Ламинированная ДСП – что это за материал и для чего он нужен?
Обычные первые плиты ДСП появились еще в 1918 году. Благодаря прогрессу за многие годы материалы стали качественнее, надежнее, в наши дни уже доступны влагостойкие ламинированные доски для производства различной продукции. Существует много видов плит, изготовленных из дерева. К ним относятся МДФ и ЛДСП с разными характеристиками и своими особенностями.
Для того чтобы выбор материала для собственного шкафа или комода был осмысленным, необходимо знать достоинства и недостатки мебельных материалов.
Ламинированные древесностружечные плиты на основе термореактивных полимеров – это основной и часто применяемый материал для производства массовых элементов обстановки в промышленности, также он широко используется в строительстве. Такие плиты достаточно устойчивы к механическим и химическим воздействиям (бензин, ацетон, вода, растворители, спирт, кислота, кофе и другие вещества). Из этого можно сделать вывод, что ЛДСП – отличное сырье для производства медицинской, лабораторной, учебной, бытовой и офисной мебели.
Благодаря своей невысокой стоимости и великолепным строительным свойствам ДСП — самый широко используемый материал для изготовления мебели эконом-класса.
ЛДСП – это представитель старых всем известных древесно-стружечных плит (ДСП) в более шлифованном виде.
ЛДСП – материал, который изготовлен на основе натуральной древесины. Это тот же ДСП, но белее отшлифован, на поверхности которой стойкая меламиновая пленка. То есть главное их отличие – покрытие. Когда она запрессовывается в саму структуру доски – делает ее более влагостойкой и намного прочнее. Это «рыхлое» сырье, его стоимость бюджетная, по дизайну за счет пленки и покрытия можно достичь различных цветовых решений, в том числе и с рисунком натуральной древесины. Он широко используется в производстве корпусных изделий для кухни, офиса, дома, других предметов интерьера дома как основной материал. Из него изготавливают стенды для выставок, мебель для интерьера магазинов, аптек и супермаркетов. С МДФ происходит так же, но при этом такие доски более дорогие.
Большая часть офисной мебели производится именно из ДСП.
Ламинирование плиты ДСП производится различными цветами и разных текстур:
фантазийные векторные декоры;
- геометрия;
- орнаменты;
- однотонные бумаги;
- рисунки и имитация древесины.
Однако есть у этого материала и свои минусы – это вредные формальдегидные выделения.
Декоративная пленка для облицовки пропитывается смолой, она изготовлена из специальной декоративной бумаги, плотностью 60-90 г/м2.
Ламинирование – процесс нанесения декоративного покрытия под действием давления и воздействия температуры.
Ламинирование происходит в прессе. В процессе прессования бумага становится плотнее, по свойствам она наравне с пластиком. Сверху образовывается плотная глянцевая пленка, снизу такая же, но другой структуры — клеевая. Покрытие ламинированных досок достаточно прочное, образуется за счет растекания смолы по всей поверхности ДСП при давлении 25-28 Мпа и температуре 140-210°С. Для производства их ширина не может быть меньше 10 мм, но и не больше 22 мм. При ламинировании из плиты ДСП не выделяются пары альдегида, которые вредны для окружающей среды.
Ламинирование считается более надежным и дорогим способом изготовления ЛДСП.
Она впрессовывается в структуру плиты, делая её более прочной и влагостойкой.
Виды ЛДСП в мебели
Производители по-разному маркируют структуру ЛДСП, но обычно так:
- BS – это офисная;
- SE – дерево с поверхностными порами;
- SM — гладкая поверхность;
- МАТ — матовая гладкая поверхность;
- PR – пористая структура;
- PE – «апельсиновая корка».
Вне зависимости от способа нанесения такое ДСП называется ДСП с меламиновым покрытием.
Для производства чаще всего используются первые две: BS и SE. PR – также популярна, но используется реже, SM используется в производстве внутренних перегородок. Могут встречаться другие маркировки.
Широко используется для изготовления мебели, заполнения двери типа купе и прочих эдементов декора интерьера.
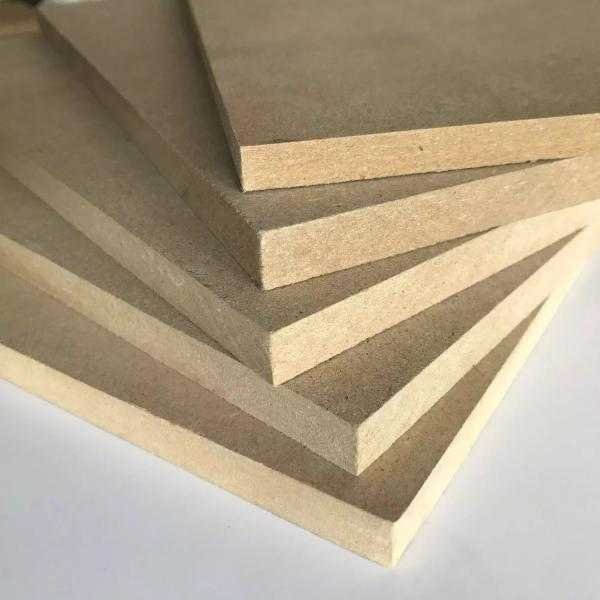
Основные размеры ЛДСП
Существует 18 стандартных показателей длины: 1830, 2040, 2440, 2500, 2600, 2700, 2750, 2840, 3220, 3500, 3600, 3660, 3690, 3750, 4100, 5200, 5500 и 5680 мм. При этом допустимая неточность длины составляет ±5 мм.
Ширина плит ЛДСП определяется 9 показателями: 1220, 1250, 1500, 1750, 1800, 1830, 2135, 2440 и 2500 мм. Как и в случае с длиной, допустимая погрешность не превышает ±5 мм.
Толщина ЛДСП колеблется от 3 до 38 мм при допустимой неточности ±0,3 мм.
Следует уточнить, что в зависимости от возможностей оборудования, каждый производитель выпускает несколько основных размеров ЛДСП, однако самыми популярными на рынке считаются следующие:
- 2800х2620 мм;
- 2800х2070 мм;
- 2620х1830 мм;
- 2500х1830 мм.
Толщина ЛДСП находится в диапазоне от 3 до 38 мм.
Преимущества и недостатки ЛДСП в мебели
Чтобы выбрать хорошее сырье для конкретной мебели необходимо знать его особенности в том числе плюсы и минусы. Любой материал из ДСП изготавливают из опилок и древесной стружки, пропитанных формальдегидной смолой как связующее вещество. ДСП выделяет формальдегид, который плохо сказывается на окружающей среде и здоровье человека, но в ЛДСП есть защитная пленка – ламинированный слой, который не позволяет веществу испаряться из досок.
Многообразие цветов и фактур, имитация фактуры натурального дерева.
Это не пластик, не железо, а все та же всем знакомая древесина.
Чтобы изготовить ламинированную пленку используется бумага определенной фактуры и орнамента. Ее пропитывают меламиновой смолой, вследствие чего та становится определенного уровня жесткости и более рыхлой. Потом под прессом поверхность доски соединяют с пленкой – так образовывается ламинированный лист стандартной толщины.
Устойчивость механическим повреждениям.
ЛДСП достаточно устойчивый материал к механическим и термическим воздействиям с большим ассортиментом фактур и расцветок. Его можно разработать в форме ценной породы дерева. Благодаря устойчивости к высоким температурам на столешницы из этого сырья можно ставить горячую посуду.
Устойчивость к термическому воздействию ( к горячим кофейникам и сковородкам).
ЛДСП – это материалы, изготовленные на основе натурального дерева .
К минусам стоит отнести отсутствие возможности тонкой обработки и наличие формальдегидных смол в составе ДСП, а плюсы в высокой механической и химической устойчивости.
ЛДСП – это представитель старых всем известных древесно-стружечных плит (ДСП) в более шлифованном виде.
Что такое ДСП и технология ее производства
Из чего делают ДСП? Этот композитный материал изготавливается из отходов почти любой древесины: кругляка, сучьев, горбыли, обрези, щепы.
Этапы изготовления ДСП:
- дробление материала на стружку;
- сортировка стружки: для наружных слоев используют более мелкую фракцию, для среднего – более крупную;
- возврат слишком крупной фракции на дополнительное измельчение;
- смешивание подготовленной стружки с клеем и формирование ковра, уплотняемого прессом.
Полученные листы охлаждают, шлифуют и режут на требуемые куски. Стандартные варианты – 2,22х1,22, 2,44х1,83, 2,75х1,83, 2,8х2,07 м. Толщина материала – 10, 16, 18, 22, 25 мм.
Мебель из МДФ — что это такое?
МДФ – улучшенная технология производства ДСП материалов. Доска состоит из мелких спрессованных фракций опилок. Благодаря такому способу скрепления материал получается высокопрочным, однородным и безвредным для здоровья. Благодаря этим показателям он может использоваться для производства любой мебели, в том числе и для детской комнаты. Стоимость его немного выше.
Основное отличие ЛДСП от ДСП – это покрытие Она впрессовывается в структуру плиты, делая её более прочной и влагостойкой.
Основными плюсами является высокая прочность плит, однородность, легкость обработки, влагостойкость, антидеформационные способности, широкий ассортимент и красивый дизайн.
МДФ довольно плотный материал – это делает его незаменимым в производстве мебели требующей вытачивания изящных линий, округлостей и пр.
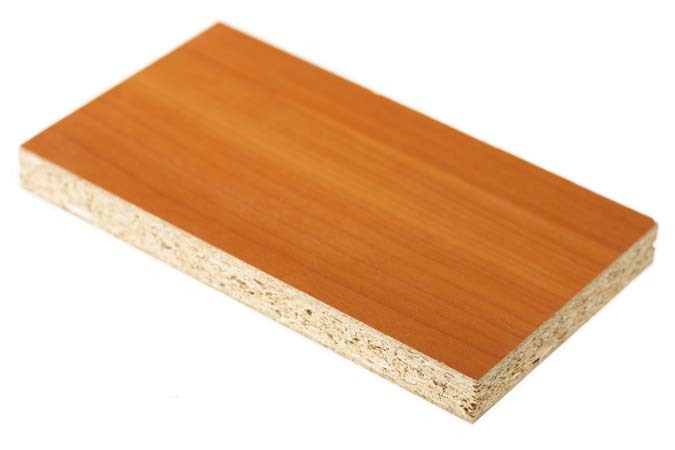
Минусы: высокая цена, доски боятся механических повреждений и ударов, легко воспламеняются.
МДФ является экологичным материалом и не имеет ограничений по применению.
Виды ламинированных древесно-стружечных плит
Существует около полутора десятком особенностей, наличие или отсутствие которых определяют вид ЛДСП, мы обозначим четыре основных.
Особенность конструкции
- если толщина ламинированной древесно-стружечной плиты не превышает 1 сантиметра – это однослойная ЛДСП, которая может применяться для изготовления различного вида декоративных панелей;
- если толщина ламинированной древесно-стружечной плиты достигает 2 сантиметров – это трехслойная ЛДСП, которая активно используется для производства корпусной мебели;
- если толщина ламинированной древесно-стружечной плиты варьируется от 2 до 4 сантиметров – это многослойная ЛДСП, из которой могут производить напольное покрытие.
Количество смол
Исходя из количества формальдегидных смол, которые были использованы при производстве плит, ЛДСП можно разделить на 2 класса. Как правильно расшифровать их аббревиатуру?
- Класс Е1 – ЛДСП будет относиться к данному классу, если в 100 граммах готовой продукции будет содержаться не более 10 миллиграмм смол;
- класс Е2 – ЛДСП будет относиться к данному классу, если в 100 граммах готовой продукции будет содержаться до 30 миллиграмм формальдегидных смол.
Сорт ЛДСП
Определяющим фактором при распределении ЛДСП на сорта, является наличие (или отсутствие) каких-либо дефектов.
- 1 сорт – если дефектов на плитах не обнаружено;
- 2 сорт – если при осмотре было обнаружено несколько поверхностных дефектов;
- 3 сорт – если при осмотре было обнаружено значительное количество внешних дефектов, а также наличие явных или скрытых внутренних дефектов.
Технология ламинирования
Покрывать древесно-стружечную плиту пленкой можно с применением трех разных технологий.
- Ламинирование
. При использовании данной технологии на подготовленную древесно-стружечную основу наносят три слоя специальной бумаги: первый слой – толстый (до 1 миллиметра), в последующем он используется для нанесения какого-либо рисунка, второй – тонкий, его толщина не превышает десятой доли миллиметра.Третий слой – это прозрачная бумага, сверху покрытая слоем из смеси смол. С помощью термической обработки, третий слой образует прочную защитную пленку. При ламинировании исключено использование любого вида клея, его функции берет на себя смесь смол.
- Каширование
. В отличие от ламинирования, при кашировании требуется одновременная подготовка всех слоев изделия, которые пропитываются смесью смол и, в нужном порядке, стыкуются друг с другом. Нанесение рисунка достигается при использовании холодного пресса, от воздействия которого смола всех слоев изделия смешивается. В результате получается широкая и длинная лента, которая подвергается предварительной сушке, а затем еще раз подогревается и прессуется. К сожалению, нельзя не признать, что пленка, после технологии каширования уступает по качеству той пленке, которая была изготовлена с помощью технологии ламинирования. - Гладкое ламинирование.
В отличие от простого ламинирования это технология не предполагает нанесения на поверхности изделия рисунка.Кроме того поверхность состоит только из двух слоев: первый – бумажный, второй – состоит из пленки специального состава, которая под воздействием температуры преобразуется в гладкое и достаточно прочное покрытие.
Как правильно выбрать ЛДСП?
На сегодняшний день существует немалое количество ДСП разного назначения. Их отличия заключаются в толщине, составе, износоустойчивости, плотности. Такие особенности связаны с использованием в разных областях производства плит. Существует стереотип о плотности плиты. Считается, чем она плотнее, тем лучше. Но это не совсем так. Плюс этих досок — в бюджетном сырье (низкосортной древесине). К ней относятся «тонкомеры», горбыль, рейки. Главное, чтобы эти материалы отвечали следующим стандартам.
- Фракции стружки не должны быть мелкими.
- Сечение стружки должно быть квадратным, а форма лепестковая. Если нарушить эти требования физико-химические свойства готовой плиты ухудшатся (пострадают изгиб и сопротивление).
ЛДСП имеет широкую цветовую гамму, что широко используется при производстве корпусной мебели.

Часто потребители задаются вопросами: что это за материал такой для кровати — МДФ? Чем отличается МДФ от ЛДСП для мебели? Рассмотрим эти нюансы подробнее.
Пленка представляет собой бумагу, пропитанную меламиновыми смолами, поэтому часто можно встретить и такой термин, как «меламиновая плита».
Преимущества ДСП:
- низкая цена;
- не рассыхается, не расслаивается, не плесневеет;
- благодаря химическим добавкам в плите не живут жучки;
- срок эксплуатации более 10 лет.
Плюсы МДФ:
- приемлемая цена для потребителей со средними доходами;
- прочность;
- влагостойкость;
- включает все вышеперечисленные плюсы ДСП.
ЛДСП можно мыть и чистить — он влагоустойчив.
Выбор материала зависит от того, что планируется изготовить. ЛДСП можно использовать в изготовлении мебели, предназначенной для офиса, дома, магазина, супермаркета. МДФ лучше выбрать для детской мебели.
Высокие температуры ему также не страшны.

Производство древесноволокнистых плит позволяет изготавливать продукцию по доступным ценам для различных интерьеров. Благодаря мебели МДФ и ЛДСП каждый дом будет наполнен уютом, теплом и комфортом.
Его достоинством, помимо всего вышеперечисленного, считается его великолепная возможность имитировать различные текстуры, чаще всего – имитация фактуры дерева.
Обращайте внимание на нормы содержания формальдегида в корпусной мебели.
Обзор производителей ЛДСП
Сегодня не составит труда найти ЛДСП в широком разнообразии. Чтобы иметь представление о предложении, стоит ознакомиться с основными производителями.
Эггер
Эта марка находится на почетном месте во всем своем сегменте, и ее продукция существует на рынке, начиная с 1961 года. Компания постоянно расширяет ассортиментный ряд и совершенствует производственную технологию. Она изготавливает не только ЛДСП, но и кромки, столешницы. Все изделия имеют презентабельный внешний вид и служат очень долго. В составе отсутствуют вредные химические вещества.
Эггер
Кроношпан
Это предприятие является наиболее крупным на территории Украины и всей Европы. Оно предлагает большой выбор листовых материалов, изготовленных с использованием древесины, а именно – ДСП ламинированного и шлифованного типа. Работает с 2004 года в г. Нововолынске, хотя деятельность начиналась в 1897 году в Австрии.
Кроношпан
Ламарти
Бренд производит экологически чистый материал, соответствующий стандартам качества России и Европы. Все продукты отличаются высоким уровнем надежности и технологичности, 70% позиций – полностью уникальны.
Ламарти
Невский Ламинат
Завод работает в Санкт-Петербурге и предлагает огромный выбор материалов для основ и тиснений ЛДСП. В каталоге представлены также вариации МДФ и ВДСП различной толщины.
Невский Ламинат
ЛДСП в мебели: 50 фото-идей
ПредыдущаяДругоеФункциональный элемент декора – чехлы на стулья
Следующая
ДругоеМебельный воск: виды, применение, как правильно использовать.
Отличия данного материала от ламината и МДФ
Несмотря на то, что ЛДСП часто называют ламинатом, это не совсем верно, ведь ламинат – это общее название целого класса отделочных плит, изготовленных из различных материалов.
Ламинированную ДСП, предназначенную для чистовой обшивки потолка или чистового покрытия пола, можно заменить ламинированной плитой из МДФ, а вот произвести такую замену в отношении плит для мебели невозможно.
Ведь MDF сопоставима с ЛДСП по стойкости к сдавливанию, но не обладает необходимой прочностью на изгиб и не может удерживать шурупы. Поэтому, выбирая материал для каких-то работ, необходимо помнить – ламинат, это общее название отделочных материалов, покрытых специальной пленкой.
Могут ли использовать гриф ДСП коммерческие организации
Гриф для служебного пользования, с точки зрения нормативов действующего российского законодательства, рассматривается исключительно в отношении отдельных государственных служб. Таким образом, использовать данную пометку в своей деятельности негосударственные организации, как коммерческие, так и некоммерческие, не могут. В то же время, в рамках ведения коммерческой деятельности все же предусмотрены механизмы ограждения различной конфиденциальной информации от посторонних. В частности, основными подобными механизмами являются:
Коммерческая тайна. Если субъект хозяйствования обладает какой-либо информацией, доступ к которой позволяет ему получать прибыль, или может привести к определенным убыткам при ее разглашении, то такая информация может быть отнесена к коммерческой тайне и находиться под защитой со стороны российского законодательства.- Персональная информация. Доступ к чьим-либо персональным данным в российском законодательстве строго регламентирован, и информация, содержащая их, не может находиться в открытом доступе в принципе, за исключением отдельных, строго определенных случаев.
Нарушение порядка обработки персональных данных также может привести к привлечению к ответственности.
Непосредственно же применение грифа ДСП к документам, которые субъект хозяйствования не хочет допускать к использованию третьими лицами законом не предусмотрено, если этот субъект не относится к государственным структурам. Таким образом, применение такого грифа к документации может привести к следующим негативным последствиям:
- Отсутствие законодательной защиты. Если вместо грифа коммерческой тайны на документ, содержащий подобную информацию, будет нанесен гриф ДСП, то данный документ может быть не признан коммерческой тайной, а значит и никакой ответственности за его разглашение никто не понесет.
- Уголовное или административное преследование. В отдельных случаях, использование данного грифа может привести к квалификации данного действия со стороны негосударственной организации или физического лица в качестве подозреваемого в совершении мошенничества или присвоения полномочий.
Ламинированный ДСП: производство, виды, применение |
Всем знаком такой материал как ДСП, он используется с незапамятных времен. Но прогресс не стоит на месте, и все популярные материалы совершенствуются и обретают новые положительные качества и характеристики. Одним из таких материалов является усовершенствованный вариант плит ДСП — ЛДСП. Попробуем разобраться, что это за материал и чем он лучше старого-доброго ДСП.
ЛДСП или ламинированный ДСП — это разновидность композиционного материала обработанного с помощью ламинации. Такая себе модификация всем известных древесно-стружечных плит, с более совершенными характеристиками.
Процесс производства ЛДСП включает в себя несколько этапов:
— производство ДСП путем горячего прессования древесной стружки смешанной с различными связующими добавками не минерального происхождения. Чаще всего в качестве связки используют формальдегидную смолу;
— ламинирование древесно-стружечных плит.
В случае с ЛДСП для ламинации используют бумагу пропитанную меламиновой смолой, импрегнат. Ее наносят на поверхность доски с помощью пресса давление, в котором составляет более 25 Мпа и при температуре 150-200 градусов. При таких показателях смола растекается по всей поверхности доски и уплотняется, по своим параметрам приближается к пластику.
Таким образом, на поверхности ДСП образуется прочная глянцевая пленка, которая существенно улучшает внешний вид и характеристики материала.
Характеристики ЛДСП
Благодаря способу производства ламинированный ДСП имеет ряд положительных характеристик, которые выгодно отличают этот материал от других композиционных материалов.
Достоинства ЛДСП:
— высокая прочность. ЛДСП благодаря своей структуре имеет показатели прочности выше, чем у некоторых пород древесины. Может выдерживать большие нагрузки, стойкий к излому;
— высокая влагостойкость. Ламинированный ДСП благодаря верхнему слою имеет гораздо высокую сопротивляемость влаге, чем обычные плиты ДСП, для которых влага очень плохо влияет;
— выдерживает высокие температуры. На поверхности плит ЛДСП не остаются следы от горячей посуды, покрытие не растрескивается, не плавится;
— выпускается в разнообразных цветах и с нанесением узоров. Это позволяет применять плиты ЛДСП в интерьерах с абсолютно разнообразным дизайном;
— долговечность и износостойкость. Ламинированный ДСП прослужит вам при правильном уходе не менее 10 лет;
— невысокая стоимость.
— практичность. Благодаря своим механическим и эстетическим характеристикам плиты ЛДСП имеют очень широкий диапазон применения, с ними просто работать и просто ухаживать за готовыми изделиями.
Недостатков у этого материала не много, но все же они есть, и промолчать о них было бы не честно.
Недостатки ЛДСП:
— наличие в составе материла смол формальдегида. Этот компонент, используемый в качестве связки составляющих в плите, нельзя назвать экологичным и безопасным для окружающей среды и здоровья человека в частности. Но есть и положительная сторона: благодаря наличию в ЛДСП прочной пленки на поверхности пары формальдегида выделяются гораздо меньше чем из обычного ДСП.
— невозможность вытачивать из ЛДСП фигурные детали и глубоко фрезеровать. ЛДСП достаточно хрупкий при обработке материал и при распиливании на мелкие детали может крошиться и ломаться.
Виды ЛДСП
Существует множество разновидностей ЛДСП. Они разделяются по маркам, сортам, конструкционным особенностям, техническим характеристикам, вариантам обработки ит.д.
По особенностям конструкции выделяют:
— однослойная ЛДСП. Толщина такой доски составляет не белее 1 сантиметра. Такой вид ламинированной ДСП используют чаще в его в качестве декоративных панелей;
— трехслойная ЛДСП. Толщина — до двух сантиметров. Используется в мебельной промышленности;
— многослойная ЛДСП. Толщина — от двух до четырех сантиметров. Чаще всего используется в качестве напольного покрытия или в строительстве.
По количеству смол формальдегида ЛДСП делят на классы:
— Е1 — содержание смолы в ста граммах сухой плиты не более 10 мг;
— Е2 — содержание смолы до 30 мг на 100 грамм плиты.
По количеству дефектов плиты ЛДСП делят на сорта:
— I — полное отсутствие дефектов
— II — наличие нескольких незначительных, не грубых дефектов;
— III — количество дефектов не ограничено.
По разновидности наружного слоя выделяют такие виды ЛДСП:
— мелкоструктурная;
— обычная;
— крупнозернистая.
По степени обработки ЛДСП бывают:
— шлифованные;
— не шлифованные.
Применение ЛДСП
Область применения плит ЛДСП очень широка. Такой материал может быть использован во всех сферах жизнедеятельности человека.
Использование ЛДСП возможно в строительстве, ремонте и отделке помещений как жилых, так и офисных, для производства мебели.
Благодаря своим характеристикам область использования ЛДСП значительно шире, чем область применения дерева.
Благодаря влагостойкости ЛДСП успешно используется в ванных комнатах и других помещениях с высокой влажностью.
Благодаря высокой прочности к механическим повреждениям из плит ЛДСП производят напольное покрытие.
ЛДСП обладает высокой стойкостью к высоким температурам это дает возможность использовать этот материал в качестве столешниц и другой кухонной мебели. На ней не будет следов от горячей посуды.
Из ЛДСП изготавливают красивую и прочную мебель, как для офисов, так и для квартир. Производят разное торговое оборудование. Например, витрины и прилавки.
Ирина Железняк, Собкор интернет-издания «AtmWood. Дерево-промышленный вестник»
Ламинированная ДСП (ЛДСП) что это, где используется
Ламинированная ДСП – один из наиболее популярных и распространенных плитных материалов для мебельного производства и интерьерных отделочных работ. Плиты МДФ немного потеснили ЛДСП в данной нише, но этот материал по-прежнему остается востребованным за счет хорошего соотношения цены, эксплуатационных и декоративных характеристик.
Что такое ламинированная ДСП
Ламинированная древесно-стружечная плита, сокращенно ЛДСП – это плитный материал, который получают путем прессования ковра из смеси древесной стружки со смолами с последующим нанесением ламинирующего защитно-декоративного покрытия. Стружку предварительно просушивают, очищают от примесей, сортируют по размеру, перемешивают со смолой до получения однородной массы и формируют ковер, обычно из 3 слоев. На внешние слои ЛДСП пускают стружку более мелкой фракции, в результате образуется мелкоструктурная поверхность, которая лучше поддается шлифовке. Ковер подвергают сначала холодному, затем горячему прессованию, масса уплотняется, а смола под действием высоких температур твердеет, в результате получается достаточно прочная плита.
После охлаждения ее шлифуют и на отшлифованную поверхность накладывают меламиновую пленку – бумагу, пропитанную термореактивной смолой. Плиту еще раз подвергают давлению и нагреву, термореактивные компоненты меламиновой пленки плавятся и склеивают покрытие с основанием, а благодаря давлению их сцепление получается максимально надежным. Иногда плита пресса имеет рельефную рабочую поверхность для создания тиснения на ламинированном покрытии.
Виды ЛДСП
В соответствии с ГОСТ от 2014 года ЛДСП классифицируются по таким критериям:
- группы качества (зависят от физико-механических свойств ДСП-основы) – плиты группы А более прочные, лучше сопротивляются деформациям на изгиб и растяжение, а также отличаются сниженным водопоглощением, менее подвержены разбуханию и короблению в условиях высокой влажности.
ЛДСП группы Б уступают им по этим характеристикам, а группы У (улучшенные) – превосходят;
- класс эмиссии, который определяется содержанием формальдегидных смол в плите и уровнем их выделения в воздух;
- сорт (качество покрытия) – покрытие ЛДСП I сорта практически не имеет дефектов, во II сорте они допускаются;
- особенности декоративного покрытия, такие как степень блеска (глянцевые и матовые), характер декора (однотонный или с рисунком), текстура (гладкая/рельефная).
Также различают ЛДСП с односторонней и двусторонней облицовкой, последние могут быть с одинаковой облицовкой обеих пластей и с разной (I/II сорта).
Ассортимент ЛДСП разнообразен, рисунок может имитировать природные материалы, чаще всего разные породы древесины, реже – камень, также бывает фантазийный, в виде орнамента. Набор текстур не так богат – шагрень (под кожу), под дуб, апельсиновая корка (пупырчатая), пористая. У зарубежных производителей свои критерии классификации. Так, в ГОСТе упоминается только 2 класса эмиссии: Е2, максимально допустимый на сегодняшний день, и Е1, считается минимальным. В то же время, в некоторых странах ЛДСП класса Е2 уже снята с производства, а ряд производителей предлагает плиты с эмиссией Е0,5 и даже Е0. В них содержание смол, а значит, и их эмиссия (выделение из плиты в воздух) настолько низкое, что не представляет ни малейшей угрозы для здоровья. Также стоит упомянуть, что на рынке стройматериалов можно встретить ЛДСП, уровень эмиссии которых превосходит Е2. Поэтому не следует покупать ЛДСП сомнительного происхождения, без сертификата, в котором указан класс эмиссии.
Преимущества и недостатки ламинированной ДСП
У ЛДСП есть немало достоинств:
- довольно доступная цена, поскольку для изготовления используются отходы деревоперерабатывающей промышленности, некондиционная древесина;
- достаточно высокая прочность, устойчивость к механическим нагрузкам, присущая плитам ДСП;
- простота обработки, раскроя;
- за счет содержаниям смол в составе плиты хорошо противостоят гниению, биопоражениям;
- ламинация обеспечивает дополнительную защиту от механических повреждений и проникновения влаги в структуру плиты;
- покрытие препятствует эмиссии смол, если дополнительно закрыть кромками все открытые срезы на торцах, можно свести ее к минимуму.
То есть материал более безопасный, чем обычная ДСП;
- ЛДСП хорошо выдерживают высокие температуры;
- мебель и отделка из ЛДСП неприхотлива к уходу;
- плиты и изделия из них привлекательно выглядят, ламинация может имитировать ценные породы древесины.
Не лишен материал и ряда недостатков:
- нанесение покрытия повышает стоимость ДСП;
- ДСП не относится к водостойким материалам, в случае нарушения целостности покрытия, при наличии незакрытых срезов в условиях высокой влажности, продолжительного контакта с водой плиты разбухают, деформируются, начинают разрушаться;
- ЛДСП более прихотлива к обработке, чем плита без покрытия. При недостаточно аккуратном раскрое возможны сколы ламинации, поэтому его лучше выполнять на профессиональном оборудовании;
- ЛДСП нельзя фрезеровать, вырезать из нее фигурные, криволинейные детали крайне сложно, и кромка таких деталей обычно разрушается;
- плиты содержат формальдегидные смолы, поэтому их нельзя назвать абсолютно безопасными для окружающей среды и здоровья человека.
Что лучше: ЛДСП или МДФ
МДФ, плитный материал, спрессованный из древесных волокон мелкой фракции, в последнее время составляет достойную конкуренцию ЛДСП, применяется в тех же сферах. Оба материала относятся к древесным плитам, но различаются составом и структурой. Плиты ЛДСП состоят из относительно крупных элементов (стружки), поэтому структура недостаточно однородная, возможны перепады плотности, неровности поверхности под покрытием. МДФ состоит из компонентов мелкой фракции, что обеспечивает максимальную однородность структуры, более высокую плотность, открывает широкие возможности механической обработки. Различается также технология прессования и вид связующего древесных компонентов.
Сравнивать МДФ и ЛДСП не вполне корректно, поскольку плиты МДФ могут быть шлифованными без декоративного покрытия, а также ламинированными, шпонированными, окрашенными эмалями, а ЛДСП – это декорированная древесно-стружечная плита. Правильнее сравнивать между собой ДСП и МДФ без покрытия или ЛДСП и МДФ с ламинацией.
Параметр сравнения | Оценка по 5 бальной шкале ЛДСП/МДФ | ЛДСП | МДФ |
---|---|---|---|
Ценовая категория (доступность) | 5/2,5 | Бюджетная | Средняя |
Влагостойкость | 2/3 | Умеренная | Более высокая, даже при повреждении защитного покрытия плита может сопротивляться проникновению влаги |
Плотность и прочность | 3,5/5 | 350-650 кг/м3 хорошая | 720-870 кг/м3 отличная |
Огнестойкость | 3/2 | Горючий материал | Более горючий в сравнении с ЛДСП материал |
Состав, экологичность, безопасность | 3/4 | Содержит токсичные формальдегидные смолы | Содержит парафин, лигнин или карбамидные смолы, более безопасные для здоровья и экологии |
Способы обработки | 2,5/5 | Раскрой по прямой | Прямой и фигурный рез, фрезеровка |
Чистота реза | 2,5/5 | Удовлетворительная, возможны сколы | Отличная за счет однородной структуры |
Способность держать крепеж | 2/4,5 | Крепеж может расшатываться, повторное завинчивание в ту же точку после вывинчивания проблематично, плита крошится | Крепеж хорошо держится, материал выдерживает вывинчивание-завинчивание |
По большинству эксплуатационных характеристик ЛДСП уступает МДФ, разве что горючесть древесно-стружечных плит ниже, но незначительно. Основное достоинство ЛДСП в сравнении с ламинированной МДФ – более доступная стоимость. В мебельном производстве их часто комбинируют, фасады изготавливают из МДФ с ламинацией или другими видами декоративных покрытий, а корпуса, полки – из ЛДСП.
Где используется ламинированная ДСП
Основные сферы применения ЛДСП – мебельное производство и отделка помещений. В частности, из нее изготавливают:
- бытовую мебель для помещений с нормальной влажностью – корпуса, фасады, полки шкафов, тумб, комодов, столы, книжные полки и небольшие полочки. Для детской мебели, как правило, используют ЛДСП класса эмиссии Е1 и ниже;
- кухонные гарнитуры, столешницы. Для этих целей предпочтительней ЛДСП на основе ДСП повышенной влагостойкости;
- офисную мебель и оборудование;
- торговое, выставочное оборудование;
- стеновые и потолочные декоративные панели.
Помимо готовых панелей в интерьерных работах находят применение целые плиты ЛДСП, которые разрезают на элементы нужного размера и используют для обшивки стен, внутренних перегородок.
Особенности работы с ЛДСП
ДСП достаточно легко поддается механической обработке, но при распиле ламинированных плит высок риск образования сколов покрытия и его растрескивания возле линии реза. Чтоб этого избежать, необходимо:
- использовать режущий инструмент с максимально мелкими, частыми зубцами, диск к циркулярной пиле желательно выбирать разработанный специально для раскроя ЛДСП, он отличается уменьшенным наклоном твердосплавных зубцов;
- при работе ручной ножовкой располагать режущее полотно под острым углом к поверхности, выполнять плавные движения без сильного нажима;
- если раскрой осуществляется электролобзиком или циркулярной пилой, установить минимальную рабочую скорость подачи полотна/низкие обороты диска;
- циркулярную пилу рекомендуется комплектовать вспомогательным приспособлением – направляющей рейкой;
- вдоль намеченной линии распила наклеить полоску малярного скотча, который защитит ламинацию от растрескивания, раскалывания;
- предварительно провести по линии распила острым ручным инструментом (шилом, ножом), чтоб на ламинации образовался небольшой паз, тогда ножовка или электролобзик не будут отклоняться от намеченной линии.
В случае работы циркулярной пилой с направляющей сначала прорезать паз глубиной 3 мм, затем выполнять пропил на всю толщину плиты.
Если необходимо выполнить фигурный рез ЛДСП в домашних условиях, без профессионального форматно-раскроечного станка, используется портативная ручная электрофреза. Предварительно нужно с помощью электролобзика вырезать из обычной ДСП шаблон чуть меньшего размера, чем нужная деталь (отступ от края 1-2 мм). Шаблон приложить к заготовке из ЛДСП, зафиксировать струбцинами и пройтись по контуру фрезой.
После окончания раскроя с помощью любого инструмента необходимо обработать срез сначала напильником, затем наждачной бумагой. После зачистки, устранения неровностей сразу закрыть его кромкой или мебельным профилем.
Если в ЛДСП необходимо ввинтить крепеж, рекомендуется предварительно просверлить направляющее отверстие, это предотвратит растрескивание материала. Крупный крепеж желательно ввинчивать на расстоянии минимум 5 см от края. В случае демонтажа мебели или других сборных конструкций из ЛДСП при повторной сборке тот же крепеж не будет держаться в старых отверстиях, решением проблемы станет использование шурупов, болтов большего диаметра.
При работе с ЛДСП следует позаботиться о защите органов дыхания и глаз от пыли, помимо респиратора и защитных очков рекомендуется использовать перчатки.
ЛДСП: коротко о главном
Ламинированная древесно-стружечная плита – востребованный материал для изготовления недорогой мебели, обшивки стен, потолков и перегородок. Большой выбор цветов и текстур ламинации позволяет реализовать разные дизайнерские проекты. Для жилых помещений, детской мебели рекомендуется использовать ЛДСП класса эмиссии Е1 и ниже. Ламинированные плиты подходят для изготовления кухонной мебели, но необходимо закрыть все срезы, через которые в плиту может проникать влага, и не допускать повреждений покрытия. Раскрой ЛДСП своими руками представляет некоторую сложность, чтоб избежать лишних хлопот и гарантировано получить чистый рез без сколов, лучше заказать услуги профессионального раскроя ЛДСП.
Физико-механические свойства ДСП, ламинированной термопрессованным шпоном :: Биоресурсы
Буюксари, У.
Abstract
Целью данного исследования было изучение влияния ламинирования термически спрессованным шпоном на некоторые физические и механические свойства древесно-стружечных плит. Бук восточный ( Fagus orientalis Липский шпон прессовали в различных условиях прессования. Такими прессованными листами шпона ламинировали серийно выпускаемые образцы ДСП. Измеряли плотность, 2-часовое и 24-часовое водопоглощение (WA) и набухание по толщине (TS), прочность на изгиб (MOR) и модуль упругости (MOE) в параллельном и перпендикулярном направлениях к ориентации зерен. Результаты показали, что все древесностружечные плиты, ламинированные прессованным шпоном, имели более высокие значения MOR и MOE по сравнению с неламинированными древесно-стружечными плитами и ламинированными непрессованными шпонами. В сэндвич-панелях ламинированные листами шпона ДСП, спрессованные при давлении 4 МПа и температуре 150 оС, имели самые высокие значения МОС и МОС.
Скачать PDF
Статья полностью
ФИЗИЧЕСКИЕ И МЕХАНИЧЕСКИЕ СВОЙСТВА ДСП, ЛАМИНИРОВАННОЙ ТЕРМОПРЕССОВАННЫМ ШПОНОМ
Умит Буюксари а, *
Целью данного исследования было изучение влияния ламинирования термически спрессованным шпоном на некоторые физические и механические свойства древесно-стружечных плит. Бук восточный ( Fagus orientalis Lipsky) шпона прессовали в различных условиях прессования. Такими прессованными листами шпона ламинировали серийно выпускаемые образцы ДСП. Измеряли плотность, 2-часовое и 24-часовое водопоглощение (WA) и набухание по толщине (TS), прочность на изгиб (MOR) и модуль упругости (MOE) в параллельном и перпендикулярном направлениях к ориентации зерен. Результаты показали, что все древесностружечные плиты, ламинированные прессованным шпоном, имели более высокие значения MOR и MOE по сравнению с неламинированными древесно-стружечными плитами и ламинированными непрессованными шпонами. В сэндвич-панелях ДСП, ламинированные листами шпона и спрессованные при давлении 4 МПа и температуре 150 o C имели самые высокие значения MOR и MOE. Значения MOR и MOE уменьшались с повышением температуры выше 150 o C. Значение TS для 2-часового и 24-часового времени погружения уменьшалось с увеличением температуры прессования. Результаты этой работы могут дать некоторое представление о производстве сэндвич-панелей с улучшенными свойствами. Представляется, что прессование шпона с использованием различных температур и давлений прессования можно рассматривать как альтернативный способ разработки сэндвич-продуктов с удовлетворительными структурными свойствами.
Ключевые слова: ДСП; ламинирование; Термическое сжатие; Отек толщины; Впитывание воды; Модуль упругости; Прочность на изгиб
Контактная информация: a: Кафедра механики и технологии древесины, Университет Дюздже, Дюздже, Турция * Автор, ответственный за переписку: [email protected]
ВВЕДЕНИЕ
Процессы термического сжатия уже много лет используются в различных приложениях (Бехта и др., 2009 г.).; Унсал и Кандан, 2008 г.; Кандан и др. 2010). Общеизвестно, что сжатие древесины может положительно сказаться на общих прочностных свойствах изделий из дерева; это важно в отношении конструкционных применений, в которых желательны более высокие механические свойства (Wood Handbook 1999). В предыдущем исследовании была предпринята попытка оценить прочностные характеристики фанеры, изготовленной из непрессованного и прессованного шпона (Бехта и др., 2009). Эти авторы констатировали, что все измеренные прочностные характеристики увеличивались с увеличением степени сжатия от 5% до 15%. Увеличение степени сжатия приводит к снижению прочности на изгиб. В другом исследовании сжатие японского кедра (9Было показано, что образцы 0004 Cyrotomeria japonica ) влияют на прочностные характеристики (Adachi et al. 2009). Kamke (2006) исследовал свойства на изгиб LVL, изготовленного из прессованного и непрессованного шпона лучистой сосны. Он обнаружил, что LVL, изготовленный из прессованного шпона, имеет более высокое значение модуля упругости (MOE) по сравнению с LVL, изготовленным из непрессованного шпона. Кутнар и др. (2008) сообщили, что соответствующие значения модуля разрыва (MOR) и MOE для трехслойных композитов составляют 64,0 МПа и 8,2 ГПа для несжатых композитов и 87,0 МПа и 12,1 ГПа для сжатых композитов.
В дополнение к улучшению механических свойств изделий из древесины качество поверхности также может быть улучшено в результате процессов прессования. Уплотнение древесины вызывает сжатие любых неровностей на подложке, в результате чего поверхность становится более гладкой. Фауст и Райс (1986) определили, что использование более грубого шпона при производстве LVL снижает прочность на изгиб в среднем на 33% по сравнению с LVL, изготовленным из более гладких листов шпона. В частности, листы шпона с более гладкой поверхностью, используемые в фанере и клееном брусе (ЛВЛ), снижают расход клеевого состава, что снижает общую стоимость производства.
ДСП является одной из наиболее широко используемых внутренних древесных композитных подложек и обычно используется для производства краснодеревщиков и мебели. Массив шпона также используется в качестве грунтовки под ДСП при изготовлении дорогой мебели. Древесина бука широко используется для ламинирования подложки для древесных плит во многих европейских странах. Ламинированные древесностружечные плиты из прессованного шпона могут использоваться для различных структурных применений. Целью данного исследования было оценить MOR, MOE, набухание по толщине (TS) и водопоглощение (WA) экспериментально изготовленных панелей с использованием таких структур.
ЭКСПЕРИМЕНТАЛЬНЫЙ
Бук восточный ( Fagus orientalis Lipsky) листы шпона толщиной 1,5 мм, изготовленные методом ротационного лущения, и серийно выпускаемые панели из ДСП толщиной 18 мм были разрезаны на квадраты размером 500 мм на 500 мм. Виниры с влажностью 12% и плотностью 3 0,630 г/см прессовали с помощью горячего пресса лабораторного типа. Всего для каждого испытания прессовали 4 образца шпона. Толщина каждого шпона была измерена в четырех углах с точностью до 0,01 мм до и после сжатия, чтобы определить уменьшение толщины в зависимости от давления и температуры. ДСП ламинировали контрольным (непрессованным) и прессованным шпоном с использованием карбамидоформальдегидного клея в количестве 160 г/м 9 .0022 2 . В клеевую смесь также добавляли хлорид аммония (NH 4 Cl) в количестве 1% в расчете на сухую массу древесины. Сэндвич-панели с двумя листами шпона прессовали в горячем прессе с компьютерным управлением. Перед проведением испытаний образцы кондиционировали в климатической камере при температуре 20 900–22 o С и относительной влажности 65 % в течение трех недель.
Испытания на плотность (на основе EN 323), испытания на водопоглощение и набухание по толщине (на основе EN 317) и испытания на изгиб (на основе стандарта EN 310 на универсальной испытательной машине, оснащенной тензодатчиком, рассчитанным на 1000 кг). Ламинированные и неламинированные образцы для испытаний на изгиб показаны на рис. 1.
Рис. 1. Ламинированные и неламинированные образцы для испытаний на изгиб
Всего для каждого теста было использовано 20 образцов. Схема эксперимента, параметры сжатия шпона и производства сэндвич-панелей представлены в таблице 1. Полученные данные были подвергнуты статистическому анализу с использованием дисперсионного анализа (ANOVA) и критерия среднего разделения Дункана.
Таблица 1. Экспериментальный дизайн , параметры сжатия шпона и производства сэндвич-панелей
РЕЗУЛЬТАТЫ И ОБСУЖДЕНИЕ
Величина уменьшения толщины виниров после прессования показана в Таблице 2. В группе H было самое большое уменьшение, а в группе C — самое низкое. Уменьшение толщины увеличивалось с увеличением давления прессования и температуры. Аналогичные результаты были получены несколькими исследователями (Унсал и др., 2009, 2011; Вельцбахер и др., 2008; Табарса и Чуи, 1997; Рауткари и др., 2010). Унсал и др. (2009) установили, что уменьшение толщины древесины сосны, спрессованной при 150 ºC, составило 4,7 % при давлении прессования 5 МПа и 38,8 % при 7 МПа. Рауткари и др. (2010) обнаружили, что коэффициент сжатия (уменьшение толщины) увеличивается с увеличением давления прессования в древесине бука и ели. Степень сжатия древесины ели в тангенциальном направлении составила 2,7% при низком давлении и 7,1% при высоком давлении. Вельцбахер и др. (2008) и Табарса и Чуй (1997) установили, что толщина образцов древесины уменьшается с увеличением температуры уплотнения. Это явление можно объяснить как следствие размягчения твердой древесины при повышении температуры.
Таблица 2. Уменьшение толщины виниров
Результаты тестов ANOVA и среднего разделения Дункана для плотности, WA и TS панелей приведены в таблице 3. Плотность многослойных панелей была выше, чем плотность панелей из неламинированного ДСП. За исключением групп G и H, панели, ламинированные непрессованным шпоном, имели меньшую плотность по сравнению с панелями, ламинированными прессованным шпоном. Более низкие плотности в группах G и H могут быть связаны с потерей массы. Повышение температуры выше 150 ºC постепенно ухудшает физические и химические свойства древесины (Syrjanen and Oy 2001; Mitchell 1988).
Таблица 3. Значения плотности, толщины, набухания и водопоглощения плит
Значения в скобках являются стандартными отклонениями.
a,b,c,d,e,f Значения, имеющие одну и ту же букву, существенно не отличаются (критерий Дункана).
Плотность панели увеличивалась с увеличением давления прессования и уменьшалась с повышением температуры пресса. Это отрицательное влияние температуры (Yildiz 2002; Unsal et al. 2003; Korkut et al. 2008) и положительное влияние давления пресса (Unsal et al. 2009).; 2011) на плотность древесины наблюдали несколько исследователей.
Многослойные панели с временем погружения 2 и 24 часа имели более низкие значения WA, чем контрольная группа без ламинирования. Что касается сэндвич-панелей, древесностружечные плиты, ламинированные прессованным шпоном, имели более низкое значение WA для времени погружения в течение 2 часов и более высокое значение WA для времени погружения в течение 24 часов по сравнению с древесностружечными плитами, ламинированными непрессованным шпоном. Как для 2-часового, так и для 24-часового времени погружения значение WA уменьшалось с увеличением давления прессования при 180 ºC и 200 ºC и увеличивалось с увеличением давления прессования при 150 ºC. Для 24-часового времени погружения увеличение значения WA с увеличением давления при 150 ºC не было статистически значимым. Уменьшение значения WA при 180 ºC и 200 ºC может быть связано с уплотнением поверхности и уменьшением пористости шпона; при погружении материала вода заполняет пустоты. Этот вывод аналогичен результатам предыдущих исследований, проведенных в отношении древесных композитных панелей (Winandy and Krzysik 2007; Ayrilmis et al. 2009).; Вернуа 2007). Vernois (2007) сообщил, что WA древесины увеличивается с увеличением пористости, и когда древесина пропитывается водой, она может поглощать более 20% воды.
При времени погружения 2 часа и 24 часа, за исключением групп G и H, сэндвич-панели имели более высокие значения TS по сравнению с неламинированной ДСП. Панели из спрессованного шпона при температурах 180 o С и 200 o С имели более низкие значения TS по сравнению с панелями, ламинированными листами шпона без применения прессования. В сжатых панелях значения TS для 2-часового и 24-часового времени погружения уменьшались с увеличением температуры прессования при обоих давлениях прессования. Сходные результаты были получены Unsal et al. (2011). Они пришли к выводу, что улучшение TS при повышении температуры прессования объясняется изменением химического состава древесины.
Результаты тестов ANOVA и среднего разделения Дункана для MOR и MOE панелей показаны в таблице 4. Параллельно с ориентацией волокон неламинированная древесно-стружечная плита имела более низкое значение MOR по сравнению с ламинированными древесностружечными плитами.
Таблица 4. Значения модуля разрыва и модуля упругости образцов, параллельных и перпендикулярных ориентации зерен
Значения в скобках являются стандартными отклонениями
a,b,c,d,e,f Значения, имеющие одну и ту же букву, существенно не отличаются (критерий Дункана).
Предыдущие исследования показали, что покрытие поверхностей ДСП улучшало механические свойства панелей (Nemli 2003; Nemli et al. 2005). Наибольшее значение MOR установлено для панели типа С, ламинированной листами шпона, спрессованными под давлением 4 МПа при температуре 150 o С. Прессованные фанерно-стружечные плиты имеют более высокие значения MOR, чем древесностружечные плиты, ламинированные непрессованным шпоном. . Значения МОС уменьшались при повышении температуры выше 150 o C. Jämsä and Viitaniemi (2001) установили, что прочностные свойства древесины начинают снижаться при температурах выше 150 ºC из-за того, что при такой высокой температуре древесина становится более хрупкой. Значения МОС уменьшались с увеличением давления пресса из-за разрушения клеточных стенок. Неповрежденные клеточные стенки являются основным фактором приемлемых свойств вязкоупругой термически спрессованной древесины (Kutnar et al. 2009).
, параллельные ориентации волокон, у всех сэндвич-панелей, ламинированных прессованным шпоном, были выше, чем у неламинированных ДСП и ДСП, ламинированных непрессованным шпоном. Фанера, изготовленная из прессованной древесины березы и ольхи, показала более высокие значения МЧС, чем непрессованные образцы (Бехта и др., 2009 г.).). ДСП, ламинированные прессованным шпоном при давлении 4 МПа и температуре 150 o С, имели наибольшее значение МОЕ 5,641 ГПа, а самое низкое значение МОЕ (1,897 ГПа) наблюдалось у неламинированной ДСП. Группа C имела значения MOE на 197,4% и 15,9% выше, чем у неламинированной ДСП и ДСП, ламинированной непрессованным шпоном, соответственно. Средние значения MOE многослойных панелей уменьшались по мере увеличения давления пресса. Влияние давления пресса было более выражено при температурах 180 ºC и 200 ºC. МОЕ уменьшалось с повышением температуры более чем на 150 o °С. Температура не оказывала существенного влияния при давлении 4 МПа, но оказывала значительное влияние при давлении 6 МПа.
MOR и MOE панелей, ламинированных непрессованным шпоном, были соответственно на 318% и 157% выше, чем у неламинированных ДСП. Панели, ламинированные прессованным шпоном под давлением 4 МПа при 150 o С, имели значения MOR и MOE на 9,6% и 15,9% выше, чем панели, ламинированные непрессованным шпоном. Подобные улучшения в MOR и MOE из-за термического сжатия ранее наблюдались несколькими исследователями (Kutnar et al. 2008; Kamke 2006). Kamke (2006) отметил, что MOE LVL, полученного из прессованного шпона, на 81% выше, чем из непрессованного шпона. Кутнар и др. (2008) сообщили, что соответствующие значения MOR и MOE для трехслойных композитов составляют 64,0 МПа и 8,2 ГПа для несжатых композитов и 87,0 МПа и 12,1 ГПа для сжатых композитов. Испытания, проведенные перпендикулярно направлению волокон шпона, показали значительно более низкие MOE и MOR, чем испытания, проведенные параллельно направлению волокон. Этот результат ожидается из-за того, что прочность древесины на изгиб вдоль направления волокон в 20-25 раз выше, чем поперек направления волокон (Wood Handbook 19).99).
ВЫВОДЫ
В данной работе были исследованы некоторые механические и физические свойства панелей из ДСП, ламинированных термопрессованными листами шпона. Плотность многослойных панелей увеличивалась с увеличением давления прессования и уменьшалась с повышением температуры прессования. Все ДСП, ламинированные прессованным шпоном, имели более высокие модуль разрыва и модуль упругости по сравнению с неламинированными ДСП и ДСП, ламинированными непрессованным шпоном. Для сэндвич-панелей, ДСП, ламинированных шпоном и прессованных под давлением 4 МПа и температуре 150 o C имели самые высокие значения MOR и MOE. MOR и MOE уменьшались с повышением температуры при температурах выше 150 o C. Распухание по толщине для 2-часового и 24-часового времени погружения уменьшалось с увеличением температуры прессования. Представляется, что прессование шпона с использованием различных температур и давлений прессования можно рассматривать как альтернативный способ разработки сэндвич-продуктов с удовлетворительными структурными свойствами.
ССЫЛКИ
Адачи К., Иноуэ М., Канаяма К., Роуэлл Р. М. и Каваи С. (2004). «Удаление воды с мокрого шпона при помощи роликового прессования», J Wood Sci 50, 479-483.
Айрилмис, Н., Лауфенберг, Т.Л., и Винанди, Дж.Э. (2009). «Стабильность размеров и ползучести термообработанных наружных древесноволокнистых плит средней плотности», European Journal of Wood and Wood Products 67, 287-295.
Бехта П., Хизироглу С. и Шепелюк О. (2009). «Свойства фанеры, изготовленной из прессованного шпона, как строительного материала», Материалы и конструкция 30(4), 947-953.
Кандан, З., Хизироглу, С., и Макдональд, А. Г. (2010). «Качество поверхности термически спрессованного шпона пихты Дугласа», Materials and Design 31(7), 3574-3577.
EN 323. (1993). «Деревянные панели, определение плотности», Европейский комитет по стандартизации, Брюссель, Бельгия.
ЕН 317 (1993). «Стружечные и древесноволокнистые плиты. Определение набухания по толщине после погружения в воду», Eur. Комитет по стандартизации, Брюссель, Бельгия.
ЕН 310 (1993). «Деревянные панели, определение модуля упругости при изгибе и прочности на изгиб», Европейский комитет по стандартизации, Брюссель, Бельгия.
Фауст, Т. Д., и Райс, Дж. Т. (1986). «Влияние шероховатости поверхности шпона на качество клеевого соединения фанеры из южной сосны», Forest Products Journal 36(4), 57-62.
Ямся, С., и Виитаниеми, П. (2001). «Термическая обработка древесины для повышения долговечности без химикатов». В сб.: Рапп А.О. (ред.), Обзор термической обработки древесины. Действие по затратам E22. Труды специального семинара, Антибы, Франция, 17–22.
Коркут С., Акгуль М. и Дундар Т. (2008). «Влияние термической обработки на некоторые технологические свойства древесины сосны обыкновенной ( Pinus sylvestris L.)», Bioresource Technology 99(6), 1861-1868.
Кутнар А., Камке Ф. А. и Сернек М. (2009). «Профиль плотности и морфология вязкоупругой термически сжатой древесины», Wood Sci. Технол. 43(1-2), 57-68.
Камке, Ф.А. (2006). «Уплотненная сосна лучистая для конструкционных композитов», Maderas:Ciencia Tecnologia Journal 8(2), 83–92.
Кутнар А., Камке Ф. А. и Сернек М. (2008). «Механические свойства уплотненной древесины VTC, относящиеся к конструкционным композитам», European Journal of Wood and Wood Products, 66, 439-446.
Митчелл, П. Х. (1988). «Необратимые изменения свойств небольших образцов сосны лоблолли при нагревании на воздухе, азоте или кислороде», Wood and Fiber Science 20(3), 320-355.
Немли, Г. (2003). «Влияние технологических параметров лакокрасочных материалов на технологические свойства ДСП», Диссертация, Черноморский технический университет.
Немли, Г., Орс, Ю., и Калайджиоглу, Х. (2005). «Выбор подходящих материалов декоративного покрытия поверхности для внутреннего применения из ДСП». Строительство и строительные материалы 19(4), 307-312.
Рауткари, Л., Проперци, М., Пичелин, Ф., и Хьюз, М. (2010). «Свойства и восстановление схватывания поверхности уплотненной ели обыкновенной и бука европейского», Wood Science and Technology 44, 679-691.
Сирьянен Т. и Ой К. (2001). «Производство и классификация термически обработанной древесины в Финляндии. Обзор термической обработки древесины», В: Материалы специального семинара 9. 0004 Проводится в Антибе, Франция.
Табарса, Т., и Чуй, Ю.Х. (1997). «Влияние горячего прессования на свойства белой ели», Forest Products Journal 47, 71–76.
Унсал О., Коркут С. и Атик К. (2003). «Влияние термической обработки на некоторые свойства и цвет древесины эвкалипта ( Eucalyptus Camaldulensis Dehn.)», Maderas: Ciencia Tecnologia Journal 5(2), 145-152.
Унсал О., Кандан З., Буюксари У., Коркут С., Чанг Ю.-С. и Йео Х. (2011). «Влияние термокомпрессионной обработки на поверхностную твердость, вертикальную плотность пропила и набухание по толщине эвкалиптовых древесных плит при горячем прессовании», Mokchae Konghak 39(2), 148-155.
Унсал, О., и Кандан, З. (2008). «Влагосодержание, профиль вертикальной плотности и твердость по Янке термически сжатых панелей из древесины сосны в зависимости от давления прессования и температуры», Dry Technol 26(9), 1165-1169.
Унсал О. , Картал С. Н., Кандан З., Аранго Р., Клаузен К. и Грин Ф. (2009). «Стойкость к гниению и термитам, водопоглощение и набухание термически спрессованных деревянных панелей», International Biodeterioration and Biodegradation 63(5), 548-552.
Вернуа, М. М. (2007). «Термообработка древесины во Франции — современное состояние», Centre Technique du Bois et de l’Ameublement, Париж, Франция, 6 стр.
Винанди, Дж. Э., и Кржисик, А. (2007). «Термическая деградация древесных волокон при горячем прессовании композитов МДФ: часть I. Относительные эффекты и преимущества теплового воздействия», Wood and Fiber Science 39, 450-461.
Welzbacher, C.R., Wehsener, J., Rapp, A.O., and Haller, P. (2008). «Термомеханическое уплотнение в сочетании с термической стабильностью размеров и долговечностью», European Journal of Wood and Wood Products 66(1), 39-49.
Справочник по дереву. (1999). «Лесная служба Министерства сельского хозяйства США, Лаборатория лесных товаров», Мэдисон, Висконсин, USA General Tech. Отчет FPL-GTR-113, 463 стр.
Йылдыз, С. (2002). «Физические, механические, технологические и химические свойства древесины бука и ели, обработанной нагревом», Диссертация, Черноморский технический университет, Трабзон, Турция.
Статья отправлена: 13 октября 2011 г.; Экспертная оценка завершена: 16 ноября 2011 г.; Получена исправленная версия: 16 ноября 2011 г.; Принято: 17 января 2012 г.; Опубликовано: 20 января 2012 г.
Разъяснение материалов полок для различных целей
Трудно рекомендовать тип материала полки и указать конкретную толщину и расстояние между опорами. поскольку они во многом зависят от веса, прикладываемого к ним, и качества используемого материала. Комментарии ниже для сравнения только для определенных целей, и по возможности следует получить консультацию у производителя или поставщика материалов для полок. Эта страница относится только к материалу полок, способы крепления полок см. на другой нашей странице.
Для сравнения ниже:
- Легким грузом считаются небольшие растения, вазы, безделушки и т.
д.
- Средней нагрузкой считаются книги в мягкой обложке.
- Тяжелым грузом считаются большие книги в твердом переплете, большие растения и т. д.
Фактическая классификация предполагаемой нагрузки должна быть «здравым смыслом», если вы сомневаетесь, постройте сильнее и помните, что такое полка. изначально был разработан для того, чтобы внезапно положить тяжелый предмет на полку, ранее использовавшуюся для легких предметов.
Выступы на каждом конце за скобками всегда должны быть минимальными, как правило, не более 20% расстояния между опорными кронштейнами.
брус — сосновая доска — ДСП — МДФ — столярная плита — фанера — стекло
Ребро жесткости полки — брус
Массивная древесина
Твердая древесина прочна и доступна в различных строганых формах.
ширины для удовлетворения большинства потребностей стеллажей — там, где требуемая ширина не может быть получена, можно использовать шпунтованную и рифленую доску, чтобы избежать
отдельные доски открываются от коробления — в качестве альтернативы отдельные доски можно соединить с помощью дюбелей или других средств.
Древесина проста в обработке и может быть обработана полировкой, лаком или краской.
Толщина, необходимая для предотвращения провисания, будет зависеть от груза, размещенного на полке, а также от расстояния между опоры. Используйте древесину толщиной не менее 18 мм и поддерживайте полку на расстоянии не более 700 мм от центра или 25-миллиметровую древесину с опорами. не более 900 мм.
Реечный брус — в качестве альтернативы для широких полок можно сделать решетчатую полку из нескольких деревянных реек, прикрепленных к рейкам снизу. под рейками, а затем крепятся к опорным кронштейнам.
Ламинированная кромка из хвойной древесины
Ламинированная кромка из хвойных пород (сосновая доска и т. д.) – состоит из полос хвойной древесины (обычно шириной от 25 до 100 мм), склеенных кромкой к кромке для получения готовых досок шириной до 600 мм.
Обычно такая же прочная, как массивная древесина, и часто выглядит так же хорошо, за исключением очень близкого плана — некоторые доски могут содержать много наполнителя, чтобы сделать поверхность гладкой, это может отрицательно сказаться на прозрачной отделке. .
Используйте расстояние между опорами, как указано выше, для массивной древесины.
ДСП
Обычная ДСП — неламинированная ДСП — самый дешевый и непрочный материал. Как правило, он не подходит для стеллажей из-за плохой отделки.
Ламинированная древесно-стружечная плита — ламинированная древесно-стружечная плита дешевле, чем массивная древесина, и поставляется с различными видами шпона. Он не такой прочный, как массивная древесина, и будет иметь тенденцию провисать, за исключением очень небольшой нагрузки. Используйте ДСП толщиной не менее 12 мм и поддерживайте полку на расстоянии не более 300 мм от центра для всех грузов, кроме самых легких. Или ДСП 18 мм с опорами на расстоянии не более 700 мм друг от друга.
МДФ
МДФ (древесноволокнистая плита средней плотности) прочнее ДСП. Потребности в уходе
следует принимать при работе с МДФ, так как он производится с использованием карбамидоформальдегидной смолы, которая может быть вредной. Необходима достаточная вентиляция и ношение маски для лица, чтобы избежать вдыхания пыли при ее обработке.
Формальдегид также может выделяться с течением времени в низких концентрациях; не на всех это влияет, но на некоторых людей может негативно повлиять просто наличие в комнате куска МДФ.
МДФ можно покрасить краской в тон декору или просто покрыть лаком. Используйте МДФ толщиной не менее 18 мм и поддерживайте полку на расстоянии не более 500 мм от центра для всех грузов, кроме самых легких. Или МДФ толщиной 25 мм с опорами на расстоянии не более 700 мм друг от друга.
Блокнот
Столярная плита (с сердцевиной, идущей вдоль) прочнее ДСП и с меньшей вероятностью провиснет. С ним легко работать, и его можно покрасить, края, вероятно, нужно будет покрыть окантовкой, чтобы скрыть различные полоски. Используйте толщину не менее 18 мм и поддерживайте полку на расстоянии не более 700 мм от центра для всех грузов, кроме самых легких.
Фанера
Фанера прочнее ЛДСП и менее склонна к провисанию. С ним легко работать, и его можно покрасить, края, вероятно, нужно будет покрыть окантовкой, чтобы скрыть различные слои. Используйте толщину не менее 18 мм и поддерживайте полку на расстоянии не более 700 мм от центра для всех грузов, кроме самых легких.
Стекло
Стекло может быть привлекательным стеллажом для легкой загрузки, и многие магазины DIY продают готовые стеклянные стеллажи отдельно или как часть полного комплекта стеллажей — для стеклянных стеллажей доступны специальные кронштейны, у них есть зажимы и выступы для удержания стекла. на месте. Стекло специально закалено, поэтому его нельзя разрезать по размеру. Если требуются «нестандартные» размеры, обратитесь к продавцу остекления, где его можно разрезать по размеру, а затем закалить. Никогда не используйте обычное оконное стекло.
Ребро жесткости полки
Любой материал полки может быть усилен для увеличения нагрузки, которую он будет нести, и расстояния, необходимого между опорами. Прикрутите и приклейте планку к нижней стороне. Вместо нее или в дополнение можно использовать планку, прикрепленную к стене и поддерживающую заднюю часть полки.
Древесина окантовка
При раскрое ДСП, фанеры или столярных плит открытые края могут выглядеть непривлекательно. Окантовка из твердой древесины, обрезанная под углом, может быть легко приклеена и приколота булавками к краям, чтобы скрыть обрезанные края.
Если вы не можете получить фанеру сейчас, попробуйте это вместо этого
Каждый редакционный продукт выбирается независимо, хотя мы можем получить компенсацию или партнерскую комиссию, если вы купите что-то по нашим ссылкам. Рейтинги и цены точны, а товары есть в наличии на момент публикации.
Лесные пожары, нехватка рабочей силы и проблемы с цепочками поставок усложняют доступ к фанере и делают ее более дорогой. Вот что вы можете использовать в качестве альтернативы.
Можно с уверенностью сказать, что сегодня никто из активных строителей не помнит времени, когда фанера не была основным строительным материалом.
Лесная служба США приравнивает увеличение использования фанеры в 1920-х годах к началу индустриальной эпохи. Историки могут возразить на этот счет, но суть вы поняли. Это был предпочтительный материал для всех аспектов жилищного строительства и реконструкции в течение как минимум столетия.
К сожалению, с началом пандемии COVID-19 в 2020 году фанера стала дороже и ее труднее достать. Причин тому много, и в будущем ситуация может улучшиться. До тех пор, пока это не произойдет, по соображениям бюджета и графика разумно рассмотреть альтернативы при планировании проекта.
На этой странице
Почему дефицит фанеры?
Нехватка фанеры является частью общей нехватки пиломатериалов, в которой можно частично обвинить пандемию, а частично недавнюю волну лесных пожаров в западной части Северной Америки.
По данным Центра климатических и энергетических решений, изменение климата является основной причиной проблемы лесных пожаров. Добавьте всплеск новых жилищных проектов для удовлетворения возросшего спроса, и вы получите идеальный шторм сокращения предложения и увеличения спроса на пиломатериалы в целом, а не только на фанеру.
Летом 2021 года лесные пожары сожгли миллионы акров земли в Британской Колумбии, где расположены три из шести крупнейших производителей пиломатериалов на континенте.
Пожары вынудили Canfor, крупного производителя пиломатериалов, сократить производство более чем на 100 миллионов досок и ввести краткосрочные сокращения на канадских лесопильных предприятиях. Пожары сожгли более миллиона акров в Вашингтоне и Орегоне, которые также являются крупными производителями фанеры.
Нехватка рабочей силы, вызванная пандемией, создала узкие места на американских лесопильных заводах, что также способствовало резкому росту цен на пиломатериалы, сообщает Washington Post. Подняв цены, лесопилки подняли зарплату своим работникам, но многие все равно предпочли остаться дома, чтобы не заразиться.
Проблемы с производством постепенно решаются. Но проблемы с цепочкой поставок, вызванные нехваткой водителей грузовиков, привели к увеличению транспортных расходов, а инфляция повсеместно повышает цены на потребительские товары.
Когда проблемы цепочки поставок и нехватки рабочей силы будут решены, а инфляция начнет снижаться, Conner Industries прогнозирует, что цены на фанеру упадут. Но не ясно, когда это произойдет.
Что можно использовать вместо фанеры?
Выбор лучшей альтернативы фанере зависит от области применения. Материал должен иметь достаточную структурную целостность для строительства. Это позволяет отказаться от пенополиуретановой плиты, которая в основном используется в качестве утеплителя. Обшивка должна быть влагостойкой. Если вы используете альтернативу фанере для внутренней отделки, внешний вид важен.
Ориентированно-стружечная плита (OSB или ДСП)
Строители уже используют OSB взаимозаменяемо с фанерой для обшивки крыш и стен, а также чернового пола.
Доступный в листах того же размера, что и фанера, он изготавливается путем наслаивания стружек древесной стружки, их фиксации под давлением и обработки воском или смолой для придания конечному продукту водостойкости. Текстурированная поверхность OSB с узором из переплетенных древесных прядей делает ее пригодной только для конструкционных целей.
OSB не обязательно дешевле фанеры. На момент написания статьи 4-фут. х 8 футов. лист 19/32 дюйма. OSB стоит около 56 долларов по сравнению с 48 долларами за сопоставимую фанерную обшивку. OSB можно производить из древесных отходов, поэтому они легко доступны в торговых точках, где уже мало фанеры сопоставимой толщины.
Древесноволокнистая плита средней плотности (МДФ)
Краснодеревщики и столяры по внутренней отделке знакомы с МДФ, из которого можно делать отделку, шкафы и дверцы шкафов, а также стеновые панели.
МДФ изготавливается путем прессования древесных волокон вместе с прочным клеем в твердую, плотную матрицу. Полученные панели размером с фанеру имеют гладкую поверхность без зерен, идеально подходящую для покраски или ламинирования деревянным или пластиковым шпоном.
Поскольку он сделан из переработанных материалов, он является более экологичным строительным продуктом, чем фанера. Он тяжелее фанеры и не обладает упругостью. Но при правильной отделке он менее чувствителен к изменениям температуры и влажности. 4-футовый. х 8 футов. лист толщиной 5/8 дюйма. весит около 85 фунтов, поэтому для полных простыней требуется два человека.
Древесноволокнистая плита высокой плотности (HDF)
Также известная как древесноволокнистая плита, HDF похожа на MDF по конструкции. Но частицы древесины сжимаются с большей силой, придавая готовому изделию более твердую поверхность. Он часто используется производителями мебели и может быть использован в стеновых панелях и внутренней отделке.
К сожалению, листы HDF размером с фанеру доступны только тонкой толщины, толщиной 1/8 дюйма. ДВП самый распространенный. Строители постоянно используют его в качестве подложки для листового винила и линолеума. В крайнем случае, вы можете найти для него больше применений.
ДСП
ДСП, также изготовленная из переработанных материалов, является одной из самых дешевых альтернатив фанере.