12. Выбор способа литья | Материаловед
При выборе способа изготовления отливки определяющими факторами являются технические требования, предъявляемые к изделию, и технико-экономические показатели (себестоимость детали в изготовлении, экономически оправданная серийность и др.), учитывающие расход металла, стоимость оборудования и технической оснастки.
Важную роль при выборе способа литья играет серийность производства. Размер серии и тип производства в зависимости от массы отливок можно определить по табл. 13.1. Отливки по массе подразделяют на мелкие (до 100 кг), средние (101 – 1000 кг), крупные (1001 – 5000 кг) и очень крупные (свыше 5000 кг). В единичном, мелкосерийном и серийном производствах отливки часто изготавливаются литьем в песчаные формы, по выплавляемым моделям. В крупносерийном и массовом производствах применяют литье под давлением, в кокиль, в оболочковые формы, центробежное литье, литье в сырые песчаные формы, изготавливаемые на формовочных машинах или автоматических линиях, и др.
В табл. 13.2 приводятся данные для выбора способа литья в зависимости от требований к отливкам (габариты отливок, точность их размеров, чистота поверхности), а также возможностей способа литья (серийность производства, коэффициент использования металла, процент выхода годных изделий, себестоимость процесса литья). При выборе способа литья надо обязательно учитывать его возможности по обеспечению нужной конфигурации отливки, требуемого качества структуры металла и уровня механических и специальных эксплуатационных свойств.
Таблица 13.1. Годовой выпуск отливок в зависимости от их массы и серийности производства
Тип серийности производства | Масса отливки, кг | ||||||
<20 | 20 — 100 | 101 – 500 | 501 – 1000 | 1001 – 5000 | 5001 – 10000 | >10000 | |
Годовой выпуск отливок одного наименования, шт | |||||||
Единичное | <300 | <150 | <75 | <50 | <20 | <10 | <5 |
Мелкосерий- ное | 300 – 3000 | 150 – 2000 | 75 – 1000 | 50 – 600 | 20 – 100 | 10 – 50 | 5 – 25 |
3000 – 35000 | 2000 – 15000 | 1000 – 6000 | 600 – 3000 | 100 – 300 | 50 – 150 | 25 – 75 | |
Крупносе- рийное | 35000 – 200000 | 15000 – 100000 | 6000 – 40000 | 3000 – 20000 | 300 – 4000 | 150 – 1000 | >75 |
Массовое | >200000 | >100000 | >40000 | >20000 | >4000 | >1000 | — |
Выбранный способ литья должен обеспечить качественное литье для данного сплава и при проведении последующей термической обработки отливок.
Отметим, что минимальные толщины стенок отливок можно получать лишь на сплавах с оптимальными физико-химическими и литейными свойствами. Иначе эти значения будут существенно больше.
Трудность выбора способа литья вызвана тем, что нередко отливка может быть изготовлена сразу несколькими способами, которые обеспечивают требуемые свойства литой детали. В этом случае решающими факторами, обусловливающими выбор рационального способа литья, являются серийность производства и экономичность процесса. Эти факторы (см. табл. 13.1 и 13.2), наряду с техническими характеристиками способа литья, могут помочь правильно выбрать технологический процесс литья.
Таблица 13.2. Технические возможности и сравнительные показатели различных способов литья
Показатель | ||||||
П | Д | К | В | О | Ц | |
Максимальная масса отливок, кг | 250000 | 50 | 2000 | 100 | 200 | 50000 |
Максимальный размер отливки, м | 20 | 1,2 | 2 | 1 | 1,5 | 10 |
Максимальная толщина стенки отливки, мм | 3 | 0,5 | 2,2 | 0,5 | 1,5 | 4 |
Класс размерной точности отливок2 | 5 – 16 | 3т – 9 | 5т – 13 | 3т – 11 | 7т – 15 | 6 — 15 |
Квалитет по ГОСТ 25346 – 893 | 13 | 11 | 12 – 13 | 11 | 14 | 13 — 14 |
Степень точности поверхности отливки4 | 7 – 22 | 2 – 11 | 4 – 14 | 3 – 13 | 6 – 17 | 4 — 14 |
Шероховатость поверхности (Rₐ), мкм | 8 – 100’ | 2,5 – 20 | 4 – 40 | 3,2 – 32 | 6,3 – 80 | 4 — 40 |
Минимальный припуск на обработку (на сторону), мм | 0,3 – 6 | 0,2 – 0,5 | 0,1 – 0,6 | 0,4 – 2 | 0,3 — 1 | |
Литейные уклоны, град.![]() | 0,5 – 3 | 0,5 – 1 | 0,5 – 1,2 | 1 – 2 | 1 – 2 | 3 — 6 |
Коэффициент использования металла, % | 60 – 70 | 90 – 95 | 75 – 80 | 90 – 95 | 80 – 95 | 70 — 90 |
Выход годного, % | 30 – 50 | 50 – 65 | 40 – 60 | 30 – 60 | 50 – 60 | 90 — 100 |
Относительная себестоимость 1т отливок | 1,0 | 1,8 – 2 | 1,2 – 1,5 | 2,5 – 3 | 1,5 – 2 | 0,6 – 0,7 |
Экономически оправданная серийность, шт. | Без огр.![]() | 1000 | 400 – 800 | 1000 | 200 – 500 | 100 — 1000 |
Преобладающие типы серийности производства5 | Ед, Мс, С, Кс | Кс, Мас | С, Кс, Мас | Ед, Мс, С | С, Кс, Мас | С, Кс, Мас |
Преобладающие разновид- ности отливок по массе6 | М, Ср, Кр, Окр | М, Ср | М | М, Ср | М, Ср, Кр, Окр |
Примечания:
- Способы литья: П – в песчаные формы, Д – под давлением, К – в кокиль, В – по выплавляемым моделям, О – в оболочковые формы, Ц – центробежное литье.
- Согласно ГОСТ 26645 – 85 с изменением №1, 1989г
- Номер квалитета (ГОСТ 25346 – 89) определялся по классу наибольшей размерной точности отливки (ГОСТ 26645 – 85) для каждого способа литья путем сопоставления значений допусков.
- Согласно ГОСТ 26645 – 85 с изменением №1, 1989г
- Ед – единичное, Мс – мелкосерийное, С – серийное, Кс – рупносерийное, Мас – массовое.
- М – мелкие, Ср – средние, Кр – крупные, Окр – очень крупные.
|
|
Каковы различные типы процессов литья
Здесь вы узнаете все о литье и процессах Потребность в сложных и высококачественных продуктах резко возросла по мере увеличения промышленных требований и областей применения. К счастью, существует несколько методов литья, с помощью которых можно производить сложные и точные изделия для различных областей применения и потребностей пользователей.
Очень важно понимать плюсы и минусы различных процедур, чтобы выбрать лучший метод литья для ваших производственных нужд. Эта страница содержит краткое описание нескольких методов литья, а также их преимущества и недостатки.
Что такое процесс литья?Процесс литья – это метод изготовления металлических деталей заданной формы путем заливки расплавленного металла в форму, его затвердевания и охлаждения до комнатной температуры. Он способен создавать сложные и детализированные изделия любого размера.
В результате литье позволяет изготавливать изотропные металлические детали в больших количествах, что делает их подходящими для массового производства. Кроме того, существует несколько форм литья для удовлетворения конкретных требований пользователей, которые варьируются в зависимости от используемого материала и формы.
Какие существуют типы процессов литья? Существуют различные типы процедур литья, и каждый процесс имеет свои преимущества и недостатки в зависимости от потребностей пользователя.
Литье в песчаные формы представляет собой гибкий процесс литья, который можно использовать для литья любых сплавов черных и цветных металлов. Он обычно используется в промышленных установках для массового производства автомобильных металлических деталей, таких как блоки цилиндров, головки цилиндров, коленчатые валы и т. д.
Форма, изготовленная из материалов на основе диоксида кремния, таких как природный или синтетический песок, используется в процедуре для получения гладкой поверхности формы. Поверхность пресс-формы разделена на две части: копейку (верхнюю половину) и тягу (нижнюю половину) (нижнюю половину). Используя заливочную чашку, расплавленный металл заливают в шаблон и дают ему затвердеть, чтобы сформировать окончательную форму. Наконец, излишки металла удаляются для окончательной обработки конечного изделия металлического литья.
Процесс литья в песчаные формы имеет как преимущества, так и недостатки.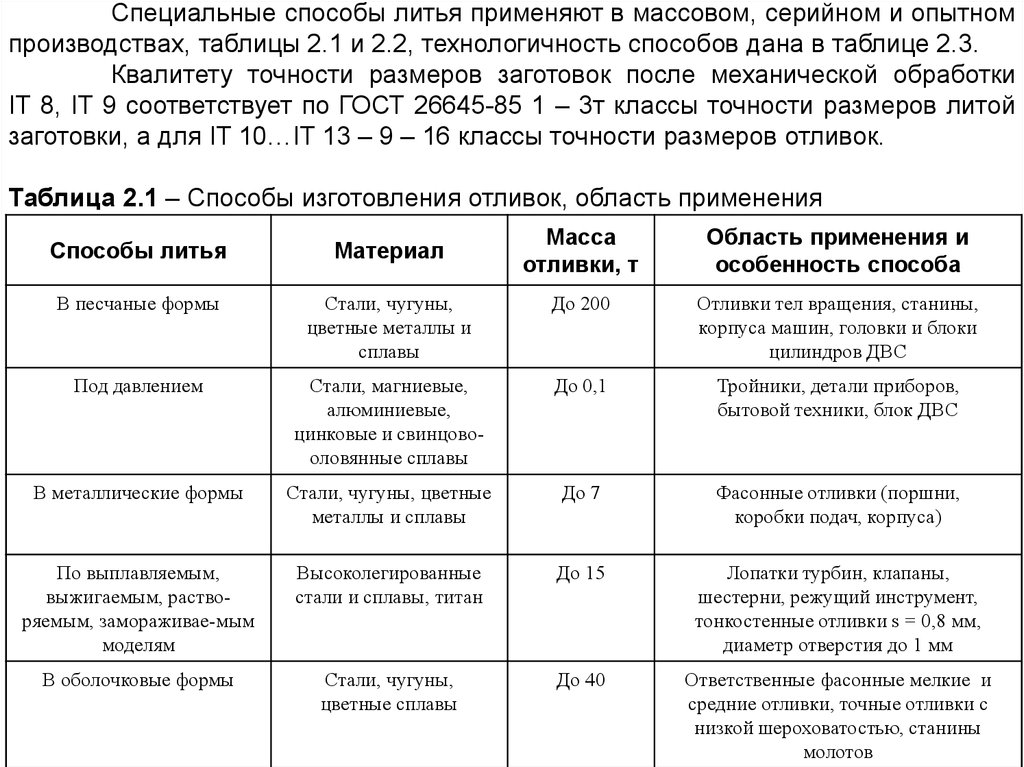
Гравитационное литье под давлением, также известное как литье в постоянные формы, позволяет изготавливать металлы и металлические сплавы с использованием многоразовых форм из таких металлов, как сталь, графит и другие. Этот процесс литья металла может производить различные предметы, такие как шестерни, корпуса редукторов, фитинги, колеса, поршни двигателя и так далее.
В этой процедуре непосредственная заливка расплавленного металла в полость кристаллизатора происходит под действием силы тяжести. Матрицу можно наклонить, чтобы отрегулировать наполнение для оптимального покрытия. Для изготовления предметов расплавленному металлу дают остыть и затвердеть внутри формы. В результате литье таких материалов, как сплавы свинца, цинка, алюминия и магния, некоторые бронзы и чугуны, становится все более популярным. В отличие от обычных процедур литья под давлением, этот процесс литья заполняет форму снизу вверх. Однако этот метод имеет большую скорость литья, чем литье в песчаные формы. Однако он существенно дороже из-за высокой стоимости металлических форм. Ознакомьтесь с его преимуществами и недостатками ниже.
В зависимости от давления существуют две формы литья под давлением. Существует два типа литья под давлением: литье под низким давлением и литье под высоким давлением. Литье под высоким давлением чаще используется в массовом производстве изделий сложной геометрической формы, требующих высокой точности. С другой стороны, литье под низким давлением является предпочтительным процессом литья для производства больших и простых деталей.
Цветные металлы и сплавы, такие как цинк, олово, медь и алюминий, впрыскиваются под высоким давлением в многоразовую форму, покрытую смазкой, при этом типе литья металла. Во избежание затвердевания металла во время процедуры быстрого впрыска поддерживается высокое давление. Наконец, после завершения процесса выполняется извлечение и отделка отливки для удаления остатков материала. В процессе заполнения формы литье под давлением отличается от литья под давлением. Литье под давлением включает в себя впрыск расплавленного металла в металлическую форму под высоким давлением. Затем расплавленный металл быстро затвердевает для получения желаемого результата.
Его преимущества и недостатки перечислены ниже.
4. Литье по выплавляемым моделямЛитье по выплавляемым моделям, также известное как литье по выплавляемым моделям, представляет собой метод производства металлических отливок путем заливки восковой модели огнеупорным материалом и связующим веществом для формирования одноразовой керамической формы, а затем заливки расплавленного металла в форму.
Литье по выплавляемым моделям — это дорогостоящий и трудоемкий процесс, который можно использовать для массового производства или сложных отливок для изготовления металлических изделий, таких как шестерни, велосипедные багажники, мотоциклетные диски и запасные части для взрывных машин.
Преимущества и недостатки перечислены ниже.
5. Литье из гипсаЛитье из гипса идентично литью в песчаные формы, однако форма состоит из материала, известного как «Парижский гипс». Гипс охлаждает металл медленнее, чем песок, из-за его ограниченной теплопроводности и теплоемкости, что помогает достичь высокой точности, особенно для деталей с узким поперечным сечением.
Однако он не подходит для высокотемпературных черных металлов. Литье по гипсовым формам позволяет изготавливать как небольшие отливки до 30 граммов, так и массивные отливки до 45 килограммов. На рисунке ниже, например, изображен литой компонент, созданный с помощью этого процесса, с толщиной сечения 1 мм.
Преимущества и недостатки перечислены ниже.
6. Центробежное литье Центробежное литье, также известное как ротационное литье, представляет собой метод производства цилиндрических объектов в промышленных условиях с использованием центробежных сил.
При этом способе литья металла расплавленный металл заливают в подготовленную фильеру. При высоком давлении центробежные силы способствуют распределению расплавленного металла внутри матрицы.
Существует три типа процессов центробежного литья: подлинное центробежное литье, полуцентробежное литье и вертикальное центробежное литье. В отличие от чистого центробежного литья, при полуцентробежном литье используется литник для полного заполнения формы. Однако из-за постоянного вращения расплавленный металл прилипает к стенкам при настоящем центробежном литье.
Вертикальное центробежное литье, с другой стороны, использует направленное формование так же, как и настоящее центробежное литье. Центробежное литье обычно дает вращающиеся конструкции, такие как цилиндры. Такие детали, как подшипники скольжения, диски сцепления, поршневые кольца и гильзы цилиндров, среди прочего. Кроме того, размещение металла в середине формы помогает уменьшить количество дефектов, таких как газовые пробоины, усадка и газовые карманы. Однако он подходит не для всех металлических сплавов.
Преимущества и недостатки перечислены ниже.
7. Литье по выплавляемым моделямМетод литья по выплавляемым моделям аналогичен литью по выплавляемым моделям, за исключением того, что модель изготавливается из пенопласта, а не из воска. После того, как конструкция изготовлена, ее покрывают огнеупорной керамикой путем окунания, нанесения покрытия, распыления или нанесения кистью. Затем расплавленный металл заливают в форму для создания желаемого продукта.
Этот процесс применим к широкому спектру материалов, включая легированную сталь, углеродистую сталь, легированный чугун, сплавы железа и другие. Процесс литья по выплавляемым моделям используется для изготовления таких продуктов, как корпуса насосов, пожарные гидранты, клапаны и фитинги. Литье по газифицируемым моделям имеет различные преимущества, в том числе высокую точность и аккуратность производства. Однако этот метод имеет несколько недостатков, которые делают его непригодным для использования в небольших объемах.
Преимущества и недостатки перечислены ниже.
8. Вакуумное литьеКак следует из названия, вакуумное литье — это тип литья, при котором производство происходит под вакуумом 100 бар или ниже для выпуска газа из полости формы. Для устранения пузырей и воздушных карманов расплавленный металл заливают в полость формы внутри вакуумной камеры.
Вакуумное вакуумирование полости штампа предотвращает попадание газов в полость во время процесса впрыска металла. Наконец, металл отверждается в нагревательной камере перед извлечением из формы. Метод вакуумного литья под давлением широко используется в различных отраслях промышленности, включая автомобильную, аэрокосмическую, электронную, морскую и телекоммуникационную. В результате, структурные компоненты шасси и элементы кузова транспортных средств входят в число компонентов, производимых с помощью этой технологии производства.
Преимущества и недостатки перечислены ниже.
Литье под давлением, в частности, является многообещающим процессом литья для критических с точки зрения безопасности элементов автомобильных систем. Примерами являются шарниры пространственной рамы, алюминиевые передние поворотные кулаки, рамы шасси, кронштейны или узлы. Этот процесс литья металла сочетает в себе преимущества литья и ковки. Например, высокое давление, используемое во время затвердевания, помогает предотвратить усадку и пористость. Однако из-за потребности в специализированных инструментах он не так распространен в крупном производстве, как другие процедуры литья.
Жидкая ковка, также известная как литье под давлением, представляет собой гибрид формовки металлов, в котором литье в несъемные формы сочетается с ковкой в штампах за одну операцию. В этой процедуре определенное количество расплавленного металлического сплава заливают в пресс-форму и формуют под давлением. Затем металлическую часть нагревают до температуры плавления и извлекают из пресс-формы.
Преимущества и недостатки приведены ниже.
10. Непрерывное литьеОбеспечивает непрерывное массовое производство металлических профилей с постоянным поперечным сечением, как следует из названия. Этот стиль литья обычно используется при производстве стальных стержней.
Кроме того, вертикальная разливка обеспечивает полунепрерывную разливку, такую как заготовки, слитки, прутки и т.д. Расплавленный металл заливают с расчетной скоростью в водоохлаждаемую форму с открытым концом, что позволяет сформировать твердую металлическую поверхность на жидком металле в сердечнике. Таким образом, затвердевание металла происходит снаружи внутрь. После завершения этой операции металлические пряди можно извлекать из формы неограниченное время. Механические ножницы или движущиеся кислородно-ацетиленовые горелки можно использовать для резки материалов на заданную длину.
Непрерывное литье производит изделия, которые обычно являются однородными, однородными и плотными. Тем не менее, это ограничено таким использованием. К другим преимуществам и недостаткам относятся:
Формование в оболочку — это процедура литья в форму, в которой используются одноразовые формы. Это похоже на процесс литья в песчаные формы, за исключением того, что вместо опоки с песком затвердевшая оболочка из песка образует камеру формы. Песок, используемый при литье в песчаные формы, более мелкий, и он смешивается со смолой, чтобы его можно было подвергнуть термической обработке и вклеить в оболочку, окружающую конструкцию. Оболочечная формовка используется для создания промышленных изделий, таких как корпуса коробок передач, шатуны, маломерные лодки, капоты автомобилей, цилиндрические головки, распределительные валы, гидроблоки и т.д. Изделия для литья имеют гладкую поверхность и точные размеры.
Однако ограничения по размеру и весу деталей являются ограничением этого типа литья. К другим преимуществам и недостаткам относятся:
Передайте ваши потребности в литье на аутсорсинг NabTech Engineering Крайне важно выбрать подходящий метод литья и опыт для вашей продукции. Nabtech Engineering , известный производитель металлических компонентов, предоставляет высококачественные услуги. Мы обслуживаем широкий спектр предприятий с многолетним опытом. Наша клиентура включает в себя все, от автомобилей до товаров для дома. Это также относится к другим отраслям, таким как декоративные изделия и уличные фонари.
11 Различные типы процесса литья
С увеличением промышленных требований и областей применения параллельно растет спрос на сложные и высококачественные продукты. К счастью, существуют различные типы процессов литья, с помощью которых можно производить сложные и точные изделия для различных областей применения и потребностей пользователей.
Чтобы выбрать правильный метод литья для ваших производственных требований, полезно знать преимущества и недостатки этих методов. В этой статье представлен краткий обзор различных типов процессов литья, их плюсов и минусов.
Обзор процесса литья
Процесс литья — это производственный метод, при котором получают металлические детали заданной формы путем заливки расплавленного металла в форму, затвердевания и охлаждения до комнатной температуры. Он способен производить сложные и сложные детали, независимо от их размеров.
Литье может производить изотропные металлические детали в больших количествах, что делает его пригодным для массового производства. Кроме того, для удовлетворения конкретных требований пользователей существуют различные типы литья, которые различаются по используемому материалу и форме.
Различные типы процессов литья
Существуют различные типы процессов литья, и каждый процесс имеет свои преимущества и недостатки в соответствии с требованиями пользователя.
1.
Процесс литья в песчаные формыЛитье в песчаные формы представляет собой универсальный процесс литья, который можно использовать для литья любого металлического сплава, черного или цветного. Он широко используется для массового производства в промышленных установках, таких как автомобильные литые детали, такие как блоки цилиндров, головки цилиндров, коленчатые валы и т. д.
В процессе используется форма, изготовленная из материалов на основе диоксида кремния, таких как природный или синтетический песок, формирующий гладкую поверхность формы. Поверхность пресс-формы состоит из 2 частей: гребня (верхняя половина) и волочения (нижняя половина). Расплавленный металл заливают в форму с помощью заливочной чашки и оставляют затвердевать, чтобы принять окончательную форму. Наконец, выполняется обрезка лишнего металла для окончательной обработки конечного изделия металлического литья.
Литье в песчаные формы имеет свои преимущества и недостатки.
Преимущества | Недостатки |
Относительно низкая себестоимость, особенно при мелкосерийном производстве | Низкая степень точность по сравнению с альтернативными методами |
Изготовление крупногабаритных деталей | Трудно использовать этот метод для изделий с заданными характеристиками размеров и веса |
Литье как черных, так и цветных сплавов | В результате получаются продукты с шероховатой поверхностью |
Способность к переработке | |
Обработка металлов с высокими температурами плавления, таких как сталь и титан | 90 194 |
2.
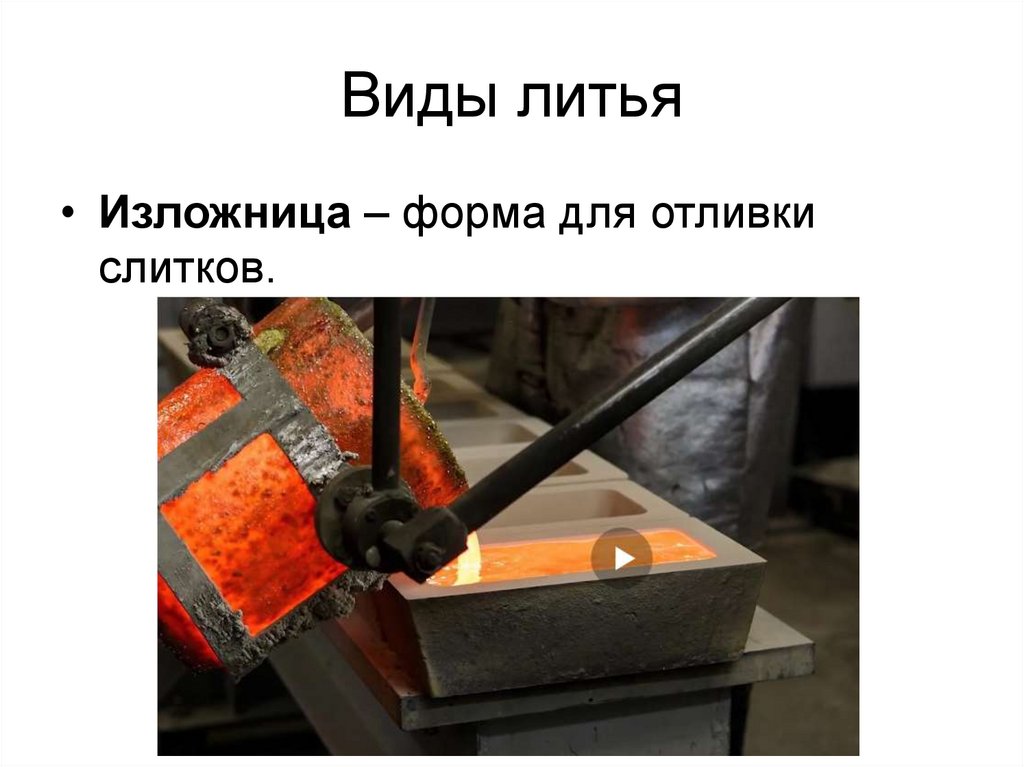
Гравитационное литье под давлением, также обычно известное как литье в постоянные формы, использует многоразовые формы из металла, такого как сталь, графит и т. д., для изготовления металла и металлических сплавов. Этот тип литья металла позволяет изготавливать различные детали, такие как шестерни, корпуса редукторов, фитинги, колеса, поршни двигателей и т. д.
В этом процессе прямая заливка расплавленного металла в полость формы происходит под действием силы тяжести. Для лучшего покрытия матрицу можно наклонять, чтобы контролировать наполнение. Затем расплавленному металлу дают остыть и затвердевать внутри формы, образуя изделия. В результате этот процесс делает литье из таких материалов, как сплавы свинца, цинка, алюминия и магния, некоторые виды бронзы и чугуна, более распространенным явлением.
Этот процесс литья основан на восходящем подходе к заполнению формы, в отличие от других процессов литья под давлением. Хотя этот процесс имеет более высокую скорость литья, чем литье в песчаные формы. Но он относительно дороже из-за дорогих металлических форм. Проверьте его преимущества и недостатки ниже.
Преимущества | Недостатки |
Обеспечивает лучшее качество поверхности изделий за счет быстрого затвердевания | Литейный комплекс объекты сложные |
Литейные изделия имеют высокую точность и жесткие допуски | Затраты на изготовление форм выше |
Многоразовые формы экономят время и повышают производительность, что снижает производственные затраты | Механизм выталкивания отливки из формы иногда образует вмятину на изделии |
Изделия обладают лучшими механическими свойствами | |
Производство тонкостенных изделий |
3.

Существует два типа литья под давлением в зависимости от давления. А именно, литье под низким давлением и литье под высоким давлением. Литье под высоким давлением более популярно для массового производства изделий сложной геометрии, требующих высокой точности. Принимая во внимание, что для производства крупных и простых деталей предпочтительным процессом литья под низким давлением является литье под низким давлением.
При этом типе металлического литья цветные металлы и сплавы, такие как цинк, олово, медь и алюминий, впрыскиваются в многоразовую форму, покрытую смазкой, под высоким давлением. Таким образом, высокое давление поддерживается на протяжении всего процесса быстрого впрыска, чтобы избежать затвердевания металла. Наконец, после завершения процесса происходит извлечение литья и отделка для удаления лишнего материала.
Литье под давлением отличается от литья под давлением процессом заполнения формы. При литье под давлением используется впрыск расплавленного металла под высоким давлением в металлическую форму. Затем расплавленный металл быстро затвердевает для получения требуемого продукта.
Его преимущества и недостатки перечислены ниже.
Преимущества | Недостатки |
Высокая точность и допуск размеров | Относительно высокая стоимость инструмента |
Высокая эффективность и хорошее качество продукции | Ограничено цветными металлами |
Меньшая потребность в механической обработке после литья | Сложно обеспечить механические свойства изделий, поэтому не используется для конструкционных деталей |
Быстрое охлаждение расплавленного металла для повышения производительности | Полная установка требует больших капиталовложений |
Процесс может продолжаться дольше без необходимости замены матрицы |
Подробнее: Выберите правильный процесс между литьем под давлением и литьем в песчаные формы для ваших приложений.
4.
Литье по выплавляемым моделямЛитье по выплавляемым моделям, также известное как литье по выплавляемым моделям, представляет собой процесс, при котором восковая модель покрывается огнеупорным материалом и связующим веществом для формирования одноразовой керамической формы, а затем расплавленный металл заливается в форму для изготовления металлических отливок. Литье по выплавляемым моделям – это дорогой и трудоемкий процесс, который может использоваться для массового производства или в сложных отливках для производства изделий из металлического литья, начиная от шестерен, велосипедных багажников, мотоциклетных дисков и запасных частей к дробеструйным машинам.
Ниже перечислены его преимущества и недостатки.
Преимущества | Недостатки | |
Может производить детали с тонкими стенками, большей сложностью и высоким качеством поверхности | Требует рабочей силы для использования | |
Снижает необходимость механической обработки после литья | Увеличивается производственный цикл | |
Может отливать трудноплавкие сплавы, такие как нержавеющая сталь, тонкая сталь и т.![]() | Более высокая стоимость изготовления форм | |
Из-за отделения оболочковой формы можно отливать под углом 90 градусов | Новые требования к штампу для создания восковых моделей для каждого цикла литья 194 | |
Припуск на усадку в форме |
5.
Гипсовая отливка Процесс аналогичен литью в песчаные формы, за исключением того, что форма изготовлена из смеси, называемой «Парижский гипс». Из-за низкой теплопроводности и теплоемкости гипс медленнее охлаждает металл по сравнению с песком, что позволяет добиться высокой точности, особенно для деталей тонкого сечения. Однако он не подходит для высокотемпературных черных металлов. В частности, с помощью процесса литья в гипсовые формы можно изготавливать небольшие отливки весом 30 грамм, а также большие отливки весом 45 кг. Например, на изображении ниже показан литой компонент с толщиной сечения 1 мм, изготовленный с помощью этого процесса.
Узнайте больше о его преимуществах и недостатках.
Преимущества | Недостатки |
Гладкая поверхность операции | |
Более высокая точность размеров, чем при литье в песчаные формы | Ограниченное применение для алюминиевых и медных сплавов |
Возможность отливки сложных форм с тонкими стенками | Может потребоваться частая замена гипсового формовочного материала |
Не подходит для тугоплавких материалов | |
Более длительное время охлаждения, влияющее на производительность | |
Нестабильный материал по сравнению с песком, который может повлиять на весь процесс |
6.

Центробежное литье, также известное как центробежное литье, представляет собой процесс промышленного изготовления цилиндрических деталей с помощью центробежных сил. Этот тип литья металла использует предварительно нагретую фильеру, в которую заливается расплавленный металл. Центробежные силы помогают распределить расплавленный металл внутри матрицы под высоким давлением.
Существуют три варианта центробежного литья; настоящий процесс центробежного литья, процесс полуцентробежного литья и процесс вертикального центробежного литья. При полуцентробежном литье, в отличие от настоящего центробежного литья, форма полностью заполняется с помощью литника. Однако при истинном центробежном литье расплавленный металл прилипает к бокам из-за непрерывного вращения. Напротив, вертикальное центробежное литье, как следует из названия, использует направленное формование, следуя тому же процессу, что и настоящее центробежное литье.
Как правило, при центробежном литье получают вращающиеся формы, такие как цилиндры. В частности, такие детали, как подшипники скольжения, диски сцепления, поршневые кольца, гильзы цилиндров и т. д. Кроме того, заливка металла в центр формы помогает уменьшить дефекты, такие как дульные отверстия, усадка и газовые карманы. Однако он подходит не для всех видов металлических сплавов.
Преимущества | Недостатки |
Повышение производительности процесса и снижение потерь | Центробежное литье требует больших капиталовложений |
Отливка имеет высокую плотность и практически не имеет дефектов | Требование квалифицированной рабочей силы |
Процесс удобен для изготовления цилиндрических и гильзовых композиционных металлических отливок | Производство специальных форм |
Отверстия и стояки не требуются |
7.
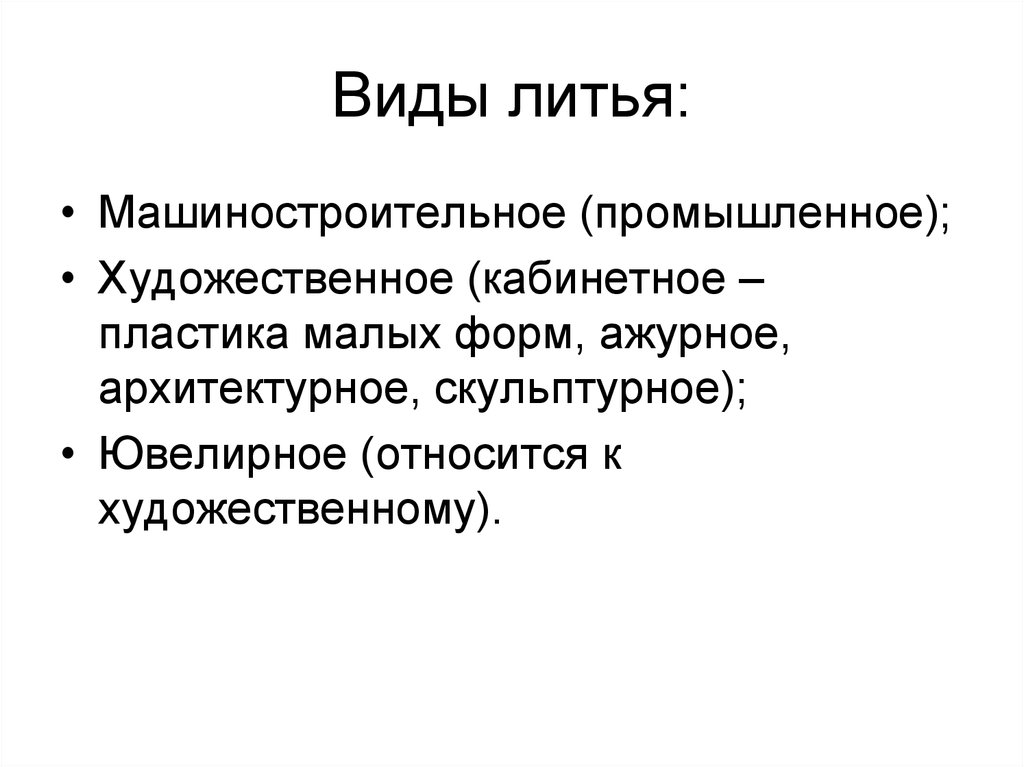
Метод литья по газифицируемым моделям аналогичен литью по выплавляемым моделям с той разницей, что вместо воска для выкройки используется пена. После того, как рисунок сформирован, покрытие огнеупорной керамикой происходит путем окунания, нанесения покрытия, распыления или нанесения кистью. Затем расплавленный металл заливают в форму, чтобы сформировать желаемый продукт.
Этот метод можно использовать для различных материалов, таких как легированная сталь, углеродистая сталь, легированный чугун, ферросплав и т. д. В частности, такие продукты, как корпуса насосов, пожарные гидранты, клапаны и фитинги, изготавливаются методом литья по газифицируемым моделям.
Литье по выплавляемым моделям обладает многочисленными преимуществами, включая высокую точность и высокую точность производства. Однако у этого процесса есть несколько ограничений, которые делают его непригодным для приложений с небольшим объемом.
Преимущества | Недостатки |
Высокая точность литья | Высокие затраты на низкий объем |
Позволяет в гибкости.![]() | |
Чистое производство | Многие производственные процессы и более длительное время доставки |
Экономический для высокого объема производства |
8.
Вакуумное литьеВакуумное литье, как следует из названия, — это тип литья, при котором производство происходит под вакуумом под давлением 100 бар или ниже для отвода газа из полости формы. В этом процессе расплавленный металл заливается в полость формы внутри вакуумной камеры, чтобы устранить пузырьки и воздушные карманы. Вакуумная откачка полости штампа уменьшает захват газов внутри полости во время процесса впрыска металла. Наконец, металл отверждается в нагревательной камере и извлекается из формы.
Процесс вакуумного литья под давлением популярен в различных отраслях промышленности, включая автомобильную, аэрокосмическую, электронную, морскую, телекоммуникационную и т. д. В результате некоторые компоненты, изготавливаемые с помощью этого производственного процесса, включают структурные компоненты шасси и детали автомобильного кузова.
Преимущества | Недостатки |
Снижение пористости, улучшение механических свойств и качества поверхности литья под давлением | Высокая стоимость оснастки |
Производство тонкостенных изделий | Форма, используемая в процессе, имеет короткий срок службы |
Возможна сварка и термическая обработка изделий | Возможные проблемы пустотности |
Подходит для мелкосерийного производства | |
Не требует дорогостоящего твердосплавного чистового инструмента | |
Уменьшает воздушные карманы и пузырьки на ранних стадиях |
9.

Ковка в жидком состоянии или литье под давлением представляет собой гибридный процесс обработки металлов давлением, который объединяет литье в неразъемные формы и штамповку в один этап. В этом процессе определенное количество расплавленного металлического сплава впрыскивается в пресс-форму и прикладывается давление для придания ему формы. Затем металлическую часть нагревают до температуры плавления и извлекают из матрицы.
В частности, литье под давлением является потенциальным процессом литья критически важных с точки зрения безопасности деталей автомобильных систем. Например, шарниры пространственной рамы, алюминиевые передние поворотные кулаки, рамы шасси, кронштейны или узлы.
Этот тип металлического литья сочетает в себе преимущества процессов литья и ковки. Например, высокое давление, применяемое во время затвердевания, помогает предотвратить усадку и пористость. Однако из-за особых требований к инструментам он не так популярен, как другие процессы литья для массового производства.
Преимущества | Недостатки |
Устраняет внутренние дефекты, такие как поры, усадочные отверстия и усадочная пористость | Меньшая гибкость геометрии детали |
Низкая шероховатость поверхности | Низкая производительность |
Может предотвратить появление трещин в литье | Высокие требования к механической обработке | Высокопрочные компоненты | Требует точного контроля, замедления всего процесса |
Отсутствие потерь материала |
10.
Непрерывное литье Как следует из названия, он позволяет последовательное массовое производство металлических профилей с постоянным поперечным сечением. Этот тип литья популярен при производстве стальных стержней. Кроме того, вертикальная разливка создает полунепрерывную разливку, такую как заготовки, слитки, прутки и т. д.
В этом процессе расплавленный металл заливают с расчетной скоростью в водоохлаждаемую форму с открытым концом, что позволяет сформировать поверхность твердого металла на жидком металле в центре. Таким образом, затвердевание металла происходит снаружи внутрь. После завершения этого процесса металлические нити могут непрерывно извлекаться из формы. Изделия заданной длины могут быть отрезаны механическими ножницами или передвижными кислородно-ацетиленовыми горелками.
Как правило, изделия, созданные методом непрерывного литья, однородны, однородны и плотны. Однако это также ограничивает его использование такими приложениями. Некоторые другие преимущества и недостатки:
Преимущества | Недостатки |
Разнообразный размерный ряд отливок от полосы толщиной в несколько миллиметров до более крупных заготовок и слябов 9 0194 | Необходимость постоянного охлаждения форм, в противном случае возникает усадка по центральной линии |
Снижение затрат благодаря непрерывному производству | Отливка только простых форм с постоянным поперечным сечением |
Низкие потери материала | Требует большой площади и больших первоначальных инвестиций |
11.
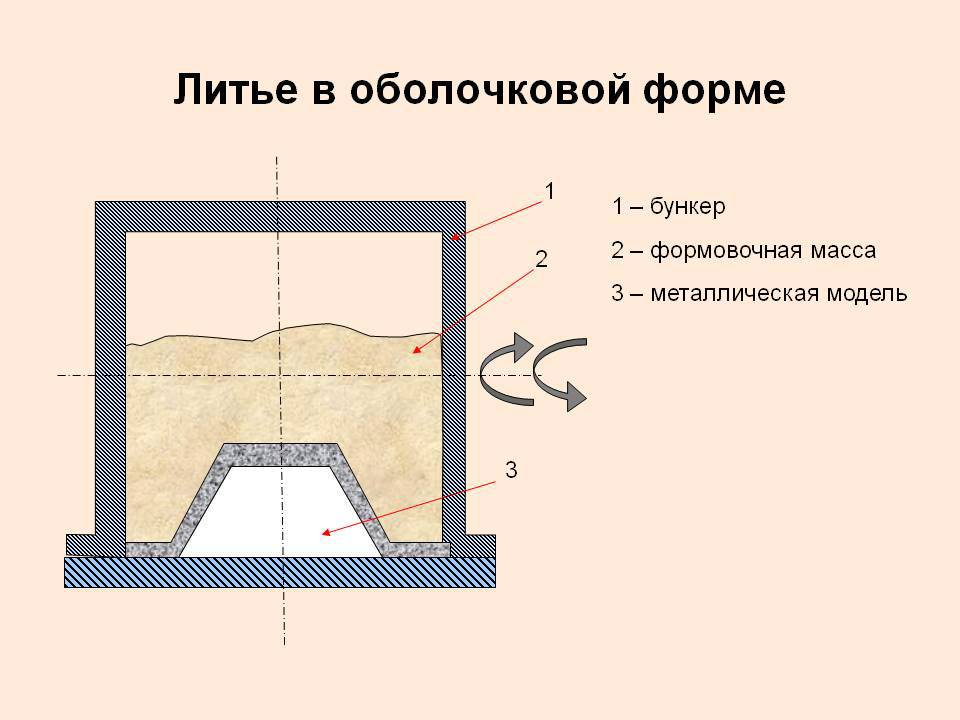
Формование в оболочку — это процесс литья в одноразовые формы. Это похоже на процесс литья в песчаные формы, за исключением того, что затвердевшая оболочка из песка образует полость формы вместо опоки из песка. Используемый песок мельче, чем тот, который используется при литье в песчаные формы, и он смешивается со смолой, чтобы его можно было подвергнуть термической обработке и затвердеть в оболочку вокруг рисунка.
Из литья в кожух изготавливаются промышленные изделия, например, корпуса редукторов, шатуны, маломерные лодки, капоты грузовых автомобилей, цилиндрические головки, распределительные валы, гидроблоки и т. д.
Изделия для литья обладают хорошей чистотой поверхности и точностью размеров. Однако ограничение этого вида литья включает ограничения по размеру и весу деталей. Некоторые другие преимущества и недостатки:
Преимущества | Недостатки |
Литье тонких и сложных деталей | Не подходит для мелкосерийного производства |
Неквалифицированная рабочая сила | Ограничения по размеру и весу |
Требуется специальный рисунок металла, что делает его дорогим для крупных отливок | |
Учет дефектов поверхности |
Основные этапы производства различных отливок
В основном процессы литья состоят из нескольких основных этапов, таких как изготовление модели, изготовление формы, выбор и заливка металлических сплавов и, наконец, отделка отлитой детали.
- Изготовление модели
Для создания модели важно определить форму формы. Для этого в качестве материалов используются воск, песок, пластик или даже дерево.
- Изготовление литейных форм
Далее возникает потребность в изготовлении различных форм для литья. Одноразовая форма может быть изготовлена из песка, гипса или керамической оболочки. У каждого из них свой способ производства. Также в печи обжигают узоры из пенопласта или воска.
- Выберите металлические сплавы
Металлические отливки производятся из черных или цветных сплавов. Сплавы представляют собой химическую смесь элементов с механическими свойствами, которые лучше всего подходят для окончательного литья. Где ферросплавы включают сталь, ковкий чугун и серый чугун. В то время как цветные металлы включают алюминиевые сплавы, бронзу и медь.
- Расплавление и заливка сплава
После выбора металлических сплавов следующим шагом является заливка металла в форму.