Высокотемпературная керамика для промышленных нагревателей Heatle
Керамика широко применяется в электротехнике как хороший изолятор и тепловой проводник. Данное сырье в промышленных и повседневных сферах деятельности пользуется высоким спросом по ряду причин, ведь свойства, которыми обладает керамика, не можно сравнить ни с одним другим материалом. Самыми важными преимуществами является способность выдерживать сверхвысокие термические нагрузки и их резкие перепады. Немаловажным фактором считается также и не подвластность коррозии. Если провести черту, сравнивая керамику с техническими аналогами вроде полимеров и металла, ее преимущества выделяются четко:
-
Металлы через время поддаются коррозии, а керамика нет.
-
Полимеры не выдерживают действия высоких температур (например, самый высоко выдержанный полимер тетрафторэтилен кристаллизуется при 600 градусах Цельсия, остальные при значительно меньших температурах), а керамика зависимо от показателя тугоплавкости без изменений в структуре может выдерживать температуры от 3500 до 4040°С.
Преимущества технической керамики в составе промышленного нагревателя:
-
Не утрачивает форму и не изменяет вид под влиянием агрессивных факторов;
-
Высокотвердая;
-
Механически прочная;
-
Характеризуется высоким показателем диэлектрики.
От качества керамики зависят свойства нагревательного элемента, поэтому HEATLE придает большое значение сырью, входящему в оснастку нагревателя. Керамический материал влияет на способность тепловой отдачи и поддержке температурного баланса по всему рабочему телу нагревательного прибора. Керамическое сырье низкого качества снижает показатель удельной мощности, поэтому наши технологи при тестировании нагревателей проводят тщательный отбор устройств поставляемых клиентам.
Если у керамического нагревателя при длительной температурной эксплуатации пересыхает керамическое покрытие или даже рассыпается, следует понимать, что приобретенное вами устройство низкого качества.
Компания HEATLE заинтересована в высоком качестве поставляемых нагревателей, так как дорожит своей репутацией. Мы тщательно контролируем состав сырья, из которого изготавливается наш товар.
Техническая керамика соответствует европейскому стандарту и требованиям ГОСТ, а также имеет сертификаты качества. На основе этого мы можем поставлять высококачественные патронные нагреватели, удельная мощность которых составляет 10 Вт/см2, у кольцевых нагревателей данный показатель может равняться Вт/см2.
Для изготовления инфракрасных элементов нагрева используется особый вид керамики под названием кордиерит. Особенностью такого материала является обеспечение максимальной тепловой отдачи во время рабочего процесса. Промышленные виды устройств как кольцевые, гибкие, плоские и патронные ТЭНы в конструкции имеют такую разновидность керамики, как периклаз. Клеммные коробки производят из технического фарфора (тоже разновидность керамического сырья), который обладает высокими диэлектрическими свойствами.
Периклаз. Применение и характеристика
Данная разновидность керамического сырья характеризуется высокой теплопроводностью и относится к хорошим электрическим изоляторам. Периклазу также свойственно переносить повышенные температуры. Основой материала является оксид магния, который добывают из морской воды или в шахтах. Чистую форму окиси магния можно получить под воздействием высокой температуры. Чтобы искусственно вывести периклаз, материал поддают обжигу при температуре свыше 1600 градусов. Природный магнезий для получения периклаза плавят с помощью электрического воздействия. Преимущества использования периклаза для электронагревателей:
-
Высокие температурные и огнеупорные свойства;
-
Хорошая изоляционная способность;
-
Устойчивость к щелочам;
-
Высокое электросопротивление.
В виде мелкодисперсного порошка периклаз используют в качестве засыпки, которая обладает гигроскопическими свойствами и натягивает в себя влагу. По этим причинам рекомендуется хранить нагреватели с периклазом в сухих помещениях. Для избегания возможности короткого замыкания патронники перед работой запускают в режиме разогрева, не создавая высокотемпературную нагрузку. Подготовка к полноценной работе должна проводиться при напряжении в 12 В.
Кордиерит. Применение и характеристика
Кордиерит считается относительно новым видом керамического материала используемого в промышленных целях. Он обладает низким коэффициентом расширения при температурных нагрузках. Преимущества использования кордиерита для электронагревателей:
-
Высокие свойства термоизоляции;
-
Хорошая электроизоляция;
-
Устойчивость к тепловым ударам;
-
Хорошая переносимость резких перепадов температуры;
-
Скорость переключения может составлять меньше 2 секунд.
Наличие описанных характеристик определило использование кордиерита в производстве инфракрасных элементов нагрева. Данный материал относится к островным силикатам и имеет два подтипа: пористый и плотный.
Технический фарфор. Описание и характеристика.
Технический фарфор выделяется высоким уровнем изоляции в электротехнике. Его еще называют: кварцевым фарфором, электрофарфором и прессфарфором. Преимущества использования технического фарфора для электронагревателей:
-
Высокая работоспособность в низковольтной и высоковольтной технике;
-
Стойкость к влажной среде;
-
Стойкость к поверхностной утечке тока.
Керамический фарфор не сгорает и не изменяет свой вид и особенности при сверхвысокой температуре. Благодаря таким характеристикам его применяют при изготовлении клеммных колодок.
Керамический фарфор относится к силикатам природного происхождения. Добывают его из каолиновой глины. Материал может делиться на разные подгруппы, зависимо от химического состава и наличия кристаллических компонентов. Фарфор сложной конфигурации в промышленности добывают сухой или мокрой прессовкой.
Керамические материалы зависимо от своих особенностей используются для разных типов нагревателей, которые в свою очередь предназначаются для конкретной среды, места установки и подачи определенных температурных значений. Вся продукция, поставляемая HEATLE, проходит ряд стандартных проверок на функциональность и качество. Заказать любой тип промышленного нагревателя, можно в любое время, воспользовавшись формой-онлайн или заказав обратную связь.
Портал керамики — Обжиг керамики. Режимы обжигов различных видов керамических изделий. Процессы, происходящие при обжиге.
- org/ListItem»>
Статьи
- Обжиг керамики. Режимы обжигов различных видов керамических изделий. Процессы, происходящие при обжиге.
Регистрация Вход
Карта сайта
Обжиг керамики. Режимы обжигов различных видов керамических изделий. Процессы, происходящие при обжиге.
- Автор: Геннадий Сурков
- печи
- обжиг
В обжиге происходят все основные изменения в глине и глазури, после которых и образуется то, что мы называем керамикой. Обжиг — это технологический процесс, параметры которого найдены практическими испытаниями, и он должен быть проведен так, как этого требуют обжигаемые изделия. Интуитивно понятно, что мы хотим вынуть из печи. От утиля ожидается звонкая прочность и некоторая пористость, чтобы он впитывал глазурь. От бисквитного фарфора — приятная шелковистость и белизна. Блестящие глазури должны хорошо блестеть, а матовые быть по-настоящему матовыми. Никто не желает кривья и треска, прилипшей к полке глазури, и всякого рода пузырей и наколов.
Сформулировать это понимание на языке цифр сложнее. Во время нагрева множество химических соединений, из которых состоит наше сырое изделие, претерпевает серьезные изменения. Дегидратация, фазовые превращения, химические взаимодействия, растворение и кристаллизация — вот их неполный список. До сих пор не существует полной теоретической модели, по которой можно было бы заранее предсказать результат, а если бы она существовала, нам потребовался бы месяц исследований состава глины и глазури, чтобы дать точное задание на расчет. Нам остается проводить эксперимент за экспериментом, выясняя, что важно, а что нет, какой должна быть температура, нужна ли выдержка, и почему
Но мы хотим получать задуманные эффекты и запланированные свойства изделий, и для этого нужно иметь возможность контролировать параметры обжига и управлять ими, зная основные, самые общие, принципы.
Теперь конкретно об этих принципах.
1. Виды обжига, зачем они нужны и что нужно контролировать прежде всего.
2. Электрические печи и два слова про другие.
1. Виды обжига, зачем они нужны и что нужно контролировать прежде всего.
- Условно разделим все материалы на 4 группы:
- — Фарфор — много плавней, при нагревании в черепке образуется много жидкой фазы. Сюда же отнесем каменные массы.
- — Фаянс — жидкой фазы почти что нет. Кстати, и фаянса-то уже никто не выпускает в его прежде классическом варианте.
..
- — Майолика — здесь будем так называть изделия из красной глины, в том числе гончарку, терракоту и т.п.
- — Шамот — по химическому составу — любой из вышеперечисленных материалов. Отличается от них тем, что содержит зерна уже обожженного материала, связанные пластичной глиной.
Для каждой группы материалов условно выделим некоторые объединяющие их моменты.
Фарфоровая схема обжига.
Сначала проводят первый, утильный, обжиг. То есть обжигают высохшие изделия без глазури. Температуру выбирают в интервале 800 — 1000°С. После первого обжига изделия приобретают прочность, достаточную даже для машинного глазурования (на конвеерной линии). Изделия остаются пористыми, но, если есть трещины, их легко выявить (по характерному дребезжанию) простукиванием деревянной палочкой. При глазуровании не надо церемониться с изделием так, как это бывает в случае сырца (однократный обжиг). Можно легко глазуровать изделия окунанием, даже если они метровых габаритов. Изделия после этого обжига называют утилем.
Затем проводят второй обжиг.Перед глазурованием и, соответственно, перед вторым, политым, обжигом, на изделие наносят подглазурную роспись. Педанты технологии после этого проводят еще и промежуточный закрепляющий обжиг, чтобы краски не смылись при окунании в глазурь.Политой обжиг, т.е. обжиг полуобожженного заглазурованного изделия, проводят при температуре созревания черепка. Это разные температуры для разных видов фарфора (а мы сюда отнесли еще и каменные массы). Настоящий фарфор требует 1380 — 1420°С, рядовой столовый фарфор — 1300 — 1380°С, санитарно-технический — 1250 — 1280°С, а каменные массы — в зависимости от того, что используют в роли плавня. Второй обжиг окончательно формирует структуру керамики и, таким образом, определяет все ее физико-химические свойства. Изделия после этого обжига (если оно не расписано) называют бельем.
Из белых фарфоровых чашек очень приятно пить чай на даче. Традиции диктуют фарфору другой вид: с цветочной росписью, картинкой, золотой или голубой каемочкой. Украшения фарфор получает в третьем, декорирующем, обжиге. Обычные надглазурные краски вжигают при 800 — 830°С, люстровые краски и препараты золота — при той же или чуть меньшей температуре. Сейчас распространился и высокотемпературный декорирующий обжиг при 1000 — 1100оС. Роспись для него проводят красками высокого огня (внутриглазурные краски) или легкоплавкими цветными глазурями. Иногда, чтобы получить яркие краски, проводят два и более декорирующих обжигов. Все они, с точки зрения классификации, третьи. Изделия после третьего обжига называют на Худсовете предприятия.
Фаянсовая схема обжига
Первый обжиг фаянса — высокий. В фаянсовых массах практически нет плавней, поэтому при обжиге образуется минимальное количество жидкой фазы, или не образуется вообще, а глины, входящие в его состав, имеют высокую тугоплавкость. Это дает возможность обжигать изделия из фаянса сразу при температурах, необходимых для созревания черепка. Как правило, это 1200-1250°C. В отличие от фарфора, черепок останется пористым, на него легко нанести слой глазури.
А второй обжиг, политой, можно проводить при любой температуре! То есть, при той, которая требуется для нормального растекания глазури: 1150 — 1250°C, если это «фаянсовые» глазури, 900 — 1000°C, если это свинцовые майолики; можно нанести белую эмаль и использовать технику росписи по сырой эмали. Во всех случаях, если глазури подобраны правильно, мы получим изделие с такой же прочностью, какой она была после первого обжига.
Третий, декорирующий, обжиг проводят так же, как и в фарфоровой схеме. Если он необходим. Ведь, по сравнению с фарфором, низкая температура политого обжига допускает применение глазурей и красок широкой цветовой гаммы.
Обжиг майолики
Здесь используются красножгущиеся глины с невысокой тугоплавкостью. Пережег может привести к их вспучиванию и сильной деформации. Красные глины вдобавок имеют узкий интервал обжига. Например, при 950°C это еще непрочное рыхлое, а при 1050oC — плотноспекшееся, стекловидное тело. Конечно, бывают и исключения, но там и тогда. Для майолики в принципе характерны низкие температуры обжига — 900 — 1100oC. И как раз примерно при этих температурах завершаются процессы разложения глинистых материалов, которые (процессы) сопровождаются выделением газообразных веществ. Это делает крайне затруднительным так называемый однократный обжиг — и черепка и глазури — за один раз. Если обратиться к нижеприведенной таблице, будет ясно, насколько близки температуры обжига майолики к критическим для керамики температурам. Самая распространенная технология — первый, утильный, и второй, политой, обжиг.
Режим первого обжига выбирают таким, чтобы в максимальной степени прошли все процессы превращения глинистых минералов. Незавершенность этих процессов обязательно скажется на качестве поверхности глазури после второго обжига. Температура утильного обжига может быть и выше, и ниже температуры политого обжига. Обычно ниже, где-то на уровне 900 — 950°C.
Режим второго обжига выбирают исходя из характеристик глазури, но, естественно, при этом нельзя превышать температуру начала деформации черепка.
Обжиг шамота
Основное отличие шамотных масс от вышеперечисленных — наличие в массе жесткого каркаса из плотных, уже прошедших соответствующий обжиг зерен. Размер зерен может варьироваться от 100 микрон до нескольких миллиметров, что определяется скорее требованиями фактуры материала, а не требованиями технологии. Жесткий каркас препятствует усадке массы в процессе обжига. (Кстати, при сушке усадка шамотных масс ненамного меньше, чем тонких пластичных масс). Это позволяет проводить обжиг при несколько более высоких температурах, не опасаясь серьезной деформации изделия. Часто материал зерен имеет другой состав, чем пластичная составляющая массы. Если тугоплавкость зерен выше, температуру обжига можно увеличить значительно.
А в целом схема обжига шамота та же, что и для других типов масс: сначала утильный, потом (если нужно) политой, потом (если нужно) декорирующий обжиги.
Однократный обжиг
Однократный обжиг — это когда на высушенное изделие наносят глазурь и обжигают все в один прием, объединяя утильный и политой обжиги. Это мечта любого производственного экономиста:
- только один раз тратится энергия на нагрев;
- ставка изделий в печь и их выемка производится один раз;
- не нужен промежуточный склад утиля;
- цикл от сырца до готового изделия сокращается вдвое, т.е. меньше относительные затраты на аренду площадей и зарплату за счет повышения производительности.
В принципе, если не считать совсем низкотемпературный декорирующий обжиг, однократно можно обжечь любой материал.
- Но:
- приходится наносить и подглазурный рисунок, и собственно глазурь на просто высушенное изделие, которое, конечно, не имеет прочности утиля;
- из-за этого исключается машинная обработка, а руками надо все делать очень акуратно, чтобы ничего не разбить;
- глазурование методом окунания — наиболее экономный с точки зрения расхода глазурей — можно проводить только для маленьких изделий, делая большую паузу между глазурованием внутри и снаружи;
- нет утиля, нет и промежуточного контроля качества (овальность, тонкие краевые трещины и т.
п.), т.е. заранее закладывается более высокий процент брака
- глазури должны быть специфицированы на однократный обжиг.
Как же определить, нужен нам однократный или двукратный обжиг? Решающим критерием для художника или художественной студии является конечный результат — то есть осуществление художественного замысла. Для мастерских, изготавливающих более или менее серийную продукцию, и для керамических фабрик, решающим могут оказаться соображения экономического порядка. Вот что нужно иметь в виду.
- Для фарфора:
- Энергозатраты на низкий утильный обжиг существенно ниже затрат на высокий обжиг. Для первого достаточны температуры порядка 900°C, воздушная окислительная среда, электрическая печь со слабой футеровкой. Для второго — хорошо футерованная и желательно пламенная печь. Стоит ли экономить на утиле?
- Глазури для фарфора начинают расплавляться при температуре, близкой к температуре созревания фарфорового черепка. В том интервале температур, где происходят процессы разложения глинистых минералов, глазурный слой походит на порошок, и газы легко проходят через него.
Таким образом, не приходится опасаться дефектов глазури, возникающих по причине газонепроницаемости расплава. Стоит ли проводить утильный обжиг?
- Фарфоровые массы — это тощие, быстро промокающие массы. Глазурование сырца требует сноровки. Утиль нужен!
- Многие крупные изделия, например, изразцы, часто надо глазуровать напылением. А при обжиге на бисквит глазуровать вообще не надо. Тогда зачем нужен утиль?!
- Для фаянса:
- Утильный обжиг (помните, он проводится на высокую температуру) нужен обязательно, если мы собираемся использовать легкоплавкие глазури. Иначе в однократном обжиге мы получим не фаянс, а нечто недожженное, напоминающее папье-маше.
- Утильный обжиг не нужен, если мы используем высокотемпературные глазури, которые, наподобие фарфоровых, начинают плавиться выше 1100°C. В этом случае наносят их, как правило, напылением сжатым воздухом.
- Для майолики — самый сложный случай.
- Утиль нужен практически всегда, и причем на максимально высокую температуру.
Многие технологи западной школы рекомендуют обжигать майолику чуть ли не до стекловидного состояния, чтобы выжечь все примеси и разложить все, что способно разложиться в утильном обжиге. Вопрос, а как потом глазуровать? Можно. Читайте об этом в разделе о глазурях.
- Если в качестве покрытия использовать ангобы или что-то вроде терра-сигилята, или если вы располагаете специальными глазурями с очень коротким интервалом плавления, можно обойтись без утиля.
Для всех материалов однократный обжиг возможен при условии тщательно отлаженной технологии, которая в случае керамики, на две трети состоит из опыта работающих.
Кажется, в нашем изложении проблем обжига все уже запутано настолько, что требуется еще одна раскладка по полочкам.
Что происходит в процессе нагрева и охлаждения.
Интервал,C | Процесс |
---|---|
20 — 100 | Удаление влаги из массы. Греть нужно медленно и, главное, равномерно.![]() |
100 — 200 | Удаление влаги из массы продолжается! Если приборы показывают 150°C, это еще не значит, что изделие нагрелось до такой температуры, особенно в толще, особенно на толстой подставке. Глазурное покрытие претерпевает усадку. Выделяющиеся из объема изделия пары воды могут привести к растрескиванию и отлету покрытия. Из люстровых покрытий выделяются летучие органические соединения. Не форсируйте нагрев! |
200 — 400 | Выгорание органических веществ. Если по каким-то причинам их много, следует обеспечить хороший приток воздуха (деколи, люстры, связующее надглазурных красок и мастик). |
550 — 600 | Серьезное фазовое превращение кварца. Оно редко проявляется на стадии нагрева, а на стадии охлаждения может привести к т.н. «холодному» треску. |
400 — 900 | Разложение минералов глины. Выделяется химически связанная вода.![]() Разлагаются азотнокислые и хлористые соли (если их использовали). |
600 — 800 | Начало расплавления свинцовых и других легкоплавких флюсов, надглазурных красок. При 750 — 800°C в третьем декорирующем обжиге происходит размягчение поверхности глазури и впекание красок, золота и т.п. Выгорание сульфидов. |
850 — 950 | Разложение мела, доломита. Начало взаимодействия карбонатов кальция и магния с кремнеземом. Эти процессы сопровождаются выделениями углекислого газа. В целом завершены все превращения глинистых веществ. Их наиболее мелкие частицы уже спеклись и обеспечили заметную прочность черепка. К концу интервала — полное расплавление майоликовых глазурей. |
1000 -1100 | Интенсивное взаимодействие извести и кремнезема сопровождается появлением жидкой фазы (например, в известковом фаянсе), уплотнением и деформацией черепка. Начало размягчения полевых шпатов. Плавление нефелин-сиенита. ![]() Интенсивное разложение сульфатов, что сопровождается выделением сернистого газа. |
1200 -1250 | Интервал спекания беложгущихся глин, фаянсовой массы. Растворение кремнезема и каолинита в расплаве полевого шпата. |
1280 — 1350 | Процесс муллитообразования. Иглы муллита пронизывают фарфоровую массу, что в дальнейшем обеспечит ей высокую прочность и термостойкость. Превращение тонкодисперсного кварца в кристобаллит. |
1200 — 1420 | Этот температурный интервал характерен для фарфора. Здесь происходят процессы восстановления рыжих оксидов железа в более благородные голубые, если обеспечены соответствующие окислительно-восстановительные условия обжига. Температуры высоки, вязкости умеренные, очень быстро протекает диффузия: например, подглазурная роспись теряет четкость очертаний. |
1420 — 1000 | Ничего особенного в процессе охлаждения не происходит.![]() Если используются глазури, склонные к кристаллизации, медленное охлаждение или выдержка 1-10 часов в этом интервале приводит к росту кристаллов. |
1000 — 700 | Начинается окисление низших оксидов меди, марганца и др. металлов (если они использованы) в высшие. Недостаток кислорода в пространстве печи может дать поверхность с металлизацией. Если требуется восстановление — самое время для него. Восстановительную среду следует поддерживать чуть ли не до комнатных температур, как минимум до 250-300°С. |
900 — 750 | И черепок, и глазурь перешли в хрупкое состояние и далее остывают как единое твердое тело. Если не согласованы КТР — возможен цек или отскок глазури и даже разрушение изделия. |
600 — 550 | Обратное фазовое превращение кварца с резким объемным изменением.![]() |
300 — 200 | Фазовое превращение кристобаллита. Он образовался, если в массе был очень тонкодисперсный кремнезем, при 1250 — 1300°C. Не следует спешить открывать дверцу печи. |
250 — 100 | Охлаждение продолжается! В глубине ставки, в толстых частях изделий температура гораздо выше, чем в тонких кромках и чем показывает термопара. Дайте изделиям остыть равномерно. |
В таблице описаны основные процессы. Поэтому сейчас еще раз кратко укажем, что главное в обжиге.
- 01Первый обжиг. В печь ставим сырец. В нем много воды, даже если он выглядит сухим. До 200 — 300°C нагреваем медленно, например за 2 — 3 часа. Обеспечиваем хорошую вентиляцию, чтобы выгорели все примеси. Конечная температура — 900 — 1000°C. Если нет уверенности в температуре, делаем выдержку 1 — 3 часа, давая возможность всей садке равномерно прогреться.
Охлаждение ведем с такой скоростью, с которой остывает печь. Форсированное охлаждение проводим только после нескольких экспериментов — цека глазурей не будет, поскольку нет глазурей, а вот холодный треск из-за кварца может иметь место.
- 02Обжиг с глазурью после утиля. В печь ставим заглазурованные изделия. Черепок уже обжигали на утиль, так что скорость на начальном участке нагрева может быть выше; главное, хорошо просушить глазурь. Нагрев до конечной температуры проводим так быстро, как позволяет печь и, главное, скорость прогрева изделий. При конечной температуре делаем выдержку от 15 минут до 1-2 часов с целью равномерного прогрева. Если скорость подъема температуры в конце нагрева невысокая (50°C в час и меньше), считаем, что выдержка уже была. Лучше, конечно, здесь пользоваться конусами Зегера. «Полочки» (выдержки при постоянной температуре) на стадии охлаждения — только для кристаллических глазурей и некоторых матовых. В остальном — как в п.1.
- 03Однократный обжиг с глазурью.
Принимаем во внимание все, что в п.1 и в п.2. Не форсируем подъем температуры в интервале 500 — 900°C — до начала плавления глазури из черепка должны удалиться все газы!
- 04Обжиг деколей, люстровых красок, надглазурных красок. Поднимаем температуру очень медленно (за 2 — 4 часа) до 400°C — надо сгореть всей органике. При этом среда должна быть окислительной (воздушной), а вентиляция — интенсивной. От 400 до 800°C — как угодно быстро. Выдержка 5 — 15 минут.
О том, какие условия обжига диктует печь, читайте ниже.
2. Электрические печи и два слова про другие.
Обжиг керамики проводят в самых разных тепловых агрегатах, называемых печами. Если для нагрева используется тепло электрического тока, печи называют электрическими, если тепло от сгорания органического топлива — топливными и обычно более конкретно:газовыми, дровяными, мазутными и т.д. За тысячи лет обжигов керамики изобретено немало конструкций топливных печей, а за последние сто лет — не меньшее число конструкций электропечей.
- свободное пространство для ставки изделий, для краткости — камера;
- огнеупорная и теплоизолирующая оболочка, для краткости — футеровка;
- тепловой источник — нагреватель, горелка и т.д.
- устройство для контроля и регулирования степени нагрева — регулятор.
- Независимо от вида и конструкции, в печи присутствует:
Каждую печь можно классифицировать по особенностям перечисленных атрибутов. Если нужно заказывать печь, обязательно указывайте эти особенности.
Объем камеры определяет производительность печи в одном обжиге в периодической печи или за цикл толкания одной вагонетки в туннельной печи. В дальнейшем мы будем говорить только о печах периодического действия. Объем камеры может составлять 1 — 2 литра; такие маленькие печки удобны для тестовых обжигов и для изготовления небольших изделий типа керамической бижутерии. Объем камер печей, обычно используемых в мастерских и студиях, составляет от 50 — 100 литров до 1 — 1,5 куб. м. Для фабричных условий характерны печи с объемом от 3 до 20 куб. м.
Футеровка и нагреватель определяют максимальную температуру, которую можно развить в камере. Чем выше требуется температура, тем более высокого класса должны быть огнеупоры, что сразу и, заметим, резко сказывается на стоимости печи. Иногда камера отделена от нагревателя дополнительной футеровкой, называемой муфелем. (Не следует называть муфелями все подряд маленькие печи!)
Регулятор содержит устройство для измерения температуры, которым обычно является термопара, устройство регулирования мощности нагревателя и управляющее устройство, согласующее действие двух первых.
Ниже приведены некоторые конфигурации печей.
Костер
ПАРАМЕТР | ЗНАЧЕНИЕ |
---|---|
Камера | 10 — 100 литров |
Футеровка | слой земли |
Теплоизоляция | cлой земли |
Нагреватель | тепло сгорающих дров |
Измеритель температуры | на глаз по свечению |
Регулятор мощности | подкидывание дров |
Управление | cобственный опыт |
Электропечь 200. 1250.L (ООО «Термокерамика»), вариант
|
Такие разные тепловые устройства здесь приведены для того, чтобы глубже понять функции элементов печи.
Камера — это рабочее пространство, куда помещаются изделия и полки с подставками, из общего объема «от стенки до стенки» нужно вычесть объем, необходимый для нагревателей. А расчет полезной загрузки камеры нужно производить с учетом толщин полок.
Пример. Полезная ширина, глубина и высота камеры — 40 см. Имеется огнеупорная плита 39х39 см, толщиной 2 см и четыре стойки 7х7 см высотой 18 см. Сколько горшков диаметром 18 см и высотой 16 см можно поместить в печь? Ответ: если без полки — 4 шт., а если с полкой — 6 шт. (а не 8; смотрите на рисунке).
Продолжая пример, зададимся вопросом, а что, собственно, выгоднее — обжечь за один раз 4 горшка или 6? Ответ заключен в анализе количества тепла, необходимого на нагрев дополнительной массы огнеприпаса. Если горшок весит грамм 300, а плита и стойки — килограммов 5… Т.е. чуть ли не все тепло пойдет на нагрев огнеприпаса! И остывать печь будет дольше. Может случиться так, что за время обжига шести горшков можно провести два обжига по 4 горшка в каждом.
На самом деле нагреваются не только горшки и огнеприпас, но и стенки печи. В костре это — сплошная масса земли. Прогреть ее трудно, остудить тоже. В современной печи должны присутствовать огнеупоры с низкой теплоемкостью, низкой теплопроводностью и высокой огнеупорностью. Вакуумформованый волокнистый материал ШВП-350 хорошо подходит для конструирования печей с рабочей температурой 1200°C. Если вся печь выполнена из тяжелого шамотного кирпича, она потребует колоссального времени на нагрев и остывание, и соответственно затрат энергии. Такая тяжелая «на подъем» печь не позволит Вам реализовать режимы скоростного нагрева, если они Вам для чего-то понадобились. Впрочем, можно увеличить мощность нагревателей.
Электрические нагреватели бывают проволочными и керамическими. Проволоку делают из нихрома (дорого, предельная температура 1100°C, зато остаются гибкими после работы) или из железных сплавов. Последние часто называют «фехраль», а импортные аналоги — «кантал»; отечественные марки имеют точное наименование — Х23Ю5Т или Х27Ю5Т. Фехраль работает до 1200 — 1350°C в зависимости от диаметра проволоки. После первого же нагрева необратимо становится хрупким, перегоревший в одном месте нагреватель нельзя починить скруткой!
К керамическим нагревателям относятся карбид-кремниевые, они же силитовые, они же карборундовые стержни: рабочая температура до 1400°C. В последние 10 лет упорно рекламируются дорогие хромит-лантановые нагреватели с рабочей температурой до 1700°C, которые имеют очень высокий ресурс работы при тех же 1300-1400°C (если не сломать, когда устанавливаешь тяжелую плиту :-)). Читайте в другом месте о том, как рассчитывать электрические нагреватели. Здесь мы рекомендуем обращаться за помощью в специализированные фирмы.
Если нагрев осуществляется газовыми горелками, в пространстве печи могут быть достигнуты любые температуры вплоть до 1700°C, а если еще использовать воздух, обогащенный кислородом, — до 2000°C. Газовые (да и другие топливные) печи хороши тем, что позволяют вести обжиг не только в окислительной, но и в нейтральной, и в восстановительной среде. Степень «восстановительности» регулируют изменением соотношения газ/воздух, в современных газовых печах это делается автоматически. Дровяные печи, к сожалению, сложнее поддаются автоматизации, но они просты в изготовлении, дешевы в эксплуатации, для них не требуется согласований с газовой инспекцией, а дают 1200°C запросто.
Чем мощнее нагреватели, тем более быстрый нагрев они могут обеспечить. И тем аккуратнее с ними нужно работать. Представьте, что произойдет в первые же пять минут с горшками, если одна сторона их обращена к мгновенно раскаляющейся стенке с нагревателями, а другая — к холодному соседнему горшку. Плавный разогрев (а точнее — равномерный по всей камере) проще всего получить, используя тиристорные силовые блоки. Регулирование выходной мощности в них происходит по принципу «больше сила тока» — «меньше сила тока», а не по принципу «включено» — «выключено». Если в Вашем распоряжении только последний способ регулирования, то задавайте на первом этапе невысокие температуры (сначала 100°C, через полчаса — 200°C, через час — 300°C, и только потом — конечную температуру). А если в печи совсем нет управляющего прибора, не отходите от нее и щелкайте выключателем каждые пять минут (Это не шутка!)
Называя разные температуры, мы до сих пор не уточняли, о чем идет речь — о температуре на нагревателе? на изделии? на термопаре? Если в печи установлена термопара, то прибор, подсоединенный к ней, будет показывать, естественно, температуру кончика термопары. По разным причинам, о которых написаны тома научной литературы, эта температура только примерно отражает тепловую ситуацию в печи. В процессе нагрева нагреватели всегда горячее, а изделия — холоднее, чем термопара. Термопара показывает температуру в некоторой точке камеры, а что делается в других местах — неизвестно. Тем не менее термопара выдает электрический сигнал, понятный электронным приборам, в том числе и автоматике управления мощностью. С этой точки зрения она незаменима. Долгая практика эксплуатации печи дает информацию о том, где в камере бывает жарче, где холоднее. Рано или поздно мы привыкаем к повадкам этого устройства. Но издавна (с конца 19 века) известен и другой способ определения момента достижения требуемой точки обжига. Это — обжиг по конусам Зегера.
Обжиг считается выполненным на данный конус, если конус, деформируясь в процессе обжига, коснулся подставки, на которую он установлен. Конус изготовлен из масс, поведение которых схоже с поведением обжигаемого материала. Если на практике выяснено, что наилучший результат достигается при обжиге на конус, скажем, 114, то все обжиги надо проводить на этот конус, не обращая особенного внимания на показания термопары. Да и термопара не нужна! Использование конусов чрезвычайно распространено в художественной керамике на Западе. И это не случайно…
Разработка и изготовление микросборок на многослойной керамике
Щербина Андрей
№ 3’2019
PDF версия
Развитие радиоэлектронной промышленности идет путем минимизации изделий, с разработкой высокоинтегрированных сборок. Однако получение максимальной производительности при минимальном занимаемом объеме неизбежно вызывает все более сильное нагревание электронных компонентов. Данная проблема решается применением подложек с высокой теплопроводностью.
В силовой электронике и микроэлектронике широко распространены керамические подложки с использованием в качестве основы процессов тонких или толстых пленок. Компанией «ТЕСТПРИБОР» освоены технологии изготовления однослойных и многослойных подложек из керамики на основе оксида алюминия (Al2O3), нитрида алюминия (AlN) и оксида бериллия (BeO).
Изделия из таких материалов характеризуются:
- высокой теплопроводностью;
- низким коэффициентом теплового расширения;
- низкими диэлектрическими потерями;
- высокой механической прочностью.
Рассмотрим один из примеров применения данных технологий.
Задание предусматривало разработку корпуса для микросборки, схема которой приведена на рис. 1 и представляет собой часть схемы DC/DC-преобразователя напряжения. Основное требование, предъявляемое к корпусу микросборки, — отвод тепла, выделяемого на полевых транзисторах (VT2 и VT3), до 4 Вт на каждом.
Рис. 1. Электрическая принципиальная схема микросборки
Условия работы кристаллов и микросборки:
- микросборка должна действовать в условиях вакуума;
- максимальная температура кристаллов не должна превышать +125 °C при работе изделия в предельно допустимой температуре +65 °C.
В отработанной схеме предусмотрены корпусные транзисторы в корпусе КТ‑94. В микросборке применяются кристаллы транзисторов, чьи параметры приведены в таблице 1. Размеры кристаллов составляют 5,6×5,0 и 7,33×7,31 мм соответственно.
Наименование | Uси, В | Iс, А | Rси, Ом | С11, нФ | Корпус | Размер, мм | Примечание |
2П768П92 | 400 | 11 | 0,42 | 1,9 | КТ-94 | 11,6×16,0 |
|
2П768П-5 | 400 | 11 | 0,42 | 1,9 | Кристалл | 5,6×5,0 | Замена |
2П794В92 | 400 | 18 | 0,2 | 3,3 | КТ-94 | 11,6×16,0 |
|
2П794В-5 | 400 | 18 | 0,2 | 3,3 | Кристалл | 7,33×7,31 | Замена |
На данном этапе развития производства есть возможность использования одного из следующих материалов – это либо оксид алюминия с чистотой 99,5%, либо нитрид алюминия. Параметры материалов приведены в таблице 2.
Материал | Оксид алюминия (99,5%) | Нитрид алюминия |
Хим. формула | Al2O3 | AlN |
Температура плавления (°C) | 2072 | 2397–2507 |
Макс. рабочая температура (°C) | 1750 | 1027–1727 |
Коэф. теплового расширения (1 • 10–6 °C–1) | 7–8,4 | 4,3–9 |
Удельная теплоемкость (Дж/(кг•К)) | 880 | 740–820 |
Теплопроводность (Вт/м2•K) | 25,5–35 | 60–77 |
Диэлектрическая проницаемость | 9,8 | 8,3–9,3 |
Объемное удельное сопротивление(Ом×см) | > 1е14 | > 1е14 |
Толщина одного слоя керамики после обжига 0,25 мм.
Прежде чем начать проектирование корпуса, рассмотрим, как отводится тепло от кристалла, установленного на керамику из оксида алюминия и нитрида алюминия, при условии, что тепло с подложки может рассеиваться только с основания корпуса микросборки на корпус изделия, куда будет установлена микросборка.
Одним из критериев определения достаточной площади для отвода тепла от кристалла является температура в установившемся режиме. Она не должна превышать +80…+85 °C при температуре окружающей среды +20 °C.
Кристалл размером 5,6×5,0 мм, помещенный в центр керамической подложки на основе оксида алюминия размером 80,0×80,0 мм (рис. 2), нагревается свыше +140 °C. При этом тепло не рассеивается по всей площади подложки, что не удовлетворяет заявленным требованиям. Аналогична ситуация и для второго кристалла размером 7,33×7,31 мм.
Рис. 2. Распределение тепла на Al2O3 размером 80×80 мм
Кристалл размером 5,6×5,0 мм, установленный в центр керамической подложки из нитрида алюминия размером 18,0×18,0 мм (рис. 3), нагревается до +80,4 °C, что удовлетворяет требованиям. Расчет температуры второго кристалла размером 7,33×7,31 мм, установленного на такую же подложку, показал результат +78,9 °C, что также удовлетворяет требованиям задания.
Рис. 3. Распределение тепла на AlN размером 18×18 мм
На рис. 4 показан расчет температуры кристаллов, размещенных на керамической подложке 36,0×18,0 мм, при работе двух транзисторов одновременно. Максимальная температура нагрева кристалла не изменилась.
Рис. 4. Распределение тепла на AlN размером 36×18 мм от двух кристаллов
Исходя из полученных результатов габариты корпуса были выбраны 36,0×18,0 мм.
Одной из технологий производства, которой обладает компания АО «ТЕСТПРИБОР», является высокотемпературная керамика HTCC.
Отличие высокотемпературной керамики от низкотемпературной заключается в более высокой температуре спекания слоев керамических плат: +1500…+1600 °C (в технологии LTCC температура спекания – менее +1000 °C).
Достоинства технологии HTCC:
- малые допуски на размеры – благодаря низкому коэффициенту теплового расширения обеспечивается повышенная стабильность размеров корпусов;
- коэффициент теплового расширения (КТР) высокотемпературной керамики достаточно близок к КТР кремния, что позволяет монтировать кристаллы непосредственно на керамическое основание;
- высокие диэлектрические и тепловые характеристики корпусов: в зависимости от используемой марки керамики электрическая прочность варьируется в пределах 45–60 кВ/мм, тангенс угла диэлектрических потерь (tgδ) 0,006–0,021, а диэлектрическая проницаемость (ε) — 6–10 в гигагерцевом диапазоне частот;
- возможность создания многослойных герметичных керамических плат: высокотемпературная керамика имеет плотную структуру, а после спекания многослойные керамические модули становятся монолитными;
- хорошее заполнение переходных отверстий и линий металлизации в плате вольфрамовой или молибденовой пастой;
- высокая твердость используемых керамических материалов.
Гарантированные технологические возможности производства приведены на рис. 5 и в таблице 3. Наша компания не останавливается на достигнутых результатах и будет совершенствовать технологии производства.
Рис. 5. Технологические возможности производства АО «ТЕСТПРИБОР»
Контактные площадки | Ширина площадки | ≥ 250 мкм | a |
Расстояние между площадками | ≥ 200 мкм | b | |
Расстояние от площадки до края подложки | ≥ 150 мкм | c | |
Сигнальные дорожки | Диаметр отверстия | ≥ 150 мкм | d |
Диаметр площадки | ≥ 400 мкм | e | |
Шаг отверстия | ≥ 650 мкм | f | |
Расстояние от площадки до края подложки | ≥ 650 мкм | g | |
Ширина дорожки | ≥ 150 мкм | h | |
Расстояние между дорожками | ≥ 100 мкм | i | |
Расстояние от дорожки до края подложки | ≥ 500 мкм | j | |
Сквозные отверстия | Диаметр отверстия | ≥ 400 мкм | k |
Диаметр площадки | a + 300 мкм | l | |
Расстояние между вырезами | ≥ 600 мкм | m | |
Расстояние от площадки до проводящего слоя | ≥2 00 мкм | n |
Исходя из технологических возможностей был разработан корпус. Так как площадь для отвода тепла под кристаллом довольно большая, то плотность микросборки получилась относительно низкая. Несколько видов корпуса приведены на рис. 6.
Рис. 6. Внешний вид корпусов
Внешний вид микросборки (корпуса с установленными компонентами) представлен на рис. 7.
Рис. 7. Внешний вид микросборки
Данная микросборка содержит четыре кристалла и 12 SMD-компонентов. Преимущества этой микросборки (и вообще микросборок) состоит в том, что она занимает меньше места, имеет меньшую массу по сравнению с той же схемой, сделанной на отдельных элементах в корпусах. Это важно для применения в изделиях, предназначенных для космоса.
В более функциональных схемах и крупных сборках при многоуровневом расположении компонентов проще выполнить защиту отдельных элементов от радиации, что уменьшает массу изделия по сравнению с тем, как если делать экран на всю сборку.
АО «ТЕСТПРИБОР» имеет возможность разработать и изготовить микросборки на многослойной керамике из Al2O3 и AlN по требованиям заказчика.
Эти материалы выдерживают самые жаркие температуры в мире
Лето не за горами, но жара уже началась. От неумолимого солнечного света до шипящих грилей, жарко (и охлаждение ) теперь являются частью повседневной рутины. PopSci поможет вам легко пережить самый знойный сезон благодаря новейшим достижениям науки, снаряжения и умным идеям «сделай сам». Добро пожаловать в жаркий месяц .
Духовка на вашей кухне легко нагреется до 400 градусов по Фаренгейту или около того, когда вы захотите приготовить ужин, но в мире полно мест, где становится намного, намного жарче. Вы можете не задумываться о них, но нить накаливания в старой лампочке, внутренняя часть реактивного двигателя и теплозащитный экран космического корабля — все они сталкиваются с гораздо более высокими температурами. Эти среды нуждаются в специальных материалах, чтобы справиться с этим экстремальным поджариванием.
Это вещества, которые позволяют этим местам функционировать, не плавясь, не горя, не распадаясь и не воспламеняясь.
Материаловеды рассматривают вещества как относящиеся к трем различным категориям: керамика, металлы и полимеры (также известные как пластмассы). Керамика наиболее устойчива к нагреву, а полимеры — наименее, хотя инженеры должны учитывать и другие качества, такие как электропроводность или вес, при выборе материалов, подходящих для задачи.
Но когда дело доходит до самых жарких мест в мире, керамические материалы всегда подходят.
«Керамика имеет самую высокую температуру плавления», — говорит Дэвид Дюнан, профессор материаловедения и инженерии Северо-Западного университета. Помимо того, что керамика хорошо справляется с высокими температурами в данный момент, она также выдерживает длительное нагревание, не разрушаясь так же быстро, как другие варианты.
Примеры керамики не ограничиваются обычными предметами, такими как стекло, кирпичи и глиняная посуда. У вас может быть даже керамический нож — острый, но хрупкий — на вашей кухне.
Ключом к их устойчивости являются связи, которые материалы имеют на атомном уровне: они ковалентны и очень прочны. (Помните школьную химию? Извините.) «Тепловые колебания не разрушают связи между атомами», — объясняет Дюнан.
Керамические материалы отлично подходят для таких мест, как доменные печи, где производится сталь. Эти материалы должны выдерживать температуры, которые могут быть выше 3000 градусов по Фаренгейту в течение длительного времени. «Домная печь — ее никогда не остановить», — говорит Дюнан. «Как только вы запустите его, он должен работать 365 дней, иначе вы его засорите».
В категории керамики есть явный лидер. «Для самой жаркой из самых жарких ситуаций вы фактически используете углерод», — отмечает Дюнан. «Это идеальная керамика для работы при высоких температурах». Например, тормоза самолета или теплозащитный экран космического корабля могут использовать этот материал в различных формах.
Углерод играет ключевую роль в тепловом щите, защищающем солнечный зонд NASA Parker от солнца. По данным НАСА, он способен выдерживать температуры до 3000 градусов по Фаренгейту, хотя на самом деле он должен выдерживать температуры около 2500 градусов.
Вы можете слышать о материале, называемом углерод-углерод, который обычно представляет собой смесь углеродного волокна и другой формы элемента, обычно графита, говорит Ян МакКью, адъюнкт-профессор материаловедения и инженерии, также Северо-Западного университета. Два слоя экрана Parker Solar Probe состоят из углерод-углерода. «Это в значительной степени предпочтительный материал для любого высокотемпературного самолета», — говорит он. «Оборона использует это; НАСА использует его».
У реактивных двигателей внутри пожар Следующими после керамики идут металлы, и особый их класс очень важен: жаропрочные сплавы на основе никеля. (Сплав представляет собой комбинацию металлов.) Этот материал играет ключевую роль в горячем внутреннем пространстве реактивного двигателя, говорит Дюнан, где лопасти турбины «находятся в прямом контакте с горящим топливом».
Эта металлическая смесь не только хорошо противостоит нагреву, но и «пластична и прочна», отмечает он. Это означает, что вещи не разобьются, если в них засосет незадачливую птицу.
Инженеры хотят, чтобы там было жарко. «В будущем люди хотели бы увеличить рабочую температуру двигателей — топливо для реактивных двигателей могло бы гореть намного горячее», — отмечает он. «Чем горячее вы сжигаете любое топливо, тем больше энергии вы извлекаете для топлива».
[Связанный: Огнеупорная одежда — популярный выбор. Вот как это работает. ]
Эти металлы обычно выдерживают температуру около 2190 градусов по Фаренгейту или ниже, говорит он. Сплавы, по словам Дунанда, десятилетиями «подгонялись», чтобы выдерживать все более и более высокие температуры. Как правило, их можно успешно эксплуатировать до температуры, составляющей около 80 процентов их температуры плавления.
Одним из огромных современных реактивных двигателей является GE9X, внутри которого используются как металлы, так и керамика.
Другая машина, похожая на реактивный двигатель, использует эти суперсплавы на основе никеля: электрические генераторы, которые сжигают природный газ.
«Если подумать, суперсплавы на основе никеля играют центральную роль в нашем электричестве и наших самолетах, поэтому современная жизнь, какой мы ее знаем, была бы очень сложной без них», — говорит он.
Отдельного упоминания заслуживает еще один особый металл: вольфрам, который имеет самую высокую температуру плавления среди всех веществ в своем классе. Он тает при поразительных 6,192 градуса по Фаренгейту, что делает его хорошим выбором для нити накала в контролируемой среде лампы накаливания.
Наконец, полимеры или пластмассы, такие как полиэтилен, плохо противостоят нагреву. Подумайте, например, о бутылке из термопластика, которую можно легко расплавить. Но некоторые все еще держатся: кевлар — это синтетическое творение из категории полимеров, называемых термореактивными. А кевлар, используемый в таких предметах одежды, как пуленепробиваемые жилеты и костюмы для бомб, очень прочен. «Прочность коррелирует с температурой плавления», — говорит Дюнан. «Поскольку это тугоплавкий полимер, вы можете использовать его при высоких температурах».
Generic DIY Jewelry Microwave D High Temperature Ceramic Kiln Microw
Choose your location
Please selectAbiaAdamawaAkwa IbomAnambraBauchiBayelsaBenueBornoCross RiverDeltaEbonyiEdoEkitiEnuguFederal Capital TerritoryGombeImoJigawaKadunaKanoKebbiKogiKwaraLagosNasarawaNigerOgunOndoOsunOyoPlateauRiversSokotoYobe
Please selectAbule Egba (Agbado Ijaye Road)Abule Egba (Ajasa Command Rd)Abule Egba (Ajegunle)Abule Egba ( Алагбадо)Абуле-Эгба (Алакуко)Абуле-Эгба (Экоро-роуд)Абуле-Эгба (Мейран-роуд)Абуле-Эгба (Новый Око-Оба)Абуле-Эгба (Старая Отта-роуд)АгбараАгеге (Аджувон-Акуте-роуд)Агеге (Допему)Агеге (Иджу-роуд)Агеге ( Old Abeokuta Road)Agege (Old Otta Road)Agege (Orile Agege)AGILITIAGUNGI (LEKKI)AJAO ESTATEALFA BEACHAMUWOANTHONY VILLAGEApapa (Ajegunle)Apapa (Amukoko)Apapa (GRA)Apapa (Kiri kiri)Apapa (Olodi)Apapa (Suru Alaba)Apapa ( Tincan)Apapa (Warf Rd)AWOYAYAAwoyaya-Контейнерный автобусAwoyaya-Eko Akete EstateAwoyaya-EputuAwoyaya-Gbetu Iwerekun RoadAwoyaya- Idowu EletuAwoyaya-Mayfair GardensAwoyaya-Ogunlana BusstopAwoyaya-OlogunfeAwoyaya-OribanwaBadagryBERGERBogijeCokerDoyinEjigbo-Ailegun RoadEjigbo-BucknorEjigbo-Ile EpoEjigbo-Isheri OsunEjigbo-Jakande Wood MarketEjigbo-NNPC RoadEjigbo-Oke-AfaEjigbo-PipelineEjigbo-PowerlineElemoroEPEFagba (Iju Road)FESTAC (1st Avenue)FESTAC (2nd Avenue)FESTAC (3rd Avenue)FESTAC (4th Avenue)FESTAC (5th Avenue)FESTAC (6th Avenue)FESTAC (7th Avenue)Gbagada- IfakoGbagada-Abule OkutaGbagada-AraromiGbagada-Deeper LifeGbagada-DiyaGbagada-ExpresswayGbagada-HospitalGbagada-L&KGbagada-New GarageGbagada- OlopomejiGbagada-PedroGbagada-SawmillGbagada-SholuyiIbeju-Lekki AiyetejuIbeju-Lekki AkodoIbeju-Lekki Amen EstateIbeju-Lekki Dangote fertilizerIbeju-Lekki Dangote RefineryIbeju-Lekki Dano MilkIbeju-Lekki Eleko JunctionIbeju-Lekki IgandoIbeju-Lekki MagbonIbeju-Lekki OnosaIbeju-Lekki OrimeduIbeju-Lekki Pan African UniversityIbeju -Лекки ШапатиIDIMUIGANDOIJANIKINIJEGUN IKOTUNIjegun-Obadore RoadIJORAIikeja (ADENIYI JONES)I keja (ALAUSA)Ikeja (ALLEN AVENUE)Ikeja (компьютерная деревня)Ikeja (GRA)IKEJA (MM Airport)Ikeja (MANGORO)Ikeja (OBA-AKRAN)Ikeja (OPEBI)IKORODU (Adamo)IKORODU (Agbede)Ikorodu (Agbowa)IKORODU (Сельское хозяйство)ИКОРОДУ (Баеку)ИКОРОДУ (Эйита)ИКОРОДУ (Гберигбе)ИКОРОДУ (Иджеде)ИКОРОДУ (Имота)ИКОРОДУ (Ита олуво)ИКОРОДУ (Итамага)ИКОРОДУ (Офин)ИКОРОДУ (Оводе-Ибесе)Икороду-роуд-АджегунлеИкороду-роуд-ИравоИкороду-роуд -Owode OnirinIKORODU(Elepe)IKORODU(Laspotech)Ikorodu(Ogolonto)IKORODU(Sabo)Ikorodu- Imota Caleb UniversityIkorodu-AgufoyeIkorodu-BensonIkorodu-GarageIkorodu-OdokekereIkorodu-OdonlaIkorodu-OgijoIKOTAIKOTUNIkoyi (Awolowo Road)Ikoyi (Bourdillon)Ikoyi (Dolphin)Ikoyi (Glover дорога)Ikoyi (Keffi)Ikoyi (Kings way road)Ikoyi (Obalende)Ikoyi (Queens Drive)IKOYI MTN ( PICKUP STATION)Ikoyi-Banana IslandILAJE (BARIGA)ILUPEJU (Lagos)ISHERI IKOTUNISHERI MAGODOISOLOIyana EjigboIYANA IBAIyana Ipaja (Abesan)Iyana Ipaja (Abesan)Iyana Ipaja Абору) Ияна Ипая (Айобо Роуд) Ияна Ипая (Командная дорога) Ияна Ипая (Эгбеда) Ияна Ипая (Икола Ро ad)Iyana Ipaja (Iyana Ipaja Road)Iyana Ipaja (Shasha)JAKANDE (LEKKI)JANKANDE (ISOLO)Jumia-Experience-CenterKetu- AgboyiKetu-AlapereKetu-CMD roadKetu-DemurinKetu-Ikosi RoadKetu-IleKetu-Iyana SchoolKetu-Tipper GarageLagos Island ( Адениджи)Остров Лагос (Марина)Остров Лагос (Оникан)Остров Лагос (Сура)Остров Лагос (TBS)ЛАКОВЕЛакове-Адеба-роудЛакове-ГольфЛакове-КаджолаЛакове-Школьные воротаLEKKI -VGCLekki 1 (Bishop Durosimi)Lekki 1 (F. T Kuboye street)Lekki 1 ( Omorinre Johnson)Lekki Phase 1 (Admiralty Road)Lekki Phase 1 (Admiralty way)Lekki Phase 1 (Fola Osibo)LEKKI-AGUNGILEKKI-AJAH (ABIJO)LEKKI-AJAH (ADDO ROAD)LEKKI-AJAH (BADORE)LEKKI-AJAH (ILAJE) )LEKKI-AJAH (ILASAN)LEKKI-AJAH (JAKANDE)LEKKI-AJAH (SANGOTEDO)Lekki-AwoyayaLekki-ChiscoLEKKI-ELFLEKKI-IGBOEFONLEKKI-IKATE ELEGUSHILEKKI-JAKANDE (KAZEEM ELETU)LEKKI-MARUWALEKKI-ONIRU ESTATELEKKI-OSAPAPA LONDONMagboro (ONIGBONGBO)MEBANMUMILE 12Mile 12 -AjelogoMile 12-Agboyi KetuMile 12-Doyin OmololuMile 12-OrishigunMILE 2Mushin -Палм-авенюАвтомагистраль Мушин-АгегеРынок Мушин-ДалэкоМушин-Фатай АтереМушин-Иди ОроМушин-Иди-АрабаРоуд Мушин-ИласамаяРоуд Мушин-ИсолоРоуд Мушин-ЛадипоРынок Мушин-МушинМушин-ОлатеджуМушин-Папа АджаоОдонгунянОгба-Акило-роудОгба-Колледж-роудОгба-Роуд Латиф Джакандеме -AgudaOgba-CountyOgba-Ifako-IdiagbonOgba-Ifako-OrimoladeOgba-Isheri RoadOgba-ObawoleOgba-OjoduOgba-Oke IraOgba-Oke Ira 2nd JuctionOGBA-Surulere Ind RdOgba-Wemco RoadOGUDUOJOOjo ShibiriOjo-Abule OshunOjo-AdalokoOjo-AgricOjo-AjangbadiOjo-Alaba InternationalOjo-Alaba RagoOjo -Alaba SuruOjo-AlakijaOjo-CassidyOjo-IjegunOjo-IlogboOjo-Ojo BarracksOjo-OkokomaikoOjo-Old Ojo roadOjo-OnirekeOjo-PPLOjo-ShibiriOjo-Tedi TownOjo-Trade FairOjo-VolksOJODUOJOKOROOJOTAOKOKOMAIKOOKOTAOmole Phase 1Omole Phase 2OREGUNOreyo- IgbeORILEOSAPA (LEKKI)OSHODI-BOLADEOSHODI-ISOLOOSHODI-MAFOLUKUOSHODI -ОРИЛЭОСОДИ-СЁГУНЛЕПальмовая роща-ОнипануСари-ИганмуГород-спутникСОМОЛУСурулере (Адениран Огунсанья)Сурулере (Агуда)Сурулере (Боде) Томас)Сурулере (Фатья Шитта)Сурулере (Иди Араба)Сурулере (Иджеша)Сурулере (Ипонри)Сурулере (Итире)Сурулере (Лавансон)Сурулере (Маша)Сурулере (Огунлана Драйв)Сурулере (Охуэлегба)VI (Адетокунбо Адемола)VI (Ахмед Белло) путь)VI (Епископ Абаяде Коул)VI(Аджосе Адеогун)VI(Акин Адешола)VI(Епископ Олувале)VI(Юсуф Абиодун)Остров Виктория (Адеола Одеку)Остров Виктория (Кофо Абайоми)Яба-Абуле ИджешаЯба-ФадейиЯба-(Сабо) Yaba-(Unilag)Yaba-Abule OjaYaba-AdekunleYaba-AkokaYaba-AlagomejuYaba-College EducationYaba-Commercial AvenueYaba-FolagoroYaba-Herbert Macaulay WayYaba-JibowuYaba-MakokoYaba-Murtala Muhammed WayYaba-Onike IwayaYaba-OyingboYaba-TejuoshoYaba-University Road9Yaba-Yaba-University Road
Доставка дверей
Доставка ₦ 1744
Готовы к доставке между 31 октября и 08 ноября , когда вы заказываете в течение следующего 8HRS 54MINS
.
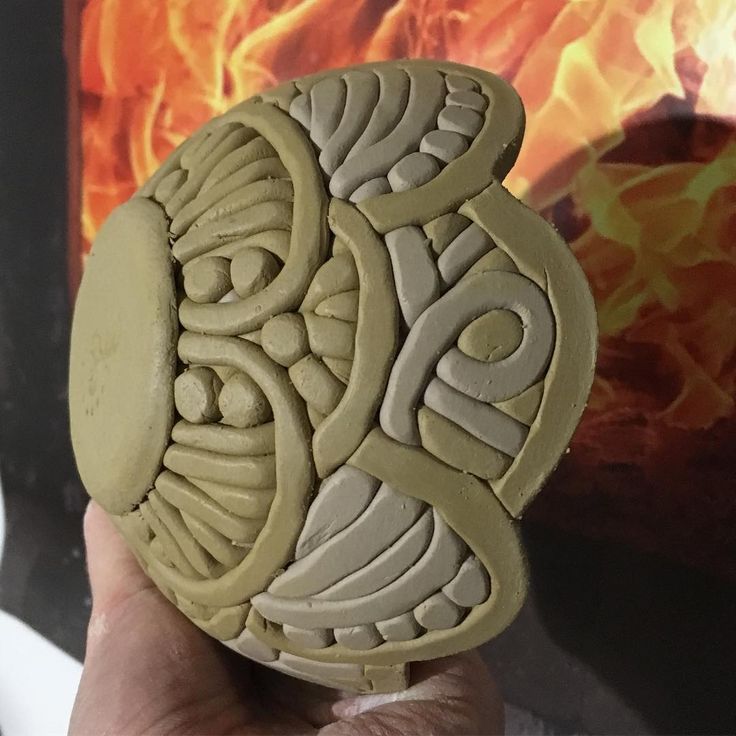
Готов к выдаче между 31 октября и 08 ноября при заказе в течение следующего 8 часов 54 минуты
Почтовая доставка
Доставка ₦ 121
Готовы к доставке между 18 ноября и 02 декабря , когда вы заказываете в течение следующих 8 часов 54 минуты
Политика возврата
Свободный возврат в течение 15 дней для официальных пунктов и 7 дней. для других подходящих элементов.Подробнее
Можете ли вы нанести керамическое покрытие на детали выхлопной системы, двигателя и турбонаддува?
Когда речь идет об автомобилях, не секрет, что нанокерамические покрытия работают практически на любой твердой поверхности. Все, от автомобильных прозрачных покрытий и хромированной отделки до фар, ветровых стекол, колес и виниловой пленки, может быть защищено нанокерамическим покрытием, если оно заранее подготовлено должным образом.
А как насчет всех этих металлических деталей выхлопной системы и турбины? Они тоже заслуживают защиты, но в последний раз мы проверяли, что они также были немного поджаренными.
Познакомьтесь со спреем для высокотемпературного керамического покрытия во всей его термостойкости.
Высокотемпературные спреи для керамического покрытия, доступные как в форме запекания в печи, так и в формулах с воздушным отверждением, а также во множестве вариантов и цветов в виде гремучих банок, заполняют столь необходимый пробел на рынке средств защиты поверхностей.
Все, от энтузиастов вторичного рынка в своих гаражах с баллончиками с краской в руках, до производителей OEM-покрытий, наносимых роботами, и гоночных команд, стремящихся контролировать температуру, десятилетиями клянутся этим материалом.
Однако это НЕ тот же вид керамического покрытия, что и в блестящей бутылке Armor Shield IX.
В приведенной ниже информации мы объясним, как спрей для керамического покрытия может защитить детали выхлопной системы и турбонагнетателя и почему это защитное покрытие стало таким популярным. Мы также углубимся в различия между высокотемпературными керамическими спреями и нанокерамическим покрытием, потому что, хотя оба продукта предназначены для защиты твердой поверхности, они сильно различаются во многих отношениях.
В чем разница между нанокерамическим покрытием и спреем для керамического покрытия? Коллекторы выхлопных газов вторичного рынка, возможно, являются наиболее часто используемым покрытием для высокотемпературного керамического покрытия.
Фото предоставлено: ATX Powder Coating/Facebook
Одно из ключевых различий между высокотемпературным распылением керамического покрытия и самодельным нанокерамическим покрытием, таким как Armor Shield IX, заключается в том, что одно наносится на поверхность, а другое встраивается в нее. . Это не делает одну форму керамического покрытия лучше другой; он просто дает каждому присущие ему сильные и слабые стороны.
Хотя оба продукта предназначены для защиты поверхности от загрязнений и физических повреждений, большинство нанокерамических покрытий не могут выдерживать экстремальные температуры в течение длительного периода времени. Высокие температуры — это хорошо, но все, что выше 440 ° по Фаренгейту в течение более чем «горячей минуты», превратит это нанокерамическое покрытие в отслаивающуюся кучу сожалений.
Напротив, высокотемпературные покрытия для выхлопных газов, как правило, не содержат нанотехнологий и, следовательно, не могут проникать во все микроскопические щели, дефекты и наплывы на поверхности.
Вместо этого высокотемпературные керамические покрытия предпочитают затвердевать поверх поверхности, что делает их идеальными для теплозащиты и придает им превосходные свойства защиты от точечной коррозии и коррозии. Многие аэрозольные керамические покрытия, предназначенные для выхлопных газов, могут выдерживать воздействие температуры 1200° по Фаренгейту в течение длительного периода времени, а продукты для экстремальных температур выдерживают более 2500° устойчивого нагрева.
В отличие от нанокерамических покрытий, которые абсолютно прозрачны, высокотемпературный материал может иметь множество цветов и вариантов окраски. От ярко-глянцевого яблочно-красного до темно-матового зеленого и далее до оттенков сатинового металлика, находящихся где-то посередине, высокотемпературные керамические покрытия предлагают множество оттенков, которые заслуживают того, чтобы их увидели. Я снова рифмую? Так и думал…
Примечание Quick Nerd: В мире поверхностных покрытий «мил» используется в качестве единицы измерения для определения уровней толщины покрытия, и, вопреки распространенному мнению, «мил» НЕ является синонимом миллиметра. Один мил высокотемпературного керамического напыления размером 1/1000 дюйма соответствует 25,4 микронам нанокерамического покрытия. Это означает, что вам придется применять Armor Shield IX более дюжины раз, чтобы достичь такого же уровня толщины!
Лучшие области применения для высокотемпературных керамических покрытийВысокотемпературные керамические лакокрасочные покрытия можно наносить практически на любую поверхность, включая дерево, пластик, акрил, стекловолокно и другие. Но благодаря своей термостойкости такие керамические покрытия действительно сияют, когда их наносят поверх теплонасыщенного металла.
Алюминий, нержавеющая сталь, углеродистая сталь, хром, чугун, магний, неодобрительный взгляд вашего бывшего… если он может обжечь вас, скорее всего, он также может быть защищен высокотемпературным керамическим покрытием.
Применение в автомобилестроении не ограничивается только компонентами выхлопной системы. Такие вещи, как воздухозаборник и трубопроводы промежуточного охладителя, корпуса турбокомпрессоров и клапанные крышки, могут быть покрыты керамическим покрытием. Были достигнуты даже успехи в покрытии внутренних частей двигателя, причем головки поршней с керамическим покрытием стали одним из самых последних достижений.
Преимущества использования высокотемпературных керамических покрытийДля энтузиастов автомобильной производительности вложение тысяч долларов в модернизацию топливной и выхлопной систем является лишь частью головоломки производительности.
Для того, чтобы защитить эти дорогие быстродействующие товары, автовладельцы либо предпочтут профессиональное порошковое покрытие своих рабочих деталей, либо прибегнут к методу распыления высокотемпературного керамического покрытия.
Хотя встроенная ссылка в приведенном выше предложении даст вам некоторое представление о мире порошковых покрытий, следующий список посвящен высокотемпературным керамическим покрытиям. Так что выбирай свой путь мудро, о могущественный любознательный.
Основная причина, по которой большинство людей выбирают керамическое покрытие для своих автомобильных и мотоциклетных деталей, заключается в том, чтобы защитить их от непогоды и контролировать нагрев, что, в свою очередь, помогает предотвратить коррозию и неизбежный натиск ржавчины.
Стандартные выпускные коллекторы, выпускные коллекторы, корпуса турбин и все последующие трубопроводы особенно подвержены этим недугам. Мало того, что эти детали нагреваются сильнее, чем джакузи на седьмом уровне ада, они также подвергаются воздействию всевозможной дорожной грязи и загрязнения ходовой части.
Вот почему продукты с более прочным высокотемпературным керамическим покрытием разработаны таким образом, чтобы уменьшить повреждения, вызванные столкновениями с дорожным мусором, камнями, ветками деревьев и т. д.
По мере того, как детали, ориентированные на выхлоп, нагреваются (здесь мы говорим об уровне нагрева), а затем начинают остывать, металлы внутри этих компонентов проходят «термический цикл».
Хотя полностью исключить термоциклирование невозможно, снижение скорости разложения сплава может помочь предотвратить преждевременное появление таких явлений, как коррозия и усталость под напряжением.
В компонентах выхлопной системы температура часто затмевает 1000° по Фаренгейту после нескольких минут работы дроссельной заслонки, а затем поднимается выше этого уровня. Высокотемпературное керамическое покрытие не только выдерживает эти обжигающе горячие уровни жестокого обращения, но и защищает такие вещи, как электроника и топливные системы, от этого огненного натиска.
Что касается компонентов турбонаддува и нагнетателя, то нанесение высокотемпературного керамического покрытия помогает поддерживать более низкую температуру поверхности и внутренней поверхности и, таким образом, снижает риск перегрева двигателя. Это, в свою очередь, уменьшает термоциклирование и продлевает срок службы деталей с быстрым температурным циклом, а также компонентов вокруг них.
Внешний вид Хотите внести контраст в моторный отсек, но опасаетесь, что краска вымокнет и отслоится? Решением, которое вы ищете, могут стать высокотемпературные керамические покрытия. Кредит Фотографии: Cerakote Вы когда-нибудь видели, как совершенно новый выпускной коллектор из нержавеющей стали приобретает великолепный медный оттенок после первого запуска? Что ж, этот великолепный блеск не будет длиться долго, так как обесцвечивание и поверхностные пятна всегда стремятся образоваться на деталях выхлопной системы, что в конечном итоге приводит к точечной коррозии и коррозии.
Нанесение высокотемпературного керамического покрытия не только улучшает поглощение тепла, но также улучшает внешний вид, устраняя риск появления ржавчины и коррозии, что может привести к неприглядному и потенциально вредному внешнему виду.
Доступно множество вариантов цвета и блеска, и привлекательность, связанная с высокотемпературными спреями для керамического покрытия, выходит далеко за рамки простого контроля температуры и защиты.
Производительность Перки От корпусов нагнетателя и турбоколлекторов до водосточных труб, крышек радиаторов и корпусов колоколов высокотемпературные керамические покрытия с удовольствием выдерживают тепло. Фото предоставлено: Dean Bithell/FacebookПоскольку двигатель внутреннего сгорания должен вдыхать топливо и воздух до воспламенения, он также должен после этого выдыхать отработавшие выхлопные газы.
Нанесение высокотемпературного керамического покрытия как снаружи, так и внутри выхлопной системы помогает улучшить поток. Это означает, что двигателю не нужно так много работать, что позволяет ему работать более эффективно и, таким образом, генерировать больше мощности.
«Некоторые составы стабильны до 2000F и требуют только отверждения при комнатной температуре. Поскольку керамические покрытия нуждаются только в отверждении в условиях окружающей среды и в то же время обладают отличными адгезионными свойствами, они хорошо подходят для пластмасс, дерева, полимеров, композитов и, конечно же, металлов».
-Crest Coating Inc.
Поскольку один слой высокотемпературного распыляемого керамического покрытия создает гладкую однородную поверхность и имеет очень высокие уровни допустимой химической стойкости, он может улучшить поток воздуха, жидкости и выхлопных газов.
При нанесении на компоненты выхлопной системы высокотемпературные керамические покрытия уменьшают тепловое вращение, поэтому тепло не впитывается в конкретную область, а равномерно распределяется по поверхности. В выхлопной системе это не только помогает продлить срок службы и снизить температуру, но также устраняет обратное давление, что улучшает поток и, таким образом, увеличивает эффективность и мощность.
Примечание Quick Nerd: Хотя большинство высокотемпературных напыляемых керамических покрытий предназначены для эксплуатации при температурах ниже 1600°F, существуют такие компании, как Cerakote, которые специализируются на производстве готовых к распылению покрытий, отверждаемых на воздухе, которые могут выдерживать до 1800°F жестокого обращения.
Различные виды высокотемпературных керамических покрытий Спрей для высокотемпературных керамических покрытий можно наносить практически на любую вообразимую деталь, но они разработаны так, чтобы лучше всего работать с металлическими деталями, которые сильно нагреваются в течение длительного периода времени.Фото предоставлено: Crest Coating Inc.
Когда дело доходит до высокотемпературных керамических покрытий, существует множество различных производителей, продуктов и методов нанесения, из которых вы можете выбирать, причем некоторые из них гораздо более суровы, чем другие.
С одной стороны, у вас есть аэрозольная краска в виде «погремушки» для самодельных высокотемпературных керамических покрытий, которые обычно изготавливаются на основе эмали и используют керамические смолы для термостойкости. Так же, как и аэрозольные грунтовки для транспортных средств, эти виды продуктов валятся на дне пула защиты поверхности и, следовательно, не всегда получают восторженные отзывы от пользователей.
Многоступенчатые профессиональные керамические покрытия, с другой стороны, имеют тенденцию быть гораздо более устойчивыми, и, следовательно, облагаются гораздо более высокой ценой. В то время как нанесение высокотемпературного керамического покрытия самостоятельно сэкономит значительное количество денег, есть много людей, которые совершенно не против отдать свои с трудом заработанные деньги профессиональному установщику.
Какой бы метод нанесения вы ни выбрали, следующие три класса плавкости широко признаны в качестве основных пороговых уровней для высокотемпературных керамических покрытий. Знание того, какой из них распылить и где он будет работать лучше всего, определит уровень эффективности и долговечности детали, поэтому выбирайте с умом, а в случае сомнений спросите мнение авторитетного установщика.
Низкотемпературные керамические покрытия часто используются на таких вещах, как корпуса дифференциалов, крышки клапанов, блоки цилиндров, опоры двигателя и опоры радиатора. Хотя образы местного магазина автозапчастей приходят на ум, когда кто-то думает о низкотемпературном спрее для керамического покрытия, профессиональные установщики часто используют и более мягкие составы.
Среднетемпературный Керамические покрытия – До 1600 ° по Фаренгейту Спрей для керамического покрытия средней дальности — это то, что вам нужно, если вы хотите покрыть выпускной коллектор, систему турбонагнетателя или нагнетателя, а также открытые внешние поверхности двигателя и глушители мотоцикла. Поскольку обычно он немного дороже, чем средний низкотемпературный спрей для керамического покрытия, материал среднего качества обеспечивает хороший баланс между доступностью и высокотемпературной функциональностью.
Наиболее жесткие формы теплозащитного керамического покрытия разработаны специально для гоночных автомобилей и внутренних частей двигателей. Выпускные коллекторы и корпуса турбокомпрессоров особенно богаты теплом, так как они одними из первых подвергаются воздействию отработавших газов, образующихся в процессе сгорания.
Но даже в этом случае керамические покрытия для экстремально высоких температур не всегда необходимы. Так что, если вы не выезжаете на трассу каждые выходные или не хотите установить новый рекорд наземной скорости, выбор этого дорогого высокотемпературного керамического покрытия будет излишним.
Несмотря на то, что нанокерамические покрытия способны выдерживать температуру до 440° по Фаренгейту, они не могут предложить многого с точки зрения теплозащиты. На самом деле, все, что выходит за пределы этого порога в 440°, скорее всего, приведет к появлению аромата, ориентированного на автомобили, за которым следует творческий поток нецензурной брани.
В то время как некоторые отчеты показывают, что наконечники выхлопных труб с нанокерамическим покрытием со временем задерживаются, есть столько же людей, которые видели, как керамическое покрытие на их грейпфрутовой стрелке глушителя начинает отслаиваться после быстрой поездки в местный порномагазин. . Я имею в виду ломбард. Я имею в виду ростовщика. Гм… хорошо… идем дальше…
Наш совет: если вы планируете нанести на выхлопные патрубки слой Armor Shield IX, наносите на свой страх и риск. Выхлопная труба может быть самой прохладной (и самой блестящей) частью выхлопа, но даже в обычных условиях вождения она может быстро превзойти этот порог в 440 градусов по Фаренгейту.
Quick Nerd Примечание: Гарантия AvalonKing на продукт может быть лучшей в отрасли, но она не распространяется на приложения с экстремально высокой температурой, поэтому, пожалуйста, не приходите просить возмещения, если этот маленький высокотемпературный эксперимент не удался. -вне.
Разделительные капли Преимущества, связанные с распылением высокотемпературной керамики, могут быть неоспоримыми, но это не всегда делает их идеальным средством для защиты твердых поверхностей. Фото: Aerocoat/Facebook Несмотря на то, что некоторые высокотемпературные керамические изделия имеют кремнийсодержащую керамическую матрицу и служат многим из тех же целей, что и самодельные нанокерамические покрытия, на этом сходство между этими двумя продуктами заканчивается.