекаются из печи для разливки. Подобно тиглям, используемым только для перекачки металла, они имеют трюмную или А-образную форму, чтобы их можно было поднимать с помощью щипцов, предназначенных для правильной поддержки тигля.
Ограничение мощности печи Последний фактор, который следует учитывать при документировании требований к тиглю на основе технических характеристик печи, — это наличие электроэнергии. Во многих местах мощность для плавления или выдержки может быть недоступна в любое время или может быть непомерно дорогой в определенные
раз или на определенных уровнях.Если это так на вашем предприятии, может быть особенно важно выбрать энергоэффективный тигель.
Металлы, которые вы плавите и / или удерживаете
Знание того, какие металлы и сплавы вы плавите или держите, многое расскажет о том, какие характеристики вам нужны в тигле. Подробный каталог металлов, которые вы собираетесь плавить, поможет установить максимальную температуру, которую тигель должен поддерживать для плавления и выдержки, определит, как металл будет взаимодействовать с материалом тигля как химически, так и физически, и это будет ключевым фактором при определении какие характеристики должен иметь ваш оптимальный тигель.В частности, при плавке сплавов на основе меди в топочных печах валковые тигли из карбида кремния работают лучше из-за более высокой термостойкости. В других типах печей тигли часто выбирают из-за их высокой плотности. Менее плотные и более пористые тигли могут вызвать эрозию.
Тигли из глино-графита и карбида кремния на углеродной и керамической связке широко используются для плавки и выдержки алюминия и алюминиевых сплавов, алюминия-бронзы, сплавов на основе меди и меди, медно-никелевых и никелево-бронзовых сплавов, драгоценных металлов, цинка. и оксид цинка.Тигли также используются при плавке чугуна. Взятые вместе как группа, эти металлы представляют собой диапазон температур от 400 ° C / 750 ° F до 1600 ° C / 2912 ° F.
Хотя некоторые типы тиглей поддерживают температуру металлов, охватывающих широкий спектр металлов, часто необходимо выбирать тигли, предназначенные для определенных металлов или сплавов и с более ограниченными диапазонами рабочих температур. Выбор таких тиглей часто бывает более выгодным, поскольку они обладают характеристиками, важными для вашей работы.Например, использование тигля, способного плавить металлы от железа до цинка, может быть не так важно для вашей операции плавления алюминиевого сплава, как наличие тигля, ограниченного необходимым температурным диапазоном, но способного противостоять коррозионным повреждениям от флюсов для обработки металлов.
Температуры плавления и выдержки
Вообще говоря, металлы и сплавы, которые вы плавите или держите, будут определять температурный диапазон, в котором должен работать ваш тигель. Ни в коем случае нельзя нагревать тигли выше их максимальной температуры.Это может привести к опасному повреждению тигля. Однако работа ниже нижнего предела температуры тигля также может вызвать проблемы. Например, тигли, предназначенные для высокотемпературного плавления сплавов на основе меди, будут окисляться при использовании при низких температурах для плавления цинка.
При выборе тиглей также необходимо учитывать методы плавления и выдержки, связанные с температурами металлов. Если ваши операции связаны с перегревом, вам необходимо принять во внимание более высокие достигнутые температуры металла.
Скорость изменения температуры
Способность тигля выдерживать скорость изменения температуры так же важна, как и его минимальные и максимальные пределы температуры. Если ваши методы работы приводят к частым циклам нагрева и охлаждения тигля или иным образом подвержены резким изменениям температуры, вам необходимо выбрать тигель, устойчивый к тепловому удару. Некоторые типы тиглей намного лучше справляются с быстрым изменением температуры, чем другие. Например, высокое содержание углерода в графите в тигле обеспечивает высокую теплопроводность и несмачиваемость.И когда этот графит образует ориентированную матрицу, тигель также обеспечивает высокую термостойкость. Это очень важно для литейного производства, где температура может изменяться на несколько сотен градусов за секунды. Ваш поставщик тиглей может посоветовать, какие тигли обеспечивают наилучшую стойкость к тепловому удару для вашего применения.
Как заряжается тигель
Если ваша печь всегда загружается расплавленным металлом, вероятно, ей не нужен тигель, обладающий высокой устойчивостью к физическим повреждениям.Однако, если основную часть шихты составляют металлические слитки или другие тяжелые материалы, и они не опускаются в печь осторожно с помощью автоматической системы загрузки, вы можете выбрать тигель, который механически прочен и способен выдержать физические удары. Тигли с высоким содержанием углерода и ориентированной графитовой структурой обеспечивают отличную ударопрочность.
Вам также понадобится тигель с прочной защитной глазурью. Повреждение глазури в результате грубого обращения может привести к окислению тигля.Экструдированные алюминиевые слитки часто имеют острые края, которые глубоко врезаются в корпус тигля, что приводит к разрушительным трещинам.
Флюсы и добавки
Все тигли обладают определенной устойчивостью к коррозии и химическому воздействию. Но большинство флюсов и других видов обработки металлов, используемых при плавлении алюминия и других цветных металлов, очень коррозийны и требуют тигля, который обеспечивает высокий уровень стойкости к химическому воздействию. Это сопротивление лучше всего обеспечивается как стабильно плотной структурой материала тигля, так и прочной защитной глазурью.Если ваше плавление предполагает использование коррозионной обработки металлов, вам, безусловно, понадобится тигель, обеспечивающий соответствующий уровень защиты от этих агентов.
Дегазация и переработка
Дегазация алюминия и алюминиевых сплавов обычно включает барботаж инертного газа, обычно азота, через ванну расплава при перемешивании ванны с помощью ротора, предназначенного для разрушения и рассеивания пузырьков газа. Эти маленькие пузырьки затем вытягивают нежелательный водород и оксиды из ванны и выносят его вместе с шлаком и включениями на поверхность, где газ выходит в воздух, а твердый материал может быть удален.Этот процесс, часто используемый вместе с флюсующими добавками, физически разрушает тигель, а также химически разрушает его. Поэтому требуется плотный и механически прочный тигель, обладающий высокой устойчивостью к химическому воздействию. Тигли из карбида кремния обеспечивают отличную стойкость к эрозии при повышенных температурах и химической коррозии. Кроме того, при изостатическом прессовании тигли образуют в своей структуре случайное расположение графита. Это способствует созданию более плотных продуктов, которые могут более эффективно выдерживать эрозионные и коррозионные условия.
Многие процессы рафинирования и обработки металлов, используемые с другими цветными металлами, также требуют наличия механически прочного и химически стойкого тигля.
При рафинировании и плавке драгоценных металлов особенно важно, чтобы тигель, который вы используете, обеспечивал чистый металл за счет несмачивающих свойств. Это означает, что тигель должен быть хорошо защищен от проникновения металла. Эта характеристика обеспечивается плотной структурой материала тигля и прочной защитной глазурью.
Удаление шлака и окалины
Плотный, несмачивающий тигель также поможет уменьшить накопление шлака и шлака и упростит очистку пустого тигля.
Опорожнение печи
Тигли для плавки и выдержки расплавленного металла, выгружаемого из печи, должны быть сконструированы таким образом, чтобы обеспечить легкий доступ к металлу и обеспечить высокую термическую эффективность. Это позволяет печи поддерживать температуру металла при минимальном расходе топлива или энергии.
Тигли для печей, которые наклоняются для разливки, часто требуют встроенных разливочных носиков, которые обеспечивают необходимый радиус действия и точность разливки.
Заключение
Обладая полным и подробным пониманием всех аспектов операций по плавке и / или выдержке металла, вы и ваш поставщик тиглей будете иметь все возможности для выбора тигельного продукта, который соответствует вашим конкретным эксплуатационным требованиям и обеспечивает неизменно более длительный срок службы.
Методы и измерения дегазации алюминия
Для производства качественных алюминиевых отливок специалисты по металлу должны удалить излишки водорода из расплавленного металла, при этом проводя испытания, чтобы убедиться в этом.
A СОВРЕМЕННОЕ ЛИТЬЕ Отчет персонала
(Щелкните здесь, чтобы увидеть историю в августовском выпуске Modern Casting.)
Расплавленный алюминий чрезвычайно реактивен, поэтому при контакте с влажным воздухом или влажными инструментами вода разлагается с выделением водорода в расплаве. Избыточные количества этого растворенного газа имеют хорошо задокументированное пагубное влияние на механические свойства конечных алюминиевых отливок. Любому, кто занимается отливкой, также хорошо известно, что растворенный газ имеет решающее влияние на распределение и величину пористости и усадки.Уровни растворенного водорода необходимо контролировать, чтобы свести к минимуму брак. Чтобы контролировать газ в алюминии, металлурги должны выполнить две задачи:
1. Предотвратить и минимизировать попадание водорода в расплав.
2. Отмерьте и удалите водород перед заливкой.
Эта статья будет посвящена измерению и удалению.
Удаление газа
Способность дегазировать расплавленный алюминий обычно достигается за счет использования продувочного газа, обычно вводимого в расплав с помощью роторной установки дегазации.Этот процесс дегазации ограничен термодинамическими законами; когда в расплав попадают пузырьки продувочного газа, они собирают водород, всплывая к поверхности. Наилучшая возможная ситуация — эти насыщенные водородом пузырьки покидают расплав и снижают уровень водорода. В этом случае эффективность процесса с термодинамической точки зрения составляет 100%. Но по мере того, как содержание газа в расплаве падает, снижается и равновесное давление водорода в пузырьках, поэтому количество продувочного газа, необходимого для удаления оставшегося водорода, должно увеличиваться.
Равновесный коэффициент удаления газа показан на рис. 1 для чистого алюминия при температуре выше 1400F (760 ° C). Например, коэффициент удаления газа 200 означает, что для удаления одного литра водорода потребуется 200 литров инертного газа. Такое поведение ограничивает способность металиста дегазировать до очень низкого уровня водорода. Растворимость также экспоненциально увеличивается с температурой, а это означает, что увеличение на 200 ° F (111 ° C) удваивает растворимость. При прочих равных условиях более высокая температура алюминиевого расплава увеличивает необходимое время дегазации.
Легирующие элементы также могут влиять на растворимость водорода. Влияние легирующих элементов характеризуется изменениями поправочного коэффициента сплава, причем некоторые распространенные литейные сплавы показаны в таблице 1. Сплавы с более высокими значениями дегазировать труднее, поэтому, например, для алюминия 535 потребуется в четыре раза больше времени для дегазации, чем для чистый алюминий. К счастью, этими факторами можно управлять, и в большинстве случаев без излишних трудностей можно добиться содержания газа и процесса, необходимого для устранения чрезмерной пористости в алюминиевых отливках.
Практические процедуры дегазации
Дегазация обычно выполняется на одном из трех участков литейного производства:
1. В передаточном ковше, используемом для перемещения металла между плавильной и раздаточной печами.
2. В тигельных печах, обычно непосредственно перед разливкой расплавленного алюминия.
3. В поточной системе, когда металл транспортируется в раздаточные печи через желоб.
Первые два варианта являются наиболее распространенными, и операция дегазации для обоих обычно выполняется с помощью дегазатора с роторным рабочим колесом (RID).На практике не все роторные дегазаторы созданы равными. Важно иметь оптимальную конструкцию головки для получения высокоэффективных маленьких пузырьков. Существенная экономия может быть получена за счет более короткого времени обработки и уменьшения использования газа. В прошлом в отрасли литья металлов тяготели к простым конструкциям головок, которые дешевле обрабатывать, но производят более крупные пузыри. Этот путь представляет собой ложную экономию из-за снижения эффективности.
Регулировка параметров процесса
Как только установка RID будет полностью опущена в жидкий металл с установленным валом, можно начинать дегазацию.Лучшее расположение вала немного смещено от центральной линии тигля или ковша, чтобы избежать образования вихрей при его круговом вращении в жидком металле. Обычно достаточно смещения 2–4 дюйма от осевой линии. Использование перегородки также является хорошей идеей, поскольку перегородка препятствует циркуляционному движению металла и уменьшает образование вихрей.
Установив RID в нужное место, следует включить устройство и установить скорость вала 300 об / мин. Также должен быть включен поток инертного газа, и операторы должны затем отрегулировать расход газа и скорость вала.Расход газа следует увеличивать до тех пор, пока не будут видны пузырьки газа, всплывающие на поверхность жидкого металла. По мере увеличения потока газа размер пузырьков должен увеличиваться.
Желаемый результат — хорошее рассеивание мелких пузырьков при сохранении относительно тихой поверхности. Когда будет найдено оптимальное сочетание расхода и скорости вращения вала, запишите параметры для использования в будущем. Также обратите внимание на общее время дегазации, которое обычно составляет от четырех до восьми минут, если только температура не очень высокая или количество необходимого газа мало.
Измерение газа
Существует два основных метода анализа газа: методы отбора проб и методы in situ. Методы отбора проб можно разделить на два класса. В первом случае жидкий образец отбирается и вводится непосредственно в измерительный прибор до того, как произойдет затвердевание. Во втором случае образец жидкости наливается в специально разработанную форму и анализируется твердый образец. Методы анализа представлены в таблице 2.
Все три метода анализа жидкой пробы в некоторой степени зависят от содержания включений в расплаве, поскольку эти включения вызывают образование пузырьков газа.На рис. 2 показана пора в отливке из сплава А356, образовавшаяся на оксидных пленках. Несмотря на эту проблему, испытание пониженным давлением (RPT), процедура исследования твердого образца, является широко используемым и эффективным инструментом. Процедура проста для понимания и выполнения. Оборудование простое, прочное и недорогое, а результаты обычно зависят от качества литья. Однако во время затвердевания необходимо контролировать давление.
Отвержденный образец для испытаний RPT разрезается и полируется для получения качественного или полуколичественного измерения содержания газа, либо плотность образца определяется путем измерения веса образца, когда он сухой, а затем суспендируется в воде.Пока в образце нет усадки, предпочтительным методом является измерение плотности, поскольку оно устраняет субъективность, связанную с визуальным осмотром поверхности среза.
При использовании методов in situ процесс отбора проб не вызывает ошибок, поэтому эти измерения потенциально могут быть наиболее точными и надежными. Большинство методов in situ включают систему рециркуляции инертного газа, вводимого в расплав с помощью пробоотборника. Инертный газ рециркулирует через расплав, собирает и пропускает через датчик дифференциальной теплопроводности для определения содержания водорода в газе.Эта рециркуляция продолжается до тех пор, пока содержание водорода не достигнет значения, равновесного с расплавом.
Перспективен новый метод измерения водорода. Последняя версия электрохимического датчика почти эквивалентна термопаре. Это был бы святой Грааль измерения газа, позволяющий нам измерять газ так же, как мы измеряем температуру с помощью портативных устройств.
Практические рекомендации по RPT
По меньшей мере 90% производителей алюминия в Северной Америке используют RPT для определения качества металла.Несколько практических подходов могут улучшить производительность.
Оборудование, необходимое для оценки вакуума расплава алюминия, состоит из насоса, манометра для контроля уровня вакуума внутри испытательной камеры и системы управления для регулирования давления (рис. 3). На практике расплавленный образец помещают на подставку, над образцом помещают камеру со смотровым окном, из камеры откачивают воздух до желаемого давления, и образцу дают затвердеть при пониженном давлении.Снижение давления в камере заставляет растворенный водород выходить из раствора в расплаве и либо выходить из образца через расплавленную поверхность, либо образовывать пузырьки внутри затвердевающего образца.
Важно, чтобы оператор мог видеть образец во время затвердевания, чтобы увидеть, образуются ли пузырьки на поверхности. На практике испытание пониженным давлением проводится двумя способами:
1. Низкое содержание газа. Иногда может потребоваться металл с низким содержанием газа, например, для высококачественных отливок для аэрокосмической промышленности или критически важных для безопасности компонентов.В этих случаях лучше всего использовать низкое испытательное давление (высокий вакуум) и подсчитывать пузырьки, образующиеся на поверхности. Когда на поверхности отливки появляется менее двух или трех пузырьков, содержание газа низкое.
2. От среднего до высокого содержания газа: Иногда более высокие уровни газа полезны, например, при отливке в постоянные формы, где более высокий уровень газа может помочь избежать усадки. В этом случае используется более высокое испытательное давление (более низкий вакуум), чтобы газ оставался внутри затвердевающего образца. Результат теста обычно измеряется путем определения плотности или удельного веса образца RPT.
В любом случае рекомендуется обучить операторов смотреть на поверхность образцов как во время испытания, так и после него. Два образца RPT показаны на рис. 3. Образец справа имеет лучшее качество металла, меньше оксидов и предположительно более низкое содержание газа.
Важно выбрать правильное испытательное давление для теста RPT. Для этого нужно знать немного больше о том, как измеряется давление и как давление определяет, когда обнаруживается пористость во время затвердевания.Большинство манометров, используемых в тестерах RPT, являются дифференциальными, они измеряют разницу давления между вакуумной испытательной камерой и окружающим воздухом. На уровне моря среднее атмосферное давление будет поддерживать столб ртути 29,92 дюйма (760 мм), или 30 дюймов для простоты. Большинство металлургов будут использовать манометрическое давление 26-28 дюймов, которое называется уровнем вакуума или давлением.
СплавA356 можно выбрать в качестве примера, чтобы показать, что происходит во время затвердевания. Металл содержит газообразный водород 0.12cc / 100g, довольно низкое содержание газа. Когда образец этого металла извлекается из тигля и помещается в RPT, давление водорода увеличивается из-за двух факторов:
1. Образец остывает до более низкой температуры.
2. По мере замораживания водород и кремний разделяются и накапливаются в оставшейся жидкости.
Давление газа продолжает расти во время затвердевания до тех пор, пока не достигнет значения, равного среднему атмосферному давлению, когда затвердело 70% образца.
При отливке этого металла методом замораживания в цехе пористость не может образоваться до тех пор, пока 70% материала не замерзнет в твердом состоянии. Однако когда применяется вакуум, ситуация иная. Сначала рассмотрим случай, когда к затвердевающему образцу прикладывают манометрическое давление 28 дюймов. Манометрическое давление 28 дюймов соответствует абсолютному давлению 50 Торр. Это немного ниже равновесного давления газа в этом образце в начале затвердевания, поэтому на поверхности образца могут образовываться пузырьки газа, прежде чем он начнет замерзать.
Получение точных результатов испытаний при пониженном давлении имеет важное значение для создания качественных отливок. Вот несколько из многих способов обеспечения надлежащих процедур RPT:
- Для отбора проб используйте тонкостенную чашку.
- Обезжиренные оксиды из расплава
- поверхность.
- Разогрейте чашку на прилегающей поверхности.
- Быстро переместите образец в вакуумную установку с надлежащими уплотнениями и мощностью насоса.
- Закройте камеру для визуального наблюдения.
- Контролировать вакуум до заданного уровня.
- Отрегулируйте время цикла, чтобы обеспечить полное затвердевание образца.
- Измерьте удельный вес образца и сравните его со спецификациями процесса (или подсчитайте пузырьки на поверхности).
Эта статья была взята из книги Джеффри К. Сигворта «Лучшие методы литья алюминиевого металла» 2014 года, опубликованной AFS и доступной для покупки на сайте www.afsinc.org/store.cfm.
E
Противостояние сценарию, в котором вы вынуждены внезапно и немедленно приостановить плавильные операции на длительный период, может стать смертным приговором для многих предприятий по литью металла. Малые и средние предприятия составляют основу отрасли, но многие из них не выживают, когда вынуждены работать в условиях длительного простоя. Однако один пострадавший от стихийного бедствия литейщик обрел устойчивость благодаря собственной настойчивости и поддержке со стороны коллег, друзей, поставщиков, команд монтажных и ремонтных служб, производителя оригинального оборудования и даже конкурентов.
Tonkawa Foundry, семейное предприятие в третьем поколении в Тонкаве, штат Оклахома, начало свою 65-ю годовщину работы в этом году, когда 17 января произошел серьезный технический сбой, разрушивший электроснабжение и плавильные печи. Благодаря эвакуации учебников По словам операционного менеджера Кэрри Хейли, никто не пострадал во время инцидента, но степень эмоционального и финансового ущерба, а также то, как долго это событие приведет к отключению Тонкавы, оставалось неясным.
Электроснабжение Тонкавы и две печи со стальным кожухом необходимо будет реконструировать.Никакая часть процесса реконструкции не могла начаться до тех пор, пока страховая компания не утвердила удаление оборудования с площадки. Потенциальная потеря сотрудников и клиентов Тонкавы из-за конкурирующих металлургов казалась неизбежной.
В течение двух дней после инцидента представители по ремонту, установке и оборудованию прибыли в Тонкава для осмотра повреждений. После того, как страховая компания выдала разрешение на начало работ, монтажная бригада в течение 24 часов мобилизовалась, чтобы снять оборудование и разобрать плавильную платформу.
С тех пор, как поврежденное оборудование было установлено в 1980-х и 1990-х годах, Tonkawa и компания по обслуживанию и ремонту оборудования быстро разработали план и определили способы повышения безопасности, эффективности и общей производительности плавильной платформы Tonkawa.
«Самым важным вопросом для нашей команды была организация плана реагирования», — сказал Стив Отто, исполнительный вице-президент подразделения установки EMSCO в Нью-Джерси. «Нам нужно было прибыть на Тонкаву готовыми к работе как можно скорее и доставить быстро и тщательно, чтобы они могли вернуться к плавке и производству отливок и минимизировать риск закрытия.
Через несколько лет после того, как была установлена плавильная платформа Тонкавы, потребовалось изменение высоты, чтобы приспособить использование ковша большей емкости под носиком печей. Вместо того, чтобы поднимать всю площадку расплава, была поднята только площадка, поддерживающая печи. В результате источник питания и рабочая станция располагались на две ступеньки ниже печей, что создавало ряд неудобств и проблем, которые влияли на общий рабочий процесс в зоне плавления. Кроме того, близость источника питания к печам не только способствовала ограниченному рабочему пространству, но и увеличивала вероятность повреждения источника питания.
Повреждения плавильной палубы потребовали ее восстановления. Было решено, что это идеальная возможность поднять всю площадку на одну высоту и расположить источник питания, рабочее место и печи на одном уровне. Компания, занимающаяся установкой печи, предоставила концепции компоновки, и с помощью Раджеша Кришнамурти, инженера по приложениям, Университет штата Оклахома, Тонкава использовал эти концепции для создания чертежей для конструкции новой платформы. В результате появилась модернизированная система плавления с равномерной высотой, стратегически размещенным источником питания, повышенной безопасностью и производительностью оператора.
«Устранение ступенек и перемещение источника питания подальше от печей было значительным улучшением для нашей плавильной платформы», — сказал совладелец Tonkawa Джим Солсбери.
В течение четырех дней после утверждения страховой компанией все поврежденное оборудование было снято и отправлено в ремонт.
Страховая компания потребовала вскрытия поврежденной печи перед началом любых ремонтных работ. Судебно-медицинский анализ проводился EMSCO в Аннистоне, штат Алабама, в присутствии персонала страховой компании, а также собрания представителей отрасли из компаний, получивших уведомления о потенциальной суброгации от страховой компании.
Печь Тонкавы была полностью разобрана, в то время как судебно-медицинский инспектор страховой компании руководил, фотографировал, каталогизировал и анализировал каждый поворот каждого болта на печи в течение девятичасового рабочего дня. Змеевик был рассечен, и образцы футеровки были сохранены для использования в будущем.
Хотя печь серьезно пострадала, ее не пришлось заменять полностью.
Произведена структурная реконструкция для устранения повреждений из-за биения в нижней части печи, изготовлен новый змеевик, а гидроцилиндры были переупакованы и герметизированы.К счастью, основные компоненты можно было утилизировать, и в конечном итоге печь была восстановлена за половину стоимости новой печи.
«В печи произошел серьезный технический сбой, — сказал Джимми Хортон, вице-президент и генеральный менеджер по южным операциям, EMSCO. «Однако блок не только был восстановлен, но и восстановлен с использованием минимального количества запасных частей».
Хотя работы на печах продолжались, Тонкава столкнулась с проблемой прогнозируемого срока поставки электроэнергии в 14 недель.
При учете трех недель, потерянных страховой компанией, и времени, необходимого для установки, Тонкава оценил общие производственные потери в 18-20 недель.С точки зрения совладельцев-братьев и сестер Сэнди Солсбери Линтон и Джима Солсбери, Тонкава не смогла бы пережить такой долгий период потери производительности. После того, как они объединились с поставщиком печи, было установлено, что причину длительного ремонта блока питания можно отнести к производителю стального шкафа, в котором размещался блок питания.
Решение? Существующий шкаф будет полностью отремонтирован, и работу будет выполнять Тонкава, а не первоначальный производитель.Это сократило 14-недельное время выполнения заказа до пяти недель.
Tonkawa — единственный источник для ряда своих клиентов. Несмотря на то, что время выполнения заказа было значительно сокращено, команде Tonkawa по-прежнему нужна была стратегия, позволяющая удерживать клиентов из одного источника в бизнесе, а также план по удержанию более крупных клиентов.
Tonkawa разливает множество износостойких высокохромистых сплавов для сельского хозяйства и дробеструйной промышленности. Компания Kansas Castings, Belle Plaine, Kan., Дружественный конкурент, расположена в 50 милях к северу от Тонкавы.Канзас Кастингс предлагал Тонкаве два-три заезда каждую пятницу на столько, сколько было необходимо.
«Мы сделали формы, поместили их на бортовой прицеп, помолились, чтобы в Оклахоме не пойдет дождь, и отвезли формы в Kansas Castings. Каждую пятницу мы производили формовку, дробеструйную очистку, чистку, шлифовку и отгрузку », — сказал Солсбери Линтон.
Другие присоединились к кругу поддержки, которая быстро окружала семью Tonkawa Foundry.
Modern Investment Casting Corporation (MICC) находится в 12 милях к востоку от Тонкавы в Понка-Сити, Окла.Хотя MICC — инвестиционный магазин, а Tonkawa — предприятие по литью в песчаные формы, отношения MICC с Тонкавой восходят к тому времени, когда у руля стоял отец Сэнди и Джима, Джин Солсбери.
«Джин всегда был готов помочь вам», — сказал владелец MICC Дэйв Кэшон. «Его совет был бесценным для нас на протяжении многих лет, поэтому, когда появилась возможность поддержать Сэнди и Джима, мы вызвались помочь».
Компания MICC предлагала каждую пятницу заливать все, что нужно Tonkawa, в ее печь. Tonkawa привезла свой сплав, ручку печи и формы, а MICC предоставила свою печь и ручку печи для трех плавок.Многие специальные детали, которые производит Tonkawa, были изготовлены при поддержке MICC.
Когда Солсбери Линтон подошла к Кэшону и попросила его выставить ей счет на покрытие накладных расходов, которые потребляла Тонкава, Кэшон сказал ей, что если она будет приносить шесть дюжин пончиков каждую пятницу утром, они бы это даже назвали.
«Мы все как одна семья», — сказал Кэшон. «Мы все принадлежим к одной отрасли, и хотя иногда мы можем быть дружественными конкурентами, вы не хотите, чтобы кто-то прошел через то, через что они прошли, и с такой же легкостью наша печь могла выйти из строя.Хотя мы все принимаем соответствующие меры и выполняем техническое обслуживание, чтобы предотвратить возникновение этих сценариев, они, к сожалению, время от времени возникают в нашей отрасли ».
Tonkawa недавно добавила сталелитейные работы в свое меню услуг, а Central Machine & Tool, Энид, Оклахома, смогла взять образцы Тонкавы и выполнить свои заказы на сталь, чтобы не отставать от этих клиентов, в то время как CFM Corporation, Blackwell, Okla., Временно взяли троих сотрудников Тонкавы и заставили их работать во время простоя.Кроме того, несколько основных поставщиков Tonkawa продлили сроки погашения задолженности.
Благодаря поставщикам, друзьям и собственному энтузиазму, настойчивости и самоотверженности сотрудников Tonkawa, бизнес встал, работает и восстанавливается — он входит в число немногих магазинов такого размера, чтобы преодолеть трудности и остаться в бизнесе после столкновения с бедой.
Спустя почти восемь месяцев после того разрушительного субботнего вечера в январе Солсбери Линтон размышлял о людях и событиях, которые помогли Тонкаве воскреснуть из пепла.«У нас, конечно, не было бы возможности увидеть, что ждет Тонкава в будущем, если бы не все добрые люди, которых заботило то, что с нами произошло. Все до сих пор проверяют нас ».