Ячеистый стол из фанеры своими руками чертежи, верстак из ОСБ
Верстак для гаража — это главный предмет мебели. Он представляет собой специально оборудованный стол, предназначенный для выполнения различных монтажных и ремонтных работ. При наличии ящиков и экранов он также используется для хранения инструментов, метизов, запчастей и других предметов.
По своему виду он больше всего напоминает письменный стол, однако из-за назначения имеет ряд особенностей — крепкую столешницу для проведения работ, мощный каркас, иногда — перфорированный экран для крепления подручного инструментария.
В этой статье мы разберёмся в видах этой мебели, из чего она состоит и как изготавливается. Вы также узнаете, как её можно сделать своими руками.
Содержание
- Виды верстаков, которые можно использовать в гараже
- Конструкция верстака
- Подготовительные работы
- Материалы для слесарного верстака:
- Алгоритм работ для металлического верстака:
- Материалы для столярного стола:
- Как изготавливается деревянный верстак:
- Инструменты для работы
- Каркас столярного верстака
- Столешница верстака для столярных работ
- Ящики для хранения инструмента в столярном столе
- Используйте ящики от старой мебели
- Отсек столярного стола для переносного ящика
- Как сделать модули с удобными выдвижными ящиками
- Как сделать выдвижной ящик столярного верстака из фанеры
Виды верстаков, которые можно использовать в гараже
Эта промышленная мебель делится на два основных типа:
- слесарный верстак — обязательно должен быть металлическим;
- столярный верстак — может быть деревянным.
При этом металл — предпочтительный материал для рабочей поверхности любого типа. Это связано с тем, что различные технические жидкости могут въесться в древесину, кроме того — при работах на столе применяются острые режущие инструменты, которые повредят непрочный материал, царапает его и металлическая стружка.
Третий вариант — это комбинированный верстак. Основание в таком случае выполняется из дерева, а на него кладётся крышка — металлическая пластина. Это позволяет мебели быть лёгкой, но подходящей для столярных работ.
Помимо основного деления есть и другие важные критерии, связанные с конструкцией мебели, а также её комплектацией. При должном умении и наличии необходимого инструмента можно изготовить любую разновидность самостоятельно.
Конструкция верстака
- База — то, на чём стоит верстак. Она может быть выполнена как каркас из стоек, но может представлять собой и тумбы (с дверцей и ящиками или полками).
- Столешница — поверхность, на которой проходит весь рабочий процесс. На ней размещаются детали, также к ней зачастую крепятся тиски. Часто состоит из основы и крышки, материал которых может различаться.
- Подвесные ящики и тумбы — дополнительное оборудование, которое крепится к основе.
- Перфорированный экран — он ставится под прямым углом к столешнице, на него обычно навешивается самый необходимый инструмент.
Последние два пункта, таким образом, необязательны и зависят от особенностей эксплуатации. Например, экран особенно удобен, если работа ведётся постоянно, например, владелец — автомеханик. И напротив — если инструмент требуется нерегулярно, он может храниться просто в ящиках и на полках.
Подготовительные работы
Если Вы решили делать верстак своими руками, нужно сначала подготовиться к этому серьёзному делу.
В первую очередь стоит озаботиться вопросом места, где будет стоять мебель. Зачастую для её расположения выбирают угол гаража, где он не будет мешать и при этом будет удобен для работы.
В зависимости от этого проводят расчёты размеров будущего верстака.
- Длина выбирается в зависимости от возможностей помещения, особенностей эксплуатации и т. д.
- Рекомендованная ширина — около 500 миллиметров, такая, чтобы человек мог дотянуться до дальнего края.
- Высота рассчитывается следующим образом. Согните руки в локтях и представьте, что Вы опираетесь о крышку. Расстояние от ладоней до пола и будет высотой, удобной для работы.
Далее Вам нужен чертёж. Вы можете разработать его самостоятельно или выбрать из Интернета подходящий, скорректировав под свои размеры. На нём должны быть указаны габариты каждой детали. Для выбора конструкции можно также посмотреть фото готовых моделей.
Всё стоит спланировать заранее, хотя иногда практикуют и сборку «на месте», то есть сначала устанавливают опоры, а остальное проектируется в процессе. Таким же образом делают стол «от стенки».
Недостатки такого подхода — вероятность получить непродуманную конструкцию, которая окажется ненадёжной, а также невозможность заранее узнать количество материалов, которые нужно закупить. Если их большое количество, такой вариант более допустим, но всё равно не рекомендуется.
Важно спланировать необходимое количество отсеков для хранения, их тип и размер. Открытые полки удобны из-за доступности содержимого, но в целом это не лучший вариант — например, потому что инструмент стоит беречь от пыли и стружки. Поэтому большинство и готовых, и самодельных моделей оснащаются ящиками или дверцами, которые закрывают полки. Нужно заранее подготовить фурнитуру — ручки, петли.
Многие советуют не занимать центральную часть верстака ящиками и оставлять свободное место для ног мастера. Это повышает удобство, но полезное пространство для хранения теряется.
Материалы для слесарного верстака:
- Стальной уголок толщиной 4 мм.
- Болты, саморезы и анкерные болты.
- Фанера, 15 мм — для стенок верстака и ящиков.
- Труба с квадратным сечением 2 мм для каркаса.
- Листовая сталь толщиной около 3 мм, для крышки стола и держателей ящиков.
- Доска для столешницы, примерно 50 мм толщиной.
Часто используется дуб.
- Стальная полоса для направляющих и кронштейнов у ящиков.
Из инструментов Вам потребуются болгарка (с шлифовальным диском и диском по металлу), сварочный аппарат (с расходниками и специальной одеждой), шуруповерт, электролобзик, дрель, строительный уровень и рулетка.
Алгоритм работ для металлического верстака:
- Трубы или уголки распиливаются на опоры и перекладины, которые привариваются сверху и снизу. Уголком окантовывают столешницу.
- Небольшие отрезки уголка привариваются на расстоянии 12–15 см от пола как рёбра жёсткости.
- В верхней части, также из уголков, обустраивается обрешётка для столешницы.
- Создаются дополнительные стойки для полок и ящиков.
- Сами эти элементы делаются отдельно. Фанеру раскраивают на части, которые затем собираются саморезами.
- В каркасе просверливаются отверстия для задней стенки из фанеры.
- К боковинам привариваются стальные полосы с отверстиями для установки салазок для полок и ящиков.
- Все острые углы и сварочные швы проходят болгаркой с обдирочным кругом, ржавчина счищают специальной щёткой-насадкой.
- Каркас обрабатывают составом против коррозии и красят амосферостойкой краской.
- Обустраивается столешница из досок или цельной доски. Чтобы их прикрепить, древесина сверлится и монтируется с помощью болтов. Отверстия в каркасе делаются заранее. В других случаях обустраивается ложе, в которое укладываются доски и скрепляются друг с другом саморезами. При этом, учитывая разбухание древесины, оставляют зазоры от краёв ложа в 2–3 мм.
- Стол обшивается металлическим листом (рекомендуют оцинкованное железо), который фиксируется саморезами. Стальной лист перед этим обрабатывают преобразователем ржавчины.
- Края листа обрабатывают напильником.
- Собирается весь верстак целиком. Ставятся ящики и полки, каркас обшивают фанерой сзади и по бокам.
- Деревянные части пропитывают специальными составами против возгорания (антипирены) и поражения микроорганизмами, проводят лакировку, покраску.
- Устанавливаются тиски, размещается другой инструмент.
Чтобы верстак стоял наиболее устойчиво, стоит прикрепить его к полу, приварив к опорам уголки.
Материалы для столярного стола:
- Бруски с квадратным сечением 100х100 мм.
- Фанерные листы для крышки и задней стенки, толщиной 20 мм и более, можно использовать OSB-плиты.
- Доски 50х150 мм для обустройства каркаса.
- Болты (рекомендуют использовать квадратные мебельные, чтобы предотвратить вращение метиза в древесине), шайбы, гайки и саморезы.
Выбирая дерево, тщательно изучите его на предмет трещин и сучков. Нужно использовать качественный материал, чтобы получилась действительно долговечная мебель.
Из инструментов Вам понадобится электролобзик или ножовка, электродрель с набором свёрл по дереву, столярный угольник, рулетка, уровень, набор гаечных ключей.
Как изготавливается деревянный верстак:
- Отпиливаются доски для создания верхней рамы. Они прикручиваются друг к другу саморезами.
На середине получившегося каркаса ставят поперечную планку из доски 50х150 мм.
- Из шести одинаковых брусков делаются опорные ножки. Чтобы закрепить их на раме, их ставят к углам, просверливают по два отверстия в доске и опоре и монтируют с помощью длинных болтов с шайбами и гайками.
- Распиливаются доски для скрепления ножек внизу. Они ставятся на расстоянии примерно 30 см от пола. Доски ставятся так, чтобы их можно было использовать для установки полки. Например, одна из боковых и посередине крепятся с внутренней стороны, друг напротив друга. Остальные — с внешней стороны бруса.
- Нарезаются элементы столешницы из фанеры или OSB. Получившиеся листы крепятся заподлицо саморезами. Для защиты от повреждений фанеру покрывают оргалитом или другим материалом, который можно будет сменить после износа.
- Собираются все полки и ящики и устанавливаются в общую конструкцию.
- Древесину пропитывают различными защитными составами, верстак покрывают лаком или красят.
На всех этапах сборки конструкции следует проверять её ровность и устойчивость. При сборке рамы и монтаже опорных ножек необходимо использовать угольник. Готовая мебель проверяется на горизонтальность с помощью уровня.
Если хорошо провести подготовительные работы по планированию, тщательно придерживаться технологии изготовления и иметь в виду нагрузки, которые будет испытывать на себе конструкция, можно сделать самому качественный и долговечный верстак.
При этом важно быть уверенным в собственных силах и навыках обращения с инструментом. Сварочный аппарат и болгарка — крайне травмоопасные приборы, создающие риски для здоровья и жизни. Будьте осторожны.
В противном случае обратитесь к специалистам, которые помогут подобрать наиболее подходящий вам слесарный стол для гаража.
Столешница — основная часть верстака. Она испытывает наибольшие нагрузки в процессе эксплуатации. Выбор покрытия напрямую зависит от характера производимых действий. Различные производственные участки требуют использование определенного материала рабочей поверхности. Оцинкованные — лучше соответствуют занятиям, где велик риск повреждения сверлом, керном, ножовкой и другим режущим и ударным инструментом. Так же железное полотно предпочтительнее в зонах использования всевозможных жидкостей и в ремонтных цехах, т.к. с металла очень легко убираются потеки масла и грязь. Деревянные плиты обладают не меньшей прочностью, а при отсутствии вероятности режущих воздействий, гораздо лучшими демпфирующими и звукопоглощающими свойствами. Такие столешницы обладают более привлекательным видом. Фанера и массив дерева могут быть задействованы для сборки нестандартных рабочих мест (см. примеры). Стандартные модели имеют отверстия для крепления тумб, поэтому если необходимо установить оцинкованный лист на оригинальный верстак, то соответственно, столешница изготавливается по индивидуальным размерам.
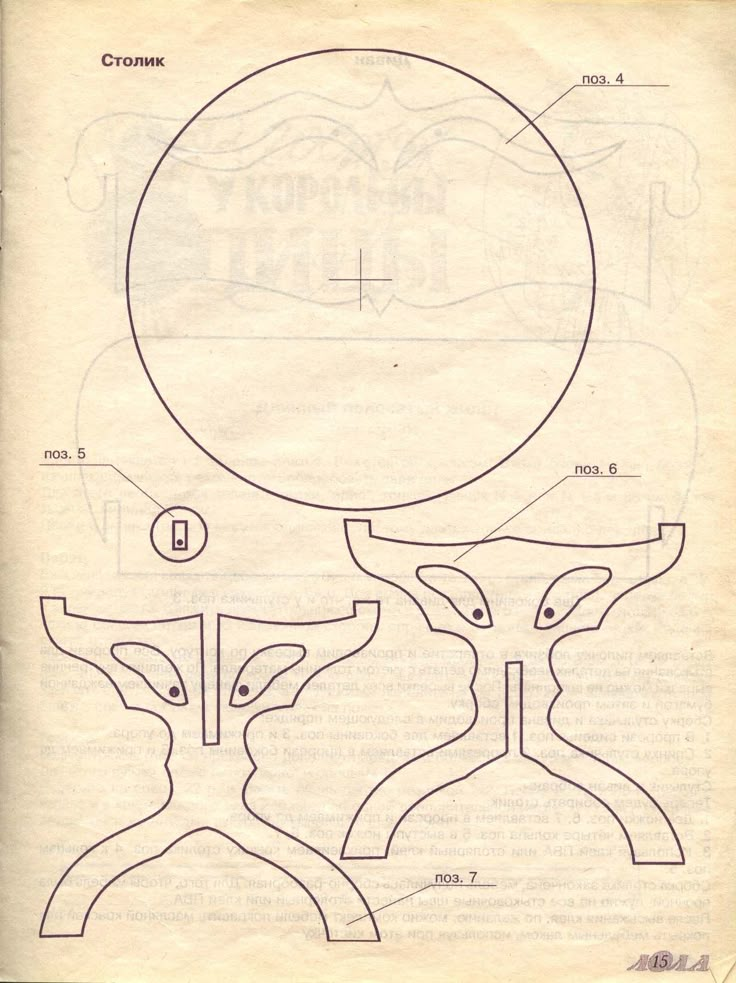
Специально для обеспечения работы в тяжелых условиях выпускается металлический настил толщиной 4мм. Он выдерживает самые высокие импульсные нагрузки. В качестве подложки применяется влагостойкая фанера разной толщины.
У этого столярного верстака надежный каркас, прочная рабочая поверхность и множество отделений для удобного хранения инструментов и приспособлений. Основную конструкцию вы сделаете своими руками за два дня, а различные полезные дополнения будете добавлять постепенно.
Инструменты для работы
Для обработки массива древесины и листовых материалов потребуется инструмент:
- Ножовка.
- Электрорубанок.
- Пила циркулярная.
- Шлифовальная машина.
- Дрель и сверла.
- Струбцины.
- Шуруповерт.
- Карандаш.
- Угольник.
- Рулетка.
- Кисть.
Каркас столярного верстака
Возьмите ровные сосновые доски без крупных сучков сечением 50х150 мм. Сырой пиломатериал просушите: чем ниже влажность досок, тем меньше вероятность коробления конструкции. Рассматриваемый столярный верстак рассчитан на комфортную работу мастера ростом 170–180 см. Чтобы изменить высоту конструкции, сделайте ножки выше или ниже.
Чертеж столярного верстака (вид спереди).
Чертеж верстака (вид сбоку).
Таблица 1 — список деталей каркаса
№ | Наименование | Чистовые размеры, мм | Материал | Количество | ||
толщина | ширина | длина | ||||
Деталь ножки | сосна | |||||
Нижняя проставка | сосна | |||||
Верхняя проставка | сосна | |||||
Поперечная проножка | сосна | |||||
Поперечина крышки | сосна | |||||
Продольная проножка | сосна | |||||
Продольная царга | сосна | |||||
Нижняя полка | ДСП, МДФ | |||||
Проставка столешницы | сосна |
Все элементы основания столярного верстака парные, поэтому размечайте на доске шириной 150 мм сразу две детали одинаковой длины.
Напилите все деревянные заготовки по длине за исключением проставок: короткие сподручнее нарезать уже строганными, а длинные следует отпилить позднее «по месту».
Замерьте ширину доски, отнимите толщину диска вашей циркулярной пилы и разделите результат пополам. Выставьте на мерной шкале высчитанный размер и убедитесь в перпендикулярном положении пильного диска. Распустите доски точно посередине.
Схема раскроя доски.
Острогайте детали и обработайте их наждачной бумагой средней зернистости.
Напилите нижние проставки и отшлифуйте торцы. Очистив поверхности от пыли, нанесите клей на малую проножку и на конец ножки.
Сожмите детали струбциной, вытрите выдавившийся клей и просверлите отверстия сверлом с зенковкой.
Скрепите заготовки шурупами 6,0х70. Подготовьте остальные ножки каркаса столярного верстака.
Снимите фаску на нижних торцах, чтобы снизить вероятность раскола древесины при подвижках верстака.
Подготовьте к склейке узлы соединения ножек с продольными проножками. Скрепите детали шурупами, выставив прямой угол.
Прикрутите все четыре ножки на свои места.
Разместите на полу половинки каркаса и продольные царги, отмерьте длину верхних проставок.
Напилите детали и закрепите на клей и шурупы.
Соберите на ровной поверхности верхнюю раму столярного верстака. Скрепляйте бруски столярным клеем и шурупами 6,0х80 мм, высверливая под них направляющие отверстия.
Соберите нижнюю обвязку верстака, использую для удобства струбцины и вспомогательные дощечки.
Положите на место верхнюю раму и выровняйте всю конструкцию. Соедините части каркаса шурупами.
Вырежьте из листового материала толщиной 16 мм нижнюю полку и закрепите её на брусках
Столешница верстака для столярных работ
Используйте для крышки верстака листы МДФ, ДСП или фанеры толщиной 16–20 мм. Склейте плиты в два слоя и получите столешницу толщиной в 32–40 мм.
Для столешницы можно взять листы ДСП, оставшиеся от ненужной мебели. Например, подойдут стенки платяного шкафа. Возьмите их за основу и добавьте мелкие куски так, чтобы крышка столярного верстака получилась размерами 670х1940 мм.
Размещайте узкие плиты ближе к задней стенке и к центру верстака. Крупные листы располагайте в верхнем слое столешницы. Склейте раскроенные заготовки.
Скрепите листы саморезами, заглубляя их в раззенкованные отверстия. Обрежьте кромки ручной циркулярной пилой на расстоянии 20 мм от края.
Выровняйте столешницу относительно каркаса и закрепите шурупами.
Острогайте рейки для кромочных накладок. Отпилите скосы в 45° и нарежьте планки по длине. Положите на крышку верстака кусок ДВП, добавьте сверху ровную панель и скрепите всё это струбцинами.
Так проще крепить накладки. Выровняйте концы по краям столешницы и прижмите рейку к панели – верхняя плоскость встанет заподлицо с крышкой верстака. Придерживая планку одной рукой, высверлите направляющие отверстия и закрепить детали шурупами.
Переставьте приспособление на другую сторону и установите остальные накладки. Обработайте планки шлифмашиной.
Просверлите в углу плиты отверстие, позволяющее легко вытолкнуть ДВП из углубления при его замене.
Очистите поверхности от пыли и покройте деревянные части каркаса морилкой. Уложите ДВП в углубление крышки. Если вы используете куски материала, то зафиксируйте их с помощью двухстороннего скотча. Установите на верстаке столярные тиски.
Ящики для хранения инструмента в столярном столе
Заполняя пространство под крышкой столярного верстака, используйте модульный принцип. Отдельные блоки делать проще и удобнее впоследствии изменять, когда потребуется место для нового инструмента. Будет определенный перерасход материала, зато увеличится масса верстака и его устойчивости хватит для работы с электроинструментом.
Схема организация мест хранения: 1 – ящик полного выдвижения; 2 – вместительный ящик из фанеры; 3 – контейнер из ДСП; 4 – широкий ящик; 5 – отсек для переносного инструментального ящика; 6 – место для кейсов и заготовок.
Используйте ящики от старой мебели
Подберите подходящие по габаритам ящики от ненужного письменного стола или комода.
Подпишите деревянные элементы и аккуратно разъедините их. Очистите от клея шипы и проушины.
Обрежьте планки по ширине, удаляя стертые углы и растрескавшиеся пазы. Если родное дно ящика хлипкое, приготовьте более толстую фанеру или ДВП. Сделайте новые пазы на циркулярной пиле.
Соберите ящик «на сухую», при необходимости подгоните детали. Очистите поверхности и склейте конструкцию. Используйте монтажные уголки для точной сборки прямых углов.
Когда высохнет клей, отшлифуйте углы и стороны ящика, закрепив его для удобства работы.
Подготовьте направляющие планки и рассчитайте размеры модуля.
Расчет блока для трех выдвижных ящиков
Напилите нижнюю, верхнюю и боковые панели. Прикрутите шурупами направляющие рейки.
Соберите панели в модуль и опробуйте ход ящиков. Разместите блок внутри верстака, подложив под него подпорки.
Высверлите направляющие отверстия, раззенкуйте и закрутите саморезы. Крепите ДСП к верхним брусьям и к ножкам верстака.
Установите на ящики передние накладки. Разметив расположение корпуса, прихватите его одним шурупом. Вставьте ящик на место и скорректируйте положение панели. Аккуратно выньте ящик и заверните остальные шурупы.
Закрепите оставшиеся накладки – модуль с широкими выдвижными ящиками готов.
Отсек столярного стола для переносного ящика
Средний модуль изготавливается во всю высоту подверстачья для усиления жесткости столярного верстака. Для корпуса возьмите ДСП толщиной 16 мм и вырежьте две боковины, дно и крышку.
Корпус среднего модуля: 1 – схема каркаса; 2 – боковая стенка; 3 – нижняя и верхняя панели.
Прикрепите к боковинам направляющие планки, соберите каркас на шурупах и установите вплотную к правому блоку.
Подготовьте детали для выдвижного ящика.
Чертежи элементов ящика: 1 – длинная стенка; 2 – короткая стенка; 3 – днище; 4 – передняя накладка; 5 – рейка.
Циркулярной пилой выберите пазы в стенках, что можно сделать обычным диском. Выставьте глубину пропила 6 мм, а ширину 8 мм. Прогоните все четыре детали. Сдвиньте продольный упор пилы на 2 мм и выполните пробный пропил. Проверьте паз и отрегулируйте упор, если нужно. Прогоните остальные заготовки.
Соберите модуль и установите снизу рейки, защищающие кромки ДСП от сколов и обеспечивающие более «гладкий» ход.
Закрепите лицевую панель шурупами и поставьте ящик на место.
Как сделать модули с удобными выдвижными ящиками
Устройство корпусов этих модулей идентично предыдущим конструкциям. Размещаемый на роликовых направляющих выдвижной контейнер изготавливается с учетом монтажного зазора, поэтому его ширина будет меньше внутреннего размера корпуса на 26 мм (для распространенных направляющих толщиной 12 мм).
Устройство модуля и детали ящика: 1 – сборочная схема; 2 – задняя и передняя стенки; 3 – передняя панель; 4 – днище; 5 – боковые стенки.
Перед сборкой корпуса закрепите на боковинах ограничительные деревянные рейки и металлические направляющие.
Схема монтажа направляющих на стенках корпуса.
Закрепите готовый модуль под крышкой верстака.
Для установки направляющих на ящике отщелкните фиксаторы и вытащите малые рельсы.
Закрепите детали на стенках. Нужное расстояние от кромки до направляющей определите самостоятельно исходя из конкретной конструкции и зазора в 10 мм между стенкой ящика и верхней панели каркаса.
Выдвиньте до упора средние рельсы.
Вставляйте одновременно оба направляющие, придерживая пальцами средние рельсы. Если ящик «пошел» туго, выньте его и попробуйте заново.
Поставьте переднюю накладку на место.
Как сделать выдвижной ящик столярного верстака из фанеры
Напилите заготовки корпуса ящика из 10-миллиметровой фанеры, а для днища возьмите лист толщиной 5 мм.
Схема раскроя деталей для двух фанерных ящиков: 1 – передняя панель; 2 – задний вкладыш; 3 – боковая стенка; 4 – передний вкладыш.
Обработайте заготовки шлифовальной машиной.
Сделайте пазы под фанерное дно в боковых стенках, заднем и переднем вкладышем. Зачистите заусенцы наждачной бумагой.
Склейте и скрутите шурупами детали передней и задней стенок.
Нанесите клей на стыки и в паз.
Соберите конструкцию, использую уголки и струбцины.
Скрепите детали шурупами, высверливая направляющие отверстия.
Соберите своими руками второй фанерный ящик.
Установите на задней стенке столярного верстака панель, предназначенную для увеличения жесткости конструкции и для размещения ручного инструмента.
Покройте отделочным составом ящики и обрезанные торцы древесно-стружечных плит.
Подведите к изготовленному своими руками верстаку электропитание и займитесь наполнением контейнеров инструментами.
чертежи, размеры и пошаговые инструкции с фото
Фанера – один из самых доступных и качественных древесных материалов и потому её часто используют для изготовления различных предметов интерьера. Особой популярностью этот материал пользуется у людей, которые создают мебель в домашних условиях. Даже при отсутствии опыта, собрать простой журнальный столик из фанеры или ячеистый стол-верстак, не составит особого труда.
Что такое фанера
Фанера представляет собой плиту из тонких слоёв древесины, склеенных между собой. Этот материал отличается прочностью, лёгкостью в обработке и доступной стоимостью. Благодаря множеству преимуществ, фанера является достойной альтернативой натуральному дереву.
Столики из фанеры.
Некоторые особенности работы с фанерой
Фанера – это очень простой в обработке материал, с которым может справиться даже новичок. Из плит легко вырезать детали нужной формы и размера, и в отличие от древесно-стружечных изделий, на них не появляются сколы. Для изготовления фанеры используют разные породы дерева.
Самым оптимальным вариантом считаются плиты из берёзы.
Также при выборе материала следует обратить внимание на класс водостойкости. Плиты класса ФК подходят только для изготовления домашней или офисной мебели, а вот класс ФСФ подойдёт для уличного использования. Выбирая фанеру для столешницы, лучше остановиться на ламинированных плитах толщиной не меньше 20 мм.
Ламинированная фанера.
Плюсы и минусы самодельной мебели из фанеры
Самостоятельное изготовление мебели из фанеры имеет множество преимуществ:
- лёгкость работы с материалом;
- низкая стоимость;
- прочность конструкции;
- гибкость материала;
- экологичность
- свобода в выборе дизайна.
Существенных недостатков у самодельной мебели из фанеры нет.
Основные виды столов из фанеры
Мебель из фанеры отличается надёжностью и практичностью. Из этого материала изготавливают разные модели столов для офиса, дома, дачи и сада.
Как сделать стол из фанеры своими руками
Чтобы изготовить столик из фанеры, понадобится лишь свободное время и немного усилий. Работать с фанерой очень просто и, если внимательно следовать инструкции, всё обязательно получится.
Чертёж и размеры стола из фанеры
Перед изготовлением деталей, следует подготовить схематический рисунок, с указанием всех размеров. Чертёж может быть нарисован от руки или сделан с помощью компьютерной программы.
Можно воспользоваться готовыми рисунками понравившихся моделей из интернета.
Материалы и инструменты
Чтобы получить прочный и красивый стол, очень важно выбрать качественный материал. Плита фанеры для столешницы не должна быть очень тонкой. Минимальная толщина может составлять 10-15 мм, но лучше использовать листы от 20 мм. Также необходимо выбрать материал для ножек фанерного стола:
- металлические трубы;
- брусья из дерева;
- основание из фанеры.
В зависимости от толщины используемой фанеры, необходимо подготовить инструмент для вырезки деталей. Для самых тонких плит толщиной 3-5 мм, достаточно будет простого канцелярского ножа, фанера от 5 до 10 мм распиливается ножовкой или лобзиком, а материал толщиной более 10 мм предполагает использование электролобзика или дисковой пилы.
Также для работы с фанерой понадобятся:
- циркуль;
- рулетка;
- уровень;
- карандаш;
- шуруповёрт;
- машинка для шлифовки;
- наждачная бумага;
- струбцины;
- мебельный степлер;
- морилка;
- краска;
- кисти и валик.
Как сделать простой фанерный стол
Пошаговый алгоритм изготовления простого фанерного стола для кухни, включает такие этапы:
- Исходя из выбранной модели составляют чертёж с указанием габаритов стола и размерами деталей.
- Из плотного картона изготавливают полноразмерные шаблоны всех элементов стола.
- На фанерную плиту наносят разметку с помощью карандаша и картонного шаблона.
- Все элементы аккуратно вырезают с помощью подходящего инструмента.
- Готовые детали тщательно шлифуют, чтобы избавится от шероховатостей и неровностей. Особое внимание уделяют стыкам.
- На всех деталях простым карандашом отмечают места установки крепежей.
- В размеченных местах просверливают отверстия. Сперва используют сверло меньшего диаметра, а после дополнительно обрабатывают большим.
- Все детали плотно соединяют с помощью саморезов, не оставляя зазоров, а места креплений прячут под специальными заглушками.
- Готовый стол при желании покрывают лаком или окрашивают.
Как сделать ячеистый стол из фанеры
Ячеистый стол – это необычная конструкция, которую используют для работы с гипсокартоном, фанерой и другими листовыми материалами. Главной особенностью такого стола, является отсутствие крепёжных элементов. Все детали изделия, кроме ножек, соединяются за счёт специальных ячеек. Ячеистый стол можно легко собрать и разобрать, без использования каких-либо инструментов. Для изготовления такой модели, достаточно следовать пошаговой инструкции:
- Для ячеистого стола лучше всего использовать ламинированные плиты из берёзы. Толщина листа должна составлять не меньше 1,5 см, а размеры – 122*244 см.
- На плиту фанеры переносят изображение всех деталей стола.
- Из листа материала аккуратно выпиливаются детали, со всеми необходимыми отверстиями на них.
- Элементы каркаса соединяются между собой с помощью ячеек.
- Детали для ножек скрепляют под прямым углом с помощью саморезов.
- Каркас и ножки также соединяют без использования крепёжных элементов.
Готовый верстак может быть использован мастерами для самых разных задач. При желании на отверстия можно установить заглушки, превратив его в обычный стол.
Обработка и декор готового изделия
Шлифовка | Когда стол из фанеры будет готов, его поверхность необходимо отшлифовать и покрыть морилкой.![]() |
Покрытие лаком | После того как морилка полностью высохнет, столешницу можно покрыть лаком или покрасить. Если для изготовления использовалась качественная фанера, то лучше сохранить природный рисунок и использовать лишь прозрачный лак. |
Окантовка | Чтобы края столешницы выглядели аккуратнее, можно использовать специальную окантовочную ленту. |
Особенности изготовления разных моделей столов из фанеры
Фанера является популярным материалом, поэтому из неё изготавливают самые разнообразные столы. Некоторые модели выделяются среди остальных и заслуживают особого внимания.
Фанерный стол с зонтиком
Такая модель отлично подойдёт для установки на даче, в саду или около бассейна. Основание столика имеет форму усечённой трапеции, а сверху устанавливается небольшая квадратная столешница, с отверстием по центру. Конструкция хорошо дополнит зонт, но удержать его не сможет. Для надёжной фиксации зонта, необходимо изготовить утяжелитель из бетона.
Мебель
Монтажный стол своими руками
Чтобы они были прочными и аккуратными нужен сварочный стол. На нём работать комфортнее, так как детали при необходимости закрепляются струбцинами или держателями. Для гаража, где мало места подойдёт складной вариант. Сварочный стол. Содержание 1 Разновидности столов для сварки 1. При периодическом выполнении несложных операций выбирается простой вариант.
Поиск данных по Вашему запросу:
Схемы, справочники, даташиты:
Прайс-листы, цены:
Обсуждения, статьи, мануалы:
Дождитесь окончания поиска во всех базах.
По завершению появится ссылка для доступа к найденным материалам.
Содержание:
- Стол своими руками: делаем деревянный и складной столы, изучив чертежи и пошаговые инструкции
- Как сделать кухонный стол своими руками
- Монтажные столы
- Как собрать сварочный стол в домашних условиях
- Столик своими руками
- Верстак в гараж своими руками: особенности конструкции, фото
- Сварочные столы своими руками
- Складной стол своими руками 1000 фото, чертежи, инструкции
ПОСМОТРИТЕ ВИДЕО ПО ТЕМЕ: Универсальный рабочий ячеистый стол. Сделан своими руками!
Стол своими руками: делаем деревянный и складной столы, изучив чертежи и пошаговые инструкции
Для домашней мастерской, если в ней часто производятся сварочные работы, просто необходима небольшая сварочная подмость, благодаря которой можно будет организовать комфортное рабочее место и при этом сэкономить некоторое пространство. Стол, выполненный из металла, кроме удобства при сварных работах еще будет исполнять и роль заземляющего контура, кроме этого, на его нижних полках можно будет расположить сварочный аппарат, электроды и другие вспомогательные инструменты.
Любой столик, предназначенный для сварочных работ, кроме удобства должен обладать еще и полной безопасностью для сварщика, так как при работе используется ток высокой силы с довольно большим напряжением. Для этого его конструкция должна отвечать следующим требованиям :.
И самое основное требование — в его конструкции не должны использоваться, а также храниться огнеопасные и выделяющие при нагреве ядовитые вещества материалы. Существует два вида столов для производства сварных работ для домашних мастерских — это обычные, самые простые столы для периодической сварки средней сложности и полупрофессиональные сборочно-сварочные столы, на которых выполняются более сложные задачи.
Отличается прочностью, простотой сборки и довольно удобной конструкцией для работы сварщика. Его конструкция состоит из жесткой рамы , которая сваривается из металла и состоит из четырех стальных стоек из уголка или профильных труб, сваренных между собой. По нижней части, на высоте примерно мм от пола, стойки сварены уголками, сверху они приварены к прочной раме, на которой находится металлическая столешница.
На стальной раме , на которой расположена столешница, желательно приварить кронштейны для сварочного провода, а под столешницей рекомендуется разместить неглубокий поддон для сборки пыли и окалины.
С левой или правой стороны может находиться тумба с несколькими отделениями для хранения различных инструментов. Оставшееся место приспособлено для временного складирования более крупной оснастки. Это уже довольно сложная конструкция сборочно-сварочного стола с дополнительной комплектацией. Эргономические свойства таких столов практически не отличаются от обычных, но на них предусматривается установка дополнительного оборудования для фрезеровки, сверления и других металлообрабатывающих операций.
Также столы могут оборудоваться встроенными вентиляционными системами. Ножки стола для жесткости всей конструкции, часто прочно прикрепляются к полу анкерными болтами или бетонной стяжкой. Важной особенностью этих столов является возможность поворачивать рабочую платформу, благодаря чему сварщик может накладывать сварные швы на свариваемые детали с одной рабочей точки.
Сборочно-сварные столы часто комплектуются быстросъемными слесарными тисками, комплектом различного размера струбцин и поворотными приставками для установки сварочного аппарата. Защитные ширмы от лучей сварки, вентиляционных воздуховодов и другие облицовочные материалы рабочей зоны должны быть из негорючих материалов.
Если раньше для этого применялась асбестовая ткань, то в настоящее время используются современные материалы Суперсил или базальтокартон. Освещение рабочей зоны должно быть настроено так, чтобы не создавались блики, мешающие работе сварщика стекла сварочных масок практически их не поглощают. Конструкция должна иметь поворотный механизм рабочей платформы и встроенную вентиляцию.
Для изготовления стола используются разнообразные материалы в виде стальных уголков, профильных труб, мелких швеллеров и двутавров с листовым прокатом. Главным условием к нему является устойчивость и способность выдерживать большой вес обрабатываемых на нем заготовок. Рабочую поверхность столешницу желательно изготавливать из швеллера или уголка, установленного на одно из ребер плоскостью вверх.
Между деталями столешницы должен оставаться зазор для струбцин и других крепежных инструментов, которыми будут при надобности крепиться свариваемые заготовки. Вспомогательные конструкции , с помощью которых можно увеличить площадь рабочей поверхности, лучше изготовить из профильных труб, так, как они по весу легче стального уголка.
Каркас защитного экрана также рекомендуется изготовить из профильной трубы и обшить тонким листовым металлом. Экран желательно сделать с боковыми бортами. Чтобы создать максимально комфортные условия работы, рекомендуется приобрести дополнительный набор инструментов с функциями надежной фиксации свариваемых деталей на рабочем столе с возможностью быстрого изменения их пространственного положения.
Они должны иметь прочность и стойкость при резких температурных переменах. К таким инструментам относятся струбцины , с помощью которых заготовки могут крепиться между собой или к рабочему столу. Их функция практически та же, что и у струбцин, но более широкого использования. Благодаря им можно устанавливать определенный угол и фиксировать более сложные соединения заготовок между собой. Магнитное основание.
Рекомендуется для фиксации мелких заготовок, которые закрепить другими механическими приспособлениями невозможно. Проблема с самостоятельным изготовлением стола для сварки заключается в том, что на данный момент очень мало информации о подобных конструкциях. Если взять за основу модели, изготовленные для промышленных целей, то их чертежи являются довольно сложными для использования в домашних мастерских, а многие функции вообще невозможно использовать. Альтернативой может быть самый простой чертеж, который можно просто доработать и улучшить самостоятельно.
Самый простой и доступный вариант стола , который можно быстро и без труда изготовить своими руками, доработав его самостоятельно. За пример изготовления можно взять конструкцию для производства сварочных работ, изготовленную из металлических профилированных труб и стального уголка. Естественно, что при изготовлении можно использовать другие размеры, материалы и менять геометрические формы самого стола.
Столешницу не рекомендуется делать из сплошного полотна. Заготовки труб нарезаются с помощью болгарки, а торцы зачищаются от заусениц. В первую очередь варится наружная рама, которая должна иметь четко одинаковые диагонали.
Внутренние профили вырезаются по проему изготовленной рамы и вставляются в ее середину швеллера укладываются на раму на расстоянии мм друг от друга, после чего все сварные швы зачищаются болгаркой. Ручки для конструкции сварочного стола могут понадобиться для удобства его перестановки на новое место.
Их длина должна примерно составлять около мм. Вырезанные стойки привариваются по углам ранее изготовленной крышки стола. После того как ножки приварятся к столешнице, для усиления жесткости всей конструкции делается дополнительная обвязка по нижней части стоек. Уголок варится плоской стороной в сторону нижней части стоек. В середину уголка будет уложена полка из ДСП или толстой фанеры для хранения различного сварочного инструмента и самого аппарата.
Во время приваривание ножек к крышке стола важно не допустить их перекоса. Они должны стыковаться с рамой четко под 90 градусов. Чтобы обеспечить такой ровный угол, необходимо использовать металлический угольник и рулетку. К стойкам желательно приварить колесики для удобства перемещения стола, но это только в том случае, когда его приходится часто перекатывать. Если он будет стоять стационарно, их лучше не использовать, так как при работе стол будет неустойчив, и нужно будет делать дополнительное тормозное крепление для колес.
К стойкам стола приваривается несколько крючков для хранения сварочного кабеля, держателя других приспособлений. Гвозди просто загибаются и привариваются с наружной стороны стоек. Короб приваривается под столешницей к стойкам под небольшим уклоном. Изготавливается из металлического листа и имеет небольшие бортики.
Его функция заключается в сборе мелкого мусора, окалины и шлака, сбитого со сварных швов. При этом он защищает от попадания этих же отходов на инструменты и приспособления, которые расположены на нижней полке, уложенной на обвязке стоек. Инструменты лучше всего хранить в специальном ящике, сделанном из ДСП или листового металла.
Лучше всего, если вместо него будет изготовлена тумбочка с несколькими полками, по которым можно рассортировать инструмент. Главная Сварка Сварочный стол, изготовленный своими руками для работы сварщика. Автор статьи Нагорный Александр Григорьевич. Сварка аргонодуговая. Сварочные аппараты Кемпи. Сварные швы.
Как сделать кухонный стол своими руками
Всем привет! Делюсь с Драйвовчанами своей самоделкой монтажный столик для сборки блоков фотокниги. Это покупной вариант Изучив процесс изготовления блока фотокниги чтобы книга открывалась на градусов, необходимо выдержать зазор в 2 мм 1 мм. Фото процесса нет, но есть готовый вариант, с которым разберется даже школьник. Планка в 1 мм. Для соблюдения разности склеивания.
Купить сварочно-монтажный стол от производителя. Быстрая доставка по всей Сварочный стол своими руками – практичные советы.
Монтажные столы
Поддоны для транспортировки и хранения груза — одна из самых необходимых вещей в производстве и продаже. Изготавливаются, как правило, ручным способом из осины или сосны. Создано Видео работы станков. Биржа оборудования. Все права защищены. Все о деревообрабатывающих станках и металлобрабатывающем оборудовании. Доска объявлений Деревообрабатывающее оборудование Станки для паллет, поддонов Продам Монтажный стол для изготовления сборки поддонов.
Как собрать сварочный стол в домашних условиях
Любой мастер, который регулярно занимается сварочными работами, прекрасно понимает сложность сборки отдельных конструкций. Облегчить задачу способен сварочный стол, который собрать своими руками не составит труда даже начинающему сварщику. Он является простой, но очень полезной конструкцией, которая позволяет выполнять основную массу сварочных и других операций. Причем делать это с комфортом. Важно только правильно его создать.
Столярный верстак и монтажный стол — необходимые вещи в арсенале любого домашнего мастера. Обработать деревянные заготовки, собрать оригинальное изделие или мебель авторской работы — этим предметам всегда найдётся применение.
Столик своими руками
Для домашней мастерской, если в ней часто производятся сварочные работы, просто необходима небольшая сварочная подмость, благодаря которой можно будет организовать комфортное рабочее место и при этом сэкономить некоторое пространство. Стол, выполненный из металла, кроме удобства при сварных работах еще будет исполнять и роль заземляющего контура, кроме этого, на его нижних полках можно будет расположить сварочный аппарат, электроды и другие вспомогательные инструменты. Любой столик, предназначенный для сварочных работ, кроме удобства должен обладать еще и полной безопасностью для сварщика, так как при работе используется ток высокой силы с довольно большим напряжением. Для этого его конструкция должна отвечать следующим требованиям :. И самое основное требование — в его конструкции не должны использоваться, а также храниться огнеопасные и выделяющие при нагреве ядовитые вещества материалы. Существует два вида столов для производства сварных работ для домашних мастерских — это обычные, самые простые столы для периодической сварки средней сложности и полупрофессиональные сборочно-сварочные столы, на которых выполняются более сложные задачи.
Верстак в гараж своими руками: особенности конструкции, фото
Все знают, что гараж необходим для того, чтобы ставить в нем автомобиль. Однако многие автовладельцы это помещение используют как склад ненужных вещей, а если позволяет пространство, то переделывают его под небольшую мастерскую. Следовательно, в нем устанавливают соответствующее оборудование — стеллажи, полки и верстак. Последний представляет собой многофункциональный рабочий стол, применяемый для обработки различных материалов, осуществления слесарных, монтажных и электромеханических работ. Верстаки для гаража можно сделать своими руками. Рабочий верстак для гаража часто сравнивают с письменным столом, потому что он обеспечивает удобство проведения разнообразных работ и дает возможность все необходимые инструменты держать под рукой.
Стол для сварщика своими руками: изготовление и полезные советы. Рубрика: потребуется сборочно-монтажный полупрофессиональный вариант.
Сварочные столы своими руками
Сварочный домашний стол должен быть наиболее функциональным. Лучше всего постараться собрать комбинированную конструкцию, которая подойдет не только для сварочных, но и для других монтажных работ. В бытовых условиях сварочные столы должны быть не только удобными для проведения работ, но и абсолютно безопасными, так как работы, связанные со сваркой, отличаются использованием довольно высокой силы тока и большим напряжением. Чтобы получить конструкцию, которая будет отвечать всем необходимым требованиям:.
Складной стол своими руками 1000 фото, чертежи, инструкции
Вашему производству нужны сварочные столы? Вы наверняка рассматриваете зарубежную продукцию?! Но не спешите ее заказывать, ведь есть возможность сэкономить, не поступившись качеством. Сварочно-монтажные столы VTM вы можете купить гораздо дешевле зарубежных аналогов, но с тем же функционалом и гарантированным качеством исполнения. Это несколько моделей столов, изготовленных из стали мм, они выдерживают вес до кг. Серия включает:.
Стол радиомонтажника повышает безопасность и комфорт выполнение задач.
Продумывая обстановку кухни и подбирая варианты мебели, любой владелец задумывается о покупке кухонного стола. От правильного выбора зависит функциональность и привлекательность, а также гармоничное сочетание с другими предметами интерьера. Стол служит не только для банального приема пищи, но и местом, где собирается семья для обсуждения каких-либо насущных тем. Поэтому немаловажно подойти к вопросу подбора с серьезным подходом. Одним из вариантов получить качественный стол является самостоятельное изготовление. Так вы получите желаемое приобретение, в точности соответствующее вашим пожеланиям. В интернете существует немало подробных инструкций сборки столов из разнообразных материалов.
Вы еще ставите прикормку и снасти на землю? Пора обзавестись специальным столиком. Цены на него в рыболовных магазинах немаленькие у. Но и своими руками можно сделать стол, который облегчит жизнь на рыбалке и сможет пригодиться для отдыха на природе.
Стол из дерева для старшеклассников и студентов своими руками – полный комплект чертежей
Процесс изготовления и чертежи стола для старшеклассников и студентов
Главное отличие нашего стола – он собирается и разбирается без использования специальных инструментов, студенты могут легко его перевозить с квартиры на квартиру, не беспокоясь поломать конструкцию во время транспортирования. И дома такой стол можно без проблем доставить летом из городской квартиры на дачу личным легковым автомобилем. Материал изготовления – хвойные доски и шлифованная ОСП, можно использовать ламинированную плиту или ламинированную фанеру. Для изготовления мебели вам понадобится наличие полного комплекта деревообрабатывающих инструментов, очень желательно иметь свою небольшую мастерскую с несколькими деревообрабатывающими станками. Довольно хорошо зарекомендовал себя бытовой универсальный деревообрабатывающий станок, на нем можно выполнять все столярные операции и соединения, качество отличное, производительность труда возрастает в несколько раз, а стоимость такого оборудования по сегодняшним меркам не считается очень высокой.
Стол для старшеклассников |
Стол в разобранном виде |
Краткое описание конструкции
Стол состоит из прямоугольной несущей рамы, с обеих сторон для соединения используются две перекладины, которые установлены на шкантиках и фиксируются саморезами. Такого простого соединения вам будет достаточно, чтобы обеспечить необходимую жесткость стола и легкость его разборки. Вместо шкантиков можете крепить конфирматами, но этот вариант не выдерживает многократных разбираний/собираний и по этой причине не совсем приемлем в данном случае.
Установка перекладин |
Две перекладины в месте пересечения запилите под углом в полдерева, соединение сделайте скользящим, но без больших зазоров. Они должны легко собираться и одновременно обладать устойчивостью к боковым нагрузкам во время работы за столом. Столешницу изготавливайте из шлифованной ОСП, необходимо покрыть ее прочным износостойким лаком не менее чем в два толстых слоя. Такой вариант столешницы наиболее дешевый, если вас финансы не особо беспокоят, то можете для столешницы использовать более качественные и дорогие материалы.
Собранный узел столешницы |
Чертежи рамы стола
Рама стола |
Части рамы 1 |
Части рамы 2 |
Части рамы 3 |
Части рамы 4 |
Части рамы 5 |
Части рамы 6 |
Части рамы 7 |
Части рамы 8 |
Как изготовить столешницу
Школьники и студенты не относятся к той категории пользователей, которые бережно относятся к мебели. Мы учли этот фактор и сделали для столешницы «защитные приспособления» – по всему периметру приделана деревянная профильная рейка, которая надежно защищает края стола от механических повреждений. Фиксируйте профильную рейку на шкантиках, дополнительно снизу под углом можете ввинтить саморезы соответствующей длины и диаметра. Поскольку профиль толще столешницы, то его края будут упираться в несущие планки каркаса и тем самым блокировать перемещения столешницы в горизонтальных направлениях – повышается устойчивость всей конструкции.
Окантовка |
Чертежи столешницы
Столешница |
Окантовка столешницы |
Изготовление каркаса для выдвижных ящиков
Это также довольно сложный узел с инженерной точки зрения. Чисто столярных трудностей во время изготовления не должно возникать, а вот с принципиальной схемой вы должны разобраться до тонкостей. Каркас для ящиков также должен легко разбираться без применения специальных инструментов, все отдельные элементы имеют разборные узлы крепления и одновременно гарантируют вполне достаточную жесткость конструкции. Прежде чем приступать к изготовлению, внимательно изучите назначение каждой детали и алгоритм ее установки.
Выдвижные ящики скользят по деревянным направляющим, для придания боковой устойчивости нужно установить диагональную стяжку. Принцип ее изготовления и установки точно такой же, как и в каркасе столешницы. Отличаются только размеры и количество. Для ящиков достаточного одной диагональной стяжки, а для каркаса стола пришлось устанавливать две. Ящики могут крепиться с любой стороны стола – это еще одно преимущество предлагаемой вам модели.
Чтобы разобрать каркас для ящиков достаточно лишь снять диагональную рейку и вынуть нижние конструкции из поперечин. Эти элементы соединяются в шип/паз, соединение должно быть скользящим, столярный клей не используется. Вверху конструкция крепится к несущим поперечинам рамы стола на четырех шкантах. Поскольку ящики довольно тяжелые сами по себе, а плюс еще учебники, то шкантики ставьте прочные, диаметр не менее десяти миллиметров, глубина отверстий не менее двадцати миллиметров. Тип соединения – скользящий, соединение должно разбираться в противоположную сторону от движения ящиков. Только так можно обезопасить себя от самопроизвольной разборки конструкции во время пользования ящиками.
Чертежи деталей каркаса для ящиков
Установочное место ящиков |
Детали для установки ящиков |
Детали для установки ящика 1 |
Детали для установки ящика 2 |
Детали для установки ящика 3 |
Детали для установки ящика 4 |
Выдвижные ящики
И эти элементы стола должны разбираться. Правда, здесь без минификсов уже не обойтись, придется использовать этот довольно сложный вид соединения мебельных деталей. Если вам не хочется пользоваться минификсами, то делайте более простые крепления на конфирматах или шкантиках. Ничего нового и особо сложного в изготовлении деталей ящика нет, алгоритм столярных работ обыкновенный. Дно ящика мы сделали из ДВП, вы можете заменить ее тонкой фанерой.
В боковых стенках ящика профрезеруйте канавки, размеры канавок должны отвечать размерам направляющие реек. И еще одно – для реек лучше использовать более твердую древесину, чем имеют хвойные породы, для таких целей вполне подходит береза. Для обеспечения более легкого скольжения места трения намажьте парафином, лучше намазывать горячим парафином при помощи обыкновенной небольшой кисточки. Излишки покрытия уберите сухой тряпочкой.
Чертежи выдвижного ящика
Детали ящика 2 |
Детали ящика 3 |
Дно ящика |
Финишная отделка стола
Наш вариант – использовать износостойкие лаки, не пожалеть денег и приобрести лак для деревянных полов. Покрывайте лаком детали перед сборкой, лучше пользоваться пневматическим краскопультом. Конечно, если он у вас есть в мастерской. Почему краскопульт гарантирует высокое качество? Все просто, микрокапельки лака ударяются о поверхность с большой скоростью, высокая кинетическая энергия удара гарантирует прочное и равномерное прилипание вещества к деревянной поверхности. Перед нанесением лака тщательно очистите поверхности от частичек пыли, деревянные детали должны быть полностью сухими.
← Деревянная кушетка своими руками – технология изготовления и полный комплект чертежей Как своими руками сделать стандартную односпальную кровать из хвойных досок — инструкция →
Рекомендуем посмотреть:
-
Фанера ХВОЯ | 18мм | 1220 мм х 2440 мм | хвойная | сорт 2/3 | НШ(ЦЕНА ПО ЗАПРОСУ)
0 руб
-
OSB | 8мм | 1220 мм х 2440 мм
0 руб
-
Фанера ФСФ | 15мм | 1500 мм х 3000 мм | березовая | строительная | НШ
2 900 руб
-
Фанера ЛАМИНИРОВАННАЯ ФОФ (КИТАЙ) | 18мм | 1220 мм х 2440 мм | береза
2 600 руб
-
Фанера ФК | 9мм | 1520 мм х 1520 мм | березовая | сорт 2/3 | Ш2
0 руб
-
Фанера ФК | 10мм | 1520 мм х 1520 мм | березовая | строительная | НШ
420 руб
-
OSB | 15мм | 1220 мм х 2440 мм
690 руб
-
Фанера ФК | 6мм | 1520 мм х 1520 мм | березовая | строительная | НШ
290 руб 500 руб
-
Фанера ФСФ | 12мм | 1220 мм х 2440 мм | березовая | сорт 4/4 | НШ
1 170 руб
-
Фанера ФСФ | 12мм | 1500 мм х 3000 мм | березовая | сорт 3/4 | Ш1
3 670 руб
-
Фанера ФСФ | 9мм | 1500 мм х 3000 мм | березовая | сорт 4/4 | НШ
2 480 руб
-
OSB | 18мм | 1250 мм х 2500 мм
945 руб
-
Фанера ХВОЯ | 12мм | 1220 мм х 2440 мм | хвойная | сорт 2/3 | НШ(ЦЕНА ПО ЗАПРОСУ)
0 руб
-
Фанера ФК | 15мм | 1520 мм х 1520 мм | березовая | сорт 2/3 | Ш2
0 руб
-
Фанера ХВОЯ | 6.
5мм | 1220 мм х 2440 мм | хвойная | сорт 3/4 | НШ(ЦЕНА ПО ЗАПРОСУ)
0 руб
-
Фанера ФК | 4мм | 1520 мм х 1520 мм | березовая | сорт 4/4 | НШ
200 руб 380 руб
-
Фанера ФСФ | 9мм | 1220 мм х 2440 мм | березовая | сорт 4/4 | НШ
900 руб
-
Фанера ЛАМИНИРОВАННАЯ ФОФ | 21мм | 1220 мм х 2440 мм | береза
3 500 руб
-
Фанера ФСФ | 12мм | 1500 мм х 3000 мм | березовая | строительная | НШ
2 541 руб
-
Фанера ФСФ | 12мм | 1500 мм х 3000 мм | березовая | сорт 2/3 | Ш2
0 руб
Также советуем почитать
13. 11.2015 → Столы
Сборно-разборный стол со скамейками для дачи из толстых досок
Предлагаемая скамейка изготовлена в «ретро стиле» и предназначается для использования на дачных участках. Материал изготовления – обрезные доски толщиной 40 мм, имеется комплект чертежей и описание столярных работ.
16.11.2015 → Столы
Процесс изготовления сборно-разборного столика из хвойных досок
Сборно-разборный столик можно использовать в небольших по размерам кухнях, а летом вывозить на дачу. Материал изготовления – хвойные доски, в статье есть полный комплект чертежей и профессиональные советы по работам.
25.11.2015 → Столы
Складные детские парта-стул из листовой фанеры
Делать домашнюю мебель своими руками всегда приятно, а делать эти вещи для своего ребенка – вдвойне приятно. Мы расскажем, как изготовить складную парту-стул из обыкновенного листа фанеры. Для работ потребуется минимум времени.
13.12.2015 → Столы
Раскладной стол для пикника из фанеры за полчаса
Столик для пикника это обязательный атрибут для семьи, которая ведет активный образ жизни. Конечно, в поход с собой его не возьмешь, но вот для выезда на природу на машине он отлично подойдет.
Как сделать стол шлифовальной машинки из фанеры
Шлифовальный станок из дрели своими руками: чертежи, фото и видео
Шлифовальный станок весьма распространен и востребован среди инструментальной оснастки, имеющееся в мастерской, поэтому его изготовление будет практичным и оправданным. С его помощью можно обрабатывать не только деревянные заготовки, но и некоторые виду других материалов, например пластики и некоторые металлические заготовки, конечно, без фанатизма (не болгарка же!). В данной статье мы опишем процесс создания такого станка.
Всевозможных вариантов конструкций шлифовальных станков существует огромное множество. И все эти варианты имеют свое применение и назначение. С помощью гриндера из болгарки можно шлифовать и точить крупные заготовки и придавать им нужную форму – его мастер держит в руках. Второй вариант – это шлифовальный станок, в котором, так же как и у гриндера, абразивным материалом является шлифовальная лента (шкурка), но он стационарный и на нем удобно обрабатывать небольшие заготовки, соблюдая при этом угол подачи, так как есть перпендикулярный стол.
Вариант шлифовального станка, который будет описан в данной статье намного проще двух предшествующих вариантов; абразивным элементом является шлифовальный круг с установленной на нем наждачной бумагой. Преимущество такого варианта очевидны – это:
- Простота изготовления;
- Шлифовальная поверхность намного больше, чем у ленточных вариантов;
- Плоскость шлифования жесткая, в отличии от ленточных, где шкурка может прогибаться под давлением заготовки;
- Данный станок является универсальным, то есть является одним из трех станков, которые выполнены на базе сверлильного станка (итого, со сверлильным всего 4 штуки).
Сверлильный | Токарный | Рейсмусовый |
Вот три статьи, в которых описано их изготовление:
Такое конструктивное решение, позволяющее на одной базе собрать четыре варианта станков, является универсальным и весьма практическим решением, так как экономит материал, время и место в мастерской, а так же в качестве привода имеет один электроинструмент – Дрель.
Шлифовальный станок, пожалуй, самый простой, так как нужно изготовить только шлифовальный стол. Все остальное уже готово.
Подготовка к работе
Подготовка к работе важна, так как именно на данном этапе определяется полный состав требуемого инструмента, механизмов, материалов, фурнитуры и крепежа. Именно на данном этапе нужно убедиться в наличии всего необходимого, чтобы не прерывать и не останавливать работу. Поэтому перед началом, рекомендуем просмотреть материал полностью и убедиться в том, что все есть в наличии.
Инструменты
В процессе работы Вам понадобится некоторый ручной и электроинструмент, проверим список:
- Инструмент для прямого пиления: Циркулярная пила или распиловочный станок.
- Электролобзик.
- Шуруповерт.
- Дополнительный ручной инструмент: молоток, струбцины, угольник, отвертка, разметочный карандаш и пр.
Материалы, фурнитура и крепеж
Для изготовления шлифовального станка на базе дрели Вам потребуется:
- Фанера толщиной 15 мм. Также может быть использована ДСП.
- Крыльчатая гайка – 2 шт.;
- Болт М6 и саморезы.
Основные конструктивные элементы
Основными конструктивными элементами шлифовального станка являются:
Изготовление шлифовального станка своими руками
Процесс создания станка мы состоит из создания его конструктивных элементов, а каждый создание каждого элемента мы подробно разберем, разбив на последовательные технологические операции. К каждой операции мы приложим фото, а в конце статьи поместим видео всего процесса создания шлифовального станка своими руками.
Основание (Рама и шпиндельная коробка) станка
Как отмечалось ранее – данный станок делается на база уже существующего (созданного ранее) сверлильного станка, поэтому, чтобы не дублировать информацию, предлагаем ознакомиться с технологией и процессом в соответствующей статье, там все детально описано. Таким образом, считаем, что рама и шпиндельная коробка уже готовы. Вот их внешний вид.
Шлифовальный стол
Шлифовальный стол имеет перевернутую П-образную конструкцию и довольно прост в изготовлении. Необходимо напилить следующие заготовки:
Деталь | Ширина х Длина х (Высота) | Материал |
Боковая стенка | 120 х 120 | Фанера 10 мм |
Нижняя часть | 120 х80 | Фанера 10 мм |
Элементы жесткости | 120 х 25 х 20 | Массив |
Направляющая | 200 х 30х 40 | Массив |
Столешница | 200 х 200 | Фанера 10 мм |
Теперь начинаем сборку. Затем собираем основание стола. Для этого крепим саморезами боковые стенки в торец нижней части стола. Получается перевернутая «П-образная» конструкция.
Далее крепим к элементам жесткости столешницу с помощью саморезов.
Теперь пришло время установить направляющую. Она является силовым элементом, поэтому место ее соединения нужно промазать клеем и дополнительно прижать саморезами.
Должна получится вот такая конструкция.
Затем необходимо установить этот стол на основание с помощью прижимных элементов (проще говоря, дощечка с болтом по центру).
Устанавливаем их снизу основания, болтами наверх. Устанавливаем шлифовальный стол на основание (направляющей вниз) и фиксируем гайками.
Шлифовальный станок готов.
Заключение
В данной статье описан полный пошаговый процесс создания шлифовального станка на база стандартной дрели, приложены все необходимые материалы – это фото и видеоматериалы. Надеемся, что после изучения у читателя не останется вопросов по технологии изготовления и сборки.
Габаритные размеры станка
Размещаем таблицу с габаритными размерами шлифовального станка сделанного своими руками:
Параметр | Значение |
Длина | 290 мм |
Высота | 240 мм |
Ширина | 600 мм |
Чертежи заготовок шлифовального станка
Приводим чертежи деталей , которые используются для изготовления станка.
Видео, по которому делался этот материал:
Источник: verstakdoma.ru
Ленточная шлифовальная машина из фанеры
Привет всем, в этой инструкции мы рассмотрим, как сделать маленький ленточный шлифовальный станок. Эта машинка позволит вам с легкостью выполнять шлифовку мелких предметов, это очень полезная машина для тех, кто занимается рукоделием, моделированием и так далее. Машина имеет небольшую мощность, поэтому собирается она из фанеры, этот материал имеет более чем достаточный запас прочности для такого станка. Материалы автор использует доступные, так, например, двигатель был использован от насоса, он имеет мощность около 250 Вт. Если самоделка вас заинтересовала, предлагаю изучить проект более детально!
Материалы и инструменты, которые использовал автор:
Список материалов:
— фанера;
— мебельные винты и гайки;
— двигатель на 250Вт /1725 оборотов в минуту;
— подшипники;
— резьбовые стержни;
— столярный клей или эпоксидный;
— дверные петли;
— наждачная бумага для изготовления ремня.
Процесс изготовления самоделки:
Шаг первый. Двигатель
Подберем подходящий двигатель для станка, машина у нас небольших размеров и мощный двигатель тут не нужен. Автор использовал для таких целей двигатель от насоса, его мощность составляет всего 250 Ватт, а что касается оборотов, то моторчик развивает в минуту 1725 оборотов. Важно заранее определить, в каком направлении вращается вал двигателя, у выбранного автором двигателя вал вращается против часовой стрелки, если смотреть на него спереди.
Сразу можно удлинить питающие провода, у автора они были очень короткие, так что он поставил распределительную коробку на моторчик.
Шаг второй. Вырезаем стойку
Вырезаем основную стойку станка, делаем нужный чертеж и вырезаем деталь на циркулярной пиле. В верхней части стойки есть паз, нужен он для шарнирного крепления верхнего кронштейна с ведомым колесом. Благодаря изменению углу колеса мы сможем центрировать ремень. Также сверлим в стойке отверстия и забиваем мебельные гайки.
Само собой, стойка и многие другие силовые детали собираются из нескольких слоев фанеры, так что таких деталей нужно нарезать несколько.
Что касается нижней крышки станка, то благодаря ней образуется своего рода пылесборник в нижней части станка. В крышке сверлим отверстие для патрубка, к нему можно будет подключать пылесос для высасывания пыли из станка.
Шаг четвертый. Заготовки для колес
Делаем ведомое и ведущее колесо для станка, в верхнем колесе должен находиться подшипник, ну а нижнее устанавливается на вал двигателя. Колеса делаются из трех слоев фанеры, сперва вырезаем квадраты, сверлим отверстия в центре. Ну а далее на помощь приходит фрезер, используя специальную насадку, автор как циркулем вырезает колеса.
В некоторых деталях нужно будет вырезать внутренние части, для этого автор сперва использует электрический лобзик, а потом дорабатываем детали на шпиндельном шлифовальном станке.
Шаг восьмой. Установка колеса на вал двигателя
Чтобы закрепить колесо из фанеры на валу двигателя, нам понадобится изготовить специальную соединительную деталь. Для этого понадобится шкив из алюминия, который можно закрепить на валу моторчик. Автор сделал крепеж из железа, но такой материал сложнее в обработке. Закрепив моторчик, автор придает шкиву желаемую форму, работая как на токарном станке. Далее в детали сверлим отверстия и нарезаем резьбу под винты в количестве 4 штуки.
Колесо можно прикручивать, учитывайте при этом, что биения должны быть минимальными, колесо должно быть закреплено четко по центру. Если биения есть, колесо можно отшлифовать, включив двигатель.
Шаг девятый. Сборка станка
Станок можно собирать, все соединения должны быть хорошо скручены саморезами или мебельными винтами. Стыкуемые части хорошо промазываем клеем, подойдет эпоксидный или столярный клей.
Двигатель висит на двух кронштейнах, спереди и сзади. Дополнительно двигатель прикручивается к кронштейнам при помощи винтов. Само собой, способ крепления мотора зависит от формы его корпуса, так что к каждому случаю нужно искать свои решения.
Нужно также установить упорную плиту, о которую мы будем упирать изделие при работе. Для ее изготовления можно использовать листовое железо, вырезаем деталь болгаркой.
Верхнее колесо крепим к кронштейну болтом с гайкой и изготавливаем шлифовальный ремень. Просто склеиваем из наждачной бумаги ленту нужной длины.
Обязательно для станка нужно сделать столик, он должен регулироваться по углу. Чтобы решить проблему, у автора столик закреплен на дверной петле, а снизу подпирается специальным регулирующими устройством.
Включается станок включателем клавишного типа, а чтобы машина не включилась случайным нажатием, автор сделал специальную защиту из фанеры над кнопкой. Станок готов, можно приступать к испытаниям, как все работает, можно увидеть на видео. Работает станок отлично, мощности вполне хватает, машина безопасна и сравнительно тихая. Надеюсь, вам проект понравился, и вы нашли для себя полезные мысли. Удачи и тверских вдохновений, если решите повторить подобное. Не забывайте делиться с нами своими идеями и самоделками!
Источник: usamodelkina.
ru
Как своими руками сделать стол из фанеры, пошаговое руководство
Если какой-либо из столов в доме приходит в негодность, его нужно поменять на новый. Качественная мебель в магазине стоит дорого, а дешевые изделия не отличаются большим сроком эксплуатации. Как вариант, можно сделать стол из фанеры своими руками, для его изготовления нужен минимум материалов и инструментов. Мебель получается прочной, надежной и полностью соответствует дизайну помещения.
Преимущества самостоятельного изготовления
Фанера состоит из нескольких слоев тонкого шпона, которые склеиваются между собой. Листы, которых в полотне от 3 до 23, складываются перпендикулярно друг к другу и склеиваются под прессом. Материал обладает следующими свойствами:
- Прочность. При изготовлении фанеры каждый новый слой увеличивает прочность предыдущего, поэтому стол будет служить длительное время.
- Гибкость. Материал позволяет сделать оригинальный декор, не трескаясь и не деформируясь при сгибании.
- Простая обработка. Легко резать и обрабатывать простыми инструментами.
- Невысокая стоимость. Фанера считается одним из самых дешевых строительных материалов.
Сырьем для изготовления стола из фанеры может стать материал марки Ш-2, который перед использованием обрабатывается с двух сторон.
Если мебель предполагается устанавливать на улице или в помещении с повышенной влажностью, то больше подойдет фанера с водостойким покрытием.
Сделанный своими руками стол из фанеры имеет ряд преимуществ:
- прочность;
- экологическая безопасность;
- легкость;
- простой ремонт в случае поломки;
- низкая стоимость.
Особенно важна простота обработки материала, с которой справится даже начинающий мастер.
Популярные модели
Фанерные столы можно сделать своими руками для любых целей. Популярными моделями являются:
- Кухонный. Красивый кухонный стол из фанеры должен быть прочным, поэтому при изготовлении используется материал с толстым слоем.
- Журнальный. Простота конструкции позволяет справиться с изготовлением столика даже новичку. Предмет играет главным образом декоративную роль, поэтому его необходимо украсить различными элементами.
- Садовый. Столик из фанеры для садового участка может быть различной конфигурации, на любых ножках. Главное, покрыть его составом, предохраняющим от влаги.
- Письменный. Строгий письменный стол изготавливается из ламинированной фанеры. Выдвижная деталь для клавиатуры превратит письменный стол в компьютерный. Модель предполагает комфорт во время работы, ноги должны быть удобно расположены под столом.
- Складной. Интересный складной стол из фанеры значительно экономит ограниченное пространство помещения. Предмет при необходимости можно сложить или использовать в разобранном состоянии.
- Трансформер. Модель легко превращается в стол-консоль или журнальный столик.
Кроме того, можно сделать фанерный ячеистый стол, который полностью заменит верстак. Предназначается модель для работы с листовыми материалами, позволяет зафиксировать заготовки, распилить их, обеспечивая удобство.
Материалы и инструменты
Прежде чем начать делать стол из фанеры, нужно приготовить качественный материал. При выборе следует обращать внимание на тип и сорт фанеры, толщину, породу дерева. Кроме того, необходимо приготовить специальные инструменты.
Для резки фанеры разной толщины подходят различные инструменты. Для листа 3 мм вполне подойдет обычный канцелярский нож, до 10 мм используется ножовка или лобзик, а если фанера имеет толщину больше 10 мм, то не обойтись без дисковой пилы или электрического лобзика.
Кроме того, для процесса работы используются такие предметы:
- карандаш;
- циркуль;
- линейка из металла;
- рулетка;
- струбцины;
- наждачная бумага или шлифмашина;
- шуруповерт;
- валик и кисти;
- степлер для мебели;
- краска, лак, морилка.
Обязательно надо приготовить ножки для стола. Производятся они из следующих материалов:
- Металлические трубы. Материал прочный, но, если его не обработать, будет подвергаться коррозии.
- Деревянные бруски. Также долговечный материал, но в условиях повышенной влажности может начаться гниение древесины, поэтому необходима обработка специальными покрытиями.
- Фанерное основание. Выполняется из толстой фанеры в различных конфигурациях.
Важно, чтобы ножки были прочными и надежными, тогда стол из фанеры будет стоять на них устойчиво.
Поэтапный алгоритм изготовления кухонного стола
В мастер-классе описано, как своими руками сделать стол из фанеры. Алгоритм выполнения работы:
- На бумагу переносятся чертежи в соответствии с дизайнерским решением, размерами.
- Вырезание фрагментов. Изображения переводятся на плотный картон, из которого вырезаются детали.
- Подготовка материала. Выбирать нужно качественную фанеру однородного цвета, не имеющую дефектов.
- Разметка деталей. На фанерный лист накладываются картонные шаблоны, обводятся карандашом.
- Вырезка деталей. С помощью инструментов вырезаются все детали: столешница, стойки или ноги.
- Обработка поверхностей. Все детали шлифуются наждачной бумагой или шлифовальной машинкой.
Особенно тщательно шлифуются стыки, так как элементы должны вплотную прилегать друг к другу.
Далее нужно проделать следующие шаги:
- Наметка расположения крепежных элементов. Карандашом делаются отметки в местах, где будет расположен крепеж.
- Сверление отверстий. Сначала просверливаются отверстия с диаметром, который меньше, чем у саморезов. Потом верх отверстий обрабатывается сверлом, у которого диаметр больше.
- Соединение деталей. Составляющие (столешница, ножки, боковые вставки) соединяются саморезами. Важно, чтобы между деталями не было зазоров. На шляпки саморезов надеваются специальные заглушки.
- Финишное покрытие.
По собственному усмотрению столешница и другие детали покрываются лаком или краской.
Важно, чтобы стол из фанеры был устойчивым, поэтому можно дополнить ножки горизонтальными перекладинами.
Пошаговый мастер-класс по созданию ячеистого стола
Создание ячеистого стола облегчит процесс работы с листовыми материалами с большой площадью. Верстак можно собрать наподобие конструктора, используя саморезы только для крепления ножек. Получившийся фанерный стол легко разбирать и собирать, что удобно при транспортировке или хранении. После составления чертежей и перенесения вырезанных деталей на картон можно приступать к изготовлению верстака пошагово:
- Подготовка материала. Ламинированная фанера должна иметь размеры 122 х 244 см, толщину – не менее 1,5 см. Лучше брать сырье из березы.
- Нанесение деталей на фанеру и вырезание. На листе материала обводятся все детали и вырезаются.
- Выполнение технологических отверстий. На готовых элементах выпиливаются отверстия.
Большие пропилы и отверстия потребуются при работе на столе, тоненькие, расположенные в боковых частях и в центре, пригодятся для монтажа верстака.
- Сборка. Детали собираются за счет пропилов.
- Подготовка ножек. Два элемента соединяются под прямым углом, на каждом делаются пропилы, с помощью которых ножки фиксируются к столу.
Конструкция выдерживает значительный вес, работать можно с материалом больших размеров. Ячейки используются как удобно, по своему усмотрению, а установив заглушки, модель превращают в обычный стол.
Источник: mblx.ru
Как сделать шлифовальную машинку
Когда работа с деревянной поверхностью подходит к завершению, наступает этап финишной шлифовки. Чтобы выполнить шлифовку без заусенцев, царапин, красиво закруглить острые углы любой детали, необходимо воспользоваться шлифовальной машинкой по дереву. Этот инструмент поможет выполнить шлифовку профессионально даже новичку, который впервые взял аппарат в руки. При наличии желания можно сделать шлифовальную машинку самостоятельно, используя лишь подручные средства.
Существующие виды шлифовальных машинок + (Видео)
Промышленностью выпускаются несколько видов машинок, отличающихся как конструктивно, так и по назначению. Вот основные из них:
- Эксцентриковая или орбитальная, в этом случае подошва инструмента одновременно вращается вокруг своей оси и по некоторой орбите. Получается так, что каждый раз она проходит немного в другом месте, поэтому царапины и заусенцы затираются с каждым проходом все сильнее и сильнее.
- Вибрационная модель. Здесь рабочая подошва осуществляет возвратно-поступательные движения с частотой порядка 20000 движений в минуту. Именно за счет этих движений и происходит шлифовка.
- Угловая шлифовальная машина, которую в народе принято называть «болгаркой». С помощью этого инструмента проводят грубую обработку деталей, крупных бревен и т.п. Для обработки применяются абразивные круги необходимой зернистости.
- Ленточная шлифовальная машинка, которая обычно используется для работ на больших поверхностях.
Конструктивно она представляет собой валики, приводимые в движение электродвигателем, на которые надета наждачная лента.
Изготовление ленточной шлифмашинки своими руками + (Видео)
Сделать ленточную шлифмашинку самостоятельно совсем не сложно, необходимо выполнить следующие этапы:
- подобрать подходящие материалы и детали;
- сделать надежную основу для закрепления инструмента;
- установить подходящую столешницу;
- закрепить вертикальные стойки с натяжителем и барабаном;
- смонтировать мотор и барабаны;
- закрепить наждачную ленту.
Чтобы обрабатывать довольно крупные детали и элементы необходимо изготовить крупную копию серийной шлифмашинки. Например, если взять электродвигатель мощностью 2 Квт или более мощный с частотой вращения ротора 1500 оборотов в минуту, то редуктор можно не ставить. Мощности такого двигателя вполне достаточно, чтобы вращать барабан порядка 20 см в диаметре и обрабатывать детали около 2 м.
Также можно использовать электрический двигатель от старой стиральной машинки. Станину в этом случае делают из толстого листа железа, подготовив место для установки мотора и тщательно закрепив его болтами для устранения вибрации. Конструкция такой машинки представляет собой 2 барабана, причем один из них зафиксирован, а второй может натягиваться и вращается на подшипниках вокруг оси. Основу для станка желательно выполнить из металла или нескольких листов толстой фанеры. Барабаны делают на токарном станке из ДСП. Лента нарезается из полотен наждачной бумаги шириной порядка 20 см и закрепляется на станине. Чем больше будут размеры стола, тем большие по размеру детали можно будет укладывать и обрабатывать в дальнейшем. Чертежи готовых изделий можно найти в сети.
Делаем шлифмашинку из болгарки
Многие могут сказать, что «болгарка» это же и есть угловая шлифовальная машинка, однако тут скрываются некоторые тонкости. Следует иметь ввиду, что УШМ имеет очень высокие обороты и зачастую довольно приличный вес. Чтобы отполировать поверхность болгаркой необходимо иметь немалый опыт в этом деле и пользоваться специальными полировочными дисками и кругами. Шлифовальная машинка имеет намного меньшие обороты двигателя и вес. Для работы заводской шлифовальной машинкой не требуется определенного опыта и сноровки.
Самостоятельно сделать из болгарки хорошую шлифовальную машинку, не уступающую по своим параметрам заводской машинке, можно только путем доработки ее электрической схемы, путем монтажа регулятора на более низкие обороты и путем применения специальных шлифовальных насадок.
Делаем шлифмашинку из дрели
Чтобы превратить обычную, бытовую электрическую дрель в шлифовальную машинку нужно оснастить ее специальной насадкой – рабочим барабаном или специальной опорной тарелкой, в зависимости от поставленной задачи.
Опорная или шлифовальная тарелка представляет собой пластиковую или резиновую основу с наклеенной наждачной бумагой и хвостовиком для зажима в патрон дрели. Тарелки с гибким валом подходят для работы с незакрепленной дрелью, а с жестким лучше применять только для хорошо закрепленной дрели.
Шлифовальные барабаны для бытовой дрели конструктивно представляют собой обычный цилиндр, хвостовик и наклеенную на цилиндр наждачную бумагу. При использовании барабанов рабочая поверхность шлифмашинки располагается параллельно оси вращения.
Делаем орбитальную шлифмашинку
В настоящее время сделать орбитальную машинку своими руками можно только из поломанной орбитальной машинки. Связано это со сложным устройством вращения рабочего диска, повторить которое самостоятельно довольно проблематично. Также следует иметь ввиду, что изготовленная специализированной фирмой машинка будет стоить не слишком много, а сделать ее своими руками будет очень сложно и займет много времени.
Делаем шлифмашинку из компьютерного винчестера + (Видео)
Любой, отслуживший свое жесткий диск можно переделать в миниатюрную шлифовальную машинку. Для этого необходимо выполнить следующие шаги:
- полностью разобрать винчестер и убрать из корпуса все, что расположено слева от магнитных дисков;
- вырезать рабочий круг из наждачной бумаги, сделать по центру круга отверстие для шпинделя;
- наклеить на вращающийся диск винчестера несколько полосок двустороннего скотча и закрепить на нем наждачную бумагу;
- сделать защитный экран, защищающий глаза от возможного вылета изготовленного наждачного диска;
- подключить готовую конструкцию к блоку питания от компьютера и пользоваться.
Конечно такая конструкция не обладает высокой мощностью, но заточить небольшой нож или ножницы вполне возможно.
Источник: instrument-blog.ru
САМОДЕЛКИН ДРУГ
Самодельный шлифовальный станок по дереву
Уважаемые посетители сайта «Самоделкин друг» из представленного автором материала вы узнаете о том, как сделать самостоятельно шлифовальный станок для обработки небольших деревянных деталей из старенького двигателя от стиральной машины и фанеры. Для человека «мастерового» необходимо иметь у себя в мастерской несколько станков для обработки металла и естественно дерева. Дабы упростить свой труд при шлифовании небольших деталей, необходимо использовать опять же станок. На сегодняшний день в строительных магазинах есть огромный выбор разного рода деревообрабатывающих и шлифовальных станков, но хороший аппарат и стоит не мало, а дешевый проработает недолго.
И вот пришла нашему автору идея создать шлифовальный станок к себе в каморку своими руками, для чего у него имелся отличный моторчик от стиральной машинки еще Советского производства, а так же фанера и ДСП того же периода выпуска, так что все необходимое имелось в запасе.
И так, давайте разберем конкретно, что понадобилось автору для сборки шлифовального станка? А так же рассмотрим весь процесс его создания от начала и до конца, посмотрим видео работы.
Материалы
- двигатель от стиральной машинки
- фанера ДСП
- уголок 4 шт
- саморез
- болт
- гайка
- шайба
- конденсатор
- выключатель
- наждачная бумага (круг)
- резина
Инструменты
- электролобзик
- дрель
- напильник
- набор гаечных ключей
- отвертка
- плоскогубцы
- линейка
- карандаш
Процесс создания шлифовального станка своими руками.
И так, для начала автор достал из закромов припрятанный для лучших времен двигатель от стиральной машинки, протер от пыли и проверил работоспособность подключив к сети, работает ) После чего произвел подключение по следующей схеме. Для удобства переноски станка, сделал импровизированную ручку. При помощи циркуля разметил центр на шкиву двигателя и просверлил 3 отверстия, для последующей установки шлифовального круга. Взял кусок фанеры, начертил круг и выпилил по намеченному контуру при помощи электролобзика.Для крепления двигателя к станине, автор использует вот такие вот уголки. Подключил двигатель, конденсатор и выключатель в виде тумблера. К станине прикрутил 2 дощечки. На полученные точки опоры прикрутил полочку, для удобства ведения работы. После чего мастер делает нескользящие ножки для станины из резины. Прикручивает саморезами. И вот собственно такой вот замечательный станочек получился. Работать с таким станком одно удовольствие, положил детальку на полочку и поворачивая в нужную сторону производится шлифовка. Самое главное автор абсолютно не потратился на данный станок, а хватит его надолго) Вам понравился материал, приходите к нам в группу ВКонтакте. Так же мастер оставил видео для закрепления пройденного материала. Приятного просмотра! Спасибо за внимание!
Источник: www.samodelkindrug.ru
Самодельный сотовый стол с ножками из промышленных труб
Мы с Треем решили обновить нашу столовую новым столом. Мне понравился мой стол из деревянных поддонов. Мы через многое прошли с этим столом. Вы, наверное, заметили это в бесчисленных постах о еде здесь, на ABM. Но я просто чувствовал, что готов к переменам.
Несколько соображений/проблем, с которыми мы столкнулись: Наша столовая больше похожа на столовую/уголок для завтрака. Он совсем небольшой. У нас есть люди, чтобы выпить или поужинать. Таким образом, чем больше посадочных мест мы можем разместить (с комфортом) в пространстве, тем лучше. Мы действительно хотели обновить наш стол до шести, а не до четырех.
Хотел бы я, чтобы у нас было место для стола на восемь человек, как обеденный стол Элси. Может быть, в нашем следующем доме. Не боится мечтать. Я также хотел стол, который я мог бы легко передвигать. Я знаю, странно.
Но, в зависимости от того, в какое время суток я фотографирую рецепты, которые вы видите здесь, в блоге, мне часто приходится передвигать обеденный стол ближе к окну. А ножки-шпильки иногда не подходят для катания на самокате. Трею пришла в голову идея создать стол в форме шестиугольника. Это оказалось ОТЛИЧНЫМ решением для максимального увеличения количества сидячих мест в нашей маленькой столовой. Мы также решили использовать водопроводные трубы с колесиками для ножек стола. В последнее время мне нравится внешний вид столов с трубчатыми ножками.
Сразу купить стол с трубчатыми ножками довольно дорого (мы видели их по цене выше 1500 долларов). Сантехнические трубы стоят дороже, чем вы думаете (или, по крайней мере, больше, чем мы думаем). Чтобы построить наш стол с нуля, со всеми материалами, стоило около 250 долларов, большая часть которых была потрачена на набивные трубы.
Итак, этот стол все еще был своего рода инвестицией. Но мы, конечно, сэкономили немалые деньги, сделав свой собственный, а не купив его (не говоря уже о том, что мы не смогли найти в продаже стол, который действительно соответствовал бы нашим точным потребностям). Если сантехнические трубы просто не соответствуют вашему бюджету, вы можете легко сократить свои расходы с помощью шпилек или даже окрашенных труб из ПВХ. Необходимые материалы:
четыре ниппеля из черного железа 10×1 дюйм (да, мы узнали, что они на самом деле так называются)
восемь фитингов из черного железа 8×1
один фитинг из черного железа 16×1 дюйм
четыре 1-дюймовых напольных фланца
четыре колеса для установки 1-дюймовой трубы (у нас есть 3-дюймовые ролики размера 6 с тормозами отсюда)
шесть 1-дюймовых тройников из черного железа
четыре 8-футовых деревянных доски 1×12 ( может быть немного длиннее, мы его обрежем)
шесть 4-футовых деревяшек 1×2 (может быть немного длиннее, мы его тоже обрежем)
один 4-футовый кусок твердого дерева 1×8 (может быть до 3 дюймов шире или длиннее)
транспортир
карандаш
16 (не менее) 0,75-дюймовых винтов
50 (или около того) 1,25-дюймовых винтов
наждачная бумага
морилка (если используете) и полиуретан (мы использовали полуглянцевый)
Вам также понадобится пара чистых тряпок или щеток, пила и дрель. За исключением встроенных роликов (вы можете заменить их еще 4 фланцами, если вам не нужна мобильность), мы смогли найти все необходимые материалы в наших местных хозяйственных магазинах. ваш 4-футовый кусок дерева с помощью 1,25-дюймовых винтов. Затем вы рисуете свой шестиугольник. Не позволяйте себе слишком увлечься этой частью, но здесь есть небольшая математика. Трей нашел этот правильный шестиугольник (все углы и стороны правильного шестиугольника равны) калькулятор, чтобы немного упростить себе задачу. Чтобы определить свою сторону, вам просто нужно измерить ширину 4 досок 1×12 рядом друг с другом и разделить ее на 2. Это число и будет вашим внутренним радиусом.
Возможно, вы знаете или не знаете, что 1×12 не обязательно означает, что ваша древесина имеет размер 1 дюйм на 12 дюймов. На самом деле это измерения до того, как древесина высохнет, поэтому 1×12 больше похоже на 0,8×11,25. Никогда не понимал, почему он так помечен, но я оставлю это экспертам.
Во всяком случае, , к счастью, ваши магазины коробок, такие как Home Depot и Lowe’s, в значительной степени соответствуют размерам древесины, так что вы, вероятно, можете использовать наши измерения:
• Радиус внутреннего радиуса: 22,5 дюйма
• Стороны: 26 дюймов
• Углы углов: 120° (верно для всех правильных шестиугольников)
На самом деле, все, что вам нужно знать, это длина сторон вашего шестиугольника (все они равны 26 дюймов) и углы ваших углов. . Потом остальное рассосется. Итак, отцентрируйте, измерьте и отметьте 26 дюймов с каждой стороны ваших 4 деревянных досок, соединенных вместе.
Они должны быть точно напротив друг друга. Теперь вытащите свой транспортир (очень дешевый, его можно найти в любом хозяйственном магазине), установите его на 120° и поместите в конец всей 26-дюймовой боковой разметки.
Начертите себе начальную контрольную линию и используйте более длинную линейку, чтобы продолжить ее, завершив боковую сторону. На самом деле вам нужно сделать это только 4 раза, так как оставшиеся 2 угла создадутся сами собой. Вот так и рисуется ваш шестиугольник.
Следуйте чертежу, чтобы обрезать края стола. Соберите трубы, чтобы убедиться, что они хорошо подходят к вашему столу. Может быть, вы хотите заменить одну из своих частей трубы на что-то более длинное или короткое (мы провели небольшую проверку методом проб и ошибок).
Это может сделать один человек, но намного проще вдвоем, особенно если этот второй человек готов вернуться в хозяйственный магазин за трубой другой длины. Просто к вашему сведению. Что касается губы, мы не удосужились быть почти такими же точными в наших углах, поскольку их практически никогда не было видно. Отрежьте 6 26-дюймовых частей от ваших 1x2s. Затем обрежьте чрезмерно компенсированные внутренние углы (как будто вы делаете нижний уровень пирамиды).
Мы только что посмотрели на углы, но убедились, что края остаются ровно 26 дюймов. Итак, когда вы смотрели на готовый стол, углы были безупречными. Затем с помощью 1,25-дюймовых винтов закрепите выступ на месте. Это укрепит стол и сделает его более чистым/профессиональным.
СОВЕТ: Ваша древесина никогда не будет идеальной и обязательно будет немного коробиться то здесь, то там. После того, как вы зафиксировали губу, посмотрите, не торчат ли немного некоторые из ваших основных досок. Если это так, просто используйте обрезки ваших досок 1×2, чтобы еще больше скрепить четыре основные доски вместе. Просто убедитесь, что вы ничего не мешаете ножкам вашего стола. Затем отшлифуйте весь стол, чтобы он был очень гладким. Если вы окрашиваете, добавьте свой выбор цвета. Мы использовали пятно от пшеницы. Дайте полностью высохнуть. Уплотнение полиуретаном. Мы использовали два слоя для дополнительной защиты.
Когда все высохнет, вы готовы прикрутить ножки и колеса к столешнице (здесь вы используете 0,75-дюймовые винты). Вы также можете сделать это до того, как будете шлифовать/окрашивать.
Но мы все еще ждали, пока наши колеса придут по почте. Есть несколько способов добавить колеса на стол, но они очень просты. Просто вставьте их, немного затяните болт внизу, и все готово! Мне нравится наш новый стол! Мы добавили еще два стула-призрака (подаренные нам Элси) к уже имеющимся четырем. Я думаю, стулья-призраки идеально подходят для нашей столовой. Это не дает пространству выглядеть чрезмерно загроможденным, так как мы пытаемся разместить 6 человек и стулья в относительно небольшом пространстве.
Мы также перенесли наш старинный ковер из коровьей шкуры из гостиной в столовую. Наша столовая является одним из самых посещаемых мест в нашем доме, и мне нравится, как наш коврик из коровьей шкуры выдерживает всю собачью шерсть (у нас три собаки, слишком много?) и пешеходное движение до сих пор.
Несмотря на то, что они винтажные (не знаю, сколько им лет на самом деле), они удивительно долговечны и легко чистятся. Не могу дождаться нашего следующего ужина. Теперь мы можем пригласить дополнительную пару! Спасибо, что позволили нам поделиться со всеми вами нашим новым обеденным столом. Хо. Эмма + Трей
P.S. Все наши стулья-призраки от Amazon, доска для колышков сделана своими руками, ковер из коровьей шкуры изготовлен в винтажном стиле от Red Velvet, а буквы «везде» — в винтажном стиле от Funtiques.
Кредиты // Авторы: Эмма Чепмен и Трей Джордж, фото: Эмма Чепмен
Как составить стол
Столы
Сделай сам
3 года назад
Иногда вы ходите по мебельному магазину в поисках красивого стола, которым можно обставить свой дом, и удивляетесь огромному количеству этих столов. У большинства из них заканчивается короткий срок годности, и вам приходится еще раз копаться в карманах, чтобы заменить стол.
В других случаях мы тратим много времени на поиск стола, соответствующего нашему вкусу, и вынуждены останавливаться на том, что можем себе позволить, потому что стол, который нам нравится, обычно стоит дорого.
Что ж, хорошая новость заключается в том, что вы можете собрать стол, который хотите, не выходя из собственного дома, всего за несколько недель. Это руководство покажет вам, как построить таблицу.
Если вы хотите узнать больше о мастерстве деревообработки, ознакомьтесь с нашей БЕСПЛАТНОЙ электронной книгой «50 планов деревообработки»
Инструменты
Прежде всего, вам нужны инструменты, если вы хотите построить хотя бы простой стол.
Вот некоторые из необходимых инструментов:
1. Пила для вырезания необходимых размеров из деревянных досок, необходимых для стола
2. Шлифовальный станок/наждачная бумага, необходимая для сглаживания поверхностей и краев стола.
3. Шуруповерт для забивания шурупов в древесину
4. Стамеска для вырубки пазов
5. Карманный шаблон для сверления отверстий в соединениях стола
6. Дрель для сверления отверстий в дереве.
7. Рулетка (мы рекомендуем Stanley Powerlock) для измерения размеров стола
Как построить стол — шаги
1. План
Первый шаг к созданию стола — разработка дизайна. Есть разные виды столов. Вы должны не торопиться и искать модель, которую вы хотите. Поищите в Google различные дизайны столов, пока не остановитесь на том, который вам нравится. Если вы все еще не удовлетворены, рассмотрите коллекцию чертежей Ted’s Woodworking.
После того, как вы определились с планом, который вам нравится, следующим шагом будет создание грубого наброска дизайна на листе бумаги, чтобы получить приблизительное представление о том, как будет выглядеть стол. Рисунок также поможет вам понять конструкцию стола. Размер стола не так важен при наброске вашего дизайна.
Пример плана стола. Следующим шагом после создания проекта будет поиск пиломатериалов. При поиске пиломатериалов обратите внимание, что размеры пиломатериалов на полтора сантиметра меньше, поэтому прибавьте полсантиметра к размерам, указанным в магазине. Вы можете выбрать либо твердую древесину, такую как клен, которая обычно дорогая, либо выбрать мягкую древесину, такую как сосна, которая дешевле, но также прочнее и может служить десятилетиями. В конце концов, поиск лучшего дерева для столов зависит только от вас.
Также полезно разбить свой стол на простые компоненты, такие как столешница, фартук и ножки, чтобы иметь представление о том, сколько вам понадобится, чтобы время от времени не ходить в магазин. Вы даже можете избавить себя от необходимости распиливать пиломатериалы, попросив в магазине распилить их для вас, что облегчит вам сборку стола.
2. Изготовьте столешницу
После того, как вы распилили пиломатериалы в магазине или сами распилили их в соответствии с нужными вам размерами, следующим шагом будет изготовление столешницы. Изготовление столешницы должно выполняться на плоской поверхности, чтобы придать столу плоскую поверхность. Найдите ровную поверхность и положите на нее нарезанные куски пиломатериала.
Говоря о столешницах, вы всегда можете подняться на ступеньку выше с помощью стола из эпоксидной смолы, сделанного своими руками! Вот пример того, что у нас есть:
Вы можете расположить их в соответствии с тем, как вы хотите, чтобы столешница выглядела. Сожмите куски пиломатериала вместе и просверлите карманные отверстия с помощью приспособления для карманных отверстий. Вставьте винты в просверленные отверстия, чтобы скрепить части пиломатериалов вместе. Сверление отверстий перед закручиванием шурупов предотвратит растрескивание дерева.
Используйте нижнюю часть готовой столешницы, чтобы отследить положение фартуков. Фартуки крепятся к столешнице и ножкам. Используйте карандаш, чтобы очертить положения фартука под столешницей, затем используйте столярный клей, чтобы соединить фартуки в намеченном месте.
Если вы хотите увидеть больше волшебства деревообработки, ознакомьтесь с нашей БЕСПЛАТНОЙ электронной книгой с 50 планами деревообработки.
стол. И нам, конечно же, нужен крепкий стол. Итак, вырезая ножки стола, выстраивайте ножки рядом друг с другом. Это позволит вам измерить ноги относительно друг друга и сделать необходимые надрезы, чтобы они имели одинаковые размеры.
Когда у вас будут одинаковые размеры ножек, проверьте, где фартуки соединяются друг с другом, так как это образует угловые соединения, где будут располагаться ножки. Расположите ножки и приклейте их, используя столярный клей, чтобы зафиксировать соединения фартука.
Прикрепите ножки к шарнирам фартука, просверлив два отверстия через фартук в ножке стола, по отверстию с каждой стороны ножка крепится к фартуку. В каждой ножке будет по два отверстия. Вверните винты через отверстия, чтобы прикрепить ножку к фартуку.
Вы также можете использовать перекладины, чтобы соединить ножки друг с другом, чтобы сделать стол более устойчивым. Измерьте длину между ножками и вырежьте деревянную доску в соответствии с размерами. Вставьте поперечные балки и просверлите винты, чтобы прикрепить их к ножкам.
ПРИМЕЧАНИЕ. Внимательно прочитайте инструкции производителя столярного клея о том, как долго ждать, пока клей высохнет. Не переворачивайте стол, пока клей не высохнет. Убедившись, что клей для дерева полностью высох, переверните стол и убедитесь, что он устойчив и не шатается. Вы можете отвинтить винты, чтобы изменить положение ножек, если стол шатается.
4. Сглаживание и окрашивание
Здесь вы придадите столу ощущение гладкости. Тем не менее, шлифовка и окрашивание стола не являются обязательными, если вам нравится отделка вашего стола. Но если вы хотите сгладить его, вы можете использовать наждачную бумагу, чтобы сгладить грубые участки, или ленточный шлифовальный станок, который даже упростит вашу работу.
При использовании ленточной шлифовальной машины обязательно проведите ею по поверхности один раз, чтобы не оставить на столе неизгладимых следов. Смойте пыль со стола влажной тряпкой и подождите, пока стол высохнет, прежде чем окрашивать его. Затем вы можете приступить к окрашиванию стола, используя слой по вашему выбору.
По нашему мнению, если вам нравится дизайн, упомянутый выше, вы также можете придумать что-нибудь другое, например обеденный стол в фермерском доме своими руками (пример ниже) или фоторамку в деревенском стиле. Кроме того, кофейный столик своими руками, сделанный из не выровненных досок, может добавить приятный штрих!
Вы даже можете смешивать различные покрытия, чтобы получить уникальный цвет, которым можно окрасить стол, сделанный своими руками. Не забудьте нанести защитное покрытие, когда слой высохнет. Полиуретан обеспечивает хорошую защитную отделку покрытия.
Вот как можно сделать стол!
Если вы хотите узнать больше о волшебстве деревообработки, ознакомьтесь с нашей электронной книгой БЕСПЛАТНО 50 планов деревообработки 🙂
Сборка обеденного стола своими руками
стол. Все, что вам понадобится, это лист фанеры, несколько ножек стола, циркулярная пила, дрель и шлифовальный станок.
Это довольно простой самодельный проект по обработке дерева, но Крис Саломоне подробно описывает его, чтобы у вас были наилучшие шансы на хороший результат.
Он также расскажет о нескольких параметрах, таких как детали краев, общий размер и многое другое. Он также предоставил бесплатную версию этого плана, которую вы можете скачать здесь.
Вы можете найти больше замечательных проектов и техник Криса Саломоне на его сайте.
Рекомендуемые инструменты:
Основной комплект адаптивной системы резки Kreg Настольная пила Rockler для поперечной резки Прецизионный угловой калибр Rockler Зажимная линейка Bora 50″ NGX Kreg 720PRO Приспособление для карманных отверстий Kreg Straight Edge Guide XL Chris Salomone: Привет и добро пожаловать в серию видеороликов о сборке этого стола, который вы видите позади меня в перевернутом виде.
Теперь это видео будет немного отличаться от обычного, потому что оно будет структурировано больше, как наши планы, только для части, которая немного проще или, я думаю, больше сделана своими руками, чем наши обычные планы. Не вдаваясь в подробности, давайте поговорим об этом произведении. Этот будет называться обеденным столом общего назначения, и причина, по которой я назвал это, заключается в том, что он основан на этих ножках.
На самом деле это не ноги, это всего лишь прототипы, но в любом случае они основаны на этих ногах, над созданием которых я работал с компанией Semi Exact. Полуточный общий конкретный и оксюморон, вот и название. В конце видео я расскажу об этом подробнее, но пока не хочу увязнуть. Хорошо, прежде чем мы углубимся в это, я хочу упомянуть несколько вещей. Главным образом в дополнение к этому видео, на нашем веб-сайте есть загружаемый PDF-файл, который вы можете получить с некоторыми письменными инструкциями и более объемными чертежами, которые помогут вам в сборке.
Иногда вы можете заметить, что на этих чертежах размеры, о которых мы говорим в видео, могут не отражать то, что изображено на чертеже. Помимо этого, вероятно, будут случаи, когда ваши размеры будут отличаться как от видео, так и от рисунка. Это нормально, это действительно реальность построения вещей, есть вариации. Тем не менее, главный вывод заключается в том, чтобы не просто слепо отклоняться от цифр, которые мы даем, а вместо этого ссылаться на свой собственный проект, чтобы убедиться, что вы получите наилучший возможный результат. По мере продвижения мы постараемся указать на эти моменты.
Кроме того, по мере того, как мы прорабатываем сборку, я обычно делаю все максимально упрощенно, а затем представляю варианты или альтернативы. Независимо от того, что вы решите делать, убедитесь, что вы чувствуете себя комфортно со своими инструментами и понимаете, как они работают. Если вы когда-нибудь почувствуете дискомфорт от определенной стрижки, не делайте этого, найдите альтернативу.
Обычно я бы сказал, если вам неудобно, свяжитесь со мной, но это для наших планов, которые мы продаем десятками, и это для видео на YouTube, которое, надеюсь, будет просмотрено тысячи раз, даже десятки тысяч.
Думаю, не связывайтесь со мной, я не успеваю за этим, и вместо этого я скажу это в Google. Ладно, приступим к сборке. Для версии стола, которую я собираюсь построить в этом видео из дерева, все, что вам понадобится, это один лист фанеры толщиной 4 на 8 на 3/4 дюйма. Подойдет любой вид, но я собираюсь использовать балтийскую березу. Это даст нам готовый стол длиной около 90 дюймов, шириной 38-1/2 дюйма и высотой около 29-1/2 дюйма. Кстати, в наших реальных планах мы даем размеры как в имперских, так и в метрических единицах, но для целей этого видео я просто буду придерживаться строго имперских.
Извините, наверное, остальной мир. В любом случае, в дополнение к этому, очевидно, вам понадобится что-то для ног, и мы используем ноги, над дизайном которых я работал с Semi Exact, но вы, безусловно, можете сделать свои собственные или использовать ножки-шпильки.
Просто знайте, что размеры могут отличаться. Тогда, с точки зрения инструментов, абсолютный минимум, который вам понадобится, это циркулярная пила, дрель и шлифовальный станок. В видео я также собираюсь использовать фрезер, несколько зажимов и некоторые другие специальные инструменты, чтобы продемонстрировать несколько более быстрых способов, но все это необязательно.
Ладно, думаю, иди забери свои материалы и встретимся в следующей главе. В этой главе мы начнем разбивать нашу фанеру на то, что станет готовой крышкой. Давайте начнем с обсуждения того, как собирается вершина, а затем мы поговорим о том, как лучше всего выполнить этот порядок операций для получения наилучших результатов. Я полагаю, что если бы вы хотели построить этот стол самым простым способом, вы могли бы просто взять два куска фанеры, склеить и/или привинтить их вместе, прикрепить ножки и на этом закончить.
Мы хотим сделать это, используя только один лист фанеры. Если мы посмотрим на верхнюю часть снизу, вы увидите, что мы собираемся начать с одной большой верхней части.
Затем у нас будет четыре части по периметру, которые придадут верхней части более толстый вид. Затем у нас будут эти две опорные детали, я буду называть их частями живота позже в плане, которые будут там, чтобы помочь предотвратить провисание стола. Затем, наконец, каждая ножка получит небольшой опорный блок, который сделает стол правильно закрытым.
Теперь, поскольку мы все, вероятно, используем разную фанеру, и все мы собираемся сделать это немного по-разному, обратите внимание, что ваша деталь может немного провиснуть в центре. Мой делает это немного, но, честно говоря, он довольно крепкий. Честно говоря, я думаю, что это всего лишь один из недостатков попытки растянуть один кусок фанеры так далеко, как вы можете его вынести. Если вас это вообще беспокоит, я бы посоветовал либо использовать больше дерева, чтобы укрепить вещи, либо просто сделать стол немного меньше. Либо один из них, либо их комбинация поможет вам в этом.
Опять же, я сделал свой стол настолько большим, насколько это возможно, и он довольно прочный.
В любом случае, на этом чертеже вы можете увидеть наши куски фанеры с вложенными в нее деталями, а также вид собранной столешницы снизу. Я собираюсь быстро раскрасить все, чтобы вы могли получить приблизительное представление о том, откуда будет взята каждая часть. Что касается порядка операций, вам следует начать с поперечного разрезания этого раздела, чтобы у нас остался кусок размером 90 на 48 дюймов.
Затем мы собираемся вырвать три полоски шириной 2 дюйма, затем одну полоску шириной 3 дюйма, и то, что у нас останется, будет нашим верхом. Теперь давайте настроимся, бросим на стол кусок фанеры и начнем резать. Первый разрез, который вы хотите сделать, это удалить заводскую кромку с одного конца вашей панели, и для этого вам понадобится что-то с прямым краем. Теперь я использую одну из этих направляющих с прямым краем, в которой говорилось, что кусок фанеры с парой зажимов будет работать так же хорошо.
В любом случае, я собираюсь настроить его так, чтобы я знал, что он перпендикулярен длинному краю моей фанеры, и удалить заводской край или столько, сколько мне нужно, чтобы мой кусок выглядел чистым по периметру.
То, где вы разместите линейку, будет связано с вашей циркулярной пилой. Для меня лезвие примерно в 3-1 / 2 дюймах от края базовой пластины. После того, как я сделаю этот первый разрез, я собираюсь измерить расстояние от моей направляющей края, которую я установил, до того места, где произошел фактический разрез.
Затем я буду использовать это расстояние для любых расчетов, и оно будет более точным, чем попытка измерить расстояние от лезвия до опорной плиты. Тем не менее, они должны быть довольно близки, поэтому разница будет незначительной, и я собираюсь использовать 3-1/2 в будущем. Затем я собираюсь измерить и отметить 90 дюймов от края, который мы только что обрезали, и сделать отметки на каждом краю моей фанеры. Здесь я хочу начать второй разрез. Это будет определять окончательную длину столешницы. Если вы хотите что-то другое, отрегулируйте соответственно.
В любом случае, помните, что нам нужно поместить направляющую на 3-1/2 дюйма выше. Я собираюсь сделать отметки с каждой стороны, а затем прижать направляющую линейки к заготовке, и если вы хотите убедиться, что вы все сделали правильно, вы можете измерить ее там, где находится ваш зажим.
Что для меня было бы 90 минус 3-1/2 или 86-1/2 дюйма. Как только вы почувствуете себя уверенно, сделайте этот разрез. Хорошо, мы можем пока отложить обрезки в сторону, и мы вернемся к этому позже, чтобы прикрепить их к нашим ногам. Далее с нашим большим куском оставшейся фанеры нам нужно удалить заводские края на длинных концах.
Здесь я измеряю и отмечаю чуть более 3-1/2 дюймов с каждого конца, затем прикрепляю длинную линейку к этим отметкам и делаю разрез. Кстати, рекомендую не уподобляться мне в этих шортах и использовать средства защиты органов дыхания. Хорошо, следующее, что мы хотим сделать, это разорвать три длинных полоски шириной 2 дюйма и одну длинную полоску шириной 3 дюйма. Мы собираемся начать с 2 дюймов. Для этого мне нужно установить направляющую края на 5-1/2 дюйма, потому что 2 + 3-1/2 = 5-1/2.
Более быстрый способ сделать это вместо того, чтобы каждый раз измерять его, состоит в том, чтобы установить комбинированный квадрат на 5-1/2 дюйма и использовать его для разметки.
Здесь я отмечаю это, а затем делаю разрез, а затем я собираюсь повторить этот процесс еще два раза, чтобы сделать еще две полоски шириной 90 дюймов на 2 дюйма. Затем я сделаю это еще раз, чтобы вместо этого сделать полосу размером 90 на 3 дюйма [тишина]. Как только вы закончите это делать, у вас должно получиться три 2-дюймовых полоски на столе, одна 3-дюймовая полоса и этот кусок размером примерно 48 на 5-1/2 дюйма.
Здесь я измеряю то, что у меня осталось для топа, и похоже, что он будет 90 дюймов в длину и около 38-1/2 дюймов в ширину. В этом разделе мы собираемся вырезать и прикрепить наши четыре части по периметру, чтобы создать иллюзию толщины стола в полтора дюйма, а не в три четверти дюйма. Продолжая с того места, где мы остановились, первым шагом будет выбор лицевой стороны вершины, которую вы хотите использовать. потом перевернуть все вверх дном. Затем я собираюсь использовать клей и зажимы, чтобы прикрепить наши две длинные детали к нижней стороне.
Это уже идеальная длина из-за порядка операций, который мы использовали для достижения этой точки.
Если у вас нет тонны зажимов, вы также можете использовать клей и гвоздевой пистолет или шурупы. Единственное, о чем я вас предупрежу, это пока не кладите их слишком близко к краю, так как вы можете случайно обнажить их, когда через несколько минут мы будем резать наш скос. Прикрепив два длинных куска, я возьму нашу третью и последнюю полосу шириной два дюйма и разрежу ее примерно пополам. На данный момент они будут около 45 дюймов в длину.
Затем я зажму их между длинными кусками и отмечу, где именно нам нужно обрезать, чтобы получить нужную длину. Для этого разреза вы можете сделать это любым количеством способов. Вы можете использовать циркулярную пилу со скоростным угольником, как мы делали для начального пропила. Можно использовать торцовочную пилу, если она у вас есть. Если у вас есть настольная пила, вы можете использовать самодельные салазки для поперечной резки или что-то вроде этих салазок Rockler. Вы также можете использовать угловой упор на настольной пиле или что-то вроде этой станции поперечной резки Kreg.
Дело в том, что вы можете использовать любое количество инструментов, чтобы выполнить работу. Я скину ссылки на инструменты, которые я здесь показывал. Независимо от того, как вы туда доберетесь, после того, как вы это сделаете, приклейте их к каждому концу и дайте им высохнуть.
Я уверен, что есть имя получше, чем носилки для поддержки живота, но я называю их так, как угодно. Я думаю, причина, по которой я их так называю, в том, что они похожи на маленький животик на нижней стороне стола или, может быть, на подрамник для поддержки крыльев. Я не знаю. В любом случае, на данный момент у нас остались только эти два куска. В этой главе мы собираемся превратить эти куски в опоры для живота. Это, вероятно, самая сложная форма, которую содержит этот стол, кроме, как я полагаю, ножек, но вы их не делаете.
Если вы предпочитаете простоту, вы можете просто оставить их прямоугольниками. Я лично не думаю, что это выглядит так красиво, но, честно говоря, это не имеет большого значения, поскольку вы не можете увидеть эти вещи с высоты стоя и / или когда стол окружен стульями.
Это не имеет большого значения. В любом случае, первое, что мы собираемся сделать, это разрезать этот кусок пополам, а затем отмерить 42 дюйма и отрезать каждый кусок до этой конечной длины. Теперь, если вы действительно хотите сделать форму крыла живота, вам нужно будет отметить линию в центре, а затем отметить линию на полтора дюйма вниз от вершины на обоих концах, а затем соединить точки.
Затем я также отметил угол в 45 градусов на каждом конце. Опять же, вы можете сделать любую форму, которая вам нравится, потому что эти углы на самом деле просто для красоты. [молчание] Что бы вы ни делали, как только вы наметите свою форму, вероятно, самым простым или наиболее доступным подходом, я думаю, будет лобзик. Вы просто обрежете линию, а затем отшлифуете ее, чтобы все почистить. Однако, если у вас есть гусеничная пила, это гораздо более быстрый и точный способ сделать такие разрезы. Я собираюсь использовать свой ACS, чтобы быстро сделать эти фигуры.
Давайте отложим их и вернемся к ним чуть позже.
Я начал с того, что разделил этот кусок на четыре части. Для начала мои кусочки были около 5 дюймов в ширину и 11,5 дюймов в длину. Тем не менее, я закончил тем, что хотел более тонкие части. После этого я разорвал их на четыре дюйма в ширину. Какого бы размера они ни были с этими деталями в руках, начните с того, что сделайте отметку по центру детали вдоль, а затем перенесите эту линию на концы частей как на передней, так и на задней части каждой части. Затем я собираюсь выровнять передний край ноги до конца фанеры так, чтобы центральная линия проходила по центру ноги.
Тогда я пока прикреплю их двумя полудюймовыми винтами. Они временные и будут заменены позже. Как вы можете видеть по открывающейся двери и моей другой обуви и моей другой одежде, сейчас следующий день. Я собираюсь начать день с того, что возьму квадрат скорости и отмечу угол в 45 градусов от угла к центру, и мы собираемся сделать это на каждом углу стола. Затем я собираюсь удлинить эту линию, просто используя что-нибудь с прямым краем.
Далее, я возьму одну из своих ног и повозлюсь с размещением, чтобы выяснить, где именно я хочу, чтобы эта штука в конечном счете жила. Для меня это оказалось примерно на 20 дюймов вдоль каждой из моих 45-градусных отметок, которые я сделал. Затем, чтобы выяснить, где разместить наши части живота, мы начнем с разметки центральной линии на нижней стороне каждой из длинных частей. Затем я собираюсь отметить центральную линию на каждой из моих частей живота. Затем, если я приложу эти метки друг к другу, я смогу отметить общую длину частей живота на нижней стороне стола.
Затем я возьму комбинированный квадрат и установлю его так, чтобы сделать отметку примерно в 10 дюймах от внутреннего края периметра, а затем отметить линию именно там, где я хочу разместить живот. . Я также перенесу эту центральную линию к центру моей столешницы, чтобы я мог выровнять ее с центральной линией моей части живота, чтобы убедиться, что они расположены прямо в центре стола. Не то, чтобы это действительно имело такое большое значение, но я люблю, когда все сосредоточено.
В любом случае, после того, как все было размечено, я собираюсь взять приспособление для карманных отверстий и просверлить места для пяти винтов по длине каждой детали.
Если у вас нет приспособления для карманных отверстий, вы можете использовать обычные винты с потайной головкой или просто клей, или, честно говоря, вы можете его купить. Они не такие дорогие и очень удобные. Я уверен, что вы будете использовать его для чего-то еще позже. Теперь давайте отложим части ног и живота, поработаем над деталями, а затем мы получим их снова, когда придет время все прикреплять. Большая часть того, что мы делаем в этой главе, является необязательным. Опять же, есть несколько способов сделать это. Я начну с того, что сломаю все острые края, которые я не собираюсь разводить.
Для меня это внутренняя кромка нижней стороны. Затем я собираюсь отшлифовать внешние края, и для этого я собираюсь увеличить зернистость до 180. Я также собираюсь удостовериться, что слегка скруглил все четыре угла.
Если вы хотите остановиться здесь, а затем просто сломать верхний и нижний края, как мы сделали на внутренней губе, вы можете это сделать. Я хотел сделать 45-градусный выступ на нижнем крае и закругление на четверть дюйма на верхнем крае. Мы начнем с того, что сверло-шампер пройдет по столу, сделав несколько проходов, чтобы достичь желаемой глубины.
Для меня это примерно пять восьмых дюйма. Теперь, если у вас нет фрезера и/или вы чувствуете себя уверенно, вы можете наклонить лезвие циркулярной пилы и использовать поверочную линейку, чтобы срезать таким образом скос. В любом случае, опять здесь, это следующее утро. Я снова отшлифовал свою фаску, просто удалив небольшие следы ожогов и убедившись, что она приятна на ощупь. Затем я мог бы перевернуть весь стол так, чтобы он был правильной стороной вверх, а затем использовать закругление вдоль верхних краев.
Наконец, независимо от того, что вы делаете с краями, мы собираемся отшлифовать всю верхнюю часть наждачной бумагой с зернистостью 180, а затем с зернистостью 220.
После этого нам нужно будет перевернуть эту штуку обратно, чтобы прикрепить ножки. Я собираюсь использовать движущееся одеяло и просто быть особенно осторожным. Если у вас его нет, вы можете просто подождать до самого конца, чтобы отшлифовать верхнюю часть. Мы уже сделали большую часть работы, когда дело доходит до прикрепления частей живота. На самом деле, на этом этапе нам просто нужно расположить их по нашим меткам, а затем прикрепить каждый пятью винтами.
Ноги похожи. Единственный трюк здесь заключается в том, что мы собираемся выровнять отметки, которые мы сделали в центре концов наших фанерных пространств, с отметками под углом 45 градусов, которые мы сделали от наших углов, чтобы убедиться, что ножки находятся в правильном положении. угол. Чтобы прикрепить их, мы будем использовать винты длиной один с четвертью дюйма через прорези, через промежутки и в нижнюю часть фанеры. В этом видео я вкручиваю только два винта в каждую ногу. Это потому, что это прототипы ножек, и я знаю, что заменю их настоящими, как только получу.
Вот на этом рисунке показано, как я могу их прикрепить. Отсюда вы можете просто использовать любую отделку, которая вам нравится, используя лучшую, и все готово. Что ж, позвольте мне первым поздравить вас с отлично выполненной работой. У вас есть готовый обеденный стол. У меня еще нет готового обеденного стола, и это потому, что, как я уже говорил ранее, я все еще жду, чтобы получить непрототипную версию ножек. Я надеюсь, что здесь я смогу добавить некоторые фотографии реальных вещей, но независимо от того, произойдет это или нет, вы сможете увидеть их и получить больше информации непосредственно от Semi Exact.
Ссылки в описании. Несколько последних вещей. В начале видео я упомянул, что у нас есть PDF-файл, который вы можете скачать, в котором будет больше информации, чертежи с размерами и руководства. Ссылка на это есть в описании. Кроме того, если вам нравится такой контент и вы хотите иметь планы на значительно более длинную и сложную сборку, ознакомьтесь с ними на сайте.
Я также упомянул в начале видео, что работал с Semi Exact над созданием этих ног.
Откровенно говоря, я не продаю эти ноги и не получаю деньги напрямую от продажи этих ног. Semi Exact продает их. Тем не менее, я вложил деньги в компанию несколько месяцев назад, потому что мне очень нравится их философия и направление, в котором они движутся, и я хотел быть частью этого. Я также был взволнован идеей разработки вещей, которые я просто никогда не мог сделать самостоятельно, таких как металлические ноги. Я думаю, если вкратце, то я не хочу, чтобы люди покупали эти ноги, потому что они хотят поддержать меня.
Умный настольный лазерный резак и гравер
Познакомьтесь с машинами xTool
Простой в использовании, умный, мощный и быстрый станок для резки для дома, бизнеса и школы.
Подробнее
Улучшенная работа с принадлежностями
Чистота и безопасность.
Аксессуары xTool помогут вам добиться большего.
[Предзаказ] Инфракрасный лазерный модуль xTool 1064 нм
Набор рабочих панелей xTool Honeycomb для D1/D1 Pro
Корпус xTool
Комплект xTool D1/D1 Pro Air Assist
Подробнее
Создавайте с помощью xTool Materials
Создавайте удивительные проекты из дерева, акрила, кожи и других материалов.
Подробнее
Подробнее
Гениальные идеи от реальных владельцев xTool
Все эти изображения были собраны из группы xTool на Facebook. Присоединяйтесь к нашей группе, чтобы услышать реальные отзывы о продуктах xTool,
, получить творческое вдохновение и поделиться своими идеями!Узнайте, что люди говорят о xTool
Мы гордимся нашим качеством и сервисом, вдохновленным вашей историей! Присоединяйтесь к нам!
Пусть клиенты говорят за нас
из 6469 отзывовОчень красиво
Забыл добавить фото своего корпуса.
Я построил.
kevin erickson
27.09.2022
xTool D1 Pro 20 Вт: высокоточный диодный станок для лазерной гравировки и резки своими руками
XTool D1 Pro
Love it. Это мой первый лазер. Делает все, что я хочу. Стекло еще не пробовал резать, но может быть. Сошлись легко. Сделайте себе одолжение и сделайте или купите корпус с каким-нибудь вытяжным вентилятором.
Мне слишком весело с этой штукой.Richard Chiddy
20.09.2022
xTool D1 Pro 20W: высокоточный диодный станок для лазерной гравировки и резки своими руками
Очень доволен!
Присматривался к новой марке дерева, которой я занимаюсь деревообработкой, и они хотели 300 долларов за хороший электрический с логотипом моей компании. Ну решил, что пришло время получить лазерный гравер вместо этого немного больше, и я очень счастлив. Мне потребовалось всего около 30 минут, чтобы собрать его и записать первый проект. Все еще изучаю настройки с разными древесинами, но пусть он записывает мой логотип в мои проекты и многое другое.
Прошло около месяца, и я даже создал пару вывесок, и у меня есть идеи для многих других вещей, которые хорошо сочетаются с моими проектами по деревообработке. Уже подумываю о приобретении комплекта удлинителей и пневматического ассистента!
Robert Peebles
16.09.2022
xTool D1 Pro 10W: высокоточный диодный станок для лазерной гравировки и резки своими руками
Моя новейшая ИГРУШКА такая веселая!
Я называю все свои машины — швейную машину, вышивальную машину, резак Cameo и т.д. ИГРУШКАМИ! Я играл с этим — пробовал немного этого и немного этого, но теперь чувствую себя комфортно с этим. Он отлично справляется с теми мелочами, которые я пробовал, теперь, когда я начинаю понимать, как тестировать материалы и узнавать, для чего можно изменить настройки. Сам по себе инструмент — отличная штука, и я с нетерпением жду, когда программное обеспечение догонит его. Тем временем я в значительной степени использую свое программное обеспечение Silhouette для подготовки вещей, а затем передаю их в XCS для обработки.
Как новичок в лазерной обработке, я действительно могу порекомендовать это как отличное место для начала обучения. (Я очень доволен встроенными предохранителями для предотвращения несчастных случаев, такими как крышка и автоматическое отключение, если крышка открыта!)
Marilyn Gardiner
15.09.2022
xTool M1: идеальная машина для лазерной и лезвийной резки для изготовления подарков
Необходимая вещь
воздушная помощь. Вспомогательный воздух делает резку лазером более эффективной и чистой, но имеет тенденцию продувать разрез и создавать воздушную подушку под проектом, которая может позволить ему двигаться (если не использовать эту панель). Магниты, которые поставляются с панелью, отлично подходят для выравнивания повторяющихся проектов и сохранения стабильности материала.
Ray Lewis
15.09.2022
Набор рабочих панелей xTool Honeycomb для D1 Pro/D1
Хорошо, за исключением больших ручек для кружек не вращается полностью, поэтому у него есть некоторые ограничения.
Убедитесь, что ручки кружки не слишком велики. В остальном работает отлично.
L G
14.09.2022
xTool RA2 Pro
Нерешительный, но счастливый
Я определенно колебался, стоит ли тратить деньги на машину, о которой я ничего не знал, и подойдет ли она мне. Я рискнул и приобрел D1pro 20W, и теперь я очень счастлив, что сделал это. Это была кривая обучения, но я смог сделать несколько действительно хороших вещей. Начинаю чувствовать себя уверенно в том, что делаю, и надеюсь, что скоро начну продавать.
Steven Colletti
13.09.2022
xTool D1 Pro 20 Вт / 10 Вт: высокоточный диодный станок для лазерной гравировки и резки своими руками
Ухмылка от уха до уха!
Много лет откладывал покупку лазера. У меня есть плазменный стол с ЧПУ, фрезерный станок с ЧПУ и другие станки, но по какой-то причине я решил ДОЖДАТЬСЯ, чтобы получить лазер.
Должен сказать вам, что с этой машиной есть ОДНА ОГРОМНАЯ ПРОБЛЕМА. ЭТО СЛИШКОМ МНОГО ВЕСЕЛЫХ!!!
Я добавил удлиненную раму, воздушную помощь, сотовые решетки, поворотный аксессуар и удлинители ножек.
Я купил трехступенчатый HEPA-фильтр на Amazon, чтобы контролировать дым и испарения при резке в помещении. Я добавил цепи к машине, которую купил на Amazon, для управления кабелями и воздушным шлангом.
Я уже планирую купить ДРУГОЙ станок X-TOOL D1 PRO в ближайшее время. Я установлю его на алюминиевую раму размером 50 x 100 дюймов, сделанную из профилей 8020, и он сможет записать изображение на целый лист фанеры 4×8! Я также приобрел красный инфракрасный лазерный модуль с длиной волны 1064 нм, так что мне не терпится поэкспериментировать с ним!
X-Tool — это очень хорошая ЦЕННОСТЬ, и он хорошо сделан. Я запускаю его с помощью программного обеспечения LIGHTBURN, которое продается другой компанией.
Джозеф Джонс
10.09.2022
xTool RA2 Pro для D1 Pro/D1 + переходники (8 упаковок)
Превосходит ожидания
Я купил D1 10W с насадкой Ra2. Это просто потрясающе. Простая настройка из коробки для выполнения моего первого проекта за час без опыта.
Ra2 точно такой же. Потребовалась секунда, чтобы выяснить ориентацию, но как только она была установлена, было легко сделать мой первый тумблер и даже бейсбольный мяч.
Коди основной
05.09.2022
для RA2 Pro номер отслеживания
Love my D1
Я получил свой D1 чуть больше месяца назад, и он мне очень нравится… Я не переставал творить с тех пор 😃
Паула Генри
31.08.2022
Лазерная линза для xTool D1
Очиститель дыма M1
Нам нравится наше новое дополнение
Энтони Уитли
29.08.2022
Очиститель дыма xTool
Пока все хорошо
Его было легко настроить и использовать. Он отлично справляется с удалением дыма и запаха из окна, и мне нравится, как все закрыто, что делает его безопасным для любопытных детей. Меня беспокоит только то, что они не будут продолжать улучшать программное обеспечение и не начнут взимать плату за такие услуги, как Glowforge.
Popeye Welty
29.
08.2022
xTool M1: идеальная машина для лазерной и лезвийной резки для изготовления подарков
Awesome
xtool машина Я сказал, что мне придется получить один. Я заказал с 26 июля, получил бы через неделю, но в пути я напутал с информацией, но общение было хорошим. Я начал сегодня, и все прошло хорошо, слава богу. мне уже нравится не жалею жду с нетерпением
fenton campbell
29.08.2022
xTool D1 Pro: высокоточный диодный станок для лазерной гравировки и резки своими руками
Дайте волю своему творчеству!
Мне понравился оригинальный xTool D1, но расширения действительно вывели творчество на новый уровень. Сначала я не решался устанавливать расширения, потому что так привык к исходному рабочему пространству. Однако, как только я его собрал, я сразу увидел потенциал того, что можно сделать. Я с нетерпением жду возможности сделать несколько действительно крутых, больших проектов.
Онлайн-инструкции по сборке были точны. Было бы неплохо немного больше ясности по обновлению прошивки, но я разобрался.
С нетерпением жду возможности сделать что-нибудь грандиозное!
Raymond J.
29.08.2022
xTool D1 Pro/D1 Extension Kit
У нас есть победитель!
У меня есть Xtool D1 с лазерами мощностью 10 Вт и 20 Вт. Также воздушная помощь и 10w M1
И многое другое. Я жду комплект расширения для D1. Так что я хорошо знаком с линейкой Xtool. Машины отличного качества, хорошо собраны, программное обеспечение простое в освоении.
Прежде чем я начал использовать инструмент X, я посмотрел на Glowforge и несколько других машин. Если учесть цену и качество, инструмент X превосходит их всех! Несколько раз у меня возникали вопросы, на которые компания отвечала на следующий день. Если учесть цену, программное обеспечение, простоту использования и качество, Xtool выигрывает!Росс Вудард
12.07.2022
xTool M1: лучший лазерно-лезвийный станок для изготовления подарков
Наша история
Как часть Makeblock, xTool придерживается той же миссии, что и Makeblock: создавать творчество легче для каждого человека.
Вот почему мы предлагаем различные лазерные станки, чтобы помочь людям воплотить свои творческие идеи в жизнь.
Просмотреть еще
Журнальный столик из фанеры «елочка», сделанный своими руками
Мой журнальный столик для гостиной готов! Да, это может быть моя любимая вещь, которую я когда-либо строил. Если не мой фаворит, то определенно в моей пятерке лучших. Вот как это получилось…
Разве это не красиво!? И это фанера! Не просто фанера, а кромка фанеры. То есть часть, которую большинство людей обычно пытаются скрыть. Но вместо того, чтобы прикрыть его, я сделал его особенностью этого журнального столика. Вот видео процесса…
Вы должны дать мне немного милости с этим видео. Я ждал до вчерашнего дня, чтобы сделать свое повествование, и, конечно же, я проснулся от простуды.
Я вообще не могла дышать носом, у меня слезились глаза, постоянно чихала и болело горло. Это было похоже на то, как Моника Геллер в Эпизод с сестрой Рэйчел (она же, где Моника была больна) рассказывает видео. Но в итоге все обошлось… д. Хорошо… д. (Это действительно сложное слово!) 😀
И, кстати, если вам когда-нибудь интересно узнать о моих рекомендациях по инструментам и продуктам для мастеров-любителей, вы можете увидеть, что я использую и что рекомендую, на моей витрине Amazon Storefront. Нажмите здесь, чтобы найти это. Когда вы там, вы найдете три разные категории на данный момент (я могу добавить больше в будущем). Так что для этого проекта вы, вероятно, захотите щелкнуть Инструменты и товары для дома, чтобы увидеть специфику. Многие из моих вариантов станут отличным подарком и для мастеров-любителей!
В любом случае, это был очень трудоемкий проект, так как мне пришлось склеить и прибить более 550 кусков фанеры для столешницы (и это для относительно небольшого журнального столика), но ничего особо сложного в этой постройке нет.
Если у вас много терпения, умеренные навыки сборки и уверенность в обращении с электроинструментами, вы вполне можете это сделать! Позвольте мне показать вам, как я это сделал…
Я начал с одного полного листа березовой фанеры. Я попросил Home Depot разрезать его на удобные для меня кусочки (кусочки шириной около 12 дюймов), а затем я принес его домой и нарезал эти кусочки на полоски шириной 1,5 дюйма.
Затем я разрезал эти полоски на 3-дюймовые кусочки.
Так как мне пришлось вырезать очень много деталей (более 550 штук), я прикрепил кусок МДФ к своей торцовочной пиле, чтобы мне не приходилось измерять каждый кусок перед резкой. Этот процесс на самом деле пошел намного быстрее, чем я ожидал.
Когда я разрезала детали, я положила их на рабочий стол в виде елочки.
Это был единственный способ определить, сколько деталей мне понадобится, чтобы сделать стол нужного мне размера. Я пытался вычислить это, но все время приходил к одному и тому же очевидно неверному ответу, что мне нужно четыре ЛИСТА фанеры для верха.
😀 Я знала, что так быть не может. Очевидно, я делал некоторые ошибки в своих расчетах (хорошо, что я никогда не хотел быть инженером), так что этот путь казался мне проще. Как оказалось, мне понадобилось примерно 2/3 листа фанеры.
Когда у меня было достаточно деталей для столешницы, я отшлифовала каждую деталь вручную.
Причина, по которой я это сделал, заключается в том, что, несмотря на то, что у меня на пиле было совершенно новое полотно с мелкими зубьями, оно все еще оставляло эти волосатые древесные волокна повсюду. И они мешали деталям плотно прилегать друг к другу. Я хотел, чтобы сборка была как можно проще, поэтому я решил, что немного дополнительного времени (или двух часов) на шлифовку облегчит задачу в дальнейшем.
Чтобы начать дизайн елочки, я сделал серию L-образных фигур, используя пары деревянных деталей. Я склеил и прибил их вместе, используя 1,5-дюймовые гвозди 18-го калибра. Затем я склеил и прибил эти L-образные детали вместе, пока у меня не получился ряд из них, достаточно длинный для ширины моего стола.
Я хотел, чтобы ширина моего стола в готовом виде составляла около 18 дюймов, а поскольку рисунок «елочкой» оставляет зазубренные края, которые необходимо обрезать, я сделал каждый ряд шириной около 24-26 дюймов. Я просто измерил, когда шел, чтобы убедиться, что у меня достаточно места в середине (минус неровные края) для моего стола.
В последующих рядах я приклеивал и прибивал каждую деталь к краю детали предыдущего ряда, а также к лицевой стороне детали текущего ряда. В видео этой сборки я показываю, что происходит, когда вы не можете прибить детали к концам частей в предыдущем ряду. Спойлер: все развалится. 😀 Что должно было быть очевидно для меня, но как-то ускользнуло от моего внимания при первой попытке построить столешницу.
После того, как я оставил столешницу на ночь, чтобы клей высох, я вынес ее на улицу и обработал ленточной шлифовальной машиной с наждачной бумагой зернистостью 40.
Если бы у меня был рубанок (или доступ к рубанку, который будет работать с чем-то шириной почти 30 дюймов), сейчас самое время им воспользоваться.
Но, к сожалению, мне пришлось прибегнуть к использованию ленточной шлифовальной машины. Он сделал свою работу, и сделал это очень быстро, но это один из моих наименее любимых инструментов.
Но затем я приступил к очень приятной работе по тонкому шлифованию на моей роторной шлифовальной машине.
Так как верхняя часть почти гладкая, я использовал направляющую для гусеничной пилы, чтобы обрезать края. Я так боялся, что допущу здесь ошибку, и вся моя тяжелая работа будет испорчена, но мне удалось идеально обрезать края с помощью направляющей для циркулярной пилы Kreg. Я также очень быстро терял дневной свет, но я был полон решимости сделать это до того, как стемнеет.
На следующий день я перешел к шагу, который, как мне кажется, вывел эту столешницу на новый уровень — фрезеровке краев с помощью фрезы с закруглением радиусом 1/2 дюйма.
За этим последовало много деревянной начинки. Если бы мне пришлось делать это снова, я бы убедился, что у меня под рукой есть шпатлевка по дереву, и я бы нанес ее на всю поверхность и края.
В фанере МНОГО пустот и трещин, и если вам нравится идеально гладкая поверхность, как мне, то шпаклевка по дереву — это то, что вам нужно.
После высыхания я приступил к окончательной шлифовке. Я начал с моей роторной шлифовальной машины и отшлифовал до зернистости 150, а затем закончил шлифованием всего вручную до зернистости 220.
К тому времени, когда все было отшлифовано, эта штука была очень гладкой. И мне просто нравится этот закругленный край и то, как дизайн изящно перетекает через край вот так…
Чтобы закончить верх, я использовал немного прозрачного полиуретана на водной основе (кое-что осталось со студийного пола) и смешал немного универсальной подкраски в белый оксид. Я хотел осветлить и осветлить древесину, а также убрать часть желтого цвета, не скрывая текстуру дерева и рисунок. Это сработало отлично.
Когда все высохло, я снова отшлифовал наждачной бумагой с зернистостью 220, а затем нанес еще один слой прозрачного полимера.
Я хотел, чтобы верхняя часть была звездой этой сборки мебели, поэтому я сделал основание максимально простым.
Он состоит из четырех ножек и восьми частей носилок, вырезанных из пиломатериалов площадью 1 квадратный дюйм. Этот пиломатериал начинался как 1,5-дюймовый квадрат (тот же самый, который я использовал на своем студийном столе), но он казался слишком громоздким для такого маленького стола. Так что я разрезал куски до 1 квадратного дюйма на настольной пиле, и это казалось идеальным.
Эта база не может быть проще. Я просто приклеил и прибил верхние части подрамника прямо к нижней части столешницы, а затем приклеил и прибил ножки к подрамникам.
Я перевернул его правой стороной вверх, приклеил и прибил нижние части подрамника на место.
Я имею в виду, что нет ничего проще. Теперь я хочу подчеркнуть, что если бы я строил это для использования в качестве скамейки, я бы добавил больше опорных элементов и соединил бы все вместе с дополнительными столярными изделиями, такими как винты с потайными головками. Но когда клей на нем высох, он стал очень прочным и достаточным для использования в качестве журнального столика.