Дж. Стронг «Практика современной физической лаборотории». Глава XV ФОРМОВКА И ЛИТЬЁ Процесс формовки и отливки металлов очень мало изменился за всё время своего существования. Изменения затронули только обслуживающие аппараты, но сущность процесса осталась той же, какой была во времена доисторического человека. Процесс отливки металла казался удивительным искусством тем, кто никогда им не занимался, а специалисты ревностно охраняли секреты своего ремесла, чтобы другие не узнали, как оно несложно. Цель этой главы — познакомить читателя с деталями процесса отливки
металлов. Только немногие лаборатории имеют оборудование для работы с расплавленным
металлом, так что экспериментатор часто бывает вынужден пользоваться услугами специальных литеен. Однако в большинстве случаев
экспериментатор имеет возможность изготовить в своей лаборатории модель, по
которой будет сделана отливка. Отливка по восковым моделям. Имеется два метода отливки металлических изделий:
отливка по восковым моделям и отливка в песочных формах. Первый метод
заключается в следующем. Восковую модель покрывают песком и огнеупорной глиной
и затем обжигают, освобождая форму от воска. Получается готовая форма для
заливки металла. Таким методом пользуются при отливке скульптур, золотых зубов,
инкрустаций и во всех других случаях, когда требуется только одна отливка; ибо
очевидно, что по олной модели можно отлить таким способом только одно изделие.
Отсюда название метода «потеряный воск». Преимущество метода отливки по восковым моделям состоит в том, что модель можно сделать сколь угодно сложной, независимо от наличия выемок. Елинственно, о чём следует позаботиться, это об устройстве отверстий для заливки металла и выхода воздуха. При отливке пустотелых скульптур внутренний сердечник обычно поддерживается в форме стержнями из того же металла, из какого должна быть отлита статуя. Материал, идущий на изготовление моделей, состоит из смеси пчелиного
воска и парафина. Его можно получить уже приготовленным или
без труда изготовить самому, так как пропорция воска и парафина не является
строгой. Маленькие модели укрепляют на конце небольшого стержня. Чтобы снять модель,
к стержню прикладывают кусок горячего металла; когда стержень достаточно нагреется, воск начнёт таять и модель
соскользнёт с конца стержня. Если требуется отлить изделие из свинца, гарта, баббита, олова и его
сплавов, припоя или других подобных металлов, то форму можно делать из гипса. Если в центре миски над водой осталась небольшая кучка порошка, то нужно подождать, пока она сделается влажной, и
затем осторожно размешать содержимое
миски, чтобы освободить его от пузырьков воздуха. После этого с помощью
мягкой кисти осторожно покрывают модель приготовленной смесью (рис. Дантисты пользуются усечённым конусом
(наклон 5—10°), причём дном служит меньшее основание. Такой конус гарантирует,
что при заливке металла форма останется внутри сосуда и не будет разбита. Это
станет очевидным из следующего абзаца, где описывается процесс заливки металла
в форму. Когда смесь затвердела, прут, поддерживающий модель, вытаскивают и
вокруг оставшейся дыры (литника) делают воронку для приёма жидкого металла
(рис. Форму помещают на металлический диск, в центре которого имеется
отверстие, соединённое трубкой с небольшим резервуаром. На трубку надет зажим,
запирающий её до тех пор, пока металл не будет расплавлен. К резервуару
присоединён маленький ручкой насос, позволяющий уменьшить давление в резервуаре
до половины или четверти атмосферного. ![]() так, что жёлоб тигля примыкает к литнику. Остаётся взвести пружину, положить металл в тигель и нarpеть его с помощью ручной горелки. Когда металл расплавится, освобождают тормоз, брусок приводит во вращение и центробежная сила заставляет металл войти в форму. Необходимо, чтобы дно
формы было достаточно прочным, в противном случае оно
может не выдержать, и расплавленный металл будет разбрызган по комнате. Модели для приготовления песочных форм. Обычно
отливка всевозможных деталей независимо от их размеров и металла, из
которого они должны быть отлиты, производится в песочных формах.
Отливка в постоянных формах,
хотя и является существенной, применяется лишь тогда, когда высокая стоимость
металлических форм оправдывается большим количеством отливаемых деталей. Прежде чем приступить к
изготовлению модели, следует в
первую очередь составить точный чертёж отливаемой детали (рис. 403) Затем по этому чертежу изготовляют чертёж модели.
Последний может быть выполнен на
тонкой бумаге (рис. 404). Чтобы было удобно работать с
этим чертежом, следует проставить на нём все необходимые размеры.
Для того чтобы
проиллюстрировать отливку в песочных формах, на рисунках показан
процесс изготовления полярной оси телескопа. Конструкция оси
предусматривает заливку баббитом, так как при этом устраняется
необходимость зажимать всю ось в патроне токарного станка для её
высверливания, — операция, выполнимая лишь на очень большом токарном
станке. Проектируя модель, следует прежде всего выбрать плоскость разъёма формы.
Плоскость эта должна быть выбрана так, чтобы обе части модели можно было
вынуть из песочной формы. Для этого плоскость разъёма должна проходить таким
образом, чтобы все точки отливаемого изделия, будучи нормально спроектированы
на неё, оказались внутри сечения или на нём. Если такой плоскости не имеется,
то выбирают ту, которая лучше всего удовлетворяет выдвинутому требованию;
выступающие же части выполняют с помощью формовочных шишек. Модель также должна разниматься вдоль плоскости разъёма, если только эта
плоскость не совпадает с одной из поверхностей
отливаемого предмета. В последнем случае модель делают из одного куска (рис. 405). Так как при вытаскивании из песочной формы предмета с параллельными сторонами
стенки формы из-за трения разрушаются, то необходимо придавать модели некоторую
конусность относительно плоскости разъёма. Для точных работ конусность эта
может быть уменьшена до 1/2°, в большинстве же случаев её делают равной
3°. Для круглых предметов с плоскостью разъёма, проходящей через ось,
конусность совсем не требуется. Если одна из частей модели имеет выступ, не лежащий в плоскости разъёма, тр между ним и плоскостью разъёма вставляют отдельную
болванку, которую можно вынуть, когда первая половина формы готова. Болванка
эта носит название «фальшивой шишки». Объёму, занимаемому фальшивой шишкой в
первой половине формы, соответствует равный объём песка во второй половине.
Фальшивая шишка также должна иметь конусность. Из приведённого ниже описания
процесса изготовления формы станет ясно, чтв фальшивыми шишками следует
пользоваться только в одной половине формы. Этой половиной должна быть часть
формы, изготовляемая по той половине модели, в которой имеются углубления для
штырей, скрепляющих обе половины модели. Если нужно отлить изделие со сквозным отверстием, то в тех местах, где у
отлитого изделия должно быть отверстие, на модели делают выступы. Эти выступы
образуют в песке во время формовки углубления, куда помещаются концы шишки,
чтобы она не всплыла во время заливки расплавленного металла. Конусность
выступов должна соответствовать остальным частям модели. Для шишек следует
изготовить отдельные чертежи, учитывающие наличие упомянутых выступов (рис. Шишку формуют отдельно из песка или другого формовочного материал и
помещают в форму, для того чтобы получить в отлитом изделии отверстие или
внутреннюю полость. Если отверстие не сквозное, то шишка пересекает поверхность
изделия только в одном месте и лежит в песке формы только одним концом. При
этом необходимо, чтобы выступ на модели, образующий в песке углубление для
конца шишки, был достаточно длинным, так как иначе шишка, заделанная одним
концом, будет укреплена непрочно. Если такая конструкция невыполнима, то можно
сделать у шишки выступы, служащие для неё опорами внутри формы. Такие выступы
образуют внутри отлитого изделия пустоты, которые приходится потом заделывать.
Другой способ заключается в том, что шишку поддерживают металлическими подставками.
Подставки эти, имеющие вид булавок с широкой головкой и изогнутым стержнем,
втыкаются формовщиком в песочную форму и в дальнейшем сплавляются с металлом
отливки. Так как почти все металлы при затвердевании получают усадку, то размеры модели следует несколько увеличить, чтобы компенсировать усадку. Величина усадки зависит от того, из какого металла изготовляется отливка; в табл. I приведены значения усадки для различных металлов. Приведённые в таблице цифры показывают, сколько сантиметров нало прибавить к размерам модели на каждый метр. Удобно пользоваться усадочными масштабами с делениями большими, чем деления обыкновенного метра на величину усадки. Если по одной модели предстоит выполнить большое число отливок, то
обычно, пользуясь деревянной моделью как первичной, отливают рабочую модель из
алюминия или другого металла и уже по этой модели изготовляют формы. Иначе обстоит дело при отливке изделий из сплавов, особенно если
температуры плавления металлов, входящих в состав этих сплавов, сильно
отличаются друг от друга. Если охлаждение сплава идёт медленно, то за время
охлаждения в нём успевают вырасти большие кристаллы. Некоторые металлы,
входящие в состав сплавов, могут выкристаллизовываться, придавая хрупкость
толстым отливкам из сплава и рассыпая в них целые гнёзда кристаллов. Лучше
всего, повидимому, отливать из сплавов детали толщиной от 5 до 8 мм, но
и толщина в 3 мм не является предельной. Деревянные модели изготовляют из белой сосны, сахарной сосны или
красного дерева. Дерево, идущее на изготовление моделей, не должно иметь сучков
и должно быть хорошо высушено. Если модель состоит из двух кусков (не считая
фальшивых шишек), то оба эти куска должны быть скреплены между собой так, чтобы формовщик мог разнять и вновь соединить их.
При изготовлении модели лучше всего сначала обработать плоскость разъёма вместе
со скрепляющими шипами. Для скрепления частей разъёмной модели можно пользоваться
деревянными штырями или специальными штифтами с гнёздами (рис. Изготовление моделей принципиально ничем не отличается от обычной практики деревообделочного производства. Для скрепления отдельных частей модели можно пользоваться клеем и всеми известными приёмами соединения деревянных деталей при условии, что полученная модель будет иметь желаемую форму. Внешние поверхности модели должны быть совершенно гладкими. Любая шероховатость или неровность поверхности приведёт к тому, что формовщик при освобождении модели из формы вынужден будет сильно постукивать по модели. В результате форма и, следовательно, отливка будут иметь большие размеры, что проектировалось. Особенно гладкими должны быть те места, где модели придана конусность. Каждая часть разъёмной модели, а также фальшивые шишки снабжаются специальной
пластинкой, которая вделывается впотай со стороны плоскости разъёма (рис. Установлено, что при изготовлении отливок острые углы, внутренние и образованные внешними поверхностями, являются источником всевозможных неприятностей. Острые края формы могут осыпаться, а если отливку
и удаётся изготовить, то действующие в ней внутренние напряжения могут
разрушить её вдоль этих углов. Чтобы
избавиться от подобных неприятностей, принято углы закруглять. Можно
сразу изготовить модель с закругленными углами, но легче сделать закруглённый
переход из воска. Изготовляемые для закругления углов ленты имеют различный размер, так что радиус закругления можно
выбрать по желанию. Точно так же можно приобрести или изготовить подходящего
размера инструмент для вдавливания ленты. После того как углы модели закруглены,
её вновь покрывают шеллаком. Если модель предназначена для изготовления только
одной формы, то закруглённый переход можно сделать из наиболее твёрдых сортов
пластилина или пластицина. Эги материалы хорошо пристают к покрытий шеллаком модели, а нужный профиль им можно
придать пальцами или с помощью деревянного инструмента, после чего их следует
покрыть шеллаком. Если
при отливке изделия шишки не применяются, то всю модель покрывают чистым шеллаком; если же шишки применяются,
то модель покрывают темночёрной смесью шеллака с сажей (смесь эта хорошо
растворяется в спирту), а выступы, соответствующие концам шишки, покрывают
чистым шеллаком или окрашивают в красный цвет. Такая разноцветная окраска
сразу показывает формовщику, где должна лежать шишка (рис. 410). (В СССР выступы («знаки») принято красить чёрной краской; цвет же
модели по называет, для какой отливки модель предназначена: красный — для
чугуна, синий — для стали, жёлтый — для цветных металлов. Если отливка требует применения шишек, то сразу же возникает вопрос об
изготовлении шишечных ящиков. Последние представляют, по существу, деревянные
формы для формовки шишек. Требования относительно конусности и усадки остаются
для них теми же, что и при изготовлении моделей. Цилиндрические шишки формуют в
разъёмных ящиках, состоящих из двух половин. Плоскость разъёма в этом случае не
имеет никакого отношения к плоскости разъёма модели. Соединять обе части шишечного
ящика не требуется, так как обе половины шишки формуются отдельно и склеиваются
после прокаливания. Если обе половины шишки одинаковы, то изготовляют только
одну часть шишечного ящика. Если же шишки цилиндрические, то изготовлять самим
ящик вообще не ‘нужно, так как большинство литеен имеет запас готовых ящиков
или даже шишек. Отметим ещё один важный момент: так как модель намечает в форме только концы шишки и так как шишка может быть несимметрична, то полезно делать концы шишки разными, чтобы формовщик был вынужден поместить шишку внутрь формы только в нужном положении. Весьма интересен применяемый уже много лет способ изготовления шишечного
ящика для цилиндрических шишек. Отливка в песочных формах. Чтобы изготовить форму, формовщик
поступает следующим образом. Прежде всего он разнимает
модель, укладывает на стол плоскостью разъёма вниз ту часть модели, в которой
нет соединительных штырей, и ставит на место фальшивые шишки. Поверх этой части
накладывается деревянная или металлическая рама — нижняя опока. Когда нижняя опока до половины наполнена, песок осторожно утрамбовывают
вокруг модели с помощью деревянного инструмента, имеющего форму двойной
лопатки, один конец которой — плоский, а другой имеет вид усечённого тупого
клина [рис. 414(b)]. После этого добавляют новые порции песка, пока нижняя опока не будет
заполнена до краёв хорошо утрамбованным песком. Затем песок протыкают во многих
местах тонкой проволочкой, чтобы облегчить выход пара и газов, образующихся при
заливке расплавленного металла в форму [рис.
414 (с)]. Потом нижнюю опоку целиком переворачивают,
кладут на стол плоскостью разъёма кверху и вынимают фальшивые шишки, как
показано на рис. Вторую половину модели накладывают на
первую так, чтобы соединительные штыри .вошли в гнёзда. Чтобы обе половины формы не слиплись, плоскость разъёма формы посыпают сухим песком
[рис. 414(f)]. Затем верхнюю опоку ставят на нижнюю, наполняют её песком и утрамбовывают так же, как
это делали с нижней опокой [рис. 414(g)]. Так же, как и в нижней опоке,
песок протыкают тонкой проволокой, как
показано на рис. 414(h). В том месте, где под слоем находящегося в опоке
песка нет модели, проделывают лить ик, проходящий чуть дальше плоскости
разъёма. Проделывают его с помощью куска тонкостенной латунной трубки,
осторожно втыкая её в песок и удаляя затем вместе со штабиком песка [рис. 414(i)]. Литник диаметром около 25 мм достаточен
для отливок весом от 5 до 50 кг. Удобно проделывать литник не сразу, а вытаскивая за раз слой песка толщиной около 25 мм. Нельзя устраивать литник упирающимся непосредственно в модель, так как в этом случае форма могла бы быть повреждена заливаемым металлом. Вокруг отверстия литника делают углубление для заливки расплавленного металла [рис. 414 (j) и (k)]. Верхнюю опоку осторожно снимают с нижней и кладут рядом, плоскостью разъёма кверху. В отверстие пластинки, вделанной в плоскость разъёма нижней половины модели, вставляют стержень и слегка постукивают по нему со всех сторон, чтобы освободить модель от прилипшего песка [рис. 414(l)]. Затем во второе отверстие пластинки ввинчивают ручку и осторожно вынимают
модель из формы [рис. 414 (m)]. В плоскости разъёма проделывают жёлоб от литника к форме. Из верхней опоки модель вытаскивают таким же способом,
как из нижней [рис. 414 (р)]. Если отливка очень
велика или имеет сложные очертания, то в верхней опоке проделывают один или
несколько выпоров. Единственное отличие выпоров от литника состоит в том, что
выпоры делают в наиболее высоко поднятых частях формы. В формах сложного
очертания выпоры образуют выход для находящегося в форме воздуха. В больших
формах выпоры служат для улавливания подымающегося на
поверхность шлака и резервуарами для непомещающегося в форму металла, который
снова стекает в форму по мере того, как остывает и получает усадку отливка
[рис. 414 (q)]. Теперь можно уложить в форму шишки и составить верхнюю и нижнюю опоки.
Если форма предназначена для тонких отливок из сплавов, то предварительно
следует прогреть обе половины формы с помощью ручной горелки. Процесс изготовления шишки заключается в следующем. Шишечные ящики
наполняют смесью крупного песка со связывающим веществом, утрамбовывают и
снимают излишек песка, проводя по плоскости разъёма ящика краем ровной
пластинки. Перевернув шишечные ящики на лист металла и слегка
постукивая по ним, освобождают обе половины шишки и потом отжигают их в
печи в течение нескольких часов. Затем половинки склеивают между собой смесью,
из которой они сделаны, или клеем и снова отжигают (рис. 415). Для изготовления
шишек применяют чистый кварцевый песок, просеянный через сито № 50, но задержанный
ситом № 70. В качестве связывающих может служить большое количество веществ,
полный список которых читатель найдёт в руководствах по литейному делу. Если
в качестве связывающего вещества взято льняное масло, то шишки отжигают в течение полутора часов при температуре 220°С. Если пользуются другими связывающими веществами, то прокаливание ведётся в течение полутора
часов при 175°С. Наиболее прочные шишки получают, когда пользуются льняным
маслом; смола и дёготь дают наименее прочные шишки. Тонкие, ломкие шишки часто укрепляют железной проволокой. Если шишка
очень велика, то необходимо, чтобы газы, образующиеся в ней при заливке металла,
имели выход, так как в противном случае они могут раздуть отливку. Чтобы этого
не случилось, в песок, идущий на изготовление шишек, вкладывают полоски воска.
Когда шишки прокаливаются, воск вытекает, оставляя отверстия для выхода газов. Расплавленный металл вливают в форму осторожно. Предварительно
следует снять шлак и накипь, образующиеся на поверхности находящегося в ковше
или тигле металла. Если металл имеет достаточно низкую температуру
плавления, позволяющую использовать железный сосуд, то можно воспользоваться
чайником, у которого носик сообщается с нижней частью. В этом случае при
заливке металла в форму плавающий шлак и окислы останутся внутри чайника. Если
форма вмещает большое количество металла, то рабочий, обычно, размешивает в ней метал, погружая в выпор железный прут и двигая его вверх и вниз. Благодаря размешиванию, находящийся в выпоре
металл не затвердевает до тех пор, пока не затвердеют внешние слои отливки. Обычно большие отливки оставляют остывать на всю ночь. Меньшие отливки
можно извлекать из формы немедленно. Иногда, при изготовлении инструментов,
небольшие отливки извлекают из форм ещё нагретыми до
красного каления и погружают их в воду. Образующийся при этом пар сдувает
песок с поверхности отливки и даже выдувает из неё шишки. Полученные таким
образом отливки оказываются совершенно чистыми. Когда отливка вынута из формы [рис. 414 (u)], нужно обрубить литник, выпоры и
жёлоб. Если отливка изготовляется самой лабораторией, то нужно помнить о том,
что литники и выпоры увеличивают количество металла, необходимого для изготовления
отливки. Литейная не включает этот металл в стоимость
отливки, так как литник и выпоры идут снова в дело. Баббиты состоят в основном из сплава свинца и олова с некоторым количеством
сурьмы, достаточным для того, чтобы при застывании металл несколько расширялся. Отливка в формах из раковин. Остаётся ещё один метод отливки изделий, который может оказаться полезным в лабораторных условиях, — отливка в формах из раковин каракатицы. Достоинства этого метода заключаются в его простоте и быстроте изготовления отливки:
изготовление и заливка формы отнимают около получаса. Однако отливаемое изделие
не может иметь толщину более 6 — 7 мм, ширину более 40 мм и длину
более 75 мм. Модель должна быть металлической, так как она подвергается
давлению. Конусность может быть весьма мала или даже совсем отсутствовать. Не
должно быть шишек. Рис. 418 даёт ясное представление об этом методе. Мягкая
известковая поверхность раковины весьма податлива и сохраняет очень чёткий
отпечаток любого вдавленного предмета. Джон Стронг «Практика современной физической лаборотории», ОГИЗ, Ленинград, 1948, стр. 415-437. |
Какие бывают типы литейных материалов?
Существует много типов литых материалов, используемых при изготовлении скульптурных или механических деталей, которые могут быть слишком сложными, чтобы их можно было изготовить с использованием другой техники. Различные типы материала в жидком или сжиженном виде выливают в отливку или форму, содержащую полую область в форме желаемой детали или изделия, а затем дают затвердеть в твердую форму формы. Одним из самых старых типов литейных материалов является песок, который используется для изготовления одного большого формованного изделия. Уретановый каучук используется в процессе заливки бетона и других заполнителей для использования как внутри, так и снаружи помещений. Гипс является основным ингредиентом, используемым для литья материалов из различных типов металлов с низкой температурой плавления.
Возможно, наименее сложное и наиболее широко используемое из всех различных процессов литья, литье в песчаные формы позволяет изготавливать литые изделия по очень низкой цене. Так как форма разрушается после каждого использования, этот тип литья лучше всего подходит для производителей, которым нужно только несколько формованных изделий. Песок, используемый при литье в песок, удерживается вместе с помощью химических связующих, глины или некоторых типов полимеризованных масел. Песок литейные формы также используются при литье очень крупных деталей. Например, вся стальная рама для железнодорожного вагона, бульдозера или судна может быть изготовлена из одной литейной формы для литья песка.
Уретановый каучук является одним из самых прочных из всех литейных материалов и используется в основном для изделий из бетона или других заполнителей, которые будут подвергаться воздействию элементов. Как и в случае с материалами для литья, такими как гипс, изготавливается модель, а уретановая резина заливается или формируется вокруг модели. После высыхания уретан осторожно извлекается из модели, создавая негативную форму изделия. После заливки бетона в форму он подвергается вибрации, которая оттягивает пузырьки воздуха от поверхности бетона, создавая гладкую поверхность, которая позволяет легко отрывать уретан. В процессе мокрого бетонирования используются резиновые формы для создания небольших декоративных элементов, таких как блоки подпорных стен, медальоны, карнизы, балясины и брусчатка.
Подобно литью в песчаные формы, для литья гипсовых форм используются те же основные методы, за исключением того, что вместо песка используется гипс из Парижа. В некоторых случаях гипсовые литейные материалы позволяют выполнять не только одну отливку. Модель детали или предмета создается путем заливки штукатурки вокруг детали, что приводит к образованию отрицательной формы или гипсовой отливки. Расплавленный металл или другой жидкий материал затем выливают в форму для изготовления конечной детали. Избыток штукатурки удаляется с помощью механического выбивания и струй воды под давлением. Такие литейные материалы способны обрабатывать только цветные металлы с низкой температурой плавления, такие как медь, алюминий и цинк.
ДРУГИЕ ЯЗЫКИ
СВЯЗУЮЩИЕ ДЛЯ ЛИТЕЙНЫХ ФОРМ — Справочник химика 21
СВЯЗУЮЩИЕ для ЛИТЕЙНЫХ ФОРМ [c.209] Фигурные детали из расплавов металлов изготовляют в литейных формах многократного либо одноразового использования [1, 2]. Литейные формы многократного использования (постоянные), изготовленные из металла, графита или керамики, применяют при разливке цветных металлов с низкой температурой плавления. Литейные формы одноразового пользования, изготовленные из формовочного песка, неорганических или органических связующих и различных добавок, применяют при разливке чугуна и других металлов. Расплавленный металл выливают в полость литейной формы, где он затвердевает в отливку нужной конфигурации. Под действием высокой температуры расплавленного металла форма становится хрупкой и легко удаляется с отливки для каждой разливки металла необходимо иметь одну форму и один стержень (рис. 14.1). [c.209]
Литейное производство является одним из главных потребителей фенольных смол. За последние 5 лет увеличение потребности в фенольных смолах было вызвано не расщирением литейного дела, а различными нововведениями в технологических процессах и, в частности, применением новых типов связующих. Структура литейного производства в различных странах далеко ие одинакова. Что же касается объема производства, то по этому показателю первое место в Западной Европе занимает ФРГ, а затем следуют Великобритания, Франция и Италия. До недавнего времени в ФРГ было 494 литейных производств с числом рабочих 103300 (1977 г.

В связи с тем, что в гарниссажных печах имеет место газовыделение с поверхностей графитового тигля и литейных форм, его также необходимо учитывать при расчете скорости откачки. [c.214]
Пероксиды применяют для повышения адгезии при получении комбинированных материалов типа полиэтилена на алюминии или железе. В сочетании с ЗОз в качестве окислителя, переводящего ЗОз в 50з, гидропероксиды и пероксид метилэтилкетона используют при изготовлении песчаных литейных форм с применением в качестве связующих фурановых и эпоксидных смол [90]. [c.26]
Использование синтетических смол в качестве связующего в литейных формах (корковое литье) позволяет автоматизировать их производство, сократить на 30—40% расход металла, уменьшить в 1,5 раза площади формовочных цехов и резко сократить последующую механическую обработку литых изделий. [c.10]
Формовочные смеси. Этот материал содержит в своем составе глинистые связующие компоненты и углеродсодержащие добавки, которые должны удаляться или дезактивироваться в случае дальнейшего использования очищенного песка в производстве стержней. Иначе углеродсодержащие компоненты и глина будут обусловливать ухудшение механических свойств стержней вследствие плохой адгезии смол к песку. Глина также абсорбирует большое количество добавляемых смол, что приводит к снижению механических свойств стержней и удорожанию процесса. Песок из литейных форм при многократном использовании в формовочных операциях подвергается разрушению и в нем накапливается большое количество мелких частиц. [c.149]
Основные области применения щелочных силикатных связующих в качестве связующего для лакокрасочной промышленности, для покрытий различного назначения, для изготовления литейных форм и стержней, для жаростойких бетонов, для укрепления грунтов и т.

От свойств литейных форм (их прочности, газопроницаемости) во многом зависит качество получаемых отливок. Поэтому представляет существенный интерес использовать омагниченную воду для затворения шихты, содержащей в качестве связующего бентонит, огнеупорную глину или цемент. Результаты исследования А. Чумаковой с соавторами [176], проведенного при различном содержании в шихте огнеупорной глины типа бентонита, времени перемешивания смеси в бегунах и различном режиме магнитной обработки технической воды, показали, что использование омагниченной воды позволяет повысить прочность песчано-глинистых и песчано-бентонитовых смесей на 25—30%. Газопроницаемость смесей тоже возрастает. [c.191]
Концентрация хрома в верхней зоне легированного слоя образца стали 25Л достигает 40—45%, а на некоторых других таких же образцах приближается к концентрации хрома в легирующей поверхности литейной формы. На границе с легированным слоем в структуре стали имеется ферритная полоса, обедненная перлитом. В отожженных образцах эта полоса но размерам гораздо больше, чем в неотожженных, что, по-видимому, связано с ди( )фузией углерода из стали в легированный слой к области, сильно насыщенной хромом. [c.278]
Первое применение стальной шерсти связано с именами Гальвани и Вольта, которые использовали ее для очистки поверхности металлов от ржавчины. Металлическую шерсть для этих целей применяют в быту и до сих пор. Однако теперь основное ее назначение — использование для технических целей. В годы второй мировой войны на изготовление маскировочных сеток в капиталистических странах было израсходовано —11 тыс. т стальной шерсти. Маленькие запалы, сделанные из стальной шерсти, используют для сварки на кораблях и танках. Прокладки из металлической шерсти применяют в большинстве литейных форм, теплообменниках, стиральных машинах. Хорошо зарекомендовала себя такая шерсть в качестве фильтрующего материала на нефтеперерабатывающих заводах, в установках кондиционирования воздуха, печах и т. д. Кроме того, она используется для армирования пластмасс, керамики, асбеста, металлов. Стальная шерсть находит применение в деревообрабатывающей промышленности для зачистки, шлифования и полировки поверхностей. [c.391]
Из диэлектрических материалов после перемешивания их с подходящими добавками можно приготовить плавлением электроды или образцы заданной формы тем же способом, которым плавят в литейных формах порошкообразные металлы (разд. 2.2.3). Брикеты становятся электрически проводящими после добавления к пробе угольного порошка или порошкообразных металлов (Си, Ag, N1 и т. д.) спектральной чистоты в соотношениях 1 1, 2 1 и т. д. В то же время эти добавки служат в качестве связующего вещества и воздействуют на состав, температуру и другие параметры плазмы источника излучения. Кроме того, в зависимости от поставленной задачи в анализируемую пробу вводят внутренние стандарты и различные добавки, регулирующие испарение, протекающие в источнике излучения реакции и другие процессы. [c.43]
Крепитель ДП применяется в литейном производстве в качестве связующего материала при изготовлении стержней П класса и некоторых стержней И класса сложности, а также как противопригарное средство для литейных форм, заливаемых по сырому способу, для чугунного и стального литья. [c.81]
Применяют в литейном производстве в качестве связующего материала при изготовлении стержней II, III, IV и V классов сложности и литейных форм для чугунного, стального и цветного литья. [c.82]
Конденсацией фенола с формальдегидом в присутствии кислот получают НС с более высокой температурой каплепадения по Уббелоде (126—135 °С), чем обычные НС (90—125°С). Их применяют в качестве связующих в производстве абразивных и асботехнических изделий и песчано-смоляных оболочковых литейных форм. Хорошо известны связующие ПБ (пульвербакелит), представляющие собой схмеси тонкоизмельченной НС с уротропином (7-8%). [c.201]
Значительное применение растворимое стекло различной модульности и концентрации находит в литейном производстве в качестве связующего вещества при изготовлении крепителей для литейных форм и стержней. В результате выделения [c.101]
СФЖ-3015) клеевой древесины и клеевых деревянных конструкций, связующее для литейных форм и стержней, изготовленных мегодом холодного отверждения [c.148]
Высокоплавкие пеки используются в производстве электроугольных изделии, углеродных конструкционных материалов, металлургического кокса, брикетированных углей и коксов, лаков, мастик, кровельных материалов, пеконаполненных полимеров, препарированных смол. Умеренно высокотемпературные пеки с Тразм=Ю5..,140 С используются в цветной металлургии кик связующие в производстве предварительно обожжённых и самообжигаюши.чся (с боковым теплоподводом) анодов. Пеки с Тразм=120,,,140°С и коксуемостью 51.,,54% используются в чёрной металлургии для изготовления углеродных литейных форм, а пеки с Трю. [c.120]
В тонкой и грубой керамике улучшение формовочных свойств глинистых материалов связано с влиянием ионов натрия на диспергирование частичек и изменение их пластичных свойств.
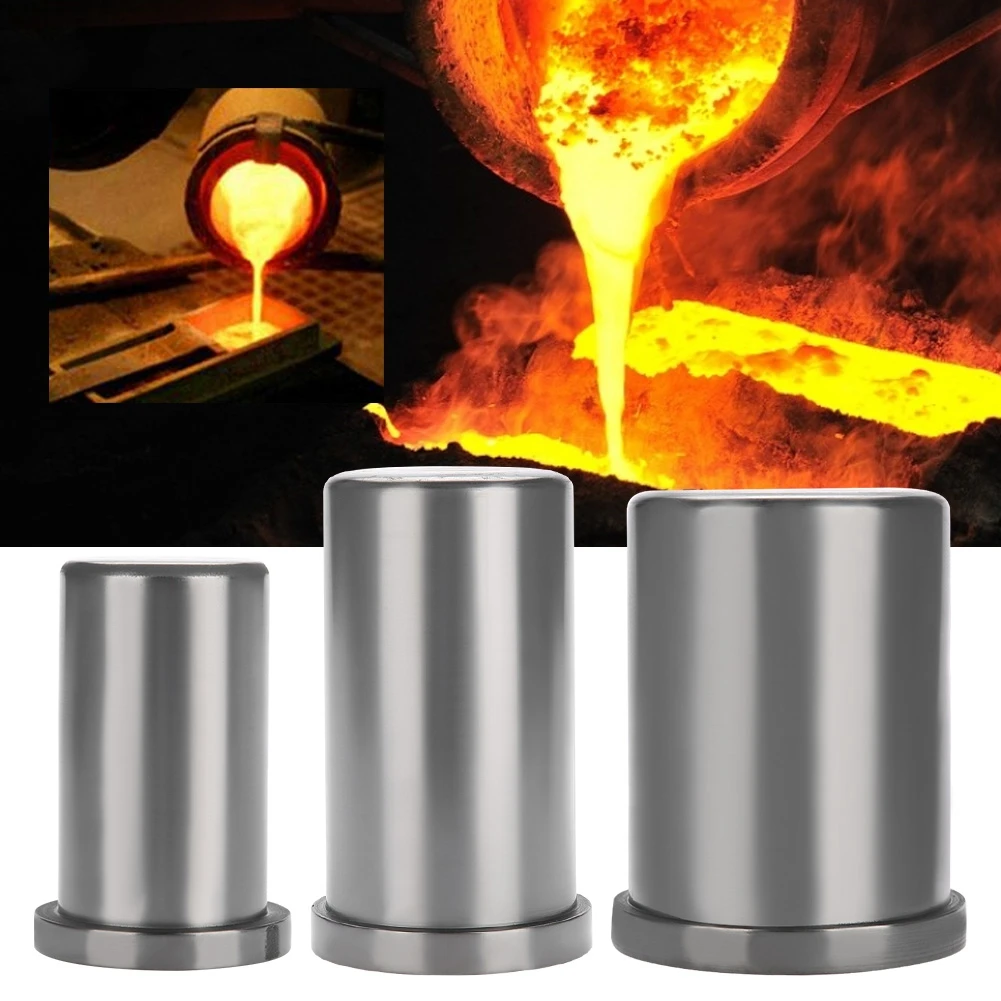
Далее, очень важным фактором является конфигурация зерен песка и распределение зерен по размерам. Когда жидкий металл соприкасается с литейной формой, из нее начинают выделяться пар и различные газы, образующиеся при разложении органических связующих. Для того чтобы обеспечить удаление газов и предотвратить создание избыточного давления в полости литейной формы (что, возможно, является причиной образования дефектов в отливке и повреждения формы), последняя должна быть пористой. Однако образование газов нграет и положительную роль, предотвращая проникновение металла через норы и способствуя созданию хорошей поверхности отливки. Таким образом, необходимо поддерживать баланс между газовыделеиием и газопроницаемостью формы [1]. [c.213]
Вследствие значительного повышения цен на песок, а также на его транспортирование и разгрузку важное значение приобретает вопрос утилизации литейных форм. В настоящее время разработаны установки ио регеиерации песчаных материалов следующими способами механическая регенерация (дробление, измельчение и удаление пыли) пневматическая регенерация (вибрационно-ударное грохочение) мокрая регенерация (вымывание неоргатшческих связующих) термическая регеиерацпя (ирокаливание). [c.213]
Качество поверхности стержней улучшают, покрывая их тонким слоем огнеупорного материала. Процесс изготовления литейных форм в горячих ящиках применим для массового производства малых и средних по объему отливок (рис. 14.5, 14.6). В автомобильной промышленности таким способом изготовляют картер коробки передач, картер двигателя, блок и головку блока цилиндров, кожух зубчатой передачи [21]. В качестве связующих применяют резольные смолы, модифицированные карбамидоформальдегидными, смолой на основе фурилового спирта и смесью смол на основе фури-лового спирта и карбамидоформальдегидной смолы в сочетании с катализатором. В качестве катализатора используют водные растворы аммониевых солей сильных органических или неорганических кислот аммиак взаимодействует с формальдегидом с образованием кислоты, что вызывает начало реакции отверждения. Процесс отверждения начинается уже при смешивании первых порций отвердителя и смолы, поэтому смесь надо готовить очень быстро, особенно нри повышенных температурах. [c.218]
После удаления ЗО2 и нек-рых примесей, напр, фурфурола и цимола, и доведения pH до 4,2-4,5 из орг. в-в С.щ. получают биохим. переработкой с обогащением питат. солями (N, Р, К)-этанол, многоатомные спирты, карбоновые к-ты, р-рители, кормовые дрожжи и др. хим. переработкой-ванилин, фенолы, ароматич. к-ты. Упариванием С.Щ., освобожденного от углеводов (обычно до срдержания сухого остатка ок. 50%), производят т.наз. концентрат сульфитно-сшфтовой барды (КССБ), используемый для дубления кож, пластификации цемента, как связующее при изготовлении литейных форм и т.д. [c.464]
Щелочные лигнины, лигносульфонаты и модифицированные лигнины находят самое разнообразное применение [10, 92, 96]. Их используют в качестве диспергаторов (для углеродной сажи, инсектицидов, гербицидов, пестицидов, глин, красителей, пигментов, керамических материалов) эмульгаторов, стабилизаторов и наполнителей (для почв, дорожных покрытий, асфальта, восков, кау-чуков, мыла, латексов, пены для огнетушения) соединений, связывающих металлы (в технологической воде, сельскохозяйственных микроудобрениях) добавок (к бурильным растворам, бетону, цементу, моющим составам, дубильным веществам, резинам, пластикам на основе виниловых мономеров) связующих и клеящих веществ (для гранулированных кормов, типографской краски, слоистых пластиков, литейных форм, руд) частичных заменителей реагентов (при получении карбамидоформальдегидных и феноло-формальдегидных смол, фурановых и эпоксидных смол, полиуретанов). Кроме того, их применяют в качестве коагулянтов белков, защитных коллоидов в паровых котлах, ионообменных материалов, акцепторов кислорода, компонентов наполнителей отрицательных пластин аккумуляторных батарей. [c.419]
Ацетоновые растворы кремниевых кислот (АРК) используют в качестве связующих при изготовлении из маршаллита (песка) литейных форм по выплавляемым моделям. АРК являются многокомпонентной системой, состоящей из коллоидной кремневой кислоты, ацетона и водосолевого раствора. Получают их нейтрализацией раствора силиката натрия соляной кислотой [138]. При нейтрализации происходит гидратация кремнекислородных цепей. При введении ацетона гидратная оболочка поликремниевых кислот, видимо, замещается сольватной оболочкой ацетона, а при добавлении Na l происходит высаливание и выделение кремниевых кислот в ацетоновую фазу. В свежем АРК мицеллы имеют шарообразную форму, при старении АРК происходит уменьшение концентрации поверхностных ОН-групп кремнезема, сопровожающееся полимеризационно-поликонден-сационным процессом. Все это вызывает потерю раствором вяжущих свойств. [c.144]
Крепитель ДП применяют в качестве связующего материала при изготовлении стержней дтя чугунного и стального литья, а также как противопригарное средство для литейных форм Дчя изготовления двухкомпонентного крепителя ДП пек с температурой размягчения 70 °С и выше измельчают в ще КОБОЙ дробилке, а формовочную глину — в барабанной глино дробилке Затем глину сушат в горизонтальном барабане ды мовыми газами при 150—160 °С до влажности 0,5—1 % ненова [c.165]
Возникающий на электроде галогенид лития представляет собой рыхлый непроводящий порошок. Лучше циклируются литиевые пастовые электроды 90% лития, 10% карбонильного никеля и карбоксиметилцеллюлоза как связующее. Токосъем — монель. Пасту наносили на сетку в литейной форме, прессовали и сушили в вакуумной печи. Такие электроды выдерживают анодную и катодную нагрузку до 10 ма1см при поляризации не более 0,1 в. Из этих данных следует, что литиевый пастовый электрод можно заряжать и разряжать с высокой скоростью. [c.98]
При м е II е н и с для р а з л и ч ных других ц е л е й. Коллоидный кремнезем может быть использован в качестве связующего вещества для различных материалов, употребляемых для изготовления литейных форм. Применение коллоидного кремнезема в качестве связующего вещества для форм из песка описано Марщаллом [121]. [c.121]
Применяется в кaчe tвe связующего для получения абразивных изделий и для изготовления оболочковых литейных форм. [c.200]
При получении целлюлозы по этому способу на 1 т целлюлозы получается около 10—12 т сульфитных щелоков. Использование этих щелоков имеет огромное народнохозяйственное значение, так как спускаемые в реки и другие водоемы, они не только загрязняют их, но и приносят огромный ущерб рыбному хозяйству. При переработке этих щелоков можно получать этиловый спирт С2Н5ОН, дубильные экстракты, связующие материалы для песчаных литейных форм и т. д. [c.180]
Применение отверждающихся фенольных смол дало возможность изготавливать традиционные монолитные литейные формы и стержни с улучшенными прочностными показателями, чего нельзя было достигнуть, используя обычные связующие — жидкое стекло, масла, бентонит и др. Разработанный Кронингом в 1944 г. новый способ производства литейных форм основан на применении смеси измельченных новолачных смол с уротропином [49]. [c.273]
Связующие ПК-104 (ГОСТ 13507—68) и ПК-В (для изделий ВАЗа) (ТУ 6-95-1370—70). Связующее ПК-104 представляет собой тонко измельченную смесь фенолоформальдегидной новолачной смолы марки СФ-011 и уротропина. Применяется при изготовлении литейных оболочковых форм и стержней. Связующее ПК-В представляет собой тонко измельченную смесь фенолоформальдегидной новолачной смолы марки СФ-012 и уротропина. Предназначается для изготовления центробежных песчако-смоляных литейных форм и стержней. [c.20]
От свойств литейных форм (их прочности, газопроницаемости) во многом зависит качество получаемых отливок. Поэтому представляет существенный интерес использованпе омагнпчеппой воды для затворения шихты, содерлкачестве связующего бентонит, ог- [c.238]
Литейные сплавы, их плавка и получение отливок
Производство Литейные сплавы, их плавка и получение отливок
просмотров — 162
Литейные сплавы. При достаточной жидко текучести расплавленный металл легко растекается и хорошо заполняет самые узкие места в форме. Некоторые металлы (к примеру, медь) в расплавленном состоянии густые и плохо заполняют формы, в связи с этим мало пригодны для фасонного литья. Такие сплавы, как бронза и латунь, достаточно жидкотекучи.
Важнейшие требования к литейным сплавам:
* малая усадка, ᴛ.ᴇ. незначительное уменьшение линейных размеров и объема при затвердевании и остывании. Для фасонного литья допустима усадка до 2.5%. Чем больше усадка, тем крупнее усадочные раковины и вероятнее появление трещин, так как податливость формовочной смеси ограничена;
* однородность, заключается примерно в одинаковом химическом составе всех частей отливки. Сплавы с большей ликвацией по плотности непригодны для отливки обычными способами;
* легкоплавкость — свойство металлов плавиться при невысокой температуре. Из легкоплавких металлов легче получит отливки.
Чугунное литье. Основную массу чугунного литья производят из серого чугуна. Вместе с тем, отливки получают и из белого чугуна с последующим отжигом на ковкий чугун. Литье из серого чугуна — основная продукция литейных цехов. Это объясняется в первую очередь его невысокой стоимостью, хорошими литейными свойствами, относительно невысокой температурой плавления (1100 — 1200 0С), хорошей жидко текучестью, малой усадкой — около 1%, однородностью отливок.
Хрупкость чугуна несколько ограничивает его применение. При этом множество деталей машин и механизмов не испытывающих больших ударных нагрузок, отливают из серого чугуна. Значительное улучшение свойств чугунного литья достигается модифицированием.
Отливки из белого чугуна отжигают на ковкий чугун. Содержание углерода в этом чугуне ограничивается до 2.2 — 2.3%. Чтобы предотвратить образование свободного графита в процессе литья, содержание кремния не должно превышать 1.4%. Повышенная жидко текучесть чугуна достигается при наличии фосфора (для машинного литья до 0. 2%). Марганец препятствует распадению карбидов железа (Fe3C) при отжиге, в связи с этим его содержание не должно превышать 0.6% (а для ферритных чугунов 0.5%). Усадка белых чугунов составляет около 2%.
Для плавки чугуна в литейных цехах чаще всего применяют вагранки. Вагранка представляет собой шахтную печь (рис.47), выложенную шамотным кирпичом 2 в стальном кожухе 3. Загрузка шихты производится через колошниковое отверстие 5 с колошниковой площадки 4. Воздух для горения топлива (кокса) поступает в вагранку от вентилятора по трубам через стальную коробку 6, опоясывающую вагранку, и через фурмы 7. Часть вагранки от верхнего ряда фурм до колошникового отверстия называют шахтой. Выше шахты находится дымовая труба с искрогасителем. Нижнюю часть, от лещади 1 до фурм называют горном. Лещадь наклонена в сторону копильника 9, где накапливается расплавленный чугун и выравнивается его состав. У копильника находится летка 10 и желоб 11 для выпуска чугуна, а также одна или две шлаковые лётки 8. Обычно вагранка работает 8 — 10 часов в сутки. Производительность её зависит от диаметра шахты и колеблется в пределах от 1 т до 25 т чугуна в час. В литейных цехах машиностроительных заводов вагранки выдают 3 — 8 т в час.
Иногда вагранки строятся без копильника, и тогда чугун и шлак выпускают через лётки из горна.
Загрузка шихты производится бадьей 12 с опускающимся конусным или откидным дном.
Для выдачи литья заданного химического состава составляют шихту из чушкового чугуна, чугунного и стального лома и ферросплавов в определенных пропорциях.
Рис.47.Схема вагранки с копильником
Подготовленная металлическая шихта͵ топливо и флюсы загружаются в вагранку отдельными порциями (колошами).
При плавке в вагранке кислород дутья выжигает примеси кремния 10 -15%, марганца 17 — 22%, железа 0.4 — 1.5%; содержание фосфора остается без изменения; углерод несколько выгорает, но его потеря компенсируется науглероживанием чугуна от кокса. Содержание серы несколько увеличивается за счет кокса, в связи с этим для вагранок используют литейный кокс с пониженным содержанием серы.
Образующиеся окислы шлакуются известняком.
Для получения высококачественных сортов серого чугуна, а также легированного и ковкого чугуна применяют двойные (дуплекс) процессы: плавку в вагранке и дуговой или пламенной печи, что дает возможность перегреть чугун и выдать его точно заданного состава.
Стальное литье. Литейные свойства стали хуже, чем у чугуна: она не столь жидкотекуча и хуже заполняет форму. Усадка стали 2% и выше, в связи с этим усадочные раковины в отливках бывают значительных размеров, сталь тугоплавка (температура плавления 1400 — 1540 0С). Чтобы избежать брака по усадочным раковинам, в формах, кроме выпоров, предусматривают наросты (прибыли), достаточные для питания жидкой сталью застывающей отливки, особенно в её верхних массивных частях.
При этом высокая прочность и вязкость стальных отливок определяет их преимущества перед другими видами литья, в связи с этим стальные отливки применяют для ответственных деталей.
Формовочные смеси для стальных отливок должны отличаться огнеупорностью и хорошей податливостью. При этом для сухих форм применяют тощие смеси из кварцевого песка и огнеупорной глины с добавкой отработанной смеси, а также быстротвердеющие смеси с жидким стеклом.
На литье идут доэвтектоидные углеродистые стали с содержанием 0.1 -.0.6%С, сталь Л15 — Л55 и легированные стали с марганцем, кремнием, никелем, хромом, медью, ванадием, молибденом, вольфрамом, титаном.
Сталь из малых конвертеров мартеновских печей и электропечей заливают в формы.
Емкость малых конвертеров -2 — 3 т. Чугун для них плавят в вагранке. Дутье в малый конвертер поступает через малый конвертер сбоку. Это позволяет, изменяя наклон конвертера, продувать металл по поверхности для сжигания выделяющейся окиси углерода и лучшего перегрева стали, которую выдают из конвертера при 1650 0С для большей жидко текучести.
Перегретая сталь годится для самых сложных отливок. В малых конвертерах, а также в мартеновских печах выплавляют главным образом, сталь обыкновенного качества, содержащую 0.2 — 0.3% С, а в электропечах — качественную углеродистую и легированную сталь.
Литье из сплавов цветных металлов. У кремнистых латуней и алюминиевых бронз усадка составляет 1.5 — 2.5%, и они сравнительно легко окисляются, в связи с этим при заливке должно быть обеспечено плавное заполнение форм.
Часто в одной опоке набивают несколько форм, соединенных питателями с общим стояком. Вес литниковой системы и прибылей иногда составляет до 150% от веса готовой отливки.
Медные сплавы для литья расплавляют в дуговых электропечах, индукционных печах со стальным сердечником и без сердечника, а также в пламенных печах.
На рис.48изображена качающееся дуговая электропечь. В таких печах дуга независима: она зажигается между графитовыми электродами 1. Расплавление шихты происходит за счет тепла, излучаемого дугой. Для ускорения расплавления шихты и для обеспечения однородности состава металла печи покачивают с помощью поворотного механизма 2. Этим же механизмом наклоняют печь при сливе готового металла.
Рис.48.Качающаяся дуговая электропечь
На рис. 49показана схема индукционной печи со стальным сердечником 1. Эти печи применяют для непрерывной массовой плавки металла одной марки, так как печь работает только при наличии кольца 2 из жидкого металла, представляющего по электрической схеме «виток» вторичной обмотки трансформатора и окружающего находящуюся под футеровкой первичную катушку 3. Расплавленный металл выливают из печи частями, вновь погружая каждый раз «свежий», чтобы быстро расплавить от соприкосновения с перегретым жидким металлом.
Рис.49.Схема индукционной печи со стальным сердечником
Пламенные печи применяют реже, так как печные газы окисляют медные сплавы. Вместе с тем, в этих печах расходуется много топлива.
Для расплавления алюминиевых и магниевых сплавов применяют ванные электропечи с излучающим нагревателем сопротивления. В небольших цехах используют горны.
На рис.50.изображен поворотный пламенный тигельный горн со стальным тиглем 1. Топливо (мазут) подводится по трубе 3 и сгорает в пространстве 2; продукты горения отводятся через вытяжной колпак трубы 4.
Рис.50.Пламенный тигельныйгорн
Заливка форм, выбивка и очистка литья. Чугун подают на заливку в поворотном ковше, выложенном шамотным кирпичом. Для уменьшения теплопотерь применяют барабанные ковши или ковши с крышкой (рис. 51). В них удобно модифицировать чугун. Для разливки стали применяют стопорные ковши.
Рис.51.Ковш с крышкой
Остывшие отливки выбивают из формы с помощью встряхивающих решеток, вибраторов и других машин; стержни выбивают вручную, на пневматических машинах или гидрокамерах струей воды под давлением 30 — 100 ат.
Прибыли, литники и выпоры от стальных отливок отделяют газовой резкой, а от чугунных — пилами. Очищают отливки от остатков формовочных и стержневых смесей окатыванием в барабанах или пескоструйными, дробеструйными и дробеметными аппаратами. Применяют также песко-гидравлическую очистку, при которой струю воды с песком под давлением до 70 ат и выше направляют на отливку.
Для зачистки заусенцев служат обдирочно-шлифовальные машины с крупнозернистыми абразивными кругами.
Литье в металлические формы (кокильное литье)
Металлические формы для литья в (кокиль) изготавливают из чугуна или стали. При литье из легких сплавов применяют чугунные и стальные стержни, а в случае литья из стали, чугуна и медных сплавов — песчаные стержни. Для относительно легких сплавов цветных металлов металлические формы выдерживают сотни тысяч заливок, стойкость форма при литье чугуна колеблется в пределах 1500 — 5000 заливок, а при отливке стали — от 25 до 700 в зависимости от размера отливок; в связи с этим литье в металлические формы для крупных стальных отливок выгодно лишь в случае простых форм, когда стоимость изготовления их невелика. Применительно к сплавам цветных металлов и чугуну данный способ более выгоден, так как, кроме более точных размеров отливок, они лучше по структуре и механическим свойствам.
Против отбеливания чугуна и для большей стойкости форм их покрывают тонким слоем огнеупора и сажи, тем самым замедляется скорость охлаждения чугуна. Вместе с тем, перед заливкой чугуна формы подогревают до 200 — 300 0С. Отбеливанию препятствует также увеличение кремния в чугуне.
Для литья сложных деталей применяют металлические формы из нескольких частей (разъемные).
На рис.52показана металлическая форма со штырями (пальцами) снаружи для ускорения охлаждения.
При массовом производстве литье в металлические формы можно автоматизировать, как, на пример, на заводах-автоматах, где отливают алюминиевые поршни для двигателей внутреннего сгорания.
Отбеленным закаленным литьем называют чугунное литье с отбелом на нужную глубину при быстром охлаждении в металлической форме (кокиле). В закаленном слое весь или почти весь углерод остается связанным (в цементите).
Твердость НВзакаленных деталей колеблется в пределах от 300 до 500 и выше, глубина отбела от 12 до 30 мм. Скорость охлаждения отливки должна обеспечивать постепенный переход белого чугуна в серый, в противном случае отбеленный слой может выкрашиваться.
Рис.52.Сборная металлическая форма
Наибольшее распространение отбеленное литье получило в производстве прокатных валков и колес железнодорожных вагонов. На рис.53приведена форма, подготовленная для заливки прокатного валка. Здесь кокилем (металлической формой) является только средняя часть 1, которая образует рабочую поверхность валка; верхняя 2 и нижняя 5 части формуются в опоках из формовочной смеси по модели и образуют шейки валка, которые впоследствии обрабатываются на станках.
Рис.53.Форма для отливки прокатного валка
Через литниковую чашу 3 и литниковый стояк 4 чугун сифоном подводят в нижнюю часть собранной формы.
Литье металлов в домашних услови
Литье металлов в домашних условиЛитье металлов в домашних условиях
Изготовить небольшую деталь сравнительно простой формы из легкоплавких цветных металлов и сплавов (олово, медь, алюминий, цинк, свинец, латунь) в домашних условиях под силу любому мастеру-любителю.
Рассмотрим технологию изготовления литейной формы. Литейную форму создают в формовочном ящике, изготавливаемом из неструганых досок (для лучшего контакта с формовочной землей) и называемом опокой. Размеры опоки должны быть примерно в 1,5 раза больше размеров детали. Опока (рис. 2.5.1) состоит из двух частей: нижней (ящик с дном) и верхней (рамка с двумя-тремя поперечинами в середине). Для прочного соединения обеих частей опоки на ящике устанавливают фиксаторы, а на рамке делают углубления.
Формовочная земля состоит из 75 % чистого мелкого песка, 20 % глины и 5 %
каменноугольной пыли. Все компоненты должны быть тщательно перемешаны до
получения однородной массы.
Рис. 2.5.1. Опока
Моделью для изготовления формы может служить как сама деталь, так и специальная модель, выполненная из дерева или иного материала. Если моделью для формовки служит уже сработанная в отдельных местах деталь (например, защелка замка автомобильной двери), то сработанные места наращивают шпатлевкой (желательно эпоксидной) до размеров новой детали. После полного затвердевания наращенные места обрабатывают напильником и зачищают шкуркой.
При формовке в нижнюю часть опоки насыпают формовочную землю и слегка ее
утрамбовывают. Модель припудривают порошкообразным графитом или тальком и
вжимают ее в землю наполовину. Размещают модель таким образом, чтобы выступы и
другие ее части легко вынимались из формы и не разрушали ее. Землю в ящике снова
посыпают графитом или тальком, на нижнюю часть опоки устанавливают верхнюю,
совмещая фиксаторы с отверстиями. В неответственной части будущей детали ставят
коническую пробку широкой частью кверху для формирования литника, через который
расплавленный металл будут заливать в форму (рис. 2.5.2). После этого в опоку с
избытком насыпают формовочную землю и хорошо ее утрамбовывают. Затем очень
аккуратно вынимают пробку под литник, острым предметом снимают верхнюю часть
формы и вынимают модель из нижней. На обеих частях формы должны быть углубления,
которые точно отображают форму детали. Иногда приходится подправлять модель
тонким гибким ножом, удаляя излишки формовочной земли или, наоборот, добавляя ее
в том месте формы, где она прилипла к модели и вынулась вместе с ней.
Если деталь длинная, то в одном ее конце устраивают литник, а в другом формируют отверстие, аналогичное
Рис. 2.5.2. Формовка металла
литниковому, но служащее для удаления воздуха из формы по мере заполнения ее расплавленным металлом. После подсыхания обеих половин формы, их соединяют и хорошо сжимают, чтобы не осталось щели между верхней и нижней частями. В результате получилась форма, готовая к заливке металлом.
Плавят металл в стальной или чугунной емкости, имеющей носик, через который
расплавленный металл заливают в литниковое отверстие формы. В качестве печи
используют небольшой горн или муфельную печь.
При плавлении цинка в посуду поверх металла целесообразно насыпать слой древесного угля, чтобы воспрепятствовать выгоранию металла.
После расплавления металл 4—5 мин выдерживают в печи для максимального прогрева. Эта операция способствует качественному заполнению формы в тонких местах. Расплавленный металл заливать в форму необходимо непрерывной, но тонкой струёй, чтобы не происходило размывания формы.
После полного остывания металла форму разнимают и вынимают готовую деталь. Изделия, получаемые описанным методом, как правило, имеют шероховатую поверхность и нуждаются в дополнительной чистовой обработке.
Рассмотрим теперь технологию литья более сложную, чем предыдущая, но позволяющую
получать изделия высокого качества и точности. Эта технология дает возможность
отливать в домашних условиях технические изделия сложной формы, скульптуры,
барельефы и прочее.
Модель будущего изделия изготавливают из воска, парафина или иного легкоплавкого материала, затем ее заформовывают в неразъемной жаростойкой массе. При незначительном нагревании или даже кипячении в воде восковую модель выплавляют из формы через отверстие (будущий литник), а в полученную форму заливают расплавленный металл. При тщательном формовании данный способ позволяет повторить в изделии мельчайшие элементы модели.
Изготовление модели.
Материал, применяемый для создания модели, должен иметь температуру плавления в пределах 50—90 град. С и плотность, меньшую, чем плотность воды, чтобы при выплавлении модели он беспрепятственно всплывал на поверхность. Этим требованиям лучше всего соответствует воск пчелиный, сплав одинаковых частей стеарина и парафина, зубопротезные воски: “Воск для базисов”, “Воск моделировочный”, “Воск для бюгельных работ”.
Если необходимо иметь точную форму, например ключ сложной конфигурации, то
сначала с помощью оригинала изготавливают гипсовую форму, а уже в ней отливают
восковую модель.
Процесс создания восковой модели мало чем отличается от изготовления отливки. Разница лишь в том, что для заливки гипса не нужна опока, ее с успехом заменит картонная коробка подходящих размеров.
Последовательность изготовления небольшой восковой модели следующая. Гипс
разводят до консистенции жидкой сметаны, выливают его в коробку и, пока он не
схватился, в него вдавливают модель-оригинал на половину ее высоты (рис. 2.5.3).
Оригинал предварительно покрывают тонким слоем вазелина. Одновременно в гипс по
краям коробки вдавливают на половину длины две спички, которые будут исполнять
функции фиксаторов. После затвердевания гипса его поверхность, а также
выступающие части спичек-фиксаторов покрывают равномерным тонким слоем вазелина
и свежим раствором гипса заливают верхнюю часть коробки. Перед заливанием
верхней части модели на ее край ставят металлическую вставку из толстой
проволоки или гвоздя для образования литникового отверстия. После затвердевания
гипса верхнюю часть отсоединяют от нижней с помощью тонкого ножа, вынимают
оригинал и литниковую вставку, придают конусность верхней части литникового
отверстия (для удобства при заливке воска), соединяют обе половины формы,
ориентируясь на спички-фиксаторы, плотно сжимают.
В результате имеем готовую форму для получения восковой модели. Расплавленную восковую массу заливают через литниковое отверстие в форму, и после охлаждения аккуратно вынимают. Если изделие неправильной формы и имеет большое количество выступов, то наряду с литниковым отверстием формируют одно или несколько тонких отверстий для выхода воздуха, вытесняемого расплавленным воском. С готовой модели аккуратно удаляют остатки литника и воздуховыводящих каналов, а также заусенцы.
Рис. 2.5.3. Последовательность изготовления восковой модели
Изготовление формы.
Готовую восковую модель формуют в огнестойкую форму, однако, перед этим к модели
присоединяют литник, изготовленный из воска. Формовочная масса, которой заливают
восковую модель, при литье изделия из алюминия и легкоплавких бронз (температура
плавления 860—880 град.С) состоит из следующих компонентов (в массовых частях):
1-й состав
Гипс……………………1
Тальк………………….2
Мел……………………2
Песок (мелкий) …1
2-й состав
Гипс…………………….1
Песок (мелкий)…… 2
3-й состав
Гипс……………….1
Кремнезем………3
Медицинская промышленность выпускает составы “Силаур ЗБ” и “Силаур 9”, в которые входят высококачественные гипс и кремнезем. Эти препараты можно с успехом применять в качестве формовочной смеси.
Формовочную массу разводят водой до сметаноподобного состояния, после чего ею
полностью заливают восковую модель. Для этого на дно емкости наливают небольшое
количество массы, аккуратно устанавливают на нее восковую модель и постепенно
заливают массу вокруг модели, контролируя отсутствие пузырьков воздуха. Полное
затвердевание формы произойдет через 40—60 мин.
Если изделие планируют отливать из металла или сплава, температура плавления которого превышает 880 град.С, восковую модель предварительно обрабатывают слоем огнестойкой обмазки (толщина слоя примерно 1 мм), а уже затем заливают формовочной массой.
В качестве огнестойкой обмазки целесообразно применять средства “Силамин” и “Формалит”,
выпускаемые медицинской промышленностью. В состав “Сила-мина” входят
магнезитовый порошок, кварцевый песок, этилсиликат и в качестве затвердителя —
раствор жидкого стекла. “Формалит” состоит из пылевидного кварца и этилсиликата.
В случае отсутствия указанных средств восковую модель можно обработать смесью
талька и водного раствора жидкого стекла (1 часть жидкого стекла и 3 части
воды). Покрытую смесью восковую модель присыпают чистым кварцевым песком, затем
опять покрывают смесью и присыпают песком. В общей сложности операцию повторяют
4—5 раз. Если отливаемое изделие достаточно велико и, следовательно, велик объем
заливаемого в форму расплавленного металла, то необходимо нанести 6—7 слоев
самодельной огнеупорной обмазки. После того как обмазка высохнет, модель
погружают на 2 мин в водный раствор (18—20 %) аммиака (нашатыря) для
закрепления. Теперь настал черед выплавки восковой модели из формы, образованной
застывшей формовочной смесью.
Чаще всего форму просто кипятят в воде. Литниковое отверстие должно находиться в
верхней части формы, погруженной в воду, чтобы расплавленный воск мог свободно
выходить наружу и всплывать на поверхность воды. Если отливаемая деталь имеет
сложную поверхность, то в процессе кипячения необходимо многократно
переворачивать форму для полного ее освобождения от воска. После удаления
восковой массы внутри формы образуется полость, точно соответствующая модели.
Перед заливкой металла форму необходимо прокалить в муфельной печи или горне.
Сначала печь разогревают до 550—600 град. С, потом в нее кладут форму и
поднимают температуру до 900 град. С. При этой температуре прокаливание длится
2—4 ч (в зависимости от массы формы).
После прокаливания форму охлаждают до комнатной температуры, если в нее заливают алюминиевые сплавы или чугун. Если же заливают латунь или бронзу, то форму охлаждают лишь до 500 град. С. Нержавеющую сталь заливают в форму, имеющую температуру 850 град. С.
Заливка металла.
В сравнительно большие формы расплавленный металл затекает под действием
собственного веса, вытесняя находящийся там воздух. Но если отливка имеет
маленькие размеры, то хорошего качества изделия добиться невозможно, так как
воздух не позволяет жидкому металлу заполнить все полости формы. Преодолеть эту
трудность можно, поместив форму в ручную центрифугу. Центробежная сила помогает
вытеснить воздух и дает возможность металлу полностью заполнить все пустоты
формы. Однако производить эту операцию необходимо быстро, пока металл находится
в расплавленном состоянии.
Готовую отливку вынимают из формы, разрушая отливку. Затем механическим путем
удаляют литник и каналы для отвода воздуха (если они есть). При необходимости
готовое изделие подвергают косметической обработке.
§ 20. Удельная теплота парообразования и конденсации
1. На что расходуется энергия, подводимая к жидкости при кипении?
Условие:
Решение:
Советы:
Т.е. подводимое тепло увеличивает кинетическую энергию молекул жидкости, которые вылетают из объема жидкости и не возвращаются обратно.
2. Что показывает удельная теплота парообразования?
Условие:
Решение:
Советы:
Обычно удельная теплота парообразования обозначается буквой L, единица измерения - Дж/кг.
3. Как можно показать на опыте, что при конденсации пара выделяется энергия?
Условие:
Решение:
Советы:
Вода в трубах становится теплой и потом горячей.![]()
4. Чему равна энергия, выделяемая водяным паром массой 1 кг при конденсации?
Условие:
Решение:
Советы:
Имеется в виду, что этот пар находится при атмосферном давлении, иначе значение энергии конденсации будет другим - увеличивается при уменьшении давления и наоборот, уменьшается при увеличении давления.
5. Где в технике используют энергию, выделяемую при конденсации водяного пара?
Условие:
Решение:
Советы:
В теплообменнике пар отдает энергию при конденсации теплоносителю. Теплоносителем может быть вода или другая неагрессивная, невзрывоопасная и непожароопасная жидкость с температурой кипения не выше +60ºС, нефтепродукты - битум, мазут, дизельное топливо.
Упражнение 16.1. Как надо понимать, что удельная теплота парообразования воды равна 2300 кДж/кг?
Условие:
Решение:
Советы:
Подразумевается, что это происходит при атмосферном давлении.
Упражнение 16.2. Как надо понимать, что удельная теплота конденсации аммиака равна 1400 кДж/кг?
Условие:
Решение:
Советы:
Имеется в виду, что это будет происходить при атмосферном давлении.![]()
Упражнение 16.3. У какого из приведенных в таблице 6 веществ при обращении из жидкого состояния в пар внутренняя энергия увеличивается больше? Ответ обоснуйте.
Условие:
Решение:
Советы:
При изменении внешнего давления вышеприведенный вывод может быть неверен - другое вещество будет обладать большей внутренней энергии.
Упражнение 16.4. Какое количество энергии требуется для обращения воды массой 150 г в пар при температуре 100°C?
Условие:
Решение:
Советы:
Задача решена верно только если подразумевается атмосферное давление.
Упражнение 16.5. Какое количество энергии нужно затратить, чтобы воду массой 5 кг, взятую при температуре 0°C, довести до кипения и испарить её?
Условие:
Решение:
Советы:
Всё это верно только при атмосферном давлении и при пренебрежении затрат тепла на нагрев окружающего воздуха и сосуда, в котором находится вода.
Упражнение 16.6. Какое количество энергии выделит вода массой 2 кг при охлаждении от 100 до 0°C? Какое количество энергии выделится, если вместо воды взять столько же пара при 100°C?
Условие:
Решение:
Советы:
Всё это верно при атмосферном давлении.![]()
Задание 1. По таблице 6 определите, у какого из веществ при обращении из жидкого состояния в пар внутренняя энергия увеличивается сильнее. Ответ обоснуйте.
Условие:
Решение:
Советы:
При изменении давления этот вывод может быть неверен.
Задание 2. Подготовьте доклад на одну из тем (по выбору). Как образуется роса, иней, дождь и снег. Круговорот воды в природе. Литьё металлов.
Условие:
Решение:
Советы:
При остывании жидкого металла и его кристаллизации выделяется тепло кристаллизации, равное теплоте плавления данного вещества.
Алюминиевые алюминиевые изделия Алюминиевый процесс литья в форме песка ASTM A356 T6 Материал Производитель и поставщик Китай
Описание продукта и процесс
литые алюминиевые изделия алюминий зеленый песок литье процесс ASTM A356 T6 материал
Производственный процесс: процесс литья зеленого песка, процесс литья песка с предварительной обработкой
Процесс обработки: машина с ЧПУ, обрабатывающий центр, токарный станок, мельница, сверлильный станок и т. Д.
Процесс обработки поверхности: анодное окисление, покрытие Dacromet, порошковое покрытие и т. Д.
Материал и использование продукта
Обычно производят с ZL101, ZL101A, ZL102, ZL104, ZL106, ZL107, ZL109, ASTM A356 T6, A319, A413, LM6, LM20, LM25 и т. Д.
Алюминиевые литейные изделия широко используются в электронной промышленности, автомобильных деталях, железнодорожных деталях, частях электродвигателя, частях аэронавигационного оборудования, частях кораблей, оборудовании для лечения, системе связи, других компонентах оборудования и т. Д.
АЛЮМИНИЕВЫЙ ПЕСОК
Пескоструйная обработка является одним из самых быстрых и экономичных методов литья, применяемых при изготовлении металлических прототипов, и является отличным решением для малых и средних прогонов деталей, которые не требуют точной повторяемости формы, а также являются единственным решением для очень больших объекты, которые не могут быть изготовлены с использованием других методов массового производства.
Песок является отличным недорогим литым материалом, поскольку он огнеупорный и химически инертный. Пескоструйная отливка также идеально подходит для производства очень сложных компонентов, требующих песчаных сердечников (холодный ящик или ракушечный песок) для самых сложных деталей и имеющих внутренние участки с изменениями толщины.
Процесс литья алюминиевого песка
Зеленый песок, который является новым или регенерированным песком, смешанным с натуральными или синтетическими связующими, является наиболее часто используемым материалом для изготовления алюминиевых одноразовых форм. Зеленые песчаные формы получают свое название от того факта, что они все еще влажны, когда расплавленный металл наливается в них. Процесс литья алюминия с использованием зеленого песка и метод гравитационного наполнения можно резюмировать следующим образом:
плесень создается путем помещения смеси песка, глины и воды на узор (реплика объекта на литье). Хотя этот процесс можно сделать вручную, машины обычно используются для достижения лучшей точности формы. Когда образец удаляется, глина будет иметь полость, которая соответствует форме рисунка.
Песчаная пресс-форма состоит из двух или более частей, верхняя часть известна как совпадение, а нижняя — перетаскиванием. Также можно использовать дополнительные части, называемые щеками. Формы заключены в две части (или более, если используются щеки), которые называются колбой для защиты. Перед закрытием колбы любые стержни из песка, необходимые для изготовления деталей детали, помещаются в половинки формы. Система стробирования размещена внутри, и для того, чтобы расплавленный сплав был подан в литье, был сформирован спру.
Две половины закрыты и зажаты вместе, а затем расплавленный металл выливают в форму. Когда металл начинает охлаждаться и происходит некоторое сокращение, расплавленный металл подается из стояков, которые были помещены в систему литья.
Поскольку песок и глина не поглощают тепло, время охлаждения намного дольше, чем время непрерывного литья или литья под давлением. Охлаждения (металлические пластины) могут быть вставлены в песчаную форму, чтобы обеспечить равную скорость охлаждения во время литья. Вследствие более медленного охлаждения наблюдается заметное снижение механических свойств сплавов, таких как алюминий 319 и 356, магния и бронзы по сравнению с теми же сплавами, отлитыми с использованием методов непрерывного или литья под давлением на основе вторичного дендрита Значение интервала между запятыми (SDAS).
После заданного времени выдержки, чтобы металл мог затвердеть, происходит трение. Тепло от расплавленного металла, который выливается в него, высушивает влагу, благодаря чему литье легко расщепляется при охлаждении металла.
Алюминиевые дефекты литья под давлением, которые нужно искать, — это остаточная оксидная пленка, включение, эрозия сердечника, газовые отверстия и пористость усадки.
Алюминиевые компоненты из литого алюминия широко используются в автомобильной и транспортной промышленности, в том числе в аэрокосмической промышленности. Части, обычно выпускаемые с литьем песком, включают в себя силовые передачи, опоры, подвески, кожухи, шестерни и многие другие.
Алюминиевый песок с точки зрения численного моделирования
Симуляционная модель, которая оптимизирует процесс и компоновку песчаного литья, требует полного моделирования динамики жидкости, включая изменение ламинарного потока расплавленного металла в нежелательный турбулентный поток. Модель также должна учитывать естественную воздухопроницаемость пресс-формы, позволяя легко покидать газы и пар, создаваемые процессом литья, благодаря хорошей проницаемости песчаных форм и сердечников. Некоторые типичные параметры процесса и их соответствующие результаты, которые должны быть включены в модель:
Риск включения в случае скорости турбулентного вихря и расплавленного металла выше предлагаемого диапазона 0,5 м / с;
Температура изменяется во время процесса наполнения, чтобы предсказать появление холодных остановок.
Возможный перегрев, когда сердечники касаются металла, вызванного низким поглощением тепла песком, что может привести к поверхностным дефектам, таким как раковины;
Различные скорости охлаждения, поскольку они могут генерировать высокий уровень остаточного напряжения и значительное искажение кастинга.
Освоение процесса литья песка посредством моделирования
Используя инженерное моделирование для оптимизации процесса литья песка для алюминия и легких сплавов, мы можем привести литейные цеха к производству «нулевого дефекта», что приведет к соответствию размеров изделий. Инженерное моделирование может помочь с:
Оптимизация конструкции стробирующей системы, чтобы избежать заполнения дефектов, вызванных турбулентностью.
Избегая наличия усадочных пористостей, воздействуя на переменные процесса и геометрию фидера прямо на этапе проектирования.
Сокращение испытаний на литье.
Прогнозирование локальной микроструктуры и механических свойств.
Правильная оценка деформации литья и остаточного напряжения.
И все это может быть достигнуто, сокращая время выхода на рынок конечного продукта.
Hot Tags: литые алюминиевые изделия алюминий зеленый песок литье процесс ASTM A356 T6 материал, Китай, производитель, поставщик
Процесс литья — обзор
Процесс
Используются различные процессы литья. Они имеют тенденцию перекрываться и могут быть идентифицированы другими методами обработки. Примером является литье под давлением жидкости, которое можно определить как литье под давлением (Глава 4) или реактивное литье под давлением (Глава 12). Много десятилетий назад процесс реактивного литья под давлением первоначально назывался жидкостным литьем под давлением.
В некоторых случаях химическая реакция происходит во время процесса литья, в результате которого низкомолекулярный мономер превращается в высокомолекулярный термопласт (главы 1 и 2).Самые распространенные примеры — акрил и нейлон. В других случаях полимеризация и сшивание происходят одновременно в процессе литья, что приводит к термореактивной полимеризации. Примеры включают полиуретановые смолы (PUR), ненасыщенные полиэфирные пластмассы (UP), эпоксидные пластмассы (EP) и силиконовые пластмассы (Si).
Экзотермические системы термического отверждения могут использоваться при обработке при комнатной температуре путем добавления пластических добавок и / или промоторов. Они используются для обеспечения необходимого тепла посредством химических реакций.Эту реакцию необходимо контролировать, чтобы не происходил перегрев, особенно для крупных деталей, где могут возникнуть повреждения, например пустот и несоответствия требованиям к размерам.
В дополнение к обычному процессу жидкого литья используются другие, в том числе литье по выплавляемым моделям, которое возникло много веков назад. Ранние египтяне разработали литье по выплавляемым моделям для изготовления ювелирных изделий, где воск для скульптуры погружали в керамическую суспензию, затем сушили и нагревали для удаления воска. В свою очередь, в керамическую полость поступал расплавленный металл, чтобы сформировать желаемую готовую деталь.Этот метод продолжал использоваться с модификациями, которые первоначально привели к литью различных материалов, в том числе пластмасс. Появились и другие системы, такие как так называемый воск по выплавляемым моделям или растворимый стержневой воск. Позднее стали использоваться эвтектические сплавы с низкой температурой плавления, что позволило получать сложные отливки с высокой производительностью (глава 15).
Процесс центробежного литья, также называемый центробежным формованием, представляет собой метод формования пластика, при котором сухой или жидкий пластик помещается во вращающуюся форму, такую как труба (Глава 13).Когда он вращается вокруг одной оси, к пресс-форме прилагается тепло. Возникающая центробежная сила заставит расплавленный пластик соответствовать конфигурации внутренней полости формы. Этот метод отличается от ротационного формования, поскольку он вращается только вокруг одной оси. Такие изделия, как трубы, трубы и резервуары (за исключением торцевых крышек), которые имеют кругло-цилиндрическую форму, могут быть изготовлены из неармированного или армированного стекловолокна (GRP) методом центробежного литья. В случае прерывистого армирования волокнами смесь измельченных волокон и предварительно катализированного жидкого пластика распределяется вдоль оси вращающегося цилиндрического инструмента.Когда материал падает на внутреннюю поверхность инструмента, он захватывается, и центробежные силы помогают уплотнять его в однородный слой, а также удерживать его на месте во время отверждения. Последовательные проходы по длине цилиндра могут привести к увеличению толщины. Окончательная внутренняя поверхность, хотя и не так хороша, как внешняя, достаточно гладкая. На внешней поверхности могут быть сформированы элементы (фланцы, резьба, ребра и т. Д.), Если форма состоит из соответствующих секций, позволяющих извлекать готовый продукт.Процесс может быть изменен для обеспечения непрерывного производства труб.
Существует модифицированный процесс центробежного литья, который позволяет производить трубы / трубки из ТР, армированные непрерывной нитью, с точным размещением волокон и гладкими внутренними и внешними поверхностями. TP, как нейлон и полипропилен, армированы такими волокнами, как стекло и углерод. Такие продукты, как автомобильные приводные валы и подшипники, производятся с содержанием волокна до 60 мас.%. Эти трубы имеют очень низкий вращательный дисбаланс и жесткий допуск по толщине стенки (Глава 15).
Процесс, называемый TER-центрифугированием (д-р Инг Х. Шурманн, Технический университет Дармштадта, Германия) начинается с наматывания сухих армирующих волокон вокруг термопластической трубки, которую можно изготовить экструзией или литьем под давлением. Волокна могут быть расположены таким образом, чтобы соответствовать определенной нагрузке. Затем трубка и волокна загружаются в литейную форму, вращаются с контролируемой скоростью и нагреваются. Когда расплавленная пластиковая трубка вращается, пластмасса пропитывает волокна.
Существует процесс литья окунанием, также называемый окунанием или формованием окунанием.Это процесс погружения горячеформованной формы, обычно металлической, в жидкий пластик. После снятия и охлаждения изделие вокруг формы вынимается из формы.
Литье из слякоти, также называемое литьем из слякоти или литьем, широко используется. Это метод, при котором ТП в жидкой форме заливают в горячую форму, которая является неподвижной или движущейся, в которой образуется вязкая пленка. Излишки слякоти сливаются, форма охлаждается, а формовка удаляется. Используется для производства дождевых или снегоходов, автомобильных приборных панелей, ботинок, гофрированных и негофрированных сложных труб, крышек и т. Д.
При литье из растворителя тщательно готовят пластик, смешанный с его компонентами (растворителем, стабилизаторами, добавками, пластификаторами и т. Д.) При определенной скорости перемешивания. Эти растворимые пластмассы заливаются в форму или на движущуюся ленту, чтобы сформировать пленку, к которой применяется тепло с использованием зон контроля нагрева для предотвращения образования пузырей. Скорость испарения растворителя обратно пропорциональна квадрату толщины. Для снижения затрат и соблюдения нормативных требований используются системы регенерации растворителей, которые обладают взрывобезопасной защитой.Существуют также системы, в которых используются растворы растворителей на водной основе, такие как пластик на основе поливинилового спирта.
Для центробежного литья можно использовать пластмассовые формы, такие как силикон, для производства изделий с жесткими допусками, высокой рентабельности и ограниченного производства из различных материалов. В этом процессе используется легко регулируемая центробежная сила для впрыскивания жидких термореактивных пластиков в круглую дискообразную эластомерную форму под давлением, полностью и быстро заполняя полости формы.
Простая немеханическая версия реактивного литья под давлением (Глава 12) или жидкостного литья под давлением — это литье из пенопласта.Вспенивающие компоненты заливаются в полость формы, которая обычно нагревается (Глава 8).
Используются различные технологии литья под давлением. В комплекте есть связующие на пластиковой основе, смешанные с песком. Производятся различные типы форм и стержней, в том числе без выпечки или холодного ящика, горячего ящика, скорлупы и сушеные в печи. Обычные связующие — фенольные, фурановые и термореактивный полиэстер. Существует литье корпуса литейного производства, также называемое литьем из сухой смеси. Это тип процесса, используемый в литейной промышленности, при котором смесь песка и пластика (фенола, термореактивного полиэстера и т. Д.)) помещается на предварительно нагретый металлический узор (получается половина формы), в результате чего пластик течет и образует тонкую оболочку поверх шаблона. Также используется жидкий пластик, предварительно покрытый песком. После непродолжительного отверждения при высокой температуре форма снимается с ее рисунка и соединяется с аналогичной половиной, полученной по той же технологии. Готовая форма готова для приема расплавленного металла. Выдувание жидкой смеси пластика и песка в стержневой ящик также позволяет получить формы для скорлупы.
Различные материалы пропитаны различными пластиками для улучшения характеристик и / или украшения.Он включает применение в качестве матрицы для армирующего волокна, создающего исключительно высокопрочные конструкции, насыщение цемента / бетона или дерева для повышения прочности и увеличения устойчивости к воздействию окружающей среды, заполнение слегка пористых металлов для их герметизации и т. Д. Степень пропитки или насыщения зависит от таких переменных, как в качестве используемого процесса, который включает литье, нанесение покрытия, экструзию, сушку в башне и т. д. с вакуумом в подложке или без него.
Процесс струйной пропитки — это процесс, связанный с литьем, заливкой и инкапсулированием термореактивного пластика, где также используется жидкий реактивный пластик с низкой вязкостью для обеспечения струйной пропитки.Например, катализированный пластик капает на катушку электрического трансформатора. Капиллярное действие втягивает жидкость в свои отверстия с достаточно медленной скоростью, чтобы воздух мог уйти, когда он вытесняется жидкостью. После полной пропитки деталь подвергается нагреву для отверждения пластика.
Вариант литья известен как жидкостное литье под давлением (LIM) и включает в себя дозирование, смешивание и дозирование жидких компонентов, а также непосредственный впрыск полученной смеси в полость формы, которая зажимается под давлением.В этом процессе литья жидкость впрыскивается под давлением, которое намного меньше, чем при обычном литье под давлением (главы 4 и 16). Упрощенный вид этого процесса литья показан на рисунке 11. 1. Для более точного смешивания доступно оборудование, такое как схема, показанная на рисунке 11.2.
Рисунок 11.1. Пример процесса литья под давлением
Рисунок 11.2. Пример более точного смешивания компонентов для литья под давлением
LIM можно также назвать реакционным литьем под давлением (RIM).Этот процесс LIM включает в себя дозирование, смешивание и дозирование двух жидких пластиковых составов. Этот состав направляют в закрытую форму. Его можно использовать для герметизации электрических и электронных устройств, декоративных украшений, медицинских устройств, автозапчастей и т. Д. Он отличается от реактивного литья под давлением (RIM), где используется механическое перемешивание, а не ударный смеситель высокого давления. Промывка смеси в конце цикла легко выполняется автоматически. Используемые пластмассы включают силиконы, акрил и т. Д.Во избежание засорения оборудования для впрыска жидкости пластиком рекомендуется использовать сопло с подпружиненным штифтом. Пружинная нагрузка позволяет вам установить давление так, чтобы оно было выше, чем давление внутри цилиндра экструдера, тем самым сохраняя порт чистым и открытым.
Что такое литье металла? Типы литья металла
Отливка металла определяется как процесс, при котором расплавленный металл заливают в форму, которая содержит полую полость желаемой геометрической формы, и ему дают остыть с образованием затвердевшей детали.Термин « отливка » также используется для описания детали, изготовленной в процессе литья, возраст которого составляет 6000 лет. Исторически он использовался для изготовления сложных и / или крупных деталей, которые было бы сложно или дорого производить с использованием других производственных процессов.
Рисунок 1. Отливка металла В первую очередь, отливка дает слитков и формы . Слиток представляет собой отливку простой формы, предназначенную для дальнейшей обработки, такой как экструзия металла, ковка и т. Д. Фигурное литье предназначено для отливок, близких к конечной или конечной, для получения сложных геометрических форм, которые ближе к конечной детали.
Металлическое литье можно разделить на две группы по основному характеру конструкции кристаллизатора. то есть одноразовая форма и постоянная отливка . В дальнейшем его можно разделить на группы в зависимости от материала выкройки.
- Расходная форма
- Постоянный узор
- Литье в песчаные формы
- Гипсовая лепнина
- Форма корпуса
- Керамическая форма
- Выкройка расходная
- Постоянный узор
- Перманентная форма
Перед выбором подходящей металлической отливки для данной конструкции инженерного изделия необходимо учитывать следующие факторы.
- Форма и размер детали
- Требуемое количество
- Требуемый допуск
- Материал
Отливка в сменную форму
Отливка в сменную форму, как следует из названия, использует временную форму одноразового использования для производства окончательной отливки, так как форма будет сломана, чтобы получить отливку. Эти формы обычно изготавливаются из таких материалов, как песок, керамика и гипс. Обычно их склеивают с помощью связующих веществ, называемых связующими, для улучшения их свойств.Сложные и сложные геометрические формы можно отливать с использованием одноразовых литейных форм.
Рисунок 2: алюминиевый сплав a356, рама копира, гипсовая форма, отливка из алюминия (credit_link)Отливка в постоянную форму
Иногда называемое отливкой в формы длительного пользования, для непрерывного литья в формы используются постоянные формы, которые повторно используются после каждого производственного цикла. Хотя постоянное литье в формы позволяет получать повторяемые детали из-за повторного использования одной и той же формы, с ее помощью можно производить только простые отливки, поскольку для удаления отливок необходимо открывать форму.
Рисунок 3. Отливка в неразъемную форму (кредит — Alibaba)Отливка в композитную форму
Как следует из названия, для производства отливок используются как одноразовые, так и многоразовые литейные формы. Обычно к ним относятся такие материалы, как песок, дерево, графит и металл.
Рис. 4. Отливка из композитных материалов (кредитная карта — highwell-china).Ступени литья металла
- Изготовление выкройки — Реплика отливаемой детали изготавливается из подходящего материала, такого как дерево, металлопластик или гипс.
- Изготовление пресс-форм — Изготовление пресс-форм — это многоступенчатый процесс, в котором шаблоны и стержни используются для создания пресс-формы. Тип и способ изготовления форм будут различаться в зависимости от типа отливки металла. Например, для литья в песчаные формы используется песок внутри опоки для создания форм, а для литья под давлением используются формы из закаленной инструментальной стали.
- Плавление и разливка металла — Жидкость затем плавится и выливается в полость формы под действием силы тяжести или высокого давления. Затем отливке дают затвердеть, прежде чем отливки будут извлечены из формы.Опять же, удаление литой детали будет зависеть от типа отливки металла.
- Последующая обработка — На этом заключительном этапе отлитый металлический объект извлекается из формы, а затем зачищается. Во время зачистки предмет очищается от формовочного материала, удаляются неровности.
Элементы литниковой системы
Одним из наиболее распространенных процессов литья металлов является литье в песчаные формы, форма которого состоит из двух половин. Содержащаяся внутри коробки, называемой фляжкой, верхняя половина называется колпачком, а нижняя половина — сопротивлением.Как показано на изображении (Рисунок 5) ниже, колба также разделена на две половины. Линия, разделяющая две половинки, называется линией разделения.
Рис. 5 Затворная система для металлического литья (источник: Groover (2010))Затворная система — это канал или путь, по которому расплавленный металл течет в полость. Как показано выше, литниковая система состоит из разливочного стакана и нижнего литника, через который металл попадает в желоб, ведущий в основную полость. Разливочная чашка сводит к минимуму разбрызгивание и турбулентность, когда металл протекает через литник, который сужается для облегчения потока.Большая часть отливки подвержена усадке во время охлаждения, и для минимизации проблемы усадки используется стояк. Подъемник — это простой резервуар в форме, который подает расплавленный материал к участкам усадки для компенсации его затвердевания. Есть четыре различных типа стояков, а именно. верхний подступенок, боковой подступенок, жалюзи и открытый подступенок.
Пригодность материала
Хотя можно использовать почти все металлы, наиболее распространенными являются железо, сталь, алюминий, магний и сплавы на основе меди, такие как бронза.
Цинк, алюминий, магний и латунь широко используются при литье под давлением, тогда как алюминиевый сплав, латунный сплав, чугун и литая сталь являются очень популярными материалами для литья под давлением.
Типовое применение
Почти все технические изделия, которые мы используем, от стиральных машин до сверл для колонн, от автомобилей до велосипедов, производятся из металлических деталей, которые, скорее всего, будут изготавливаться с использованием одного из процессов литья металла. Этот старинный производственный процесс со временем повысил точность и допуски.
Как правило, отливки используются для изготовления блоков двигателей автомобилей, коленчатых валов, корпусов электроинструментов, таких как сверлильные станки, детали сантехники, лопатки турбин, металлические статуи, некоторые шестерни и корпуса коробок передач.
Как и в случае с любым другим производственным процессом, базовое понимание процесса, лежащих в его основе научных данных, его плюсов и минусов имеет важное значение для производства недорогих качественных инженерных продуктов.
Преимущества металлического литья
- Металлическое литье позволяет изготавливать изделия сложной формы
- Такие детали, как внутренние полости или полые секции, достигаются легко
- Крупногабаритные детали можно изготавливать в цельнолитом виде
- Материалы, которые сложно или дорого производить с использованием других производственных процессов, можно отливать.
- По сравнению с другими производственными процессами, литье для средних и крупных партий дешевле
- Почти все металлы можно отливать
- Форма, близкая к конечной, часто без постобработки или с очень незначительной постобработкой
По указанным выше причинам литье металла является одной из важных технологий изготовления формы сетки.К другим относятся ковка чистой формы, штамповка листового металла, аддитивное производство и литье металла под давлением.
Недостатки металлического литья
- Относительно грубая обработка поверхности и, следовательно, более широкий допуск должен быть разрешен и не подходит для стыковки интерфейсов
- Металлическое литье, такое как кожух, имеет ограничения по размеру и рисунку
- Изготовление выкроек требует много времени и средств, хотя в последнее время для изготовления пресс-форм используются такие процессы аддитивного производства, как струйное распыление связующего.
- Литье под давлением может быть очень дорогим для малых и средних партий из-за высокой стоимости штампа
- Размер детали и выбор материала зависят от выбранного процесса литья.Например, для отливок в постоянные формы можно использовать только цветные металлы
Список литературы и рекомендуемая литература
- Били П. (2001). Литейная технология (второе издание). Оксфорд: Баттерворт Хайнеманн.
- Калпакчян, С., & Шмид, С. Р. (2009). Производство и технология (шестое издание). Лондон: Пирсон.
Глоссарий терминов — Boose Aluminium
Глоссарий терминов
Старение
Изменение свойств металлов и сплавов, которое происходит медленно при комнатной температуре и быстро наступает при более высоких температурах.Изменение металла или сплава, при котором его структура восстанавливается из нестабильного состояния, вызванного закалкой, закалочным старением или холодной обработкой, деформационным старением. Изменение в составе состоит. Изменение свойств часто, но не всегда, происходит из-за фазового перехода, выделения, но никогда не связано с изменением химического состава металла или сплава.
Обратная тяга
Обратный конус от заданного направления вытяжки из шаблона или стержневого ящика; предотвращает удаление рисунка из формы без повреждения формы.
Слепой стояк
Подъемник не открывается в атмосферу или не достигает внешней части формы.
Удар
Дефект литья из-за улавливания газа в расплавленном или частично расплавленном металле.
Выдувное отверстие
Дыра или пустота, оставшаяся в отливке из-за захваченного воздуха или газов
Твердость по Бринеллю
Значение твердости металла по произвольной шкале, представляющей кг / мм2, определенное путем измерения диаметра отпечатка, нанесенного шариком заданного диаметра, приложенным под известной нагрузкой.Значения выражены в числах твердости по Бринеллю, BHN
Пряжка
Выпуклость большой плоской поверхности отливки; в литье по выплавляемым моделям из-за отслаивания покрытия методом окунания от модели. Дефект на поверхности отливки в виде вмятины в результате расширения струпа. Вмятина в отливке, возникшая в результате расширения песка, может быть названа началом дефекта расширения.
Пригоревший на песке
Неправильное название, обычно указывающее на проникновение металла в песок, в результате чего смесь песка и металла прилипает к поверхности отливки.На поверхности отливки прилипает песок, который очень трудно удалить. Это состояние может быть связано с мягкими формами, плохим уплотнением песка, недостаточным покрытием формы (графитовой) краской или высокой температурой заливки.
Литая пластина
Металлическая пластина, обычно алюминиевая, отлитая с рисунком выступа с одной стороны и рисунком сопротивления с другой.
Процесс, при котором расплавленный металл заливают в форму и дают возможность затвердеть.Акт заливки металла.
Кастинг (существительное)Металлический предмет, полученный заливкой расплавленного металла в форму. Металлический профиль, за исключением ворот и подступенков, полученный в результате заливки металла в форму.
Схема отливки
Проверка размеров по применимым чертежам и спецификациям.
Венчик
Металлические опоры или распорки, используемые в формах для поддержания стержней или частей формы, которые не являются самонесущими.Эти размеры сохраняются в венцах в процессе литья, а затем они становятся частью самой отливки, поскольку расплавленный металл затвердевает вокруг венчика и превращает его в готовую отливку
Охлаждение
Металлические, графитовые или углеродные блоки, которые вводятся в форму или стержень для локального увеличения скорости отвода тепла во время затвердевания и уменьшения дефектов усадки, включая направленное затвердевание и уменьшение дефектов усадки. Устройство, используемое для охлаждения изолированной области формы.
Дроссель
Ограничение в литниковой системе, которая контролирует расход металла в полость формы.
Дроссель или первичный дроссель
Часть литниковой системы, которая в наибольшей степени ограничивает или регулирует поток металла в полость формы
Close Over
Операция опускания части формы на выступающую часть, например стержень.
Процесс холодного ящика
Быстрый процесс изготовления стержней, который не требует применения тепла для отверждения стержней.Отверждение сердцевины осуществляется путем химической реакции, а не путем обычного обжига. В песок, из которого сделан сердечник, добавляется фенольная смола. Эта смола вступает в химическую реакцию при воздействии ускорителя, обычно активного органического газа, и очень быстро затвердевает, образуя органическую связь в основном песке. Эта реакция происходит при комнатной температуре и не требует специальных ядерных ящиков или оборудования. Кроме того, поскольку связка является органической, песок легко разрушается во время встряхивания и может быть легко извлечен из отливки.
Cold Lap
Морщинистые отметины на поверхности слитка или отливки от начального промерзания поверхности.
Верхняя половина горизонтально разделенной формы. Верхняя или самая верхняя часть колбы, формы или выкройки.
ЯдроВставка из связанного песка, помещенная в форму для образования поднутрения или полого участка в отливке, который не может быть сформирован по рисунку. Сердечник часто используется для создания отверстий и полостей различной формы в отливке.Формованное тело из песка, которое формирует внутреннюю часть отливки, а также выбранные внешние особенности.
Core Box
Форма, в которой формируется стержень. Коробка из дерева, металла или пластика, полость которой имеет форму желаемой сердцевины, которая должна быть в ней сделана.
Ребро сердечника
Дефект отливки, углубление в отливке, вызванное ребром на сердечнике, которое не было удалено перед установкой сердечника, или пастой, просочившейся между стыками
Поплавок сердечника
Дефект литья, вызванный перемещением сердечника к верхней поверхности кристаллизатора в результате плавучести сердечника в жидкой стали, что приводит к отклонению от заданной толщины стенки.
Core Shift
Дефект, возникающий из-за смещения стержня из его надлежащего положения в полости формы. Отклонение от указанных размеров секции с сердечником из-за изменения положения сердечника или несоосности сердечников при сборке
Выступ на шаблоне, который оставляет отпечаток в форме для поддержки сердечника.
Сдавливание
Дефект литья, например коробление или разрыв части формы из-за неправильного совмещения при закрытии.Также имеется вмятина на поверхности отливки из-за смещения песка в кристаллизаторе, когда форма закрыта.
Раздавленная полоса или буртик
Вмятина на линии разъема шаблонной пластины, которая обеспечивает хороший контакт выступа и сопротивления за счет образования песчаного гребня, который прижимается к другой поверхности формы или стержня
Дегазация
Обычно химическая реакция, возникающая в результате добавления соединения к расплавленному металлу для удаления газов из металла.Часто в этой операции используются инертные газы.
Грязь
Неограниченный термин, относящийся к любому постороннему материалу, попадающему в полость формы и обычно образующему дефект на поверхности отливки
Грязеуловитель
Колодец, используемый в литниковой системе для улавливания первого вылитого металла, который может содержать грязь или нежелательные частицы (неэффективно).
Дисперсная усадка
Небольшие усадочные полости, рассредоточенные по отливке, которые не обязательно являются причиной брака.
Дюбель
Штифт, используемый между частями разделенных шаблонов или стержневых ящиков, чтобы находить и удерживать их на месте, правильно совмещая
Нижняя или нижняя часть формы, шаблона или опоки.
Чертеж
Термин, используемый для закалки, чтобы удалить узор из формы, как внешний дефект сжатия на поверхности формы. Для снятия выкройки с формы
Падение (выпадение)
Дефект литья, вызванный падением песка с выступа или другой выступающей части.
Отводной затвор
Термин для заливочного затвора или желоба, ведущего непосредственно в верхнюю часть формы.
Окалина
Оксиды металлов и прочая накипь на поверхности расплавленного металла или в металле или сплаве (в основном термин, связанный с цветными металлами).
Dye Penetrant
Penetrant используется для обнаружения трещин, в который добавлен краситель, чтобы сделать его более заметным при нормальном или черном освещении. При нормальном освещении краситель обычно красный и нефлуоресцентный.При черном освещении краситель флуоресцентный и имеет желто-зеленый цвет.
Удлинение
Мера пластичности материала. В процентах он указывает на величину деформации материала до остаточной деформации. Чем выше число, тем пластичнее. См. Пластичность.
Расширение, песок
Увеличение размеров песка в условиях повышенных температур.
Скругление
Вогнутая угловая деталь, часто предварительно отформованная полоса кожи или воска, используемая в литейных узорах, используемых на пересечении двух поверхностей для закругления острого угла.
Фильтр
Фильтрация посторонних газов в отливке, при отливке отливки.
Ребро
Тонкий выступ металла отливки, образовавшийся в результате несовершенного соединения пресс-формы или стержня. См. Литье, сердечник.
Чистовая обработка (станок)
Количество металла, разрешенного к обработке.
Тонкое ребро или металлическая перегородка, выходящая из отливки вдоль линии стыка из-за того, что выступ и сопротивление не совпадают полностью или если стержень и отпечаток стержня не совпадают
Flat Back
Шаблон с плоской поверхностью на стыке формы.Он полностью находится внутри бугеля, и этот стык литейной формы представляет собой плоскую поверхность. См. «Копировать», «Перетащить», «Плесень», «Шаблон».
Flux
Любое вещество, используемое для термоядерного синтеза. Также любой материал, который восстанавливает, окисляет или разлагает примеси, так что они уносятся в виде шлаков или газов.
Литейный ковш
Емкость для удержания расплавленного металла и подачи его от вагранки к изложницам.
Отверстия для газа
Полости округлой формы, вызванные образованием или скоплением газа или захваченного воздуха в отливке; отверстия могут быть сферическими, уплощенными или удлиненными.
Пористость по газу
Состояние, существующее в отливке, вызванное улавливанием газа в расплавленном металле или газами литейной формы, выделяющимися во время разливки отливки.
Ворота
В частности, точка, в которой расплавленный металл входит в литейную полость. Иногда используется как общий термин для обозначения всей сборки соединенных колонн и каналов, несущих металл от верха кристаллизатора к той части, которая формирует собственно литейную полость. Этот термин также применяется к деталям узора, которые образуют проходы, или к металлу, который их заполняет.
Полный комплект заслонок, направляющих и литников, через которые расплавленный металл течет в полость кристаллизатора. См. Полость, ворота, формы, направляющие, литники.
Зеленая проницаемость
Свойство формованной массы песка в закаленном состоянии, которое является мерой ее способности пропускать через нее газы.
Green Strength
Прочность на разрыв (сжатие, сдвиг, растяжение или поперечное) смеси отпущенного песка при комнатной температуре.
Шлифование
Удаление упоров ворот, ребер и других выступов на отливках с помощью абразивного круга. См. Литье, ворота, ласты.
Сопряжение из твердого песка (стыковочная пластина)
Тело из песка, форма которого соответствует линии разъема, на которую укладывается узор, для создания формы. Песок становится твердым, добавляя льняное масло и глет, портландцемент и т. Д. См. Match.
Твердость
Устойчивость материала к вдавливанию, измеренная такими методами, как Бринелля, Роквелла и Виккерса.Термин твердость также относится к жесткости материала или его устойчивости к царапинам, истиранию или порезам. См. BHN, Твердость по Бринеллю, алмаз Виккерса .
Твердость / по Бринеллю
Относительный термин, относящийся к сопротивлению металла пластической деформации от заданной стандартной нагрузки, приложенной к стандартной пробивной головке. См. BHN, Твердость по Бринеллю, алмаз Виккерса.
Heat
Отдельная шихта металла, используемая для заливки непосредственно в полости формы; заезд может быть полностью частью основной заезды. См. Полость пресс-формы.
Комбинация операций нагрева и охлаждения, рассчитанных по времени и применяемых к металлу или сплаву в твердом состоянии таким образом, чтобы обеспечить желаемые свойства.
Горячие точки
Области повышенной массы, обычно обнаруживаемые на стыке секций.
Горячий разрыв
Излом неправильной формы в отливке, образовавшийся до завершения затвердевания металла в результате напряжений, возникающих из-за крутых температурных градиентов внутри отливки во время затвердевания и слишком большой жесткости материала стержня или формы. См. Ядро, затвердевание.
Оттиск
Полость в штампе для литья под давлением или в форме. См. Полость, плесень.
Включения
Частицы шлака, огнеупорных материалов, песка или продуктов раскисления, задержанные в отливке во время затвердевания. См. Грязное литье, затвердевание.
Ingates
Каналы, по которым расплавленный металл поступает в полость кристаллизатора. См. Выход .
Слиток
Отливка для последующей ковки или горячей обработки. Также форма используется для удобной обработки чугуна, алюминия и других товарных металлов. то есть Свиньи.
Вставка
Деталь, обычно изготавливаемая из металла, которая помещается в форму и может стать неотъемлемой частью отливки. См. Литье, Форма.
Изолирующая гильза
Полые цилиндры или гильзы из гипса, диатомовой земли, перлита, вермикулита и т. Д.Размещается в форме в местах литников и стояков для уменьшения потерь тепла и скорости затвердевания содержащегося в них металла. См. Стояк, литник.
Инвест, Core Invest
Выбив
Для удаления песка и отливок из опоки
Испытание на проникновение жидкости
Метод неразрушающего контроля, подходящий для оценки целостности поверхности немагнитных и ферромагнитных деталей.
Свободный элемент
Часть выкройки, прикрепленная таким образом, что остается в форме и удаляется после того, как основа выкройки будет нарисована.При литье под давлением — тип сердечника (который образует поднутрения, расположенный внутри штампа, но не прикрепленный к нему и расположенный таким образом, чтобы его можно было выталкивать вместе с литьем под давлением, из которого он извлекается и повторно используется для того же назначение. См. Core Box, Pattern.
Чистовая обработка станка (заготовка станка)
Припуск припуска на поверхности шаблона для обработки отливки до требуемых размеров
Master Pattern
Оригинальный образец, предназначенный для изготовления отливок, которые затем используются в качестве металлических образцов. См. Кастинг.
Матричная пластина
Металлическая или другая пластина, на которой рисунки, разделенные по линии разъема, крепятся вплотную к литниковой системе, образуя единое целое.
Проникновение металла
Дефект на поверхности отливки, который выглядит так, как будто металл заполнил пустоты между песчинками, не смещая их.
Микропористость
Чрезвычайно мелкая пористость в отливках, вызванная усадкой или выделением газа и проявляющаяся на рентгенографической пленке в виде пятен. См. Микроусадка.
Микроусадка
Очень мелкодисперсная пористость, возникающая в результате междендритной усадки, разрешается только с помощью микроскопа; может быть виден на рентгенограммах в виде пятен. Травление показывает, что они возникают на пересечении сходящихся направлений дендритов.
Микроструктура
Структура и характерное состояние металлов, выявленные на шлифованном и полированном (протравленном или нетравленом) образце при увеличении более 10 диаметров. См. Микросекцию.
Misrun
Обозначает неровность поверхности отливки, вызванную неполным заполнением формы из-за низкой температуры заливки, противодавления газа из-за недостаточной вентиляции модуля и недостаточной вентиляции.
Обычно состоит из верхней и нижней части, сделанной из песка, металла или любой другой паковочной массы, которая содержит полость, в которую заливается расплавленный металл для получения отливки определенной формы и очертания. См. Полость для пресс-формы .
Полость формы
Оттиск в форме, полученный путем удаления шаблона. Он заполнен расплавленным металлом, чтобы сформировать отливку. Затворы и стояки не считаются частью полости формы. См. Литье, Ворота, Подступенки.
Сдвиг пресс-формы
Дефект отливки, возникающий, когда две полости в опорной и опорной формах не совпадают должным образом. См. Полость, полость пресс-формы, колпачок, перетаскивание.
Формовочная машина
Ручная или пневматическая машина, на которой изготавливаются формы и которая утрамбовывает песок путем сжатия или тряски, или и того, и другого.
Формовочный песок
Смесь песка и глины, пригодная для изготовления форм.
Пески, содержащие более 5% природной глины, обычно от 8 до 20%. См. Формовочный песок на естественной связке.
Muller
Тип литейно-песчано-смесительной машины. См. Литейный песок.
Mulling
Тщательное перемешивание песка, воды и связующих ингредиентов для получения темперированного готового к использованию формовочного или стержневого песка. См. Core Sand.
Nobake Binder
Синтетическое связующее для песка на жидкой смоле, которое полностью затвердевает при комнатной температуре и обычно не требует обжига, используется в процессе холодного отверждения. См. Процесс холодного отверждения.
Формы / стержни, изготовленные из связанного смолой песка для отверждения воздуха. Также известен как процесс схватывания на воздухе, потому что формы оставляют для затвердевания при нормальных атмосферных условиях. См. Core, Mold.
Неразрушающий контроль (инспекция, NDT)Испытания или осмотр, не разрушающие проверяемый или проверяемый объект.
Цветные металлы
Отрицательный термин относится к сплаву, в котором преобладающим металлом или растворителем не является железо. См. Сплав.
Открытый стояк
Подъемник, верх которого открыт для атмосферы через верх формы. См. Стояк.
Окисление
Любая реакция, при которой элемент реагирует с кислородом
Шов, разделительная линия, где форма отделяется, чтобы можно было удалить узор
Линия разделения
Линия на шаблоне или отливке, соответствующая разделению между верхней и нижней частями песчаной формы.Стык, в котором пресс-форма отделяется, чтобы можно было удалить узор. См. Литье, Копировать, Перетащить, Плесень, Шаблон.
Оригинал, используемый как форма для изготовления дубликатов. Размеры шаблона немного увеличены, чтобы противодействовать усадке отливки при ее затвердевании и охлаждении в форме. Хотя выкройки могут быть выполнены как одно целое, сложная отливка может состоять из двух или более частей. Узор может быть сделан из дерева, пластика, металла или другого материала. См. Литье, форма, затвердевание.
Черновой вариант шаблона
Конус, допускаемый на вертикальных поверхностях шаблона, чтобы облегчить извлечение шаблона из формы или штампа.
Форма Усадка
Припуск на усадку, сделанный для всех моделей, чтобы компенсировать изменение размеров, когда затвердевшая отливка охлаждается в кристаллизаторе от температуры замерзания до комнатной температуры. Рисунок увеличивается за счет величины усадки, характерной для конкретного металла в отливке, и величины возникающего в результате сжатия.Правила или шкалы доступны для использования. Также известно как правило усадки
Узор, разделенный
Узор обычно состоит из двух частей, иногда более чем из двух.
Модельер (и)
Мастер, занимающийся изготовлением литейных моделей из дерева, пластика или металлов, таких как алюминий, латунь и т. Д. См. Образец.
Peen
Прокалывающее действие, достигаемое ударом металлической дроби, часто используется для улучшения усталостных свойств за счет сжатия поверхности.Также маленький конец молотка формовщика.
Проницаемость
Свойство материала формы пропускать газы. Свойство песчаных форм, позволяющее пропускать газы.
Физические свойства
Свойства вещества, такие как плотность, электрическая и теплопроводность, расширение и удельная теплоемкость. Этот термин не следует использовать как синоним «механические свойства».
Точечное отверстие
Небольшое отверстие под поверхностью отливки. См. Кастинг.
Карман
Песок, окруженный расплавленным металлом со всех сторон, кроме одной.
Неправильность отливок, проявляющаяся в виде раковин и усадочных раковин.
Пористость (выдувные отверстия)
Отверстия в отливке из-за газов, захваченных в кристаллизаторе, реакции расплавленного металла с влагой в формовочном песке или несовершенного сплавления венчиков с расплавленным металлом. (Поверхностная пористость может быть вызвана перегревом литейной формы или лицевых панелей, но ее не следует путать с включениями песка.) См. Выдувное отверстие, выдувное отверстие, включение, формовочный песок.
Заливка
Заполнение формы расплавленным металлом. Подача расплавленного металла из печи в ковш, из ковша в ковш или из ковша в изложницы. См. Формы, Ковш.
Разливочный бассейн, чашка, колодец
Расположен на верхней части литника или нижней части. Эта часть ворот.
Первичный штуцер (штуцер)
Та часть литниковой системы, которая в наибольшей степени ограничивает или регулирует поток металла в полость формы. См. Ворота.
Удаление воздуха
Удаление воздуха и других нежелательных газов из печей или нагревательных ящиков.
Закалка
Быстрое охлаждение закалки; обычно достигается погружением объекта, который необходимо закалить, в воду, масло или растворы солей или органических соединений в воде.
Радиографический контроль
Проверка прочности отливки путем изучения рентгенограмм, сделанных на различных участках или всей отливки.
Радиографический контроль
Использование рентгеновских или гамма-лучей при изучении внутренней структуры объектов для определения их однородности.
Утрамбованный сердечник
Сердечник прикреплен к шаблону и утрамбован в форме, где он остается при извлечении шаблона
Оснастка
Затворы, подступенки, незакрепленные детали и т. Д., Необходимые на шаблоне для создания звукового литья. См. Литье, Ворота, Подступенок, Отдельные детали, Узор.
Резервуар с расплавленным металлом, из которого отливка может вытягиваться для компенсации усадки, возникающей при затвердевании металла.См. Feeder.
Контакт стояка (Контакт ворот)
Соединительный проход между стояком и отливкой. См. Литье, стояк.
Подъемник, глухой
Подъемник, который не выходит за пределы верхней части выступа и полностью окружен песком; открылся в атмосферу с помощью ядра петарды.
Подступенок, открытый
Подъемник обычной формы, обычно расположенный в самой тяжелой части отливки и проходящий по всей высоте уступа.
Riser-Gating
Практика спуска металла для разливки через стояк для обеспечения направленного затвердевания.
Бегунок
Деталь трапециевидной формы, которая проходит горизонтально к полости формы и соединяет основание литника с воротами . См. Gate, Sprue.
Биение
Металл протекает через дефект формы.
Песок
При литье металла — рыхлый гранулированный материал с высоким содержанием SiO2, образующийся в результате разрушения породы.Название песок относится к размеру зерна, а не к минеральному составу. Диаметр отдельных зерен может варьироваться приблизительно от 6 до 270 меш. Большинство формовочных песков состоят в основном из минерального кварца (кремнезема). Причина этого в том, что песка много, он тугоплавкий и дешевый; Различные пески включают циркон, оливин, хромит, CaCO3, черный песок (зерна лавы), минералы титана и другие.
Пескоструйная очистка
Пескоструйная обработка сжатым воздухом (или паром).Он используется для очистки отливок, резки, полировки или украшения стекла или других твердых материалов, а также для очистки фасадов зданий и т. Д.
Литье в песчаные формы
Отливки из металла, производимые в песчаных формах. См. Кастинг.
Песочные отверстия
Полости неправильной формы и размера, на внутренней поверхности которых отчетливо виден отпечаток гранулированного материала.
Включения песка
Полости или дефекты поверхности отливки, вызванные вымыванием песка в полость формы .См. Полость для плесени.
Пористость песка
Объем порового пространства или складок в песке. (Не синоним проницаемости).
Лом
Любой металлолом, расплавленный, обычно с подходящими добавками, для производства отливок.
Металлолом
Металл для переплавки; включает списанные в лом изделия, изготовленные оборудованием, такие как рельсы или конструкционная сталь, и бракованные отливки (металл, подлежащий переплавке, отливки, которые необходимо переплавлять).
Шов
Поверхностный дефект отливки, связанный, но в меньшей степени, чем с холодным затвором; гребень на поверхности отливки, вызванный трещиной на лицевой поверхности формы. См. Холодный затвор.
Shell Process
Процесс, при котором не содержащий глины кварцевый песок, покрытый термореактивной смолой или смешанный со смолой, помещается на нагретый металлический узор на короткий период времени с образованием частично затвердевшей оболочки. Основная масса песчаной смеси внутри получившейся оболочки удаляется для дальнейшего использования.Затем узор и оболочка нагревают дополнительно для затвердевания или полимеризации смеси смола и песка, и оболочка удаляется с узора. Часто ядра оболочки изготавливаются с использованием процесса Hot Box. См. Процесс Hot Box.
Дефект литья, возникший в результате несоответствия сопротивления и сопротивления. Иногда бывает Core Shift, который также приводит к бракованному литью. См. Core Shift.
Дробь
Металлический абразив, обычно используемый для очистки литейных поверхностей.При литье под давлением это фаза цикла литья, когда расплавленный металл вдавливается в матрицу.
Дробеструйная очистка (дробеструйная обработка)
Процесс очистки отливок с использованием металлического абразива (дроби или дроби), приводимого в движение центробежной или воздушной силой.
Усадка
Разница в объеме жидкого металла и твердого металла или пустота (усадочное отверстие), оставшаяся в отливке из-за этого.
Усадочное отверстие
Полость в отливке из-за недостаточной подачи металла.
Усадка
Разница в объеме жидкого и твердого металла в данной полости. Усадка металла в форме при затвердевании. Этот термин также используется для описания дефекта отливки, то есть усадочной полости. Это происходит из-за плохой конструкции, недостаточной подачи металла или недостаточной подачи.
Трещины от усадки
Трещины, которые образуются в металле в результате разрыва зерен за счет сжатия до полного затвердевания. См. Затвердевание.
Кремнеземистый песок
Песок с минимальным содержанием кремнезема 95%, используемый для формования литейных форм.
Сердцевина плиты
Плоская сердцевина.
Включения шлака
Дефекты поверхности отливки, похожие на включения песка, но содержащие примеси из шихтовых материалов, кремнезема и глины, эродированных из огнеупорной футеровки, золы от топлива в процессе плавки. Также могут возникать реакции металл-тугоплавкость, происходящие в ковше во время разливки отливки. См. Включения.
Затвердевание
Процесс перехода металла (или сплава) из жидкого в твердое состояние.
Диапазон затвердевания
Только чистые металлы затвердевают или замерзают при одной определенной температуре. Сплавы содержат разные компоненты, которые затвердевают при разных температурах, и разные температуры от температуры первого компонента до температуры последнего и до замерзания компонента называются диапазоном затвердевания. См. Затвердевание.
Спектография
Процесс определения концентрации металлических компонентов в металле или сплаве по интенсивности волн определенной длины, генерируемой при термическом или электрическом возбуждении металла или сплава.
Разделенный узор
Рисунок, который разделен для удобства формования.
Литниковый канал
Вертикальный канал, по которому расплавленный металл от разливочного резервуара попадает в желоб.См. «Бегуны».
Давление сжатия
Давление, прикладываемое формовочной машиной для прижатия колбы с содержащимся песком к неподвижной выжимной головке или доске на формовочной машине.
Отжимная машина
Механическое, обычно пневматическое устройство, используемое для набивки песка в колбу. См. Flask.
Наклейка
Шишка на поверхности отливки, вызванная прилипанием части лицевой поверхности формы к шаблону. Также формовочный инструмент используется при формовании.
Strike Off (м. Операция по удалению излишков песка с верхней части стержневого ящика или опоки.
Чистота поверхности
Состояние или внешний вид поверхности отливки.
Вздутие
Дефект литья, состоящий в увеличении сечения металла из-за вытеснения песка давлением металла. См. Дефект.
Разрывы
Дефект вызван обратной тягой, повреждением рисунка или неровным рисунком.См. Дефект.
Испытательный стержень
Стандартный образец стержня, предназначенный для определения механических свойств металла, из которого он был отлит.
Термическое расширение
Увеличение линейных размеров и объема материала при изменении температуры.
Стяжной стержень
Стержень-стержень или стержнеобразная часть отливки добавлены для предотвращения деформации, вызванной неравномерным сжатием между отдельными элементами.
Допуск
Допустимое отклонение размера от номинального или желаемого значения.Минимальный зазор между сопрягаемыми частями.
Точки оснастки
Фиксированные позиции на литых поверхностях, используемые для привязки во время компоновки и обработки.
Выточка
Часть пресс-формы или штампа, требующая недостатка. См. Недостаток.
Прожилки
Дефекты поверхности отливок в виде прожилок или морщин, возникающие в результате трещин в песке из-за повышенных температур и чаще всего возникают в кернах.См. Отливка, сердечники, дефект.
Жилки
Несплошность на поверхности отливки, проявляющаяся в виде приподнятого узкого линейного гребня, который образуется при растрескивании песчаной формы или стержня из-за расширения песка во время заполнения формы расплавленным металлом. См. Дефект.
Вентиляционное отверстие
Небольшое отверстие или проход, через который газы могут выходить во время заливки формы. Его еще называют вентиляционным отверстием.
Вязкость
Сопротивление текучей среды течению, количественная характеристика отдельного вещества при данной температуре и других определенных внешних условиях.
Пустота
Усадочная полость, образующаяся в отливке во время затвердевания. См. Раздел «Отливка, полость, усадка, затвердевание».
Форма лучистой энергии с чрезвычайно короткой длиной волны, которая способна проникать через материалы, поглощающие или отражающие обычный свет. Рентгеновские лучи являются формой неразрушающего контроля.
Выход
Сравнение веса готовой отливки с общим весом металла, отлитого в форму. Значение, выраженное в процентах, указывающее отношение веса отливки к общему составу отливки и ее литниковой системы.
Предел текучести
Мера величины механического напряжения, которое материал может выдержать до того, как он деформируется необратимо.
Полное литье в форму | КИМУРА
История процесса литья в полную форму
Происхождение названия
Процесс литья в полную форму известен под множеством различных названий, включая литье по схеме испарения, процесс потери пены, процесс EPC и процесс FMC.
Литье в полную форму — это термин, который соответствует полым формам в методе деревянного моделирования, который характеризуется наличием пустого пространства внутри литейных форм.
История
Основной патент на процесс литья в полную форму, заявка на который была подана американцем Х. Ф. Шройером, был выдан в 1958 году. Метод сухого песка был изобретен Х.Б. Дитер и Т. Смит в 1964 году. В 1967 году А. Виттмозер и Хоффман из Германии изобрели магнитный метод литья.
Лицензия на основной патент на процесс полного литья в формы была приобретена немецкой компанией Gruenzweig & Hartmann (сокращенно G + H), производившей изоляционные материалы, в 1961 году.Виттмозер из RWTH Ахенского университета, который был назначен вице-президентом этой компании, стремился коммерциализировать эту технологию и распространить ее по всему миру. Виттмозер, по сути, стал отцом процесса полного литья в формы.
В Японии компания Mitsubishi Yuka Badische Co., Ltd. приобрела патентную лицензию у Full Mold International, компании, управляемой Виттмозером, примерно в 1965 году, после чего Mitsubishi Heavy Industries занялась технологическим развитием. В какой-то момент до 120 компаний принадлежали к группе предприятий, которые выполняли полный процесс литья в формы.В ноябре 1966 года KIMURA как компания стала членом этой семьи.
В то время процесс полного литья в формы давал такие низкокачественные продукты, что только пресс-формы для автомобилей могли в полной мере использовать его преимущества. Внезапная кончина Виттмозера, сыгравшего центральную роль в популяризации процесса полного литья в формы, в ноябре 1993 года заставила лицензионную группу прекратить деятельность, что, в свою очередь, побудило компании разработать процесс самостоятельно. Понятно, что процесс полного литья в формы осуществляется химическими производителями пенополистирола с целью расширения ассортимента изделий из пенополистирола.Во всем мире развернулись дебаты, чтобы определить, какой метод лучше: метод заливки сверху, одобренный Виттмозером, или метод заливки снизу, одобренный президентом Кимурой. В 1980 году срок действия основного патента истек. До этого момента процесс полного литья в формы в основном использовался для крупных отливок, таких как штампы пресса. Однако впоследствии процесс полного литья в форму стал применяться к более мелким изделиям, включая трубы нестандартной формы и автомобильные детали.
General Motors применила технологию полного литья для своих головок цилиндров из алюминиевого сплава в 1980 году, в то время как Ford и Fiat сделали то же самое для массового производства небольших изделий в 1982 и 1984 годах соответственно. Эти применения были в первую очередь основаны на методах формования, реализованных с помощью виброплиных формовочных машин, в которых использовался песок без связующих. Эту технологию чаще всего называют процессом потери пены. Примерно в то же время в Японии для массового производства небольших изделий был принят процесс полного литья в форму, что знаменует появление второй стрелы для процесса полного литья в форму.
Для крупномасштабных отливок процесс литья в полную форму с трудом распространился с точки зрения применения за пределы штампов пресса из-за проблемы остатков (которые остаются после сжигания пенополистирола), что является заметным недостатком этого метода. Тем не менее, процесс литья в полную форму, не требующий деревянных шаблонов, несомненно, является идеальным методом для производства отдельных отливок. С 1974 года мы пытаемся применить технологию полных форм к станкам и промышленному оборудованию и называем эту технологию процессом литья в полностью новую форму (сокращенно «new-FMC»).Поскольку эта новая технология FMC была нашей собственной запатентованной технологией и поскольку она была ограничена отдельными устройствами, она не могла стимулировать новый бум.
В 1987 году мы приняли метод изготовления полных моделей пресс-форм, основанный на использовании системы CAD / CAM. Это открыло новый путь для массового производства отливок. В итоге мы взяли на себя задачу массового производства отливок для станков путем применения процесса литья в полную форму. Эта технология была разработана для применения в композитных отливках станков и промышленного оборудования.
Система CAD / CAM, которая была принята для всего процесса изготовления модели пресс-формы в 1987 году, полностью изменила способ создания моделей впоследствии. Традиционно для создания выкройки сначала представляли пространство, которое должно занимать изделие, на основе его двухмерного чертежа, а затем создавали детали с помощью ленточных пил и других инструментов и собирали эти детали вместе. В соответствии с развитием компьютеров, процесс изготовления выкроек вручную уступил место процессу изготовления паттернов с использованием систем CAD / CAM.К 2002 году мы больше не делали выкройки вручную. Эта революция в процессе изготовления моделей открыла жизнеспособный путь к массовому производству отливок в формы.
Что такое металлическое литье и компоненты формы для литья металла
Получите из него хороший компонент, у вас есть что-то, называемое литниковой системой, это водопровод формы, вы можете думать об этом как о аналоге водопроводной системы, поэтому у вас есть разные проходы для разрыва формы, входящие в полость формы, и через час, которые позволяют проходить расплавленному металлу, и система вентиляции может на самом деле довольно сложная, потому что она контролирует скорость потока и способ, которым этот расплавленный металл проходит насквозь, и он должен иметь возможность проходить через весь этот расплавленный металл достаточно своевременно, чтобы делать две вещи: первая — заполнять полость формы без затвердевания до того, как вся форма затвердеет, средний сектор, а также не заливать его слишком быстро, чтобы в конечном итоге вы получаете сильную турбулентность, много воздуха, захваченного жидким металлом, и, возможно, получаете много воздушных карманов и пористость в готовой отливке, поэтому система вентиляции состоит из нескольких элементов, поэтому вы можете например, сливной бассейн или просто резервуар, который находится здесь вверху, резервуар и резервуар — это просто измерительное устройство, это измерительное устройство для потока металлов, поэтому тигель или ковш наливают в сливной резервуар, заполняя его. в нем дозируется расплавленный металл в форму.
Следующее, что входит в процесс литья, — это литник, вы можете рассматривать его как главную линию подачи в отливку или в форму. Он исходит из этого разливочного резервуара, опускается в литник, и именно здесь фактически начинается весь процесс литья, поскольку жидкий металл фактически начинает выходить в форму. Таким образом, он проходит через этот литник и попадает в то, что называется дросселем, который является просто еще одним механизмом, контролирующим скорость потока. Этот дроссель замедляет поток в середине, так что он не просто устремляется к вашему компоненту в полость формы с большим количеством воздуха, захваченного в нем, он помогает регулировать или замедлять скорость потока расплавленного металла. .
Следующий компонент, который у вас есть, — это бегунок, это проход к удаленному устройству, так что думайте об этом как о просто водопроводе, еще одной части, поднимающейся по трубопроводу, которая идет от штуцера и просто проходит через форму. и, в конечном итоге, доставить расплавленный металл туда, куда ему нужно. В других случаях у вас может быть несколько компонентов внутри формы, к каждой из которых должно быть несколько линий направляющих, поэтому, если думать об этом как о водопроводной системе, у вас есть что-то, называемое воротами.
Затвор — это просто порт или проход, который фактически входит в полость формы, поэтому это просто вход в полость формы, и иногда диаметр этого затвора контролируется и регулируется, если вам нужно замедлить или ускорить поток металла, поступающий в полость формы, но в первую очередь это просто вход в полость формы. Следующая часть — это сама полость пресс-формы, так что именно из нее получается конечный продукт, и обычно это специально разработанная деталь, имеющая определенные особенности, которые вам понадобятся при окончательном литье, возможно, у вас не будет всех конкретных отверстий или резьбовых соединений. секций, зазоров или окончательной отделки на нем, но это дает вам реальное литье, с которым вы собираетесь работать, и оттуда у вас есть конечный продукт в процессе литья.Как правило, это хорошая идея, особенно для более сложных частей со сложной геометрией, это то, что называется стояком, который представляет собой просто резервуар, в котором находится расплавленный металл, чтобы уменьшить усадку. Полость формы заполняется там могут быть некоторые тонкие участки стенки, могут быть другие области, которые вас немного беспокоит, когда расплавленный металл горячий, и этот расплавленный металл остывает, он сжимается, он сжимается, так что у вас есть это вещь, называемая стояком, которая специально разработана для охлаждения и затвердевания.Наконец, вы разрабатываете что-то вроде того, что может затвердеть на основе формы, а также общих сторон, поэтому он превращается в резервуар, и когда ваша середина и ваша отливка или полость вашей формы начинают сжиматься или остывать и сжиматься, это работает как резервуар для отправки расплавленного металла обратно в качестве засыпки для областей, которые могут иметь некоторые проблемы с усадкой, и это действительно единственная цель или основная цель стояка, другая его цель — он потенциально может выводить любые газы или, если есть какая-либо пористость, он может помочь вам избежать каких-либо незакрепленных или пустых карманов здесь, потому что это позволяет газам выходить, если они засыпаны расплавленным металлом, так что это другая вторичная цель подъема.
Без названия
Без названияБыстрая оснастка для литья металлов
Сценарий применения RT в литье в песчаные формы
Это один из основных процессов, используемых при производстве литых деталей. В этом процессе расплавленный металл заливается в одноразовую форму, сформированную из формовочного песка, содержащего связующее. Полость в песке сформирована с помощью узора. Узор, который имеет примерно такую же форму, что и настоящая отливка, является основным инструментом в процессе формовки из песка.Модели при литье в песчаные формы обычно изготавливаются из дерева, пластика или металла (поскольку материал рисунка определяет срок его службы, его выбор зависит от объема производства). Если литая деталь имеет внутренние полости или каналы, то в полость формы следует вставить песчаный стержень или стержни. Ящики для стержней, которые используются для производства песчаных кернов, являются вторым инструментом при литье в песчаные формы. Основные требования к оснастке для литья в песчаные формы:
- выкройки (а также стержневые ящики) должны быть выполнены с достаточной точностью;
- Материал выкроек (стержневых ящиков) должен обеспечивать им соответствующую технологическую прочность с точки зрения износостойкости и размерной стабильности.
Инструменты прямого действия
Теоретически все технологии RP позволяют создавать модели, которые после соответствующей отделки можно использовать непосредственно в качестве шаблонов при формовании из песка. LOM — это наиболее распространенное приложение, используемое для изготовления моделей для отливок очень больших размеров.
Отливка из серого чугуна и его прототипLOM |
Единственное слабое место бумажных шаблонов LOM и стержневых ящиков — их восприимчивость к влажности.Последние можно исправить, нанеся специальные покрытия или картины.
Инструмент для косвенного использования
Все модели, созданные с помощью RP, могут использоваться в качестве косвенного или промежуточного инструмента для формовки из песка. Например, как выкройки при производстве форм из силиконовой резины, которые, в свою очередь, используются для изготовления прочных пластмассовых моделей. Единственное ограничение здесь — размер модели.
Песочная формовка без патерна
Текущий прогресс, достигнутый в технологии SLS, позволяет спекать формовочный песок, покрытый смолой, отверждаемой ультрафиолетом.Это дает возможность создавать песчаные формы и стержни непосредственно на станке SLS. Оба производителя систем SLS, 3D Systems и EOS GmbH, производят системы с такой возможностью.
Сложный песчаный сердечник, сделанный путем лазерного спекания формовочного песка (3D-система) и фактическая отливка алюминия, изготовленная с использованием сердечника |
Формы и стержни из песка для лазерного спекания (система EOS, EOS S)
Блок рулевого управления | Гидравлический контроллер | Рабочее колесо |
Однако изготовление песчаных стержней или форм с помощью лазерного спекания занимает значительно больше времени, чем традиционные методы с использованием шаблонов и стержневых ящиков.Таким образом, изготовление форм без выкройки выгодно в случаях, когда:
- необходимо отливать всего одну или несколько отливок, а изготовление набора многоразового инструмента нерационально;
- Отливка настолько сложна, что изготовление формы и стержня по традиционной технологии чрезвычайно сложно или невозможно.
Схема применения RT в литье по выплавляемым моделям
В этом процессе используются одноразовые формы, изготовленные с использованием утраченного рисунка из воска или другого материала, который можно расплавить или сжечь.Этот потерянный узор погружают в огнеупорную суспензию, которая покрывает восковой узор и образует пленку. Затем оболочку сушат, и процесс погружения в суспензию и сушки повторяют до тех пор, пока не будет достигнута желаемая толщина оболочки. После этого плавление или выжигание убирают утраченный узор. Это приводит к форме, которую можно заполнить расплавленным металлом.
Инструментом в этом процессе является форма многоразового использования для разливки по утраченной модели. Эти формы традиционно изготавливаются из металла (обычно алюминия) в случае крупносерийного производства или из эпоксидной смолы или даже резины в случае среднего и мелкосерийного производства.
Инструменты прямого действия
Воск для литья под давлением можно впрыскивать в форму, созданную с помощью одной из технологий RP. Пример оснастки для литья по выплавляемым моделям, созданной на станке LOM, показан на рисунке ниже. Полости в половинках формы покрыты специальной краской для увеличения стойкости формы, кроме того, форма полностью изготовлена на установке RP.
Форма, полученная с помощью LOM, восковая модель по потерем и окончательная отливка |
Инструмент для косвенного использования
СозданныеRP объектов могут косвенно использоваться в процессах литья по выплавляемым моделям, например, в качестве эталонного шаблона для создания формы из силиконовой резины, которая может использоваться для небольших пазов изготовления восковых моделей.
Процесс без инструментов
Утраченные шаблоны могут быть изготовлены непосредственно на станках RP.
Системы RP, основанные на принципе FDM (а также машины SI), способны работать с традиционным воском для литья по выплавляемым моделям в качестве строительного материала. Следовательно, они нашли очень широкое применение в качестве систем изготовления утерянных образцов. Тем не менее, другие технологии RP также использовались для производства прямой утраченной модели.
Полимерные материалы, используемые в SLA, труднее выгореть, чем традиционные материалы, используемые для изготовления потерянных моделей.Эти материалы также имеют тенденцию к расширению и растрескиванию формы. Чтобы решить эти проблемы, шаблон, созданный SLA, состоит из полых тонких секций, которые при выгорании имеют тенденцию сминаться, а не расширяться.
Модель литья по выплавляемым моделям, созданная SLA, и собственно алюминиевая отливка |
Пластмассы, используемые в процессах SLS, также могут использоваться в качестве строительного материала для утраченных узоров.
Модель литья по выплавляемым моделям, полученная из SLS, и собственно алюминиевая отливка |
Модификация технологии LOM, разработанная специально для производства потерянных образцов, называемая «Потерянная бумага», генерирует объекты, которые не расширяются и не растрескивают оболочку во время цикла горения.
Среди материалов, используемых в 3D-печати, есть также подходящие для изготовления утраченных шаблонов.
Модель литья по выплавляемым моделям, полученная методом LOM, и собственно алюминиевая отливка |
Основными требованиями к потерянным образцам, изготовленным по технологии прямого RP, являются высокая точность размеров и низкая стоимость. НАСА построило компонент газоотводного клапана в качестве тестового примера для оценки сравнения различных методов RP. Шаблон, созданный методом RP, затем используется для разработки отливки с использованием литья по выплавляемым моделям.Затем произведенные отливки и модели оцениваются на предмет критической точности размеров и стоимости. Их результаты показывают, что высокая точность размеров шаблона не является критичной, точность окончательной отливки имеет более важное значение. Например, потерянный шаблон, созданный по SLA, отличается от исходной CAD-модели не более чем на 0,006 дюйма, тогда как тот же параметр для шаблона, сгенерированного SI, составляет 0,013 дюйма. Однако окончательная отливка отличается от начального чертежа в САПР 0,029 дюйма для SLA и 0,013 дюйма для SI. Поэтому, несмотря на разнообразие применяемых методов, только методы 3D-печати и СИ действительно эффективны при крупносерийном производстве литых деталей по технологии литья по выплавляемым моделям.
Прямое производство Shell
Этот метод можно рассматривать как следующий уровень в производстве инструментов, поскольку исключается даже необходимость в потерянном шаблоне. Технология основана на технологии 3D-печати с использованием керамического порошка. Изготовленная таким способом тонкостенная керамическая оболочка имеет внутренние полости, повторяющие форму желаемой отливки. Такой RT-подход можно рассматривать как метод создания корпуса отливки по выплавляемым моделям без утраченных шаблонов.
:: наверх ::.Сценарий применения RT при непрерывном литье в формы
В этом процессе используются многоразовые (постоянные) формы из металла. Стержни, используемые при литье в постоянные формы, также могут быть изготовлены из металла (стержни многократного использования) или песка (стержни одноразового использования). Поскольку металлические формы и стержни можно использовать повторно, они являются незаменимым инструментом при непрерывном литье в формы. Технологии RP могут использоваться в процессе изготовления постоянных форм как прямые, так и косвенные инструменты. Помимо металлических стержней, песчаные стержни, изготовленные методами RP, также могут быть использованы при литье в постоянную форму.
Инструменты прямого действия
Современные машины SLS способны спекать металлические порошки. Это дает возможность непосредственно создавать постоянные формы и стержни для разливки металлов с низкой температурой плавления, таких как алюминий, цинк и их сплавы.
В настоящее время существует два различных подхода к спеканию металлических порошков. В версии технологии спекания металлов 3D System детали создаются с использованием металлического порошка с полимерным покрытием. Полимер расплавляется под действием лазерного луча, и металлические частицы связываются вместе.Для достижения требуемых механических свойств детали должны пройти процесс чистовой обработки, при котором деталь нагревается, полимер выгорает, а частицы металла спекаются. Чтобы устранить пористость, деталь должна быть пропитана другим металлом (обычно сплавом на основе меди).
В отличие от 3D System, детали машин EOS создаются с использованием чистого металлического порошка без связующего или покрытия. Лазер частично плавит порошок, и частицы связываются вместе. Для устранения пористости деталь также должна быть пропитана другим металлом, например медью.
Детали, спеченные лазером, сравнимы по долговечности с литыми или коваными деталями, изготовленными из того же или подобного материала. Основным ограничением для обеих систем спекания металлов (3D System и EOS) является размер создаваемых моделей:
- 370x320x445 мм для 3D System Vanguard
- 250x250x200 мм для EOS M 250X
Также существует возможность создания металлической формы непосредственно из данных САПР без каких-либо других дополнительных процессов обработки, таких как инфильтрация или спекание.Такую возможность предоставляет процесс LENS, который позволяет создавать полностью плотные металлические формы. Ограничение процесса LENS по размерам генерируемых деталей (в нашем случае пресс-форм):
- 300x300x300 мм для OPTOMEC LENS 750
- 455x455x1000 мм для OPTOMEC LENS 850
Косвенный инструмент
Наиболее распространенным традиционным методом изготовления постоянных форм является литье в песчаные формы с механической обработкой или без нее. Эту технологию можно улучшить, используя модели, сгенерированные RP, в качестве шаблонов.Подход к использованию моделей, сгенерированных RP, в качестве шаблона при литье в песчаные формы уже описан выше.
Прототип пресс-формы, созданный SLA, и окончательный набор постоянных пресс-форм |
:: наверх ::.
С точки зрения инструментов, нет существенных различий между литьем под давлением и литьем в постоянную форму, поскольку в обеих технологиях используются металлические формы многократного использования. Однако матрицы для литья под давлением должны будут выдерживать очень высокое давление, и поэтому их труднее производить по сравнению с постоянными формами.В результате существует ограничение в отношении технологий, используемых для этого приложения. Процесс SLS с металлическими порошками используется для прямой оснастки для литья под давлением. Пример вставок для литья под давлением, изготовленных из стали путем прямого лазерного спекания металла, показан ниже.
Форма для литья алюминия из стали прямого спекания |
Матрица доказала, что с помощью этой вставки можно изготавливать приемлемые алюминиевые отливки.Было заявлено, что всего было произведено 500 отливок с использованием штампа, и штамп все еще годен для использования после изготовления 500 деталей. Другой пример инструментальных вставок для литья под давлением из магниевого сплава, полученных прямым спеканием металла, показан ниже.
Вставки для инструментов (корпус мобильного телефона Ericsson T28), изготовленные с использованием SLS для процесса литья под давлением |
:: наверх ::.