Технологические особенности плавки цветных металлов и сплавов в электропечах :: Технология металлов
Плавка алюминия
Алюминий и его сплавы применяются практически во всех отраслях промышленности, а также при производстве предметов домашнего обихода.
При комнатной температуре алюминий покрывается тонкой пленкой окиси (А12O3), которая надежно предохраняет его от дальнейшего окисления. Скорость окисления алюминия с повышением температуры резко возрастает. Поэтому при плавке алюминия и его сплавов в плавильных печах поверхности расплавляемых кусков и зеркало ванны быстро покрываются слоем окиси.
Температура плавления окиси алюминия (2050° С) примерно в три раза выше температуры плавления металлического алюминия (660°С), а плотность окиси (3,9 г/см3) примерно в 1,5 раза больше плотности жидкого алюминия (2,7 г/см3).
Поэтому окись алюминия находится в ванне печи во
взвешенном состоянии. Наличие окислов и карбидов резко ухудшает литейные
свойства сплавов, а также снижает их антикоррозионные качества. Отливки, получаемые
под давлением, часто имеют тонкие стенки, а окислы и карбиды закупоривают
проходы и прекращают доступ жидкого сплава в узкие полости формы, вызывая
литейный брак.
Металлические примеси в сплаве главным образом влияют на механические свойства изделий.
В настоящее время плавка алюминия проводится преимущественно в пламенных отражательных печах, работающих на углеродистом топливе, и в электрических печах. Естественно, качественные и экономические показатели при этом получаются не одинаковые.
При плавке алюминия в отражательных пламенных печах и в камерных электропечах сопротивления нагрев отдельных кусков садки начинается в зоне наиболее высоких температур, т. е. сверху. При этом поверхность садки быстро окисляется и поглощает значительное количество газов.
В тигельных индукционных электропечах для плавки
алюминия при отсутствии «болота» (слоя жидкого металла, оставленного в тигле
от предыдущей плавки) быстрому нагреву подвергается слой садки, расположенный
возле внутренних боковых стенок тигля.
Индукционные канальные электропечи со стальным сердечником при плавке алюминия и его сплавов имеют ряд ценных преимуществ, основные из которых перечислены ниже.
В канальной индукционной электропечи расплавление кусков алюминия происходит в зоне максимальных температур под слоем жидкого металла, поверхность которого закрыта пленкой окиси алюминия.
Зона максимальных температур в канальных электропечах находится в узком канале и в прилегающих к нему участках шихты.
Температура металла па поверхности шахты всегда имеет
минимальное значение, в результате чего готовые отливки, получаемые из
канальных электропечей, содержат меньшее количество окислов, чем отливки,
полученные в печах других типов. Этим же преимуществом обладают тигельные
индукционные электропечи, в которых по технологическим требованиям в тигле
после каждой плавки оставляют часть жидкого металла 20—35% от емкости тигля
печи.
Жидкий алюминий и его сплавы обладают способностью поглощать газы и особенно водород. В пламенных печах большое количество водорода находится в топочных газах. Кроме того, в плавильные печи всех типов он может быть занесен сырой шихтой.
Вода при высокой температуре и при наличии жидкого алюминия распадается на кислород и водород. кислород вступает во взаимодействие с алюминием по реакции
3Н2О + 2Аl → Аl2O3 + 3Н2
Выделившийся при этом водород поглощается сплавом, влияние энергоносителя и конструкции плавильной печи на степень насыщения алюминиевых сплавов водородом показано ниже:
( Объем водорода на 100 г металла см3)
Газовый горн (плавка без флюса) ……….2,5
Газовый горн (плавка под флюсом) ………1,05
Отражательная
печь на газообразном топливе. ……….2,5—3
Отражательная печь на мазуте …….3—4
Электропечь сопротивления ……..1,05
Электропечь канальная индукционная …………0,13
Электромиксер………0,12
Жидкий алюминий хорошо растворяет многие металлы и, в частности железо, образуя хрупкие соединения FeAl2 и Fe2Al7, снижающие качество отливок.
Влияние времени выдержки жидкого алюминия в металлическом тигле на насыщение его железом показано ниже:
Время выдержки, Содержание железа,
мин %
25 1,75
35 1,90
40 1,97
45 2,01
65 2,30
100 2,50
Плавка алюминия в канальных электропечах не лишена
технологических недостатков. Образовавшаяся на поверхности жидкого металла
пленка окиси, не смоченная жидким металлом, в результате сил поверхностного
натяжения и сцепления пленки с футеровкой шахты, плотно закрывает зеркало
ванны.
Однако если целостность пленки нарушить, то оголенные участки жидкого металла быстро окислятся, а изломанные куски пленки начнут оседать на дно ванны. При интенсивной циркуляции жидкого металла в печи куски окиси затягиваются в каналы и, оседая на его стенках, уменьшают его рабочее сечение. В практике это явление называется зарастанием канала.
Полностью избавиться от зарастания каналов в индукционных канальных печах практически невозможно, так как нарушение поверхностной пленки окиси может быть вызвано причинами, не зависящими от конструкции печи (отдельных ее узлов) и от технологических режимов.
Необходимо отметить, что очистка каналов связана с
большими технологическими трудностями. Работа по очистке каналов чрезвычайно
сложная и тяжелая, она влечет за собой вынужденные простои и уменьшение
производительности печи, сокращение срока службы футеровки и загрязнение
металла окислами.
Нормальная Работа канальной электропечи возможна только при условии, что в ней всегда будет оставаться некоторое количество (до 35% от полной емкости печи) жидкого металла.
В тех случаях, когда по технологическим требованиям необходимо изменить химический состав расплавляемого сплава, печь должна быть полностью освобождена от ранее выплавляемого сплава и залита жидким сплавом нужного химического состава. Это в значительной степени ограничивает производственные возможности электропечи и снижает ее экономические показатели.
Наиболее экономически эффективно эксплуатируются канальные электропечи при круглосуточной работе, выплавляя однородные сплавы, замена которых не требует полного освобождения электропечи от жидкого металла.
Тигельные электропечи для плавки алюминия этих недостатков практически не имеют, но они имеют худший к. п. д. и коэффициент мощности.
Плавка магния
Магний принадлежит к группе легких металлов.
Обычно магний и его сплавы выплавляются в тигельных или отражательных печах под слоем флюса, так ак обнаженный жидкий металл мгновенно воспламеняется.
Тигельные печи предпочтительнее, чем отражательные, потому что в них топочные газы не могут соприкасаться с флюсами, находящимися на поверхности жидкого магния. Для плавки магния и его сплавов в тигельныхпечах рекомендуются стальные тигли, так как они не вступают в химические соединения ни с магнием ни с его флюсами. Графитовые тигли обогащают металл углеродом, а набивные из огнеупорных материалов вступают в химические соединения с флюсами.
Из сказанного следует, что тепловая энергия, необходимая
для расплавления и особенно для перегрева жидкого металла, должна передаваться
металлу с максимально возможной скоростью, и металл в тигле должен находиться
в спокойном состоянии.
Полностью удовлетворяют этим условиям только тигельные индукционные печи промышленной частоты. Электрическая энергия в тигельных индукционных печах превращается в тепловую, главным образом в стальном тигле. Поэтому установки с тигельными индукционными печами имеют очень высокий к. п. д., до 85%, в то время как к. п. д. тигельных электропечей сопротивления колеблется в пределах 40—70%, а у тигельных мазутных печей он не превышает 10%.
Скорость нагрева садки в тигельных индукционных печах теоретически может быть очень большой, поэтому эти печи имеют большую производительность. Так, че-тырсхтонаня индукционная тигельная печь типа ИГТ-7 отечественного производства может при круглосуточной работе выдать до 60 т магниевого сплава.
В настоящее время для плавки магниевых сплавов изготавливают тигельные индукционные печи промышленной частоты емкостью до 16 г.
Плавка магния и его сплавов в тигельных печах сопротивления
и в индукционных канальных электропечах в настоящее время почти не
осуществляется, так как печи сопротивления имеют очень небольшую Скорость нагрева,
а в канальных электропечах быстрее зарастают узкие каналы.
Плавка цинка
Цинк и его сплавы широко применяются как защитные покровы других легкоокисляющихся металлов и для изготовления архитектурных сооружений. Характерной особенностью цинка является его низкая температура кипения 916° С. Испарение цинка начинается при более низких температурах. Индукционные электропечи со стальным сердечником и с закрытыми каналами являются наилучшими печами для плавки цинка, так как только в канальных индукционных электропечах температура жидкого металла достигает своего максимального значения внутри печи (в узких каналах), где и происходит Испарение цинка. Но пары цинка, выходя из каналов, попадают в зону более низких температур, где происходит их конденсация. Этим и объясняется тот факт, что при плавке цинка и его сплавов в канальных индукционных электропечах выход металла составляет примерно 98,5%, тогда как в пламенных отражательных печах он не всегда достигает 94%.
Другой особенностью цинка является то, что его пары
имеют значительное давление, благодаря чему они проникают в поры некоторых
футеровочных материалов, где вступают в химическое взаимодействие с металлами,
находящимися в футеровке, и разрушают ее. В настоящее время имеются массы для
футеровок, лишенных названного выше недостатка. Примером такого состава
является масса, содержащая 53% обожженной глины, 35% синей гончарной глины и
12% каолина.
В качестве связующего вещества может быть использован сульфидный щелок.
Пары цинка, кроме того, ядовиты, поэтому печная установка должна иметь хорошую вытяжную вентиляцию.
Наиболее желательными компонентами в цинковых сплавах являются мышьяк, сурьма и железо. Первые два понижают антикоррозионную стойкость, а железо при высоких температурах образует с цинком хрупкое химическое соединение, которое, опускаясь на дно печи, попадает в каналы и засоряет их. Поэтому при плавке цинковых сплавов температуру жидкого металла повышать выше технологически установленной не рекомендуется.
В настоящее время отечественная промышленность серийно иготовляет канальные индукционные электропечи для переплава катодного цинка емкостью 25 и 40 т.
Плавка меди
Медь представляет собой тягучий мягкий металл красного
цвета, с высокими электро- и теплопроводностью. В технике медь получила
широкое распространение как в чистом виде, так и в виде сплавов. На медной основе
получают многие сплавы с ценными физическими свойствами, из которых основными
являются латунь, бронза, томпак и др.
Основным потребителем как первичной, так и вторичной меди является электротехническая промышленность. Вся производимая отечественной промышленностью медь распределяется примерно так:
на изготовление токопроводящих деталей 50%; на производство сплавов на медной основе —40%; все прочие производства — 10%.
Для получения сплавов на медной основе наибольшее
распространение получили индукционные канальные электропечи. В этих печах
производятся сплавы, температура разливки которых не превышает 1300— 1400° С,
так как физические свойства футеровки ограничивают возможность плавки сплавов,
требующих более высоких температур. Для плавки специальных сплавов, имеющих
температуру разлива выше 1400° С, используются тигельные индукционные
электропечи промышленной и повышенной частоты, а также дуговые печи косвенного
нагрева и барабанные электропечи сопротивления. Недостатком дуговых
электропечей является несколько повышенный угар металла, вызываемый местным
перегревом в зоне электрической дуги. Поэтому дуговые электропечи имеют
ограниченное применение.
Для плавки меди и ее сплавов также применяются электропечи сопротивления барабанного типа. Эти электропечи могут быть использованы для плавки других сплавов цветных металлов с температурой плавления до 1500° С.
Плавка никеля
Никель отличается высокой антикоррозионной стойкостью и пластичностью при механической обработке. В технике он применяется как в чистом виде, так и в сплавах. Практически в настоящее время применяются никелевые сплавы высокого омического сопротивления. Кроме того, никель расходуется на антикоррозионные и художественные покрытия различных деталей.
Плавку никеля и его сплавов проводят в тигельных и
канальных электропечах. При этом особое внимание следует обращать на качество
футеровки, так как температура плавления никеля равна 1452° С, а разливка его
осуществляется при 1550° С. Канальные электропечи, предназначенные для плавки
никеля, должны иметь увеличенное сечение каналов, что объясняется большим
удельным электрическим сопротивлением жидкого никеля. Жидкий никель очень
интенсивно поглощает газы. Поэтому для получения качественных сплавов никеля с
хромом с наименьшим количество углерода рекомендуется плавки проводить в
вакуумных тигельных индукционных электропечах.
Однако до настоящего времени большинство сплавов на основе никеля типа Х15Н60, Х20Н80, ЭИ437, применяемых для нагревательных элементов электропечей сопротивления, выплавляется в обычных электродуговых печах с графитовыми электродами.
Плавка титана
Титан — металл химически активный и тугоплавкий. Он плавится при 1667° С. С повышением температуры титана его химическая активность резко возрастает. Особенную активность он проявляет после перехода в жидкое состояние.
Жидкий титан хорошо взаимодействует с кислыми,
основными и нейтральными огнеупорными материалами, применяемыми в настоящее
время в металлургии. Поэтому титан и его сплавы в печах с обычной футеровкой
практически получать невозможно. В открытых печах плавить титан нельзя, так
как, находясь в жидком состоянии, он быстро окисляется и может полностью
сгореть. Даже в вакууме при температуре, близкой к 2000° С, он хорошо
взаимодействует с алюминием и углеродом, образуя карбиды титана, которые
способствуют понижению пластичности и ухудшению обрабатываемости в холодном состоянии.
В настоящее время жидкий титан для получения фасонных отливок выплавляют только в вакуумных дуговых печах гарниссажного типа с расходуемым электродом.
Плавка и разливка алюминиевых сплавов Категория: Литейное производство Плавка и разливка алюминиевых сплавов Для плавки алюминиевых сплавов используют тигельные печи, обогреваемые различными видами топлива, стационарные пламенные и электрические — сопротивления и индукционные. 1. Шихтовые материалы В качестве исходных шихтовых материалов применяют первичные и вторичные металлы и сплавы, оборотные сплавы и лигатуры. Первичный алюминий поставляется по ГОСТ 11069—74 в виде чушек массой 5, 15 и 1000 кг. Для производства алюминиевых сплавов обычно используют алюминий марок А5, А6 и АО, а для изготовления отливок высокоответственного назначения — алюминий особой и высокой чистоты. Вторичные алюминиевые сплавы получают переплавкой и рафинированием лома и отходов. Они поставляются в виде чушек различных марок по ГОСТ 1583—73. Свежие металлы. В состав алюминиевых сплавов входят цинк, магний, кремний, марганец, медь, бериллий, никель, железо, титан и другие элементы. Для алюминиевых сплавов обычно применяют цинк марок Ц1 и Ц2. Магний поставляется по ГОСТ 804—72 в чушках массой 8,0±1 кг. Ввиду большой склонности его к коррозии поверхность чушек подвергается антикоррозионной обработке. Кремний вводят в алюминиевые сплавы в виде чушкового силумина (сплав кремния с алюминием), поставляемого по ГОСТ 1521—76, а марганец —в виде лигатуры алюминий — марганец, содержащей около 10% марганца. Качество отливок в большой степени зависит от тщательности подготовки шихтовых материалов к плавке и способов их хранения. Они должны храниться в сухих крытых помещениях раздельно по маркам сплавов. Оборотный сплав должен очищаться от песка в очистных барабанах. Лигатуры. При плавке алюминиевых сплавов, как правило, применяют двойные лигатуры — сплавы из двух компонентов. Введение лигатур обеспечивает получение сплава с точным содержанием элементов, что особенно важно для сплавов, содержащих магний, так как даже малые добавки его сказываются на свойствах сплавов. 2. Расчет шихты Шихта для приготовления алюминиевых сплавов может состоять из чушкового алюминия, силумина, оборотного металла, лигатур и чистых металлов. Рассмотрим пример расчета шихты для сплава АЛ5 при плавке в тигельной печи. Средний химический состав этого сплава: 5% кремния, 0,4% магния, 1,25% меди, остальное — алюминий. Для доведения до необходимого количества содержания кремния применяем чушковый силумин (с Si=13%), а магния и меди— алюминиево-магнневую и алюминиево-медную лигатуры. 3. Флюсы, рафинирующие и модифицирующие материалы Для получения высококачественных сплавов осуществляют плавку под флюсом, рафинирование сплава для удаления неметаллических включений, а также модифицирование для получения мелкой структуры и повышения механических свойств. Для рафинирования и модифицирования алюминиевых сплавов часто применяют универсальные флюсы, состоящие из смеси солей и криолита. Универсальные флюсы используются как в жидком, так и в порошкообразном состоянии. 4. Плавка в тигельных печах Плавку алюминиевых сплавов в небольших объемах осуществляют в тигельных печах, работающих на нефти и газе. Печь состоит из стального кожуха с футеровкой и вставленного в него сверху чугунного тигля. Последний своим широким фланцем крепится к стальному кольцу, перекрывающему шахту сверху, что обеспечивает полную изоляцию расплавленного металла от печных газов. Печь установлена на сварной или литой раме. Поворот ее осуществляется штурвалом. Для увеличения срока службы тиглей и уменьшения насыщения сплавов железом внутреннюю поверхность их рекомендуется окрашивать краской, состоящей из 60% кварцевого песка, 30% огнеупорной глины и 10% жидкого стекла. Рис. 1. Поворотная тигельная печь. 5. Плавка в электрических печах Плавку алюминиевых сплавов производят в электрических печах сопротивления, тигельных и отражательных печах, а также в индукционных. Плавка в электрических отражательных печах. На предприятиях, где алюминиевые сплавы выплавляются в больших объемах, применяют электрические печи САН (печи сопротивления для алюминиевых сплавов, наклоняющиеся) и камерные стационарные. Печь САН (рис. 2) имеет удлиненный металлический корпус, установленный на катках и укрепленный на фундаменте. Корпус изнутри выложен кирпичом. В торцах печи расположены две форкамеры, а в середине — центральная ванна. Свод печи выложен фасонными огнеупорными кирпичами, в гнездах которых уложены нагревательные спирали. Такие же спирали имеются и в форкамерах. Шихту загружают через окна. Она плавится в форкамерах за счет тепла, отраженного от свода и стенок печи, и по наклонным плоскостям стекает в центральную ванну. Слив готового металла из печи осуществляется через лётку при повороте печи на опорных катках с помощью штурвала или электропривода. Плавка в тигельных электрических печах сопротивления. При сравнительно небольших масштабах производства для плавки алюминиевых и магниевых сплавов применяют однотигельные печи сопротивления САТ-0,15 и САТ-0,25, а также двухтигельные печи СЖ.Б-230 и ОКБ-75. Рис. 2. Электрическая печь типа САН. Печи CAT выполнены в виде сварного цилиндрического кожуха, футерованного фасонным легковесношамотным кирпичом, и имеют теплоизоляцию. Плавка в индукционных электрических печах. Различают индукционные печи со стальным сердечником и индукционные тигельные печи ИАТ. Печи со стальным сердечником широко применяются для плавки как алюминиевых, так и медных сплавов. Они имеют ряд преимуществ по сравнению с печами сопротивления: более высокую производительность, меньший удельный расход электроэнергии, возможность рафинирования металла в печи, обеспечивают высокое качество сплава с минимальным содержанием газов. В этих печах интенсивное движение металла происходит в устьях каналов, а поверхность жидкого сплава в самой печи находится в спокойном состоянии, что обеспечивает сплошность окисной пленки и предохраняет сплав от дальнейшего окисления. Рис. 3. Тигельная электропечь. В последнее время получили распространение бессердечниковые тигельные индукционные печи ИАТ емкостью 0,4—0,6 т и производительностью 0,235—2,0 т/ч. 6. Особенности технологии плавки и разливки алюминиевых сплавов Для большинства алюминиевых сплавов принята одна технология плавки вне зависимости от конструкции печи. Шихтовые материалы перед загрузкой тщательно очищают от загрязнений и подогревают до 100—150 °С для удаления с их поверхности влаги. Плавка алюминиево-кремнистых сплавов. Как уже указывалось, лучше всего вести плавку в индукционных печах высокой или промышленной частоты и в электрических печах сопротивления. В качестве шихтовых материалов применяют чушковые силумины, первичный алюминий и оборотный металл (до 50% от массы шихты). Плавку осуществляют в следующей последовательности. Печь или тигель нагревают до температуры 600—700 °С, загружают в них подогретые чушки силумина и предварительно очищенный в барабане оборотный сплав. Рафинирование осуществляют путем погружения навески хлористого цинка на дно тигля с помощью «колокольчика», который медленно водят по дну тигля до полного прекращения выделения пузырьков газа. Модифицирование смесью хлористых и фтористых солей калия и натрия производят путем покрытия ими очищенной от шлака поверхности сплава и выдержки в течение 12—14 мин. Затем соли рубят и замешивают в сплав в течение 2 мин, после чего модификатор снимают с поверхности сплава. При использовании универсальных флюсов операции рафинирования и модифицирования совмещают. Плавка алюминиевых сплавов, содержащих магний. Во избежание насыщения сплава вредными примесями — железом и кремнием — плавка ведется только в графитовых тиглях. Вспомогательный инструмент — счищалка, колокольчики и др. — также изготовляется из графита или титана. В качестве шихтовых материалов применяют первичный алюминий высокой чистоты, магний и лигатуры алюминиево-бериллие-вую, алюминиево-титановую, алюминиево-циркониевую и оборотный сплав соответствующей марки (до 50—60% от массы всей шихты). После нагрева тигля до температуры 600 °С. загружают чушки первичного алюминия и алюминиево-бериллиевую лигатуру. При температуре сплава 670—700 °С вводят лигатуры алюминий — титан и алюминий — цирконий и после полного растворения всех лигатур с помощью графитового колокольчика вводят магний. При этом необходимо следить, чтобы магний все время был погружен в сплав. После ввода магния сплав рафинируют. Затем с поверхности ванны снимают шлак, сплав тщательно перемешивают и опять снимают шлак, после чего производят разливку. На протяжении всей плавки не допускается перегрев сплава свыше 750 °С. Для разливки применяют разливочные тигли и футерованные ковши емкостью до 1000 кг. Длина струи сплава должна быть минимальной. Тигли, ковши и разливочный инструмент обязательно прокаливают и покрывают специальными красками. Реклама:Читать далее:Плавка и разливка магниевых сплавов
Статьи по теме:
Главная → Справочник → Статьи → Блог → Форум |
Плавильные печи и печи для сплавов | Плавка и литье алюминия
Независимо от того, являетесь ли вы литейщиком, литейщиком, литейщиком, переработчиком или поставщиком сплавов, Inductotherm предлагает
высокоэффективных и проверенных в отрасли печей для переплавки и легирования.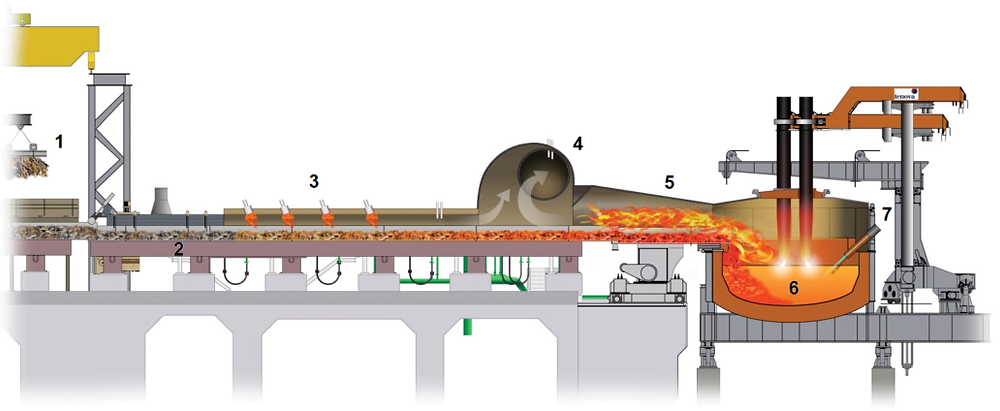
Индукция предлагает алюминиевой промышленности множество преимуществ
Inductotherm является лидером отрасли в разработке и производстве технологически передовых систем практически для всех металлов и материалов, включая алюминий. Алюминиевая технология Inductotherm работает от начала до конца. Преобразование глинозема в чистый алюминий и, в конечном счете, в полезные алюминиевые сплавы является энергоемким процессом, поэтому энергоэффективные печи производства Inductotherm доказали свою ценность на алюминиевых заводах по всему миру. Технологии индукционных печей Inductotherm могут конкурировать с более традиционными методами, такими как печи, работающие на ископаемом топливе, и печи сопротивления. Индукция практична для всех применений плавки алюминия и предлагает много преимуществ по сравнению с обычными печами для плавки алюминия.
Для каких применений алюминия можно успешно использовать индукцию?
- Литейное производство
- Ролики для алюминиевых заготовок
- Переработка/переплавка
- Литье под давлением
- Плавление стружки
- Литье по выплавляемым моделям
- Первичный алюминий
- Вторичный алюминий
Плавление алюминиевой стружки
Алюминиевую стружку сложно расплавить из-за ее склонности плавать на поверхности расплавленного алюминия при добавлении в большинство печей.
Система плавки алюминиевой стружки, использующая традиционную индукционную печь без тигельного стержня, может помочь решить эту проблему за счет присущего ей перемешивания. Перемешивание помогает погрузить и разбить комки алюминиевой стружки, что позволяет плавить их более эффективно, чем в печи с небольшим перемешиванием или без него.
Преимущества использования технологии индукционной плавки для плавки и литья алюминия:
- Гибкость в эксплуатации
- Системы индукционных печей меньше по размеру и имеют более управляемую площадь
- Легко заменяемые сплавы
- При необходимости можно немедленно отключить без дорогостоящих последствий
- Повышенная эффективность
- При индукции источником тепла является сам металл
- Газовая печь s примерно на 20% эффективнее, тогда как наши Система Acutrak ® DEH имеет КПД до 92 %, а большинство индукционных печей обычно имеют КПД 60 %.
0014
- В газовых и пламенных печах металл подвергается воздействию газов и кислорода, которые добавляют примеси к металлу
- Лучшая рабочая среда/дружелюбие к рабочему
- При индукционной плавке мало остаточного тепла и минимальный шум
- Газ- топочные печи выделяют много тепла, а топочные печи очень шумные
Впервые на индукции? Вот что вам нужно знать о том, как работает индукция
Когда ток протекает через индукционную катушку, формируется магнитное поле. Подача переменного тока через эту катушку приведет к изменению направления магнитного поля с той же скоростью, что и частота переменного тока. При добавлении алюминиевой шихты действует закон Фарадея. Наведенное напряжение приведет к протеканию тока через материал в магнитном поле. Когда ток течет через материал, возникает сопротивление движению электронов. Материалы, более устойчивые к потоку электронов, будут выделять больше тепла при протекании через них тока. Индукционное тепло генерируется в материале изделия за счет протекания тока. Затем тепло от поверхности продукта передается через материал с теплопроводностью.
Когда металл расплавляется, магнитное поле также приводит в движение ванну. Это называется индуктивным перемешиванием, и оно перемешивает ванну для получения более однородной смеси, которая способствует сплавлению. Системы водяного охлаждения обычно обеспечивают охлаждение теплообменников, однако, поскольку алюминий является низкотемпературным металлом, наша система прямого электрического нагрева Acutrak ® может охлаждаться воздухом, что делает ее отличным вариантом для плавки алюминия.
Лучшие индукционные печи и системы для алюминия
В зависимости от области применения Inductotherm предлагает различные передовые системы печей для плавки алюминия.
Прямой электрический нагрев (DEH)
- Точно контролируемая индукционная плавка
- Более быстрая, чистая и эффективная плавка
- Автономный блок питания и компактная печь для сокращения времени, усилий и затрат на установку
- Идеально подходит для литья под давлением, постоянных форм и алюминиевого литья
- Акутрак ® Система DEH хорошо подходит для операций литья под давлением, литья в постоянные формы и для литейных цехов
Печи Hybrid™
- Проверенная технология безтигельных индукционных печей
- Дополнительные преимущества верхнего кожуха канальной печи
- Большая гибкость сплава и огнеупорный срок службы
- Возможность использования инертного газа, удаления окалины и быстрой смены сплава
- Идеально подходит для аэрокосмической и коммерческой разливки слябов и заготовок
- Разливщики алюминиевых заготовок могут решить, что наша уникальная печь Hybrid™ станет для них отличным выбором
Традиционные тигельные печи Inductotherm
- Индукционные тигельные печи обеспечивают превосходную производительность и выдающуюся долговечность для всех нужд вашего плавильного цеха независимо от размера литейного производства
- Способен удовлетворить высокие требования литейщиков по выплавляемым моделям, специализированных литейных заводов и алюминиевой промышленности
- Dura-Line ® Печи предназначены для того, чтобы предоставить литейным предприятиям еще один выбор для малых и средних предприятий, в то время как наши печи с тяжелым стальным корпусом созданы для самых крупных литейных производств
Съемные тигельные печи
- Широко используются в алюминиевых цехах
- Убедитесь, что расплавленный алюминий всегда доступен из одного или другого тигля
- Обеспечивает большую гибкость сплава
- Выберите дизайн и конфигурацию в соответствии с вашим пространством и эксплуатационными требованиями
- Наши съемные тигельные печи, выталкивающая печь или подъемно-поворотная печь, могут помочь обеспечить постоянную доступность расплавленного алюминия из одного или другого тигля
Системы прямого электрического нагрева (DEH) Acutrak ® хорошо подходят для операций литья под давлением, литья в постоянные формы и для литейных производств.
УЗНАТЬ БОЛЬШЕ »
Печь Hybrid™компании Inductotherm использует конструктивные преимущества как бестигельных, так и канальных плавильных раздаточных печей.
УЗНАТЬ БОЛЬШЕ »
Индукционные плавильные печи Dura-Line ® идеально подходят для тех случаев, когда вам нужны большие характеристики печи в индукционной плавильной печи среднего размера.
УЗНАТЬ БОЛЬШЕ »
Печи Inductotherm с тяжелым стальным корпусом— самые прочные печи на современном рынке.
УЗНАТЬ БОЛЬШЕ »
Выталкивающие печиобеспечивают литейщиков цветных и драгоценных металлов чистыми, компактными и высокопроизводительными тигельными плавильными системами.
УЗНАТЬ БОЛЬШЕ »
Подъемно-поворотные печиявляются отличной альтернативой нашим выталкивающим печам, когда подпочвенные условия или ограничения фундамента делают нецелесообразным создание приямка, необходимого для цилиндров выталкивающей печи.
УЗНАТЬ БОЛЬШЕ »
Высокоэффективная и высококачественная плавка алюминия | Foundry Management & Technology
С ростом спроса на более легкие металлические отливки в таких отраслях, как автомобилестроение, двигатели внутреннего сгорания, бытовая техника и авиастроение, неудивительно, что алюминиевые литейщики и производители литья под давлением ищут способы более эффективной плавки. Однако, поскольку они не хотят, чтобы эффективность снижалась за счет качества продукции, также ведется поиск подходящих систем управления.
С этой целью Управление промышленных технологий Министерства энергетики США (OIT) и многочисленные партнеры реализовали два научно-исследовательских проекта, направленных на поиск способов оптимизации процесса плавки алюминия.
Чистая плавка алюминия Первый проект предусматривает нагрев алюминия погружением для снижения энергопотребления и воздействия на окружающую среду. Обычно отражательные печи используются для нагревания алюминия до температуры плавления с открытым пламенем, настенными горелками прямого нагрева. В большинстве случаев реверберационные печи имеют КПД плавления в среднем 26-31%. Кроме того, они отличаются высокой скоростью обработки и низкими эксплуатационными расходами и затратами на техническое обслуживание. Однако существуют высокие скорости окисления металлов, низкая эффективность и большие требования к площади.
OIT вместе с несколькими партнерами, включая Aleris Recycling, Amcast Industrial Corp., Исследовательский центр Министерства энергетики США в Олбани, E3M Inc., Hydro Aluminium North America, Logan Aluminium, Metaullics Inc., Национальную лабораторию Ок-Ридж, Secat Inc., SECO/ Warwick Corp., Trace Die Casting, Университет Кентукки и Wise Alloys L.L.C. — рассматривает печи с погружным нагревателем как хорошую альтернативу. Печи с погружным нагревателем нагревают металлическую ванну прямым контактом. Горелка погружается в расплавленный алюминий, а горелка с предварительным смешиванием обеспечивает циркуляцию горячих дымовых газов через корпус. Газы сгорания никогда не вступают в контакт с расплавленным алюминием, что помогает снизить потери на окисление. Погружная горелка обеспечивает лучшую передачу тепла к расплавленной загрузке, что также повышает термический КПД. С помощью одной погружной горелки уже достигнута эффективность плавления алюминия на уровне 60-65%, а еще один погружной электронагреватель лабораторного масштаба находится в разработке, что поможет разработать будущие модели, которые могут достичь эффективности до 97%.
Только в литейных цехах прогнозируется, что экономия энергии за счет использования печей с погружным нагревателем составит от 2,7 до 4,2 трлн БТЕ/год через 10 лет, при условии, что приблизительно 25% выплавляемого алюминия было произведено с помощью этого метода. Это может привести к экономии до 24 миллионов долларов США в год и обеспечить такие преимущества для окружающей среды, как сокращение выбросов углерода, NOx, CO, летучих органических соединений и твердых частиц.
Улучшенная плавка для машин для литья под давлением
Более эффективная плавка алюминия также находится в центре внимания проекта исследователей из Университета Кейс Вестерн Резерв в Кливленде. В частности, в рамках проекта будут рассмотрены многочисленные аспекты плавки алюминия и обращения с ним при литье под давлением, в том числе повышение энергоэффективности, а также улучшение качества расплавленного металла.
Литейщики для литья под давлением обычно также используют отражательные печи для плавки алюминия, но эффективность камер часто составляет менее 10%, когда в качестве топлива для сжигания используется газ. Из этих печей расплавленный металл переносится в небольшие раздаточные печи, также с эффективностью 10% или ниже. Неудивительно, что рост цен на топливо означает, что этот метод плавки будет продолжать дорожать.
Потребление энергии при плавке при литье под давлением можно было бы снизить, если бы плавка производилась в частично закрытых электрических печах или газовых печах с более высоким КПД. В предлагаемом исследовании будут участвовать производители и пользователи плавильных печей, изоляционных материалов, дегазационного и насосного оборудования, фильтровальных и перегрузочных ковшей. Помимо CWRU, у проекта есть ряд исследовательских партнеров, включая Североамериканскую ассоциацию литья под давлением, Коалиционное партнерство по литейным металлам, Inductotherm, Mercury Marine, Spartan Light Metals Products и Striko Dynarad. Есть надежда, что, используя более современное электроплавильное оборудование и процедуру частичного погружения, можно будет снизить потребление энергии более чем на 50%.