Шлакоблоки — технология производства
Несмотря на то, что чем дальше, тем увереннее приходится говорить о шлакоблоке в прошедшем времени, говорить о нем приходится. Огромное количество строительных стеновых материалов пришли на смену морально устаревшему шлакоблоку, тем не менее интерес к нему периодически проявляется. Нестабильность экономики способствует этому, поскольку шлакоблок очень дешев. Насколько он хорош, знают инженеры и физики, нас интересуют его самые обычные качества и технологии, по которым производили этот материал.
Содержание
- Как делают шлакоблок
- Преимущества шлакоблока
- Станок для производства шлакоблока
- Чертеж станка для производства шлакоблока
Как делают шлакоблок
Этот материал всегда рассматривался, как альтернативный кирпичу материал, и действительно, он имеет похожие показатели. Только кирпичи не так просто достаются, как шлакоблоки технология производства которых проста и незатейлива. Тем не менее, требует некоторых уточнений.
Шлакоблок — это доменные шлаки, печные шлаки, вода, цемент или гипс, перемешанные в разных пропорциях. Время шло, а технология производства шлакоблока улучшалась, появлялись все новые заполнители: щебенка, битый кирпич, керамзит, но чем бы не наполняли смесь, публика упрямо называла изделие шлакоблоком. Сам ход изготовления таков: проводили подготовку бетонной смеси из цемента или гипса, шлака или любого иного заполнителя, разводили водой, помещали в бетономешалку и разгружали в формы. Формы помещали на вибростол или под вибропресс для более эффективного уплотнения. После этого шлакоблок обретал знакомую всем форму.
Преимущества шлакоблока
Не зря его сравнивают с кирпичом, поскольку только путем этого сравнения можно было подчеркнуть выигрышную цену материала, а также некоторые другие положительные и интересные в строительстве характеристики:
- Очень низкая цена по сравнению с кирпичом.
- Производство шлакоблока не требовало никаких особенных условий и оборудования.
- Строительство дома из шлакоблока занимало меньше времени.
- Себестоимость куба шлакоблока и куба кирпича несравнима.
- Производить шлакоблок можно было просто на строительной площадке, что вообще сводило затраты на стройку в целом к минимуму.
Тем не менее, от шлакоблока стали отказываться по нескольким причинам, и сам шлак стал главной из них — в нем содержалось слишком много вредных веществ, несовместимых с жилыми постройками. Сразу же после производства шлакоблок должен был выстояться не менее одного года (по правильной технологии), а это уже вело к дополнительным затратам. В связи с этими дополнительными расходами применение вредного материала просто себя не окупало, поэтому на последний пункт в технологии попросту закрывают глаза.
Станок для производства шлакоблока
Бурное развитие частного строительства на фоне общего экономического спада возвращает шлакоблок в ряды строительных материалов. Для его производства создаются кустарные мастерские, мелкие предприятия, частные мелкие линии, в которых востребованность в оборудовании для производства шлакоблока только растет. Промышленность с удовольствием откликается на запросы публики и не перестает демонстрировать все новые варианты вибростолов и станков, при помощи которых возможно изготовление шлакоблока мелкими партиями.
В основном все станки делятся на две большие группы:
- мобильные;
- стационарные.
В частном строительстве применяются как простейшие, так и более сложные модели станков, причем большинство из них сделано своими руками. Мы не станем говорить об их производительности и качестве, поскольку ОТК у каждого в этом случае свое. Простейший станок для производства шлакоблока представляет собой деревянный ящик с перегородками. Каждая секция выполнена такого размера, который необходим на конкретном строительстве. Пустоты выполняются обычными бутылками из-под шампанского. Выглядит это так:
Для изготовления блока в таком станке используют более жидкие растворы. Раствор заливается в форму, а после предварительного застывания вынимается и помещается на отдельную площадку для застывания. Естественно, что качество такого строительного материала сомнительно и нестабильно.
Чертеж станка для производства шлакоблока
Станок с вибростолом или вибропрессом — более сложное устройство. Без определенной слесарной подготовки изготовить его будет проблематично, тем не менее, и такие станки собирают, успешно эксплуатируют, отливают блоки и строят из них дома. Вот примерный чертеж такого станка с примерными размерами.
Станок предназначен для изготовления блоков размером 390х190х188 мм с пустотностью 30%.
Самое ответственное задание — выполнить матрицу, в которой будет сформирован блок. Она выполняется из листа стали толщиной не менее 3 мм.
Целесообразность изготовления такого станка каждый может для себя определить сам. При работе над приспособлением стоит особое внимание уделить точности и прочности сварных швов.
Изготовление шлакоблоков на вибропрессе Рифей-04, организация и технология производства шлакоблока
Рифей-04 — технология производства и изготовления шлакоблоков с минимальным уровнем механизации
Вибропресс Рифей-04 ТСпозволяет наладить изготовление шлакоблоков и производство строительных материалов с минимальными затратами и максимальной эффективностью. Станок обладает высокой производительностью и уже 20 лет остается одним из лидеров продаж на рынке оборудования для производства шлакоблоков. Потребители ценят данную модель вибропресса за отсутствие необходимости вкладывать большие деньги в околопрессовое оборудование.
Мини-завод Рифей-04 ТС подходит бизнесменам, не располагающим значительными средствами и планирующим постепенно наращивать объемы производства и получать все большую прибыль.
Прежде чем остановиться на выборе данной модели вибропресса, ознакомьтесь со следующими документами:
- паспорт на вибропрессующую линию Рифей-04 ТС;
- упрощенное экономическое обоснование выпуска шлакоблоков на Рифей-04 ТС;
- требования к организации производства шлакоблоков на Рифей-04 ТС (смотрите информацию ниже).
Требования к размещению вибропресса
- Комплекс эксплуатируется в закрытом помещении или под навесом, оптимальная температура – от +5 до +45 градусов. Высота помещения – 3 метра.
- Для размещения вибропресса, складов сырья и продукции требуется помещение площадью, как минимум, 150 м2.
- Для успешной и безопасной работы вибропресса перед монтажом необходима заливка виброизолирующего фундамента.
- Линия требует подведения воды и электроэнергии с напряжением 380 вольт. Максимальная мощность вибропресса – 13,35 кВт в час.
Сырье и материалы
Технология производства шлакоблоков подразумевает использование качественной жесткой бетонной смеси, состоящей из заполнителя (шлаки, песок, отсевы производства щебня, керамзит, мраморная крошка), воды и вяжущего компонента (цемент).
Примерные варианты составов бетонных смесей описаны в разделе «Составы бетонов».
После формования сырые шлакоблоки должны подвергаться одной из двух процедур:
- Вылеживание при температуре от +15 до +45 градусов в течение 1 суток или при температуре от +5 до +10 градусов 2 в течение 2 суток. После вылеживания изделия становятся достаточно прочными для транспортировки и складирования.
Полную марочную прочность шлакоблоки приобретают после 28 суток вылеживания при температуре 20 градусов.
- Термовлажностная обработка в пропарочной камере в течение 6-8 часов при температуре от +50 до +75 градусов и влажности от 90%. Изделия приобретают 60-80 процентов конечной прочности.
Дополнительное оборудование, необходимое для успешного производства шлакоблоков на базе вибропресса Рифей-04 ТС
- Силос или растариватель для хранения цемента.
- Шнековый транспортер для перемещения цемента в смеситель.
- Бункеры с ленточным транспортером для хранения и подачи заполнителя в смеситель. Если перечисленное оборудование отсутствует, возможна подача компонентов в смеситель вручную.
- Поддоны из фанеры марки ФСФ с толщиной 30 миллиметров. Необходимы для вылеживания готовых сырых изделий в процессе пропаривания или естественного твердения. Для работы вибропресса требуются поддоны в количестве от 150 до 500 штук.
При наличии пропарочной камеры количество поддонов снижается.
Базовый комплект поставки вибропресса включает в себя 4 поддона, применяемые для изготовления опытной партии шлакоблоков.
Сварные металлические стеллажи. Необходимы для сбора и перемещения поддонов с готовыми изделиями. На стеллаж помещается 6 поддонов, и для вибропресса модели Рифей-04 ТС требуется 25-85 стеллажей.
Стеллажи и поддоны Вы можете заказать у нас вместе с вибропрессом или изготовить самостоятельно по чертежам, представленным в разделе сайта «Справочная информация».
- Грузоподъемное оборудование (погрузчик, кран-балка, кран-укосина, таль) необходимо для обеспечения максимальной производимости вибропресса.
Технология производства: алгоритм работы вибропрессующего комплекса для изготовления шлакоблоков
- Первый этап изготовления любых бетонных смесей – приготовление бетонной смеси из заполнителя, цемента и воды. Количество компонентов смеси определяется оператором визуально.
Вяжущий компонент и заполнитель подаются в смеситель с помощью бункеров или другого дополнительного оборудования, или вручную.
- После того, как смесь стала однородной, оператор должен открыть на дне бетоносмесителя люк, чтобы смесь переместилась на транспортер, который доставит ее на матрицу вибропресса, куда она загрузится за счет вибрации вибростола.
- После полной загрузки матрицы бетонная смесь будет уплотнена с помощью пуансона и вибраторов матрицы.
- Готовые сырые изделия выдавливаются на поддоны и перемещаются на стеллажи вручную, до их полной загрузки.
- Далее изделия транспортируются с помощью грузоподъемной техники в пропарочную камеру или место для вылеживания.
- После того, как изделия достигли достаточной прочности, они готовы к транспортировке к потребителю или на склад. Согласно технологии производства, шлакоблоки приобретают полную марочную прочность уже на складе готовой продукции.
Для работы с вибропрессом необходимо привлечение двух человек – оператора и вспомогательного рабочего.
Твитнуть
Как сделать шлакоблок в домашних условиях
- ПОСЛЕДНИЕ ЗАПИСИ Краски и эмали по металлу и ржавчине Пленка гидроизоляционная для крыши Как выбрать хорошую акриловую ванну Какие бывают розетки, их устройство, типы и классификация
- РУБРИКИ
- Автоматическое открывание, проветривание и полив теплиц
- Акриловые краски
- Балкон
- Блоки арболитовые
- Бурение скважин на воду
- Вода из скважины
- Водосток кровельный
- Воздух в квартире
- Выращивание дома
- Гидроизоляция
- Гидрофобизация материалов
- Дорожки садовые
- Камин своими руками
- Каркасный дом
- Кладка печи своими руками
- Крыша из металлочерепицы
- МДФ
- Монтаж кровли
- Монтаж ламината
- Монтаж линолеума
- Монтаж подложки под ламинат
- Натяжные потолки
- Опилкобетон
- ОСБ плита
- Отделка откосов
- Оштукатуривание
- Полипропиленовые трубы
- Расход материалов
- Тротуарная плитка
- Устройство отмостки
- Утепление
- Утепляем баню самостоятельно
- Фасад
- Фундамент из свай
- Шлакоблок
- Эмаль для ванны
Шлакоблок
Шлакоблоки получили широкое распространение в возведении не только хозяйственных построек, гаражей, но и капительного строительства. Они имеют низкую цену, поскольку состоят из недорогих материалов, обладают хорошими теплоизоляционными, шумопоглощающим характеристиками. Небольшой удельный вес позволяет сэкономить и на фундаменте, который может быть возведен облегченным. Внушительные габариты блоков позволяют значительно сократить время на строительство объектов.
Еще одним преимуществом этого конструктивного материала является то, что он может приобретаться не только в готовом исполнении, но и производиться самостоятельно. Это позволяет весомо снизить расходы на строительстве абсолютно любого объекта, независимого от его назначения. Конечно, производство шлакоблоков требует определенных временных затрат, но они полностью окупаются благодаря значительной денежной экономии, особенно при возведении достаточно крупных построек.
Производство шлакоблоков в домашних условиях
Технология получения шлакоблока своими руками предполагает два различных подхода:
- Простой. Заключается в задействовании исключительно емкостей, в которых раствор доходит до нужной кондиции.
- Сложный. Подразумевает задействование вибрационных устройств. Чаще всего используют вибростол либо снабжают саму форму моторчиком, имеющим вибрационную функцию.
Наиболее качественные изделия получаются вторым способом, но и первый позволяет изготовить достаточно хороший строительный материал.
Вибростанок
Необходим при возведении капитальной постройки, строительный материал для которой должен иметь повышенные качественные и прочностные характеристики. Установку можно приобрести уже в готовом решении либо изготовить самостоятельно.
Чтобы сделать станок для шлакоблока, потребуются:
- грузы;
- цилиндры;
- металлический лист,
- асинхронный двигатель.
Если шлакоблоки требуются для возведения хозяйственной постройки, то вполне можно обойтись без вибростанка.
Пошаговая инструкция по производству установки
Самодельный вибростанок изготавливают следующим образом:
- делают по две стальные заготовки 40х25 и 20х25, четыре ребра жесткости 4х4 и прижим 39.
5х19.5 см;
- крупные пластины идут на заготовку матрицы 40х20х25 см, сварочный шов которой должен располагаться с вешней стороны;
- цилиндры, которые формируют пустоты в конечных изделиях, нарезают из труб с диаметров 80 см;
- нарезанные части трубы размещают вертикальным рядом внутри матрицы, а к длинной стороне установки болтами через монтажные отверстия фиксируют вибратор;
- над полученным приспособлением крепят козырек, защищающий установленный двигатель от пагубного воздействия атмосферных осадков.
Установка готова к применению после приваривания к ручкам фиксатора. Полученный самодельный станов можно эксплуатировать по назначению сразу после окончания работ по его созданию.
Если конструкция недостаточно устойчива, это тоже можно исправить. С этой целью на края козырька следует прикрепить какую-либо опору.
Формы для шлакоблоков
Фабричные формы выполняются железными либо стальными, способными выдерживать вес больших объемов раствора, исчисляемых целыми тоннами. В домашнем производстве они изготавливаются из дерева и стального листа, служат нисколько емкостью для отлива шлакоблоков, но выполняют роль своеобразной опалубки. Главное, учитывать толщину материала. Иначе изделия получатся меньших размеров, нежели планировалось.
Чтобы сэкономить время и материал, формы делают, как правило, без дна, подкладывают под них обычную пленку. Это позволяет в значительной мере упростить весь процесс производства шлакоблоков. Формы должны быть выполнены из безупречно ровных деревянных частей, а рабочей поверхностью служить бетонная поверхность, стол с гладкой столешницей либо железный лист тоже без каких-либо дефектов.
Чтобы сформировать пустоты используют стеклянные бутылки. Пластиковые брать не рекомендуется, поскольку они могут деформироваться. Тару заполняют водой. Иначе она просто начнет всплывать на поверхность раствора.
Подробная инструкция по изготовлению емкости для шлакоблоков
Распространенный размер блоков составляет 40х20х20 сантиметров. Конструктивные элементы могут выполняться и отличных от стандартных габаритов. Это особенно удобно для частных застройщиков.
Чтобы сделать формы под шлакоблоки, необходимо:
- взять шлифованные доски с длиной в 14 см и шириной кратной данному размеру;
- ножовкой из рейки нарезать отрезки, которые будут служить поперечными перегородками;
- совместить отрезки с продольными сторонами для получения прямоугольного каркаса;
- раскроить стальной лист либо любой прочный и гладкий материал на пластины 14х30 см;
- внутри полученной конструкции делают распилы — пазы, шириной равной разделительным планкам;
- распределительные отрезки вставляют в распилы, получая форму для изготовления от трех и большего количества шлакоблоков.
Чтобы емкость для застывания раствора прослужила максимально долго и была качественной, на заключительном этапе и деревянные, и металлические детали рекомендуется покрыть масляной краской. Эта форма подходит для производства блоков 14х14х30 см. Если требуются элементы с иными габаритами, исходные значения меняют на другие размеры.
Состав смеси для шлакоблоков
Получить качественные шлакоблоки возможно только при использовании правильно замешанного раствора. Его получают из следующих составляющих:
- цемента;
- песка;
- воды;
- шлаковых компонентов.
Чтобы конечные элементы обладали высокими характеристиками, обязательно придерживаются правильных пропорций между составными компонентами:
- шлак — 7 частей;
- цемент — 1 часть;
- песок — 3 части;
- вода — 1 часть.
Оптимальным вариантом является использование цемента марок М400 или М500. Первый стоит дешевле, но второй позволяет сократить количество сырья на 10-15%, повысить качество получаемого шлакоблока.
Учитывая то, что самой затратной частью является именно цемент, экономия на его покупке не совсем целесообразна. Кроме того, чем выше марка, тем меньше расход, что тоже нужно принимать во внимание.
Шлаковые компоненты
Шлакоблоки получили свое название потому, что большая часть раствора приходится именно на шлак. В его качестве используют абсолютно любые строительные отходы:
- металлургические и щебневые;
- бой, образующийся от цемента, кирпичей, стекла;
- зола или торф;
- древесные опилки.
Никаких особых требований к этой составляющей смеси нет. Какой именно шлак использовать, зависит от того, что есть в распоряжении застройщика. Наряду с отходами, может добавляться и гранулированный пенополистирол.
Производство шлакоблоков на вибростанке
Технология производства и на изготовленной своими руками, и на приобретаемой мини-установке идентична:
- производственный цикл начинается с замеса раствора в бетономешалке;
- полученная смесь заливается в форму, выравнивается посредством мастерка;
- вибратор включается и на протяжении от 20 до 60 секунд раствор выдерживается в форме;
- устройство отключается, установка поднимается, а готовый шлакоблок высвобождается.
Особого внимания при выравнивании раствора заслуживают углы, которые обязательно должны быть тщательно заполнены. Иначе геометрия конечного изделия может пострадать.
Изготовление шлакоблоков с помощью форм
Немного сложнее, чем при использовании специальной установки. Это обусловлено тем, что раствор приходится утрамбовывать самостоятельно.
Само производство выглядит следующим образом:
- подготовленные компоненты в требуемых пропорциях помещают в бетономешалку, смешивают;
- готовым раствором заполняют формы, а утрамбовку проводят молотком, простукивая емкости, чтобы вышел весь воздух;
- если блоки предполагается делать с пустотами, то в каждый элемент устанавливают наполненные водой бутылки, как правило, достаточно двух штук.
Наибольшую сложность изготовления блоков без вибростанка вызывает утрамбовка. Если внутри смеси остается воздух, это негативно отражается на качестве конечного изделия.
Сушка шлакоблоков
Изготовление блоков занимает от двух и до четырех суток. Конечную прочность, при которой элементы полностью становятся готовыми к использованию, они набирают спустя 28 дней. Именно столько времени требуется для получения пригодного для возведение того или иного объекта строительного материала.
В период сушки необходимо предпринять меры, которые не допускают растрескивание блоков, пока они затвердевают. Чтобы элементы не пошли трещинами, их периодически смачивают. Особенно это важно тогда, когда блоки изготавливают в жаркую летнюю погоду.
Следует помнить о том, что пустоты никак не отражаются на прочности изделий. Они, наоборот, увеличивают шумопоглащающие и теплоизоляционные свойства материала, что положительно отражается на качестве постройки.
Общие рекомендации
Чтобы получить шлакоблоки для возведения строения, которое простоит долгие годы, следует соблюдать следующие нюансы:
- не располагать блоки во время сушки друг на друге;
- всегда сначала делать чертежи форм и блоков, чтобы никаких сложностей не возникало при строительстве;
- соблюдать рекомендуемые пропорции при замешивании раствора и технологию производства.
На двадцать девятые сутки, когда шлакоблоки полностью затвердели и высохли, их уже можно укладывать один на другой.
Watershed Materials — Технология для новых бетонных блоков
Watershed Materials разрабатывает технологию для более устойчивых, лучше выглядящих бетонных блоков с использованием меньшего количества цемента, переработанных материалов и новой машины для изготовления блоков.
Без цемента
Цемент имеет гигантский углеродный след и является самым дорогим компонентом современной бетонной кладки. Компания Watershed Materials с помощью Национального научного фонда разработала запатентованные составы смесей для производства прочной, эластичной, доступной и красивой кладки с использованием меньшего количества цемента.
Наша технология раскрывает силу минералов вокруг нас — известняка, гранита, риолита. Горные породы образуются в природе в течение миллионов лет, когда под давлением рыхлые зерна сплавляются в твердый камень. Компания Watershed Materials разработала технологию, позволяющую активировать этот процесс за секунды, а не за тысячелетия.
Готовый к рынку продукт Watershed Materials — блок Watershed — обеспечивает снижение расхода цемента на 50% и снижение потребляемой энергии на 65% по сравнению с обычной бетонной кладкой. Геополимерная технология Watershed Materials и состав известково-шлаковой смеси предлагают будущее без цемента.
Новая машина для производства бетонных блоков
Компания Watershed Materials получила грант в размере 740 000 долларов США от Национального научного фонда на создание революционно новой машины для массового производства конструкционной кладки. Мы применяем совершенно новую стратегию для эффективного производства недорогой кирпичной кладки с низким содержанием цемента из широкого спектра материалов, включая местные минералы, побочную продукцию карьеров и даже переработанный бетон.
Watershed Materials предлагает новую машину для нового века каменной кладки, которая сочетает в себе древнюю технологию, впервые разработанную римлянами, с современной наукой о наночастицах.
Свяжитесь с нами, если вы заинтересованы в нашей технологии производства блоков.
Вторичное сырье
Традиционная бетонная кладка изготавливается из тускло-серой первозданной породы, которая обрабатывается с большим количеством энергии и воды. Компания Watershed Materials разработала технологию, позволяющую использовать до 100 % переработанного материала местного производства в качестве заполнителя для новой эволюции экологичной каменной кладки.
Переработанные постиндустриальные материалы, включая карьерные отходы или переработанный бетон, используемые в сыром виде без промывки или интенсивной обработки, могут быть использованы для производства красивой каменной кладки, которая выражает красоту, теплоту и региональность местных материалов.
Технология Watershed Materials не включает красителей, красителей или искусственных пигментов. Поверхностная обработка не требуется, что устраняет опасения по поводу летучих органических соединений (ЛОС) и других вредных покрытий.
Геополимерная технология
Компания Watershed Materials разработала решение для производства высокопрочной кладки с низким углеродным следом с использованием геополимеров на основе природных минералов. Эта технология позволяет превращать природные глины, которые легко найти на всей планете, в надежные продукты для кладки и предлагает устойчивую альтернативу традиционной бетонной кладке.
Недавние испытательные образцы конструкций из геополимерных смесей достигли прочности на сжатие 7000 фунтов на квадратный дюйм, что вдвое превышает прочность обычного бетона, без использования цемента, без золы-уноса, без доменного шлака, без метакаолина и без высокотемпературного обжига или отверждения. Наряду с высокой прочностью на сжатие составы геополимерных смесей продемонстрировали замечательную устойчивость к воде и химической эрозии.
Представляем Watershed Block™. Красивый. Доступный. Устойчивый. Стабильный.
Ежегодно производятся десятки миллиардов бетонных блоков, содержащих слишком много цемента и слишком мало регионального характера. Watershed Block предлагает новый подход к бетонной кладке, сочетающий в себе современную эстетику, местные материалы и уважение к окружающей среде.
Водораздельный блок — обзор продукта
Stanford Block
Цветовая палитра блока Stanford Watershed вдохновлена богатым красновато-коричневым песчаником под кампусом Стэнфордского университета. АСТМ С90 соответствует. См. сведения о продукте ->
Известково-белый блок
Известково-белый водораздельный блок не содержит цемента и имеет ярко-белый вид, который получается из извести и белой глины. Соответствует ASTM C90. См. сведения о продукте ->
Syar Slate Block
Syar Slate Watershed Block, представляющий собой смесь одного происхождения, выделяет темный юрский базальт из карьера Syar в округе Солано. Соответствует ASTM C90. См. сведения о продукте ->
Блок Марк Вест
Льняной оттенок блока Водораздел Марк Вест происходит из минералов из двух карьеров в горах Маякамас в Сономе. Соответствует ASTM C90. См. сведения о продукте ->
Pascale Block
Разноцветные желтовато-коричневые и коричневые оттенки поверхности Pascale Watershed Block из смеси двух каменных продуктов. Самый высокий профиль устойчивости. См. сведения о продукте ->
Блок Sweetwater
Цвет восхода солнца блока Sweetwater Watershed обусловлен теплым, почти персиковым оттенком преобладающей дробленой мелочи. Самый высокий профиль устойчивости. См. сведения о продукте ->
Производственный процесс CMU | Nitterhouse Masonry
Процесс производства CMU | Каменная кладка НиттерхаусИзготовление бетонных блоков в Nitterhouse MasonryКомпания Nitterhouse Masonry Products гордится каждым произведенным блоком, брусчаткой и камнем. Мы всегда следим за тем, чтобы вся наша продукция производилась в соответствии с высочайшими стандартами и максимально возможного качества.
Процесс изготовления бетонной кладки (БКМ) практически не изменился с момента его появления в начале 1900-х годов. Сырье смешивают с водой, формуют в форму и оставляют на некоторое время для отверждения. Основной процесс прост, но с прогрессом в отрасли за эти годы производство CMU стало наукой химического машиностроения и архитектурной целостности.
С момента своего основания в 1923 году как Nitterhouse Concrete Products до семьи компаний по производству бетона и камня, которая сегодня называется Nitterhouse, мы создали более совершенные системы для увеличения производства, контроля качества, мониторинга процессов и широкого спектра архитектурных бетонных изделий. В нашем процессе CMU используются лучшие технологии и оборудование, управляемые и контролируемые специальной командой, которая гордится каждым производимым блоком.
Мы предлагаем широкий выбор визуальных эффектов и производим определенные конструкции, которые обеспечивают определенные структурные особенности для уникальных применений. Вы обнаружите, что эстетически приятная природная красота камня проявляется по-разному, в зависимости от типа блока. Кроме того, переработанный материал в нашем переработанном CMU может быть именно тем, что необходимо для вашей следующей экологически ориентированной сборки.
Несмотря на то, что у вас есть большой выбор внешнего вида архитектурного блока, основной процесс изготовления бетонного блока одинаков. Будут варьироваться тип и количество сырья, а также время отверждения, а окружающая среда будет регулироваться в зависимости от качеств, необходимых для готового продукта. Мы предоставляем наш процесс производства блоков CMU, чтобы помочь архитекторам реализовать наши производственные возможности, чтобы помочь инженерам выбрать блок, структурно стабильный для их проекта, и чтобы подрядчики по каменной кладке знали, что можно быстро изготовить, когда это необходимо.
Материалы Обычно для формирования бетонного блока требуется только два типа материалов: заполнители и цементы. Заполнители, такие как песок и щебень, образуют основную структуру блока. Цемент действует как связующее, которое удерживает заполнители вместе и затвердевает при смешивании с водой.
Песок, камень и цемент доставляются на наши заводы большегрузными самосвалами из местных карьеров. Агрегаты хранятся в открытых бункерах на нашем дворе. Так как цемент чувствителен к влаге, он задувается в наши цементные силосы. У нас есть различные типы и размеры заполнителей и цемента для производства нашей разнообразной линейки архитектурных бетонных блоков.
Каждая единица бетонных блоков будет содержать следующие материалы в различных количествах и вариациях в зависимости от того, какой тип архитектурного блока используется на производственной линии:
бетонных смесей, применяемых в общестроительных целях, смесь для бетонных блоков будет иметь более высокое соотношение песка к гравию и воде. В результате получается сухая, жесткая смесь с высокой прочностью на сжатие, которая сохраняет свою форму при извлечении из блочной формы.
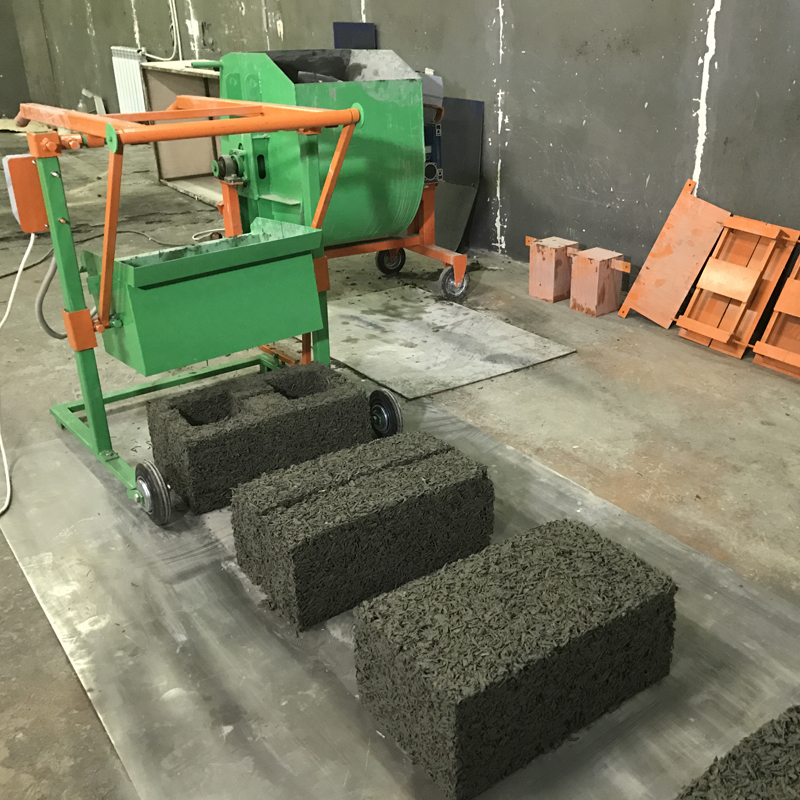
Материалы, необходимые в течение дня, вывозятся во дворе фронтальным погрузчиком и сбрасываются в закрытые отсеки, связанные с производственной линией. Наш оператор станка выбирает количество сырья, необходимого для партии, производимой в нашей компьютеризированной системе, которая точно измеряет и выпускает материал для изготовления блока того типа, который мы используем.
Вот как происходит процесс:
Этап 1
Смешивание
После измерения необходимого количества материалов они выгружаются на конвейерную ленту. Конвейер перемещает материалы в наш смеситель объемом 1,75 кубических ярда, где вода добавляется по мере заливки заполнителей и бетона. Вода также точно контролируется нашей электронной измерительной системой, чтобы смесь не была слишком влажной или слишком сухой.
Затем добавляют любые дополнительные добавки, такие как гидрофобизаторы или пигменты, и смесь перемешивают в течение шести-восьми минут.
Этап 2
Формование
Когда смесь надлежащим образом перемешана, бетон перемещается на другую конвейерную ленту, которая поступает на нашу машину для изготовления блоков. Одна из наших различных форм будет настроена для конкретного типа CMU, который мы производим в партии. После того, как замес разлит в формы, блок-машина вибрацией уплотняет бетонную смесь. Мы делаем это, чтобы придать бетону прочность и уплотнить бетон в блок.
Формование бетона является наиболее важным этапом изготовления КМУ. Надлежащее сжатие имеет важное значение для получения качественного готового продукта. Материалы подаются в формы с измеренной скоростью потока, а время и сила вибрации точно контролируются, чтобы обеспечить соответствующую высоту и прочность блока.
Когда достигается надлежащее сжатие и консолидация, блок выталкивается из формы на стальной поддон, чтобы его можно было транспортировать в нашу печь для отверждения. На его этапе цемент называют «зеленым блоком», прежде чем он вылечит и затвердеет.
Этап 3
Отверждение
Затем поддоны перемещаются на тележки, которые перемещаются в нашу паровую печь низкого давления для нагрева. Как правило, стеллаж из бетонных блоков выдерживается в печи при нормальной влажности и температуре (от 70 до 100 градусов по Фаренгейту) на срок до трех часов. Затем в печь постепенно вводят пар и медленно повышают температуру до соответствующего уровня.
Когда достигается максимальная температура, подача пара и тепла отключается, и блоки сохнут еще от 12 до 18 часов в горячем влажном воздухе. Затем из печи выгоняют влажный воздух и повышают температуру до полного высыхания блока.
Блок обычно отверждается в течение 16-24 часов при высокой влажности и средней температуре около 100 градусов по Фаренгейту.
Этап 4
Кубирование и хранение
По завершении отверждения бетонный блок выкатывают из печи. Затем каждый блок распаковывается и помещается на наш конвейер. Они переходят к нашей системе кубирования, которая укладывает блоки на деревянный поддон. Каждый блок выровнен и сложен, чтобы сформировать куб, четыре блока в поперечнике, два блока в глубину и шесть блоков в высоту.
Наши блоки с разъемной поверхностью, например, отлиты из двух блоков, соединенных вместе. После затвердевания двойные блоки проходят через наш сплиттер. Разделитель ударяет по соединенным блокам, вызывая их разрушение и создавая шероховатую текстуру на одной стороне каждого куска. Затем их кубируют и складывают.
Мы заворачиваем куб в пластик для безопасности и защиты от непогоды, и его доставляют на вилочном погрузчике в соответствующую секцию нашего двора для этого конкретного типа блоков или для определенного заказа. Отсюда будут подъезжать блок-фуры и загружать продукцию по мере необходимости.
Обеспечение качества при производстве CMU Различные участки нашего завода постоянно контролируются, чтобы подтвердить, что мы производим блоки с особыми характеристиками. Будь то прочность, устойчивость к атмосферным воздействиям и химическим веществам или спецификации конструкции, у нас есть электронный контроль, и операторы машин постоянно следят за тем, чтобы готовый блок работал в соответствии с требованиями. Мы гарантируем:
- Заполнители и цемент взвешиваются электронным способом, чтобы убедиться, что правильные части каждого материала, которые влияют на внешний вид, ощущение и долговечность блока, являются правильными.
- Содержание влаги в песке и гравии измеряется с помощью ультразвуковых датчиков, поэтому в смесь можно добавить точное количество воды для точного содержания воды, необходимого для партии.
- Размер и плотность каждого блока проверяются с помощью датчиков лазерного луча, когда каждый блок выходит из машины для изготовления блоков.
- Среда отверждения регулируется электронным способом для контроля времени цикла, температуры и давления. Вся информация записывается для каждой партии.
- Готовые блоки проверяются на различные качества, такие как звукопроницаемость, водопроницаемость, огнестойкость, прочность и усадка.
Бетонный блок должен выдерживать суровые погодные условия, пожар и другие виды серьезных повреждений. Нет ничего лучше, чем блок, если вам нужен прочный, огнестойкий, устойчивый к насекомым и вторжению строительный материал. Мы следим за тем, чтобы в каждом блоке, покидающем наш завод, сохранялась целостность.
Многоликость архитектурных бетонных блоковКомпания Nitterhouse Masonry Products гордится каждым произведенным блоком, брусчаткой и камнем. Мы всегда следим за тем, чтобы вся наша продукция производилась в соответствии с высочайшими стандартами и максимально возможного качества. Наша линейка архитектурных бетонных блоков включает в себя множество вариантов с текстурированным внешним видом или гладкой отделкой из шпона, а также различных цветов, форм и размеров, чтобы предоставить профессионалам в области дизайна широкий спектр вариантов строительства из бетонной кладки.
Нужен ли вам базовый бетонный блок для срочной работы, у вас есть архитектурная специальность для строительства или вам нужен особый вид сложного офисного здания, мы можем изготовить блок, который вам нужен. Ознакомьтесь с каждой единицей бетонного блока, чтобы узнать все, что доступно для вашего следующего строительного проекта:
- Отделка шлифованной поверхности. Наш шлифованный CMU отшлифован как минимум с одной стороны, что придает ему гладкую и богатую поверхность. Благодаря 20 стандартным цветам у вас будет множество вариантов комбинирования цветов, но мы также можем настроить пигмент в соответствии с вашими требованиями к дизайну.
- Раздельная лицевая поверхность. Этот текстурированный блок выпускается со стандартной отделкой Split Face, Split Wide Profile и Split Fluted, чтобы соответствовать широкому диапазону архитектурных образов. Глубина и размеры этой конструкции являются фаворитами для различных внутренних и внешних строительных проектов и, как и многие из наших CMU, могут использоваться на уровне земли или ниже.
- Античная отделка. Наш антикварный CMU обработан дробеструйной обработкой, которая красиво обнажает камень под ним.
У нас есть несколько стандартных цветов, и если они вам не подходят, мы можем настроить цвет специально для вашего проекта. Этот блок обеспечивает прекрасный вид состаренного вида с деревенской текстурой, который используется как для внутреннего, так и для внешнего строительства.
- Монарх Традиционный. Вы получаете внешний вид глиняного кирпича с качеством блока в нашей традиционной линии Monarch. Эти CMU имеют длину и глубину обычного блока, но высоту стандартного кирпича. Вы можете использовать этот блок в классе и ниже. Мы разработали их в соответствии со стандартами ASTM-C90 для несущей бетонной кладки.
- Элитный КМУ. Нет необходимости укладывать блоки, а затем облицовывать их керамической плиткой для внутренних работ. Наш Elite CMU — выдающийся строительный материал как для внутреннего, так и для внешнего совершенства. Благодаря выбору цвета, например, лососевому или оружейному металлу, эти наполненные и полированные блоки идеально подходят для крупных коммерческих проектов, таких как школы или муниципальные здания, которым требуется оттенок цвета и стиля.
Лица шлифуются, а затем заполняются наполнителем из акриловой смолы. После полировки они герметизируются нашим герметиком, совместимым с летучими органическими соединениями (ЛОС).
- Переработанный CMU. Наш «Эко-умный» переработанный CMU изготавливается с шлифованной и разделенной поверхностью. Минимум 30% переработанного материала — это популярный выбор для вашего проекта, ориентированного на защиту окружающей среды. Переработанный контент принесет вам баллы LEED (Лидерство в энергетическом и экологическом дизайне) за ваши экологические усилия.
- Камень наследия. Наш камень наследия — это блок архитектурного шпона, демонстрирующий совокупное содержание блока. Он изготовлен с прочностью 8500 фунтов на квадратный дюйм и абсорбцией менее 5%. В нашей линейке Legacy есть четыре разных отделки, которые часто смешиваются в одном проекте для визуальной привлекательности и структуры:
- Linear Collection – две отделки на одном блоке: шлифованная поверхность и дробеструйная обработка.
Ширина каждой полосы настраивается в соответствии с уникальным дизайном, а между двумя разными отделками есть глубокие линии с насечками.
- Textured – лицевая сторона обработана дробеструйной обработкой, что придает текстуру и объем.
- Терраццо – шлифованная поверхность, гладкая и полированная, определяет этот бетонный блок. Его часто используют для оклейки полос.
- Точеная грань — обработанные таким образом, чтобы они напоминали ограненный известняк, эти камни часто используются для акцентных полос, чтобы разбить большие участки одного цвета и текстуры.
- Linear Collection – две отделки на одном блоке: шлифованная поверхность и дробеструйная обработка.
Выберите желаемый блок в различных специализированных формах для конкретных строительных приложений. Мы производим специальные формы из бетонных блоков для строительства соединительных балок, контрольных швов, закругленных углов и многих других архитектурных проектов.
Все архитектурные CMU Nitterhouse герметизированы герметиком на водной основе из акриловой смолы, совместимым с летучими органическими соединениями, и должны быть покрыты другой герметизирующей пропиткой после завершения кладочных работ. Мы также добавляем водоотталкивающую добавку во все наши партии бетонных блоков, чтобы уменьшить абсорбцию и проницаемость. Мы предоставляем эту добавку для добавления в раствор при кладке стен.
Кирпичный блок для звукового строительства и креативного дизайна
Занимаясь бизнесом более 90 лет, мы расширяем линейку продуктов и производственные возможности по мере изменения технологий и передового опыта. От деловых амбиций каменщика Уильяма Л. Ниттерхауса, строящего свой собственный блок в своем гараже, до семейной линии в пятом поколении, которая сегодня занимается нашим производством камня, мы поставили перед собой задачу обеспечить лучшее качество, варианты и дизайн.
В будущем индустрия производства блоков будет продолжать внедрять новые формы, размеры и экономические преимущества в строительстве зданий. Энергоэффективность и долговечные конструкции будут оставаться в авангарде новых разработок. Наши дизайнеры создали превосходные продукты, которые зарекомендовали себя как гармоничное сочетание эстетической привлекательности и структурной надежности для любого типа здания.
Независимо от того, хотите ли вы построить общественный центр или высотное здание, вы обнаружите, что мы можем предоставить именно то, что вам нужно, чтобы сделать ваш проект исключительным. Ознакомьтесь с нашей полной линейкой архитектурных бетонных блоков и откройте для себя разнообразие, которое даст вам гибкость при проектировании. Для получения дополнительной информации о нашем процессе производства блоков или о любом из наших продуктов для каменной кладки, пожалуйста, свяжитесь с нами сегодня.
Машины для производства бетонных блоков — Columbia Machine
Самые технологически совершенные машины для производства бетонных блоков на рынке позволяют вам создавать самые разнообразные бетонные блоки с лучшим в отрасли временем цикла.
Связаться
CVT
Технология вибрации Columbia позволяет производителям создавать продукцию самого высокого качества и самый широкий ассортимент продукции в мире.
Машины для производства бетонных блоков
Наши машины для производства бетонных блоков разработаны для производства высококачественных бетонных блоков для любого рынка. Найдите машину для производства бетонных блоков, соответствующую вашим производственным требованиям.
Запчасти и обслуживание
Наш квалифицированный персонал готов помочь вам и вашей работе в нужное русло, предоставив опытные консультации, а также оперативный доступ к запасным частям.
Мы продолжаем инвестировать в оборудование Columbia, потому что мы твердо верим, что Columbia производит самые точные и стабильные бетонные блоки на рынке.
— Аллан Иствуд, Лигнацит
Columbia Vibration Technology
Запатентованная вибрационная технология Columbia, CVT, сочетает в себе более чем 80-летний инновационный инжиниринг и проверенные на практике конструкции с ведущими в отрасли производственными возможностями.
Узнать больше
Представляем CPM+
Конструкция машины для производства бетонных изделий CPM+ основывается на успехе предыдущего поколения серии CPM. Оригинальный CPM надежно работает на заводах по всему миру с 1995. За прошедшие годы Columbia Machine стала свидетелем изменений в отраслях, которые мы обслуживаем, предъявляя повышенные требования к производственным предприятиям. CPM+ разработан для удовлетворения этих требований.
Машины для производства бетонных блоков
Проверено в самых сложных условиях. Машины для производства бетонных блоков Columbia заслужили репутацию превосходных инженерных решений, непревзойденной производительности и высочайшего качества производства. Наши машины для производства бетонных блоков используют проверенные на практике технологии, чтобы производить продукцию непревзойденного качества, точности и разнообразия. Благодаря частотно-регулируемому приводу, прямой вибрации пресс-формы и плавному гидравлическому перемещению, Columbia является эталоном в отрасли.
Машины для производства бетонных блоков с малыми поддонами
Эти классические рабочие лошадки будут производить лучшие в отрасли бетонные блоки на протяжении десятилетий.
Технические характеристики модели
СПМ20
Детали производства бетонных блоков
Продукт в час
500
Продуктов за цикл
2
Высота изделия мин.
2″
(50 мм)
Высота изделия МАКС.
8 дюймов
(200 мм)
Стандартная длина поддона
20 дюймов
(508 мм)
Технические характеристики машины для производства бетонных блоков
Ширина
53 дюйма
(1350 мм)
Высота
102 дюйма
(2594 мм)
Длина
87 дюймов
(2214 мм)
Масса
10 487 фунтов
(4575 кг)
Загрузить брошюру »
Модель 21
Детали производства бетонных блоков
Продуктов в час
500
Продуктов за цикл
2
Высота изделия мин.
2 дюйма
(51 мм)
Высота изделия МАКС.
8 дюймов
(203 мм)
Стандартная длина поддона
20 дюймов
(508 мм)
Технические характеристики машины для производства бетонных блоков
Ширина
64 дюйма
(1626 мм)
Высота
95 дюймов
(2413 мм)
Длина
110 дюймов
(2794 мм)
Масса
11 200 фунтов
(5080 кг)
Загрузить брошюру »
Модель 22
Детали производства бетонных блоков
Продуктов в час
960
Продуктов за цикл
2
Высота изделия мин.
2 дюйма
(51 мм)
Высота изделия МАКС.
12 дюймов
(305 мм)
Стандартная длина поддона
18 дюймов
(457 мм)
Технические характеристики машины для производства бетонных блоков
Ширина
75 дюймов
(1905 мм)
Высота
94,325 дюйма
(2396 мм)
Длина
107 дюймов
(2718 мм)
Масса
13 500 фунтов
(6123 кг)
Загрузить брошюру »
Модель 16
Детали производства бетонных блоков
Продуктов в час
1440
Продуктов за цикл
3
Высота изделия мин.
0,75 дюйма
(19 мм)
Высота изделия МАКС.
12 дюймов
(305 мм)
Стандартная длина поддона
26 дюймов
(660 мм)
Технические характеристики машины для производства бетонных блоков
Ширина
83,5 дюйма
(2121 мм)
Высота
92,5 дюйма
(2350 мм)
Длина
94 дюйма
(2388 мм)
Масса
15 300 фунтов
(6940 кг)
Загрузить брошюру »
CPM+30
Детали производства бетонных блоков
Продуктов за цикл
3
Высота изделия мин.
0,75 дюйма
(19 мм)
Высота изделия МАКС.
12 дюймов
(305 мм)
Технические характеристики машины для производства бетонных блоков
Ширина
165 дюймов
(4191 мм)
Высота
134 дюйма
(3404 мм)
Длина
174″
(4420 мм)
Масса
39 130 фунтов
(17 749 кг)
Размеры поддонов
Длина мин.
18,5″
(470 мм)
Длина МАКС.
27,5″
(670 мм)
Ширина
26 дюймов
(660 мм)
Стандартная толщина
0,31 дюйма
(7,8 мм)
Загрузить брошюру »
Машины для производства бетонных блоков со средними поддонами
Мощные машины для производства бетонных блоков на 4-6 штук с вертикальной вибрацией, чтобы раз за разом производить неизменно превосходную продукцию.
Технические характеристики модели
СРМ+40
Детали производства бетонных блоков
Продуктов за цикл
4
Высота изделия мин.
0,75 дюйма
(19 мм)
Высота изделия МАКС.
12 дюймов
(305 мм)
Технические характеристики машины для производства бетонных блоков
Ширина
160 дюймов
(4064 мм)
Высота
134 дюйма
(3404 мм)
Длина
174″
(4420 мм)
Масса
39 130 фунтов
(17 749 кг)
Размер поддона
Длина мин.
18,5″
(470 мм)
Длина МАКС.
27,5″
(700 мм)
Ширина
37 дюймов
(940 мм)
Стандартная толщина
0,38 дюйма
(9,7 мм)
Загрузить брошюру »
CPM+50
Детали производства бетонных блоков
Продуктов за цикл
5
Высота изделия мин.
0,75 дюйма
(19 мм)
Высота изделия МАКС.
12 дюймов
(305 мм)
Технические характеристики машины для производства бетонных блоков
Ширина
165 дюймов
(4191 мм)
Высота
134 дюйма
(3404 мм)
Длина
174″
(4420 мм)
Масса
39 130 фунтов
(17 749 кг)
Размер поддона
Длина мин.
18,5 дюйма
(470 мм)
Длина МАКС.
27,5″
(700 мм)
Ширина
42 дюйма
(1067 мм)
Стандартная толщина
0,44 дюйма
(11,2 мм)
Загрузить брошюру »
CPM+60
Детали производства бетонных блоков
Продукт за цикл
6
Высота изделия мин.
0,75 дюйма
(19 мм)
Высота изделия МАКС.
12 дюймов
(305 мм)
Технические характеристики машины для производства бетонных блоков
Ширина
188 дюймов
(4775 мм)
Высота
134 дюйма
(3404 мм)
Длина
174″
(4420 мм)
Масса
42 500 фунтов
(20 185 кг)
Размер поддона
Длина поддона МИН.
18,5″
(470 мм)
Макс. длина поддона
27,5″
(700 мм)
Ширина
55,1 дюйма
(1400 мм)
Стандартная толщина
.50
(12,7 мм)
Загрузить брошюру »
Модель 1600
Детали производства бетонных блоков
Продукт за цикл
4
Высота изделия мин.
2 дюйма
(50,8 мм)
Высота изделия МАКС.
12 дюймов
(305 мм)
Технические характеристики машины для производства бетонных блоков
Ширина
91″
(2311 мм)
Высота
92,5 дюйма
(2350 мм)
Длина
94 дюйма
(238 мм)
Масса
22000 фунтов
(9979 кг)
Размер поддона
Ширина поддона
37 дюймов
(940 мм)
Глубина поддона
18,5″
(470 мм)
Толщина
. 375″
(9,5 мм)
Загрузить брошюру »
Машины для производства бетонных блоков с большими поддонами
Наша самая технологичная машина для производства бетонных блоков в формате больших поддонов.
Технические характеристики модели
СРМ+120
Детали производства бетонных блоков
Продуктов за цикл
12
Высота изделия мин.
1,57 дюйма
(40 мм)
Высота изделия МАКС.
12 дюймов
(305 мм)
Технические характеристики машины для производства бетонных блоков
Ширина
154 дюйма
(3912 мм)
Высота
138 дюймов
(3505 мм)
Длина
230 дюймов
(5842 мм)
Масса
69 000 фунтов
(31 298 кг)
Размер поддона
Длина мин.
37,4 дюйма
(950 мм)
Длина МАКС.